Complete Machinist Career Guide
Machinists are the skilled artisans who bring engineering designs to life, transforming raw materials into precision components for everything from aerospace to medical devices. They operate sophisticated machinery, often computer-controlled, to craft parts with extreme accuracy, a critical skill in modern manufacturing. This hands-on career offers a tangible sense of accomplishment and a pathway to expertise in a vital industry.
Key Facts & Statistics
Median Salary
$51,320 USD
(U.S. Bureau of Labor Statistics, May 2023)
Range: $35k - $75k+ USD, depending on experience and specialization
Growth Outlook
1%
as fast as average (U.S. Bureau of Labor Statistics, 2022-2032)
Annual Openings
≈30k
openings annually (U.S. Bureau of Labor Statistics, 2022-2032)
Top Industries
Typical Education
High school diploma or equivalent, often followed by a postsecondary certificate, associate's degree, or apprenticeship
What is a Machinist?
A Machinist is a skilled tradesperson who creates precision parts and components from raw materials, such as metal, plastic, or composites, using machine tools. They operate a variety of equipment, from traditional manual lathes and milling machines to advanced Computer Numerical Control (CNC) machines, to cut, shape, and finish materials according to engineering blueprints and specifications.
This role is distinct from a machine operator, who primarily loads and unloads parts and presses buttons on pre-programmed machines. A Machinist possesses a deeper understanding of machining processes, material properties, and precision measurement. They are responsible for setting up machines, selecting cutting tools, calculating dimensions and tolerances, programming CNC machines, and performing quality checks to ensure the fabricated parts meet exact standards, often with tolerances measured in thousandths of an inch.
What does a Machinist do?
Key Responsibilities
- Read and interpret blueprints, schematics, and engineering drawings to understand part specifications and tolerances.
- Set up and operate manual and CNC (Computer Numerical Control) machines, including lathes, mills, grinders, and drill presses.
- Monitor machine operations to detect malfunctions or out-of-tolerance machining, making adjustments as needed.
- Inspect finished products for conformance to specifications, using precision measuring instruments like calipers, micrometers, and gauges.
- Perform routine maintenance on machinery, such as cleaning, lubricating, and checking fluid levels, to ensure optimal performance.
- Calculate dimensions and tolerances using knowledge of mathematics and instruments such as micrometers and calipers.
- Select, align, and secure holding fixtures, cutting tools, attachments, accessories, and materials onto machines, preparing for operations and ensuring safety standards are met.
Work Environment
Machinists typically work in manufacturing plants, workshops, or production facilities. These environments are often noisy due to operating machinery and may require standing for long periods. Safety is a major concern, necessitating the use of personal protective equipment (PPE) such as safety glasses, ear protection, and steel-toed boots.
The work can be physically demanding, involving lifting materials and operating heavy equipment. While some tasks are solitary, machinists often collaborate with engineers, quality control specialists, and other production staff. Work schedules are usually full-time, often including shifts outside of normal business hours, such as evenings or weekends, especially in facilities with continuous production. The pace is steady, requiring meticulous attention to detail and adherence to strict deadlines.
Tools & Technologies
Machinists primarily use a variety of precision machinery including manual lathes, milling machines, surface grinders, and drill presses. Increasingly, they operate and program CNC (Computer Numerical Control) machines, which require proficiency with CAD/CAM software (like Fusion 360, Mastercam, SolidWorks CAM) for designing and generating toolpaths. They also utilize precision measuring instruments such as micrometers, calipers, bore gauges, height gauges, and optical comparators to verify part dimensions and ensure quality.
Beyond machinery, machinists work with a range of cutting tools, workholding devices, and coolants. They also use hand tools for deburring and finishing, and general workshop tools for maintenance and setup. Familiarity with machine control interfaces, G-code, and M-code is essential for CNC operation. The specific tools can vary significantly depending on the industry, from aerospace and medical device manufacturing to automotive and general fabrication.
Machinist Skills & Qualifications
A Machinist's qualifications are primarily built on practical experience and demonstrated proficiency. While formal education provides a strong theoretical foundation, hands-on ability and a keen understanding of precision manufacturing processes are paramount. Entry-level positions often require vocational training or an apprenticeship, which can be more valuable than a traditional four-year degree for immediate shop floor readiness.
Requirements vary significantly by company size and the type of manufacturing. Smaller job shops might seek generalists skilled in operating various manual and CNC machines, while larger aerospace or medical device manufacturers demand specialists with expertise in specific materials, complex geometries, or advanced CNC programming. Seniority directly correlates with the need for independent problem-solving, advanced setup capabilities, and leadership skills. Machinists in regulated industries, like aerospace or medical, face stricter quality control and documentation requirements.
Certifications, such as those from the National Institute for Metalworking Skills (NIMS), significantly enhance a Machinist's marketability and validate specific competencies. These certifications often carry more weight than academic degrees in the hiring process for shop floor roles. The skill landscape evolves with automation and advanced materials; Machinists must continuously adapt to new CNC technologies, CAD/CAM software, and precision measurement tools. Balancing broad machining knowledge with deep expertise in specific areas, like 5-axis machining or EDM, determines career trajectory. Misconceptions include believing that all machining is manual; modern machining heavily relies on computer-controlled equipment.
Education Requirements
Technical Skills
- Blueprint Reading and GD&T (Geometric Dimensioning and Tolerancing)
- Manual Machining (Lathe, Mill, Grinder operation)
- CNC Machine Operation (Setup, Tooling, Offsets)
- CNC Programming (G-code, M-code, conversational programming)
- CAD/CAM Software Proficiency (e.g., Mastercam, Fusion 360, SolidWorks CAM)
- Precision Measurement Tools (Calipers, Micrometers, Height Gages, CMM)
- Material Science (Metals, Plastics, Composites properties)
- Tooling Selection and Application
- Quality Control Procedures and Inspection
- Machine Maintenance and Troubleshooting
- Fixture Design and Setup
- Advanced Machining Techniques (e.g., 5-axis machining, EDM, grinding)
Soft Skills
- Attention to Detail: Critical for ensuring parts meet precise specifications and for identifying minute defects.
- Problem-Solving: Essential for troubleshooting machine malfunctions, optimizing cutting parameters, and resolving quality issues.
- Spatial Reasoning: Necessary to visualize complex part geometries from blueprints and understand tool paths in 3D space.
- Mechanical Aptitude: Important for understanding how machines work, performing maintenance, and diagnosing operational problems.
- Patience: Required for meticulous setups, intricate machining operations, and repetitive quality checks.
- Safety Consciousness: Crucial for operating dangerous machinery responsibly and adhering to strict shop safety protocols.
- Adaptability: Important for learning new machine technologies, programming languages, and manufacturing processes.
- Communication: Vital for collaborating with engineers, quality control, and other team members on project requirements and issues, and for documenting work accurately, especially in regulated environments like aerospace or medical manufacturing, which require clear, precise communication regarding procedures and observations.
How to Become a Machinist
Entering the machinist field offers several practical pathways, ranging from formal education to on-the-job training. While traditional apprenticeships remain a strong route, many now find success through vocational programs or community college degrees in machine tool technology. The timeline to becoming a proficient machinist can vary; a complete beginner might spend 1-2 years in a program or apprenticeship, while someone with related mechanical experience could transition faster, perhaps within 6-12 months.
Entry strategies often depend on the local industrial landscape. Large manufacturing hubs might favor candidates from established vocational schools, while smaller, specialized machine shops could prioritize hands-on experience gained through entry-level roles like machine operator or shop helper. Misconceptions exist, such as believing a four-year degree is necessary; instead, practical skills, precision, and problem-solving abilities are far more valued. Building a portfolio of personal projects or demonstrating proficiency on various machines through practical tests often outweighs academic credentials alone.
Networking within local manufacturing communities, attending industry trade shows, and connecting with experienced machinists can open doors to mentorship and job opportunities not widely advertised. The hiring landscape values adaptability and a willingness to learn new technologies, as modern machining increasingly integrates computer-aided manufacturing (CAM) and automation. Overcoming entry barriers often involves demonstrating a strong work ethic and a genuine passion for precision craftsmanship, even if formal experience is limited.
Step 1
Step 2
Step 3
Step 4
Step 5
Education & Training Needed to Become a Machinist
The educational landscape for a Machinist emphasizes practical skills and hands-on experience, often more so than traditional academic degrees. Formal degree programs, like Associate of Applied Science (AAS) in Machine Tool Technology, typically take two years and can cost between $10,000 and $25,000 at community colleges. These programs provide a strong theoretical foundation in blueprint reading, CAD/CAM, and various machining processes, alongside significant lab work. Graduates gain a well-rounded understanding of the trade.
Alternatively, apprenticeships offer a direct pathway, combining paid on-the-job training with classroom instruction. These typically last 3-5 years, with costs often covered by the employer or significantly subsidized. Apprenticeships are highly valued by employers, as they produce workers with immediate, relevant experience. Vocational and technical school programs, ranging from 6 months to 18 months, focus on specific machine operations and safety, with costs from $5,000 to $15,000. Self-study, often through online courses and manuals, can supplement formal training but rarely suffices as a standalone path for entry-level roles, requiring significant self-discipline and access to equipment for practice.
Employer acceptance varies; while some advanced manufacturing roles prefer AAS degrees for their theoretical depth, many shops highly value certified apprentices for their proven practical proficiency. Continuous learning is crucial for Machinists, especially with the rapid evolution of CNC technology and automation. Specializations like CNC programming, precision grinding, or advanced materials handling require ongoing professional development and certifications. The cost-benefit analysis favors pathways that blend theoretical knowledge with extensive hands-on practice, as practical experience remains paramount for career advancement in machining.
Machinist Salary & Outlook
Compensation for a Machinist varies significantly based on several factors, reflecting the precision and specialized skills required for the role. Geographic location plays a crucial role; areas with a high concentration of manufacturing, aerospace, or automotive industries often offer higher wages due to increased demand and competitive markets. For example, states like Michigan, Ohio, and California typically present different earning potentials compared to regions with less industrial activity.
Years of experience dramatically influence salary. An Apprentice Machinist starting their career will earn less than a Master Machinist with decades of expertise and specialized certifications. Expertise in advanced CNC programming, CAD/CAM software, or working with exotic materials can command premium compensation. Total compensation extends beyond base salary to include overtime pay, which is common in manufacturing, and sometimes performance bonuses. Comprehensive benefits packages, including health insurance, retirement plans like 401(k)s, and tool allowances, significantly add to the overall value of the compensation.
Industry-specific trends also shape machinist salaries. The aerospace and defense sectors often offer higher pay due to the stringent precision and critical nature of their components. In contrast, general manufacturing may have a different pay scale. Remote work opportunities are rare for machinists, as the role requires hands-on operation of machinery. However, some highly specialized programming or design roles might allow for partial remote work, influencing geographic arbitrage. International markets also present varied compensation, but the figures provided here are in USD, primarily reflecting the US market.
Salary by Experience Level
Level | US Median | US Average |
---|---|---|
Apprentice Machinist | $38k USD | $40k USD |
Junior Machinist | $50k USD | $52k USD |
Machinist | $63k USD | $65k USD |
Senior Machinist | $75k USD | $78k USD |
Lead Machinist | $85k USD | $88k USD |
Master Machinist | $97k USD | $100k USD |
Market Commentary
The job market for Machinists shows steady demand, driven by the ongoing need for precision manufacturing across various industries. Projections indicate a stable outlook, with the Bureau of Labor Statistics forecasting a slight increase in employment for machinists and tool and die makers through 2032. This growth is primarily fueled by the resurgence of domestic manufacturing, supply chain diversification efforts, and continued technological advancements in machinery.
Emerging opportunities for machinists increasingly involve operating and programming advanced Computer Numerical Control (CNC) machines. This requires a blend of traditional machining skills with strong computer literacy and problem-solving abilities. The demand for machinists proficient in CAD/CAM software and additive manufacturing (3D printing) is also rising, as these technologies become integrated into production workflows. Companies seek candidates who can adapt to new automation and robotic integration within manufacturing processes.
Supply and demand dynamics for skilled machinists often show a shortage of qualified candidates, particularly those with advanced CNC programming and troubleshooting expertise. This imbalance typically results in competitive wages and stable employment for experienced professionals. While automation and AI are transforming manufacturing, they are more likely to augment the machinist role rather than replace it entirely. Machinists will increasingly focus on overseeing automated systems, complex setups, and quality control. Geographic hotspots for machinists include the Midwest and Southeast United States, driven by robust automotive, aerospace, and general manufacturing industries. Continuous learning in new technologies and materials is crucial for future-proofing a machinist career.
Machinist Career Path
Career progression for a Machinist typically involves a structured journey from foundational learning to advanced specialization and leadership. Individuals begin with extensive hands-on training, gradually mastering complex machinery and precision techniques. Advancement often depends on demonstrated skill, accuracy, and the ability to work with diverse materials and specifications.
The field offers both individual contributor (IC) tracks, where machinists become highly specialized experts, and potential leadership pathways into roles like Lead Machinist or Master Machinist, involving mentorship and process optimization. Performance, continuous skill development, and the willingness to learn new technologies significantly influence advancement speed. Company size and industry sector also play a role; larger manufacturing firms may offer more structured advancement, while smaller shops might provide broader exposure.
Lateral movement often involves specializing in areas like CNC programming, tool and die making, or quality control. Networking within the manufacturing community and seeking mentorship from experienced machinists are crucial for professional growth. Certifications in specific machining processes or CAD/CAM software can mark significant milestones and open new opportunities, enhancing a machinist's reputation and expertise.
Apprentice Machinist
0-2 yearsKey Focus Areas
Junior Machinist
2-4 yearsKey Focus Areas
Machinist
4-7 yearsKey Focus Areas
Senior Machinist
7-10 yearsKey Focus Areas
Lead Machinist
10-15 yearsKey Focus Areas
Master Machinist
15+ yearsKey Focus Areas
Apprentice Machinist
0-2 yearsWorks under direct supervision, assisting experienced machinists with machine setup and operation. Primarily focuses on learning fundamental machining processes and shop procedures. Performs routine tasks such as material loading, deburring, and basic quality checks. Decisions are strictly guided by supervisors.
Key Focus Areas
Develop a strong understanding of machine shop safety protocols. Master basic machine operation, including manual lathes, mills, and grinders. Learn to read blueprints and technical drawings accurately. Focus on foundational measurement techniques and tool identification.
Junior Machinist
2-4 yearsOperates various manual and entry-level CNC machines with limited supervision, performing more complex cuts and finishes. Responsible for ensuring parts meet specified dimensions and quality standards. Collaborates with senior machinists on project execution and troubleshooting. Takes responsibility for individual machine maintenance tasks.
Key Focus Areas
Improve precision in machining operations and reduce setup times. Gain proficiency in operating a wider range of manual and basic CNC machines. Develop problem-solving skills for common machining challenges. Begin understanding material properties and their impact on machining.
Machinist
4-7 yearsIndependently sets up and operates a variety of complex manual and CNC machines to produce precision parts. Interprets intricate blueprints and selects appropriate tooling and machining strategies. Makes independent decisions regarding process adjustments to maintain quality and efficiency. Often works on critical components or prototypes.
Key Focus Areas
Master advanced machining techniques and complex setups for both manual and CNC equipment. Develop strong troubleshooting skills for machine malfunctions and production issues. Understand G-code and M-code for CNC programming adjustments. Focus on optimizing machining processes for efficiency.
Senior Machinist
7-10 yearsLeads complex machining projects, often involving tight tolerances and exotic materials. Provides technical guidance and mentorship to junior machinists on challenging setups and operations. Independently identifies and resolves complex machining problems, optimizing production workflows. Contributes to tooling selection and process design decisions.
Key Focus Areas
Specialize in specific machining processes or materials, becoming a subject matter expert. Develop advanced CNC programming skills, including CAM software utilization. Enhance leadership potential by informally guiding junior team members. Focus on process improvement and waste reduction.
Lead Machinist
10-15 yearsOversees a small team of machinists, assigning tasks, providing training, and ensuring production targets are met. Acts as the primary point of contact for technical issues and provides hands-on assistance for difficult setups. Responsible for maintaining machine uptime and ensuring adherence to safety and quality standards. Participates in capacity planning.
Key Focus Areas
Develop strong leadership and communication skills to manage a team. Master production scheduling and workflow optimization. Gain expertise in quality control methodologies and advanced inspection techniques. Focus on continuous improvement initiatives and cross-training.
Master Machinist
15+ yearsServes as the ultimate technical authority and expert in all machining operations. Designs and implements advanced manufacturing processes, often leading R&D projects for new machining techniques. Provides high-level consultation and strategic guidance on tooling, machine acquisition, and production optimization. Mentors all levels of machinists and influences overall shop strategy.
Key Focus Areas
Achieve comprehensive mastery of all machining disciplines and advanced manufacturing technologies. Develop strategic thinking for long-term production planning and resource allocation. Cultivate exceptional problem-solving skills for highly complex, systemic issues. Focus on innovation and adopting new industry standards.
Job Application Toolkit
Ace your application with our purpose-built resources:
Global Machinist Opportunities
Machinists find global demand as manufacturing evolves. This profession translates across countries, adapting to local industry standards while maintaining core skills in precision machining.
Global demand remains strong in 2025, particularly in advanced manufacturing hubs. Regulatory differences often involve safety standards and equipment certifications.
Many machinists consider international moves for better pay or specialized industry exposure. International certifications, such as ISO or specific machine operation licenses, can improve global mobility.
Global Salaries
Machinist salaries vary significantly worldwide, reflecting economic conditions and manufacturing sophistication. In North America, a skilled machinist earns between $45,000 and $70,000 USD annually in countries like the United States or Canada. Entry-level positions start lower, while experienced professionals with specialized CNC skills command higher wages.
European countries offer diverse salary landscapes. In Germany, a machinist typically earns €35,000 to €55,000 ($38,000-$60,000 USD), benefiting from strong social welfare programs and extensive vacation time. The UK sees salaries from £28,000 to £45,000 ($35,000-$57,000 USD). Southern European nations like Spain or Italy have lower nominal salaries but often better purchasing power due to a lower cost of living.
Asia-Pacific markets, especially in developed economies like Japan or South Korea, offer competitive salaries ranging from ¥4,000,000 to ¥6,500,000 ($27,000-$44,000 USD) or ₩40,000,000 to ₩60,000,000 ($30,000-$45,000 USD) respectively. These regions often provide comprehensive health benefits and performance-based bonuses. In contrast, emerging markets may offer lower nominal salaries but still represent good local purchasing power.
Latin America's machinist salaries are generally lower, often between $15,000 and $30,000 USD in countries like Mexico or Brazil, but the cost of living is also considerably less. Tax implications and take-home pay vary widely, with some European countries having higher income tax rates but more extensive public services. Experience and specific certifications, such as a Red Seal in Canada or advanced CNC programming skills, significantly boost earning potential internationally.
Remote Work
International remote work for a machinist is highly limited due to the hands-on nature of the role. Machinists operate physical machinery that requires a dedicated workshop or factory environment. Digital nomad opportunities are not applicable for this profession.
Some related tasks, such as CAD/CAM programming or design, can occur remotely. However, the core responsibilities of machine operation, setup, and maintenance necessitate physical presence. Companies hiring machinists globally focus on on-site roles rather than remote arrangements.
Therefore, salary expectations for machinists are tied to the local geographic market where the manufacturing takes place. Geographic arbitrage is generally not a factor for this role. Equipment requirements are industrial and cannot be replicated in a typical home office setup.
Visa & Immigration
Machinists typically pursue skilled worker visas for international employment. Popular destinations include Germany, Canada, Australia, and the United States, all with robust manufacturing sectors. Each country has specific requirements for skilled trades.
For instance, Canada's Express Entry system or Provincial Nominee Programs often list machinists as in-demand. Germany offers the Skilled Immigration Act, requiring recognized qualifications and a job offer. Australia's skilled migration program often includes machinists on its occupation lists, requiring skills assessments.
Education credential recognition is crucial; applicants often need to demonstrate equivalence to local vocational standards. Professional licensing is less common for machinists, but specific certifications for equipment or safety may be required. Visa timelines vary from a few months to over a year, depending on the country and application volume.
Pathways to permanent residency exist in many countries for skilled workers who integrate successfully. Language requirements vary; some countries like Canada or Germany may require language proficiency tests. Family visas are usually available for dependents of skilled worker visa holders, allowing them to accompany the primary applicant.
2025 Market Reality for Machinists
Understanding the current market realities for machinists is crucial for career success. The manufacturing landscape has transformed significantly between 2023 and 2025, influenced by post-pandemic supply chain adjustments and the accelerating integration of AI into design and production workflows.
Broader economic factors, such as inflation and industrial output fluctuations, directly impact the demand for manufactured goods and, consequently, the need for skilled machinists. Market realities also vary considerably by experience level, with entry-level roles facing different challenges than highly specialized positions. Geographic location and the size of the manufacturing facility further shape job prospects. This analysis provides an honest assessment of these dynamics, helping machinists navigate the path ahead.
Current Challenges
Machinists face increased competition for advanced roles as manufacturing consolidates. Economic uncertainty also leads some companies to delay equipment upgrades, impacting demand for new parts. Automation and AI tools, while boosting productivity, also mean fewer machinists are needed for the same output, especially in high-volume production.
Entry-level positions often see saturation, making initial job searches longer. Expect a job search to take several months, particularly if seeking specialized roles or specific geographic locations. Skill gaps in advanced CNC programming and multi-axis machining remain a hurdle for many.
Growth Opportunities
Despite challenges, strong demand exists for machinists specializing in advanced CNC programming, particularly for five-axis machines and additive manufacturing post-processing. Emerging roles in hybrid manufacturing, which combines traditional machining with 3D printing, offer new avenues. Machinists proficient in interpreting complex CAD/CAM files and troubleshooting automated systems are highly sought after.
Professionals can position themselves advantageously by pursuing certifications in specific CNC controls (e.g., Fanuc, Siemens) or specialized software. Underserved markets often include smaller, custom fabrication shops that require versatile machinists, or defense contractors in less populated areas. Expertise in working with exotic materials like titanium or superalloys provides a significant competitive edge.
Market corrections can create opportunities for machinists to transition into more stable, high-precision industries like medical device manufacturing or aerospace, which maintain consistent demand. Investing in continuous education for new software versions or advanced machine operation techniques is a strategic move. These sectors prioritize precision and quality, valuing skilled machinists who can deliver exacting specifications consistently.
Current Market Trends
Demand for skilled machinists remains consistent, particularly for those proficient in advanced CNC (Computer Numerical Control) programming and multi-axis machining. Companies seek individuals who can operate, set up, and troubleshoot complex machinery, moving beyond manual lathe and mill operation. The industry is experiencing a push towards automation and precision manufacturing, driven by sectors like aerospace, medical devices, and custom fabrication.
Generative AI is influencing design processes, which then impacts the complexity of parts machinists produce. This requires machinists to interpret more intricate blueprints and adapt their programming skills. Economic conditions, while stable for precision manufacturing, show some volatility in general industrial production, affecting overall job availability. Layoffs in broader manufacturing sectors have not significantly impacted highly skilled machinists due to specialized demand.
Employer requirements now heavily emphasize CAD/CAM software proficiency alongside traditional machining skills. There is a growing need for machinists who understand metrology and quality control systems beyond basic measurements. Salary trends are showing modest growth for experienced CNC machinists, especially those with expertise in five-axis machines or exotic materials. Entry-level wages are relatively stagnant due to a larger pool of candidates with basic skills.
Geographically, strong markets exist in regions with robust aerospace, automotive, and medical device manufacturing clusters, such as the Midwest, Southeast, and parts of the West Coast. Remote work is not applicable here; machinists must be on-site. Hiring remains steady throughout the year, with slight upticks in demand during periods of new product development or large contract fulfillment.
Emerging Specializations
The field of machining is undergoing a significant transformation driven by advancements in automation, materials science, and digital manufacturing. New specialization opportunities are emerging rapidly, moving beyond traditional manual or CNC operations. Understanding these shifts and positioning oneself early in these cutting-edge areas is crucial for career advancement and securing high-demand roles in 2025 and beyond.
Early adoption of these emerging specializations often leads to premium compensation and accelerated career growth. These roles require a blend of traditional machining expertise with new digital and analytical competencies. While established machining areas remain vital, the highest growth and innovation are found at the intersection of machining and advanced technologies.
Many emerging areas are currently in a growth phase, but they are quickly moving towards mainstream adoption. Significant job opportunities will materialize as industries scale up their advanced manufacturing capabilities. Pursuing these cutting-edge specializations involves a strategic risk-reward calculation; while they demand continuous learning, they offer substantial long-term career advantages and resilience against automation of routine tasks.
Additive Manufacturing Post-Processor
Additive manufacturing, commonly known as 3D printing, is evolving beyond prototyping into full-scale industrial production, particularly for complex metal parts. Machinists specializing in post-processing for additive manufacturing ensure dimensional accuracy, surface finish, and structural integrity of printed components. This involves precision milling, turning, and grinding to meet strict engineering specifications, bridging the gap between raw printed parts and final functional products.
Robotics and Automation Machinist
The integration of robotics and automation into machining operations is creating demand for machinists who can program, operate, and troubleshoot robotic systems. These specialists develop robotic work cells for automated part loading/unloading, tool changing, and in-process inspection. They optimize robot paths and integrate them seamlessly with CNC machines, enhancing efficiency, safety, and precision in high-volume production environments.
Data-Driven Machining Specialist
With the rise of Industry 4.0, data-driven machining involves leveraging sensor data from machines to optimize performance, predict maintenance needs, and improve quality. Machinists in this specialization collect, analyze, and interpret machine data to identify trends, troubleshoot issues, and enhance operational efficiency. They use software tools for real-time monitoring and predictive analytics, moving towards a more proactive and intelligent manufacturing process.
Ultra-Precision Machinist
High-precision machining focuses on manufacturing components with extremely tight tolerances and superior surface finishes, often for critical applications in aerospace, medical devices, and optics. This specialization requires mastery of advanced machining processes like ultra-precision grinding, diamond turning, and micro-machining. It demands exceptional attention to detail and deep knowledge of material properties and their response to various cutting parameters.
Sustainable Machining Technician
Sustainable machining focuses on minimizing environmental impact throughout the manufacturing process. This involves optimizing cutting fluids for reduced consumption and waste, implementing energy-efficient machining strategies, and exploring dry machining or minimum quantity lubrication (MQL) techniques. Machinists in this area also work with recyclable materials and processes that reduce carbon footprint, aligning with growing industry demands for eco-friendly production.
Pros & Cons of Being a Machinist
Making an informed career choice requires a clear understanding of both the benefits and the challenges. The daily realities of a profession like a machinist can vary significantly based on the specific industry, the company's culture, the type of machinery used, and an individual's personal aptitude and preferences. For instance, a pro for one person, such as hands-on work, might be a con for another who prefers a desk job. Moreover, the advantages and challenges can evolve as one progresses from an entry-level position to a senior or specialized role. This assessment provides an honest, balanced look at what to expect as a machinist, helping prospective candidates set realistic expectations for their journey.
Pros
Machinists gain tangible skills in operating and programming complex machinery like lathes, mills, and grinders, which are highly valued across manufacturing and fabrication industries.
There is strong demand for skilled machinists across various sectors, including aerospace, automotive, medical devices, and general manufacturing, ensuring good job security.
Machinists experience a sense of accomplishment by creating precise components from raw materials, seeing the direct results of their craftsmanship in finished products.
The role offers continuous intellectual stimulation through problem-solving, as machinists must troubleshoot issues, optimize processes, and interpret complex blueprints and schematics.
Entry into the field is accessible through vocational schools, community colleges, or apprenticeships, providing practical training without requiring a four-year university degree.
Many machinist roles offer competitive wages, especially for those with specialized skills in CNC programming or operating advanced multi-axis machines, allowing for a stable income.
Machinists often work as part of a team, collaborating with engineers, designers, and other technicians, which can foster a sense of camaraderie and shared purpose in a production environment.
Cons
Machinists often work in noisy environments due to the operation of machinery, requiring consistent use of hearing protection which can be uncomfortable over long shifts.
The work can be physically demanding, involving standing for extended periods, lifting heavy materials, and repetitive motions that may lead to fatigue or musculoskeletal issues over time.
Exposure to coolants, lubricants, and metal particles is common, necessitating strict adherence to safety protocols and the use of personal protective equipment to prevent skin irritation or respiratory problems.
Machinists must possess a high degree of precision and attention to detail, as errors can lead to costly material waste, damaged equipment, or defective parts, creating pressure to maintain accuracy.
The job often requires working irregular hours, including night shifts, weekends, or overtime, especially when production deadlines are tight or machinery needs maintenance outside regular operating hours.
Learning the trade involves a significant investment in time, typically through apprenticeships or vocational programs, and continuous learning is necessary to keep up with new machinery and materials.
Career advancement opportunities may be limited within a single shop, often requiring a move to a larger facility or specializing in complex CNC programming to see significant progression.
Frequently Asked Questions
Machinists face distinct challenges in mastering precision and operating complex machinery safely. This section addresses key concerns about entering this hands-on trade, from acquiring the necessary skills to understanding career stability and growth in a manufacturing environment.
What are the common pathways to become a qualified Machinist, and do I need a degree?
Most machinists begin with vocational training programs or apprenticeships, which typically last 1-4 years. Vocational schools offer certificates or associate degrees in machining technology, providing foundational knowledge. Apprenticeships combine on-the-job training with classroom instruction, allowing you to earn while you learn. While not always mandatory, certifications like NIMS (National Institute for Metalworking Skills) can significantly enhance job prospects and validate your expertise.
What is the typical salary range for a Machinist, both entry-level and experienced?
An entry-level Machinist typically earns between $35,000 and $45,000 annually, depending on location and specific industry. With experience and specialized skills, such as CNC programming or operating multi-axis machines, salaries can rise significantly, often reaching $55,000 to $70,000 or more. Overtime opportunities are common in manufacturing, which can boost overall earnings.
Is the Machinist trade a stable career, or is it at high risk of automation?
The demand for skilled Machinists remains steady, especially for those proficient in CNC (Computer Numerical Control) machining. Many experienced machinists are retiring, creating opportunities for new talent to fill critical roles in manufacturing sectors like aerospace, automotive, and medical devices. While some jobs are automated, the need for human operators, programmers, and maintenance technicians for complex machines persists.
What are the career advancement opportunities for a Machinist beyond the basic role?
Career growth for a Machinist can lead to several advanced roles. You can specialize in CNC programming, becoming a highly sought-after expert in automating machine operations. Other paths include becoming a lead Machinist, a shop supervisor, a quality control inspector, or even transitioning into roles like manufacturing engineering or tooling design. Continuous learning and adapting to new technologies are key for advancement.
What is the typical work schedule and work-life balance like for a Machinist?
The work-life balance for a Machinist often depends on the specific employer and industry. Many manufacturing facilities operate on multiple shifts, including evenings and weekends, which can impact personal time. While some shops offer standard daytime hours, be prepared for potential shift work or overtime, especially when production demands are high. This career typically involves consistent hours and a predictable schedule once established.
What are the common safety concerns or hazards in a Machinist's daily work?
Safety is paramount in a machine shop. Machinists work with heavy machinery, sharp tools, and fast-moving parts, which requires constant vigilance. Risks include cuts, abrasions, eye injuries, and exposure to coolants and metal dust. Companies are legally required to provide personal protective equipment (PPE) and adhere to strict safety protocols. Following these procedures diligently minimizes risks, making the environment safe.
How important is computer software knowledge (like CAD/CAM) for a Machinist, and is it required for entry-level roles?
While some basic CAD/CAM software knowledge helps, the core skills for an entry-level Machinist involve mechanical aptitude, precision measurement, and understanding blueprints. Many employers provide on-the-job training for specific software. As you advance, proficiency in CAD/CAM for designing parts and programming CNC machines becomes increasingly valuable and often expected for higher-paying roles.
Related Careers
Explore similar roles that might align with your interests and skills:
Cnc Machinist
A growing field with similar skill requirements and career progression opportunities.
Explore career guideManual Machinist
A growing field with similar skill requirements and career progression opportunities.
Explore career guidePrecision Machinist
A growing field with similar skill requirements and career progression opportunities.
Explore career guideProduction Machinist
A growing field with similar skill requirements and career progression opportunities.
Explore career guideTool Room Machinist
A growing field with similar skill requirements and career progression opportunities.
Explore career guideAssess your Machinist readiness
Understanding where you stand today is the first step toward your career goals. Our Career Coach helps identify skill gaps and create personalized plans.
Skills Gap Analysis
Get a detailed assessment of your current skills versus Machinist requirements. Our AI Career Coach identifies specific areas for improvement with personalized recommendations.
See your skills gapCareer Readiness Assessment
Evaluate your overall readiness for Machinist roles with our AI Career Coach. Receive personalized recommendations for education, projects, and experience to boost your competitiveness.
Assess your readinessSimple pricing, powerful features
Upgrade to Himalayas Plus and turbocharge your job search.
Himalayas
Himalayas Plus
Himalayas Max
Find your dream job
Sign up now and join over 100,000 remote workers who receive personalized job alerts, curated job matches, and more for free!
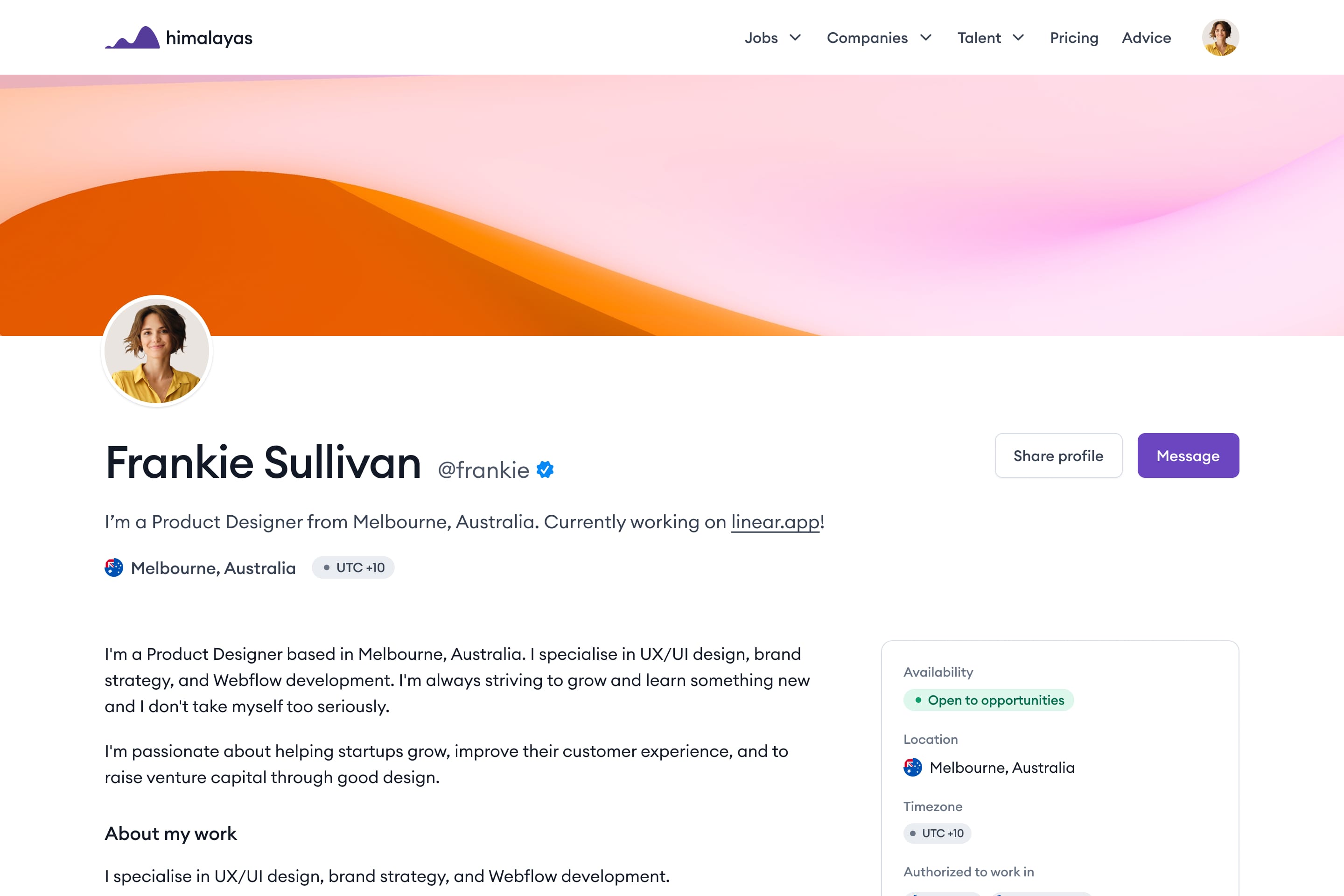