5 Assembly Operator Interview Questions and Answers
Assembly Operators are responsible for putting together parts or components to create finished products. They work on assembly lines, using tools and machinery to ensure products meet quality standards and production goals. Entry-level operators focus on learning the assembly process and following instructions, while senior operators may handle more complex tasks, troubleshoot issues, and ensure efficiency. Lead operators and supervisors oversee teams, manage workflow, and ensure safety and quality compliance. Need to practice for an interview? Try our AI interview practice for free then unlock unlimited access for just $9/month.
Unlimited interview practice for $9 / month
Improve your confidence with an AI mock interviewer.
No credit card required
1. Entry-level Assembly Operator Interview Questions and Answers
1.1. Can you describe a time when you had to follow specific instructions to complete a task?
Introduction
This question evaluates your attention to detail and ability to follow processes, which are critical skills for an assembly operator.
How to answer
- Use the STAR method to structure your response: Situation, Task, Action, Result.
- Describe the specific instructions you were given and why they were important.
- Explain how you ensured you understood the instructions correctly.
- Detail the steps you took to complete the task accurately.
- Share the outcome and any positive feedback you received.
What not to say
- Focusing too much on personal opinions about the instructions instead of the task.
- Mentioning instances where you did not follow instructions correctly.
- Providing vague examples that lack detail on the task or outcome.
- Neglecting to mention the importance of teamwork or collaboration if applicable.
Example answer
“In my previous internship at a manufacturing plant, I was tasked with assembling a component following strict specifications. I carefully read the assembly manual and confirmed my understanding with my supervisor. By meticulously following each step, I was able to complete the assembly ahead of schedule, resulting in no defects and positive praise from my team lead.”
Skills tested
Question type
1.2. How would you handle a situation where you notice a malfunctioning machine while working on the assembly line?
Introduction
This question assesses your problem-solving skills and ability to communicate issues effectively in a manufacturing environment.
How to answer
- Describe the importance of safety and reporting issues promptly.
- Explain the steps you would take to assess the situation.
- Detail how you would communicate the problem to your supervisor or maintenance team.
- Mention any protocols you would follow for the safety of yourself and others.
- Share an understanding of the impact of machine issues on the production line.
What not to say
- Ignoring the issue and continuing to work.
- Suggesting that it's not your responsibility to report machine problems.
- Failing to mention safety protocols or procedures.
- Being vague about the actions taken or the importance of communication.
Example answer
“If I noticed a malfunctioning machine, I would first ensure my own safety and the safety of my coworkers. I would then stop my work and assess if the issue posed an immediate risk. Next, I would notify my supervisor or the maintenance team about the malfunction, providing details about the issue. I understand that addressing such problems quickly is vital to maintaining production efficiency and safety.”
Skills tested
Question type
2. Assembly Operator Interview Questions and Answers
2.1. Can you describe a time when you had to troubleshoot a mechanical issue on the assembly line?
Introduction
This question is crucial for assessing your problem-solving skills and technical knowledge as an assembly operator, which are essential for maintaining production efficiency.
How to answer
- Begin with a clear description of the mechanical issue you encountered
- Explain the steps you took to diagnose the problem
- Detail the solution you implemented and the resources you utilized
- Quantify the impact of your solution on production efficiency or downtime
- Reflect on what you learned from the experience
What not to say
- Describing a situation where you did not take initiative to solve the problem
- Failing to explain the reasoning behind your troubleshooting steps
- Overlooking the importance of teamwork or communication in resolving the issue
- Not quantifying the results or improvements achieved
Example answer
“At Toyota, I noticed that one of the assembly machines was consistently jamming. I took the initiative to inspect the machine and discovered a misalignment in the feed mechanism. After realigning it and performing a test run, the jamming issue was resolved, leading to a 20% increase in throughput for that station. This experience taught me the importance of proactive maintenance and attention to detail.”
Skills tested
Question type
2.2. How do you ensure quality control in your assembly work?
Introduction
Quality control is vital in assembly operations to prevent defects and ensure customer satisfaction. This question evaluates your understanding of quality assurance processes.
How to answer
- Outline the specific quality control measures you follow during assembly
- Discuss how you identify and report defects or issues
- Explain how you balance speed and quality in your work
- Mention any relevant tools or techniques you use for quality assessment
- Share an example of how your attention to quality improved a process
What not to say
- Suggesting that quality control is not your responsibility
- Providing vague answers without specific examples or techniques
- Neglecting to mention the importance of teamwork in quality control
- Focusing only on quantity over quality
Example answer
“In my role at Honda, I implemented a checklist for each assembly task, ensuring that I met all quality standards before moving on to the next step. I also trained my colleagues to spot potential defects early. This proactive approach reduced our defect rate by 15%, and I learned that quality assurance is a shared responsibility that enhances overall productivity.”
Skills tested
Question type
3. Senior Assembly Operator Interview Questions and Answers
3.1. Can you describe a time when you identified a safety issue on the assembly line and how you addressed it?
Introduction
This question evaluates your awareness of safety protocols and your initiative in enhancing workplace safety, which is crucial for an assembly operator role.
How to answer
- Begin with a specific example of the safety issue you noticed.
- Explain the steps you took to address the issue and the rationale behind your actions.
- Detail how you communicated the problem to your supervisor or team.
- Discuss any changes implemented as a result of your actions and their impact on safety.
- Highlight the importance of safety culture in the workplace.
What not to say
- Ignoring your responsibilities in addressing safety concerns.
- Failing to provide a concrete example or just speaking in generalities.
- Not showing any follow-up actions taken after the initial identification of the issue.
- Neglecting to acknowledge the importance of teamwork in enhancing safety.
Example answer
“While working at Rolls-Royce, I noticed that a section of the assembly line had inadequate lighting, which posed a risk for injuries. I promptly reported it to my line manager and suggested temporary lighting solutions. After our team discussed it, we implemented additional lights, which improved visibility and reduced near-misses by 30%. This experience underscored the importance of vigilance and proactive safety measures in our work environment.”
Skills tested
Question type
3.2. How do you ensure quality control in your work as an assembly operator?
Introduction
This question assesses your understanding of quality control processes and your commitment to maintaining high standards in production.
How to answer
- Describe the specific quality control methods you follow in your role.
- Discuss how you verify your work after completing tasks.
- Explain how you collaborate with quality assurance teams.
- Share an example of a time when you caught a quality issue before it reached the customer.
- Highlight the importance of continuous improvement in quality.
What not to say
- Suggesting that quality control is solely the responsibility of a separate team.
- Failing to mention any specific quality control practices you use.
- Ignoring the importance of customer satisfaction in quality control.
- Not providing examples of how you’ve contributed to quality assurance.
Example answer
“In my role at BAE Systems, I follow a checklist for quality control after each assembly task. I perform visual inspections and functional tests to ensure compliance with specifications. Once, I noticed a misaligned component before it was sent for final inspection, which could have led to product failure. By addressing it immediately, we saved time and maintained our quality standards. I believe that quality control is a personal responsibility for every operator.”
Skills tested
Question type
4. Lead Assembly Operator Interview Questions and Answers
4.1. Can you describe a time when you improved an assembly process to enhance efficiency?
Introduction
This question assesses your problem-solving skills and ability to optimize production processes, which is crucial for a lead assembly operator role.
How to answer
- Use the STAR method (Situation, Task, Action, Result) to structure your response.
- Clearly define the process you identified for improvement and the inefficiencies involved.
- Explain the steps you took to analyze and address the issues, including any tools or methods used.
- Quantify the results of your improvements, focusing on efficiency gains or cost reductions.
- Highlight any collaboration with team members or cross-departmental communication that facilitated the change.
What not to say
- Avoid vague answers without specific actions taken.
- Do not claim credit for improvements made by others.
- Refrain from focusing solely on problems without discussing solutions.
- Avoid metrics that are not quantifiable or relevant.
Example answer
“In my previous role at Ford, I noticed that our assembly line was experiencing frequent delays due to manual part sorting. I proposed implementing a color-coded part bin system, which I designed and tested with my team. This change reduced sorting time by 30% and improved overall line efficiency by 15%. This experience showed me the importance of proactive problem-solving and team involvement in process improvements.”
Skills tested
Question type
4.2. How do you ensure quality control within your assembly team?
Introduction
This question evaluates your understanding of quality assurance processes and your ability to enforce them within your team, which is essential for maintaining production standards.
How to answer
- Discuss specific quality control measures or processes you have implemented or followed.
- Explain how you train and communicate quality expectations to your team.
- Describe how you monitor and assess product quality during assembly.
- Share examples of how you address quality issues when they arise.
- Highlight any metrics or tools you use to track quality performance.
What not to say
- Avoid saying that quality control is solely the responsibility of a different team.
- Do not provide generic answers that lack specific examples.
- Refrain from neglecting the importance of training and communication.
- Avoid blaming others for quality issues without discussing your role in resolution.
Example answer
“At Boeing, I established a quality control checklist that every operator had to complete at the start of their shift. I also conducted weekly training sessions to reinforce the importance of quality standards. When defects were identified, I worked with my team to analyze the root cause and implement corrective actions. This approach led to a 20% reduction in defects over six months, demonstrating my commitment to quality and continuous improvement.”
Skills tested
Question type
5. Assembly Supervisor Interview Questions and Answers
5.1. Can you describe a time when you improved the efficiency of an assembly line?
Introduction
This question is crucial for an Assembly Supervisor as it assesses your ability to identify inefficiencies and implement solutions that enhance productivity in a manufacturing environment.
How to answer
- Use the STAR method (Situation, Task, Action, Result) to structure your response
- Clearly outline the inefficiency you identified and its impact on production
- Detail the specific actions you took to address the issue, including any tools or methodologies you used
- Quantify the results of your actions, such as time saved or increased output
- Discuss how you involved your team in the process to foster collaboration
What not to say
- Avoid vague statements that do not specify the issue or solution
- Do not take full credit without acknowledging team contributions
- Refrain from discussing irrelevant experiences outside of assembly line management
- Avoid focusing solely on the problem without showcasing the solution
Example answer
“At a previous role at Embraer, I noticed our assembly line was consistently running behind schedule due to outdated equipment. I initiated a review of our processes and collaborated with the maintenance team to upgrade machinery and retrain staff on efficient practices. This led to a 20% increase in output and reduced downtime by 15%. Involving my team in the process helped gain their support and input, which was invaluable for the success of the changes.”
Skills tested
Question type
5.2. How do you ensure the quality of products on the assembly line?
Introduction
Quality control is vital in manufacturing, and this question assesses your approach to maintaining high standards in production processes.
How to answer
- Explain your understanding of quality control measures relevant to the assembly process
- Discuss any specific quality assurance tools or methodologies you have implemented
- Provide examples of how you trained your team on quality standards and practices
- Share a situation where you identified a quality issue and the steps taken to resolve it
- Highlight the importance of continuous improvement in quality assurance
What not to say
- Claiming quality control is solely the responsibility of a separate department
- Failing to provide concrete examples of quality assurance practices
- Neglecting to mention team training and involvement in quality processes
- Avoiding discussion on how to handle quality failures
Example answer
“At Volkswagen, I implemented a daily quality check system where assembly workers were responsible for inspecting their work before passing it on to the next station. I also introduced regular training sessions on quality standards and the importance of early detection of defects. When we faced a recurring issue with misaligned parts, I led a root cause analysis and refined our processes, resulting in a 30% reduction in defects over six months and significantly improving team accountability.”
Skills tested
Question type
Similar Interview Questions and Sample Answers
Simple pricing, powerful features
Upgrade to Himalayas Plus and turbocharge your job search.
Himalayas
Himalayas Plus
Himalayas Max
Find your dream job
Sign up now and join over 100,000 remote workers who receive personalized job alerts, curated job matches, and more for free!
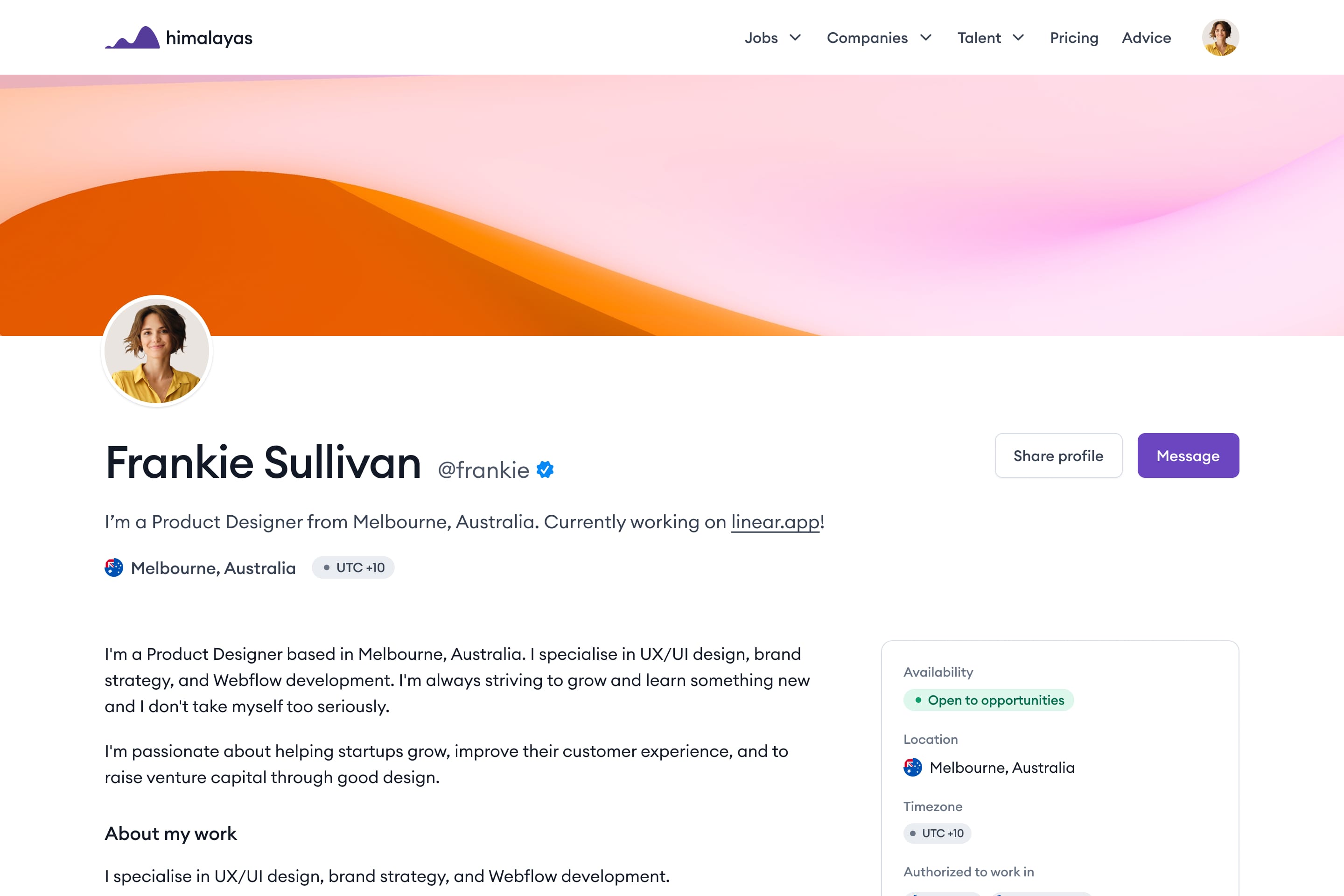