Complete Mold Maker Career Guide
Mold makers are precision craftspeople who design and build the intricate molds and dies essential for mass-producing everything from plastic components to metal parts. This highly specialized role combines engineering principles with meticulous hands-on skill, creating the foundational tooling that drives modern manufacturing. It offers a stable career for those who enjoy detailed work and seeing their creations enable large-scale production.
Key Facts & Statistics
Median Salary
$62,990 USD
(U.S. Bureau of Labor Statistics, May 2023)
Range: $40,000 - $90,000+ USD
Growth Outlook
1%
as fast as average (U.S. Bureau of Labor Statistics, 2022-2032)
Annual Openings
≈17,000
openings annually (U.S. Bureau of Labor Statistics)
Top Industries
Typical Education
High school diploma or equivalent, typically followed by an apprenticeship or vocational training in machining or tool and die making.
What is a Mold Maker?
A Mold Maker is a highly skilled craftsperson who designs, builds, maintains, and repairs the precision tooling used to create products through molding processes, such as injection molding, blow molding, or die casting. These professionals are the backbone of manufacturing, crafting the intricate forms that give shape to everything from plastic consumer goods and automotive parts to medical devices.
Unlike general machinists who fabricate a wide range of parts, mold makers specialize specifically in the complex, multi-component assemblies that are molds. They combine advanced machining skills with a deep understanding of materials, design principles, and manufacturing processes to produce tools capable of replicating thousands or millions of identical parts with extreme accuracy and consistency.
What does a Mold Maker do?
Key Responsibilities
- Interpret blueprints, schematics, and CAD designs to plan the sequence of operations for mold construction.
- Operate precision machining tools such as CNC mills, lathes, grinders, and EDM machines to fabricate mold components with exact tolerances.
- Assemble complex mold components, ensuring precise alignment and functionality of moving parts, cooling channels, and ejection systems.
- Perform rigorous quality control inspections on finished mold components and assembled molds using micrometers, calipers, and optical comparators.
- Conduct test runs of newly built molds to identify and troubleshoot issues related to part quality, flash, or short shots, making necessary adjustments.
- Maintain and repair existing molds, diagnosing wear and tear, replacing damaged inserts, and restoring molds to optimal operational condition.
- Collaborate with design engineers and production teams to optimize mold designs for manufacturability, efficiency, and product quality.
Work Environment
Mold makers typically work in a manufacturing or tool-and-die shop environment. This often involves a combination of machine operation, bench work for assembly and finishing, and quality inspection. The work is highly detailed and requires significant focus, often performed in a well-lit and climate-controlled area, though shops can be noisy due to machinery.
Collaboration with design engineers, machinists, and production managers is common, but much of the work involves independent, meticulous craftsmanship. The pace of work varies; some projects have tight deadlines, while others allow for more extended, detailed efforts. This role usually follows a standard workday schedule, though overtime may be necessary to meet production demands.
Tools & Technologies
Mold makers use a wide array of specialized tools and technologies. They frequently operate CNC (Computer Numerical Control) machining centers, including mills, lathes, and grinders, which are programmed to cut materials with extreme precision. Electrical discharge machining (EDM) machines, both sinker and wire EDM, are essential for intricate details and hard-to-machine materials. Traditional hand tools, such as files, chisels, and polishing equipment, are also critical for finishing and fitting mold components.
Software includes CAD (Computer-Aided Design) for reviewing designs and CAM (Computer-Aided Manufacturing) for programming machines. Measurement tools like micrometers, calipers, height gauges, optical comparators, and coordinate measuring machines (CMMs) are used for quality assurance. They also work with various materials such as steel alloys, aluminum, and sometimes exotic metals or ceramics.
Mold Maker Skills & Qualifications
A Mold Maker's qualifications are highly specialized, focusing on precision craftsmanship and deep material science knowledge. Employers prioritize practical experience and demonstrated skill over formal academic degrees. Apprenticeships and vocational training are the most common and valued pathways into this profession, often leading to journeyman status.
Requirements for a Mold Maker vary significantly by industry sector. The medical device, aerospace, and automotive industries demand extremely high tolerances and specific material expertise. Smaller job shops might require broader skills across various mold types, while larger manufacturers often seek specialists in injection, compression, or blow molding. Seniority levels dictate the complexity of projects, with entry-level roles focusing on basic machining and assembly, and senior roles involving complex mold design, troubleshooting, and leadership.
While certifications are not always mandatory, achieving journeyman status through a recognized apprenticeship program is highly regarded. This signifies a comprehensive understanding of the trade. The skill landscape is evolving with the increased use of CAD/CAM software and CNC machining. However, the foundational manual machining and precision measurement skills remain critical for success in this demanding trade.
Education Requirements
Technical Skills
- CNC machining (Milling, Lathe, EDM - Electrical Discharge Machining) operation and programming
- Manual machining (Milling, Lathe, Grinding) for precision component fabrication
- CAD/CAM software proficiency (e.g., SolidWorks, Mastercam, AutoCAD) for design and toolpath generation
- Precision measurement tools and techniques (micrometers, calipers, gauges, CMM - Coordinate Measuring Machine)
- Blueprint reading and GD&T (Geometric Dimensioning and Tolerancing) interpretation
- Heat treatment processes for mold steels and other materials
- Mold assembly, fitting, and polishing techniques
- Troubleshooting and repair of existing molds
- Material science knowledge (various steels, aluminum, carbides, plastics)
- Mold design principles (gating, cooling, ejection systems)
- Jig and fixture design and fabrication
- Preventative maintenance procedures for mold tooling
Soft Skills
- Attention to detail: Crucial for achieving the extremely tight tolerances required in mold making, where errors can lead to costly rework or scrapped parts.
- Problem-solving: Essential for diagnosing issues with mold performance, identifying root causes of defects, and developing effective solutions during design and manufacturing.
- Patience and persistence: Mold making often involves repetitive tasks and meticulous adjustments; patience is needed to ensure precision, and persistence to overcome complex challenges.
- Manual dexterity: Fundamental for handling small components, performing delicate assembly, and executing precise hand finishing operations.
- Spatial reasoning: Important for visualizing complex 3D mold designs from 2D blueprints and understanding how components fit together.
- Adaptability: Necessary to adjust to new mold designs, materials, and manufacturing technologies, as the industry evolves.
- Communication: Important for collaborating with designers, engineers, and production teams to ensure molds meet specifications and production goals.
How to Become a Mold Maker
Entering the mold making field offers several pathways, each with unique advantages and timelines. Traditional routes often involve apprenticeships or vocational training, providing hands-on experience and direct industry exposure. These paths can range from two to five years, depending on the program's intensity and whether it includes formal certification or an associate's degree.
Non-traditional entry might include transitioning from a related manufacturing role, like machining or tool and die making, where transferable skills shorten the learning curve significantly. Some individuals might also gain entry through on-the-job training at smaller shops, which can be faster but may offer less structured learning. Geographic location heavily influences opportunities; manufacturing hubs in the Midwest or Southeast United States, for example, typically have more openings and established training programs.
Understanding the distinction between mold making for plastics versus metals, or for different industries like medical devices versus automotive, helps in targeting the right training and job opportunities. While a degree is not always mandatory, a strong portfolio showcasing practical skills and a commitment to precision craftsmanship is crucial. Networking within local manufacturing associations and attending industry trade shows also opens doors to mentorship and employment.
Step 1
Step 2
Step 3
Step 4
Step 5
Step 6
Education & Training Needed to Become a Mold Maker
Becoming a skilled Mold Maker typically involves a blend of formal education and extensive hands-on training. Unlike many tech roles, a traditional four-year university degree is not usually a prerequisite for this specialized trade. Instead, vocational schools, community college programs, and apprenticeships form the backbone of a Mold Maker's education. These pathways emphasize practical skills like precision machining, CAD/CAM software operation, and material science, all crucial for creating intricate molds.
Apprenticeships are a highly respected and effective route, often lasting 4-5 years. They combine paid on-the-job training with classroom instruction. Apprenticeships can cost very little, sometimes even paying a modest wage, and lead directly to employment. Vocational programs and associate's degrees in Tool & Die Making or Machining Technology typically take 1-2 years and cost between $5,000-$20,000, depending on the institution. While these programs provide a strong theoretical foundation, practical experience is still paramount, often gained through entry-level positions or further on-the-job training.
Employers highly value hands-on experience and proven precision skills. Certifications from organizations like the National Institute for Metalworking Skills (NIMS) are well-regarded, demonstrating competency in specific machining operations. Continuous learning in areas like advanced CNC programming, 3D printing for mold inserts, and new materials is essential. The cost-benefit analysis favors apprenticeships and vocational programs for their direct industry relevance and lower financial outlay compared to more generalized degrees. The market perception strongly favors practical skills and demonstrable experience over purely academic credentials for a Mold Maker.
Mold Maker Salary & Outlook
Compensation for a Mold Maker reflects a blend of specialized skills, precision, and experience. Geographic location significantly influences earnings, with higher salaries often found in regions with strong manufacturing bases and a higher cost of living, such as the Midwest automotive corridor or aerospace hubs. Conversely, areas with less industrial demand may offer lower pay.
Years of experience dramatically impact a Mold Maker's salary. Entry-level positions and apprenticeships provide foundational pay, while senior and master mold makers command premium wages due to their extensive expertise in complex tooling and problem-solving. Specialization in areas like injection molding, blow molding, or die casting, coupled with advanced CAD/CAM software proficiency, can also lead to higher earning potential.
Total compensation packages extend beyond base salary. Many employers offer performance bonuses tied to project completion or quality metrics. Comprehensive benefits, including health insurance, retirement contributions (401k), and paid time off, are standard. Some companies also invest in professional development and certifications, enhancing a Mold Maker's long-term value. Salary negotiation leverage increases with proven expertise, a strong portfolio of successful projects, and a deep understanding of manufacturing processes. While remote work is uncommon for this hands-on role, global demand for skilled mold makers means international markets may offer varying compensation structures, typically benchmarked against USD figures.
Salary by Experience Level
Level | US Median | US Average |
---|---|---|
Apprentice Mold Maker | $38k USD | $40k USD |
Junior Mold Maker | $52k USD | $55k USD |
Mold Maker | $68k USD | $70k USD |
Senior Mold Maker | $82k USD | $85k USD |
Lead Mold Maker | $97k USD | $100k USD |
Master Mold Maker | $110k USD | $115k USD |
Market Commentary
The job market for Mold Makers remains stable, driven by the continuous need for precision tooling across various manufacturing sectors, including automotive, aerospace, medical devices, and consumer goods. While some automation in design and machining has occurred, the demand for highly skilled Mold Makers who can interpret complex designs, troubleshoot, and perform intricate finishing work persists. Projections indicate consistent demand, particularly for those with advanced skills in CNC machining and additive manufacturing integration.
A notable supply-demand imbalance exists, with fewer individuals entering the trades, creating a shortage of experienced Mold Makers. This scarcity contributes to competitive salaries and strong job security for qualified professionals. Emerging opportunities include working with new materials, such as advanced composites and ceramics, and integrating smart manufacturing techniques like IoT-enabled tooling for predictive maintenance.
The profession is relatively recession-resistant due to the foundational role molds play in nearly all manufactured products. While economic downturns may slow new product development, maintenance and replacement of existing molds remain crucial. Geographic hotspots for Mold Makers align with major manufacturing hubs in states like Michigan, Ohio, Indiana, and North Carolina. Future-proofing involves continuous learning in advanced machining, materials science, and digital manufacturing technologies to adapt to evolving industry standards and maintain relevance in an increasingly automated landscape.
Mold Maker Career Path
Career progression for a Mold Maker involves a highly specialized path, emphasizing hands-on skill development, precision, and deep material science knowledge. Advancement typically follows a clear trajectory from foundational learning to expert craftsmanship and leadership, often within a single company or across a few specialized workshops. Individual contributor (IC) tracks dominate this field, with management roles emerging only at the most senior levels, often overseeing a shop or a team of mold makers.
Advancement speed depends heavily on an individual's aptitude for precision work, commitment to continuous learning in new technologies like additive manufacturing, and the specific demands of the industry served (e.g., medical, automotive, aerospace). Larger companies or those with diverse product lines may offer more varied learning experiences, while smaller, specialized shops might allow for deeper expertise in niche areas. Lateral movement often involves shifting between industries requiring different mold types, such as from injection molding to blow molding, demanding adaptation of core skills.
Networking within the local manufacturing community and participation in industry associations, though less formal than in other fields, can provide insights into best practices and new techniques. Mentorship plays an absolutely crucial role, especially during the apprenticeship and junior stages, as experienced Mold Makers pass down invaluable tacit knowledge. Certifications in specific machinery operation, CAD/CAM software, or advanced materials processing can mark significant milestones and enhance progression opportunities. Some experienced Mold Makers may pivot into design engineering, quality assurance, or even entrepreneurship, opening their own specialized shops.
Apprentice Mold Maker
0-3 yearsKey Focus Areas
Junior Mold Maker
3-5 years total experienceKey Focus Areas
Apprentice Mold Maker
0-3 yearsWorks under direct supervision, assisting experienced Mold Makers with preparatory tasks like material cutting, basic machining, and mold cleaning. Focuses on learning fundamental techniques and shop procedures. Decisions are highly guided, with minimal independent authority.
Key Focus Areas
Developing foundational hand-tool skills, understanding safety protocols, and learning basic machine operation (lathes, mills). Focus on material handling, measurement precision using calipers and micrometers, and blueprint reading. Beginning to grasp the principles of mold design and component identification.
Junior Mold Maker
3-5 years total experiencePerforms routine mold fabrication tasks, including machining, grinding, and polishing of mold components. Works on less complex mold repairs and modifications under general supervision. Contributes to quality checks and assembly of mold sections. Exercises limited independent decision-making on task execution.
Key Focus Areas
Refining precision machining skills, understanding different mold types and their applications. Developing proficiency in CAD/CAM software for basic part programming. Learning about various mold materials and their properties. Beginning to troubleshoot minor issues with supervision.
Job Application Toolkit
Ace your application with our purpose-built resources:
Global Mold Maker Opportunities
Mold Makers design and produce molds for manufacturing, a critical role globally. Demand for skilled Mold Makers remains steady across industrial nations, especially in automotive, aerospace, and medical device sectors. International opportunities exist due to specialized skill requirements. Cultural nuances affect workplace practices, while regulatory differences influence material and safety standards. Professionals seek international roles for advanced training or higher earning potential. No specific international certifications are broadly recognized; practical experience and apprenticeships are most valued globally.
Global Salaries
Salaries for Mold Makers vary significantly by region and experience. In North America, entry-level Mold Makers earn around $45,000-$55,000 USD annually. Experienced professionals in the United States and Canada can command $65,000-$85,000 USD, often with overtime. European salaries differ; in Germany, experienced Mold Makers might earn €40,000-€60,000 (approx. $43,000-$65,000 USD), while in the UK, it ranges from £30,000-£45,000 (approx. $38,000-$57,000 USD). These figures reflect high manufacturing standards and strong apprenticeship systems.
Asia-Pacific markets, like South Korea and Japan, offer competitive wages for skilled Mold Makers, often between ¥4,000,000-¥6,000,000 JPY (approx. $25,000-$38,000 USD) in Japan for experienced roles, accounting for lower cost of living. In Australia, salaries typically range from AUD $60,000-$80,000 (approx. $40,000-$53,000 USD). Latin American countries, such as Mexico, offer lower nominal salaries, perhaps $15,000-$30,000 USD, but purchasing power can be higher.
Cost of living adjustments are crucial. A higher nominal salary in Switzerland might have less purchasing power than a modest salary in a lower-cost region. Salary structures also include varying benefits: European countries often have robust healthcare and longer vacation. North America typically offers more performance-based bonuses. Tax implications significantly impact take-home pay; for example, Nordic countries have higher income taxes but comprehensive social benefits. International pay scales are not standardized for this trade; compensation depends on local industry demand, company size, and specific skill sets like CAD/CAM proficiency or specialized material knowledge.
Remote Work
International remote work for Mold Makers is extremely limited due to the hands-on nature of the job. The role requires direct interaction with machinery, materials, and physical prototypes in a workshop or factory setting. Design aspects, such as CAD/CAM work, can be performed remotely. However, this constitutes only a fraction of the Mold Maker's overall responsibilities. Most employers require on-site presence for mold fabrication, testing, and maintenance.
Digital nomad opportunities are not applicable to the core Mold Maker role. Some companies might allow senior Mold Makers to contribute to design or project management remotely, but this is rare. Salary expectations for remote design work would align more with engineering or design roles, not the full Mold Maker compensation. Practical considerations like specialized equipment and a dedicated workspace make full remote work unfeasible for this profession. Companies rarely hire international remote Mold Makers, as the physical presence is paramount.
Visa & Immigration
Mold Makers often qualify for skilled worker visas in countries with strong manufacturing sectors. Popular destinations include Germany, Canada, Australia, and the United States. Germany's skilled worker visa (Fachkräfteeinwanderungsgesetz) requires recognized vocational qualifications and a job offer. Canada's Express Entry system considers skilled trades, with points awarded for experience and language proficiency. Australia’s skilled migration program lists Mold Maker on its occupation lists, requiring skills assessment and English language tests.
The U.S. offers H-2B visas for temporary non-agricultural workers, which can include skilled trades, but typically requires a U.S. employer to sponsor. Credential recognition is vital; countries often require vocational qualifications to be assessed for equivalency. Visa timelines vary from a few months to over a year. Pathways to permanent residency often exist after several years of skilled employment. Language requirements depend on the country; for example, German proficiency is beneficial for working in Germany. Family visas are generally available for spouses and dependents once the primary applicant secures a work permit.
2025 Market Reality for Mold Makers
Understanding the current market reality for mold makers is critical for career longevity and strategic planning. The industry has navigated significant shifts from 2023 to 2025, driven by post-pandemic supply chain reconfigurations and the accelerating integration of advanced manufacturing technologies, including AI.
Broader economic factors, such as inflation and consumer spending, directly influence manufacturing output and, by extension, the demand for new tooling. Market realities for mold makers vary considerably; experienced professionals with niche skills find more stable opportunities than entry-level candidates. Geographic location, particularly proximity to manufacturing clusters, and the size of the company also play a significant role in job availability and compensation. This analysis provides an honest assessment of these dynamics, helping mold makers navigate their career paths effectively.
Current Challenges
Mold makers face significant challenges, including a shrinking talent pool as experienced professionals retire. Automation and 3D printing technologies also reshape traditional roles, demanding new skill sets. Economic slowdowns can reduce demand for new tooling, impacting job stability. Competition from overseas manufacturing further pressures domestic opportunities, requiring greater specialization and efficiency from local shops.
Growth Opportunities
Despite challenges, significant opportunities exist for mold makers specializing in high-precision sectors like medical devices, aerospace components, and electric vehicle parts. These industries require intricate, high-tolerance molds that command premium skills and offer stable demand. Emerging roles involve working with additive manufacturing (3D printing) for tooling, creating hybrid manufacturing processes that combine traditional mold making with advanced digital fabrication.
Mold makers who proactively upskill in advanced CAD/CAM, subtractive and additive manufacturing, and robotic automation are positioned for greater success. Developing expertise in materials science, especially with new composites and alloys, also provides a competitive edge. Underserved markets often exist in regions with a strong, growing manufacturing base but a declining pool of skilled tradespeople. Targeting smaller, specialized shops that focus on prototyping or short-run production can also uncover niche opportunities, as these often require highly adaptable and skilled mold makers.
Current Market Trends
The mold making sector is experiencing a nuanced shift in 2025. Demand remains steady for highly specialized or complex molds, particularly in medical, aerospace, and defense industries. However, the market for simpler, high-volume molds faces stiff competition from international suppliers. Automation and advanced CNC machining are no longer just trends; they are foundational requirements for efficiency and precision.
Generative AI and simulation software are beginning to influence design processes, enabling faster prototyping and optimization, which in turn demands mold makers who can interpret complex digital models and work with intricate designs. This integration means employers increasingly seek candidates with strong CAD/CAM skills and a willingness to adapt to new software. Traditional manual skills, while still valued, are now often complemented by digital proficiency.
Salary trends are stable for experienced, multi-skilled mold makers, especially those proficient in high-precision work or specialized materials. Entry-level positions face more saturation and wage stagnation. Remote work is virtually non-existent for hands-on mold making, tying opportunities to specific geographic manufacturing hubs. However, some design and programming aspects can be done remotely. Seasonal fluctuations are minimal, but economic downturns in manufacturing can directly impact new project starts and, consequently, demand for new molds.
Emerging Specializations
Technological advancements and evolving industry demands consistently create new specialization opportunities across various fields. For mold makers, this evolution means moving beyond traditional techniques towards areas integrating advanced manufacturing processes and digital technologies. Understanding these shifts allows professionals to strategically position themselves for future career growth.
Early positioning in emerging specializations, particularly from 2025 onwards, offers significant advantages. These roles often command premium compensation due to specialized skill sets and limited talent pools. They also provide enhanced career growth trajectories, as individuals become pioneers in rapidly expanding niches. While established specializations offer stability, emerging areas promise innovation and leadership roles.
Many cutting-edge areas, initially niche, typically transition into mainstream opportunities within five to ten years, creating substantial job markets. Investing in these emerging skills now can lead to becoming an industry expert as the demand escalates. However, pursuing cutting-edge areas involves a balance of risk and reward; while the potential for high returns is significant, it requires continuous learning and adaptability to evolving technologies.
Additive Manufacturing Mold Design Specialist
Smart Mold & Sensor Integration Engineer
Sustainable Material Mold Design Specialist
Hybrid Tooling Development Engineer
Micro-Molding Tooling Specialist
Pros & Cons of Being a Mold Maker
Understanding both the advantages and challenges of any career path is crucial before making a commitment. This is particularly true for a Mold Maker, where the day-to-day realities can differ significantly from general perceptions.
Career experiences are highly variable, influenced by factors such as company culture, the specific industry sector (e.g., automotive, medical, consumer goods), and individual specialization within mold making. What one person considers a benefit, another might view as a drawback, depending on personal values, lifestyle preferences, and career stage.
For instance, early-career Mold Makers might prioritize skill acquisition and learning, while seasoned professionals might focus on project complexity or mentorship opportunities. This assessment aims to provide an honest, balanced perspective to help set realistic expectations for anyone considering this skilled trade.
Pros
- Mold making is a highly skilled trade that offers a strong sense of accomplishment, as you create tangible, precise tools essential for manufacturing countless products.
- There is consistent demand for skilled Mold Makers across various industries, including automotive, aerospace, medical devices, and consumer goods, ensuring good job security.
- The work is intellectually stimulating, involving complex problem-solving, precision engineering, and the application of advanced machining techniques and CAD/CAM software.
- Many Mold Makers earn competitive wages, especially those with specialized skills or experience in complex tooling, reflecting the high value placed on their craftsmanship.
- The field offers opportunities for continuous learning and skill development, as new materials, technologies, and design methodologies constantly evolve, keeping the work engaging.
- Mold making provides a pathway into diverse manufacturing sectors, allowing professionals to specialize or transition between industries based on personal interest or market demand.
- For those who enjoy hands-on work and seeing a project from concept to completion, the satisfaction of producing a perfect mold that enables mass production is a significant reward.
Cons
- The work environment can be physically demanding, involving heavy lifting, standing for long hours, and working with large machinery, which may lead to physical strain over time.
- Exposure to various materials like resins, metals, and chemicals used in mold making can pose health risks if proper safety protocols and personal protective equipment are not strictly followed.
- The job often requires precision and meticulous attention to detail, which can be mentally taxing and lead to eye strain or fatigue during long periods of intricate work.
- Learning the craft of mold making involves a steep and continuous learning curve, as new materials, technologies, and manufacturing processes emerge regularly, requiring ongoing education.
- Work schedules can sometimes be unpredictable, with tight deadlines or urgent orders requiring overtime, weekend work, or shifts to meet production demands.
- Career advancement opportunities may be limited within smaller shops, often requiring relocation or a shift into management or specialized design roles to progress significantly.
- The industry can be sensitive to economic downturns, as demand for new molds often correlates with manufacturing and product development cycles, potentially impacting job security during recessions.
Frequently Asked Questions
Mold Makers face unique challenges combining precision machining with artistic craftsmanship. This section addresses common questions about entering this skilled trade, from apprenticeship requirements to the physical demands and long-term career stability in a field critical to manufacturing across many industries.
What is the typical path to becoming a certified Mold Maker, and how long does it take?
Becoming a qualified Mold Maker typically involves completing a formal apprenticeship, which can take 4-5 years. These programs combine on-the-job training with classroom instruction, covering blueprint reading, CAD/CAM software, various machining processes, and material science. Some enter the field through vocational schools or community college programs, followed by several years of on-the-job experience to gain proficiency.
What are the salary expectations for a Mold Maker, both entry-level and experienced?
Mold Makers earn competitive wages, reflecting the high skill level required. Entry-level apprenticeships start lower, but experienced Mold Makers can earn significantly more, especially with specialized skills or in industries with high demand. Salary varies based on location, industry (e.g., automotive, medical, consumer goods), and specific employer. Many positions also offer benefits like health insurance and retirement plans.
What is the typical work-life balance like for a Mold Maker, considering hours and physical demands?
The work-life balance for a Mold Maker can vary. Many positions are full-time, standard weekday hours, but some shops operate on multiple shifts or require overtime to meet production deadlines, particularly in industries with high demand. The work is often hands-on and precise, which can be mentally engaging but also physically demanding. It is important to clarify typical hours and overtime expectations during the job search.
Is there a strong job market for Mold Makers, or is the field declining due to automation?
The demand for skilled Mold Makers remains steady because molds are essential for manufacturing countless products across diverse industries, including plastics, rubber, and metal casting. While automation impacts some aspects of manufacturing, the complex design, precision machining, and finishing of molds still require highly skilled human expertise. Continuous learning of new technologies and materials ensures strong job security.
What are the typical career advancement opportunities for an experienced Mold Maker?
Mold Makers can advance in several ways. They might specialize in complex mold designs, CNC programming, or specific materials. Opportunities also exist to move into supervisory roles, lead teams, or become project managers overseeing mold production. Some experienced Mold Makers transition into teaching roles at vocational schools or become independent consultants, leveraging their extensive knowledge.
What are some common misconceptions about the Mold Maker profession that people should know?
A common misconception is that Mold Making is a purely manual trade. While hands-on skill is crucial, modern Mold Making relies heavily on advanced computer-aided design (CAD) and computer-aided manufacturing (CAM) software, CNC machines, and precision measurement tools. Professionals in this field need strong technical aptitude, problem-solving skills, and a willingness to continuously learn new technologies.
What are the biggest challenges Mold Makers face in their day-to-day work?
The most challenging aspects often involve maintaining extreme precision, troubleshooting complex design issues, and working with very tight tolerances. Even minor errors can lead to significant material waste and production delays. Mold Makers must also adapt to new technologies and materials, which requires continuous learning and a commitment to staying updated with industry advancements.
Can Mold Makers work remotely, or is this primarily an on-site profession?
While some larger manufacturing companies might have facilities that allow for some remote work in design or programming phases, the core work of a Mold Maker is hands-on and requires presence in a specialized workshop or factory setting. This includes operating machinery, assembling components, and performing quality checks. Therefore, the role is typically not conducive to full-time remote work.
Related Careers
Explore similar roles that might align with your interests and skills:
Toolmaker
A growing field with similar skill requirements and career progression opportunities.
Explore career guideFoundry Molder
A growing field with similar skill requirements and career progression opportunities.
Explore career guideMetal Patternmaker
A growing field with similar skill requirements and career progression opportunities.
Explore career guidePlastic Die Maker Apprentice
A growing field with similar skill requirements and career progression opportunities.
Explore career guideSand Molder
A growing field with similar skill requirements and career progression opportunities.
Explore career guideAssess your Mold Maker readiness
Understanding where you stand today is the first step toward your career goals. Our Career Coach helps identify skill gaps and create personalized plans.
Skills Gap Analysis
Get a detailed assessment of your current skills versus Mold Maker requirements. Our AI Career Coach identifies specific areas for improvement with personalized recommendations.
See your skills gapCareer Readiness Assessment
Evaluate your overall readiness for Mold Maker roles with our AI Career Coach. Receive personalized recommendations for education, projects, and experience to boost your competitiveness.
Assess your readinessSimple pricing, powerful features
Upgrade to Himalayas Plus and turbocharge your job search.
Himalayas
Himalayas Plus
Himalayas Max
Find your dream job
Sign up now and join over 100,000 remote workers who receive personalized job alerts, curated job matches, and more for free!
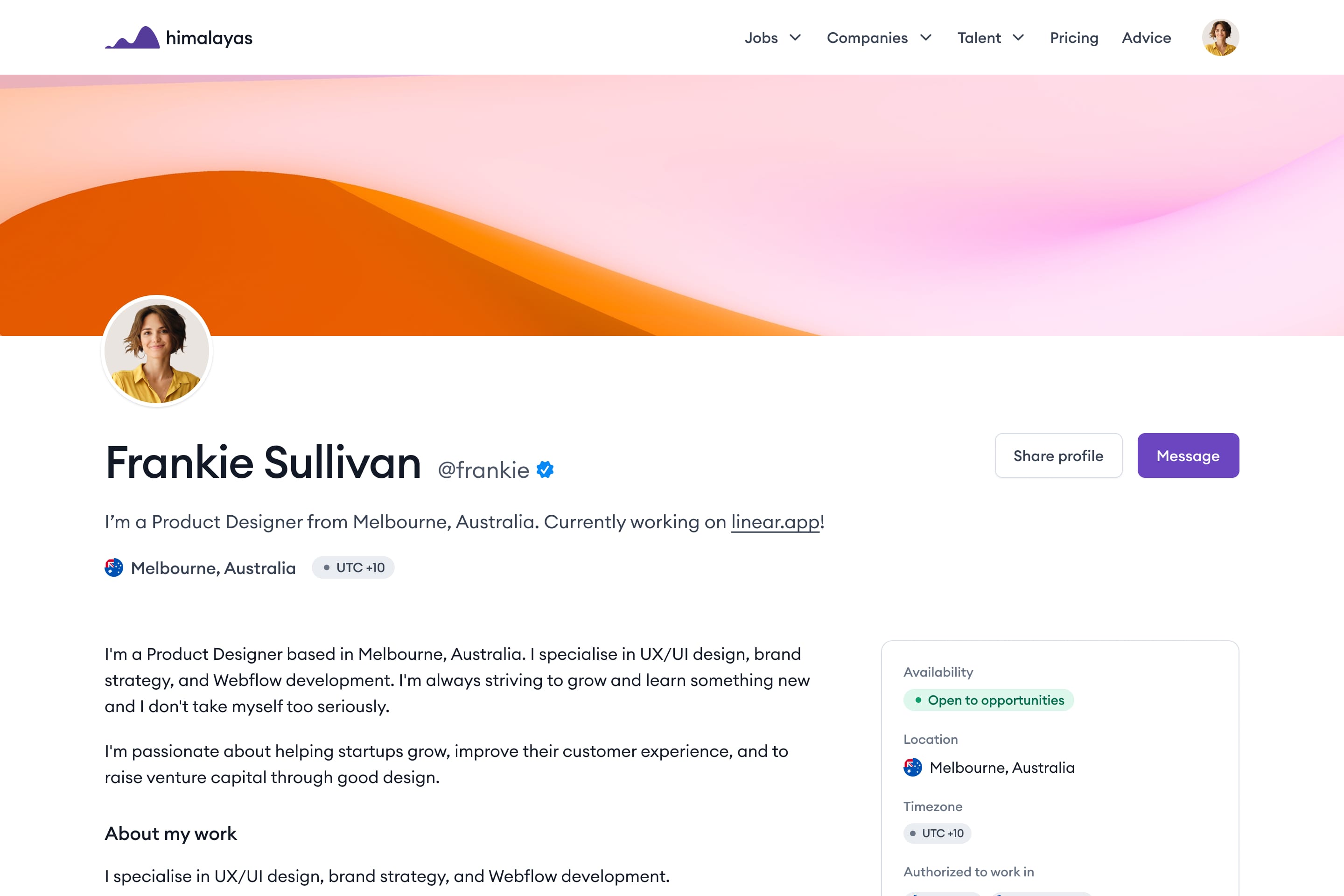