6 Toolmaker Interview Questions and Answers
Toolmakers are skilled craftsmen who create precision tools, dies, and molds used in manufacturing processes. They work with a variety of materials and machinery to produce components that meet exact specifications. Junior toolmakers focus on learning and assisting with basic tasks, while senior and master toolmakers handle complex projects, mentor others, and oversee quality control. Supervisors manage teams and ensure efficient production workflows. Need to practice for an interview? Try our AI interview practice for free then unlock unlimited access for just $9/month.
Unlimited interview practice for $9 / month
Improve your confidence with an AI mock interviewer.
No credit card required
1. Apprentice Toolmaker Interview Questions and Answers
1.1. Can you describe a project where you had to use precision measuring tools?
Introduction
This question is crucial as it assesses your hands-on experience with precision tools, which is essential for a toolmaker's role.
How to answer
- Start by briefly describing the project and its objectives
- Specify the precision measuring tools you used and why they were important
- Detail the steps you took to ensure accuracy
- Discuss any challenges you faced and how you overcame them
- Conclude with the results of your work and what you learned
What not to say
- Avoid vague descriptions without specific tools or techniques
- Don't focus solely on the outcome without explaining your process
- Refrain from discussing unrelated projects that do not highlight measuring skills
- Avoid exaggerating your role or contributions
Example answer
“During my internship at a local machine shop, I worked on a project to create a custom die for an automotive part. I used calipers and micrometers to measure parts to within 0.01mm accuracy. Faced with a miscalculation, I re-measured and adjusted my approach, ultimately delivering the die with a precision that passed all quality checks. This experience taught me the importance of meticulous attention to detail.”
Skills tested
Question type
1.2. How do you prioritize safety while working with tools and machinery?
Introduction
Safety is paramount in toolmaking. This question evaluates your awareness and practices regarding workplace safety.
How to answer
- Discuss your understanding of safety protocols and their importance
- Explain specific safety practices you follow while working with tools
- Share an example of a time you identified a potential safety hazard
- Describe how you would handle a situation where safety protocols were not being followed
- Emphasize your commitment to maintaining a safe working environment
What not to say
- Downplaying the importance of safety in the workplace
- Failing to provide concrete examples of safety practices
- Suggesting that safety measures slow down productivity
- Neglecting to mention the role of teamwork in safety
Example answer
“In my training, I learned that safety is non-negotiable. I always wear personal protective equipment and ensure my workspace is organized to prevent accidents. Once, I noticed a colleague not wearing their safety goggles while operating a machine. I reminded them of the safety protocols, and we discussed the potential risks. I believe that fostering a culture of safety is everyone's responsibility.”
Skills tested
Question type
2. Junior Toolmaker Interview Questions and Answers
2.1. Can you describe a project where you had to use precision measurement tools to create a component?
Introduction
This question is important for assessing your technical skills and understanding of precision in toolmaking, which is critical for ensuring quality in manufactured components.
How to answer
- Begin with a brief overview of the project and its objectives.
- Detail the specific measurement tools you utilized (e.g., calipers, micrometers).
- Explain how you ensured accuracy in your measurements and adjustments.
- Discuss any challenges you encountered and how you overcame them.
- Conclude with the outcome of the project and any lessons learned.
What not to say
- Providing vague answers without specifics on tools or methods.
- Failing to mention the importance of precision in the context of the project.
- Ignoring any challenges faced or lessons learned.
- Overemphasizing the use of machinery without discussing measurement.
Example answer
“In my previous internship at a manufacturing company, I worked on a project to produce a series of precision gears. I used calipers and micrometers to ensure that each component met strict specifications. During the project, I found that one of the gears was slightly out of tolerance. I recalibrated my tools and adjusted the machining process, ultimately achieving an accuracy of ±0.01mm. This experience taught me the importance of double-checking measurements and the role of precision in toolmaking.”
Skills tested
Question type
2.2. Describe a time when you had to work as part of a team to complete a project. What was your role?
Introduction
This question evaluates your teamwork skills and your ability to collaborate effectively, which are crucial in a workshop environment where toolmakers often depend on each other to achieve project goals.
How to answer
- Set the scene by describing the project and the team's objectives.
- Clearly define your role within the team and the specific contributions you made.
- Highlight how you communicated and collaborated with team members.
- Discuss any conflicts that arose and how you resolved them.
- Explain the overall outcome of the project and what you learned about teamwork.
What not to say
- Taking sole credit for the team's success without acknowledging others.
- Focusing only on personal achievements rather than team dynamics.
- Neglecting to mention any challenges or how they were overcome.
- Describing a negative experience without reflecting on what you learned.
Example answer
“During my apprenticeship, I was part of a team tasked with redesigning a tool for a client. My role was to assist in the design phase, where I collaborated closely with the lead toolmaker. We held regular meetings to discuss progress and challenges. When we faced a design flaw, I suggested a modification based on my understanding of the machining process, which helped us move forward. The project was completed on time, and I learned how vital clear communication is in a team setting.”
Skills tested
Question type
2.3. How do you ensure safety and compliance when working with tools and machinery?
Introduction
This question is crucial for understanding your awareness of safety protocols and compliance regulations, which are paramount in the toolmaking industry to prevent accidents and ensure a safe working environment.
How to answer
- Discuss your knowledge of safety regulations and company policies.
- Explain your personal practices for ensuring safety (e.g., wearing protective gear, following protocols).
- Provide an example of a time you identified a safety hazard and how you addressed it.
- Mention the importance of training and continuous improvement in safety practices.
- Conclude with your commitment to maintaining a safe working environment.
What not to say
- Underestimating the importance of safety protocols.
- Suggesting that safety is someone else's responsibility.
- Failing to provide specific examples of safety practices.
- Ignoring the role of training and compliance in safety measures.
Example answer
“Safety is my top priority when working with tools and machinery. I always wear appropriate protective gear and adhere to the safety protocols established by my previous employer. Once, while working on a milling machine, I noticed that a guard was missing, which posed a risk. I immediately reported it to my supervisor and ensured the machine was taken out of operation until it was fixed. I believe that ongoing training and a culture of safety can prevent accidents and promote a secure workplace.”
Skills tested
Question type
3. Toolmaker Interview Questions and Answers
3.1. Can you describe a challenging toolmaking project you worked on and how you overcame the difficulties?
Introduction
This question assesses your problem-solving skills, technical expertise, and ability to work under pressure, which are critical for a toolmaker.
How to answer
- Outline the specifics of the project, including the type of tools involved and their intended application
- Explain the challenges you faced, such as material constraints or design issues
- Detail the steps you took to analyze and resolve the problem
- Highlight any innovative solutions or techniques you applied
- Conclude with the outcome and any lessons learned from the experience
What not to say
- Avoid being vague about the challenges or your role in the project
- Don't focus solely on technical details without discussing problem-solving
- Avoid placing blame on others for difficulties encountered
- Steer clear of generic responses that lack specific examples
Example answer
“In my role at Tata Precision Tools, I faced a significant challenge when designing a precision die for a new automotive part. The initial design led to frequent alignment issues during production. I conducted a thorough analysis and collaborated with my team to redesign the die using a different material that improved stability. This adjustment not only resolved the alignment issues but also reduced production time by 20%. I learned the importance of iterative design and collaboration.”
Skills tested
Question type
3.2. How do you ensure precision and quality in your toolmaking processes?
Introduction
This question evaluates your attention to detail and understanding of quality control processes, which are vital for any toolmaker.
How to answer
- Describe the specific techniques and tools you use to maintain precision
- Explain your quality control measures at different stages of tool production
- Mention any relevant certifications or standards you adhere to
- Discuss how you handle errors or deviations in the production process
- Share examples of how your focus on quality improved outcomes in previous work
What not to say
- Avoid saying that quality is simply a matter of luck or intuition
- Don't provide vague answers without specific examples of quality measures
- Steer clear of suggesting that quality control is someone else's responsibility
- Avoid discussing only past successes without acknowledging challenges
Example answer
“I utilize precision measuring tools such as calipers and micrometers at every stage of the toolmaking process. My commitment to quality involves regular inspections and compliance with ISO standards. For instance, at HMT Limited, I implemented a checklist system that caught potential defects early, reducing rework by 30%. Quality is a collective effort, and I ensure my team is trained in best practices.”
Skills tested
Question type
4. Senior Toolmaker Interview Questions and Answers
4.1. Can you describe a complex toolmaking project you oversaw from start to finish?
Introduction
This question is crucial for assessing your technical expertise, project management skills, and ability to see a project through from concept to completion, which is essential for a Senior Toolmaker.
How to answer
- Begin with the project's scope and objectives, explaining its complexity
- Detail your role and responsibilities during the project
- Discuss the tools and technologies you utilized
- Highlight any challenges faced and how you overcame them
- Conclude with the project's outcome and any measurable results
What not to say
- Discussing a project without specifying your contributions
- Focusing solely on the technical aspects without mentioning teamwork or leadership
- Neglecting to address any challenges faced
- Providing vague results that lack quantifiable metrics
Example answer
“At Bosch, I led a team on a project to develop a new injection mold for a high-precision automotive component. I coordinated with design engineers to finalize specifications and used advanced CAD software for modeling. We faced issues with material shrinkage, but by adjusting the cooling system, we improved dimensional accuracy by 20%. The final mold reduced production time by 15%, significantly improving efficiency.”
Skills tested
Question type
4.2. How do you ensure quality control in your toolmaking processes?
Introduction
Quality control is vital in toolmaking to ensure precision and efficiency. This question assesses your knowledge of quality assurance processes and your attention to detail.
How to answer
- Describe the quality control methods you implement during production
- Explain how you train team members on quality standards
- Discuss any tools or technologies you use for quality assurance
- Share examples of how your quality control measures improved outcomes
- Mention any certifications or standards you adhere to
What not to say
- Suggesting quality control is someone else's responsibility
- Providing a generic answer that lacks specific processes
- Overlooking the importance of continuous improvement
- Ignoring the role of team training in quality assurance
Example answer
“At Siemens, I implemented a multistage quality control process for our tooling operations. This included regular inspections using precision measuring instruments and training sessions for the team on ISO standards. By integrating real-time monitoring software, we reduced defects by 30% over six months, leading to significant cost savings.”
Skills tested
Question type
5. Master Toolmaker Interview Questions and Answers
5.1. Can you describe a complex tooling project you worked on and the challenges you faced?
Introduction
This question assesses your technical expertise, problem-solving skills, and ability to manage complex projects, which are vital for a Master Toolmaker.
How to answer
- Use the STAR method (Situation, Task, Action, Result) to structure your response.
- Clearly explain the project scope and objectives.
- Detail the specific challenges you encountered and how you addressed them.
- Discuss the tools and techniques you used in the process.
- Quantify the success of the project with measurable outcomes.
What not to say
- Focusing only on the technical aspects without discussing challenges.
- Failing to explain how you overcame difficulties.
- Ignoring team dynamics or collaboration if applicable.
- Not providing specific metrics or results to demonstrate success.
Example answer
“At a precision manufacturing company, I led a project to design a complex injection mold for a new automotive part. We faced unexpected tolerances that required re-engineering the design. By collaborating closely with the design team and utilizing advanced CAD software, we revised the mold and reduced production time by 20%. The project was completed on schedule, leading to a 15% increase in production efficiency.”
Skills tested
Question type
5.2. How do you ensure quality control in your tooling processes?
Introduction
This question evaluates your understanding of quality assurance practices and your ability to maintain high standards, which are crucial in the toolmaking industry.
How to answer
- Describe the quality control measures you implement at each stage of the tooling process.
- Discuss how you train and guide team members on quality standards.
- Provide examples of tools or methods you use for quality checks, such as gauges or measurement systems.
- Explain how you handle defects and ensure corrective actions are taken.
- Mention any certifications or standards you adhere to in your quality control processes.
What not to say
- Neglecting to mention specific quality control methods.
- Implying that quality control is someone else's responsibility.
- Failing to provide examples of past quality issues and how you resolved them.
- Overlooking the importance of continuous improvement.
Example answer
“I implement a rigorous quality control process that includes regular inspections at each tooling stage. I use coordinate measuring machines (CMM) to ensure precision and train my team on the importance of adhering to specifications. When we encountered a defect in a mold, I led a root cause analysis and adjusted our processes, resulting in a 30% reduction in defects in the next production run.”
Skills tested
Question type
5.3. What innovations have you introduced in your tooling practices, and what impact did they have?
Introduction
This question looks at your creativity and ability to drive improvements in tooling processes, which are essential traits for a Master Toolmaker.
How to answer
- Describe specific innovations you have implemented in your tooling practices.
- Explain the rationale behind these innovations and the problems they addressed.
- Quantify the results of your innovations, such as time saved or cost reductions.
- Discuss how you communicated and implemented these changes with your team.
- Highlight any recognition or feedback received from stakeholders regarding your innovations.
What not to say
- Providing vague or general ideas without specific examples.
- Focusing on innovations that did not succeed without discussing learning outcomes.
- Failing to connect innovations to measurable impacts.
- Neglecting to mention collaboration with others in the innovation process.
Example answer
“I introduced a new CNC programming technique that incorporated adaptive machining for a complex part we were producing. This innovation reduced cycle time by 25% and improved tool life significantly. I shared this technique with my team through workshops, which fostered a culture of continuous improvement in our shop. As a result, we were recognized with an internal award for operational excellence.”
Skills tested
Question type
6. Toolmaking Supervisor Interview Questions and Answers
6.1. Can you describe a situation where you had to resolve a conflict between team members on the shop floor?
Introduction
This question is crucial for a Toolmaking Supervisor as it assesses your conflict resolution skills and ability to maintain a harmonious work environment, which is essential for productivity and team morale.
How to answer
- Use the STAR method to outline the situation, task, action, and result
- Clearly explain the nature of the conflict and its impact on the team's performance
- Describe the specific steps you took to mediate the situation
- Highlight the resolution and how it improved team dynamics or productivity
- Mention any follow-up actions you took to prevent future conflicts
What not to say
- Avoid blaming one party without acknowledging your role in the situation
- Do not provide vague examples that lack specific details
- Refrain from suggesting that conflict is not part of team dynamics
- Avoid discussing conflicts without demonstrating a resolution
Example answer
“In my previous role at a manufacturing plant, two machinists had a disagreement over tool usage that was affecting their productivity. I facilitated a meeting where both could express their perspectives. By mediating the discussion and establishing a shared understanding of tool responsibilities, we not only resolved the conflict but also implemented a new tool usage policy that improved efficiency by 20%. This experience taught me the importance of addressing conflicts directly and fostering open communication.”
Skills tested
Question type
6.2. How do you ensure that your team meets production deadlines while maintaining quality standards?
Introduction
This question evaluates your ability to balance efficiency and quality, which is vital in supervisory roles within toolmaking where precision is crucial.
How to answer
- Discuss your planning and scheduling techniques
- Explain how you prioritize tasks and allocate resources effectively
- Share methods you use to monitor progress and quality control
- Describe how you motivate your team to meet deadlines while maintaining quality
- Provide examples of successful outcomes from past experiences
What not to say
- Claiming that deadlines are more important than quality
- Not mentioning any specific tools or methodologies for tracking progress
- Being vague about your leadership style under pressure
- Overlooking team dynamics in achieving production goals
Example answer
“At ABC Tooling, I implemented a project management software that allowed us to track production timelines and quality metrics in real-time. By setting clear milestones and conducting regular check-ins, my team was able to meet a critical deadline for a major client while achieving a 98% quality pass rate. I believe that fostering a culture of accountability and continuous improvement is key to balancing deadlines and quality.”
Skills tested
Question type
Similar Interview Questions and Sample Answers
Simple pricing, powerful features
Upgrade to Himalayas Plus and turbocharge your job search.
Himalayas
Himalayas Plus
Himalayas Max
Find your dream job
Sign up now and join over 100,000 remote workers who receive personalized job alerts, curated job matches, and more for free!
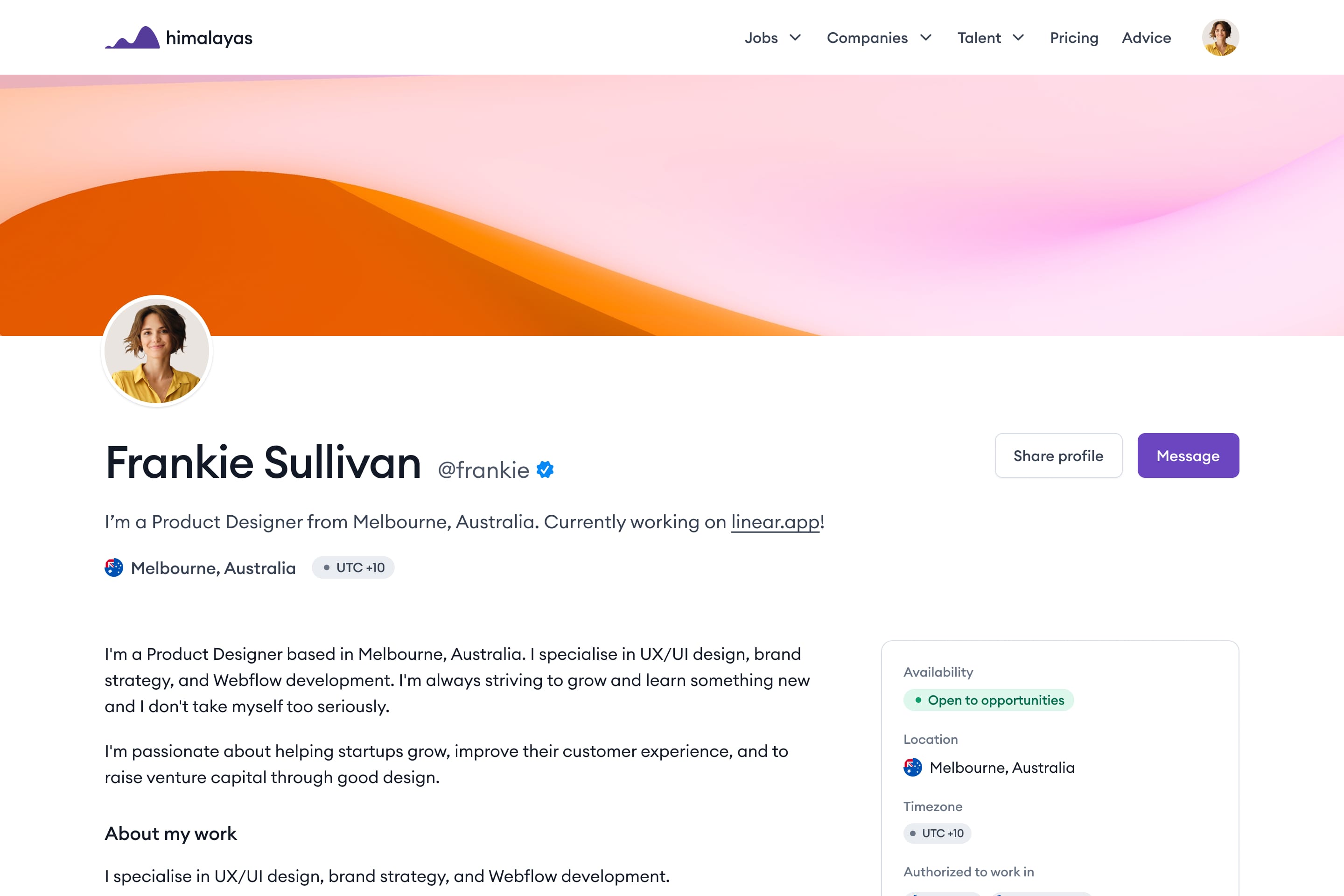