Complete Fabrication Engineer Career Guide
Fabrication engineers are the architects of physical products, transforming conceptual designs into tangible realities across diverse industries. They specialize in optimizing manufacturing processes, ensuring products are built efficiently, precisely, and cost-effectively. This role combines engineering principles with hands-on production knowledge, making it critical for companies pushing the boundaries of innovation and manufacturing excellence.
Key Facts & Statistics
Median Salary
$99,040 USD
(U.S. national median, BLS, May 2023)
Range: $60k - $150k+ USD
Growth Outlook
6%
as fast as average (BLS, 2022-2032)
Annual Openings
≈15,000
openings annually (BLS, 2022-2032)
Top Industries
Typical Education
Bachelor's degree in Mechanical Engineering, Manufacturing Engineering, or Industrial Engineering
What is a Fabrication Engineer?
A Fabrication Engineer specializes in the processes and techniques used to manufacture physical products, from raw materials to finished components. This role focuses on translating product designs into efficient, repeatable, and high-quality manufacturing operations. They bridge the gap between product design and actual production, ensuring that parts can be made effectively and economically.
Unlike a Design Engineer who focuses on product functionality, or a Manufacturing Engineer who might have a broader scope across an entire production line, a Fabrication Engineer specifically optimizes the 'making' of individual parts. They solve challenges related to material forming, cutting, joining, and finishing, ensuring that components meet precise specifications and are produced at scale. Their expertise is crucial for industries ranging from aerospace and automotive to consumer electronics and medical devices.
What does a Fabrication Engineer do?
Key Responsibilities
- Develop detailed fabrication processes and procedures for manufacturing components, ensuring efficiency and quality standards.
- Design and optimize manufacturing layouts, workflows, and tooling to improve production rates and reduce waste.
- Conduct root cause analysis for fabrication defects and implement corrective actions to prevent recurrence.
- Collaborate with design engineers to review product designs for manufacturability and provide feedback on material selection and assembly methods.
- Oversee the implementation of new fabrication equipment and technologies, including calibration and performance testing.
- Perform cost analyses and material assessments to identify opportunities for cost reduction in fabrication processes.
- Train production staff on new fabrication techniques, safety protocols, and quality control procedures to maintain operational excellence.
Work Environment
Fabrication engineers primarily work in manufacturing plants, production facilities, or research and development centers. Their environment often involves a mix of office work for design and analysis, and hands-on time on the factory floor. They collaborate closely with production teams, quality control specialists, and design engineers. The work pace can be dynamic, especially during new product introductions or when troubleshooting production issues. While most work is on-site, some roles might involve travel to supplier sites or other company facilities. The environment can be noisy and may require personal protective equipment.
Tools & Technologies
Fabrication engineers routinely use Computer-Aided Design (CAD) software such as SolidWorks, AutoCAD, or CATIA for designing and simulating parts. They employ Computer-Aided Manufacturing (CAM) software to generate machine code for CNC machines, laser cutters, and 3D printers. Process simulation tools like Ansys or Abaqus assist in optimizing manufacturing sequences. They also work with various metrology equipment, including Coordinate Measuring Machines (CMMs) and laser scanners, for quality control. Familiarity with Enterprise Resource Planning (ERP) or Manufacturing Execution Systems (MES) is important for production planning and data management.
Fabrication Engineer Skills & Qualifications
A Fabrication Engineer designs, optimizes, and oversees manufacturing processes for creating components and products. This role requires a blend of mechanical engineering principles, materials science, and practical manufacturing knowledge. The qualification landscape prioritizes a strong foundation in engineering theory combined with hands-on experience in various fabrication techniques.
Requirements for Fabrication Engineers vary significantly by industry sector. The aerospace industry demands meticulous attention to detail and adherence to strict regulatory standards, often requiring specialized certifications in areas like welding or composite manufacturing. In contrast, the automotive sector might emphasize high-volume production efficiency and automation. Company size also plays a role; larger corporations may have specialized teams for different fabrication aspects, while smaller firms often expect engineers to possess a broader skill set across design, process, and quality control.
Formal education, typically a Bachelor's degree, forms the bedrock for this profession. However, practical experience gained through internships, co-op programs, or technician roles is equally critical, especially for entry-level positions. While certifications in specific processes like welding (e.g., AWS Certified Welding Engineer) or lean manufacturing add significant value, they usually complement a degree rather than replace it. The field is evolving with the increasing adoption of advanced manufacturing technologies such as additive manufacturing (3D printing) and robotics, making continuous learning and adaptation essential for long-term career success.
Education Requirements
Technical Skills
- CAD/CAM Software Proficiency (e.g., SolidWorks, AutoCAD, CATIA, Mastercam) for design, simulation, and toolpath generation.
- Materials Science and Selection (metals, polymers, composites) with understanding of their properties, processing, and application in fabrication.
- Welding Processes and Metallurgy (MIG, TIG, Arc, Laser welding) including joint design, filler materials, and defect analysis.
- Machining Processes (CNC milling, turning, grinding, EDM) with knowledge of tooling, speeds, feeds, and G-code programming.
- Sheet Metal Fabrication (bending, cutting, forming, stamping) and associated equipment operation.
- Additive Manufacturing (3D printing technologies like FDM, SLA, SLS, DMLS) for prototyping and production.
- Lean Manufacturing and Six Sigma Principles for process optimization, waste reduction, and quality improvement.
- Metrology and Inspection Techniques (CMM, optical comparators, gauges) for dimensional verification and quality control.
- Fixture and Tooling Design for efficient and repeatable manufacturing operations.
- Robotics and Automation for integrating automated systems into fabrication lines.
- Finite Element Analysis (FEA) for simulating material behavior and structural integrity under stress.
- Process Planning and Documentation for creating detailed manufacturing instructions and standard operating procedures.
Soft Skills
- Problem-solving and Root Cause Analysis: Fabrication Engineers must diagnose and resolve complex manufacturing issues, from material defects to process inefficiencies, requiring systematic analysis to identify underlying causes.
- Attention to Detail and Precision: Ensuring components meet exact specifications and quality standards is paramount in fabrication, where small errors can lead to significant failures or rework.
- Communication and Documentation: Clearly conveying design specifications, process instructions, and quality reports to technicians, suppliers, and management is crucial for successful production.
- Collaboration and Teamwork: Working effectively with design engineers, production teams, quality control, and suppliers to optimize manufacturing processes and troubleshoot issues.
- Adaptability and Continuous Improvement: The manufacturing landscape constantly changes with new materials and technologies, requiring Fabrication Engineers to quickly learn and integrate new methods and drive ongoing process enhancements.
- Project Management and Organization: Overseeing fabrication projects from concept to completion, managing timelines, resources, and budgets to ensure efficient and timely delivery.
- Safety Consciousness: Prioritizing and implementing safety protocols in manufacturing environments to protect personnel and prevent accidents.
- Critical Thinking and Decision-Making: Evaluating various fabrication methods, material choices, and process parameters to make informed decisions that balance cost, quality, and production efficiency.
How to Become a Fabrication Engineer
Entering the Fabrication Engineer field involves various pathways, from traditional engineering degrees to more hands-on vocational training combined with practical experience. Aspiring engineers should understand that while a formal degree in mechanical, manufacturing, or materials engineering provides a strong theoretical foundation, real-world fabrication skills and project experience are equally critical for success. The timeline for entry can range from 1-2 years for those with a related technical background who focus on skill acquisition, to 4-5 years for individuals pursuing a full bachelor's degree.
Entry strategies often vary by company size and industry. Larger corporations might prioritize candidates with accredited engineering degrees and internship experience, especially in highly regulated sectors like aerospace or medical devices. Smaller manufacturing firms or startups might be more open to candidates with strong portfolios of hands-on projects, certifications in specific fabrication processes (e.g., welding, CNC machining), and demonstrated problem-solving abilities, even without a four-year degree. Geographic location also plays a role; industrial hubs often offer more entry-level opportunities and apprenticeships.
A common misconception is that a Fabrication Engineer solely operates machinery; instead, the role centers on designing, optimizing, and overseeing manufacturing processes, often requiring a blend of theoretical knowledge and practical application. Building a strong network within the manufacturing community through industry events, professional organizations, and online forums significantly enhances job prospects. Hiring managers look for a clear understanding of materials science, process efficiency, quality control, and safety protocols. Overcoming barriers often involves supplementing academic knowledge with hands-on projects and internships to bridge the gap between theory and practical application.
Step 1
Step 2
Step 3
Step 4
Step 5
Step 6
Step 7
Education & Training Needed to Become a Fabrication Engineer
Becoming a Fabrication Engineer requires a blend of theoretical knowledge and practical skills. Formal university degrees, typically a Bachelor's in Mechanical Engineering, Manufacturing Engineering, or Materials Science, provide a strong theoretical foundation. These 4-year programs usually cost between $40,000 and $120,000 or more, offering in-depth understanding of material properties, manufacturing processes, and design principles, which employers highly value. While a bachelor's degree is often preferred, some entry-level roles may accept candidates with an Associate's degree in a relevant technical field or extensive vocational training.
Alternative pathways, such as vocational schools, technical colleges, or specialized certifications, focus more on hands-on skills like welding, CNC machining, and additive manufacturing. These programs range from 6 months to 2 years, costing $5,000 to $25,000. While they offer quicker entry into the field, they often require supplemental on-the-job training or further certifications to advance to a full Fabrication Engineer role. Self-study through online courses and industry manuals can complement formal education but rarely suffices as a standalone credential for this engineering position.
Employers generally prefer candidates with a Bachelor's degree due to the complex problem-solving and analytical skills required in this role. Continuous learning is crucial, as manufacturing technologies evolve rapidly. Professional development often involves certifications in specific software (e.g., CAD/CAM), advanced manufacturing techniques (e.g., laser fabrication), or quality control standards (e.g., Six Sigma). Practical experience, gained through internships or apprenticeships, significantly enhances a candidate's marketability, often outweighing a purely academic background in the eyes of hiring managers.
Fabrication Engineer Salary & Outlook
Compensation for a Fabrication Engineer varies significantly based on multiple factors. Geographic location plays a crucial role; areas with a high concentration of manufacturing, aerospace, or automotive industries often offer higher salaries due to increased demand and cost of living. Conversely, regions with lower living expenses may present more modest compensation.
Years of experience, specialized skills in areas like additive manufacturing, advanced materials, or automation, and the complexity of projects handled directly impact earning potential. Total compensation packages frequently extend beyond base salary to include performance bonuses, stock options in larger corporations, and comprehensive benefits such as health insurance, retirement contributions, and professional development allowances. Industry-specific trends, such as the growth in electric vehicle production or renewable energy, can also drive salary increases for engineers with relevant expertise.
Negotiation leverage comes from a strong portfolio of successful projects, unique technical skills, and a demonstrated ability to optimize production processes. Remote work opportunities for Fabrication Engineers are less common given the hands-on nature of the role, but some design or analysis aspects may offer flexibility. International markets present different salary structures, with figures often benchmarked against local economic conditions rather than direct USD equivalents, making the U.S. market a key reference point for global compensation trends.
Salary by Experience Level
Level | US Median | US Average |
---|---|---|
Junior Fabrication Engineer | $68k USD | $72k USD |
Fabrication Engineer | $85k USD | $89k USD |
Senior Fabrication Engineer | $110k USD | $115k USD |
Lead Fabrication Engineer | $132k USD | $138k USD |
Fabrication Engineering Manager | $158k USD | $165k USD |
Market Commentary
The job market for Fabrication Engineers shows steady growth, driven by ongoing advancements in manufacturing technologies and the need for optimized production processes. Projections indicate a 5-7% growth over the next decade, aligning with the broader engineering sector, as industries continually seek to improve efficiency and reduce costs. Emerging opportunities are particularly strong in additive manufacturing, robotics, and advanced materials engineering, requiring engineers to adapt to new tools and methodologies.
Demand for Fabrication Engineers remains robust in sectors like aerospace, automotive, medical devices, and consumer electronics. These industries rely heavily on precise and efficient fabrication to bring products to market. Supply and demand dynamics are relatively balanced, though a shortage of engineers with highly specialized skills in areas like DfAM (Design for Additive Manufacturing) or complex automation integration persists. This creates premium opportunities for those with cutting-edge expertise.
Future-proofing this career involves continuous learning in digital fabrication techniques, data analytics for process optimization, and AI-driven manufacturing. While automation enhances productivity, it also elevates the role of the Fabrication Engineer from manual tasks to overseeing complex systems and innovating new production methods. The profession is generally resilient, as the need for physical product creation remains constant, even during economic shifts. Geographic hotspots for these roles include manufacturing hubs in the Midwest, Southeast, and West Coast of the U.S., with increasing opportunities in rapidly industrializing international markets.
Fabrication Engineer Career Path
Career progression for a Fabrication Engineer involves a blend of technical mastery, project leadership, and eventually, people management. Professionals typically begin by honing their hands-on skills and understanding fundamental fabrication processes. Advancement often means taking on more complex designs, leading projects, and optimizing manufacturing workflows.
Progression can follow an individual contributor (IC) track, where engineers become highly specialized technical experts, or a management track, which emphasizes team leadership and strategic oversight. Factors influencing advancement speed include demonstrated problem-solving abilities, the complexity of projects managed, and the engineer's commitment to continuous learning. Specialization in areas like additive manufacturing, advanced welding techniques, or automation can open unique pathways.
Company size significantly impacts career paths; larger corporations might offer more structured advancement and diverse departments, while startups could provide broader exposure and quicker assumption of responsibility. Networking within the manufacturing and engineering community, engaging with industry associations, and pursuing relevant certifications enhance visibility and opportunities. Lateral moves to roles in quality assurance, R&D, or process improvement are also common pivots within the broader manufacturing sector.
Junior Fabrication Engineer
0-2 yearsKey Focus Areas
Fabrication Engineer
2-5 yearsKey Focus Areas
Senior Fabrication Engineer
5-8 yearsKey Focus Areas
Lead Fabrication Engineer
8-12 yearsKey Focus Areas
Fabrication Engineering Manager
12+ yearsKey Focus Areas
Junior Fabrication Engineer
0-2 yearsAssists senior engineers with design analysis, material selection, and process planning for fabrication projects. Executes basic fabrication tasks, operates machinery under supervision, and collects data for process optimization. Primarily supports ongoing projects and learns standard operating procedures.
Key Focus Areas
Develop foundational knowledge in material properties, manufacturing processes (welding, machining, forming), and CAD software. Focus on safety protocols, blueprint reading, and basic problem-solving. Seek mentorship to understand the practical aspects of fabrication and quality control standards.
Fabrication Engineer
2-5 yearsIndependently designs and implements fabrication processes for moderately complex components and assemblies. Conducts material testing, analyzes production data, and proposes solutions for manufacturing challenges. Collaborates with design teams to ensure manufacturability and supports production line improvements.
Key Focus Areas
Master advanced fabrication techniques, optimize existing processes for efficiency and cost reduction, and develop strong troubleshooting skills. Begin to take ownership of project segments, focusing on design-for-manufacturability principles and improving quality outcomes. Pursue certifications in specific fabrication methods.
Senior Fabrication Engineer
5-8 yearsLeads the development and optimization of advanced fabrication processes for critical projects. Provides technical guidance to a team of engineers and technicians, ensuring adherence to quality and timeline objectives. Identifies and implements innovative manufacturing technologies, significantly impacting production efficiency and product quality.
Key Focus Areas
Lead complex fabrication projects, mentor junior engineers, and drive continuous improvement initiatives. Develop expertise in process automation, advanced materials, and statistical process control. Focus on project management, risk assessment, and cross-functional team collaboration.
Lead Fabrication Engineer
8-12 yearsOversees multiple complex fabrication projects or a significant product line, providing technical leadership and strategic direction. Responsible for major process improvements, technology adoption, and ensuring the technical excellence of the fabrication team. Makes critical decisions impacting budget, resources, and project success.
Key Focus Areas
Develop strategic planning skills, define technical roadmaps for fabrication capabilities, and drive innovation within the department. Focus on high-level problem-solving, technology scouting, and fostering a culture of continuous improvement. Cultivate strong stakeholder management and communication skills.
Fabrication Engineering Manager
12+ yearsManages a team of Fabrication Engineers, overseeing all aspects of fabrication process development, optimization, and execution. Sets departmental goals, allocates resources, and ensures projects meet technical, quality, and cost objectives. Responsible for talent acquisition, performance reviews, and career development within the team.
Key Focus Areas
Master leadership and management principles, including budgeting, resource allocation, and performance management. Develop strategic vision for the fabrication department, aligning it with broader organizational goals. Focus on talent development, team building, and fostering cross-departmental collaboration.
Job Application Toolkit
Ace your application with our purpose-built resources:
Fabrication Engineer Resume Examples
Proven layouts and keywords hiring managers scan for.
View examplesFabrication Engineer Cover Letter Examples
Personalizable templates that showcase your impact.
View examplesTop Fabrication Engineer Interview Questions
Practice with the questions asked most often.
View examplesFabrication Engineer Job Description Template
Ready-to-use JD for recruiters and hiring teams.
View examplesGlobal Fabrication Engineer Opportunities
Fabrication Engineers globally design, optimize, and oversee manufacturing processes, specializing in material transformation and assembly. International demand is strong in advanced manufacturing, automotive, aerospace, and medical device sectors. Professionals find opportunities in regions prioritizing industrial growth and technological innovation. Regulatory differences in material standards and safety protocols impact international projects. Many engineers seek global roles for diverse project experience and exposure to cutting-edge technologies. Industry-specific certifications, like those in welding or advanced materials, enhance global mobility.
Global Salaries
Salaries for Fabrication Engineers vary significantly by region and industry. In North America, particularly the USA, entry-level engineers earn $65,000-$85,000 USD, while experienced professionals command $90,000-$130,000 USD annually. Canada offers slightly lower ranges, typically $60,000-$100,000 CAD ($45,000-$75,000 USD). European salaries differ widely: Germany offers €50,000-€80,000 ($55,000-$88,000 USD), reflecting its strong manufacturing base. The UK sees £35,000-£60,000 ($45,000-$75,000 USD).
Asia-Pacific markets like Singapore and South Korea provide competitive salaries, often $40,000-$70,000 USD, with lower cost of living benefits. Australian engineers might earn AUD $70,000-$110,000 ($48,000-$75,000 USD). Latin America, such as Mexico or Brazil, offers more modest compensation, typically $25,000-$45,000 USD, but with significantly lower living costs. Purchasing power parity is crucial; a lower nominal salary in one country might offer a comparable or better lifestyle than a higher one elsewhere.
Salary structures also differ. European countries often include more robust social benefits, like extensive vacation and public healthcare, which might not be reflected in the base salary. North American packages often feature private health insurance and performance bonuses. Tax implications significantly affect take-home pay, with some European nations having higher income taxes. Experience and specialized skills, like additive manufacturing or robotics integration, consistently increase earning potential across all regions.
Remote Work
While much of a Fabrication Engineer's role involves hands-on work, some aspects support international remote work. Design, simulation, process planning, and project management can often be performed remotely. This trend is growing, especially for senior roles focusing on strategic development rather than daily production oversight. Legal and tax implications are complex; engineers must understand their tax residency and employer's global hiring policies. Time zone differences can pose challenges for international team collaboration, requiring flexible work schedules.
Digital nomad visas are emerging in countries like Portugal and Estonia, offering pathways for remote professionals, though specific industry relevance varies. Some global engineering consultancies or software companies hire Fabrication Engineers for remote roles. Compensation for remote work might be adjusted based on the engineer's location, impacting geographic arbitrage opportunities. Reliable high-speed internet and a dedicated home office setup are essential for effective remote work in this field.
Visa & Immigration
Fabrication Engineers often qualify for skilled worker visas in many countries, such as the H-1B in the USA, the Skilled Worker visa in the UK, or the Blue Card in the EU. Popular destinations include Germany, Canada, Australia, and the USA, all with specific requirements. Generally, a relevant Bachelor's degree in engineering is mandatory, often requiring credential recognition. Professional licensing, like a Professional Engineer (PE) license in North America or Chartered Engineer status in the UK, facilitates immigration and employment.
Visa timelines vary, typically ranging from a few months to over a year, depending on the country and visa type. Employers often sponsor these visas. Pathways to permanent residency exist in countries like Canada and Australia through points-based systems, where engineering skills are highly valued. English language proficiency (e.g., IELTS, TOEFL) is often required for visa applications in English-speaking countries. Some countries offer fast-track programs for engineers in high-demand sectors. Family visas allow dependents to accompany the primary applicant.
2025 Market Reality for Fabrication Engineers
Understanding current market conditions is crucial for fabrication engineers aiming for career success. The field has evolved significantly from 2023 to 2025, influenced by post-pandemic supply chain recalibrations and the rapid integration of AI and automation.
Broader economic factors like industrial output and infrastructure spending directly impact hiring, while the demand for specialized skills now varies sharply by experience level, geographic region, and the size of manufacturing operations. This analysis provides an honest assessment of these realities, helping engineers set realistic expectations and craft effective career strategies.
Current Challenges
Fabrication engineers face heightened competition, especially at entry and mid-levels, as companies seek highly specialized skills for complex projects. Economic uncertainty sometimes delays large capital projects, impacting demand. A noticeable skill gap exists, with employers prioritizing engineers proficient in advanced automation, robotics integration, and additive manufacturing. Job searches can extend due to these specific demands.
Growth Opportunities
Strong demand persists for fabrication engineers in advanced manufacturing, particularly in sectors like electric vehicles, renewable energy infrastructure, and medical device production. Emerging roles focus on additive manufacturing (3D printing), robotics integration, and process automation design. Engineers who specialize in these areas find immediate opportunities.
Professionals can gain a competitive edge by mastering simulation software, digital twin technologies, and data analytics for manufacturing processes. Expertise in AI-driven design optimization and predictive maintenance systems is also highly valued. Underserved markets exist in regions undergoing industrial revitalization or those with new government-backed manufacturing initiatives.
Strategic career moves might involve targeting companies investing heavily in Industry 4.0 technologies, or smaller, agile firms pioneering new fabrication methods. The current market rewards engineers who can bridge the gap between theoretical design and practical, automated production. Investing in certifications for specific industrial robotics platforms or advanced materials processing can provide a significant advantage.
Current Market Trends
Hiring for fabrication engineers shows stable demand, particularly in sectors focused on advanced manufacturing, aerospace, defense, and specialized consumer electronics. Industries are increasingly investing in automation and smart factories, which reshapes the role. This shift emphasizes process optimization and integration of new technologies.
The integration of generative AI and machine learning is profoundly affecting fabrication, moving from conceptual design to simulation and optimizing production parameters. This requires engineers to understand AI-driven design tools and predictive maintenance systems. Companies seek engineers who can not only design but also implement and troubleshoot complex automated systems. Salary trends are generally positive for those with specialized skills in automation, robotics, and digital twin technologies, while more traditional roles see slower growth.
Geographic variations are significant; strong demand exists in manufacturing hubs like the Midwest, parts of the Southeast, and specific aerospace clusters in the West. Remote work is less common for hands-on fabrication roles, though some design and simulation tasks can be performed remotely. Market saturation is low for highly skilled, experienced engineers, but entry-level positions face more competition. Cyclical trends tied to industrial investment and defense contracts influence hiring patterns.
Emerging Specializations
The field of fabrication engineering is undergoing significant transformation, driven by advancements in automation, materials science, and digital manufacturing. These technological shifts are not merely optimizing existing processes; they are creating entirely new avenues for specialization. Understanding these emerging niches is crucial for fabrication engineers looking to position themselves strategically for career growth in 2025 and beyond.
Early positioning in these nascent areas often leads to a distinct competitive advantage, enabling engineers to become go-to experts before the fields become oversaturated. Such specialization frequently commands premium compensation and offers accelerated career progression, as demand for these specific skill sets outpaces supply. While established specializations offer stability, pursuing emerging areas taps into future industry needs, promising substantial long-term opportunities.
Many of these cutting-edge specializations are currently in rapid development, meaning they will transition from niche to mainstream within the next three to five years, creating a significant number of job opportunities. Investing in these areas involves a calculated risk, as not all emerging trends achieve widespread adoption. However, the potential for high reward and leadership in shaping future manufacturing paradigms often outweighs the initial uncertainty.
Advanced Additive Manufacturing Specialist
Additive manufacturing, particularly with advanced metals and composites, is moving beyond prototyping into large-scale, critical component production. Fabrication engineers specializing in this domain focus on designing for additive processes, optimizing build parameters, ensuring material integrity, and developing post-processing techniques for complex geometries. This area is critical for industries requiring lightweight, high-strength parts with intricate internal structures.
AI/ML for Fabrication Optimization Engineer
The integration of artificial intelligence and machine learning is revolutionizing fabrication by enabling predictive maintenance, autonomous process optimization, and enhanced quality control. Fabrication engineers in this area develop and implement AI models to analyze sensor data from manufacturing equipment, predict failures, optimize machine parameters for efficiency, and automate inspection processes. This specialization enhances operational intelligence and reduces waste.
Robotic Fabrication Systems Engineer
As manufacturing moves towards greater automation, the demand for fabrication engineers who can design, implement, and manage highly automated and robotic fabrication cells is increasing. This involves integrating robotic arms for welding, cutting, and assembly, alongside automated material handling systems. Specialists ensure seamless communication between robotic systems, vision systems, and overall production control systems.
Sustainable Fabrication Process Engineer
Sustainability is becoming a core driver in manufacturing, pushing for reduced environmental impact throughout the fabrication lifecycle. Fabrication engineers specializing in sustainable practices focus on optimizing material utilization, designing for recyclability, minimizing energy consumption in fabrication processes, and implementing closed-loop manufacturing systems. This area often involves life cycle assessment (LCA) and compliance with emerging green manufacturing standards.
Advanced Metrology and NDT Engineer
The increasing complexity of fabricated parts and the need for stringent quality assurance are driving demand for advanced metrology and non-destructive testing (NDT) specialists. These engineers develop and apply cutting-edge inspection techniques, such as computed tomography (CT) scanning, phased array ultrasonics, and optical metrology, to ensure the integrity and dimensional accuracy of components. They are crucial for high-reliability applications in aerospace and medical devices.
Pros & Cons of Being a Fabrication Engineer
Making informed career decisions requires a realistic understanding of both the benefits and challenges associated with a particular profession. Career experiences vary significantly based on company culture, industry sector, specialization area, and individual preferences. The pros and cons of a role like Fabrication Engineer can also shift at different career stages, from entry-level responsibilities to senior leadership. What one person views as a pro, another might see as a con, depending on their personal values and lifestyle priorities. This assessment provides an honest, balanced perspective on the realities of working as a Fabrication Engineer, helping you set appropriate expectations for this demanding and rewarding field.
Pros
- Fabrication engineers play a critical role in bringing designs to life, offering a high degree of job satisfaction from seeing tangible products created through their expertise in manufacturing processes.
- There is consistent demand for skilled fabrication engineers across diverse industries such as aerospace, automotive, medical devices, and consumer goods, ensuring strong job security and numerous employment opportunities.
- The role involves applying principles from mechanical engineering, materials science, and industrial design, providing continuous intellectual stimulation through complex problem-solving and process optimization challenges.
- Fabrication engineers often work with cutting-edge manufacturing technologies, including advanced robotics, additive manufacturing, and automated systems, which offers opportunities for continuous learning and skill development.
- With experience, fabrication engineers can advance into leadership roles such as manufacturing manager, production supervisor, or even R&D positions, or specialize in areas like process improvement or quality control.
- The skills acquired as a fabrication engineer, such as process optimization, material selection, and quality assurance, are highly transferable, allowing transitions into other engineering disciplines or consulting roles.
- Fabrication engineers typically earn competitive salaries, especially as they gain experience and specialize in advanced manufacturing techniques or manage larger production facilities, reflecting the specialized knowledge required.
Cons
- Fabrication engineers often work in environments with loud machinery, hazardous materials, and heavy equipment, requiring strict adherence to safety protocols and potentially leading to physical strain or injury over time.
- The role frequently involves troubleshooting complex manufacturing issues and process breakdowns, which can be highly stressful and demand quick, effective problem-solving under pressure to minimize production downtime.
- Fabrication processes require constant monitoring and adjustment, leading to irregular hours, on-call duties, or weekend work, especially when production schedules are tight or equipment failures occur.
- Success in this field depends heavily on precision and accuracy; even minor errors in design or execution can lead to costly material waste, product defects, or production delays, creating significant pressure.
- The field demands continuous learning and adaptation to new materials, manufacturing techniques, and automation technologies, requiring ongoing professional development and skill acquisition to remain competitive.
- Career progression can sometimes be limited within a single plant, as advancement often requires relocating to larger facilities or moving into management, which may not appeal to all engineers.
- Interacting with diverse teams, including production staff, designers, and quality control, can present communication challenges, as engineers must translate complex technical information for non-technical colleagues and resolve interpersonal conflicts related to production issues and deadlines.
Frequently Asked Questions
Fabrication Engineers face unique challenges in bridging design concepts with manufacturing reality. This section addresses crucial questions about entering this specialized role, focusing on the blend of mechanical expertise, material science, and process optimization required to excel in creating tangible products.
What educational background and certifications are essential for becoming a Fabrication Engineer?
Becoming a Fabrication Engineer typically requires a bachelor's degree in mechanical engineering, manufacturing engineering, materials science, or a related field. Some entry-level roles might accept candidates with an associate's degree and significant practical experience or certifications. Hands-on experience with CAD software, CNC machining, welding, and various fabrication techniques is highly beneficial for securing a position.
How long does it realistically take to become job-ready as a Fabrication Engineer if I'm starting from scratch?
The timeline to become job-ready as a Fabrication Engineer varies. A four-year bachelor's degree is the standard path. If you already have a relevant engineering degree, gaining specialized skills through internships or short courses might take 6-12 months. For those starting from scratch, expect 4-5 years for formal education and initial practical experience to be competitive for entry-level roles.
What are the typical salary expectations for a Fabrication Engineer at different experience levels?
Entry-level Fabrication Engineers can expect starting salaries to range from $60,000 to $75,000 annually, depending on location, industry, and company size. With 3-5 years of experience, salaries often rise to $75,000 - $95,000. Senior or specialized Fabrication Engineers with extensive experience and project management responsibilities can earn over $100,000, particularly in high-demand sectors like aerospace or automotive.
What kind of work-life balance can I expect as a Fabrication Engineer, and what is the typical work environment like?
The work-life balance for Fabrication Engineers often depends on the industry and project demands. During critical production phases or project deadlines, longer hours might be necessary. Generally, it's a standard full-time role with some potential for occasional overtime. The work environment is typically a mix of office design work and hands-on involvement in manufacturing facilities, which can be dynamic.
Is the job market for Fabrication Engineers stable, and what industries have the highest demand for this role?
The job market for Fabrication Engineers is generally stable and growing, driven by advancements in manufacturing, automation, and material science. Industries such as automotive, aerospace, medical devices, and heavy machinery consistently need these skills. As manufacturing processes evolve, the demand for engineers who can optimize and innovate fabrication techniques remains strong, offering good job security.
What are the typical career growth opportunities and paths for a Fabrication Engineer?
Career growth paths for Fabrication Engineers include specializing in specific materials, processes (e.g., additive manufacturing, advanced welding), or becoming experts in quality control or automation. Many advance into lead engineer roles, project management, or operations management positions. Some transition into research and development, focusing on new fabrication technologies or materials. Continuous learning and professional development are key to advancement.
Can Fabrication Engineers work remotely, or is it primarily an on-site role?
Working remotely as a Fabrication Engineer is less common than in purely software-based roles due to the hands-on nature of the work. While design and planning tasks can be done remotely, direct involvement with manufacturing processes, equipment, and production lines often requires on-site presence. Hybrid models might be possible where engineers split time between the office/facility and remote work for specific tasks.
Related Careers
Explore similar roles that might align with your interests and skills:
Fabrication Manager
A growing field with similar skill requirements and career progression opportunities.
Explore career guideFabricator
A growing field with similar skill requirements and career progression opportunities.
Explore career guideManufacturing Engineer
A growing field with similar skill requirements and career progression opportunities.
Explore career guideMetal Fabricator
A growing field with similar skill requirements and career progression opportunities.
Explore career guideWelder Fabricator
A growing field with similar skill requirements and career progression opportunities.
Explore career guideAssess your Fabrication Engineer readiness
Understanding where you stand today is the first step toward your career goals. Our Career Coach helps identify skill gaps and create personalized plans.
Skills Gap Analysis
Get a detailed assessment of your current skills versus Fabrication Engineer requirements. Our AI Career Coach identifies specific areas for improvement with personalized recommendations.
See your skills gapCareer Readiness Assessment
Evaluate your overall readiness for Fabrication Engineer roles with our AI Career Coach. Receive personalized recommendations for education, projects, and experience to boost your competitiveness.
Assess your readinessSimple pricing, powerful features
Upgrade to Himalayas Plus and turbocharge your job search.
Himalayas
Himalayas Plus
Himalayas Max
Find your dream job
Sign up now and join over 100,000 remote workers who receive personalized job alerts, curated job matches, and more for free!
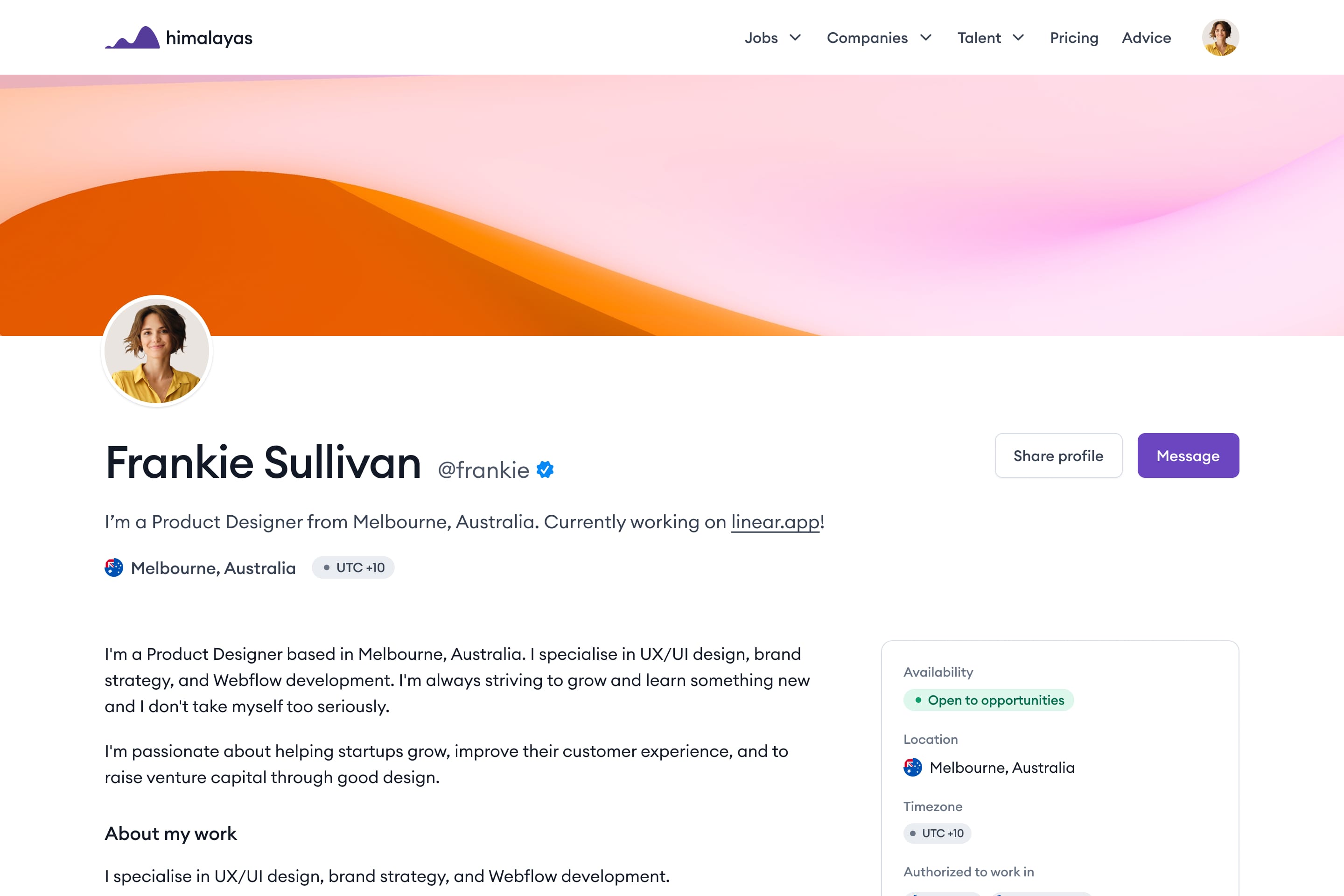