Complete Toolmaker Career Guide
Toolmakers are the precision artisans behind modern manufacturing, crafting and repairing the specialized dies, jigs, and fixtures that enable mass production. This essential role demands exceptional mechanical aptitude, problem-solving skills, and meticulous attention to detail to ensure the accuracy and efficiency of production lines. If you enjoy hands-on work that blends traditional craftsmanship with advanced technology, a career as a Toolmaker offers stable opportunities and a direct impact on product quality.
Key Facts & Statistics
Median Salary
$63,080 USD
(U.S. national median, BLS May 2023)
Range: $40k - $85k+ USD
Growth Outlook
Annual Openings
≈10k
openings annually (BLS)
Top Industries
Typical Education
Postsecondary nondegree award or apprenticeship; some enter with a high school diploma and extensive on-the-job training.
What is a Toolmaker?
A toolmaker is a highly skilled artisan and precision machinist specializing in the design, fabrication, and repair of custom tools, dies, jigs, fixtures, and gauges. These precision components are essential for manufacturing processes, enabling the mass production of parts with accuracy and consistency. Unlike a general machinist who produces individual parts, a toolmaker creates the instruments that other machines use to produce parts, often from raw materials to finished, finely tuned devices.
The core purpose of a toolmaker is to ensure that production lines can operate efficiently and produce high-quality products. This role demands an exceptional understanding of metallurgy, mechanical principles, and extreme precision. They are distinct from production machinists, who focus on operating existing machinery for volume production, and from machine operators, who primarily run automated equipment. Toolmakers are the problem-solvers and innovators behind the manufacturing equipment itself.
What does a Toolmaker do?
Key Responsibilities
- Study blueprints, sketches, or computer-aided design (CAD) files to determine dimensions and tolerances of finished tools, dies, jigs, or fixtures.
- Set up and operate a variety of machine tools, such as lathes, milling machines, grinders, and drill presses, to fabricate metal parts.
- Perform precision grinding, filing, and polishing to ensure components meet exacting specifications and surface finish requirements.
- Inspect finished tools and parts for conformance to specifications, using precision measuring instruments like micrometers, calipers, and optical comparators.
- Assemble and fit components of tools and dies, ensuring proper alignment and function through careful adjustments and testing.
- Troubleshoot and repair malfunctioning tools or dies, identifying the root cause of issues and implementing corrective modifications.
- Maintain and calibrate shop machinery and equipment, ensuring optimal performance and adherence to safety standards.
Work Environment
Toolmakers typically work in manufacturing plants, machine shops, or specialized tool and die shops. The environment is often noisy due to machinery and requires adherence to strict safety protocols, including wearing personal protective equipment like safety glasses and hearing protection. The work involves a mix of standing, bending, and lifting, often requiring physical dexterity.
Collaboration is common, as toolmakers often work closely with engineers, machinists, and production teams to ensure tools meet design and production requirements. The pace can be steady and focused on precision, but may also involve urgent troubleshooting when production lines halt due to tool failures. While largely on-site, some specialized roles might involve occasional travel for installation or repair. Work schedules are generally full-time, often including overtime or shift work to meet production deadlines.
Tools & Technologies
Toolmakers regularly use a wide array of precision machinery and measuring instruments. They operate conventional and CNC (Computer Numerical Control) machine tools, including lathes, milling machines, surface grinders, and electrical discharge machining (EDM) equipment for complex shapes. Proficiency with CAD/CAM (Computer-Aided Design/Manufacturing) software like SolidWorks, AutoCAD, or Mastercam is crucial for design, programming, and simulation.
Essential hand tools include files, chisels, hammers, and various wrenches. Precision measuring devices like micrometers, calipers, height gauges, optical comparators, and coordinate measuring machines (CMMs) are vital for quality control and verification. They also work with a variety of materials, including tool steels, carbides, and non-ferrous metals, often requiring knowledge of heat treatment processes.
Toolmaker Skills & Qualifications
Becoming a successful Toolmaker requires a precise blend of formal training, practical experience, and a specific aptitude for mechanical systems. Employers prioritize hands-on experience and demonstrated proficiency over academic credentials alone, though a strong educational foundation significantly accelerates career progression. Requirements for Toolmakers vary significantly depending on the industry and the complexity of the tools produced.
For entry-level Toolmakers, vocational school diplomas or apprenticeships are often sufficient. Senior or specialized roles, particularly in aerospace, medical device manufacturing, or complex mold making, frequently demand more extensive experience, advanced certifications, and sometimes an associate's degree in a relevant field. Certifications, such as those from the National Institute for Metalworking Skills (NIMS), provide standardized validation of competency and are highly valued across the industry, often demonstrating a 'must-have' level of skill.
The skill landscape for Toolmakers is steadily evolving with the integration of CNC machining, CAD/CAM software, and advanced materials. While traditional manual machining skills remain foundational, proficiency in digital tools is becoming increasingly important for efficiency and precision. Toolmakers must balance deep expertise in specific machining techniques with a broad understanding of manufacturing processes. Alternative pathways, such as military experience in relevant mechanical trades or extensive on-the-job training in a machine shop, are also recognized, particularly when coupled with a strong portfolio of completed work. This role requires continuous learning to adapt to new technologies and materials.
Education Requirements
Technical Skills
- Manual Machining (Lathe, Mill, Grinders): Expert operation of conventional machine tools for precise material removal and finishing.
- CNC Machining (Setup, Operation, Programming): Proficiency in setting up, operating, and basic programming (G-code, M-code) of Computer Numerical Control machines.
- Grinding (Surface, Cylindrical, Jig): Advanced skills in various grinding techniques for achieving high precision and fine surface finishes.
- Tool and Die Design Principles: Understanding of design concepts for stamping dies, plastic injection molds, and other specialized tooling.
- CAD/CAM Software (e.g., SolidWorks, AutoCAD, Mastercam): Ability to read and interpret digital models, and potentially generate toolpaths.
- Metrology and Inspection Tools: Proficient use of precision measuring instruments such as micrometers, calipers, height gauges, CMMs (Coordinate Measuring Machines), and optical comparators.
- Heat Treatment Processes: Knowledge of various heat treatment methods for metals to achieve desired hardness, strength, and ductility.
- Material Science (Metals, Plastics): Understanding of properties, machinability, and applications of different metals and plastics used in tooling.
- Jig and Fixture Building: Skills in designing and fabricating custom work-holding devices and assembly aids.
- Benchwork and Fitting: Expertise in hand-finishing, assembly, and fine-tuning of intricate tool components.
Soft Skills
- Problem-solving and analytical thinking: Toolmakers frequently diagnose and troubleshoot complex issues with molds, dies, and fixtures, requiring logical deduction to identify root causes and implement effective solutions.
- Attention to detail and precision: The core of a Toolmaker's job is producing components with extremely tight tolerances; even minute errors can render a tool unusable, demanding meticulous focus on every measurement and finish.
- Patience and perseverance: Toolmaking involves intricate, time-consuming processes and often requires multiple iterations to achieve perfection. Successful Toolmakers maintain composure and commitment through challenging projects.
- Mechanical aptitude and spatial reasoning: Understanding how mechanical parts fit together and interact, and being able to visualize complex 3D shapes from 2D blueprints, is fundamental to designing and building effective tools.
- Blueprint reading and interpretation: Toolmakers must accurately translate detailed engineering drawings into physical components, requiring a strong understanding of GD&T (Geometric Dimensioning and Tolerancing) and other drafting conventions.
- Adaptability and continuous learning: The manufacturing industry constantly introduces new materials, machines, and software. Toolmakers must be willing to learn new techniques and technologies to remain effective and competitive.
How to Become a Toolmaker
Becoming a toolmaker involves a blend of traditional craftsmanship and modern manufacturing techniques. This career path is often accessible through apprenticeships, vocational training, or a combination of both, rather than solely relying on a four-year degree. The timeline can vary significantly; a dedicated apprenticeship typically lasts 3-5 years, providing hands-on experience and theoretical knowledge. For those with a related manufacturing background, transitioning might be quicker, potentially requiring specialized certifications or on-the-job training.
Entry strategies for toolmakers can differ based on location and industry. In regions with strong manufacturing sectors, apprenticeships are prevalent and highly competitive. Smaller shops might offer direct entry-level positions with internal training, while larger corporations often prefer candidates with formal certifications or apprenticeship completion. Misconceptions include believing that toolmaking is a dying art; instead, it is evolving with CNC machining and additive manufacturing, requiring continuous learning and adaptation to new technologies.
Building industry connections through vocational schools, professional organizations, and trade shows is crucial. These networks can lead to mentorship opportunities and job referrals. The hiring landscape values practical skills, precision, and a problem-solving mindset. Overcoming barriers like a lack of initial experience often involves demonstrating a strong mechanical aptitude and a willingness to learn through entry-level roles or pre-apprenticeship programs.
Complete foundational education in machining or manufacturing technology. Enroll in a vocational school, community college, or a pre-apprenticeship program that covers basic machining principles, blueprint reading, metrology, and materials science. This initial step builds the essential theoretical framework for understanding precision manufacturing.
Secure a formal apprenticeship with a reputable machine shop or manufacturing company. Apprenticeships provide structured on-the-job training under experienced toolmakers, covering various machining processes, tool and die design, and maintenance. This hands-on experience is paramount for developing practical skills and industry-specific knowledge, often lasting 3-5 years.
Develop proficiency in advanced machining techniques, including CNC programming and operation. As toolmaking increasingly integrates computer-controlled machinery, gaining expertise in CAD/CAM software and operating CNC mills, lathes, and EDMs becomes critical. Seek opportunities within your apprenticeship or through specialized courses to master these technologies.
Build a portfolio of precision machining projects and problem-solving examples. Document any tools, dies, fixtures, or custom parts you have created or repaired, highlighting the challenges faced and the solutions implemented. This portfolio serves as tangible proof of your skills and precision to potential employers.
Network with professionals in the manufacturing and tooling industry. Attend local trade shows, join professional organizations like the National Tooling and Machining Association (NTMA), and connect with experienced toolmakers. These connections can provide insights into job opportunities, mentorship, and industry trends, significantly aiding your job search.
Prepare a targeted resume and practice interview skills, emphasizing your practical experience and problem-solving abilities. Highlight your apprenticeship details, specific machining proficiencies, and any certifications obtained. Be ready to discuss your approach to complex machining challenges and demonstrate your understanding of precision and quality control during interviews.
Apply for entry-level toolmaker or apprentice toolmaker positions and be open to continuous learning. While searching, consider companies of various sizes, from small custom shops to large manufacturing facilities, as each offers unique learning environments. Once hired, commit to ongoing professional development to stay current with evolving technologies and techniques in the field.
Step 1
Complete foundational education in machining or manufacturing technology. Enroll in a vocational school, community college, or a pre-apprenticeship program that covers basic machining principles, blueprint reading, metrology, and materials science. This initial step builds the essential theoretical framework for understanding precision manufacturing.
Step 2
Secure a formal apprenticeship with a reputable machine shop or manufacturing company. Apprenticeships provide structured on-the-job training under experienced toolmakers, covering various machining processes, tool and die design, and maintenance. This hands-on experience is paramount for developing practical skills and industry-specific knowledge, often lasting 3-5 years.
Step 3
Develop proficiency in advanced machining techniques, including CNC programming and operation. As toolmaking increasingly integrates computer-controlled machinery, gaining expertise in CAD/CAM software and operating CNC mills, lathes, and EDMs becomes critical. Seek opportunities within your apprenticeship or through specialized courses to master these technologies.
Step 4
Build a portfolio of precision machining projects and problem-solving examples. Document any tools, dies, fixtures, or custom parts you have created or repaired, highlighting the challenges faced and the solutions implemented. This portfolio serves as tangible proof of your skills and precision to potential employers.
Step 5
Network with professionals in the manufacturing and tooling industry. Attend local trade shows, join professional organizations like the National Tooling and Machining Association (NTMA), and connect with experienced toolmakers. These connections can provide insights into job opportunities, mentorship, and industry trends, significantly aiding your job search.
Step 6
Prepare a targeted resume and practice interview skills, emphasizing your practical experience and problem-solving abilities. Highlight your apprenticeship details, specific machining proficiencies, and any certifications obtained. Be ready to discuss your approach to complex machining challenges and demonstrate your understanding of precision and quality control during interviews.
Step 7
Apply for entry-level toolmaker or apprentice toolmaker positions and be open to continuous learning. While searching, consider companies of various sizes, from small custom shops to large manufacturing facilities, as each offers unique learning environments. Once hired, commit to ongoing professional development to stay current with evolving technologies and techniques in the field.
Education & Training Needed to Become a Toolmaker
A Toolmaker's career path often involves a blend of formal education and extensive practical experience. Traditional routes include apprenticeships, which combine on-the-job training with classroom instruction, typically lasting 4-5 years. These programs often lead to journeyman status and are highly valued by employers, as they provide hands-on skill development crucial for precision work. Community college associate degrees in manufacturing technology or machine tool technology also serve as a strong foundation, usually taking two years to complete and costing between $6,000 and $20,000.
Alternative pathways, such as vocational school certificates, offer more focused, shorter programs, often 6-18 months, with costs ranging from $3,000 to $15,000. While these can provide entry-level skills, they usually require further on-the-job training to reach journeyman proficiency. Self-study and online courses exist for specific software or machine operations, but they rarely replace the critical hands-on experience gained through apprenticeships or dedicated vocational training. Employers prioritize candidates with proven practical skills and a strong understanding of machining principles, often valuing apprenticeship completion over a four-year degree for this specific role.
Continuous learning remains vital for Toolmakers. Keeping up with advancements in CNC machining, CAD/CAM software, and new materials ensures long-term career success. Industry certifications, such as those from the National Institute for Metalworking Skills (NIMS), enhance a Toolmaker's credentials and demonstrate specialized competence. The investment in formal training, especially apprenticeships or associate degrees, typically offers a strong return through higher earning potential and greater job security in this skilled trade.
Toolmaker Salary & Outlook
Compensation for a Toolmaker varies significantly based on several factors. Geographic location plays a crucial role, as areas with high manufacturing demand or a higher cost of living, such as the Northeast or parts of the Midwest, typically offer better wages. Local industry presence, particularly in aerospace, automotive, or medical device manufacturing, also drives salary.
Experience and specialized skills like CNC programming, CAD/CAM proficiency, or expertise with specific materials dramatically influence earning potential. Toolmakers who can design and build complex progressive dies or intricate molds often command premium compensation. Total compensation extends beyond base salary to include overtime pay, production bonuses, and comprehensive benefits packages. These benefits frequently cover health insurance, retirement plans like 401(k)s, and sometimes even profit-sharing or professional development allowances for advanced certifications.
Industry-specific trends, such as the adoption of additive manufacturing or automation, can also impact salary growth. Toolmakers who adapt to these new technologies and integrate them into their craft enhance their value. Salary negotiation leverage comes from demonstrating a proven track record of precision, efficiency, and problem-solving. While remote work is uncommon for this hands-on role, demand in specific regions can create competitive salary offers. Salary figures provided are primarily for the United States, acknowledging that international markets will have different compensation structures.
Salary by Experience Level
Level | US Median | US Average |
---|---|---|
Apprentice Toolmaker | $38k USD | $40k USD |
Junior Toolmaker | $52k USD | $55k USD |
Toolmaker | $68k USD | $70k USD |
Senior Toolmaker | $82k USD | $85k USD |
Master Toolmaker | $97k USD | $100k USD |
Toolmaking Supervisor | $110k USD | $115k USD |
Market Commentary
The job market for Toolmakers shows steady demand, driven by the ongoing need for precision manufacturing across various industries. While some manufacturing processes are automated, the intricate work of designing, building, and maintaining tools, dies, and molds still requires highly skilled human expertise. The Bureau of Labor Statistics projects stable growth for machinists and toolmakers, indicating a consistent need for these specialized trades.
Emerging opportunities for Toolmakers are often tied to advancements in manufacturing technology. Proficiency in CAD/CAM software, 3D printing for prototyping, and understanding automation systems are becoming increasingly vital. Industries like medical device manufacturing, aerospace, and defense continue to be significant employers, requiring custom tooling for highly specialized components. The supply of experienced Toolmakers often struggles to meet demand, creating a favorable market for skilled professionals.
Future-proofing this career involves continuous learning and adaptation to new materials and manufacturing processes. Toolmakers who embrace hybrid skills, combining traditional craftsmanship with digital design and advanced machining techniques, will remain highly valuable. While some aspects of manufacturing are cyclical, the fundamental need for precision tooling makes this profession relatively resilient. Geographic hotspots for Toolmakers align with major manufacturing hubs, particularly in states with strong automotive, aerospace, or industrial machinery sectors.
Toolmaker Career Path
Career progression for a Toolmaker typically begins with extensive hands-on training and evolves into highly specialized expertise. Professionals in this field often advance through a structured apprenticeship, gaining foundational skills before moving into more independent roles. Advancement hinges on mastering precision machining, materials science, and complex problem-solving, along with a keen eye for detail.
Individual contributor (IC) paths lead to roles like Master Toolmaker, focusing on intricate designs and advanced manufacturing techniques. Management tracks, such as Toolmaking Supervisor, involve leading teams, optimizing shop floor operations, and ensuring quality control. The speed of advancement depends on individual performance, the complexity of projects undertaken, and continuous skill development through certifications or specialized training.
Company size influences career paths significantly; smaller shops might offer broader exposure to different tool types, while large corporations may provide opportunities for specialization in areas like injection molding or stamping dies. Lateral movement often involves shifting between different manufacturing sectors, applying toolmaking skills to new product lines. Networking within the industry and seeking mentorship from experienced toolmakers are crucial for identifying new opportunities and accelerating professional growth.
Apprentice Toolmaker
3-4 yearsWorks under direct supervision, assisting experienced toolmakers with basic tasks. Learns to operate common machine tools, perform routine maintenance, and interpret engineering drawings. Responsibilities include material preparation, deburring, and maintaining a clean workspace.
Key Focus Areas
Develop foundational skills in manual machining (lathe, mill, grinder), blueprint reading, and basic measurement techniques. Understand material properties, safety protocols, and shop floor organization. Focus on precision, attention to detail, and following instructions meticulously.
Junior Toolmaker
4-6 years total experiencePerforms supervised setup and operation of machine tools for simpler tool components. Executes basic repairs and modifications to existing tooling. Contributes to the assembly of jigs, fixtures, and dies, following established procedures. Works on individual tasks with regular guidance.
Key Focus Areas
Improve proficiency in precision machining, including CNC operation and programming fundamentals. Gain experience with various tooling materials and heat treatment processes. Develop problem-solving skills for minor tool adjustments and repairs. Begin understanding tooling design principles.
Toolmaker
6-10 years total experienceIndependently builds, modifies, and repairs a variety of complex tools, dies, jigs, and fixtures. Diagnoses and resolves tooling issues, often suggesting design improvements. Operates advanced CNC machinery and precision measuring equipment. Manages individual projects from start to finish with minimal supervision.
Key Focus Areas
Master advanced machining techniques, including complex geometries and tight tolerances. Develop expertise in tool design, troubleshooting, and root cause analysis for tooling failures. Enhance knowledge of CAD/CAM software and advanced metrology. Cultivate independent problem-solving abilities.
Senior Toolmaker
10-15 years total experienceLeads complex toolmaking projects, often overseeing the work of junior toolmakers. Provides technical guidance and mentorship, ensuring quality and adherence to specifications. Collaborates with engineering and production teams to optimize tool performance and design. Identifies and implements efficiency improvements in tool manufacturing processes.
Key Focus Areas
Specialize in a particular area of toolmaking (e.g., progressive dies, injection molds, custom automation). Develop project management skills, including planning, scheduling, and resource allocation. Mentor junior toolmakers and contribute to process improvement initiatives. Enhance communication and collaboration skills.
Master Toolmaker
15+ years total experienceActs as a primary technical resource for the most challenging and critical toolmaking initiatives. Designs and oversees the creation of highly specialized or innovative tooling solutions. Provides expert consultation for complex manufacturing issues and new product development. May conduct training or develop best practices for the department.
Key Focus Areas
Achieve expert-level proficiency in all aspects of tool design, manufacturing, and maintenance. Develop advanced problem-solving capabilities for highly intricate or novel tooling challenges. Drive innovation in toolmaking processes and materials. Establish a reputation as a technical authority and thought leader.
Toolmaking Supervisor
12+ years total experience, including leadership experienceManages a team of toolmakers, overseeing daily operations, project assignments, and performance. Ensures the toolroom meets production deadlines, quality standards, and safety regulations. Implements continuous improvement initiatives and manages toolroom budget and resources. Responsible for staff development and training.
Key Focus Areas
Develop strong leadership, team management, and organizational skills. Focus on production planning, scheduling, and resource optimization for the toolroom. Acquire budgeting and cost control knowledge. Enhance communication, conflict resolution, and performance management abilities.
Apprentice Toolmaker
3-4 yearsWorks under direct supervision, assisting experienced toolmakers with basic tasks. Learns to operate common machine tools, perform routine maintenance, and interpret engineering drawings. Responsibilities include material preparation, deburring, and maintaining a clean workspace.
Key Focus Areas
Develop foundational skills in manual machining (lathe, mill, grinder), blueprint reading, and basic measurement techniques. Understand material properties, safety protocols, and shop floor organization. Focus on precision, attention to detail, and following instructions meticulously.
Junior Toolmaker
4-6 years total experiencePerforms supervised setup and operation of machine tools for simpler tool components. Executes basic repairs and modifications to existing tooling. Contributes to the assembly of jigs, fixtures, and dies, following established procedures. Works on individual tasks with regular guidance.
Key Focus Areas
Improve proficiency in precision machining, including CNC operation and programming fundamentals. Gain experience with various tooling materials and heat treatment processes. Develop problem-solving skills for minor tool adjustments and repairs. Begin understanding tooling design principles.
Toolmaker
6-10 years total experienceIndependently builds, modifies, and repairs a variety of complex tools, dies, jigs, and fixtures. Diagnoses and resolves tooling issues, often suggesting design improvements. Operates advanced CNC machinery and precision measuring equipment. Manages individual projects from start to finish with minimal supervision.
Key Focus Areas
Master advanced machining techniques, including complex geometries and tight tolerances. Develop expertise in tool design, troubleshooting, and root cause analysis for tooling failures. Enhance knowledge of CAD/CAM software and advanced metrology. Cultivate independent problem-solving abilities.
Senior Toolmaker
10-15 years total experienceLeads complex toolmaking projects, often overseeing the work of junior toolmakers. Provides technical guidance and mentorship, ensuring quality and adherence to specifications. Collaborates with engineering and production teams to optimize tool performance and design. Identifies and implements efficiency improvements in tool manufacturing processes.
Key Focus Areas
Specialize in a particular area of toolmaking (e.g., progressive dies, injection molds, custom automation). Develop project management skills, including planning, scheduling, and resource allocation. Mentor junior toolmakers and contribute to process improvement initiatives. Enhance communication and collaboration skills.
Master Toolmaker
15+ years total experienceActs as a primary technical resource for the most challenging and critical toolmaking initiatives. Designs and oversees the creation of highly specialized or innovative tooling solutions. Provides expert consultation for complex manufacturing issues and new product development. May conduct training or develop best practices for the department.
Key Focus Areas
Achieve expert-level proficiency in all aspects of tool design, manufacturing, and maintenance. Develop advanced problem-solving capabilities for highly intricate or novel tooling challenges. Drive innovation in toolmaking processes and materials. Establish a reputation as a technical authority and thought leader.
Toolmaking Supervisor
12+ years total experience, including leadership experienceManages a team of toolmakers, overseeing daily operations, project assignments, and performance. Ensures the toolroom meets production deadlines, quality standards, and safety regulations. Implements continuous improvement initiatives and manages toolroom budget and resources. Responsible for staff development and training.
Key Focus Areas
Develop strong leadership, team management, and organizational skills. Focus on production planning, scheduling, and resource optimization for the toolroom. Acquire budgeting and cost control knowledge. Enhance communication, conflict resolution, and performance management abilities.
Job Application Toolkit
Ace your application with our purpose-built resources:
Global Toolmaker Opportunities
Toolmakers are essential globally, designing and fabricating precision tools, dies, and molds for manufacturing across diverse industries. There is consistent international demand for skilled professionals in this trade, particularly in advanced manufacturing hubs. Cultural differences impact safety standards and production methodologies. International certifications like ISO 9001 and specific industry-recognized qualifications enhance global mobility for toolmakers. They often seek international roles for higher wages or specialized project experience.
Global Salaries
Toolmaker salaries vary significantly by region, reflecting economic development and industrial concentration. In North America, a toolmaker earns between $55,000 and $80,000 USD annually in countries like the United States and Canada. This range can increase for highly specialized or experienced individuals. European countries like Germany and Switzerland offer strong compensation, with salaries typically ranging from €45,000 to €70,000 (approximately $48,000-$75,000 USD), often including comprehensive benefits like robust healthcare and generous vacation time.
In Asia-Pacific, particularly in advanced manufacturing economies like Japan and South Korea, toolmakers can expect salaries from ¥4,500,000 to ¥7,000,000 (approximately $30,000-$47,000 USD) or ₩40,000,000 to ₩65,000,000 (approximately $29,000-$47,000 USD) respectively. While nominal figures appear lower, purchasing power parity often means a comparable standard of living. Countries in Latin America, such as Mexico, offer lower nominal salaries, typically $15,000-$30,000 USD, but with a significantly lower cost of living.
Salary structures also differ. North American packages often feature performance bonuses, while European compensation frequently includes more social benefits. Tax implications vary widely; for instance, higher income tax rates in Western Europe may reduce take-home pay compared to some parts of North America, even with similar gross salaries. Experience and specialized skills, like CNC programming or specific material expertise, significantly impact international compensation.
Remote Work
Toolmaking is a hands-on profession that inherently limits extensive remote work opportunities. The core tasks of design, fabrication, and precision measurement require physical presence in a workshop or factory setting. However, specific aspects of a toolmaker's role, such as CAD/CAM design, simulation, and project planning, can be performed remotely. This partial remote capability allows for some flexibility in the design phase.
International remote work for toolmakers is primarily limited to design and consulting roles for global clients or internal company projects. It is not feasible for the fabrication part of the job. Digital nomad opportunities are rare for hands-on toolmakers, as their work demands specialized equipment. Companies hiring internationally for remote design work in this field are typically large manufacturing firms or engineering consultancies. Equipment needs include high-performance workstations and specialized software. Salary expectations for remote design work might reflect the lower cost of living in the toolmaker's location, rather than the client's country, due to geographic arbitrage.
Visa & Immigration
Toolmakers seeking international employment typically apply for skilled worker visas. Popular destinations include Germany, Canada, Australia, and the United States, all with strong manufacturing sectors. Germany's Skilled Immigration Act simplifies pathways for qualified professionals, often requiring recognized vocational training or a university degree. Canada's Express Entry system and Provincial Nominee Programs consider skilled trades, often requiring a job offer and language proficiency via IELTS.
Australia's General Skilled Migration program also lists toolmakers, requiring skills assessment and points-based eligibility. The U.S. offers H-2B visas for temporary skilled workers, though employer sponsorship is essential and numbers are capped. Credential recognition is crucial; applicants often need to demonstrate their qualifications meet local standards. Visa timelines vary from a few months to over a year. Some countries offer pathways to permanent residency after several years of skilled employment. Language requirements are common, particularly for European countries. Family visas are usually available for dependents, allowing them to accompany the primary applicant.
2025 Market Reality for Toolmakers
Understanding current market realities is crucial for toolmakers to navigate a profession undergoing significant transformation. The field has evolved rapidly since 2023, influenced by post-pandemic supply chain recalibrations and the accelerating integration of automation and AI in manufacturing processes. Broader economic factors, such as industrial output fluctuations and global trade policies, directly impact demand for new tooling and skilled labor.
Market realities for toolmakers vary considerably by experience level, with senior, multi-skilled professionals in higher demand than entry-level candidates. Geographic location plays a vital role, as demand concentrates in manufacturing-heavy regions. Company size also matters; smaller, specialized shops often seek versatile individuals, while larger corporations may have more defined roles. This analysis provides an honest assessment of these dynamics, helping toolmakers strategically plan their careers.
Current Challenges
Toolmakers face significant competition from automation, which reduces demand for manual precision work. Economic uncertainty in manufacturing sectors, particularly automotive and aerospace, directly impacts job availability. Furthermore, a skills gap persists; many experienced toolmakers are retiring, while new entrants lack the comprehensive hands-on training required for complex tasks.
Growth Opportunities
Despite challenges, strong opportunities exist for toolmakers specializing in advanced manufacturing techniques. Expertise in multi-axis CNC machining, EDM, and especially additive manufacturing for tooling (e.g., 3D printing of molds or jigs) is highly sought after. Companies need professionals who can bridge traditional craftsmanship with digital fabrication.
Emerging roles include 'Tooling Automation Specialists' or 'Additive Manufacturing Tooling Engineers,' requiring a blend of mechanical aptitude and software proficiency. Toolmakers who can troubleshoot complex automated systems or develop optimized toolpaths for AI-assisted designs find themselves uniquely positioned. Underserved markets exist in specialized industries like medical device manufacturing or aerospace components, where precision and custom tooling remain critical and less susceptible to broad economic swings.
Developing expertise in specific materials, such as composites or exotic alloys, also provides a competitive edge. Market corrections can create opportunities for toolmakers to join companies investing in reshoring manufacturing or upgrading legacy systems. Investing in certifications for advanced CNC programming, GD&T, or specific CAD/CAM software suites enhances marketability. Pursuing roles in R&D or prototyping departments within manufacturing firms offers growth potential beyond traditional production environments.
Current Market Trends
The market for toolmakers in 2025 shows a nuanced demand. While traditional manufacturing sectors still require skilled hands, the overall hiring pace has slowed compared to pre-2023 levels. Companies increasingly invest in advanced CNC machinery and additive manufacturing (3D printing) for tooling, shifting requirements towards programming and maintenance over pure manual fabrication.
Economic conditions in 2024 and 2025, marked by fluctuating industrial output and supply chain adjustments, have led some manufacturers to optimize existing tooling rather than expanding production lines requiring new tools. Layoffs in certain automotive and consumer goods manufacturing segments have impacted toolmaker positions. Generative AI is starting to influence tool design optimization, automating some initial design phases and requiring toolmakers to interpret and refine AI-generated blueprints.
Employer requirements now heavily emphasize proficiency in CAD/CAM software, G-code programming, and interpreting complex digital models, alongside traditional machining skills. Salaries for highly experienced toolmakers with advanced CNC and programming expertise remain strong, but entry-level saturation is evident in regions with ample vocational training programs. Geographically, demand is stronger in industrial hubs like the Midwest and Southeast United States, where manufacturing facilities are concentrated, but remote work is virtually non-existent for this hands-on role.
Seasonal patterns are less pronounced, but capital expenditure cycles in manufacturing can lead to periods of increased hiring for new projects followed by leaner times. The integration of robotics in tool handling and inspection also means toolmakers need to understand automated workflows.
Emerging Specializations
The field of toolmaking is undergoing a significant transformation, driven by advancements in manufacturing technology and materials science. This evolution creates new specialization opportunities for skilled professionals beyond traditional machining and fabrication. Understanding these emerging areas allows toolmakers to strategically position themselves for future career growth.
Early positioning in these next-generation specializations is crucial for commanding premium compensation and accelerating career advancement in 2025 and beyond. As industries adopt advanced manufacturing processes, the demand for toolmakers with specialized skills in these cutting-edge areas will intensify. While established specializations remain important, focusing on emerging niches offers a distinct competitive advantage.
These emerging areas often transition from niche to mainstream within five to ten years, generating a substantial number of job opportunities. Specializing in cutting-edge fields involves a balance of risk and reward. It requires proactive learning and adaptation, but it also offers the potential for significant professional development and higher earning potential as these skills become indispensable.
Additive Manufacturing Tooling Specialist
Additive manufacturing, particularly with metals and advanced composites, is revolutionizing how tools and molds are produced. Toolmakers specializing in this area design and create complex tooling components using 3D printing technologies. This includes understanding material properties for additive processes, optimizing designs for printability, and post-processing additively manufactured parts to meet precise specifications for strength and surface finish. This shift reduces lead times and enables geometries impossible with traditional subtractive methods.
Smart Tooling & IoT Integration Expert
As manufacturing moves towards greater automation and data integration, toolmakers are increasingly involved in smart tooling. This specialization focuses on designing and implementing tools embedded with sensors, actuators, and communication capabilities. These 'smart tools' can monitor their own performance, predict maintenance needs, and provide real-time feedback to production systems, optimizing manufacturing processes and improving tool lifespan. It requires an understanding of both mechanical and basic electrical/data principles.
Advanced Composite Tooling Fabricator
The demand for lightweight, high-performance components in industries like aerospace and automotive drives innovation in composite tooling. Toolmakers in this area specialize in designing and fabricating molds and fixtures specifically for composite material lay-up and curing processes. This involves working with unique materials like carbon fiber, understanding autoclave curing cycles, and ensuring extremely tight tolerances for complex composite part geometries. Precision and material compatibility are paramount.
Micro-Precision Tooling Engineer
Precision micro-tooling involves the design and fabrication of tools with features measured in micrometers or nanometers. This specialization supports industries like medical devices, electronics, and micro-optics where incredibly small and accurate components are required. Toolmakers in this field utilize ultra-precision machining techniques, laser ablation, and advanced metrology to achieve unparalleled accuracy and surface finishes. This demands meticulous attention to detail and mastery of highly specialized equipment.
Sustainable Tooling Design Specialist
Sustainable manufacturing practices are becoming critical, leading to the emergence of eco-conscious tooling design. This specialization focuses on creating tools and molds that minimize environmental impact throughout their lifecycle. This includes designing for material efficiency, using recycled or sustainable tool materials, optimizing tool life to reduce waste, and designing tools for energy-efficient manufacturing processes. It also involves considering end-of-life recycling for tooling components.
Pros & Cons of Being a Toolmaker
Understanding both the advantages and challenges of a career as a Toolmaker is crucial for making an informed decision. Career experiences can vary significantly based on the specific industry, company culture, and the types of tools being manufactured or repaired. Factors such as a company's investment in new technology or its production demands will shape daily tasks and long-term prospects.
Furthermore, what one person considers a benefit, like detailed precision work, another might find tedious. Similarly, career stages impact the experience; early-career toolmakers might focus more on learning and assistance, while senior roles involve complex problem-solving and design. This assessment aims to provide a realistic overview, helping aspiring toolmakers set appropriate expectations for this skilled trade.
Pros
- Toolmakers possess highly specialized and in-demand skills, ensuring strong job security in manufacturing sectors that rely on precision tooling for production.
- The work offers significant intellectual stimulation, as it involves complex problem-solving, precision engineering, and the satisfaction of creating functional, high-tolerance components.
- Toolmakers often earn competitive wages, reflecting the advanced skills, extensive training, and critical role they play in maintaining manufacturing efficiency and product quality.
- This career provides a tangible sense of accomplishment, as toolmakers directly contribute to the creation of products by designing, building, and repairing the instruments that shape raw materials.
- Many toolmakers enjoy a good work-life balance, typically working standard shifts with less unpredictability than some other manufacturing roles, unless an urgent repair is needed.
- There are clear paths for career progression, including opportunities to specialize in mold making, die making, jig and fixture building, or move into supervisory, design, or quality control roles.
- The skills acquired are highly transferable across diverse industries, from automotive and aerospace to medical devices and consumer goods, offering flexibility in career choices.
Cons
- The work environment can be physically demanding, requiring prolonged standing, lifting heavy components, and working with loud machinery, which can lead to fatigue or strain over time.
- Toolmakers often face tight deadlines, especially when a production line is down due to a tooling issue, creating high-pressure situations to diagnose and repair quickly.
- This field requires continuous learning and adaptation to new materials, machining technologies, and CAD/CAM software, demanding ongoing professional development to stay competitive.
- Exposure to coolants, lubricants, metal dust, and loud noises is common, necessitating strict adherence to safety protocols and the consistent use of personal protective equipment.
- While highly skilled, the career path can sometimes feel repetitive, as core tasks involve precision machining, assembly, and maintenance of similar types of tools and dies.
- Entry into a journeyman toolmaker role often requires a multi-year apprenticeship or extensive on-the-job training, representing a significant time investment before achieving full proficiency and higher wages.
- Finding highly specialized work can sometimes be geographically limited to areas with robust manufacturing industries, potentially requiring relocation for optimal opportunities or higher pay.
Frequently Asked Questions
Toolmakers face distinct challenges combining precision craftsmanship with problem-solving. This section addresses common questions about entering this skilled trade, from mastering machining techniques to understanding the demand for highly specialized fabrication expertise.
How long does it take to become a qualified Toolmaker if I'm starting from scratch?
Becoming a qualified toolmaker typically takes 4-5 years through an apprenticeship program. These programs combine on-the-job training with classroom instruction, allowing you to earn a wage while learning. Some individuals pursue a two-year associate's degree in machine tool technology, which can shorten the apprenticeship period or provide a strong foundation before entering one.
Do I need a specific degree or certification to become a Toolmaker?
While a formal degree is not always mandatory, most toolmakers gain their skills through apprenticeships or vocational training. These programs provide the hands-on experience and theoretical knowledge essential for the precision work involved. Some employers may prefer candidates with a two-year associate's degree in manufacturing technology or a related field, especially for more complex roles.
What are the typical salary expectations for a Toolmaker, both entry-level and experienced?
Entry-level toolmakers can expect a starting salary that varies by region and industry, often ranging from $40,000 to $55,000 annually. With experience, specialized skills, and demonstrated expertise, experienced toolmakers can earn significantly more, potentially reaching $70,000 to $90,000 or higher. Overtime opportunities are also common in this field, which can boost overall earnings.
Is the Toolmaker profession in high demand, and what is its job security like?
The demand for skilled toolmakers remains steady, particularly in industries requiring custom manufacturing, such as aerospace, automotive, and medical devices. As older generations of skilled tradespeople retire, there is a consistent need for new talent to fill these specialized roles. Automation changes some aspects of the job but often increases the need for toolmakers to build and maintain the sophisticated machinery.
What is the typical work environment and daily routine for a Toolmaker?
Toolmakers typically work in manufacturing facilities, machine shops, or specialized tool and die shops. The work environment can involve standing for long periods, operating heavy machinery, and handling precision instruments. While it requires physical dexterity and attention to detail, modern shops often have climate control and safety measures in place. Some roles may involve shift work, especially in production-focused environments.
What are the career growth opportunities and advancement paths for a Toolmaker?
Career growth for toolmakers often involves specializing in particular types of tooling, such as progressive dies, injection molds, or complex jigs and fixtures. Opportunities also exist to move into supervisory roles, becoming a shop foreman or lead toolmaker. Some experienced toolmakers transition into design engineering, quality control, or even start their own custom fabrication businesses, leveraging their deep understanding of manufacturing processes.
How does the Toolmaker profession typically impact work-life balance?
The work-life balance for toolmakers can vary. Many positions offer standard daytime hours, but some manufacturing settings operate on multiple shifts, including evenings or weekends, to meet production demands. Overtime is often available and can be a significant part of a toolmaker's income, but it also means longer hours. The nature of the work, which requires intense focus and precision, means that work periods are often structured and defined.
What is the most challenging aspect of being a Toolmaker for someone new to the field?
The most challenging aspect for new toolmakers is developing the extreme precision and problem-solving skills required to create complex, high-tolerance parts. This involves not only mastering machine operation but also understanding material properties, blueprint reading, and advanced geometry. Toolmakers often troubleshoot and refine designs, which demands a deep understanding of manufacturing principles and a keen eye for detail.
Related Careers
Explore similar roles that might align with your interests and skills:
Die Maker
A growing field with similar skill requirements and career progression opportunities.
Explore career guideMachinist
A growing field with similar skill requirements and career progression opportunities.
Explore career guideMold Maker
A growing field with similar skill requirements and career progression opportunities.
Explore career guideTool Designer
A growing field with similar skill requirements and career progression opportunities.
Explore career guideTool Room Machinist
A growing field with similar skill requirements and career progression opportunities.
Explore career guideAssess your Toolmaker readiness
Understanding where you stand today is the first step toward your career goals. Our Career Coach helps identify skill gaps and create personalized plans.
Skills Gap Analysis
Get a detailed assessment of your current skills versus Toolmaker requirements. Our AI Career Coach identifies specific areas for improvement with personalized recommendations.
See your skills gapCareer Readiness Assessment
Evaluate your overall readiness for Toolmaker roles with our AI Career Coach. Receive personalized recommendations for education, projects, and experience to boost your competitiveness.
Assess your readinessSimple pricing, powerful features
Upgrade to Himalayas Plus and turbocharge your job search.
Himalayas
Himalayas Plus
Himalayas Max
Find your dream job
Sign up now and join over 100,000 remote workers who receive personalized job alerts, curated job matches, and more for free!
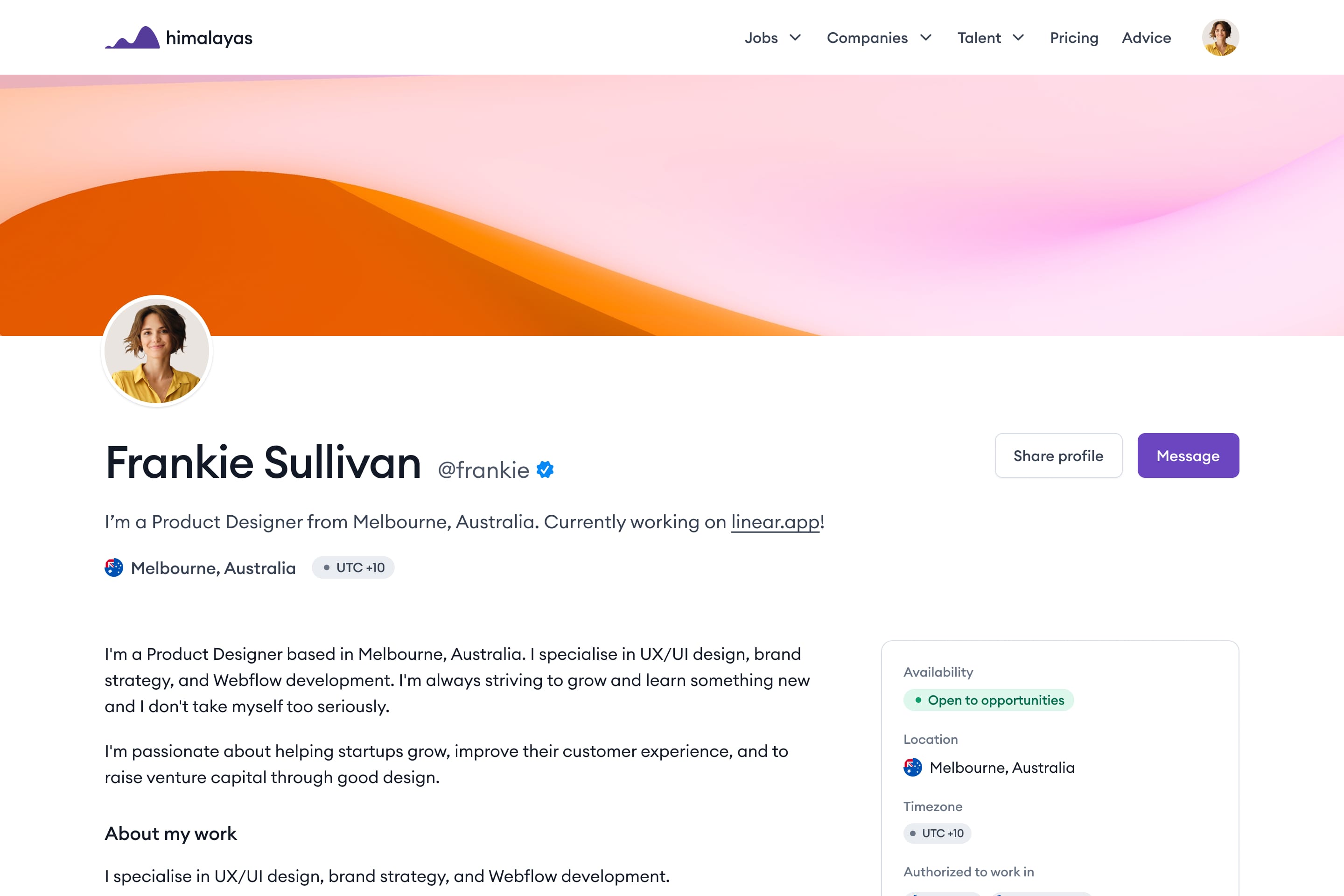