Complete Tool Room Machinist Career Guide
Tool Room Machinists are the unsung heroes of manufacturing, crafting the precision tools, dies, and fixtures that enable mass production. This role demands exceptional skill in operating advanced machinery and interpreting complex blueprints, directly impacting product quality and efficiency across diverse industries. It's a hands-on career for those who thrive on precision, problem-solving, and seeing tangible results from their expertise.
Key Facts & Statistics
Median Salary
$59,970 USD
(U.S. national median, BLS May 2023)
Range: $40k - $80k+ USD
Growth Outlook
Annual Openings
≈19k
openings annually (BLS)
Top Industries
Typical Education
High school diploma or equivalent, often with vocational training, an apprenticeship, or an associate's degree in machining technology.
What is a Tool Room Machinist?
A Tool Room Machinist is a highly skilled craftsperson who specializes in the fabrication, modification, and repair of precision tools, dies, jigs, fixtures, and machine components critical for manufacturing processes. Unlike production machinists who focus on repetitive part creation, a Tool Room Machinist produces custom, one-off, or low-volume parts with extremely tight tolerances, often for internal use within a manufacturing plant.
This role requires a deep understanding of metallurgy, machining principles, and advanced metrology. Tool Room Machinists are problem-solvers who bridge the gap between design and production, ensuring that the machinery and tooling used in manufacturing operate efficiently and produce high-quality products. They are essential for maintaining and improving a factory's operational capabilities.
What does a Tool Room Machinist do?
Key Responsibilities
- Set up and operate manual and CNC machining equipment, including lathes, mills, grinders, and drill presses, to produce precision components.
- Interpret complex engineering blueprints, schematics, and technical drawings to determine dimensions, tolerances, and material specifications.
- Perform precise measurements using micrometers, calipers, height gauges, and coordinate measuring machines (CMM) to ensure parts meet strict quality standards.
- Fabricate and repair custom tooling, fixtures, jigs, and machine parts essential for manufacturing processes.
- Conduct routine maintenance and troubleshooting on tool room machinery to ensure optimal performance and longevity.
- Collaborate with engineers and production teams to design and refine tools, improving manufacturing efficiency and product quality.
- Maintain accurate records of work performed, materials used, and tooling specifications for future reference and process improvement.
Work Environment
A Tool Room Machinist typically works in a dedicated tool room or a manufacturing facility, often in a clean, well-lit, and climate-controlled environment. The work can involve standing for long periods and requires careful attention to detail and safety protocols. It is generally an independent role, though collaboration with engineers, production managers, and other machinists is common when discussing specifications or troubleshooting.
The pace can vary from steady, precise work on custom projects to more urgent repairs or fabrication needs that arise during production. Standard daytime shifts are common, but some facilities may require evening or weekend work, especially for urgent tooling repairs. The environment is focused on precision and problem-solving, with a strong emphasis on quality craftsmanship.
Tools & Technologies
Tool Room Machinists regularly use a range of precision equipment and software. They operate manual machining tools such as lathes, milling machines, surface grinders, and drill presses. For advanced work, they utilize Computer Numerical Control (CNC) machines, including CNC mills and lathes, often programmed using CAM software like Mastercam or SolidCAM.
Measurement and inspection tools are critical, including micrometers, calipers, depth gauges, height gauges, bore gauges, and Coordinate Measuring Machines (CMMs). They also work with various cutting tools, inserts, and workholding devices. Familiarity with CAD software like SolidWorks or AutoCAD is often beneficial for interpreting designs and sometimes for minor design modifications.
Tool Room Machinist Skills & Qualifications
A Tool Room Machinist requires a precise blend of formal training and extensive hands-on experience. Employers prioritize practical skills and a proven track record of producing high-precision components over solely academic credentials. Many successful machinists enter the field through apprenticeships or vocational programs, which offer direct exposure to machinery and materials. While a two-year associate's degree in machining technology provides a strong theoretical foundation, it often serves as a complement to, rather than a replacement for, practical shop floor experience.
Requirements for a Tool Room Machinist vary significantly based on the industry and the complexity of the tools produced. Aerospace and medical device manufacturing, for instance, demand exceptionally high tolerances and specialized material knowledge, often requiring several years of dedicated experience. Smaller job shops might value versatility across different machines, while larger manufacturing facilities may seek specialization in specific types of equipment, such as CNC milling or grinding. Geographic location also plays a role; regions with strong manufacturing bases often have more formalized apprenticeship programs and a higher demand for experienced machinists.
The skill landscape for Tool Room Machinists is evolving with increasing automation. While traditional manual machining skills remain critical for prototyping and repair, proficiency in Computer Numerical Control (CNC) programming and operation is now a must-have. Companies increasingly seek machinists who can set up, program, and troubleshoot advanced CNC machines. Certifications from organizations like the National Institute for Metalworking Skills (NIMS) significantly enhance a candidate's credibility, demonstrating mastery of specific machining processes. Continuous learning, especially in new materials and machining technologies, is vital for long-term career success in this precise field.
Education Requirements
Technical Skills
- CNC Programming (G-code, M-code, conversational programming)
- Manual Machining (lathe, mill, surface grinder, drill press operation)
- Blueprint Reading and Geometric Dimensioning & Tolerancing (GD&T)
- Precision Measurement Tools (micrometers, calipers, height gauges, bore gauges, CMMs)
- Tool & Die Making Principles (stamping, forming, cutting dies)
- CAD/CAM Software Proficiency (e.g., SolidWorks, Mastercam, Fusion 360)
- Material Science (understanding properties of various metals, plastics, and composites)
- Machine Setup and Operation (fixture design, workholding, tooling selection)
- Preventative Maintenance and Troubleshooting (machine diagnostics, minor repairs)
- Grinding Operations (surface, cylindrical, and form grinding)
- Heat Treatment Processes (understanding effects on tool steels)
- Basic Electrical and Hydraulic Systems (for machine troubleshooting)
Soft Skills
- Attention to Detail: Essential for ensuring components meet exact specifications and tolerances, preventing costly errors in tool production.
- Problem-Solving: Vital for diagnosing issues with machine performance, tool wear, and material inconsistencies during complex machining operations.
- Patience: Necessary for intricate setups, meticulous measurements, and repetitive tasks that demand precision and careful execution.
- Mechanical Aptitude: Crucial for understanding how machines work, performing maintenance, and troubleshooting operational issues.
- Adaptability: Important for switching between different types of machines, materials, and project requirements, often on short notice.
- Safety Consciousness: Paramount for adhering to strict safety protocols when operating heavy machinery and handling sharp tools or hazardous materials.
- Time Management: Key for prioritizing tasks, meeting production deadlines, and efficiently managing machine setup and run times.
- Continuous Learning: Important for staying current with new machining technologies, materials, and software updates to maintain competitive skills.
How to Become a Tool Room Machinist
Breaking into the Tool Room Machinist field offers several pathways, from formal apprenticeships to vocational training and self-taught routes. While traditional apprenticeships provide a comprehensive, hands-on learning experience often spanning 3-5 years, vocational schools offer accelerated programs, typically 6-18 months, focusing on practical skills. The timeline for entry varies significantly; a complete beginner might spend 2-4 years gaining foundational skills and experience, while someone with related mechanical experience could transition in 1-2 years.
Entry strategies also depend on factors like company size and geographic location. Larger manufacturing firms in industrial hubs often prefer candidates with formal certifications or apprenticeship completions. Smaller shops or those in less competitive markets might be more open to individuals demonstrating strong practical aptitude and a willingness to learn on the job. A common misconception is that extensive academic degrees are necessary; practical skills, precision, and problem-solving abilities hold far more weight in this field.
Building a network within local manufacturing communities, attending industry events, and connecting with experienced machinists can open doors to opportunities not advertised publicly. The hiring landscape values demonstrable skills over theoretical knowledge, making a portfolio of precision parts or successful repair projects highly valuable. Overcoming barriers often involves proving mechanical aptitude and a dedication to continuous learning, particularly with new CNC technologies.
Develop foundational mechanical aptitude and shop safety knowledge. Begin by understanding basic hand tools, measurement devices like calipers and micrometers, and the principles of shop safety. Consider introductory courses in machine shop practices or self-study using textbooks and online tutorials to grasp fundamental concepts before touching machinery.
Complete formal training in machining through a vocational program or apprenticeship. Enroll in a certified machining program that covers manual lathe and mill operation, basic CNC programming, blueprint reading, and metallurgy. An apprenticeship provides invaluable on-the-on-job training and mentorship, often leading directly to employment.
Master precision measurement and quality control techniques. Practice using a variety of precision measuring tools to ensure parts meet exact specifications, as accuracy is paramount in tool room machining. Learn about GD&T (Geometric Dimensioning and Tolerancing) and how to inspect finished components for defects and adherence to design, which is critical for tool integrity.
Gain practical experience through internships, entry-level positions, or personal projects. Seek out opportunities to work in a machine shop, even in a helper or deburring role, to observe and assist experienced machinists. Alternatively, set up a home shop or join a makerspace to build small, precise projects that demonstrate your ability to work with tight tolerances.
Build a portfolio of precision parts and problem-solving examples. Document your best work, including photos or videos of parts you have machined, along with explanations of the challenges you faced and how you overcame them. Highlight any custom tools you created or complex repairs you executed, showcasing your ingenuity and technical skill.
Network with local machinists, shop owners, and industry professionals. Attend local manufacturing trade shows, join online forums for machinists, and connect with people in the field through LinkedIn. Informational interviews can provide insights into specific shop needs and potential openings, often leading to referrals.
Prepare for practical assessments and technical interviews. Practice explaining your machining processes, troubleshooting common problems, and interpreting technical drawings, as many shops conduct hands-on tests. Be ready to discuss your safety practices and demonstrate your ability to operate various machine tools accurately and efficiently during the interview process.
Step 1
Develop foundational mechanical aptitude and shop safety knowledge. Begin by understanding basic hand tools, measurement devices like calipers and micrometers, and the principles of shop safety. Consider introductory courses in machine shop practices or self-study using textbooks and online tutorials to grasp fundamental concepts before touching machinery.
Step 2
Complete formal training in machining through a vocational program or apprenticeship. Enroll in a certified machining program that covers manual lathe and mill operation, basic CNC programming, blueprint reading, and metallurgy. An apprenticeship provides invaluable on-the-on-job training and mentorship, often leading directly to employment.
Step 3
Master precision measurement and quality control techniques. Practice using a variety of precision measuring tools to ensure parts meet exact specifications, as accuracy is paramount in tool room machining. Learn about GD&T (Geometric Dimensioning and Tolerancing) and how to inspect finished components for defects and adherence to design, which is critical for tool integrity.
Step 4
Gain practical experience through internships, entry-level positions, or personal projects. Seek out opportunities to work in a machine shop, even in a helper or deburring role, to observe and assist experienced machinists. Alternatively, set up a home shop or join a makerspace to build small, precise projects that demonstrate your ability to work with tight tolerances.
Step 5
Build a portfolio of precision parts and problem-solving examples. Document your best work, including photos or videos of parts you have machined, along with explanations of the challenges you faced and how you overcame them. Highlight any custom tools you created or complex repairs you executed, showcasing your ingenuity and technical skill.
Step 6
Network with local machinists, shop owners, and industry professionals. Attend local manufacturing trade shows, join online forums for machinists, and connect with people in the field through LinkedIn. Informational interviews can provide insights into specific shop needs and potential openings, often leading to referrals.
Step 7
Prepare for practical assessments and technical interviews. Practice explaining your machining processes, troubleshooting common problems, and interpreting technical drawings, as many shops conduct hands-on tests. Be ready to discuss your safety practices and demonstrate your ability to operate various machine tools accurately and efficiently during the interview process.
Education & Training Needed to Become a Tool Room Machinist
A Tool Room Machinist requires a specialized skill set, blending traditional machining with precision tool and die making. Educational pathways vary, from formal apprenticeships and associate degrees to vocational certifications and self-study, each with distinct time and cost implications. Apprenticeships often last 3-5 years, providing extensive on-the-job training alongside classroom instruction, typically costing $0-$5,000 for materials and tuition, with apprentices earning a wage. Associate degrees in Machine Tool Technology or Manufacturing Engineering Technology span two years, costing $8,000-$25,000 at community colleges, and offer a strong theoretical foundation.
Vocational certifications, available from technical schools, focus on specific skills like CNC programming or precision grinding, often taking 6-18 months and costing $3,000-$15,000. These programs provide targeted skills quickly. Self-study, while cost-effective, requires significant discipline and access to equipment, often taking 6-24 months to build foundational skills; it lacks formal credentials but can supplement other learning. Employers highly value practical experience, often preferring candidates with apprenticeship backgrounds or associate degrees combined with hands-on work. Certifications like NIMS (National Institute for Metalworking Skills) are widely recognized industry standards, validating specific proficiencies.
Continuous learning is crucial for Tool Room Machinists due to evolving technologies like advanced CNC systems and additive manufacturing. Specialized training in CAD/CAM software, metrology, and new materials ensures ongoing relevance. The educational needs shift based on the specific tools or dies being produced and the machinery used, with larger, more complex operations often requiring more advanced training. The cost-benefit analysis favors pathways that balance theoretical knowledge with extensive practical application, leading to a strong portfolio of precision work. Programs with strong industry partnerships and job placement services often provide the best return on investment.
Tool Room Machinist Salary & Outlook
Compensation for a Tool Room Machinist varies significantly based on several factors beyond just base salary. Geographic location plays a major role; areas with a high concentration of manufacturing, such as the Midwest or parts of the Southeast in the U.S., often offer competitive wages due to demand and local industry presence. Conversely, regions with a higher cost of living may have higher nominal salaries but similar real wages.
Experience and specialized skills significantly impact earning potential. A machinist with expertise in specific CNC programming languages, advanced metrology, or complex jig and fixture design can command premium compensation. Total compensation packages frequently include overtime pay, which is common in this role, and sometimes performance bonuses related to efficiency or project completion. Benefits like health insurance, retirement contributions, and paid time off are standard.
Industry-specific trends also influence salaries. The aerospace, medical device, and automotive sectors often pay more due to the precision and critical nature of their tooling. Remote work is generally not applicable for this hands-on role, but some companies may offer relocation bonuses for highly skilled individuals. While the provided figures are in USD, international markets have their own distinct salary structures influenced by local labor laws, economic conditions, and industrial development.
Salary by Experience Level
Level | US Median | US Average |
---|---|---|
Apprentice Tool Room Machinist | $38k USD | $40k USD |
Junior Tool Room Machinist | $50k USD | $52k USD |
Tool Room Machinist | $62k USD | $65k USD |
Senior Tool Room Machinist | $75k USD | $78k USD |
Lead Tool Room Machinist | $85k USD | $88k USD |
Tool Room Supervisor | $92k USD | $95k USD |
Market Commentary
The job market for Tool Room Machinists shows a steady demand, driven by the ongoing need for custom parts, molds, dies, and specialized tooling across various manufacturing sectors. The Bureau of Labor Statistics projects a modest growth for machinists and tool and die makers, though the specific demand for tool room machinists remains robust due to their specialized skill set. This role is critical for prototyping, production support, and maintaining manufacturing efficiency.
Emerging opportunities lie in advanced manufacturing, including additive manufacturing (3D printing) integration and automation. Machinists who can program and operate sophisticated multi-axis CNC machines, understand CAD/CAM software, and work with new materials will find themselves in high demand. The supply of highly skilled tool room machinists is often lower than demand, creating a favorable market for experienced professionals.
This profession is relatively resilient to economic downturns compared to other manufacturing roles, as tooling is essential for both new product development and maintenance of existing production lines. Geographic hotspots for employment include traditional manufacturing hubs in states like Michigan, Ohio, Wisconsin, and Texas. While automation and AI are transforming manufacturing, the intricate and custom nature of tool room work ensures that the human element of skilled craftsmanship and problem-solving remains indispensable.
Tool Room Machinist Career Path
Career progression for a Tool Room Machinist involves a clear path from foundational learning to advanced specialization and leadership. This journey typically begins with intensive hands-on training, gradually transitioning into independent work on complex projects. Professionals advance by mastering precision machining techniques, materials science, and the intricate design and repair of tools, dies, jigs, and fixtures.
Advancement speed depends on several factors, including individual performance, a commitment to continuous learning, and the specific industry. Companies in aerospace or medical device manufacturing, for instance, may offer faster progression due to the demand for highly specialized skills. Tool Room Machinists can pursue an individual contributor (IC) track, becoming highly specialized experts, or transition into a management track, overseeing operations and mentoring teams.
Lateral moves might involve specializing in CAD/CAM programming, quality control, or machine maintenance within manufacturing. Networking within industry associations and pursuing certifications in advanced machining or metrology enhance career prospects. Some professionals may pivot into roles like manufacturing engineering or technical sales, leveraging their deep understanding of precision mechanics and production processes.
Apprentice Tool Room Machinist
0-2 yearsOperates under direct supervision, assisting experienced machinists with basic tasks. Focuses on learning machine setup, material handling, and routine maintenance procedures. Responsibilities include cleaning equipment and organizing the workspace.
Key Focus Areas
Mastering safety protocols, understanding machine operation fundamentals, and learning basic measurement techniques. Developing foundational knowledge of different metals and their properties. Building a strong work ethic and attention to detail.
Junior Tool Room Machinist
2-4 yearsWorks with some supervision on less complex projects, such as creating simple jigs or repairing basic tooling components. Executes precise cuts and finishes according to specifications. Contributes to maintaining tool room inventory and equipment.
Key Focus Areas
Developing proficiency in operating various manual machines (lathes, mills, grinders) and beginning to learn CNC programming basics. Improving blueprint reading skills and understanding geometric dimensioning and tolerancing (GD&T). Enhancing problem-solving abilities for minor machining issues.
Tool Room Machinist
4-8 yearsIndependently designs, fabricates, and repairs complex tools, dies, molds, and fixtures. Makes critical decisions regarding machining processes, material selection, and tolerances. Often works on prototypes and custom components requiring high precision.
Key Focus Areas
Achieving mastery in both manual and CNC machining, including advanced programming and setup. Deepening knowledge of heat treatment, surface finishes, and specialized materials. Developing strong troubleshooting skills for complex tool failures and production challenges.
Senior Tool Room Machinist
8-12 yearsHandles the most intricate and critical tooling projects, often involving tight deadlines and exacting specifications. Provides technical guidance to other machinists and reviews their work for quality and accuracy. Contributes to the development of new tooling solutions and production methods.
Key Focus Areas
Specializing in advanced machining techniques like EDM or 5-axis machining. Developing expertise in tool design optimization for manufacturability and longevity. Mentoring junior machinists and contributing to process improvement initiatives. Pursuing certifications in metrology or advanced CAD/CAM.
Lead Tool Room Machinist
12-15 yearsLeads a team of machinists on major projects, coordinating tasks and ensuring adherence to timelines and quality standards. Acts as a primary technical resource, resolving complex machining and tooling issues. Participates in equipment selection and technology adoption decisions.
Key Focus Areas
Demonstrating strong leadership and project management skills. Developing a strategic understanding of tool room operations, including scheduling, resource allocation, and budget management. Enhancing communication skills for effective collaboration with engineering and production teams.
Tool Room Supervisor
15+ yearsManages the entire tool room operation, overseeing staff, equipment, and workflow. Responsible for budgeting, scheduling, and ensuring the tool room meets production demands and quality objectives. Implements new technologies and processes to enhance efficiency and capability.
Key Focus Areas
Cultivating exceptional leadership, team management, and operational planning abilities. Developing expertise in lean manufacturing principles and continuous improvement methodologies. Building strong interpersonal skills for managing personnel and stakeholder relationships.
Apprentice Tool Room Machinist
0-2 yearsOperates under direct supervision, assisting experienced machinists with basic tasks. Focuses on learning machine setup, material handling, and routine maintenance procedures. Responsibilities include cleaning equipment and organizing the workspace.
Key Focus Areas
Mastering safety protocols, understanding machine operation fundamentals, and learning basic measurement techniques. Developing foundational knowledge of different metals and their properties. Building a strong work ethic and attention to detail.
Junior Tool Room Machinist
2-4 yearsWorks with some supervision on less complex projects, such as creating simple jigs or repairing basic tooling components. Executes precise cuts and finishes according to specifications. Contributes to maintaining tool room inventory and equipment.
Key Focus Areas
Developing proficiency in operating various manual machines (lathes, mills, grinders) and beginning to learn CNC programming basics. Improving blueprint reading skills and understanding geometric dimensioning and tolerancing (GD&T). Enhancing problem-solving abilities for minor machining issues.
Tool Room Machinist
4-8 yearsIndependently designs, fabricates, and repairs complex tools, dies, molds, and fixtures. Makes critical decisions regarding machining processes, material selection, and tolerances. Often works on prototypes and custom components requiring high precision.
Key Focus Areas
Achieving mastery in both manual and CNC machining, including advanced programming and setup. Deepening knowledge of heat treatment, surface finishes, and specialized materials. Developing strong troubleshooting skills for complex tool failures and production challenges.
Senior Tool Room Machinist
8-12 yearsHandles the most intricate and critical tooling projects, often involving tight deadlines and exacting specifications. Provides technical guidance to other machinists and reviews their work for quality and accuracy. Contributes to the development of new tooling solutions and production methods.
Key Focus Areas
Specializing in advanced machining techniques like EDM or 5-axis machining. Developing expertise in tool design optimization for manufacturability and longevity. Mentoring junior machinists and contributing to process improvement initiatives. Pursuing certifications in metrology or advanced CAD/CAM.
Lead Tool Room Machinist
12-15 yearsLeads a team of machinists on major projects, coordinating tasks and ensuring adherence to timelines and quality standards. Acts as a primary technical resource, resolving complex machining and tooling issues. Participates in equipment selection and technology adoption decisions.
Key Focus Areas
Demonstrating strong leadership and project management skills. Developing a strategic understanding of tool room operations, including scheduling, resource allocation, and budget management. Enhancing communication skills for effective collaboration with engineering and production teams.
Tool Room Supervisor
15+ yearsManages the entire tool room operation, overseeing staff, equipment, and workflow. Responsible for budgeting, scheduling, and ensuring the tool room meets production demands and quality objectives. Implements new technologies and processes to enhance efficiency and capability.
Key Focus Areas
Cultivating exceptional leadership, team management, and operational planning abilities. Developing expertise in lean manufacturing principles and continuous improvement methodologies. Building strong interpersonal skills for managing personnel and stakeholder relationships.
Job Application Toolkit
Ace your application with our purpose-built resources:
Tool Room Machinist Resume Examples
Proven layouts and keywords hiring managers scan for.
View examplesTool Room Machinist Cover Letter Examples
Personalizable templates that showcase your impact.
View examplesTop Tool Room Machinist Interview Questions
Practice with the questions asked most often.
View examplesTool Room Machinist Job Description Template
Ready-to-use JD for recruiters and hiring teams.
View examplesGlobal Tool Room Machinist Opportunities
A Tool Room Machinist designs, fabricates, and repairs precision tools, dies, jigs, and fixtures. This role is globally vital for manufacturing, requiring specialized skills that translate across industrial economies. International demand remains stable, particularly in advanced manufacturing hubs in Germany, Japan, and the United States. Regulatory differences often involve safety standards and material specifications, but core machining principles are universal. Professionals seek international roles for exposure to diverse manufacturing techniques and higher earning potential in specific markets. Global certifications like ISO 9001 experience enhance mobility.
Global Salaries
Tool Room Machinist salaries vary significantly by region, reflecting local industrial demand and cost of living. In North America, a skilled Tool Room Machinist in the United States earns between $55,000 and $75,000 USD annually, while in Canada, salaries range from CAD 50,000 to CAD 70,000. These figures offer good purchasing power in most states and provinces.
European salaries show strong variations. In Germany, a Tool Room Machinist can expect EUR 40,000 to EUR 60,000 (approximately $43,000-$65,000 USD), providing excellent purchasing power due to a robust manufacturing sector and comprehensive social benefits. The UK offers GBP 30,000 to GBP 45,000 ($38,000-$57,000 USD), but London's high cost of living impacts real income. Scandinavia also offers competitive salaries, often with higher taxes but strong social welfare.
In Asia-Pacific, Japan pays JPY 4,000,000 to JPY 6,000,000 ($27,000-$40,000 USD), which offers moderate purchasing power. Australia presents AUD 60,000 to AUD 80,000 ($40,000-$53,000 USD), where higher wages often balance a higher cost of living. Tax implications differ greatly; for instance, some European countries have higher income taxes but offer universal healthcare, reducing out-of-pocket expenses compared to the US. Experience and specialized skills in CNC machining or CAD/CAM greatly influence compensation globally.
Remote Work
International remote work for a Tool Room Machinist is extremely limited. This role requires hands-on operation of machinery, precision measurement, and direct interaction with physical materials and tools. The core functions are inherently on-site.
However, some peripheral tasks can be remote. These include CAD/CAM programming, design reviews, or technical consulting. A machinist might remotely program CNC machines or design tools, sending files for local fabrication. Digital nomad opportunities are not applicable for the hands-on aspects of this role. Companies primarily hire Tool Room Machinists for on-site presence. Any remote components would likely be supplementary to a primary on-site role, not a standalone remote position. Salary expectations for remote design or programming work would differ significantly from on-site machining roles.
Visa & Immigration
Skilled worker visas are the primary pathway for Tool Room Machinists seeking international employment. Germany offers the Skilled Immigration Act, requiring recognized qualifications and a job offer. Canada's Express Entry system and Australia's Skilled Migration Program also list machining trades, often requiring skills assessments. The United States typically uses H-1B visas for specialized occupations, though direct Tool Room Machinist roles may fall under different categories like TN status for Canadians/Mexicans.
Education credential recognition is crucial; applicants often need their vocational training or diplomas evaluated by destination country authorities. Professional licensing is not typically required but industry certifications are valuable. Visa timelines vary from a few months to over a year. Language requirements depend on the country; Germany may require A2/B1 German, while English is standard for Anglophone countries. Permanent residency pathways often exist after several years of skilled employment. Some countries may offer expedited processing for in-demand trades. Family visas for dependents are usually available alongside the main applicant's visa.
2025 Market Reality for Tool Room Machinists
Understanding the current market realities for a Tool Room Machinist is crucial for career planning. The landscape has evolved significantly between 2023 and 2025, influenced by post-pandemic manufacturing shifts and the accelerating integration of automation and AI. Broader economic factors, such as supply chain resilience and industrial growth, directly impact the demand for precision tooling.
Market realities for Tool Room Machinists vary considerably by experience level, with senior machinists often commanding higher salaries and more stable opportunities. Geographic location also plays a significant role, as demand concentrates in manufacturing-heavy regions. The size and specialization of a company further dictate the specific skills sought. This analysis provides an honest assessment, helping machinists navigate these complex conditions.
Current Challenges
Tool Room Machinists face challenges from increased automation and CNC programming proficiency demands. Competition for experienced, highly skilled machinists remains strong, but entry-level roles see saturation. Economic slowdowns impact manufacturing sectors, reducing some hiring. Companies seek versatile machinists who adapt to new technologies, creating a skill gap for those focused solely on manual machining. Job searches for specialized roles can take longer due to precise skill matching.
Growth Opportunities
Despite challenges, significant opportunities exist for Tool Room Machinists in specific niches. Strong demand persists in industries requiring custom, high-precision components and prototypes, such as defense, aerospace, and medical device manufacturing. These sectors value machinists who can produce complex parts with exacting tolerances and unique material requirements.
Emerging opportunities lie in specialization with advanced CNC machining, 5-axis milling, and additive manufacturing integration. Machinists who master CAD/CAM software and can program intricate toolpaths gain a significant competitive advantage. Pursuing certifications in metrology, quality control, or specific machine types also enhances marketability. Underserved markets often exist in smaller, specialized manufacturing firms that require bespoke tooling solutions. Investing in continuous learning, particularly in automation and digital manufacturing techniques, positions machinists favorably for future roles.
Current Market Trends
Hiring for Tool Room Machinists in 2025 shows a nuanced picture. Demand remains stable for highly skilled individuals capable of intricate, low-volume, high-precision work, particularly in aerospace, medical devices, and specialized manufacturing. The push towards automation and advanced CNC machinery continues to reshape the role; employers increasingly seek machinists proficient in CAD/CAM software and G-code programming, not just manual operation.
Economic conditions have created some caution in general manufacturing, yet sectors requiring custom tooling and prototyping maintain consistent need. Generative AI impacts tool design and optimization, influencing the machinist's role towards validation and execution rather than initial concept generation. This shifts employer requirements towards a blend of traditional craftsmanship and digital literacy. Salary trends for highly skilled machinists are rising, reflecting the specialized knowledge required, while basic manual machinist roles see less growth and more competition.
Geographically, demand is stronger in regions with robust manufacturing hubs. Remote work is not applicable for this hands-on role, intensifying local market competition. Seasonal hiring patterns are less pronounced than in other fields, with consistent need for critical tooling support year-round. The market favors machinists who can troubleshoot complex setups, maintain tight tolerances, and adapt quickly to new material properties and machining techniques.
Emerging Specializations
Technological advancements and evolving manufacturing demands are continuously reshaping the role of a Tool Room Machinist. These shifts create novel specialization opportunities beyond traditional machining, requiring a forward-looking perspective.
Early positioning in these emerging areas is crucial for career advancement from 2025 onwards. Professionals who proactively acquire skills in these cutting-edge fields can command premium compensation and experience accelerated career growth. While established specializations remain vital, exploring nascent areas provides a strategic advantage.
Many emerging areas, particularly those integrating digital technologies, are on a rapid trajectory to become mainstream within the next three to five years, creating significant job opportunities. Specializing in these cutting-edge fields involves a balance of risk and reward; while demanding investment in new skills, the potential for market leadership and high demand is substantial.
Advanced Multi-Axis CNC Machining Specialist
Hybrid Manufacturing (Additive-Subtractive) Specialist
Robotics & Automation Integration Machinist
Precision Metrology & Quality Assurance Specialist
Advanced Materials Machining Specialist
Pros & Cons of Being a Tool Room Machinist
Understanding both the advantages and challenges of a career as a tool room machinist is crucial for making an informed decision. Career experiences vary significantly by company culture, industry sector, and the specific types of tools being produced. What one person considers a benefit, another might see as a drawback, depending on their personal values and lifestyle preferences. These pros and cons may also shift at different career stages, from an apprentice to a seasoned professional. This assessment aims to provide a realistic overview, helping readers set appropriate expectations for this specialized manufacturing role.
Pros
Tool room machinists possess highly specialized and valuable skills, making them indispensable in manufacturing and engineering industries that rely on custom tooling and precision components.
The work offers intellectual satisfaction through problem-solving, as machinists often interpret complex blueprints and devise efficient methods to produce intricate tools and fixtures.
Many tool room machinist roles offer a stable work environment, typically operating during standard business hours with less unpredictable overtime compared to production machining.
A sense of craftsmanship and pride comes from creating precision tools and dies from raw materials, directly contributing to the efficiency and innovation of manufacturing processes.
The demand for skilled tool room machinists remains consistent, as many manufacturing processes cannot be fully automated and still require human expertise for custom tool fabrication and maintenance.
Opportunities exist for continuous learning, as new materials, machining techniques, and CAD/CAM software regularly emerge, allowing machinists to expand their expertise and remain current.
Salaries for experienced tool room machinists are generally competitive, reflecting the high level of skill, precision, and experience required for the role, especially in industries like aerospace or medical devices.
Cons
The work often involves repetitive tasks for extended periods, which can lead to monotony and a lack of intellectual stimulation for those who prefer dynamic, varied work.
Exposure to loud machinery, metal dust, and cutting fluids is common, requiring strict adherence to safety protocols and potentially posing long-term health risks if proper precautions are not consistently followed.
A tool room machinist must possess a high level of precision and attention to detail; even minor errors can render a custom tool unusable, leading to significant pressure and rework.
Advancement opportunities within a tool room are often limited to becoming a lead machinist or supervisor, with fewer clear vertical career paths compared to design or engineering roles.
Tool room environments can be physically demanding, requiring standing for long hours, lifting heavy materials, and performing intricate work that strains eyesight and fine motor skills.
The demand for highly specialized tool room machinists can be susceptible to economic downturns or shifts in manufacturing strategies, potentially impacting job security in certain sectors.
Learning and mastering the craft takes years of hands-on experience, and formal education can be costly, making the entry barrier significant for those without access to apprenticeships or vocational training.
Frequently Asked Questions
Tool Room Machinists face unique questions about precision, specialized equipment, and problem-solving beyond standard production. This section addresses common concerns about mastering intricate setups, understanding advanced materials, and securing a stable, rewarding career in this highly skilled trade.
How long does it take to become a proficient Tool Room Machinist from scratch?
Becoming a job-ready Tool Room Machinist typically takes 2-5 years. This includes completing an apprenticeship program, which combines on-the-job training with classroom instruction, or earning a technical degree followed by practical experience. The depth of knowledge required for precision tooling means that continuous learning is a significant part of the career.
What educational qualifications or certifications are essential for this role?
While a formal degree is not always mandatory, completing an accredited apprenticeship or a vocational program in machining or tool and die making is highly recommended. These programs provide essential hands-on experience with various machines, materials, and measurement tools. Certifications from organizations like NIMS (National Institute for Metalworking Skills) can significantly enhance your resume and job prospects.
What are the typical salary expectations for an entry-level versus an experienced Tool Room Machinist?
Entry-level Tool Room Machinists can expect to earn a competitive hourly wage, often starting around $20-$25 per hour, depending on location and company size. With experience and specialized skills, such as expertise in CNC programming or specific tooling applications, experienced machinists can earn $30-$40+ per hour. Overtime opportunities are also common due to project demands.
Is the Tool Room Machinist role a secure career path, considering automation in manufacturing?
Tool Room Machinists enjoy strong job security due to the specialized nature of their work and the ongoing demand for custom parts, molds, and prototypes across various industries. While some manufacturing jobs face automation, the problem-solving and precision skills of a Tool Room Machinist are difficult to replicate by machines, ensuring a stable career path.
What are the typical career advancement opportunities for a Tool Room Machinist?
Career growth for a Tool Room Machinist can lead to several advanced roles. Many progress to become lead machinists, supervisors, or even move into design and engineering roles, leveraging their practical knowledge of manufacturing processes. Specializing in advanced CNC programming, CAD/CAM, or specific material sciences can also open doors to higher-paying, more technical positions.
What is the typical work-life balance like for a Tool Room Machinist?
The work-life balance for a Tool Room Machinist is generally stable, with most positions following regular business hours. However, project deadlines or urgent repairs may occasionally require extended hours, including evenings or weekends. Many shops operate on a single shift, providing consistent schedules, though some larger facilities might have multiple shifts.
What are the biggest day-to-day challenges a Tool Room Machinist faces?
The primary challenges include mastering highly precise measurements and tolerances, often working with complex geometries and exotic materials. You must also adapt to new technologies and programming languages as machinery evolves. Problem-solving skills are crucial for troubleshooting issues and optimizing manufacturing processes to meet exact specifications.
Can a Tool Room Machinist work remotely, or is it strictly an on-site position?
While some administrative or planning tasks might be done remotely, the core work of a Tool Room Machinist requires hands-on operation of machinery and direct interaction with materials and tooling. Therefore, this role is primarily on-site. However, some companies might offer hybrid roles for experienced machinists who can contribute to design or process optimization from a remote location.
Related Careers
Explore similar roles that might align with your interests and skills:
Machinist
A growing field with similar skill requirements and career progression opportunities.
Explore career guideTool Designer
A growing field with similar skill requirements and career progression opportunities.
Explore career guideToolmaker
A growing field with similar skill requirements and career progression opportunities.
Explore career guidePrecision Machinist
A growing field with similar skill requirements and career progression opportunities.
Explore career guideProduction Machinist
A growing field with similar skill requirements and career progression opportunities.
Explore career guideAssess your Tool Room Machinist readiness
Understanding where you stand today is the first step toward your career goals. Our Career Coach helps identify skill gaps and create personalized plans.
Skills Gap Analysis
Get a detailed assessment of your current skills versus Tool Room Machinist requirements. Our AI Career Coach identifies specific areas for improvement with personalized recommendations.
See your skills gapCareer Readiness Assessment
Evaluate your overall readiness for Tool Room Machinist roles with our AI Career Coach. Receive personalized recommendations for education, projects, and experience to boost your competitiveness.
Assess your readinessLand your dream job with Himalayas Plus
Upgrade to unlock Himalayas' premium features and turbocharge your job search.
Himalayas
Himalayas Plus
Himalayas Max
Find your dream job
Sign up now and join over 100,000 remote workers who receive personalized job alerts, curated job matches, and more for free!
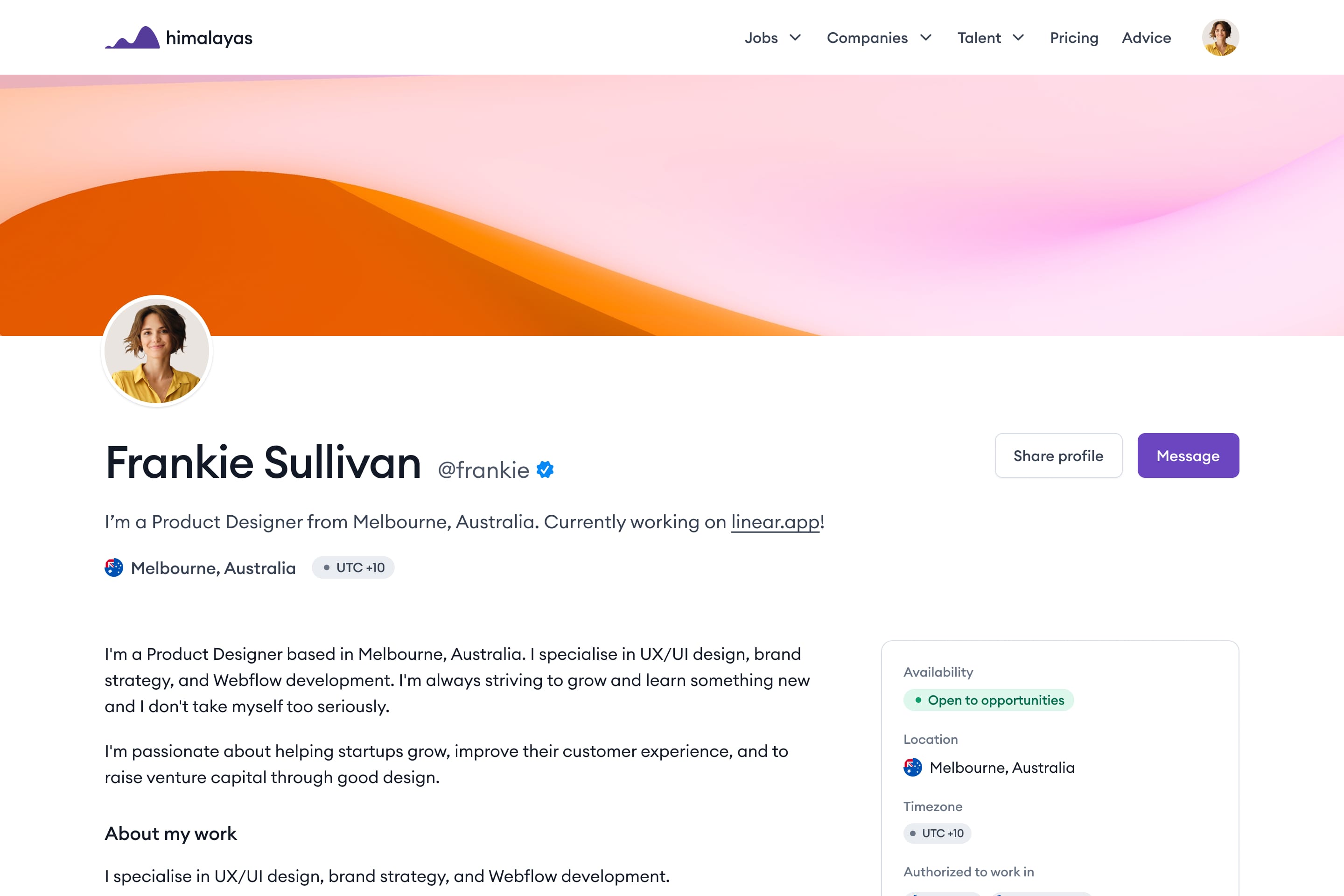