5 Team Automobile Assembler Interview Questions and Answers
Team Automobile Assemblers are responsible for assembling various components of vehicles on a production line. They ensure that parts are correctly installed, meet quality standards, and adhere to safety protocols. Junior assemblers focus on learning specific tasks and processes, while senior and lead roles involve overseeing assembly operations, troubleshooting issues, and mentoring team members. Need to practice for an interview? Try our AI interview practice for free then unlock unlimited access for just $9/month.
Unlimited interview practice for $9 / month
Improve your confidence with an AI mock interviewer.
No credit card required
1. Junior Automobile Assembler Interview Questions and Answers
1.1. Can you describe a time when you had to follow specific assembly instructions to complete a task?
Introduction
This question is crucial for assessing your attention to detail and ability to follow precise instructions, which are vital in the assembly line environment.
How to answer
- Use the STAR method to structure your answer: Situation, Task, Action, Result.
- Clearly describe the assembly task and the specific instructions you were given.
- Explain how you ensured accuracy while following the instructions.
- Discuss any challenges you faced and how you overcame them.
- Quantify the positive outcome of your actions, if possible.
What not to say
- Focusing on a task that lacked clear instructions.
- Failing to mention the importance of precision in assembly.
- Neglecting to detail your personal contributions.
- Providing a vague answer without specific examples.
Example answer
“During my internship at Renault, I was tasked with assembling a component of the engine. I followed the detailed blueprint provided, ensuring that each part was placed accurately. When I encountered a misalignment, I consulted with my supervisor and corrected it before proceeding. This attention to detail resulted in a flawless assembly, contributing to a 10% improvement in the overall production efficiency during that shift.”
Skills tested
Question type
1.2. How do you handle working in a team environment, especially under tight deadlines?
Introduction
This question evaluates your teamwork skills and ability to perform under pressure, both of which are essential in a fast-paced manufacturing setting.
How to answer
- Share your understanding of the importance of teamwork in assembly.
- Provide examples of how you’ve collaborated with others to meet deadlines.
- Discuss any strategies you use to manage stress and maintain productivity.
- Highlight how you contribute to team dynamics and communication.
- Mention any specific tools or practices you use to stay organized.
What not to say
- Indicating that you prefer to work alone.
- Failing to demonstrate any experience working in teams.
- Not acknowledging the importance of communication.
- Suggesting that deadlines are not important.
Example answer
“While working as a part-time assembler at a local workshop, I was part of a team that assembled bicycle frames. When we faced a tight deadline for a large order, I coordinated with my teammates to divide tasks based on our strengths. I facilitated clear communication to ensure everyone was aligned, and we completed the order two hours ahead of schedule. This experience taught me that teamwork and effective communication are key to meeting deadlines.”
Skills tested
Question type
2. Automobile Assembler Interview Questions and Answers
2.1. Can you describe a time when you identified a defect in a vehicle assembly process? What steps did you take to address it?
Introduction
This question evaluates your attention to detail and problem-solving skills, which are critical for ensuring the quality of assembled vehicles.
How to answer
- Start with a clear description of the assembly process and the specific defect you noticed
- Explain how you investigated or analyzed the issue
- Detail the actions you took to resolve the defect, including collaboration with team members or supervisors
- Discuss the outcome of your actions and any improvements made to the process as a result
- Reflect on any lessons learned from the experience
What not to say
- Failing to provide a specific example or using vague statements
- Minimizing the importance of quality control in assembly
- Describing a situation where you did nothing to improve the defect
- Not acknowledging the role of teamwork in problem-solving
Example answer
“While working at SAIC Motor, I noticed that a batch of vehicles had a recurring issue with the alignment of the doors. I immediately communicated my concerns to my supervisor and we conducted a thorough inspection. We identified a miscalibration in the assembly jig. I suggested a recalibration procedure and worked with the quality control team to implement regular checks. As a result, we reduced door alignment defects by 30%, which improved overall customer satisfaction.”
Skills tested
Question type
2.2. How do you ensure safety while working on the assembly line?
Introduction
Safety is paramount in assembly jobs, and this question assesses your awareness and practices regarding workplace safety.
How to answer
- Discuss specific safety protocols you follow at all times
- Share any training or certifications related to workplace safety
- Provide examples of how you have promoted safety among your colleagues
- Explain how you handle safety equipment and machinery properly
- Mention any incidents where you contributed to improving safety measures
What not to say
- Indicating that safety is not a top priority for you
- Failing to mention specific safety practices or protocols
- Describing a careless approach to using machinery
- Not acknowledging the importance of reporting safety hazards
Example answer
“At Geely, I always adhere to the safety protocols established by the company, including wearing appropriate personal protective equipment and following machine operation guidelines. I completed safety training and have encouraged my colleagues to participate in safety drills. Once, I noticed a safety guard was missing from a machine, and I immediately reported it, preventing potential accidents. My proactive approach has fostered a culture of safety in our team.”
Skills tested
Question type
3. Senior Automobile Assembler Interview Questions and Answers
3.1. Can you describe a time when you identified a quality issue on the assembly line and what actions you took?
Introduction
This question assesses your attention to detail and problem-solving skills, which are crucial for maintaining high-quality standards in automobile assembly.
How to answer
- Use the STAR method to structure your response
- Start by detailing the specific quality issue you encountered
- Explain how you identified the issue and its potential impact on production
- Describe the steps you took to address the problem, including collaboration with team members or supervisors
- Highlight the outcome, including any improvements in quality or efficiency
What not to say
- Failing to provide a specific example
- Blaming others for the quality issue instead of taking responsibility
- Ignoring the importance of teamwork in resolving the problem
- Not mentioning any measurable outcomes or improvements
Example answer
“At Toyota Australia, I noticed a recurring issue with misaligned body panels during assembly. I documented the issue and brought it to my supervisor's attention. Together, we conducted a thorough review of the assembly process and found that the calibration of the tools was off. After recalibrating the equipment, we reduced the defect rate by 30%, ensuring a higher quality product for our customers.”
Skills tested
Question type
3.2. How do you ensure safety while working on the assembly line?
Introduction
This question evaluates your understanding of safety protocols and your commitment to maintaining a safe working environment, which is vital in automobile assembly.
How to answer
- Discuss specific safety protocols or guidelines you adhere to
- Explain how you stay informed about safety updates or changes
- Share examples of how you promote safety among your colleagues
- Mention any safety training or certifications you have completed
- Highlight the importance of safety in maintaining productivity and employee well-being
What not to say
- Neglecting to mention specific safety measures
- Downplaying the importance of safety in the workplace
- Failing to acknowledge personal responsibility for safety
- Suggesting that safety protocols are optional or can be ignored
Example answer
“I prioritize safety by strictly following the Occupational Health and Safety guidelines and participating in regular safety training sessions. I conduct daily safety checks on my workstation and encourage my colleagues to do the same. For instance, after noticing some unsafe practices during a shift, I organized a brief meeting to reinforce the importance of using personal protective equipment, which led to a noticeable decrease in minor incidents on the assembly line.”
Skills tested
Question type
4. Lead Automobile Assembler Interview Questions and Answers
4.1. Can you describe a time when you identified a flaw in the assembly process and how you addressed it?
Introduction
This question is crucial for assessing your problem-solving skills and attention to detail, which are vital in the role of a Lead Automobile Assembler.
How to answer
- Use the STAR method to structure your response: Situation, Task, Action, Result.
- Clearly describe the assembly process and the specific flaw you identified.
- Explain the steps you took to investigate and address the issue.
- Detail the outcome of your actions, including any improvements to efficiency or quality.
- Highlight any collaboration with other team members or departments.
What not to say
- Dismissing the importance of quality control.
- Failing to provide specific examples or metrics to back up your claims.
- Blaming others for the flaw without taking responsibility.
- Overlooking the importance of teamwork in resolving the issue.
Example answer
“In my previous role at Fiat, I noticed that the fit of the doors on several car models was inconsistent. I initiated a review of our assembly line procedures, which revealed that the installation tools weren't calibrated correctly. I collaborated with the equipment maintenance team to recalibrate the tools, which resulted in a 30% reduction in rework and improved customer satisfaction scores significantly.”
Skills tested
Question type
4.2. How do you ensure safety standards are met on the assembly line?
Introduction
This question evaluates your commitment to safety and your ability to foster a safe working environment, which is critical in manufacturing roles.
How to answer
- Discuss your knowledge of safety regulations and standards in the automotive industry.
- Describe the safety protocols you have implemented or improved in your previous roles.
- Explain how you educate and train team members on safety practices.
- Share specific examples of how you have addressed safety violations or concerns.
- Highlight any safety metrics or improvements you achieved.
What not to say
- Suggesting that safety is not a priority.
- Failing to mention any specific safety training or protocols.
- Overlooking the importance of continuous improvement in safety practices.
- Neglecting to acknowledge the role of employee feedback in safety measures.
Example answer
“At Maserati, I implemented a safety training program for new employees, focusing on the importance of personal protective equipment (PPE) and proper machine operation. I also set up a system for reporting near-misses, which helped us reduce accidents by 40% over the course of a year. Safety is paramount, and I believe that fostering a culture of safety awareness among all team members is essential.”
Skills tested
Question type
5. Assembly Line Supervisor Interview Questions and Answers
5.1. Can you describe a situation where you had to improve efficiency on the assembly line?
Introduction
This question assesses your problem-solving skills and ability to implement process improvements, which are critical for an assembly line supervisor.
How to answer
- Begin by outlining the specific issue that was affecting efficiency
- Explain the steps you took to analyze the problem
- Detail the changes you implemented and how you communicated them to your team
- Quantify the results of your actions, such as time saved or increased output
- Share any feedback received from team members or management regarding the changes
What not to say
- Vague descriptions of problems without specifics
- Not mentioning collaboration with the team
- Failing to provide measurable outcomes
- Blaming others for inefficiencies rather than focusing on your contributions
Example answer
“At Fiat, we faced a bottleneck in our assembly line that slowed down production. I conducted a time-motion study and identified that rework on parts was causing delays. I implemented a quality check earlier in the process and trained my team on best practices for handling components. As a result, we improved our efficiency by 20% and reduced rework by 30%. The team felt more empowered, and morale improved as they saw the impact of their efforts.”
Skills tested
Question type
5.2. How do you handle conflicts between team members on the assembly line?
Introduction
This question evaluates your conflict resolution skills and ability to maintain a positive team environment, which is essential for a supervisor.
How to answer
- Describe your approach to identifying the root cause of conflicts
- Explain how you facilitate communication between conflicting parties
- Detail any mediation techniques you use to resolve disputes
- Share examples of successful conflict resolution and its outcomes
- Discuss how you promote teamwork and prevent conflicts in the first place
What not to say
- Ignoring conflict rather than addressing it directly
- Taking sides without understanding both perspectives
- Failing to provide a clear resolution process
- Not mentioning the importance of teamwork and collaboration
Example answer
“In my role at Ferrari, I noticed tension between two assembly line workers due to differing approaches to their tasks. I set up a meeting with both to discuss their perspectives. By facilitating open communication, we uncovered misunderstandings about task responsibilities. We agreed on clearer role definitions and established regular check-ins. This resolution not only improved their working relationship but also led to smoother operations on the line.”
Skills tested
Question type
Similar Interview Questions and Sample Answers
Simple pricing, powerful features
Upgrade to Himalayas Plus and turbocharge your job search.
Himalayas
Himalayas Plus
Himalayas Max
Find your dream job
Sign up now and join over 100,000 remote workers who receive personalized job alerts, curated job matches, and more for free!
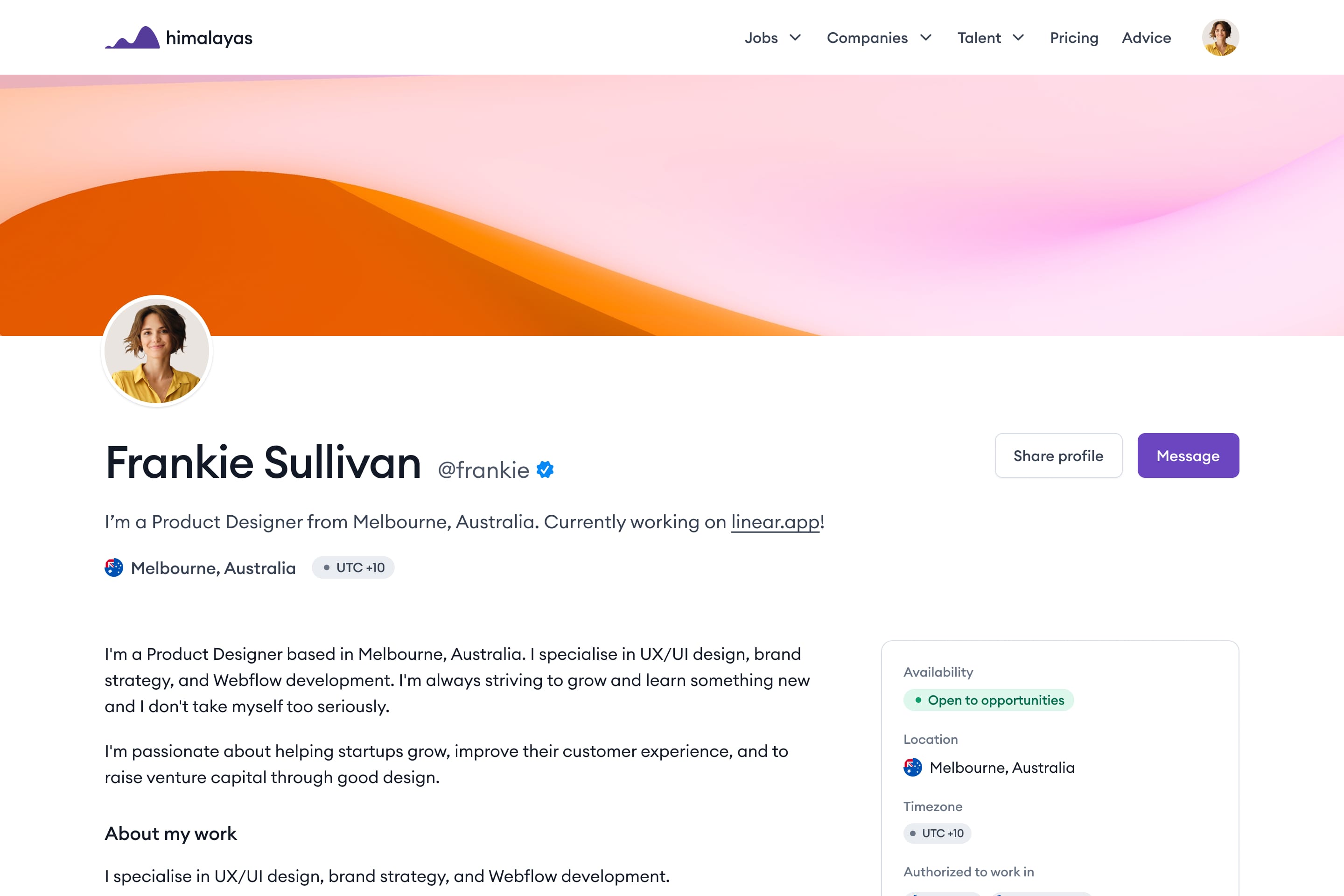