Complete Welding Supervisor Career Guide
Welding supervisors lead skilled teams, ensuring precision and safety in critical fabrication projects, from bridges to aerospace components. They translate blueprints into high-quality finished products, managing complex operations and mentoring welders. This role offers strong leadership opportunities and a chance to directly impact the structural integrity of vital infrastructure and industrial assets.
Key Facts & Statistics
Median Salary
$68,610 USD
(U.S. Bureau of Labor Statistics, May 2023 for First-Line Supervisors of Production and Operating Workers)
Range: $45k - $95k+ USD, varying significantly by experience, industry, and location
Growth Outlook
2%
(as part of first-line supervisors of production and operating workers), slower than average (U.S. Bureau of Labor Statistics, 2022-2032)
Annual Openings
≈42,200
openings annually (U.S. Bureau of Labor Statistics, 2022-2032)
Top Industries
Typical Education
High school diploma or equivalent, often with significant experience as a welder, and sometimes supplemented by postsecondary training in welding technology or supervision. Certifications in welding and safety are highly valued.
What is a Welding Supervisor?
A Welding Supervisor is a seasoned welding professional who manages and oversees all welding operations within a manufacturing, construction, or fabrication environment. This role ensures that all welding work adheres to stringent quality standards, project specifications, and safety regulations. They are responsible for the productivity, efficiency, and quality output of a team of welders, acting as both a technical expert and a team leader.
Unlike a lead welder who primarily focuses on executing complex welds and guiding peers on specific tasks, a Welding Supervisor has broader managerial responsibilities. They handle resource allocation, procedural development, quality assurance, team training, and direct communication with project management and engineering teams. This position requires a deep understanding of metallurgy, welding processes, and quality control, combined with strong leadership and organizational skills to ensure projects are completed safely, on time, and within budget.
What does a Welding Supervisor do?
Key Responsibilities
- Oversee and direct the daily activities of welding teams, ensuring adherence to project specifications and safety protocols.
- Conduct regular inspections of welding work in progress and completed welds to verify quality, structural integrity, and compliance with industry standards.
- Develop and implement welding procedures and techniques, optimizing processes for efficiency and material usage.
- Train and mentor junior welders, providing guidance on best practices, equipment operation, and problem-solving.
- Manage welding equipment maintenance schedules, coordinating repairs and calibrations to minimize downtime and ensure operational readiness.
- Collaborate with project managers and engineers to interpret blueprints, resolve technical issues, and plan welding sequences for complex fabrications.
- Maintain detailed records of welding activities, including quality control checks, material consumption, and personnel performance.
Work Environment
Welding supervisors typically work in industrial settings such as fabrication shops, construction sites, shipyards, or manufacturing plants. The environment can be noisy, dusty, and may involve exposure to fumes and heat. They spend a significant amount of time on the shop floor, actively monitoring work and interacting with their teams, but also dedicate time in an office for planning and documentation.
Collaboration is constant, working closely with welders, project managers, quality control inspectors, and safety officers. The pace can be fast, especially when meeting tight production deadlines, and often requires adaptability to changing project requirements. While most work is during standard business hours, some projects may demand extended shifts or weekend work, particularly in construction or large-scale manufacturing. Travel is generally minimal unless overseeing multiple remote sites.
Tools & Technologies
Welding supervisors regularly utilize a variety of tools and technologies to manage operations and ensure quality. They frequently use various welding machines, including MIG, TIG, Stick, and Flux-cored arc welders, along with plasma cutters and oxy-fuel torches. Quality control instruments like calipers, micrometers, and ultrasonic testing (UT) equipment are essential for inspecting welds. Supervisors also work with metal fabrication tools such as grinders, band saws, and press brakes.
For planning and documentation, they use computer-aided design (CAD) software to review blueprints, project management software for scheduling and resource allocation, and enterprise resource planning (ERP) systems for inventory management. Personal protective equipment (PPE) like welding helmets, gloves, and safety glasses are fundamental for ensuring workplace safety.
Welding Supervisor Skills & Qualifications
A Welding Supervisor oversees welding operations, ensuring projects meet quality standards, safety regulations, and production schedules. This role requires a blend of hands-on technical expertise and strong leadership abilities. Qualifications for a Welding Supervisor vary significantly based on the industry, company size, and project complexity. For instance, supervisors in aerospace or nuclear power need more rigorous certifications and regulatory knowledge than those in general fabrication shops.
Formal education, practical experience, and industry certifications each play a distinct role in qualifying for this position. While a bachelor's degree is rarely a strict requirement, an associate's degree in welding technology or a related engineering discipline is often preferred, especially for larger organizations or complex projects. Practical experience, typically 5-10 years as a journeyman welder, is paramount; it provides the foundational understanding of welding processes, materials, and troubleshooting. Certifications from organizations like the American Welding Society (AWS) are highly valued, demonstrating specialized knowledge and adherence to industry standards. These often include Certified Welding Inspector (CWI) or Certified Welding Educator (CWE) credentials, which are crucial for quality assurance and training aspects of the role.
The skill landscape for Welding Supervisors evolves with new welding technologies and automation. Understanding robotic welding, advanced material science, and digital inspection methods becomes increasingly important. While traditional manual welding skills remain essential, the ability to manage and implement new technologies distinguishes top-tier supervisors. This role demands a balance between deep technical knowledge and broad managerial capabilities, making continuous learning and adaptation critical for career progression.
Education Requirements
Technical Skills
- Expertise in various welding processes (SMAW, GMAW, GTAW, FCAW) across different material types (carbon steel, stainless steel, aluminum)
- Blueprint reading and interpretation, including welding symbols, joint designs, and dimensional tolerances
- Knowledge of welding codes and standards (e.g., AWS D1.1, ASME Section IX, API 1104)
- Proficiency in welding equipment setup, maintenance, and troubleshooting
- Quality control and inspection techniques (visual inspection, NDT basics, destructive testing principles)
- Understanding of metallurgy and material science related to welding, including heat treatment and distortion control
- Familiarity with fabrication processes and shop floor management principles
- Experience with production planning, scheduling, and resource allocation for welding operations
- Basic computer literacy for record-keeping, reporting, and using project management software
- Knowledge of industrial safety regulations and best practices (OSHA, confined space, hot work permits)
- Ability to perform welder qualification and procedure qualification tests
- Experience with welding automation and robotics (e.g., robotic welding cells, orbital welding systems)
Soft Skills
- Leadership and Team Management: Essential for guiding welding teams, delegating tasks effectively, and fostering a productive work environment.
- Problem-Solving and Decision-Making: Crucial for quickly identifying and resolving welding defects, equipment malfunctions, and production bottlenecks.
- Communication and Interpersonal Skills: Necessary for clearly conveying instructions, providing constructive feedback, and collaborating with engineers, clients, and other departments.
- Attention to Detail and Quality Focus: Paramount for ensuring all welds meet stringent quality standards, specifications, and safety regulations.
- Safety Consciousness and Risk Management: Vital for enforcing safety protocols, identifying hazards, and minimizing workplace accidents in a high-risk environment.
- Time Management and Organizational Skills: Important for managing multiple projects, prioritizing tasks, and ensuring deadlines are met efficiently.
- Adaptability and Flexibility: Useful for adjusting to changing project requirements, new technologies, and unexpected challenges on the shop floor.
- Mentorship and Training: Important for developing the skills of junior welders, providing on-the-job training, and fostering continuous improvement within the team.
How to Become a Welding Supervisor
Becoming a Welding Supervisor involves a blend of hands-on welding expertise, leadership capabilities, and a deep understanding of safety and quality standards. Traditional entry often starts with extensive experience as a welder, progressing into lead roles, while non-traditional paths might involve specialized certifications or associate degrees in welding technology, followed by accelerated on-the-job training. Expect a timeline of 3-5 years to gain the necessary experience from a beginner welder to a supervisory candidate, with career changers needing 2-3 years if they already possess strong leadership skills.
Entry strategies vary significantly by industry and company size. Large manufacturing firms or construction companies often prefer candidates with formal certifications and a proven track record of managing teams, while smaller fabrication shops might prioritize hands-on skill and a willingness to learn leadership on the job. Geographic location also plays a role; industrial hubs will have more opportunities and potentially higher competition. A common misconception is that supervision is merely an extension of welding; it requires distinct skills in project management, team motivation, and regulatory compliance.
Building a network within the welding and manufacturing sectors is crucial. Connect with experienced supervisors, attend industry workshops, and seek mentorship. The hiring landscape values practical experience and demonstrated leadership, often over just academic credentials. Overcoming barriers to entry involves actively seeking out opportunities to lead projects or mentor junior welders, even before securing a formal supervisory role. This proactive approach builds a strong foundation for advancement.
Earn fundamental welding certifications in various processes like SMAW, GMAW, and FCAW from an accredited institution or trade school. This initial step typically takes 6-12 months and provides the essential skills and safety knowledge required for any welding career, establishing a baseline of practical capability.
Accumulate 3-5 years of hands-on welding experience in diverse industrial settings such as manufacturing, construction, or fabrication. Focus on mastering complex welds, understanding different materials, and consistently meeting quality standards, which builds the credibility essential for a supervisory role.
Develop leadership and project management skills by taking on lead welder responsibilities, mentoring junior welders, or assisting with project coordination. Seek out opportunities to manage small teams, oversee specific job tasks, and troubleshoot production issues, demonstrating your readiness for increased responsibility.
Obtain advanced certifications relevant to supervisory roles, such as Certified Welding Inspector (CWI) or specific safety management certifications. These credentials validate your expertise in quality assurance and safety protocols, which are critical components of a welding supervisor's duties and enhance your marketability.
Build a professional network by attending industry events, joining professional organizations like the American Welding Society (AWS), and connecting with other supervisors and managers. Networking provides insights into industry trends, potential job openings, and mentorship opportunities that can accelerate your career progression.
Prepare a resume and portfolio that highlights your extensive welding experience, leadership accomplishments, and any relevant certifications. Focus on quantifiable achievements, such as improvements in efficiency, reductions in rework, or successful project completions, to showcase your impact and value.
Actively apply for Welding Supervisor positions, tailoring your application to each job description, and prepare for interviews that will assess both your technical knowledge and leadership capabilities. Be ready to discuss your approach to team management, problem-solving, and ensuring adherence to safety and quality standards.
Step 1
Earn fundamental welding certifications in various processes like SMAW, GMAW, and FCAW from an accredited institution or trade school. This initial step typically takes 6-12 months and provides the essential skills and safety knowledge required for any welding career, establishing a baseline of practical capability.
Step 2
Accumulate 3-5 years of hands-on welding experience in diverse industrial settings such as manufacturing, construction, or fabrication. Focus on mastering complex welds, understanding different materials, and consistently meeting quality standards, which builds the credibility essential for a supervisory role.
Step 3
Develop leadership and project management skills by taking on lead welder responsibilities, mentoring junior welders, or assisting with project coordination. Seek out opportunities to manage small teams, oversee specific job tasks, and troubleshoot production issues, demonstrating your readiness for increased responsibility.
Step 4
Obtain advanced certifications relevant to supervisory roles, such as Certified Welding Inspector (CWI) or specific safety management certifications. These credentials validate your expertise in quality assurance and safety protocols, which are critical components of a welding supervisor's duties and enhance your marketability.
Step 5
Build a professional network by attending industry events, joining professional organizations like the American Welding Society (AWS), and connecting with other supervisors and managers. Networking provides insights into industry trends, potential job openings, and mentorship opportunities that can accelerate your career progression.
Step 6
Prepare a resume and portfolio that highlights your extensive welding experience, leadership accomplishments, and any relevant certifications. Focus on quantifiable achievements, such as improvements in efficiency, reductions in rework, or successful project completions, to showcase your impact and value.
Step 7
Actively apply for Welding Supervisor positions, tailoring your application to each job description, and prepare for interviews that will assess both your technical knowledge and leadership capabilities. Be ready to discuss your approach to team management, problem-solving, and ensuring adherence to safety and quality standards.
Education & Training Needed to Become a Welding Supervisor
Becoming a Welding Supervisor involves a blend of practical experience and formal education, often leaning heavily on demonstrated skill and leadership. While a four-year bachelor's degree is uncommon and rarely required for this role, associate degrees in Welding Technology or Industrial Management provide a strong theoretical foundation. These programs typically cost $10,000-$30,000 and take two years to complete, offering in-depth knowledge of metallurgy, welding processes, quality control, and supervisory principles. Vocational schools and community colleges offer certificate programs in advanced welding techniques and supervisory skills, which are more focused and can be completed in 6-12 months for $3,000-$10,000.
Alternative learning paths include extensive on-the-job experience combined with industry certifications. Certifications from organizations like the American Welding Society (AWS) are highly valued. For instance, the AWS Certified Welding Supervisor (CWS) credential specifically targets this role, requiring a combination of education, experience, and passing an exam. These certifications demonstrate a commitment to professional standards and can significantly boost career prospects. Self-study and online courses on leadership, project management, and advanced welding codes also contribute to a supervisor's skill set, often at a lower cost, ranging from a few hundred to a couple of thousand dollars for a structured course.
Employers highly regard practical experience and relevant certifications more than a generic degree for a Welding Supervisor. The ability to lead a team, ensure quality, and troubleshoot complex welding issues is paramount. Continuous learning in new welding technologies, safety protocols, and management techniques is essential for career progression. Educational needs vary; a supervisor in a specialized industry like aerospace might require more specific certifications than one in general fabrication. Cost-benefit analysis often favors certifications and targeted vocational training due to their direct applicability and quicker return on investment compared to a lengthy, less specialized degree.
Welding Supervisor Salary & Outlook
Compensation for a Welding Supervisor varies significantly based on several factors beyond just base salary. Geographic location plays a crucial role; areas with high industrial demand for skilled welders, such as the Gulf Coast for oil and gas, or the Midwest for manufacturing, often offer higher pay. Conversely, regions with a lower cost of living may show comparatively lower salary figures.
Experience, specialized certifications (e.g., CWI, AWS certifications), and the complexity of projects managed directly influence earning potential. Supervisors overseeing critical infrastructure or specialized alloy welding typically command higher compensation. Total compensation often includes overtime pay, production bonuses, and sometimes profit-sharing, especially in contract-driven industries.
Beyond base pay, benefits packages are substantial, encompassing comprehensive health insurance, retirement contributions (401k with matching), and paid time off. Many employers also provide allowances for professional development and recertification. Larger companies and those in high-demand sectors like aerospace or shipbuilding generally offer more robust packages and higher base salaries compared to smaller fabrication shops.
Negotiation leverage comes from a proven track record of project completion, team leadership, and maintaining high safety standards. Remote work is generally not applicable to this hands-on role, but travel to different job sites can sometimes increase compensation through per diems. While these figures are in USD, international markets have their own distinct salary structures, often influenced by local labor laws and industry demand.
Salary by Experience Level
Level | US Median | US Average |
---|---|---|
Junior Welding Supervisor | $60k USD | $65k USD |
Welding Supervisor | $75k USD | $80k USD |
Senior Welding Supervisor | $90k USD | $95k USD |
Lead Welding Supervisor | $105k USD | $110k USD |
Welding Manager | $125k USD | $130k USD |
Market Commentary
The job market for Welding Supervisors remains stable with a moderate growth outlook, primarily driven by the ongoing need for infrastructure development, manufacturing, and maintenance across various industries. The Bureau of Labor Statistics projects a steady demand for skilled trades, and supervisors are critical to ensuring quality and safety in these operations. Aging infrastructure necessitates constant repair and upgrades, sustaining demand for experienced welding professionals and their supervisors.
Emerging opportunities for Welding Supervisors include roles in advanced manufacturing, where automation and robotic welding are increasingly common. Supervisors in these environments need a blend of traditional welding expertise and familiarity with automated systems. The integration of data analytics for quality control and project management also creates new avenues for those with technological aptitude.
Supply and demand dynamics show a persistent need for highly skilled and certified supervisors. There is often a shortage of candidates with both extensive welding experience and strong leadership abilities, creating competitive compensation for qualified individuals. This imbalance contributes to job security and upward salary mobility for competent supervisors.
Future-proofing this role involves continuous learning in new welding techniques, materials, and digital tools for project oversight. While some aspects of welding can be automated, the critical oversight, quality assurance, and problem-solving skills of a supervisor are resistant to full automation. Geographic hotspots for Welding Supervisors include industrial hubs in Texas, Louisiana, the Great Lakes region, and the Pacific Northwest, particularly where large-scale construction, energy, or shipbuilding projects are underway.
Welding Supervisor Career Path
Career progression for a Welding Supervisor typically involves advancing from hands-on oversight to broader operational and strategic management. This path distinguishes between individual contributor (IC) roles, which might involve highly specialized welding techniques or quality assurance, and the management track, which focuses on team leadership, project coordination, and process optimization. Most Welding Supervisors follow the management track, moving from direct team leadership to managing multiple teams or entire departments.
Advancement speed depends on several factors, including a supervisor's proven ability to maintain safety standards, improve productivity, and manage personnel effectively. Specialization in advanced welding techniques, automation, or specific industry codes (e.g., ASME, API) can accelerate progression. Company size also plays a role; larger organizations often have more layers of management, offering clearer vertical mobility. Smaller companies might offer quicker advancement to broader roles, but with fewer defined intermediate steps.
Lateral movement opportunities exist within the broader manufacturing or construction sectors, potentially shifting into roles like Quality Control Inspector, Fabrication Manager, or even Safety Officer. Networking within industry associations, pursuing advanced certifications (e.g., Certified Welding Inspector, Certified Welding Educator), and demonstrating strong leadership qualities are crucial for career growth. Continuous learning about new welding technologies, materials, and safety regulations is essential for sustained progression in this field.
Junior Welding Supervisor
2-4 years total experienceOversees a small team of welders on specific tasks, ensuring adherence to safety guidelines and project specifications. Provides direct guidance and troubleshooting support on the shop floor. Monitors work progress and helps maintain equipment. Makes immediate operational decisions for the assigned team.
Key Focus Areas
Develop foundational leadership skills, including effective communication and basic conflict resolution. Master safety protocols and quality control procedures specific to welding operations. Gain proficiency in production scheduling and resource allocation for small teams. Understand equipment maintenance and troubleshooting.
Welding Supervisor
4-7 years total experienceManages a larger team of welders or multiple smaller teams across different shifts, ensuring all projects meet deadlines and quality standards. Responsible for daily operations, including material flow, equipment readiness, and adherence to production targets. Conducts performance reviews and addresses disciplinary issues.
Key Focus Areas
Refine team management and motivational techniques. Implement process improvements to enhance efficiency and reduce waste. Develop stronger analytical skills for performance tracking and reporting. Begin mentoring junior staff and contribute to training programs.
Senior Welding Supervisor
7-10 years total experienceOversees multiple welding teams or a significant section of the welding department, responsible for optimizing workflows and implementing new technologies. Develops and enforces departmental policies and procedures. Manages budgets for labor, materials, and equipment. Plays a key role in continuous improvement initiatives.
Key Focus Areas
Focus on strategic planning for departmental goals and long-term projects. Develop advanced problem-solving skills for complex production challenges. Cultivate stronger cross-functional collaboration with engineering, logistics, and supply chain teams. Take on more formal mentorship and leadership development roles.
Lead Welding Supervisor
10-15 years total experienceActs as the primary technical and operational leader for all welding activities within a facility or major project. Drives significant process innovations and technology adoption. Responsible for long-term strategic planning, departmental budget allocation, and major capital expenditure recommendations. Mentors all levels of welding supervision.
Key Focus Areas
Master advanced project management methodologies and resource optimization. Develop expertise in lean manufacturing principles and automation integration. Cultivate strong leadership presence and influence across the organization. Engage in industry best practices and emerging technologies.
Welding Manager
15+ years total experienceManages the entire welding function across multiple facilities or large-scale, complex projects. Sets strategic objectives, oversees departmental budgets, and is accountable for overall operational performance and profitability. Leads the adoption of new technologies and ensures compliance with all regulatory standards. Plays a vital role in talent acquisition and development for the welding department.
Key Focus Areas
Focus on organizational leadership, strategic decision-making, and cross-departmental integration. Develop business acumen, financial management, and high-level negotiation skills. Build a professional network across the industry and within the company’s executive ranks. Drive cultural change and foster a high-performance environment.
Junior Welding Supervisor
2-4 years total experienceOversees a small team of welders on specific tasks, ensuring adherence to safety guidelines and project specifications. Provides direct guidance and troubleshooting support on the shop floor. Monitors work progress and helps maintain equipment. Makes immediate operational decisions for the assigned team.
Key Focus Areas
Develop foundational leadership skills, including effective communication and basic conflict resolution. Master safety protocols and quality control procedures specific to welding operations. Gain proficiency in production scheduling and resource allocation for small teams. Understand equipment maintenance and troubleshooting.
Welding Supervisor
4-7 years total experienceManages a larger team of welders or multiple smaller teams across different shifts, ensuring all projects meet deadlines and quality standards. Responsible for daily operations, including material flow, equipment readiness, and adherence to production targets. Conducts performance reviews and addresses disciplinary issues.
Key Focus Areas
Refine team management and motivational techniques. Implement process improvements to enhance efficiency and reduce waste. Develop stronger analytical skills for performance tracking and reporting. Begin mentoring junior staff and contribute to training programs.
Senior Welding Supervisor
7-10 years total experienceOversees multiple welding teams or a significant section of the welding department, responsible for optimizing workflows and implementing new technologies. Develops and enforces departmental policies and procedures. Manages budgets for labor, materials, and equipment. Plays a key role in continuous improvement initiatives.
Key Focus Areas
Focus on strategic planning for departmental goals and long-term projects. Develop advanced problem-solving skills for complex production challenges. Cultivate stronger cross-functional collaboration with engineering, logistics, and supply chain teams. Take on more formal mentorship and leadership development roles.
Lead Welding Supervisor
10-15 years total experienceActs as the primary technical and operational leader for all welding activities within a facility or major project. Drives significant process innovations and technology adoption. Responsible for long-term strategic planning, departmental budget allocation, and major capital expenditure recommendations. Mentors all levels of welding supervision.
Key Focus Areas
Master advanced project management methodologies and resource optimization. Develop expertise in lean manufacturing principles and automation integration. Cultivate strong leadership presence and influence across the organization. Engage in industry best practices and emerging technologies.
Welding Manager
15+ years total experienceManages the entire welding function across multiple facilities or large-scale, complex projects. Sets strategic objectives, oversees departmental budgets, and is accountable for overall operational performance and profitability. Leads the adoption of new technologies and ensures compliance with all regulatory standards. Plays a vital role in talent acquisition and development for the welding department.
Key Focus Areas
Focus on organizational leadership, strategic decision-making, and cross-departmental integration. Develop business acumen, financial management, and high-level negotiation skills. Build a professional network across the industry and within the company’s executive ranks. Drive cultural change and foster a high-performance environment.
Job Application Toolkit
Ace your application with our purpose-built resources:
Welding Supervisor Resume Examples
Proven layouts and keywords hiring managers scan for.
View examplesWelding Supervisor Cover Letter Examples
Personalizable templates that showcase your impact.
View examplesTop Welding Supervisor Interview Questions
Practice with the questions asked most often.
View examplesWelding Supervisor Job Description Template
Ready-to-use JD for recruiters and hiring teams.
View examplesGlobal Welding Supervisor Opportunities
Welding Supervisors manage welding operations, ensuring quality and safety across diverse industries globally. Their skills are highly transferable, with strong demand in construction, manufacturing, and energy sectors worldwide.
International projects often seek experienced supervisors for their expertise in overseeing complex fabrication. Navigating varying international standards and safety protocols is crucial for global mobility in this role.
International certifications like AWS CWI or EWF/IIW diplomas significantly enhance global career prospects for Welding Supervisors.
Global Salaries
Welding Supervisor salaries vary significantly by region and industry. In North America, a supervisor typically earns $60,000-$90,000 USD annually, with higher ranges in specialized fields like oil and gas. For example, in Canada, salaries might range from CAD 75,000-100,000. These figures generally reflect a good purchasing power in major cities.
Europe offers diverse salary landscapes. In Germany, a Welding Supervisor can expect €50,000-€75,000 (approx. $54,000-$81,000 USD), while in the UK, salaries are around £40,000-£60,000 (approx. $50,000-$75,000 USD). Northern European countries often provide robust social benefits, including generous vacation time and comprehensive healthcare, which impact overall compensation value.
In the Asia-Pacific region, compensation can be lower but still competitive relative to local cost of living. Australia sees salaries from AUD 80,000-120,000 (approx. $53,000-$80,000 USD), driven by strong mining and infrastructure sectors. In contrast, Southeast Asian countries like Malaysia might offer MYR 80,000-120,000 (approx. $17,000-$25,000 USD), where lower living costs often balance the take-home pay.
Latin America offers salaries from $30,000-$50,000 USD, with significant variations based on the country's industrial development. Tax implications and social security contributions differ widely, impacting net income. International experience and specialized certifications often command higher pay, especially in regions with high demand for skilled professionals.
Remote Work
International remote work for Welding Supervisors is very limited due to the hands-on nature of the role. This position requires direct oversight of welding operations, safety protocols, and quality control on-site. Therefore, full-time remote work is not feasible for most Welding Supervisor positions.
However, some aspects of the role, like project planning, scheduling, and administrative tasks, can be performed remotely. Companies with multiple international sites might employ a 'hybrid' model where a supervisor handles planning remotely but travels frequently for on-site supervision and inspections. Digital nomad opportunities are generally not applicable to this profession.
Any international remote work would primarily involve administrative or consultative capacities, not direct supervision. Such arrangements typically require a clear understanding of tax implications and local labor laws in both the employer's and the employee's country of residence. Most employers prioritize on-site presence for this critical role.
Visa & Immigration
Welding Supervisors often pursue skilled worker visas for international opportunities. Key destination countries include Canada, Australia, Germany, and the UK, driven by their robust industrial sectors. Requirements typically include a recognized trade qualification, several years of supervisory experience, and a job offer from an employer.
Credential recognition is crucial; professional bodies or government agencies may assess qualifications. For instance, Canada's Express Entry system often favors trades with high demand, while Australia's skilled migration program lists specific occupations. Language proficiency, usually English or the local language, is often a requirement, demonstrated through tests like IELTS or Goethe-Zertifikat.
Visa application timelines vary from a few months to over a year, depending on the country and visa type. Employers often sponsor skilled worker visas, facilitating the process. Pathways to permanent residency exist in many countries for skilled professionals after a period of employment. Family visas for dependents are usually available alongside the primary applicant's visa.
2025 Market Reality for Welding Supervisors
Understanding the current market reality for Welding Supervisors is crucial for career progression. The industry has seen notable shifts from 2023 to 2025, influenced by post-pandemic economic adjustments and the accelerating integration of automation.
Broader economic factors, such as infrastructure spending and energy sector investments, directly impact the availability of supervisory roles. Market realities for this role vary significantly by experience level, with senior supervisors in specialized fields often finding more opportunities than those with general experience. Geographic location and the size of the employing company also play a large role in job prospects and compensation. This analysis provides an honest assessment of these dynamics, helping supervisors set realistic career expectations.
Current Challenges
Welding Supervisors face increased competition for fewer senior roles. Market saturation at entry levels means a larger pool of candidates vying for promotions. Economic uncertainty in manufacturing can slow project starts, reducing demand for supervisory oversight. Adapting to new automation technologies requires continuous upskilling, creating a skills gap for those resistant to change.
Growth Opportunities
Despite challenges, significant opportunities exist for Welding Supervisors. Strong demand continues in critical infrastructure projects, such as bridge construction, pipeline maintenance, and power generation facilities, including nuclear and renewable energy. Specialized fabrication, particularly in aerospace and defense, also offers robust prospects for supervisors with niche certifications.
Emerging roles often involve overseeing hybrid teams that combine human welders with robotic systems, requiring supervisors to become experts in both traditional and automated processes. Professionals who proactively gain certifications in robotics, additive manufacturing, or advanced metallurgy position themselves advantageously. Underserved markets, such as certain regions experiencing industrial revitalization or companies investing heavily in new manufacturing technologies, present better opportunities. Supervisors with a proven track record in lean manufacturing, quality control, and team leadership through technological transitions will find themselves highly sought after. Strategic career moves might involve targeting companies adopting Industry 4.0 principles, as these organizations value forward-thinking leadership in welding operations.
Current Market Trends
Demand for Welding Supervisors remains stable in 2025, particularly in infrastructure, energy, and specialized fabrication sectors. However, the market is becoming more discerning, prioritizing supervisors with strong digital literacy and experience with automated welding systems. Companies seek leaders who can integrate new technologies like robotic welding and AI-driven quality control into daily operations.
Economic conditions show a mixed picture; while large-scale construction and renewable energy projects drive demand, smaller manufacturing outfits face tighter budgets. This creates a bifurcated market: high demand for supervisors in growth sectors, but slower movement in traditional, less innovative areas. Employer requirements now heavily emphasize safety compliance, project management software proficiency, and the ability to train teams on advanced techniques. Salaries are showing modest growth, particularly for those with certifications in specialized welding processes or automation. Remote work normalization has minimal impact here, as the role is inherently hands-on. Geographic variations are significant, with stronger markets in industrial hubs like the Gulf Coast, Midwest, and regions with active shipbuilding or aerospace industries.
Emerging Specializations
The role of a Welding Supervisor is evolving significantly, driven by rapid advancements in manufacturing technologies and a growing demand for precision and efficiency. Understanding these shifts is crucial for professionals aiming to position themselves for future leadership opportunities. New specialization areas are emerging, creating distinct career paths that blend traditional welding expertise with modern technological applications.
Early positioning in these emerging fields offers substantial advantages for career advancement from 2025 onwards. Professionals who proactively develop skills in these cutting-edge niches often command premium compensation and experience accelerated career growth. This is because they fill critical skill gaps that established specializations cannot address.
While established welding specializations remain vital, pursuing emerging areas balances risk and reward. These new fields, though less saturated now, are poised to become mainstream within the next five to ten years, creating a significant number of job opportunities. Investing in these skills now prepares supervisors to lead the next generation of welding operations, ensuring their relevance and value in an increasingly automated and data-driven industrial landscape.
Robotic Welding Systems Supervisor
This specialization focuses on overseeing welding operations that integrate robotic systems and advanced automation. Welding Supervisors in this area manage the programming, calibration, and maintenance of robotic welders, ensuring optimal performance and quality control. They bridge the gap between human expertise and automated precision, optimizing production workflows and enhancing safety within the fabrication environment.
Additive Manufacturing Welding Specialist
Additive manufacturing, particularly in metals, is transforming how components are produced, and welding supervisors are needed to oversee the post-processing and quality assurance of these parts. This involves managing the fusion of layers, identifying and correcting defects, and ensuring structural integrity. Supervisors in this field ensure that 3D-printed metal components meet stringent industry standards for strength and durability.
Smart Welding & Data Analytics Supervisor
Supervisors in this area focus on integrating advanced sensors and data analytics into welding processes to monitor quality in real-time. They implement systems that collect data on weld parameters, temperature, and material behavior, using this information to predict defects and optimize procedures. This allows for proactive quality control and continuous improvement of welding operations, reducing waste and increasing efficiency.
Advanced Materials Welding Supervisor
This specialization involves overseeing welding projects that utilize novel materials, such as advanced high-strength steels, composites, or dissimilar metal combinations. Supervisors must understand the unique metallurgical properties and welding challenges associated with these materials. They develop and implement specialized welding procedures to ensure the integrity and performance of complex structures made from these cutting-edge alloys.
Sustainable Welding Practices Lead
Supervisors in this field focus on implementing and enforcing sustainable and environmentally responsible welding practices. This includes managing processes that minimize energy consumption, reduce fume emissions, and optimize material usage to lessen environmental impact. They also oversee the proper disposal of welding waste and ensure compliance with evolving environmental regulations, contributing to greener manufacturing.
Pros & Cons of Being a Welding Supervisor
Making an informed career choice requires a clear understanding of both the benefits and challenges of a specific profession. The experience within any career, including that of a Welding Supervisor, can vary significantly based on the company culture, the industry sector (e.g., manufacturing, construction, energy), and the specific responsibilities of the role. Additionally, the pros and cons may shift at different stages of a career, with early-career supervisors facing different hurdles than those in senior positions. What one person considers an advantage, another might see as a challenge, depending on their personal values, work style, and lifestyle preferences. This assessment provides an honest, balanced perspective to help set realistic expectations for a career as a Welding Supervisor.
Pros
- Welding supervisors are in high demand across various industries, including manufacturing, construction, and energy, ensuring strong job security and numerous employment opportunities.
- The role offers significant opportunities for leadership and team management, allowing supervisors to develop valuable skills in planning, organizing, and motivating a skilled workforce.
- Supervisors gain deep expertise in welding processes, quality control, and safety protocols, making them highly respected technical experts within their organizations and the broader industry.
- Many positions offer competitive salaries and benefits packages, reflecting the specialized knowledge and critical responsibilities associated with overseeing welding operations and ensuring project success.
- The work provides a sense of accomplishment through direct involvement in critical projects, seeing tangible results from effective team management and successful project execution.
- Supervisors often have the autonomy to implement process improvements and optimize workflows, contributing directly to efficiency and productivity, which can be intellectually stimulating and rewarding.
- This role can serve as a stepping stone to higher management positions, such as production manager or operations manager, offering clear career progression paths for those seeking advancement.
Cons
- Welding supervisors often face significant pressure to meet production deadlines, which can lead to extended hours and high stress levels, especially during peak demand or when equipment issues arise.
- The role requires extensive knowledge of safety regulations and quality standards, making supervisors directly accountable for accidents or defects, which carries considerable responsibility and liability.
- Supervisors frequently mediate conflicts among team members or address performance issues, demanding strong interpersonal skills and emotional resilience to handle difficult personnel situations.
- Working in a supervisory role often means less hands-on welding and more administrative tasks, such as paperwork, scheduling, and reporting, which can be less appealing for those who enjoy the craft itself.
- The work environment can be noisy, hot, and physically demanding, requiring constant movement around the shop floor and exposure to industrial hazards, despite safety protocols.
- Continuous learning is necessary to keep up with new welding technologies, materials, and regulatory changes, requiring a commitment to ongoing professional development outside of regular work hours.
- Salary progression can plateau after reaching a certain level, especially in smaller companies, making it harder to achieve significant income increases without moving into higher management or specialized consulting roles, which are limited in number and competitive to secure, reducing opportunities for substantial financial advancement once a supervisor reaches a certain level within an organization.
Frequently Asked Questions
Welding Supervisors face unique challenges balancing technical expertise with team leadership and project management. This section addresses key questions about this specific role, from required certifications and salary expectations to managing teams and ensuring project quality and safety.
What are the essential qualifications and experience needed to become a Welding Supervisor?
Becoming a Welding Supervisor typically requires 5-10 years of hands-on welding experience, often with a focus on specific processes like Stick, MIG, or TIG. Most employers also look for a relevant associate's degree in welding technology or a related field, alongside certifications such as AWS Certified Welding Supervisor (CWS) or Certified Welding Inspector (CWI). Leadership training and strong communication skills are also crucial.
What is a typical career progression from a welder to a Welding Supervisor?
The career path to a Welding Supervisor role can vary. Many individuals start as skilled welders, gaining experience and then pursuing supervisory roles after 5-10 years. Obtaining relevant certifications like CWS or CWI can significantly accelerate progression. Some also pursue associate's or bachelor's degrees in welding engineering technology to enhance their technical and managerial skills.
What are the salary expectations for a Welding Supervisor, and how do they compare to a standard welder?
Welding Supervisors often earn between $60,000 and $90,000 annually, depending on industry, location, and experience. Larger companies, specialized projects like pipeline or structural steel, and areas with high demand for skilled trades can offer higher compensation. Benefits packages often include health insurance, retirement plans, and paid time off.
What is the typical work-life balance like for a Welding Supervisor?
The work-life balance for a Welding Supervisor can be demanding, often involving long hours, especially during project deadlines or shifts that align with production schedules. Supervisors are responsible for troubleshooting, safety, and quality control, which can require flexibility and availability outside standard hours. While it is a rewarding role, it requires a significant time commitment and adaptability.
How secure is the job market for Welding Supervisors, and what are the growth prospects?
The job market for Welding Supervisors remains stable and in demand, driven by ongoing infrastructure projects, manufacturing, and energy sector needs. Experienced supervisors are particularly sought after due to their blend of technical expertise and leadership. While economic fluctuations can impact some sectors, the overall outlook is positive, especially for those with diverse experience and certifications.
What are the biggest challenges a Welding Supervisor faces daily?
Key challenges include managing diverse teams with varying skill levels, ensuring strict adherence to safety protocols, and maintaining high-quality standards under tight deadlines. Supervisors must also stay updated on new welding technologies and materials, resolve technical issues, and effectively communicate project requirements and expectations to their team and management.
What are the potential career advancement opportunities beyond a Welding Supervisor role?
Further career growth for a Welding Supervisor can lead to roles such as Welding Manager, Quality Control Manager, or even Project Manager, especially in larger organizations. Opportunities also exist in training and development, or as independent consultants specializing in welding procedures and inspections. Continuous learning and advanced certifications support these advancements.
Related Careers
Explore similar roles that might align with your interests and skills:
Welder Fabricator
A growing field with similar skill requirements and career progression opportunities.
Explore career guideWelder Helper
A growing field with similar skill requirements and career progression opportunities.
Explore career guideWelding Inspector
A growing field with similar skill requirements and career progression opportunities.
Explore career guideMachine Welder
A growing field with similar skill requirements and career progression opportunities.
Explore career guideWelding Machine Operator
A growing field with similar skill requirements and career progression opportunities.
Explore career guideAssess your Welding Supervisor readiness
Understanding where you stand today is the first step toward your career goals. Our Career Coach helps identify skill gaps and create personalized plans.
Skills Gap Analysis
Get a detailed assessment of your current skills versus Welding Supervisor requirements. Our AI Career Coach identifies specific areas for improvement with personalized recommendations.
See your skills gapCareer Readiness Assessment
Evaluate your overall readiness for Welding Supervisor roles with our AI Career Coach. Receive personalized recommendations for education, projects, and experience to boost your competitiveness.
Assess your readinessSimple pricing, powerful features
Upgrade to Himalayas Plus and turbocharge your job search.
Himalayas
Himalayas Plus
Himalayas Max
Find your dream job
Sign up now and join over 100,000 remote workers who receive personalized job alerts, curated job matches, and more for free!
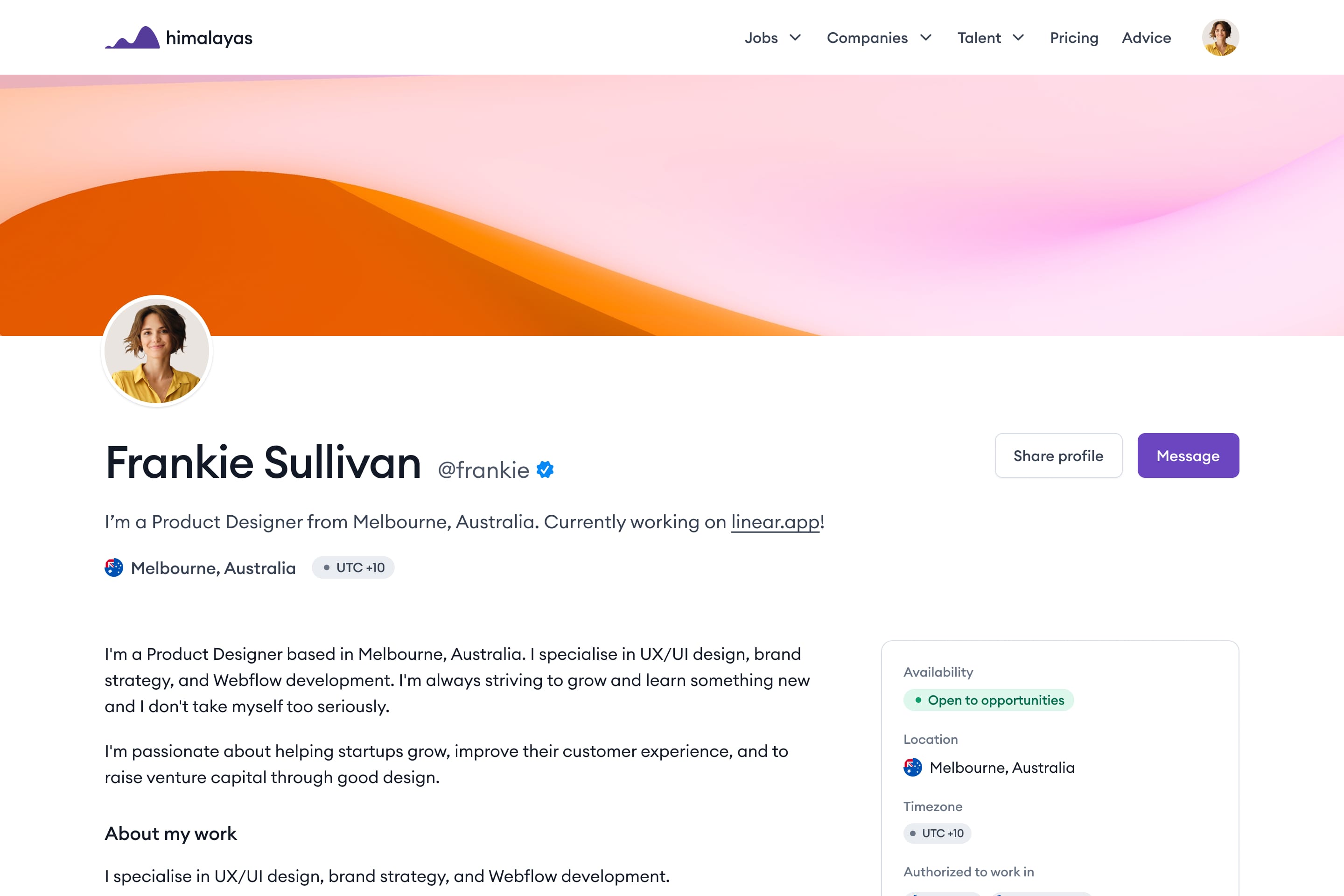