Complete Welding Inspector Career Guide
Welding inspectors are crucial guardians of safety and quality, ensuring every weld meets rigorous standards essential for structural integrity in critical infrastructure like bridges, pipelines, and buildings. This role demands a keen eye for detail and a deep understanding of metallurgy, offering a vital career path for those committed to precision and public safety. You'll combine technical expertise with a commitment to upholding the highest quality benchmarks, directly impacting the reliability of countless structures.
Key Facts & Statistics
Median Salary
$64,790 USD
(U.S. national median, BLS, May 2023)
Range: $45k - $90k+ USD (BLS, May 2023, varying by experience and certifications)
Growth Outlook
5%
as fast as average (BLS, 2022-2032)
Annual Openings
≈3,800
openings annually (BLS, 2022-2032)
Top Industries
Typical Education
High school diploma or equivalent, often supplemented by vocational training in welding and specific certifications (e.g., AWS Certified Welding Inspector - CWI)
What is a Welding Inspector?
A Welding Inspector is a highly specialized quality assurance professional responsible for ensuring the integrity and compliance of welded structures and components. They meticulously examine welds at various stages of production—before, during, and after welding—to verify adherence to specific codes, standards, and engineering drawings. Their primary objective is to prevent failures, enhance safety, and maintain the quality of fabricated metal products across industries.
Unlike a welder, who performs the joining process, or a welding engineer, who designs the procedures, the inspector acts as an independent auditor. They apply a deep understanding of metallurgy, welding processes, and non-destructive testing methods to identify defects, assess workmanship, and ultimately certify that welds meet stringent quality and safety criteria. This role is critical in industries where weld integrity is paramount, such as construction, aerospace, energy, and manufacturing.
What does a Welding Inspector do?
Key Responsibilities
- Review and interpret welding procedure specifications (WPS) and relevant codes to ensure compliance before welding begins.
- Conduct visual inspections of welds during all stages of fabrication, including pre-weld, interpass, and post-weld, to detect defects like cracks, porosity, or incomplete fusion.
- Perform non-destructive testing (NDT) methods such as liquid penetrant, magnetic particle, or ultrasonic testing to assess weld integrity and identify subsurface flaws.
- Document all inspection findings, including deviations and non-conformances, and prepare detailed inspection reports for clients or project managers.
- Verify the calibration and proper functioning of inspection equipment, ensuring accuracy in measurements and test results.
- Monitor welder performance and qualifications, providing feedback and ensuring adherence to approved welding procedures and safety protocols.
- Collaborate with welders, fabricators, and engineers to resolve quality issues and implement corrective actions for non-compliant welds or processes.
Work Environment
Welding inspectors typically work in diverse industrial settings, including fabrication shops, construction sites, manufacturing plants, shipyards, and oil and gas facilities. The environment can be dynamic and demanding, often involving exposure to noise, varying temperatures, and sometimes confined spaces or elevated platforms. While some administrative tasks happen in an office, a significant portion of the day involves hands-on inspection in the field.
The role often involves a mix of independent work, such as detailed weld examinations, and collaborative efforts with welding teams, engineers, and project managers. Work schedules can vary, with standard day shifts common, but project deadlines may necessitate overtime, especially in construction or turnaround situations. Travel to different job sites is a frequent requirement, making flexibility important for this profession.
Tools & Technologies
Welding inspectors utilize a range of specialized tools and technologies to perform their duties. They frequently use visual inspection aids like magnifying glasses, borescopes, and weld gauges to measure dimensions and identify surface imperfections. For more in-depth analysis, they operate non-destructive testing (NDT) equipment, including ultrasonic testing (UT) units, magnetic particle inspection (MPI) kits, liquid penetrant inspection (LPI) materials, and sometimes radiographic testing (RT) film viewers.
Beyond physical tools, inspectors rely on various software applications for documentation, such as Microsoft Office Suite (Word, Excel) for report generation and data tracking. They also work with digital cameras for photographic evidence and may use specialized inspection software or enterprise resource planning (ERP) systems for project management and quality control. Familiarity with specific industry codes and standards, such as AWS D1.1, ASME Boiler and Pressure Vessel Code, or API standards, is essential for interpreting requirements and ensuring compliance.
Welding Inspector Skills & Qualifications
Becoming a Welding Inspector requires a blend of formal education, extensive practical experience, and specialized certifications. Qualifications are structured to ensure inspectors possess deep knowledge of welding processes, metallurgy, and non-destructive testing (NDT) methods. The field prioritizes demonstrated competence and adherence to industry codes over purely academic credentials.
Requirements vary significantly based on the inspector's seniority, the industry sector, and the geographic region. Entry-level positions may accept candidates with vocational training and basic certifications, often under supervision. Senior roles, especially in critical sectors like oil and gas, aerospace, or nuclear, demand advanced certifications, extensive experience, and a proven track record. Company size also plays a role; larger organizations often have more stringent, formalized requirements, while smaller firms might prioritize practical experience and versatility.
Certifications, particularly those from recognized bodies like the American Welding Society (AWS) or the American Society for Nondestructive Testing (ASNT), are paramount. They often carry more weight than a general engineering degree alone. Practical experience, especially hands-on welding or fabrication experience, is invaluable; it provides a crucial understanding of the processes being inspected. Alternative pathways, such as military experience in welding or NDT, or apprenticeships followed by certification, are widely accepted and highly valued. The skill landscape is continuously evolving with new welding technologies and advanced NDT techniques, requiring inspectors to pursue ongoing professional development to maintain relevance and effectiveness.
Education Requirements
Technical Skills
- AWS Certified Welding Inspector (CWI) certification
- Knowledge of welding processes (SMAW, GMAW, GTAW, FCAW, SAW)
- Proficiency in interpreting welding procedure specifications (WPS) and procedure qualification records (PQR)
- Ability to read and interpret engineering drawings, blueprints, and welding symbols
- Understanding of destructive and non-destructive testing (NDT) methods (VT, PT, MT, UT, RT)
- Familiarity with industry codes and standards (e.g., ASME, API, AWS D1.1)
- Use of precision measuring tools (calipers, micrometers, fillet gauges, protractors)
- Material science and metallurgy fundamentals, particularly for various metals and alloys
- Documentation and report writing for inspection findings and compliance records
- Knowledge of quality control and quality assurance principles in fabrication
- Experience with weld discontinuity identification and evaluation
- Understanding of preheat, interpass, and post-weld heat treatment requirements
Soft Skills
- Attention to Detail: Essential for meticulously identifying defects, ensuring compliance with specifications, and preventing costly failures.
- Ethical Judgment: Crucial for maintaining impartiality and integrity during inspections, ensuring safety and quality standards are upheld without compromise.
- Problem-Solving: Important for diagnosing the root causes of welding discrepancies and recommending corrective actions to achieve compliance.
- Technical Communication: Necessary for clearly documenting findings, writing comprehensive inspection reports, and explaining complex technical issues to welders, engineers, and clients.
- Decision-Making: Required for making critical judgments on weld quality, acceptance, or rejection based on complex code requirements and visual evidence.
- Organizational Skills: Important for managing multiple inspection tasks, maintaining thorough records, and prioritizing work efficiently on job sites.
- Adaptability: Essential for navigating diverse welding environments, varying project specifications, and different industry codes and standards.
- Safety Awareness: Paramount for identifying potential hazards during inspections and ensuring all procedures comply with safety regulations for self and others on site.
How to Become a Welding Inspector
Becoming a Welding Inspector involves a blend of technical knowledge, practical experience, and specific certifications. While a traditional four-year degree is not typically required, vocational training and industry-recognized certifications are crucial. You can enter this field directly from a welding background, transition from a related trade, or begin with specialized inspection training.
The timeline for entry varies significantly; someone with prior welding experience might achieve certification and find a role within 6-12 months, while a complete beginner might need 1-2 years to gain foundational skills and necessary certifications. Entry strategies also differ by industry: oil and gas, construction, manufacturing, and aerospace each have specific demands and often prefer certain certifications. Larger corporations might have more structured training programs, whereas smaller firms might expect candidates to arrive fully certified.
Networking within the welding and inspection communities is vital; attending trade shows, joining professional organizations like the American Welding Society (AWS), and connecting with experienced inspectors can open doors. Breaking into this field requires a strong commitment to continuous learning and meticulous attention to detail. Your certifications and practical understanding of welding processes will be your primary assets.
Step 1
Step 2
Step 3
Step 4
Step 5
Step 6
Education & Training Needed to Become a Welding Inspector
Becoming a Welding Inspector requires a blend of theoretical knowledge and practical experience, often validated through specific certifications rather than traditional degrees. While a 4-year engineering degree (costing $40k-$100k+) can provide a strong foundation, it is not typically a direct prerequisite for this role. Many successful inspectors start with vocational training or an associate's degree in welding technology (costing $5k-$20k over 1-2 years), followed by extensive hands-on welding experience.
Alternative pathways, such as specialized welding inspection courses and certifications, are more common and highly regarded. These programs typically range from 1 to 6 months and cost between $2,000 and $10,000, depending on the scope and included examinations. Employers highly value industry-specific certifications, such as those from the American Welding Society (AWS), which demonstrate a standardized level of competency. Self-study combined with on-the-job training can also lead to certification eligibility, though this path often takes 6-18 months of dedicated effort.
Continuous learning remains crucial for Welding Inspectors. Staying updated on new welding processes, materials, and codes through workshops and advanced certifications is essential for career progression. Practical experience holds significant weight; many certification bodies require a certain number of years of relevant work experience before candidates can sit for their exams. The specific educational needs vary by the industry (e.g., oil and gas, aerospace) and the complexity of projects, with highly specialized roles often demanding more advanced certifications and a deeper theoretical understanding.
Welding Inspector Salary & Outlook
Compensation for a Welding Inspector is influenced by multiple factors beyond just base salary. Geographic location significantly affects earnings, with higher salaries typically found in regions with robust manufacturing, oil and gas, or construction industries and a higher cost of living, such as the Gulf Coast or parts of the Northeast United States. International markets also present variations, with figures often benchmarked against USD.
Years of experience, specific certifications (e.g., AWS CWI, API, ASNT), and specialized knowledge in areas like NDT methods or specific material types create dramatic salary variations. Total compensation packages often include overtime pay, per diem for travel, project bonuses, and comprehensive benefits like health insurance, retirement contributions, and professional development allowances for maintaining certifications.
Industry-specific compensation trends drive salary growth; for instance, roles in aerospace or nuclear power often command premium compensation due to stringent quality requirements. Remote work is less common for this role due to the hands-on nature of inspections, but project-based travel or temporary assignments can offer enhanced pay. Salary negotiation leverage comes from possessing in-demand certifications, a clean inspection record, and proven expertise in complex welding codes.
Salary by Experience Level
Level | US Median | US Average |
---|---|---|
Junior Welding Inspector | $55k USD | $60k USD |
Welding Inspector | $70k USD | $75k USD |
Senior Welding Inspector | $85k USD | $90k USD |
Lead Welding Inspector | $100k USD | $105k USD |
Chief Welding Inspector | $118k USD | $125k USD |
Market Commentary
The job market for Welding Inspectors remains stable, driven by continuous infrastructure development, energy sector demands, and manufacturing quality control needs. Projections indicate a steady demand, with the Bureau of Labor Statistics forecasting growth for quality control inspectors, which includes Welding Inspectors, to be around 2% over the next decade. This growth is primarily influenced by aging infrastructure requiring maintenance and new construction projects.
Emerging opportunities for Welding Inspectors include roles in renewable energy projects, such as wind turbine fabrication and maintenance, and specialized inspections for advanced materials. Technological changes, like the increasing use of automated welding and inspection technologies, require inspectors to adapt and understand these new processes, potentially creating hybrid roles that combine traditional inspection with data analysis.
The supply and demand dynamics show a consistent need for certified and experienced inspectors, particularly those with multiple certifications, as a shortage of highly skilled trades professionals persists. This creates a favorable environment for qualified candidates. This profession is relatively recession-resistant due to ongoing safety regulations and quality assurance requirements across various industries, regardless of economic cycles. Geographic hotspots for employment include industrial centers in Texas, Louisiana, California, and the Midwest, with increasing opportunities in states investing heavily in infrastructure and energy.
Welding Inspector Career Path
Career progression for a Welding Inspector involves a clear path from foundational knowledge to specialized expertise and leadership. Advancement hinges on accumulating practical experience across diverse projects, gaining certifications, and demonstrating an unwavering commitment to quality and safety standards. The field offers both individual contributor (IC) tracks, where inspectors deepen their technical specialization, and management/leadership tracks, where they oversee teams and strategic initiatives.
Advancement speed is influenced by factors such as the complexity of projects undertaken, the industry sector (e.g., oil and gas, aerospace, construction), and the acquisition of advanced certifications like AWS CWI, CSWIP, or API credentials. Larger corporations or specialized consulting firms often present more structured advancement opportunities compared to smaller operations. Lateral moves might involve transitioning between different material types, inspection methods, or industry applications, broadening an inspector's versatility.
Networking within professional organizations, engaging with industry standards committees, and seeking mentorship from seasoned inspectors are crucial for career growth. Developing a reputation for precision and integrity opens doors to more challenging and impactful roles. Continuous learning, adapting to new welding technologies, and understanding evolving regulatory landscapes are essential for sustained progression and for navigating potential career pivots into related fields like quality assurance management or NDT specialization.
Junior Welding Inspector
0-2 yearsKey Focus Areas
Welding Inspector
2-5 yearsKey Focus Areas
Senior Welding Inspector
5-8 yearsKey Focus Areas
Lead Welding Inspector
8-12 yearsKey Focus Areas
Chief Welding Inspector
12+ years total experienceKey Focus Areas
Junior Welding Inspector
0-2 yearsPerform basic visual inspections of welded components under direct supervision. Identify common welding discontinuities and document findings according to established procedures. Assist senior inspectors in preparing inspection reports and maintaining quality control records. Work primarily on less complex projects with clear guidelines.
Key Focus Areas
Develop a strong understanding of various welding processes, metallurgy fundamentals, and common welding defects. Focus on mastering visual inspection techniques and interpreting welding symbols. Acquire initial certifications like AWS Certified Welding Inspector (CWI) or equivalent national standards. Build foundational knowledge of relevant codes and specifications.
Welding Inspector
2-5 yearsConduct comprehensive visual and non-destructive testing (NDT) inspections on a wide range of welded structures and components. Independently assess weld quality against applicable codes, standards, and client specifications. Prepare detailed inspection reports, identify non-conformances, and recommend corrective actions. Collaborate with welders and engineers to resolve quality issues.
Key Focus Areas
Deepen expertise in specific NDT methods (e.g., PT, MT, UT, RT interpretation) and their application to welding inspection. Enhance knowledge of advanced material science and fracture mechanics. Develop strong report writing skills and the ability to interpret complex engineering drawings. Consider specialized certifications for specific industries or techniques.
Senior Welding Inspector
5-8 yearsLead and manage inspection activities for critical or large-scale projects. Oversee a team of junior and mid-level inspectors, ensuring adherence to project specifications and quality standards. Perform advanced and specialized inspections, including complex fabrication and repair assessments. Serve as a technical expert, making critical decisions regarding weld acceptance or rejection.
Key Focus Areas
Cultivate strong analytical and problem-solving skills for complex weld failures and root cause analysis. Develop project management capabilities, including scheduling inspections and resource allocation. Mentor junior inspectors and provide technical guidance. Pursue advanced certifications (e.g., API 510, 570, 653) relevant to specific industry segments.
Lead Welding Inspector
8-12 yearsManage multiple inspection projects or a significant departmental inspection program. Develop and implement inspection procedures, quality control plans, and safety protocols. Provide expert technical consultation to clients, project managers, and engineering teams. Responsible for training and professional development of inspection staff. Contribute to bidding and proposal processes for new projects.
Key Focus Areas
Develop strong leadership and team management skills, including conflict resolution and performance evaluation. Enhance communication skills for interacting with clients, regulatory bodies, and senior management. Focus on strategic planning for inspection programs and continuous improvement initiatives. Gain proficiency in quality management systems (ISO 9001, API Q1).
Chief Welding Inspector
12+ years total experienceOversee all welding inspection operations and quality assurance functions across an organization or major business unit. Establish and enforce company-wide welding and inspection standards and policies. Manage departmental budgets, resources, and personnel. Liaise with executive leadership, clients, and regulatory agencies to ensure compliance and uphold quality reputation. Drive strategic initiatives for technological adoption and process optimization.
Key Focus Areas
Master organizational leadership, strategic planning, and business development. Develop strong financial acumen for budget management and cost control within the inspection department. Cultivate industry thought leadership through participation in standards bodies, conferences, and publications. Focus on innovation in inspection technologies and methodologies.
Job Application Toolkit
Ace your application with our purpose-built resources:
Welding Inspector Cover Letter Examples
Personalizable templates that showcase your impact.
View examplesWelding Inspector Job Description Template
Ready-to-use JD for recruiters and hiring teams.
View examplesGlobal Welding Inspector Opportunities
Welding Inspectors ensure quality and safety in diverse industries like oil & gas, construction, and manufacturing globally. This profession has high international demand, especially in developing infrastructure and energy projects. Regulatory standards and codes vary significantly by country, requiring inspectors to adapt to different local requirements. Many professionals consider international opportunities for higher pay and diverse project experience. International certifications such as CSWIP or AWS CWI facilitate global mobility and recognition.
Global Salaries
Welding Inspector salaries vary widely across global markets due to demand, cost of living, and industry. In North America, particularly the United States and Canada, annual salaries range from USD 70,000 to USD 120,000 for experienced inspectors. These figures reflect a high demand in the energy and aerospace sectors. In Europe, countries like Germany and the UK offer salaries between EUR 50,000 and EUR 85,000 (approximately USD 55,000 to USD 95,000), with variations based on industrial hubs.
Asia-Pacific markets, including Australia and Singapore, provide strong compensation, often USD 60,000 to USD 100,000, driven by large-scale construction and mining projects. Middle Eastern countries, notably Saudi Arabia and UAE, frequently offer tax-free salaries from USD 80,000 to USD 130,000, plus benefits like housing and transport allowances, making them highly attractive. Latin America, such as Brazil and Mexico, typically sees lower ranges, about USD 30,000 to USD 60,000, influenced by local economic conditions and purchasing power.
Salary structures also differ; some regions include comprehensive health and retirement benefits, while others might offer higher base pay with fewer perks. Tax implications significantly affect take-home pay; for example, high-income tax rates in some European countries contrast with tax-free Middle Eastern earnings. International experience and advanced certifications like API or NDT Level III enhance compensation, reflecting specialized expertise and broader project capabilities.
Remote Work
Welding Inspector roles inherently involve on-site physical inspections, significantly limiting traditional remote work. Digital nomad opportunities are minimal for this profession. However, some aspects, like documentation review, report writing, and quality management system audits, can be performed remotely. This partial remote capability depends on employer policies and specific project phases.
For international teams, time zone differences pose challenges for real-time collaboration on project updates. Companies hiring internationally for this role typically require relocation for the on-site component. Salary expectations for the limited remote tasks would generally align with the country where the work is performed or the company is based. Equipment needs include specialized software for report generation and secure access to project documentation, beyond standard office setups.
Visa & Immigration
Welding Inspectors seeking international roles typically apply for skilled worker visas. Popular destinations like Canada, Australia, and the UK have specific points-based immigration systems that favor skilled trades. The US offers H-1B visas, though competition is high, or L-1 visas for intra-company transfers. Middle Eastern countries often sponsor employment visas directly through the hiring company.
Education credential recognition is crucial; professional licensing or certification (e.g., AWS CWI, CSWIP) is often mandatory. Some countries require specific local certifications or additional training. Visa timelines vary from a few weeks to several months, depending on the country and visa type. Language requirements, such as IELTS for English-speaking countries, are common. Pathways to permanent residency exist in many nations, often after several years of skilled employment.
Profession-specific advantages may include inclusion on national occupation lists due to skill shortages. Practical considerations involve securing family visas for dependents, which typically follow the primary applicant's visa. Candidates must also prepare for medical examinations and police clearance certificates as part of the application process.
2025 Market Reality for Welding Inspectors
Understanding the current market realities for welding inspectors is crucial for career planning. The landscape has shifted significantly since 2023, influenced by post-pandemic supply chain adjustments and evolving industrial demands. Broader economic factors, such as interest rates and infrastructure spending, directly impact project pipelines and, consequently, the need for inspectors.
Market conditions vary by experience level; seasoned inspectors with specialized certifications often find more stable opportunities than entry-level candidates. Geographic location plays a major role, with demand concentrated in industrial hubs. Company size also matters, as large engineering firms or energy companies may offer different stability and growth paths compared to smaller fabrication shops. This analysis provides an honest assessment to help you navigate these complexities.
Current Challenges
Welding inspectors face increased competition, particularly for entry-level roles, as some sectors experience slower growth. Economic uncertainty in manufacturing and construction can lead to fewer project starts, reducing demand. Maintaining up-to-date certifications and adapting to new inspection technologies also presents an ongoing challenge for career longevity.
Growth Opportunities
Despite market fluctuations, strong opportunities exist for welding inspectors with specialized skills and certifications. Industries such as renewable energy (wind turbine fabrication), nuclear power, and advanced manufacturing (e.g., electric vehicle components) are experiencing growth and require highly skilled inspectors. These sectors often demand inspectors with expertise in specific materials or complex welding procedures.
Emerging roles involve quality assurance for robotic welding systems or oversight of additive manufacturing processes, where traditional inspection principles meet cutting-edge technology. Inspectors who cross-train in advanced NDT methods, like eddy current testing or digital radiography, gain a significant competitive edge. Underserved markets might include regions with new industrial development or specialized fabrication needs where certified professionals are scarce.
Market corrections can create opportunities for inspectors willing to relocate or specialize in resilient sectors. Pursuing additional certifications from organizations like API (American Petroleum Institute) or ASNT (American Society for Nondestructive Testing) can unlock higher-paying roles and greater job security. Focusing on niche areas within construction or energy, where quality control is paramount, offers strategic career advantages.
Current Market Trends
Demand for welding inspectors remains steady in critical infrastructure, energy, and aerospace, driven by stringent safety and quality standards. However, the broader manufacturing and construction sectors show varied hiring patterns. Some regions with heavy industrial activity, like the Gulf Coast or parts of the Midwest, see consistent opportunities, while others experience slower growth.
Technological advancements, including automated welding processes and advanced non-destructive testing (NDT) methods like phased array ultrasonics, are reshaping the inspector's role. Inspectors now need proficiency in interpreting data from these advanced systems, moving beyond traditional visual inspection. Generative AI is not directly impacting the inspection process yet, but AI-powered image recognition tools for defect detection are emerging, potentially augmenting or streamlining some visual inspection tasks in the future.
Employer requirements increasingly emphasize a blend of hands-on experience and advanced certifications (e.g., AWS CWI, API, ASNT NDT Level II). Companies seek inspectors who understand both the practicalities of welding and the intricacies of relevant codes and standards. Salary growth is moderate, reflecting a stable but not rapidly expanding market, with higher compensation for specialized certifications or roles in high-demand industries like nuclear or oil and gas. Remote work is generally not applicable for this hands-on role.
Emerging Specializations
Technological advancements and evolving industry standards are continuously reshaping the landscape for Welding Inspectors, creating novel specialization opportunities. Understanding these shifts and positioning oneself early in emerging areas is crucial for career advancement in 2025 and beyond.
New technologies, such as advanced robotics, artificial intelligence, and non-destructive testing innovations, are driving demand for inspectors with specialized knowledge. These emerging specializations often command premium compensation and offer accelerated career growth compared to traditional paths. While established specializations remain vital, focusing on cutting-edge areas allows professionals to become leaders in future-oriented fields.
Many emerging areas, particularly those integrating digital technologies, are poised to become mainstream within the next three to five years, creating significant job opportunities. Investing in these skills now offers a substantial advantage. However, pursuing cutting-edge areas involves a balance of risk and reward; while the potential for high demand and compensation is significant, the exact trajectory of these fields can evolve rapidly. Strategic choices are key to navigating these exciting new paths.
Automated Welding Quality Assurance Inspector
Additive Manufacturing Weld Inspector
Renewable Energy Infrastructure Welding Inspector
Extreme Environment Weld Integrity Specialist
Advanced Composite & Hybrid Weld Inspector
Pros & Cons of Being a Welding Inspector
Understanding both the benefits and challenges of a career as a Welding Inspector is crucial for making an informed decision. Career experiences can vary significantly based on the industry sector, the specific company culture, and the inspector's specialization area. For example, working in aerospace inspection differs greatly from pipeline inspection. Additionally, the pros and cons may shift at different career stages; early career inspectors might focus on gaining experience, while senior inspectors might prioritize mentoring or specialized consulting. It is also important to recognize that what one person considers a pro, like extensive travel, another might view as a con, depending on their personal values and lifestyle preferences. This assessment aims to provide a realistic overview to help you set appropriate expectations for this specialized and critical role.
Pros
- Welding inspectors are in consistent demand across various industries, including construction, oil and gas, manufacturing, and aerospace, ensuring strong job security. This wide applicability means opportunities exist in diverse geographical locations.
- The role offers competitive salaries, especially for certified inspectors with specialized skills or experience in high-demand sectors like energy or infrastructure. As experience grows, so does earning potential.
- Welding inspectors play a critical role in ensuring the safety and quality of structures and products, providing a strong sense of purpose and contribution to public safety. This responsibility can be very fulfilling.
- The work is intellectually stimulating, requiring a deep understanding of metallurgy, welding processes, and various codes and standards, fostering continuous learning. Each project presents unique challenges that demand analytical thinking and problem-solving skills.
- Many positions offer opportunities for travel to different sites or projects, which can appeal to individuals who enjoy dynamic work environments and experiencing new locations. This can break the monotony of a typical office job.
- Becoming a certified welding inspector (CWI) is a respected credential that opens doors to international opportunities and specialized roles. This certification provides a clear professional benchmark and recognition within the industry.
- The field offers clear pathways for career advancement, such as becoming a senior inspector, quality control manager, or moving into consulting or training roles. Specialization in areas like non-destructive testing (NDT) can also enhance career prospects.
Cons
- Welding inspectors often work in industrial environments, such as construction sites, fabrication shops, or oil rigs, which can expose them to noise, fumes, and varying weather conditions. This can be physically demanding and potentially hazardous if safety protocols are not strictly followed.
- The role requires extensive knowledge of welding processes, codes, and standards, demanding continuous learning and certification renewals to stay current with industry changes and new technologies. This ongoing educational commitment can be time-consuming and costly.
- Inspections can be repetitive, involving detailed visual checks, measurements, and documentation of welds, which might lead to monotony for some individuals. The focus on minute details requires a high level of concentration for extended periods.
- Travel is frequently required, especially for inspectors working on large projects or across multiple sites, leading to time away from home. This can impact personal life and create logistical challenges.
- The responsibility of ensuring weld integrity means that errors or oversights can have serious safety and financial consequences, placing significant pressure on the inspector. This high-stakes environment demands meticulous attention and a strong ethical compass.
- The job often involves working within strict deadlines, particularly during project phases where inspections are critical path items, which can lead to periods of high pressure and extended hours. Project delays can directly impact an inspector's workload and stress levels.
- Career progression within a purely inspection role can sometimes be limited, primarily moving towards senior inspection roles or specialized areas rather than broad management positions. Those seeking diverse career paths might need to acquire additional skills beyond inspection.
Frequently Asked Questions
Welding Inspectors face distinct challenges ensuring structural integrity and safety across various industries. This section addresses the most common questions about transitioning into this precise role, from mastering inspection codes to navigating the certification process and understanding job demands.
What are the core qualifications and certifications needed to become a Welding Inspector?
Becoming a Certified Welding Inspector (CWI) typically requires a combination of education, experience, and passing a rigorous exam. Most candidates need at least a high school diploma, plus 3-5 years of practical welding experience. Without direct welding experience, a two-year engineering technology degree may reduce the experience requirement. The American Welding Society (AWS) CWI certification is the industry standard.
How long does it realistically take to become a certified Welding Inspector from scratch?
The timeline to become a CWI varies. If you have the required experience, preparing for and passing the AWS CWI exam can take 3-6 months of focused study, often involving a preparatory course. For those starting with no experience, gaining the necessary welding background could take 3-5 years before even beginning exam preparation. It is a multi-year commitment for most.
What are the typical salary expectations for a Welding Inspector, both entry-level and experienced?
Entry-level Welding Inspectors can expect salaries ranging from $50,000 to $70,000 annually, depending on location, industry, and specific certifications. Experienced CWIs with specialized endorsements and a strong track record can earn $80,000 to $120,000 or more. Compensation often includes benefits, and project-based work might offer higher hourly rates.
What is the typical work-life balance like for a Welding Inspector, considering travel and project demands?
Work-life balance for a Welding Inspector can vary significantly based on the industry and project. Some roles involve consistent 40-hour weeks, while others require extensive travel, irregular hours, and overtime, especially in construction or pipeline projects. Flexibility is key, as inspections often occur during critical project phases, sometimes on weekends or nights. This role often involves field work rather than a desk job.
How is the job security and market demand for Certified Welding Inspectors?
Job security for Welding Inspectors remains strong due to the critical need for quality assurance in infrastructure, energy, manufacturing, and construction. As long as welding is a primary joining method, skilled inspectors will be in demand to ensure safety and compliance. Economic downturns might slow some projects, but the fundamental need for inspection persists.
What are the common career growth paths and opportunities for advancement as a Welding Inspector?
Career growth for a CWI often involves specializing in specific inspection methods (e.g., NDT techniques), gaining additional certifications (like Senior CWI or specialized industry endorsements), or moving into management roles such as Quality Control Manager or Project Manager. Some inspectors transition into consulting or training. Continuous learning is essential for advancement.
Is remote work a realistic option for a Welding Inspector, or is it primarily an on-site role?
While some administrative tasks can be done remotely, the core function of a Welding Inspector requires on-site presence to visually inspect welds, witness tests, and verify procedures. Therefore, this is not a remote-first career. Hybrid models might exist for senior roles involving documentation or project planning, but regular travel to job sites is fundamental.
What are the biggest challenges or common frustrations faced by Welding Inspectors?
The biggest challenges often include staying current with evolving codes and standards, managing tight project deadlines, and effectively communicating non-conformances without causing conflict. Inspectors must also maintain impeccable attention to detail and withstand various environmental conditions on job sites. The role demands strong technical knowledge and interpersonal skills.
Related Careers
Explore similar roles that might align with your interests and skills:
Certified Welding Inspector
A growing field with similar skill requirements and career progression opportunities.
Explore career guideStructural Welder
A growing field with similar skill requirements and career progression opportunities.
Explore career guideWelder
A growing field with similar skill requirements and career progression opportunities.
Explore career guideWelding Engineer
A growing field with similar skill requirements and career progression opportunities.
Explore career guideWelding Supervisor
A growing field with similar skill requirements and career progression opportunities.
Explore career guideAssess your Welding Inspector readiness
Understanding where you stand today is the first step toward your career goals. Our Career Coach helps identify skill gaps and create personalized plans.
Skills Gap Analysis
Get a detailed assessment of your current skills versus Welding Inspector requirements. Our AI Career Coach identifies specific areas for improvement with personalized recommendations.
See your skills gapCareer Readiness Assessment
Evaluate your overall readiness for Welding Inspector roles with our AI Career Coach. Receive personalized recommendations for education, projects, and experience to boost your competitiveness.
Assess your readinessSimple pricing, powerful features
Upgrade to Himalayas Plus and turbocharge your job search.
Himalayas
Himalayas Plus
Himalayas Max
Find your dream job
Sign up now and join over 100,000 remote workers who receive personalized job alerts, curated job matches, and more for free!
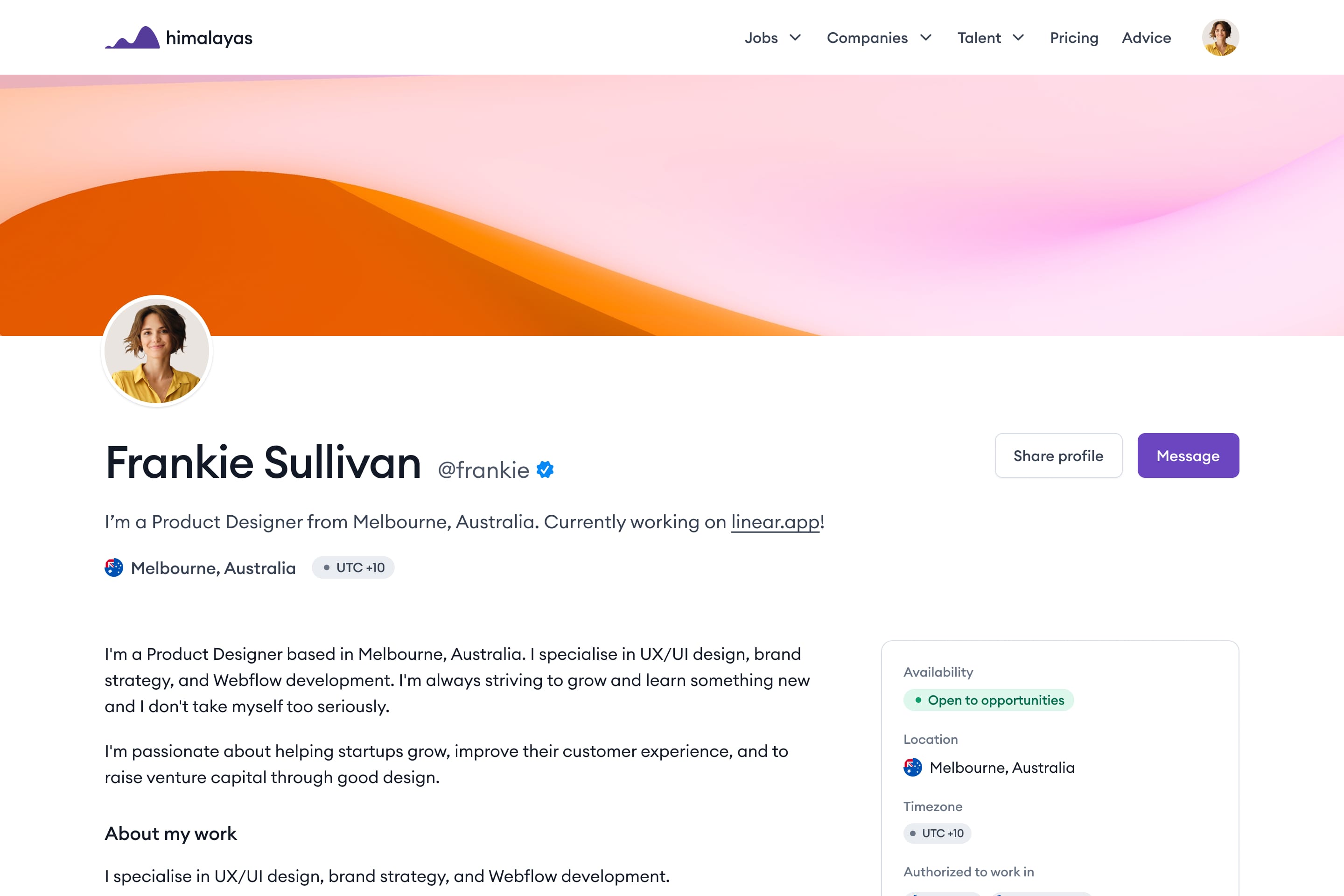