Complete Welding Engineer Career Guide
Welding engineers are critical to modern manufacturing and infrastructure, designing and optimizing the joining processes that build everything from skyscrapers to spacecraft. They blend advanced materials science with mechanical engineering principles to ensure structural integrity and efficiency, solving complex challenges in diverse industries.
This specialized role demands precision and innovation, offering a unique path for engineers who want to see their theoretical knowledge directly applied to tangible, high-impact projects.
Key Facts & Statistics
Median Salary
$99,040 USD
(U.S. national median, May 2023 BLS data)
Range: $65k - $140k+ USD
Growth Outlook
4%
as fast as average
Annual Openings
≈3,000
openings annually
Top Industries
Typical Education
Bachelor's degree in Welding Engineering, Materials Science and Engineering, or Mechanical Engineering. Master's degrees are often preferred for advanced roles.
What is a Welding Engineer?
A Welding Engineer is a specialized professional who applies scientific principles and engineering practices to the design, manufacturing, and quality control of welded structures and components. This role focuses on optimizing welding processes, materials, and procedures to ensure the integrity, performance, and cost-effectiveness of welded products across various industries such as aerospace, automotive, construction, and oil & gas.
Unlike a welder who executes the weld, or a welding technician who performs routine inspections and maintenance, the Welding Engineer is responsible for the 'how' and 'why' of welding. They develop the specifications, troubleshoot complex issues, and ensure compliance with stringent industry codes and standards, bridging the gap between design theory and practical fabrication. Their expertise prevents failures, improves efficiency, and drives innovation in joining technologies.
What does a Welding Engineer do?
Key Responsibilities
- Develop and qualify welding procedures for new projects, ensuring compliance with industry codes like ASME, AWS, and API.
- Analyze welding defects and failures, then implement corrective actions to improve product quality and reduce rework.
- Select appropriate welding processes, filler materials, and equipment based on material properties and application requirements.
- Conduct metallurgical examinations of welded joints to assess mechanical properties and microstructure integrity.
- Oversee the training and certification of welding personnel, ensuring they adhere to established procedures and safety standards.
- Collaborate with design and manufacturing teams to optimize weld designs for manufacturability, cost-efficiency, and performance.
- Perform root cause analysis on production issues related to welding, implementing robust solutions to prevent recurrence.
Work Environment
Welding Engineers primarily work in manufacturing plants, fabrication shops, or research and development facilities. Their environment often balances office work for design, analysis, and documentation with significant time spent on the shop floor or in laboratories. They frequently collaborate with production managers, quality control inspectors, design engineers, and skilled welders. The pace can be dynamic, particularly when troubleshooting urgent production issues or fast-tracking new project qualifications.
Travel may be required for site visits, vendor evaluations, or attending industry conferences. While some remote work is possible for analysis and documentation, hands-on involvement with welding processes and equipment necessitates a strong physical presence. Safety is paramount, requiring adherence to strict protocols in environments with high temperatures, fumes, and heavy machinery.
Tools & Technologies
Welding Engineers regularly use specialized software for weld simulation, such as WELDING HYBRID and SYSWELD, to predict distortion and residual stress. They also work with CAD software like SolidWorks or AutoCAD for design review and fixture conceptualization. Laboratory equipment includes optical microscopes, scanning electron microscopes (SEM), and various mechanical testing machines like tensile testers and Charpy impact testers for material analysis. Non-destructive testing (NDT) equipment such as ultrasonic testing (UT), radiographic testing (RT), and magnetic particle testing (MPT) tools are essential for quality assurance. They also utilize various welding power sources and automation systems, along with data acquisition systems for process monitoring.
Familiarity with programming languages for automated welding systems, like PLC programming or robotic control software, becomes increasingly important for advanced roles. Project management software like Jira or Asana helps manage timelines and tasks for procedure development and defect resolution. Statistical process control (SPC) software aids in analyzing welding data for continuous improvement initiatives.
Welding Engineer Skills & Qualifications
A Welding Engineer's qualifications are highly specialized, focusing on material science, metallurgy, and advanced welding processes. Employers typically prioritize a blend of formal education and practical experience. Entry-level positions usually require a bachelor's degree, while senior or research-oriented roles often benefit from a master's or even a Ph.D. Certifications are crucial, particularly those from the American Welding Society (AWS), as they validate specific expertise and adherence to industry standards.
Requirements for a Welding Engineer vary significantly based on the industry. For instance, the aerospace and nuclear sectors demand stringent regulatory compliance and advanced non-destructive testing knowledge. In contrast, heavy fabrication or construction might emphasize process optimization and cost efficiency. Company size also plays a role; larger organizations might have highly specialized roles, while smaller firms often require a broader skill set. Geographic location can influence requirements, with some regions having specific codes or industry focuses.
The skill landscape for Welding Engineers is continuously evolving. The rise of automation, robotics, and advanced materials necessitates ongoing learning in areas like additive manufacturing and digital simulation. While formal education provides foundational knowledge, practical experience with diverse welding techniques and materials is indispensable. Certifications, especially those related to specific codes (e.g., ASME, API) or advanced inspection methods, bridge the gap between theoretical knowledge and industry application. This balance between academic rigor, hands-on application, and continuous professional development defines success in this field.
Education Requirements
Technical Skills
- Advanced Welding Processes (e.g., GTAW, GMAW, SAW, FCAW, Laser Welding, Friction Stir Welding)
- Metallurgy and Material Science (e.g., ferrous and non-ferrous alloys, heat treatment, phase transformations)
- Welding Codes and Standards (e.g., AWS D1.1, ASME Section IX, API 1104, EN ISO standards)
- Non-Destructive Testing (NDT) Methods (e.g., UT, RT, PT, MT, VT) and interpretation
- Weld Design and Joint Configuration (e.g., fatigue analysis, stress analysis, distortion control)
- Welding Procedure Specification (WPS) and Procedure Qualification Record (PQR) development and review
- Failure Analysis and Root Cause Investigation of welded structures
- Computer-Aided Design (CAD) and Simulation Software (e.g., SolidWorks, ANSYS for thermal/structural analysis)
- Welding Automation and Robotics programming and integration
- Quality Control and Assurance principles specific to welding
- Additive Manufacturing (3D printing with metals) processes and material considerations
- Statistical Process Control (SPC) for welding processes
Soft Skills
- Problem-solving: Welding Engineers frequently diagnose and resolve complex issues related to weld defects, material compatibility, and process optimization.
- Attention to detail: Precision is paramount in welding engineering; small errors can lead to critical structural failures or costly reworks.
- Technical communication: Clearly explaining complex technical concepts, specifications, and procedures to welders, management, and clients is essential.
- Collaboration: Working effectively with cross-functional teams, including designers, manufacturing, quality assurance, and NDT technicians, is a daily requirement.
- Decision-making: Making informed decisions quickly under pressure regarding process parameters, material selection, and repair strategies is critical for project success and safety.
- Adaptability: The field constantly evolves with new materials and technologies, requiring engineers to quickly learn and apply new knowledge.
- Risk assessment: Identifying potential hazards and risks associated with welding processes, materials, and designs, then developing mitigation strategies, is crucial for safety and quality.
How to Become a Welding Engineer
Becoming a Welding Engineer offers several distinct entry points, ranging from traditional academic routes to more experience-based paths. For recent graduates, a Bachelor's degree in Welding Engineering, Materials Science, or Mechanical Engineering with a specialization in welding is the most direct route. Career changers or those with a strong background in skilled trades might pursue a combination of certifications and advanced diplomas, often supplemented by on-the-job training.
The timeline for entry varies significantly. A full engineering degree typically takes four years, while a combination of certifications and practical experience might take three to five years to accumulate the necessary expertise. Geographic location plays a role, with more opportunities in manufacturing hubs, energy sectors, and shipbuilding regions. Larger corporations may prioritize candidates with advanced degrees and research experience, whereas smaller fabrication shops or specialized consultancies might value practical skills and a proven project portfolio.
A common misconception is that extensive hands-on welding experience is always a prerequisite for an engineering role. While beneficial for understanding processes, the core function of a Welding Engineer involves design, metallurgy, quality control, and process optimization, not necessarily daily torch time. Building a strong network within industry associations and seeking mentorship from experienced engineers can significantly accelerate career entry and provide insights into specific industry needs.
Earn a foundational engineering degree in Welding Engineering, Materials Science, or Mechanical Engineering. Focus on coursework in metallurgy, welding processes, design of welded structures, and non-destructive testing. This academic base provides the theoretical knowledge essential for complex problem-solving in welding applications.
Gain practical experience through internships or co-op programs within manufacturing, fabrication, or research facilities. Seek opportunities to work on projects involving different welding techniques, material types, and quality control procedures. These experiences bridge the gap between academic theory and real-world engineering challenges, making your resume more competitive.
Pursue relevant certifications from recognized bodies such as the American Welding Society (AWS) or the American Society of Mechanical Engineers (ASME). Consider certifications like Certified Welding Inspector (CWI) or Certified Welding Engineer (CWEng) as they validate your expertise and commitment to industry standards. These credentials demonstrate a higher level of specialized knowledge to potential employers.
Develop a professional portfolio showcasing your engineering projects, research papers, and problem-solving abilities related to welding. Include details on your design choices, process optimizations, and the impact of your work on quality or efficiency. This tangible evidence of your capabilities is crucial for demonstrating your value during job applications.
Actively network with professionals in the welding and manufacturing industries by attending conferences, trade shows, and local chapter meetings of professional organizations. Connect with experienced Welding Engineers, recruiters, and hiring managers to learn about industry trends and potential job openings. Informational interviews can provide valuable insights and lead to mentorship opportunities.
Prepare a targeted resume and cover letter that highlights your specific welding engineering skills, relevant projects, and certifications. Practice answering common engineering and technical interview questions, focusing on your problem-solving approach and ability to apply theoretical knowledge to practical scenarios. Tailor your application materials to each job description to demonstrate a clear fit for the role.
Step 1
Earn a foundational engineering degree in Welding Engineering, Materials Science, or Mechanical Engineering. Focus on coursework in metallurgy, welding processes, design of welded structures, and non-destructive testing. This academic base provides the theoretical knowledge essential for complex problem-solving in welding applications.
Step 2
Gain practical experience through internships or co-op programs within manufacturing, fabrication, or research facilities. Seek opportunities to work on projects involving different welding techniques, material types, and quality control procedures. These experiences bridge the gap between academic theory and real-world engineering challenges, making your resume more competitive.
Step 3
Pursue relevant certifications from recognized bodies such as the American Welding Society (AWS) or the American Society of Mechanical Engineers (ASME). Consider certifications like Certified Welding Inspector (CWI) or Certified Welding Engineer (CWEng) as they validate your expertise and commitment to industry standards. These credentials demonstrate a higher level of specialized knowledge to potential employers.
Step 4
Develop a professional portfolio showcasing your engineering projects, research papers, and problem-solving abilities related to welding. Include details on your design choices, process optimizations, and the impact of your work on quality or efficiency. This tangible evidence of your capabilities is crucial for demonstrating your value during job applications.
Step 5
Actively network with professionals in the welding and manufacturing industries by attending conferences, trade shows, and local chapter meetings of professional organizations. Connect with experienced Welding Engineers, recruiters, and hiring managers to learn about industry trends and potential job openings. Informational interviews can provide valuable insights and lead to mentorship opportunities.
Step 6
Prepare a targeted resume and cover letter that highlights your specific welding engineering skills, relevant projects, and certifications. Practice answering common engineering and technical interview questions, focusing on your problem-solving approach and ability to apply theoretical knowledge to practical scenarios. Tailor your application materials to each job description to demonstrate a clear fit for the role.
Education & Training Needed to Become a Welding Engineer
Becoming a Welding Engineer requires a robust educational foundation, often distinguishing itself from a welder by emphasizing theoretical knowledge, materials science, and design principles. Formal university degrees, typically Bachelor's or Master's in Welding Engineering, Materials Science, or Mechanical Engineering with a specialization, are the most recognized pathways. These 4-year undergraduate degrees can cost $40,000-$100,000+ for in-state tuition at public universities, and significantly more for private institutions, with Master's degrees adding another 1-2 years and $20,000-$60,000.
Alternative paths, such as advanced certifications combined with extensive practical experience, exist but generally do not replace a full engineering degree for senior or design-focused roles. Bootcamps or short online courses primarily cater to welding technicians or provide supplemental skills, not the foundational engineering principles. Employers in critical industries like aerospace, automotive, or energy strongly prefer candidates with accredited engineering degrees, as these programs ensure a deep understanding of metallurgy, stress analysis, and quality control, which are essential for safe and efficient welding processes.
Continuous learning is vital for Welding Engineers, as new materials, welding technologies, and industry standards emerge regularly. Professional development often involves specialized courses in specific welding processes, non-destructive testing, or quality management systems. Organizations like the American Welding Society (AWS) offer certifications that validate expertise in niche areas, enhancing a degree-holder's marketability. The cost-benefit analysis favors a degree for long-term career growth and higher earning potential, especially considering the complex problem-solving and design responsibilities inherent to the role, which self-study or short courses cannot adequately provide.
Welding Engineer Salary & Outlook
Compensation for a Welding Engineer varies significantly, shaped by a confluence of factors beyond just base salary. Geographic location dramatically influences earning potential; high-cost-of-living areas or regions with robust manufacturing and energy sectors, such as the Gulf Coast or the Midwest, often offer higher salaries due to localized demand and economic activity. Conversely, areas with less industrial concentration may present lower figures.
Years of experience, specialized certifications (e.g., Certified Welding Inspector - CWI, Professional Engineer - PE), and expertise in advanced welding processes (e.g., laser welding, additive manufacturing) command premium compensation. Total compensation packages frequently extend beyond base pay to include performance bonuses, profit-sharing, and comprehensive benefits. These benefits typically encompass health, dental, and vision insurance, 401(k) matching contributions, and allowances for professional development or continuing education, all adding substantial value.
Industry-specific trends also drive salary growth. Sectors like aerospace, defense, oil and gas, and automotive often offer more competitive salaries due to the critical nature and complexity of their welding requirements. Company size matters too; larger corporations with more extensive operations and greater revenue typically provide higher pay scales and more robust benefits. Remote work, while less common for hands-on engineering roles, can impact salary ranges by allowing companies to source talent from lower-cost regions, potentially influencing local market rates. Salary negotiation leverage increases with proven expertise in problem-solving, process optimization, and project leadership. While these figures primarily reflect the U.S. market, international variations exist, with some global hubs offering distinct compensation structures.
Salary by Experience Level
Level | US Median | US Average |
---|---|---|
Junior Welding Engineer | $70k USD | $75k USD |
Welding Engineer | $90k USD | $95k USD |
Senior Welding Engineer | $110k USD | $115k USD |
Lead Welding Engineer | $130k USD | $135k USD |
Principal Welding Engineer | $150k USD | $155k USD |
Welding Engineering Manager | $170k USD | $175k USD |
Market Commentary
The job market for Welding Engineers shows stable demand, driven by ongoing infrastructure projects, manufacturing advancements, and the critical need for material joining expertise across various industries. The Bureau of Labor Statistics projects growth in related engineering fields, and Welding Engineers are essential to many of these sectors. Specific demand drivers include the resurgence in domestic manufacturing, investments in renewable energy infrastructure, and continuous innovation in automotive and aerospace industries requiring advanced material joining techniques.
Emerging opportunities for Welding Engineers lie in additive manufacturing, robotics integration, and the development of new alloys. Companies increasingly seek engineers who can optimize automated welding processes, develop quality control protocols for complex assemblies, and implement digital twins for process simulation. The supply of highly qualified Welding Engineers, especially those with specialized certifications or expertise in advanced materials, remains somewhat constrained, creating a favorable market for skilled professionals.
Automation and AI are transforming the role rather than replacing it, shifting focus from manual tasks to system design, programming, and oversight of robotic welding cells. This makes the profession resilient to economic downturns, as welding is fundamental to nearly all manufacturing and construction. Geographic hotspots for employment include industrial centers in Texas, Michigan, Ohio, and Pennsylvania, with growing opportunities in states investing in advanced manufacturing and clean energy. Continuous learning in areas like data analytics, materials science, and automation will be crucial for long-term career viability and growth.
Welding Engineer Career Path
Career progression for a Welding Engineer typically involves a blend of technical specialization, project leadership, and increasingly complex problem-solving. Professionals can advance along an individual contributor (IC) track, deepening their technical expertise, or transition into a management/leadership track, overseeing teams and strategic initiatives. Both paths require continuous learning and adaptation to new materials, processes, and industry standards.
Advancement speed depends on several factors, including individual performance, the specific industry (e.g., aerospace, oil & gas, automotive), and company size. Larger corporations may offer more structured progression paths and diverse project opportunities, while smaller firms or startups might provide broader responsibilities earlier. Specialization in areas like robotic welding, additive manufacturing, or specific material groups (e.g., superalloys) significantly influences career trajectory and market demand.
Networking within professional organizations like the American Welding Society (AWS), pursuing advanced certifications (e.g., AWS Certified Welding Engineer), and engaging in mentorship are crucial for career growth. Lateral moves into related fields such as materials engineering, quality assurance, or manufacturing engineering are also common. These transitions leverage core welding knowledge in new contexts, expanding professional versatility.
Junior Welding Engineer
0-2 yearsAssist senior engineers with project tasks, including data collection, basic analysis, and documentation. Perform routine inspections and tests under direct supervision. Learn to interpret welding procedures (WPS) and specifications (WPS). Contribute to problem-solving for straightforward welding issues.
Key Focus Areas
Develop foundational knowledge in welding processes, metallurgy, and material science. Focus on understanding design specifications and quality control procedures. Build proficiency in using welding software and interpreting engineering drawings. Seek mentorship to accelerate learning and practical application.
Welding Engineer
2-5 yearsManage specific welding projects or components from conception to completion. Develop and qualify welding procedures (WPS) and specifications (PQR). Conduct failure analysis and implement corrective actions for welding defects. Provide technical support to manufacturing and production teams.
Key Focus Areas
Master advanced welding techniques and process optimization. Develop strong problem-solving skills for complex metallurgical and fabrication challenges. Cultivate effective communication for technical reports and stakeholder interactions. Begin exploring specialization areas like automation or specific alloy groups.
Senior Welding Engineer
5-8 yearsAct as a technical lead for critical welding projects, ensuring compliance with industry codes and standards. Design and optimize welding processes for new product development or challenging applications. Conduct advanced metallurgical investigations and provide solutions for complex material joining issues. Collaborate with R&D teams on innovative welding technologies.
Key Focus Areas
Lead complex technical initiatives and provide expert guidance on welding challenges. Develop strategic thinking for long-term process improvements and material selection. Mentor junior engineers and contribute to their professional development. Pursue advanced certifications or industry-specific training.
Lead Welding Engineer
8-12 yearsOversee multiple welding engineering projects or programs. Provide technical leadership and strategic direction for significant engineering challenges. Set technical standards and guidelines for welding operations. Act as a primary technical liaison with clients, suppliers, and regulatory bodies. May manage a small team of engineers or technicians.
Key Focus Areas
Drive innovation in welding engineering and establish best practices across multiple projects or departments. Develop strong leadership skills, including delegation, conflict resolution, and motivational techniques. Focus on cross-functional collaboration and strategic planning. Contribute to industry standards and publications.
Principal Welding Engineer
12-15+ yearsServe as a top-tier technical authority and subject matter expert in welding engineering. Drive major technological advancements and strategic initiatives. Provide high-level consultation and problem-solving for the most complex and critical welding issues. Influence company-wide technical direction and investment in welding R&D. Often responsible for intellectual property generation.
Key Focus Areas
Shape the long-term technical vision for welding engineering within the organization. Develop expertise in emerging technologies and their strategic application. Focus on organizational impact, intellectual property, and competitive advantage. Engage in thought leadership through presentations and industry committees.
Welding Engineering Manager
10-15+ years total experience, with 2+ years in a senior or lead roleLead and manage a team of welding engineers and technicians. Responsible for departmental strategy, resource allocation, and project portfolio management. Oversee the development and implementation of welding engineering standards and best practices. Drive continuous improvement initiatives and foster a culture of technical excellence. Reports to higher-level engineering or operations management.
Key Focus Areas
Cultivate strong leadership, management, and business acumen. Develop skills in team building, performance management, and resource allocation. Focus on strategic planning, budgeting, and aligning engineering efforts with business objectives. Build relationships with executive leadership and external partners.
Junior Welding Engineer
0-2 yearsAssist senior engineers with project tasks, including data collection, basic analysis, and documentation. Perform routine inspections and tests under direct supervision. Learn to interpret welding procedures (WPS) and specifications (WPS). Contribute to problem-solving for straightforward welding issues.
Key Focus Areas
Develop foundational knowledge in welding processes, metallurgy, and material science. Focus on understanding design specifications and quality control procedures. Build proficiency in using welding software and interpreting engineering drawings. Seek mentorship to accelerate learning and practical application.
Welding Engineer
2-5 yearsManage specific welding projects or components from conception to completion. Develop and qualify welding procedures (WPS) and specifications (PQR). Conduct failure analysis and implement corrective actions for welding defects. Provide technical support to manufacturing and production teams.
Key Focus Areas
Master advanced welding techniques and process optimization. Develop strong problem-solving skills for complex metallurgical and fabrication challenges. Cultivate effective communication for technical reports and stakeholder interactions. Begin exploring specialization areas like automation or specific alloy groups.
Senior Welding Engineer
5-8 yearsAct as a technical lead for critical welding projects, ensuring compliance with industry codes and standards. Design and optimize welding processes for new product development or challenging applications. Conduct advanced metallurgical investigations and provide solutions for complex material joining issues. Collaborate with R&D teams on innovative welding technologies.
Key Focus Areas
Lead complex technical initiatives and provide expert guidance on welding challenges. Develop strategic thinking for long-term process improvements and material selection. Mentor junior engineers and contribute to their professional development. Pursue advanced certifications or industry-specific training.
Lead Welding Engineer
8-12 yearsOversee multiple welding engineering projects or programs. Provide technical leadership and strategic direction for significant engineering challenges. Set technical standards and guidelines for welding operations. Act as a primary technical liaison with clients, suppliers, and regulatory bodies. May manage a small team of engineers or technicians.
Key Focus Areas
Drive innovation in welding engineering and establish best practices across multiple projects or departments. Develop strong leadership skills, including delegation, conflict resolution, and motivational techniques. Focus on cross-functional collaboration and strategic planning. Contribute to industry standards and publications.
Principal Welding Engineer
12-15+ yearsServe as a top-tier technical authority and subject matter expert in welding engineering. Drive major technological advancements and strategic initiatives. Provide high-level consultation and problem-solving for the most complex and critical welding issues. Influence company-wide technical direction and investment in welding R&D. Often responsible for intellectual property generation.
Key Focus Areas
Shape the long-term technical vision for welding engineering within the organization. Develop expertise in emerging technologies and their strategic application. Focus on organizational impact, intellectual property, and competitive advantage. Engage in thought leadership through presentations and industry committees.
Welding Engineering Manager
10-15+ years total experience, with 2+ years in a senior or lead roleLead and manage a team of welding engineers and technicians. Responsible for departmental strategy, resource allocation, and project portfolio management. Oversee the development and implementation of welding engineering standards and best practices. Drive continuous improvement initiatives and foster a culture of technical excellence. Reports to higher-level engineering or operations management.
Key Focus Areas
Cultivate strong leadership, management, and business acumen. Develop skills in team building, performance management, and resource allocation. Focus on strategic planning, budgeting, and aligning engineering efforts with business objectives. Build relationships with executive leadership and external partners.
Job Application Toolkit
Ace your application with our purpose-built resources:
Welding Engineer Cover Letter Examples
Personalizable templates that showcase your impact.
View examplesWelding Engineer Job Description Template
Ready-to-use JD for recruiters and hiring teams.
View examplesGlobal Welding Engineer Opportunities
Welding engineers design and optimize welding processes across various industries globally. Their expertise is vital in manufacturing, construction, and energy sectors worldwide.
Global demand remains strong, particularly in countries investing in infrastructure and advanced manufacturing. Cultural and regulatory differences affect material standards and safety protocols. International certifications like IIW (International Institute of Welding) qualifications enhance global mobility for these specialists.
Global Salaries
Welding engineer salaries vary significantly by region and experience. In North America, particularly the US, a mid-career welding engineer earns between $80,000 and $120,000 USD annually. Canadian salaries are slightly lower, typically ranging from $70,000 to $100,000 CAD (approx. $52,000-$74,000 USD).
European salaries differ across countries. In Germany, a welding engineer can expect €60,000 to €90,000 (approx. $65,000-$98,000 USD), reflecting a high cost of living. UK salaries range from £40,000 to £70,000 (approx. $50,000-$88,000 USD). Scandinavian countries offer similar or slightly higher compensation, but also have higher living costs. In Asia-Pacific, salaries in Australia and New Zealand are around AUD $80,000-$110,000 (approx. $53,000-$73,000 USD). Middle Eastern countries, especially in the oil and gas sector, offer competitive, tax-free salaries, often exceeding $100,000 USD for experienced professionals, with housing and transport benefits.
Latin American countries like Brazil or Mexico offer lower nominal salaries, typically $30,000-$60,000 USD, but purchasing power can be comparable due to lower living costs. Tax implications and social security contributions significantly impact take-home pay, varying by country. For example, some European nations have higher tax rates than the US or Middle East. Benefits like health insurance, pension contributions, and vacation days also differ, affecting the overall compensation package. International experience and advanced degrees often command higher compensation, as these skills are highly valued across borders.
Remote Work
Direct hands-on welding engineering roles have limited remote work potential due to the need for on-site presence for process oversight and quality control. However, aspects like design, simulation, materials analysis, and project management can be done remotely. This blend allows for hybrid models.
Legal and tax implications for international remote work require understanding local employment laws and tax treaties. Time zone differences can pose collaboration challenges for global teams. Digital nomad visas are less common for this field, as physical presence is often a core requirement.
Some engineering consultancies or R&D departments may offer more flexible remote options. Companies hiring internationally for welding engineering roles often focus on specific project phases that can be managed off-site. Salary expectations for remote roles might see adjustments based on the engineer's location and the employer's base. Equipment needs include powerful workstations and specialized software for simulations and design.
Visa & Immigration
Welding engineers often qualify for skilled worker visas in many countries. Popular destinations include Canada (Express Entry), Australia (Skilled Migration), Germany (EU Blue Card), and the UK (Skilled Worker Visa). These visas typically require a relevant engineering degree, professional experience, and a job offer from an employer.
Credential recognition is crucial; engineering qualifications often need assessment by professional bodies in the destination country. English language proficiency tests like IELTS or TOEFL are usually required for English-speaking countries. German requires B1/B2 German language proficiency for many roles. Visa processing times vary, from a few months to over a year, depending on the country and visa type.
Pathways to permanent residency exist in countries like Canada and Australia through points-based systems. Some countries offer fast-track processing for highly sought-after engineering professions. Family visas or dependent rights allow spouses and children to accompany the primary visa holder. Intracompany transfers are also common for large multinational engineering firms, facilitating internal mobility.
2025 Market Reality for Welding Engineers
Understanding current market conditions is paramount for Welding Engineers. The field has evolved significantly from 2023 to 2025, driven by post-pandemic supply chain recalibrations and the rapid integration of AI and automation. Broader economic factors, such as industrial output and infrastructure spending, directly influence job availability and project scope.
Market realities for Welding Engineers vary considerably by experience level—entry-level positions often face more competition than senior, specialized roles. Geographic region plays a major role, with strong demand in industrial hubs versus slower growth in others. Company size also matters, as large corporations may offer more specialized roles than smaller fabrication shops. This analysis provides an honest assessment of these realities.
Current Challenges
Welding Engineers face increased competition, especially for entry-level roles, as some companies seek to automate or outsource routine tasks. Economic uncertainty in manufacturing and energy sectors can slow hiring. A mismatch often exists between traditional welding engineering skills and the growing demand for expertise in robotics, additive manufacturing, and data analytics.
Job search timelines can extend, reflecting a more cautious hiring environment in some segments.
Growth Opportunities
Despite challenges, strong opportunities exist for Welding Engineers specializing in emerging technologies. Roles focused on additive manufacturing (3D printing of metals) are experiencing significant growth, requiring expertise in metallurgy, process control, and quality assurance for complex geometries. Similarly, demand for engineers skilled in robotic welding programming and automation integration is high across diverse industries.
Professionals can gain a competitive advantage by acquiring certifications in advanced NDT methods, materials science for exotic alloys, or data analytics for process optimization. Underserved markets include small to medium-sized enterprises (SMEs) looking to modernize their welding operations, and specific geographic regions investing heavily in renewable energy infrastructure or defense projects. Market corrections can create opportunities for those adaptable enough to pivot to high-growth sectors or consultancies.
Sectors like aerospace, nuclear power, and medical device manufacturing remain robust, consistently seeking Welding Engineers with rigorous quality control and regulatory compliance expertise. Investing in continuous learning, particularly in AI-driven process control and automation, positions engineers strategically for future roles.
Current Market Trends
Hiring for Welding Engineers in 2025 shows a nuanced picture. Demand remains robust in specialized sectors like aerospace, defense, and renewable energy infrastructure, where advanced materials and critical joints require precise engineering oversight. Conversely, traditional manufacturing sectors show slower growth, with some firms consolidating roles or investing in automation to reduce reliance on manual processes.
The integration of artificial intelligence and machine learning profoundly affects the profession. Employers now seek Welding Engineers who can implement AI for predictive maintenance, defect detection, and optimizing welding parameters. This shift means less demand for purely theoretical knowledge and more for practical application of digital tools.
Economic conditions, particularly fluctuating raw material costs and interest rates, influence investment in large-scale fabrication projects, directly impacting job availability. Some regions, like the Gulf Coast for energy and the Pacific Northwest for aerospace, maintain stronger markets. Salary trends show a premium for those with expertise in automation, advanced materials (e.g., composites, exotic alloys), and non-destructive testing (NDT) methodologies. Market saturation is less of an issue at senior levels, but entry-level roles face more competition from new graduates with interdisciplinary skills. Remote work is less common for this hands-on role, but some design and analysis functions can be performed off-site.
Emerging Specializations
The welding engineering field is experiencing significant transformation, driven by advancements in materials science, automation, and data analytics. These technological shifts create new specialization opportunities that did not exist a decade ago. Professionals who strategically position themselves in these emerging areas can unlock substantial career advancement and often command premium compensation.
Early adoption and specialization in these cutting-edge niches offer a distinct advantage, allowing individuals to become pioneers and subject matter experts as these fields mature. While established specializations remain vital, focusing on emerging areas prepares welding engineers for the next generation of industrial demands, ensuring long-term relevance and growth beyond 2025.
Many emerging areas, particularly those involving advanced manufacturing or digital integration, are poised to become mainstream within the next five to ten years, creating a significant volume of job opportunities. Pursuing these specializations involves balancing the inherent risk of entering a less defined field with the substantial reward of being at the forefront of industry innovation. Understanding these trends is crucial for strategic career planning.
Robotic Welding Systems Engineer
This specialization focuses on the design, implementation, and optimization of robotic and automated welding systems. It involves integrating advanced sensors, machine vision, and control algorithms to enhance precision, speed, and consistency in welding operations. As industries increasingly adopt automation for efficiency and safety, demand for engineers who can manage complex robotic cells is escalating.
Advanced Materials Joining Specialist
This area involves developing and applying advanced welding processes for next-generation materials, such as composites, dissimilar metals, and superalloys. It requires deep knowledge of material properties, phase transformations, and innovative joining techniques like friction stir welding, laser welding, or electron beam welding. Industries like aerospace, automotive, and renewable energy are driving this demand.
Welding Process Data Scientist
This specialization focuses on using data analytics, machine learning, and artificial intelligence to monitor, predict, and optimize welding processes. It involves collecting data from welding equipment, analyzing patterns for defect prediction, optimizing parameters, and developing predictive maintenance models. This enhances quality control and reduces waste in manufacturing.
Additive Manufacturing Welding Engineer
This emerging field centers on the development and application of additive manufacturing techniques, specifically for metal components. It involves understanding the complex interplay of heat, material deposition, and solidification in processes like Wire Arc Additive Manufacturing (WAAM) or Laser Powder Bed Fusion. Welding engineers contribute by optimizing build parameters, managing distortion, and ensuring structural integrity.
XR Welding Simulation Engineer
This area concentrates on integrating virtual and augmented reality technologies into welding training, simulation, and remote assistance. It involves creating immersive environments for skill development, simulating complex welding scenarios, and enabling remote expert guidance for on-site technicians. This improves training efficiency and problem-solving in challenging environments.
Pros & Cons of Being a Welding Engineer
Making informed career decisions requires a realistic understanding of both the benefits and challenges associated with a profession. While some roles offer clear advantages, they also come with inherent difficulties that job seekers should consider. It is important to recognize that individual experiences can vary significantly based on company culture, specific industry sector, and personal preferences. Furthermore, the pros and cons of a career path may evolve at different stages, from early-career entry to senior-level leadership. What one person perceives as a benefit, another might see as a drawback, depending on their values and lifestyle priorities. This assessment aims to provide a balanced overview of the Welding Engineer role, helping aspiring professionals set appropriate expectations.
Pros
- Welding engineers command strong demand across diverse industries such as aerospace, automotive, construction, and energy, leading to excellent job security.
- The role offers significant intellectual stimulation, involving complex problem-solving related to material science, metallurgy, and advanced fabrication techniques.
- Opportunities for specialization are abundant, allowing engineers to focus on areas like robotic welding, additive manufacturing, or specific material groups, enhancing career versatility.
- Welding engineers play a critical role in ensuring product quality and safety, contributing directly to the structural integrity of vital infrastructure and products.
- The profession provides opportunities for hands-on involvement, allowing engineers to apply theoretical knowledge directly in practical, tangible ways.
- Earning potential for experienced welding engineers is competitive, especially for those with advanced degrees or certifications in specialized fields.
- The work often involves collaboration with diverse teams, including designers, fabricators, and quality assurance personnel, fostering a dynamic and interactive work environment.
Cons
- Welding engineers often face high-pressure environments, especially when overseeing critical projects where welding integrity is paramount for safety and structural stability.
- The role demands continuous learning and adaptation to new welding technologies, materials, and codes, requiring ongoing professional development and training.
- Travel to various project sites, fabrication shops, or client locations is frequently necessary, which can impact work-life balance and personal time.
- Exposure to hazardous conditions, including fumes, intense light, heat, and loud noises, is common in many work settings despite safety protocols.
- Balancing theoretical knowledge with practical application can be challenging, as real-world welding issues often present complex, unforeseen variables.
- The job requires meticulous attention to detail and adherence to strict quality control standards, making errors costly and potentially dangerous.
- Career progression might feel slow in some traditional industries, with advancement often tied to years of experience and specialized certifications rather than rapid promotion opportunities.
Frequently Asked Questions
Welding Engineers combine advanced materials science with practical application, facing distinct challenges in ensuring structural integrity and optimizing manufacturing processes. This section addresses key questions about entering this specialized field, from educational pathways to career progression and the impact of new technologies.
What educational background is essential to become a Welding Engineer?
Becoming a Welding Engineer typically requires a Bachelor's degree in Welding Engineering, Materials Science, or a related engineering discipline. Some roles may also consider candidates with a relevant engineering degree and extensive experience in welding, coupled with professional certifications like Certified Welding Engineer (CWEng) from the American Welding Society. Practical experience through internships or co-op programs is highly beneficial.
How long does it take to become a fully qualified Welding Engineer, including licensure?
The timeline to become job-ready as a Welding Engineer usually involves completing a four-year Bachelor's degree. After graduation, entry-level positions are common, and gaining professional licensure as a Professional Engineer (PE) may take an additional four years of supervised experience and passing an exam. This means a total of 8-10 years to reach a fully licensed professional status from the start of your undergraduate studies.
What are the typical salary expectations for a Welding Engineer at different career stages?
Starting salaries for Welding Engineers range from $60,000 to $80,000 annually, depending on location, industry, and specific company. With 5-10 years of experience, salaries can climb to $90,000-$120,000, and senior or specialized roles can exceed $150,000. These figures can vary significantly based on industries like aerospace, oil and gas, or manufacturing, which often offer higher compensation.
What is the typical work-life balance like for a Welding Engineer?
The work-life balance for a Welding Engineer can vary. Many roles are project-based, which may involve periods of intense work, especially during deadlines or on-site inspections. While most work is during standard business hours, some positions in manufacturing or construction may require travel or occasional evening/weekend work to oversee critical operations or troubleshoot issues. It is generally a stable profession with predictable hours once established.
Is the job market for Welding Engineers growing, and what is the long-term job security?
The job market for Welding Engineers remains stable and robust, driven by ongoing needs in manufacturing, construction, energy, and aerospace. As infrastructure ages and new technologies emerge, the demand for skilled professionals who can design, implement, and inspect welding processes remains high. Automation in welding also creates new opportunities for engineers who can manage and optimize these advanced systems.
What are the common career advancement opportunities for a Welding Engineer?
Welding Engineers have several career growth paths. They can advance into management roles, leading teams or departments in manufacturing or R&D. Specialization in areas like additive manufacturing, robotic welding, or specific materials (e.g., aerospace alloys) can also open doors to highly specialized and well-compensated positions. Consulting and expert witness work are also viable long-term options for experienced professionals.
What are the biggest challenges or unique aspects of being a Welding Engineer?
A key challenge is staying current with rapidly evolving welding technologies, materials science, and industry standards. Ensuring safety and quality control in complex welding projects also presents ongoing technical and managerial challenges. Welding Engineers often balance theoretical knowledge with practical application, requiring strong problem-solving skills to address real-world fabrication issues and material behaviors.
Can Welding Engineers work remotely, or is it primarily an on-site role?
While some administrative or design tasks can be performed remotely, the core responsibilities of a Welding Engineer often require on-site presence. This includes overseeing welding procedures, conducting inspections, troubleshooting equipment, and collaborating directly with production teams. Therefore, fully remote positions are rare, but hybrid models offering some flexibility are increasingly common, especially for senior roles that involve more project management and less direct hands-on work.
Related Careers
Explore similar roles that might align with your interests and skills:
Fabrication Engineer
A growing field with similar skill requirements and career progression opportunities.
Explore career guideWelder
A growing field with similar skill requirements and career progression opportunities.
Explore career guideWelder Fabricator
A growing field with similar skill requirements and career progression opportunities.
Explore career guideWelding Inspector
A growing field with similar skill requirements and career progression opportunities.
Explore career guideWelding Supervisor
A growing field with similar skill requirements and career progression opportunities.
Explore career guideAssess your Welding Engineer readiness
Understanding where you stand today is the first step toward your career goals. Our Career Coach helps identify skill gaps and create personalized plans.
Skills Gap Analysis
Get a detailed assessment of your current skills versus Welding Engineer requirements. Our AI Career Coach identifies specific areas for improvement with personalized recommendations.
See your skills gapCareer Readiness Assessment
Evaluate your overall readiness for Welding Engineer roles with our AI Career Coach. Receive personalized recommendations for education, projects, and experience to boost your competitiveness.
Assess your readinessSimple pricing, powerful features
Upgrade to Himalayas Plus and turbocharge your job search.
Himalayas
Himalayas Plus
Himalayas Max
Find your dream job
Sign up now and join over 100,000 remote workers who receive personalized job alerts, curated job matches, and more for free!
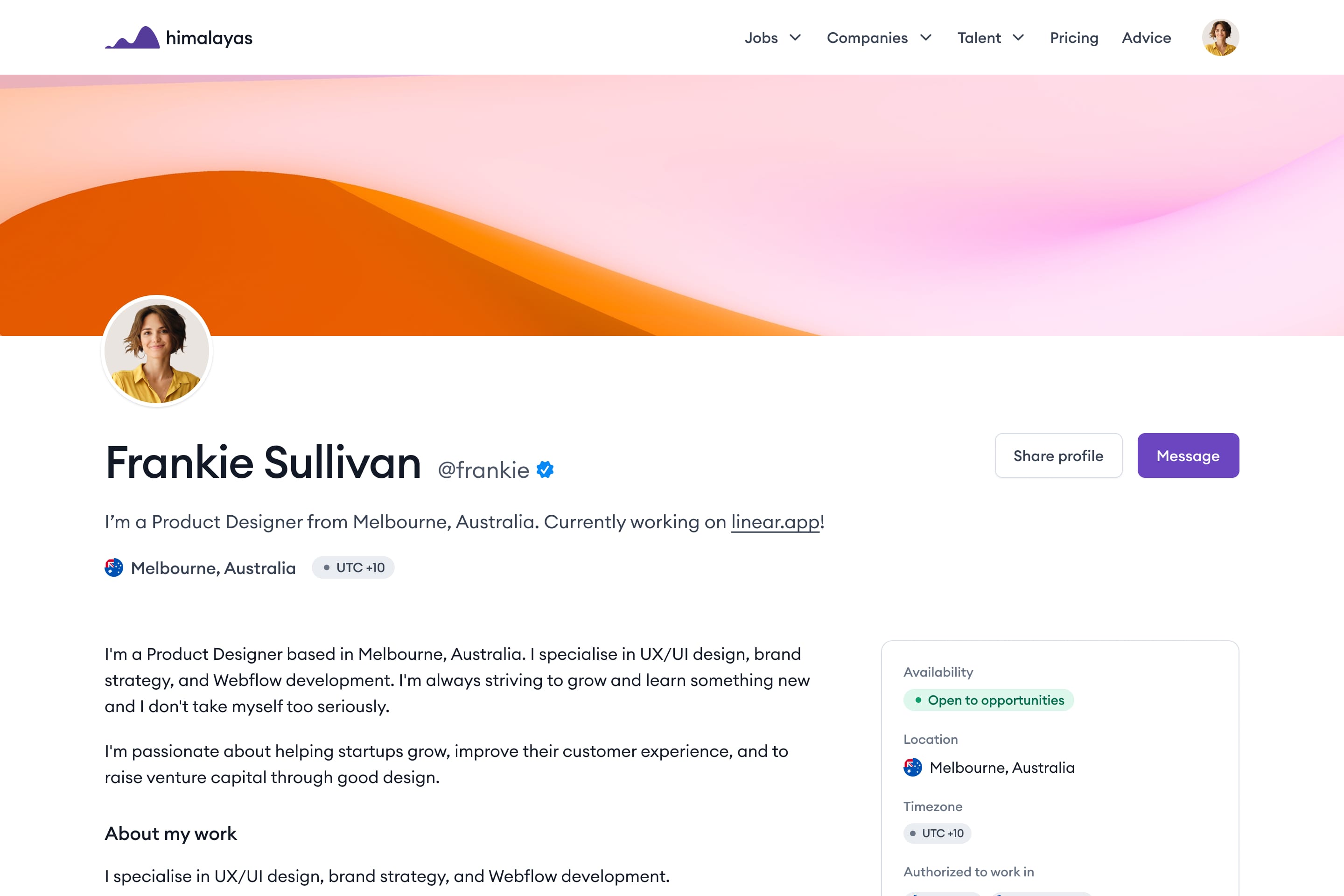