Complete Welder Career Guide
Welders are the backbone of modern construction and manufacturing, fusing metal components to build everything from skyscrapers and bridges to spacecraft and pipelines. This hands-on career offers a tangible impact, creating durable structures and products essential to our infrastructure and economy. If you enjoy precision work, problem-solving, and seeing your efforts come to life, welding offers a rewarding path with consistent demand.
Key Facts & Statistics
Median Salary
$48,930 USD
(U.S. Bureau of Labor Statistics, May 2022)
Range: $36k - $70k+ USD, with highly specialized or experienced welders earning more
Growth Outlook
2%
as fast as average (U.S. Bureau of Labor Statistics, 2022-2032)
Annual Openings
≈42,300
openings annually (U.S. Bureau of Labor Statistics, 2022-2032)
Top Industries
Typical Education
High school diploma or equivalent; postsecondary training from a technical school or community college is common, leading to certifications (e.g., AWS Certified Welder)
What is a Welder?
A Welder is a skilled tradesperson who uses specialized equipment to join metal parts together through the application of heat, pressure, or both. Their primary function involves melting and fusing metals, creating strong, durable bonds for structures, products, and repairs. This role requires precision, an understanding of metallurgy, and strict adherence to safety standards.
Unlike a fabricator who focuses on cutting, shaping, and assembling metal components, or a metalworker who might perform a broader range of metal-shaping tasks, a welder specializes specifically in the fusion process. Welders are critical to industries ranging from automotive and aerospace to construction and infrastructure, ensuring the structural integrity and functionality of countless metal assemblies.
What does a Welder do?
Key Responsibilities
- Interpret blueprints, schematics, and welding symbols to understand project requirements and material specifications.
- Set up and operate welding equipment, including adjusting voltage, amperage, and gas flow for various welding processes.
- Perform arc, MIG, TIG, and other welding techniques to join metal components accurately and cleanly.
- Inspect finished welds for quality, ensuring they meet structural integrity, cosmetic standards, and safety regulations.
- Clean and prepare metal surfaces by grinding, cutting, or filing before and after the welding process.
- Maintain welding equipment and perform minor repairs to ensure optimal functionality and safety.
- Adhere strictly to safety protocols, including wearing protective gear and maintaining a clean work area to prevent hazards and injuries.
Work Environment
Welders typically work in industrial settings such as fabrication shops, construction sites, manufacturing plants, and shipyards. The environment often involves exposure to heat, sparks, fumes, and loud noises. Safety is paramount, requiring strict adherence to protocols and the use of protective gear.
The work can be physically demanding, involving bending, kneeling, and lifting heavy materials. Welders often work independently on specific tasks but also collaborate with other tradespeople like fitters and fabricators to complete larger projects. Schedules are generally full-time, with possibilities for overtime, especially in project-driven industries. While some shop work offers a consistent pace, field work can be highly variable and project-dependent.
Tools & Technologies
Welders primarily use a range of specialized equipment, including arc welding machines (SMAW), MIG welders (GMAW), and TIG welders (GTAW), each suited for different materials and precision levels. They also operate plasma cutters, oxy-acetylene torches, and grinders for metal preparation and finishing. Essential personal protective equipment includes welding helmets, gloves, flame-resistant clothing, and safety glasses.
Beyond the core welding tools, welders utilize hand tools like hammers, clamps, and measuring tapes. They also work with various types of electrodes, welding wires, and shielding gases such as argon or carbon dioxide. Knowledge of specific metal types like stainless steel, aluminum, and carbon steel is crucial, as is the ability to read blueprints and technical drawings.
Welder Skills & Qualifications
Becoming a successful welder involves a blend of formal training and hands-on experience. Employers prioritize practical skills and certifications, often more than a traditional degree. Requirements vary significantly by the type of welding, industry, and project complexity. For instance, structural welding in construction demands different certifications and safety protocols than precision welding in aerospace or pipeline welding, which often requires extensive travel and specialized certifications.
Entry-level positions often require completion of a vocational program or an apprenticeship. More advanced or specialized roles, such as pipe welders or those working with exotic metals, demand extensive experience, advanced certifications, and a proven track record. The balance between formal education and practical experience shifts with seniority; while a basic certificate gets you started, years of diverse project experience and continuous skill refinement are essential for career progression.
The welding skill landscape is continuously evolving with new materials, automation, and advanced techniques like robotic welding. Welders must commit to lifelong learning to remain competitive. Certifications from organizations like the American Welding Society (AWS) are crucial across all levels, validating specific proficiencies and opening doors to higher-paying and more complex jobs. These certifications often carry more weight than academic degrees in this trade.
Education Requirements
Technical Skills
- Shielded Metal Arc Welding (SMAW) - Stick Welding
- Gas Metal Arc Welding (GMAW) - MIG Welding
- Gas Tungsten Arc Welding (GTAW) - TIG Welding
- Flux-Cored Arc Welding (FCAW)
- Oxy-Acetylene Cutting and Brazing
- Blueprint and Schematic Reading
- Welding Machine Operation and Maintenance
- Metal Fabrication and Fitting
- Welding Inspection and Quality Control (e.g., visual inspection, basic destructive/non-destructive testing)
- Material Science Knowledge (understanding properties of various metals like steel, aluminum, stainless steel)
- Safety Protocols and Personal Protective Equipment (PPE) Usage
- Grinding and Finishing Techniques
Soft Skills
- Attention to Detail: Welders must produce precise, high-quality welds to meet structural integrity and aesthetic standards, where even small imperfections can compromise safety or function.
- Problem-Solving: Diagnosing issues with equipment, materials, or joint preparation and finding effective solutions to achieve proper weld characteristics is critical.
- Safety Consciousness: Working with extreme heat, sparks, and heavy materials requires constant vigilance and adherence to strict safety protocols to prevent injuries.
- Physical Stamina and Dexterity: Holding awkward positions, lifting materials, and performing repetitive tasks for extended periods requires significant physical endurance and fine motor control.
- Patience and Persistence: Mastering complex welding techniques and troubleshooting difficult welds demands patience and the ability to persevere through challenging tasks.
- Adaptability: Welders often work in varied environments (indoors, outdoors, confined spaces) and with different materials and equipment, requiring constant adjustment to new conditions.
- Blueprint Reading Comprehension: Interpreting complex technical drawings and specifications is essential for understanding project requirements and executing welds correctly.
- Team Collaboration: Welders often work as part of a larger construction or manufacturing team, requiring effective communication and coordination with other tradespeople and supervisors for project success and safety.
How to Become a Welder
Breaking into welding offers multiple entry points, from formal apprenticeships to vocational training, and even self-taught foundational skills. The most direct and often preferred route involves completing a certified welding program or an apprenticeship, which provides hands-on experience and industry-recognized credentials. While a two-year associate degree offers broader technical knowledge, many employers prioritize practical skills gained through shorter certificate programs or on-the-job training.
Timeline expectations vary significantly; a dedicated individual might complete a basic certification in 3-6 months, while an apprenticeship can span 3-5 years, offering paid work experience alongside structured learning. Geographic demand also plays a role; industrial hubs and regions with significant infrastructure projects often have higher demand and better-paying opportunities compared to smaller, rural areas. Company size matters too; large construction firms or manufacturing plants may prefer certified welders, while smaller fabrication shops might be more open to entry-level candidates with strong foundational skills and a willingness to learn.
A common misconception is that welding only involves basic stick welding; in reality, the field encompasses diverse processes like MIG, TIG, and Flux-Cored Arc Welding, each with specific applications and skill requirements. Building a strong portfolio of projects, even personal ones, can significantly boost a candidate's appeal, especially for those without extensive formal experience. Networking with experienced welders and local fabrication shop owners can open doors to mentorship and job opportunities not advertised publicly. Overcoming entry barriers often involves demonstrating reliability, a strong work ethic, and a commitment to safety, alongside continuous skill development.
Step 1
Step 2
Step 3
Step 4
Step 5
Step 6
Step 7
Education & Training Needed to Become a Welder
Becoming a welder involves several distinct educational pathways. Formal degree programs, like Associate of Applied Science (AAS) degrees in Welding Technology, typically take two years and can cost between $10,000 and $30,000 at community colleges. These programs provide a strong theoretical foundation alongside extensive practical skills, covering various welding processes, metallurgy, and blueprint reading. Graduates often find roles in specialized or industrial welding applications.
Shorter, intensive welding bootcamps or vocational training programs offer a faster route, ranging from 12 to 36 weeks and costing $5,000 to $15,000. These programs focus heavily on hands-on skill development for specific welding types, such as TIG, MIG, or Stick welding. While they provide quicker entry into the workforce, they may offer less theoretical depth than degree programs. Employers generally value certifications from recognized bodies like the American Welding Society (AWS), often obtained through these shorter programs.
Self-study combined with apprenticeship or on-the-job training is another viable path, though it requires significant self-discipline and access to equipment. This route can take 6 to 18 months to gain proficiency, with costs varying based on material acquisition and potential certification exam fees. Continuous learning remains critical in welding; advanced certifications in specialized techniques or inspections lead to higher-paying roles. Practical experience is paramount, with employers prioritizing demonstrated skill and safety knowledge regardless of the initial educational path.
Welder Salary & Outlook
Welder compensation varies significantly based on several factors beyond just the base hourly wage. Geographic location plays a major role; for example, areas with high demand for skilled trades, like industrial hubs or regions with significant infrastructure projects, often offer higher pay to attract talent. Cost of living in these areas also influences salary adjustments.
Years of experience dramatically impact earning potential. Entry-level welders start at foundational rates, but specialists in TIG, MIG, or certified pipe welding command premium wages. Specific certifications, such as ASME or AWS, validate advanced skills and directly increase a welder's market value. Employers frequently offer bonuses for project completion, hazardous duty, or overtime, which can substantially boost total annual income.
Total compensation packages often include more than just salary. Many employers provide comprehensive benefits like health, dental, and vision insurance. Retirement contributions, such as 401(k) matching, add long-term financial security. Some companies also cover costs for professional development, including advanced welding certifications or safety training, enhancing a welder's skill set and career longevity. Remote work is rare for welders, but contract or travel welding roles can offer higher rates, offsetting travel expenses.
Industry-specific trends also drive salary growth. Specialized welding in aerospace, oil and gas, or nuclear facilities typically pays more due to the precision and critical nature of the work. Conversely, general fabrication or manufacturing roles might offer more stable, but lower, pay. Negotiating leverage comes from proven expertise, a strong safety record, and the ability to perform complex, specialized welds. International market variations exist, but the figures provided here are in USD, reflecting the U.S. labor market.
Salary by Experience Level
Level | US Median | US Average |
---|---|---|
Apprentice Welder | $35k USD | $38k USD |
Junior Welder | $42k USD | $45k USD |
Welder | $50k USD | $52k USD |
Senior Welder | $62k USD | $65k USD |
Lead Welder | $72k USD | $75k USD |
Welding Supervisor | $82k USD | $85k USD |
Welding Inspector | $89k USD | $92k USD |
Market Commentary
The job market for Welders shows steady demand, driven by ongoing infrastructure development, manufacturing needs, and energy sector projects. The Bureau of Labor Statistics (BLS) projects a 2% growth for welders, cutters, solderers, and brazers from 2022 to 2032, which translates to about 6,200 new jobs over the decade. This growth is slower than the average for all occupations, but consistent demand ensures job availability for skilled professionals.
Emerging opportunities for welders are often found in specialized areas. Robotic welding and automated processes are becoming more prevalent, requiring welders to adapt to overseeing and programming these systems, rather than solely manual work. This shift creates a need for welders with strong technical and diagnostic skills. Additionally, industries like renewable energy, including wind turbine construction and maintenance, present new avenues for certified welders.
Supply and demand dynamics for skilled welders remain relatively balanced, though specific regions or industries may experience shortages of highly specialized welders. An aging workforce contributes to a consistent need for new talent. Future-proofing a welding career involves continuous learning and adopting new technologies. Proficiency in different welding techniques, combined with an understanding of automation and advanced materials, will be crucial. While automation handles repetitive tasks, complex and custom welding, along with repair work, will always require human expertise.
The profession is generally recession-resistant due to its foundational role in construction, maintenance, and manufacturing. Geographic hotspots for welding jobs include states with robust manufacturing bases, such as Texas, California, Pennsylvania, and Ohio, as well as areas with significant shipbuilding or energy sector activities. Remote work is not applicable for welders, but travel welding contracts can offer higher pay for those willing to relocate temporarily for projects.
Welder Career Path
Career progression for a Welder typically involves a hands-on journey, starting with foundational skills and advancing through specialized expertise and leadership roles. This path often distinguishes between individual contributor (IC) tracks, where a welder deepens their technical mastery, and management/leadership tracks, which involve overseeing teams, projects, or quality assurance.
Advancement speed depends on several factors, including consistent high-quality performance, the acquisition of specialized welding certifications (e.g., ASME, AWS), and the specific industry. For example, welders in aerospace or nuclear power often progress differently than those in general fabrication. Lateral movement might involve shifting between different welding processes (TIG, MIG, Stick) or materials. Company size and type also influence career paths; a welder at a small custom fabrication shop may gain broader experience faster than one at a large manufacturing plant, where specialization is common.
Networking within the trade, seeking mentorship from experienced welders, and maintaining an excellent reputation for precision and reliability are crucial. Milestones include achieving advanced certifications, mastering complex joint configurations, or successfully leading a critical project. Some welders transition into roles like welding instruction, sales of welding equipment, or entrepreneurship by starting their own fabrication businesses, showcasing the diverse pathways available within this skilled trade.
Apprentice Welder
0-2 yearsKey Focus Areas
Junior Welder
2-4 yearsKey Focus Areas
Welder
4-7 yearsKey Focus Areas
Senior Welder
7-10 yearsKey Focus Areas
Lead Welder
10-12 yearsKey Focus Areas
Welding Supervisor
12-15 yearsKey Focus Areas
Welding Inspector
12+ yearsKey Focus Areas
Apprentice Welder
0-2 yearsWorks under direct supervision, primarily assisting experienced welders. Performs basic cuts, grinds, and prepares materials for welding. Executes simple, repetitive welds on non-critical components. Focuses on learning and applying safety procedures rigorously. Tasks are highly structured with clear instructions.
Key Focus Areas
Develop foundational welding techniques across various processes like Stick, MIG, and Flux-Cored. Understand safety protocols, material preparation, and basic blueprint reading. Focus on consistent bead control and joint integrity through repetitive practice and direct supervision. Build a strong work ethic and attention to detail.
Junior Welder
2-4 yearsPerforms routine welding tasks with limited supervision, applying learned techniques to various projects. Responsible for setup and basic maintenance of welding equipment. Contributes to the fabrication or repair of components, ensuring welds meet specified quality standards. Works collaboratively with team members on production goals.
Key Focus Areas
Improve speed and efficiency while maintaining weld quality. Learn to interpret more complex blueprints and welding symbols. Begin to troubleshoot minor equipment issues and understand basic metallurgy. Develop independent problem-solving skills for routine welding tasks. Seek opportunities to work with different materials and joint types.
Welder
4-7 yearsExecutes a wide range of welding tasks on critical components with minimal supervision. Interprets complex schematics and designs. Responsible for ensuring welds meet stringent quality and structural requirements. May specialize in a particular welding process or material. Provides technical input on project planning.
Key Focus Areas
Master multiple welding processes and materials, including specialized alloys. Obtain advanced certifications (e.g., AWS D1.1, D1.6). Develop strong fabrication and assembly skills. Refine problem-solving abilities for complex welding challenges. Start mentoring junior colleagues and contributing to process improvements.
Senior Welder
7-10 yearsServes as a technical expert for complex and critical welding operations. Handles challenging materials, intricate designs, and high-pressure applications. Provides guidance and technical support to other welders, ensuring adherence to quality standards and project specifications. Often involved in quality checks and process validation.
Key Focus Areas
Become an expert in specific welding codes and standards. Develop advanced troubleshooting and diagnostic skills for complex welding issues. Lead efforts in optimizing welding procedures and improving efficiency. Begin to provide technical guidance and training to less experienced welders. Focus on precision and quality control.
Lead Welder
10-12 yearsOversees a small team of welders, coordinating daily welding activities and ensuring project deadlines are met. Assigns tasks, monitors progress, and provides on-the-job training and guidance. Responsible for maintaining a safe work environment and ensuring all welds meet quality specifications. Acts as a primary point of contact for technical questions.
Key Focus Areas
Cultivate strong leadership and communication skills. Learn project coordination and resource allocation. Develop a deeper understanding of production schedules and deadlines. Focus on mentoring a team, delegating tasks effectively, and ensuring overall team productivity and safety compliance. Begin to participate in strategic planning.
Welding Supervisor
12-15 yearsManages a larger team of welders, overseeing multiple projects or a specific production line. Responsible for hiring, training, and performance evaluations. Develops and implements welding procedures, ensuring compliance with industry standards and safety regulations. Collaborates with other departments to achieve production targets and resolve issues.
Key Focus Areas
Enhance managerial and organizational skills, including performance management and conflict resolution. Develop advanced planning and scheduling capabilities. Focus on optimizing workflow, improving team efficiency, and implementing best practices. Understand budgeting and cost control related to welding operations. Pursue leadership training.
Welding Inspector
12+ yearsSpecializes in assessing weld quality and integrity, ensuring compliance with codes, standards, and specifications. Performs visual inspections and coordinates non-destructive testing. Documents inspection findings and recommends corrective actions. Plays a critical role in quality assurance and control, often working independently or leading inspection teams. May conduct audits of welding procedures and welder qualifications.
Key Focus Areas
Obtain advanced certifications in welding inspection (e.g., CWI, CSWIP). Develop expertise in non-destructive testing (NDT) methods like UT, RT, PT, MT. Understand quality management systems and auditing processes. Focus on regulatory compliance, risk assessment, and detailed report generation. Cultivate keen observational and analytical skills.
Job Application Toolkit
Ace your application with our purpose-built resources:
Global Welder Opportunities
Welders find significant global demand across manufacturing, construction, and energy sectors. This profession requires hands-on skill, translating well internationally without major cultural barriers. Countries with strong industrial bases consistently seek skilled welders. International certifications like AWS or ISO 9606 enhance global mobility, making international opportunities appealing for career growth.
Global Salaries
Welder salaries vary significantly by region and specialization. In North America, a skilled welder in the US earns between $45,000 and $70,000 USD annually, while in Canada, ranges are typically $40,000-$65,000 CAD ($30,000-$50,000 USD). These figures reflect high demand in oil & gas or specialized fabrication. European salaries differ; in Germany, a welder might earn €35,000-€55,000 (approx. $38,000-$60,000 USD), reflecting strong social benefits and higher living costs. The UK offers £28,000-£45,000 (approx. $35,000-$56,000 USD).
Asia-Pacific markets like Australia present strong opportunities, with salaries from AUD $60,000-$90,000 (approx. $40,000-$60,000 USD), often higher for specialized roles in mining or heavy industry. Latin American countries generally offer lower base salaries, for example, Mexico at $10,000-$20,000 USD, but purchasing power parity can make these competitive locally. Middle Eastern countries, particularly in the Gulf, offer tax-free salaries from $30,000-$50,000 USD, often including accommodation allowances, attracting many expatriates.
Salary structures also include varying benefits. North America often sees health insurance and retirement plans as part of compensation. European countries frequently provide extensive paid leave and national healthcare. Tax implications significantly affect take-home pay; for instance, high taxes in some European nations contrast with lower or no income tax in Gulf states. International experience and advanced certifications like pipe welding or underwater welding command higher compensation globally.
Remote Work
International remote work for welders is extremely limited due to the hands-on nature of the job. Welding requires physical presence and specialized equipment. Digital nomad opportunities do not apply to this profession. Few, if any, companies hire welders for entirely remote positions.
However, some related roles, such as welding inspectors, welding engineers, or technical trainers, might involve partial remote work for planning, reporting, or curriculum development. These roles still require on-site visits or in-person instruction periodically. Employer policies on international remote work do not generally extend to the direct welding profession.
Visa & Immigration
Skilled welder positions often qualify for skilled worker visas in countries like Canada, Australia, Germany, and the UK. These nations have specific immigration pathways for trades. General requirements include a job offer, relevant experience, and recognized certifications.
Education credential recognition is crucial. Some countries require formal assessments of welding qualifications. Language proficiency tests, such as IELTS for English-speaking countries or Goethe-Zertifikat for Germany, are often mandatory. Typical visa processing times range from a few months to over a year, depending on the country and visa type.
Popular destination countries include Canada (Express Entry), Australia (Skilled Nominated Visa subclass 190, Skilled Independent Visa subclass 189), and Germany (Skilled Immigration Act). These countries often have specific lists of in-demand occupations that include welders. Some programs may offer faster processing for highly specialized welders. Pathways to permanent residency can be available after a period of employment.
2025 Market Reality for Welders
Understanding current market conditions is vital for welders. The landscape for this skilled trade has shifted considerably, especially from 2023 to 2025, influenced by post-pandemic economic adjustments and evolving industrial technologies. Broader economic factors, such as inflation and investment in infrastructure, directly impact project pipelines and, consequently, job availability for welders.
Market realities for welders vary significantly based on experience, specific certifications, and geographic location. A highly experienced welder with specialized certifications in, for example, aerospace or pipeline work, faces a different market than an entry-level general fabricator. This analysis provides an honest assessment of current hiring trends, challenges, and genuine opportunities within the welding profession.
Current Challenges
Welders face increased competition, especially for entry-level fabrication roles, due to automation and a larger pool of candidates seeking stable trade jobs. Economic slowdowns can delay or cancel large construction and infrastructure projects, directly impacting demand for skilled welders. Mismatched skill sets pose a challenge; employers increasingly seek specialized certifications in areas like robotic welding or exotic materials, which many generalists lack. This creates a gap between available jobs and qualified applicants.
Growth Opportunities
Despite challenges, significant opportunities exist for welders with specialized skills. The energy sector, including oil and gas pipelines, nuclear power, and renewable energy infrastructure like wind turbine fabrication, offers consistent demand for certified welders. Specialized roles in aerospace, defense, and shipbuilding also present strong, high-paying prospects due to stringent quality and safety requirements.
Welders can gain a competitive edge by pursuing advanced certifications in processes like TIG welding for precision applications, orbital welding, or robotic welding system operation. Learning to interpret complex digital models and integrate with automated systems provides a distinct advantage, positioning welders for roles that blend traditional craft with modern technology. Underserved markets often include remote industrial sites or regions with new infrastructure development, where companies struggle to find local talent.
Strategic career moves might involve targeting companies investing in advanced manufacturing or those involved in critical infrastructure projects. Acquiring skills in non-destructive testing (NDT) or welding inspection can also open up new career paths. The market favors adaptability and continuous learning, particularly in embracing new materials and automated processes. Investing in specialized training now can unlock higher-paying, more stable opportunities in the long term.
Current Market Trends
Demand for welders remains stable but highly specialized as of 2025, moving away from general fabrication towards niche, high-skill areas. Infrastructure projects and renewable energy installations drive significant demand, particularly for pipefitters and structural welders. However, manufacturing sectors show varied trends; some automation replaces basic welding tasks, while others require welders to program and oversee robotic systems.
Economic conditions present a mixed picture. While some sectors like oil and gas or shipbuilding see robust activity, others tied to residential construction might experience slower growth. This means job availability can fluctuate based on specific industry performance. Generative AI and advanced automation are influencing requirements; welders now need skills in interpreting complex digital blueprints and sometimes operating computer-controlled welding equipment, shifting the role from purely manual to more technical. Employers prioritize certifications in specific processes like TIG or advanced arc welding, alongside a strong safety record.
Salary trends show modest growth for general welders, but significant premiums exist for those with specialized skills, such as underwater welding or aerospace applications. Market saturation appears in basic welding roles, while highly skilled positions remain in short supply. Geographic variations are pronounced; states with heavy manufacturing, energy production, or large infrastructure projects offer better prospects than purely service-based economies. Hiring patterns can also be cyclical, often peaking with construction seasons or major project commencements.
Emerging Specializations
The welding profession is evolving rapidly, driven by advancements in automation, materials science, and digital fabrication. These technological shifts are creating new specialization opportunities that were once unimaginable. Understanding these emerging areas is crucial for welders aiming to position themselves for significant career advancement and premium compensation in 2025 and beyond.
Early positioning in these cutting-edge specializations provides a distinct advantage, allowing professionals to become early experts in high-demand niches. While established welding specializations remain valuable, focusing on emerging fields can unlock greater earning potential and more complex, rewarding projects. This strategic choice balances the stability of traditional skills with the substantial growth potential of new frontiers.
Many emerging areas, particularly those involving advanced robotics or exotic materials, are moving from niche applications to mainstream industry practices. This transition creates a significant number of job opportunities. However, specializing in cutting-edge areas involves a calculated risk: early adoption requires continuous learning and adaptability. The reward, though, is often a role at the forefront of the industry, commanding higher compensation and offering unparalleled career growth.
Robotic Welding Technician
Additive Manufacturing Welder (3D Metal Printing)
Exotic Materials Welder
Underwater Welder
Advanced Weld Inspector (NDT Specialist)
Pros & Cons of Being a Welder
Making informed career decisions requires a thorough understanding of both the benefits and challenges associated with a particular profession. Career experiences can vary significantly based on factors such as company culture, specific industry sector, the specialization area chosen, and individual preferences or personality. The perceived pros and cons may also shift at different career stages, from early entry to mid-career advancement and senior-level roles. It is important to remember that what one person considers an advantage, another might view as a challenge, depending on their personal values and lifestyle priorities. This assessment aims to provide an honest, balanced perspective to help set appropriate expectations for a career as a welder.
Pros
- There is a high demand for skilled welders across various industries, including manufacturing, construction, automotive, and energy, ensuring consistent job opportunities.
- Welders with specialized skills, such as underwater welding or pipeline welding, can command very high salaries, offering strong earning potential as experience grows.
- Welding provides a tangible sense of accomplishment, as welders create and repair structures, vehicles, and products essential to everyday life and industry.
- The trade offers diverse work environments, from large industrial plants to small workshops, allowing welders to choose settings that best suit their preferences.
- Opportunities for career advancement include becoming a welding inspector, supervisor, or instructor, or even starting a specialized welding business.
- Many welding skills are transferable across different industries and geographic locations, providing flexibility and job mobility.
- Becoming a welder often requires vocational training or an apprenticeship rather than a four-year degree, making it a quicker and more affordable path to a skilled trade career.
Cons
- Welding often involves working in hot, noisy, and sometimes cramped environments, which can be physically demanding and uncomfortable over long shifts.
- Exposure to fumes, gases, and intense light requires strict adherence to safety protocols and the consistent use of personal protective equipment to prevent long-term health issues.
- The work can be repetitive and physically taxing, leading to strain, fatigue, and potential musculoskeletal problems over time, especially in production settings.
- Job sites may vary, requiring travel or working outdoors in inclement weather, which adds an unpredictable element to the daily routine.
- Mastering advanced welding techniques takes significant time and practice, and continuous learning is necessary to stay current with new materials and processes.
- Project deadlines can create pressure, requiring welders to work efficiently and sometimes put in extended hours to meet production schedules.
- While skilled welders earn well, entry-level positions or roles in less specialized industries might offer lower starting wages and slower progression until experience is gained, especially without formal certification from a reputable institution or apprenticeship.
Frequently Asked Questions
Welders face distinct challenges balancing precision with physical demands and safety protocols. This section addresses the most common questions about entering this trade, from mastering specific welding processes to understanding job site realities and career progression.
How long does it take to become a certified welder if I'm starting from scratch?
Becoming a job-ready welder typically takes 6 months to 2 years, depending on your chosen path. Vocational schools or community college programs often run for 9-24 months, providing hands-on training and certification preparation. Apprenticeships can last 3-5 years, combining paid on-the-job experience with classroom instruction, leading to a highly skilled status. Self-study combined with practice can also work, but gaining official certification is crucial for employment.
Do I need a college degree to become a successful welder?
No, a four-year degree is not required to become a welder. Most welders gain their skills through vocational training, community college programs, or apprenticeships. Employers prioritize practical welding skills, safety knowledge, and relevant certifications like those from the American Welding Society (AWS). While some advanced roles might benefit from engineering or metallurgy degrees, they are not a prerequisite for entry-level or even experienced welding positions.
What are the typical salary expectations for an entry-level welder versus an experienced one?
Entry-level welders can expect to earn between $35,000 and $45,000 annually, but this varies significantly by location, industry, and specific skills. Experienced and specialized welders, especially those in high-demand fields like pipeline, underwater, or aerospace welding, can earn $60,000 to over $100,000 per year. Overtime opportunities are common and can significantly boost annual income.
How physically demanding is the welding profession, and what are the common work conditions?
Welding can be physically demanding, requiring good hand-eye coordination, steady hands, and the ability to work in various positions for extended periods. It involves lifting, bending, and working in sometimes confined or elevated spaces. While it's a skilled trade that requires precision, physical stamina is also important. Proper safety gear and techniques are essential to mitigate risks associated with heat, fumes, and sparks.
Is welding a secure career path, and what is the job market like for welders?
The job outlook for welders is stable, with consistent demand across various industries including manufacturing, construction, automotive, and energy. Many experienced welders are nearing retirement, creating opportunities for new professionals. The need for skilled welders in infrastructure projects, maintenance, and specialized fabrication ensures ongoing job security. Advanced certifications and experience in specific welding processes increase employability.
What are the opportunities for career advancement and specialization within welding?
Career growth for welders can involve specialization in different welding processes (e.g., TIG, MIG, Stick), materials (e.g., aluminum, stainless steel), or industries (e.g., aerospace, shipbuilding, pipefitting). Welders can advance to roles such as welding inspectors, supervisors, instructors, or even start their own fabrication businesses. Continuing education and advanced certifications are key to unlocking these higher-paying and more responsible positions.
Can welders find remote work opportunities, or is it primarily on-site?
Many welding jobs require working on-site, whether in manufacturing plants, construction sites, or shipyards, which typically means a fixed work location. However, mobile welders, pipeline welders, and those involved in field service or repair often travel extensively. Remote work, in the traditional sense, is not common for hands-on welding roles, but some design or inspection roles might offer more flexibility.
What are the biggest challenges or learning curves for someone new to welding?
The biggest challenges for new welders often include mastering precision and consistency under pressure, adapting to diverse working environments, and strictly adhering to safety protocols. It takes time to build the muscle memory and visual acuity required for high-quality welds. Additionally, understanding different metals and their reactions to heat, along with troubleshooting common welding issues, can be a steep learning curve.
Related Careers
Explore similar roles that might align with your interests and skills:
Mig Welder
A growing field with similar skill requirements and career progression opportunities.
Explore career guideWelder Fabricator
A growing field with similar skill requirements and career progression opportunities.
Explore career guideArc Welder
A growing field with similar skill requirements and career progression opportunities.
Explore career guideWelder Fitter
A growing field with similar skill requirements and career progression opportunities.
Explore career guideWelding Machine Operator
A growing field with similar skill requirements and career progression opportunities.
Explore career guideAssess your Welder readiness
Understanding where you stand today is the first step toward your career goals. Our Career Coach helps identify skill gaps and create personalized plans.
Skills Gap Analysis
Get a detailed assessment of your current skills versus Welder requirements. Our AI Career Coach identifies specific areas for improvement with personalized recommendations.
See your skills gapCareer Readiness Assessment
Evaluate your overall readiness for Welder roles with our AI Career Coach. Receive personalized recommendations for education, projects, and experience to boost your competitiveness.
Assess your readinessSimple pricing, powerful features
Upgrade to Himalayas Plus and turbocharge your job search.
Himalayas
Himalayas Plus
Himalayas Max
Find your dream job
Sign up now and join over 100,000 remote workers who receive personalized job alerts, curated job matches, and more for free!
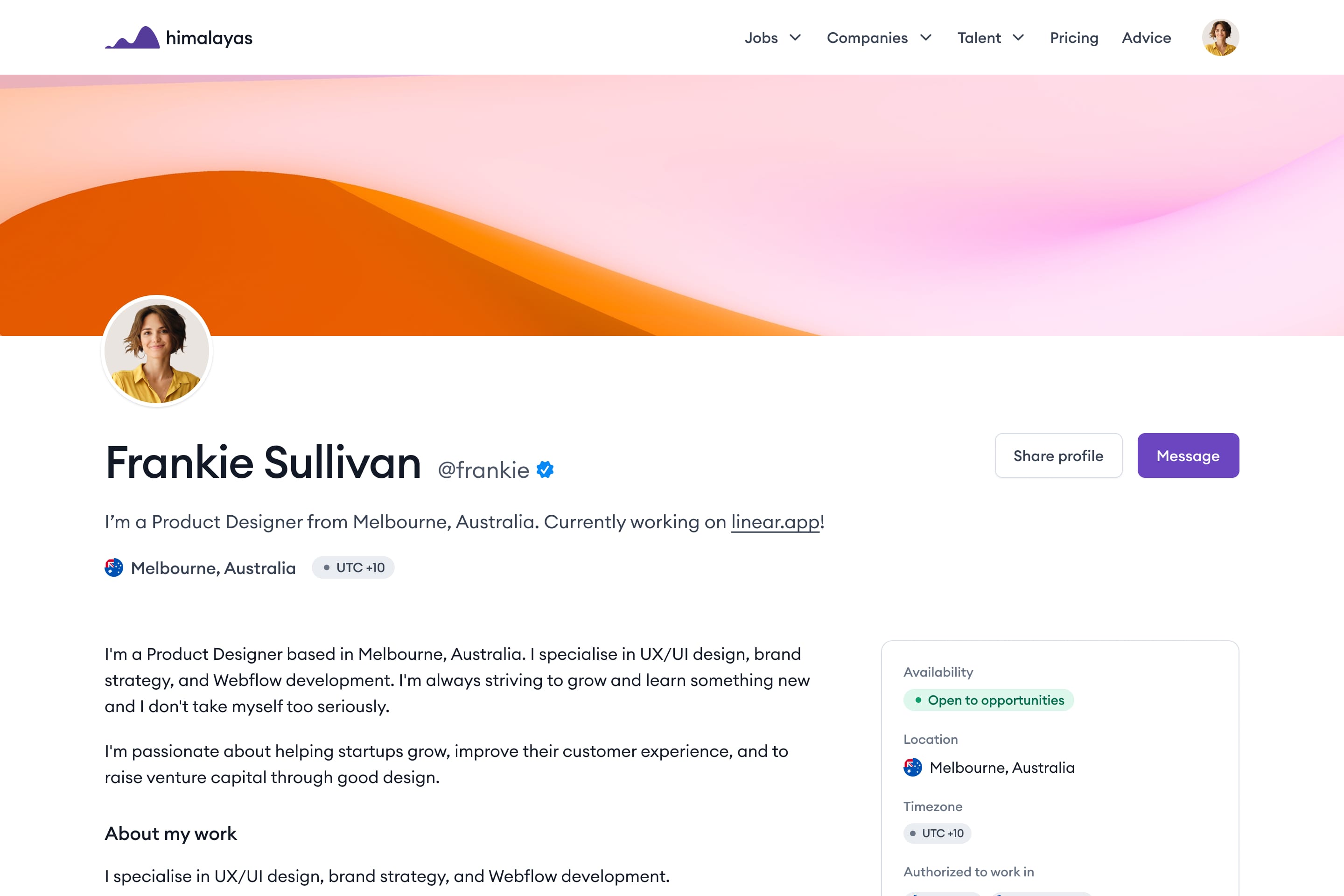