Complete Team Automobile Assembler Career Guide
Team automobile assemblers are the backbone of modern vehicle manufacturing, bringing complex designs to life on the production line. Working collaboratively, they meticulously fit parts and systems, ensuring every car meets rigorous quality and safety standards. This hands-on role offers a direct path into a vital industry, contributing to the mobility that drives our world.
Key Facts & Statistics
Median Salary
$47,210 USD
(U.S. national median, May 2022, Source: U.S. Bureau of Labor Statistics)
Range: $30k - $65k+ USD, depending on experience, location, and employer (Source: U.S. Bureau of Labor Statistics, May 2022)
Growth Outlook
1%
slower than average (Source: U.S. Bureau of Labor Statistics, 2022-2032)
Annual Openings
≈33
.2k openings annually (Source: U.S. Bureau of Labor Statistics, May 2022)
Top Industries
Typical Education
High school diploma or equivalent, with on-the-job training common; some employers prefer vocational training or an associate's degree in automotive technology.
What is a Team Automobile Assembler?
A Team Automobile Assembler is a skilled manufacturing professional responsible for constructing vehicles on an assembly line. They meticulously combine various components, from large structural elements like engines and chassis to intricate interior fittings and electrical systems, ensuring each part fits perfectly and functions as intended. This role is fundamental to the automotive industry, as these individuals directly build the vehicles that consumers drive.
Unlike general manufacturing assemblers who might work on diverse products, Team Automobile Assemblers specialize specifically in vehicle construction. They work within a highly synchronized team environment, where each member contributes to a specific segment of the assembly process. This specialization requires a deep understanding of automotive components and stringent quality control, distinguishing them from broader assembly roles that might lack the same level of complexity or precision.
What does a Team Automobile Assembler do?
Key Responsibilities
- Install vehicle components such as engines, transmissions, axles, and interior trim using hand tools and power tools.
- Perform quality checks on assembled parts to ensure they meet specified standards and rectify any defects immediately.
- Operate robotic equipment and automated machinery on the assembly line, monitoring their performance and making minor adjustments.
- Collaborate with team members to maintain a consistent production pace and address any bottlenecks or issues efficiently.
- Adhere to strict safety protocols and procedures, including wearing personal protective equipment and maintaining a clean work area.
- Read and interpret blueprints, schematics, and work instructions to ensure accurate assembly of vehicle parts.
- Troubleshoot minor equipment malfunctions and report larger issues to maintenance or supervisory staff for resolution.
Work Environment
A Team Automobile Assembler works within a fast-paced manufacturing plant, typically on an assembly line. The environment is often noisy due to machinery and requires standing for long periods. Teamwork is crucial, with individuals collaborating closely to meet production targets. Shifts often rotate, including day, evening, and night shifts, sometimes with overtime to meet demand. The pace is steady and demanding, driven by the continuous flow of the assembly line.
The role involves repetitive tasks, but also requires constant vigilance for quality and safety. While the work is indoors, temperature can vary depending on the area of the plant. There is minimal travel required, as the work is plant-based. The focus is on precision, efficiency, and adherence to strict safety standards within a highly structured and organized system.
Tools & Technologies
Team Automobile Assemblers primarily use a variety of hand tools like wrenches, screwdrivers, and torque guns, alongside power tools such as pneumatic drills and impact drivers. They also operate and monitor specialized machinery, including robotic arms for heavy lifting or precision welding, and automated guided vehicles (AGVs) for material transport. Diagnostic equipment and quality control gauges are essential for ensuring parts meet specifications.
Beyond physical tools, assemblers interact with digital work instructions displayed on tablets or computer terminals. They also use enterprise resource planning (ERP) systems to track inventory and production progress, and potentially human-machine interface (HMI) panels to control assembly line equipment. Safety equipment, including safety glasses, gloves, and ear protection, is mandatory.
Team Automobile Assembler Skills & Qualifications
A Team Automobile Assembler requires a blend of practical skills, adherence to strict procedures, and a strong safety mindset. This role focuses on the precise, repetitive assembly of vehicle components on a production line. Requirements vary significantly by the type of manufacturing facility, from highly automated plants to those relying more on manual dexterity.
For entry-level positions, employers often prioritize a strong work ethic and the ability to follow instructions over extensive formal education. Many assemblers begin with a high school diploma or equivalent, gaining specialized skills through on-the-job training. However, possessing vocational certifications or completing manufacturing technology programs can accelerate career progression and open doors to more specialized assembly tasks or team lead roles.
The skill landscape for automobile assemblers is evolving with advancements in automation and robotics. While manual dexterity remains crucial, understanding basic robotics, quality control software, and lean manufacturing principles is becoming increasingly valuable. This balance between traditional manual skills and emerging digital competencies helps assemblers adapt to modern production environments and contribute to continuous improvement initiatives.
Education Requirements
Technical Skills
- Blueprint and Schematic Reading: Interpreting technical drawings to understand component placement and assembly order.
- Tool Proficiency (Manual & Power): Skillful use of hand tools (wrenches, screwdrivers) and power tools (drills, torque wrenches, impact drivers).
- Fastener Application Techniques: Correctly applying various types of fasteners (bolts, nuts, clips, rivets) with appropriate torque.
- Component Identification and Handling: Accurately identifying, retrieving, and handling various vehicle parts without damage.
- Quality Control and Inspection: Performing visual and functional checks to ensure components meet specifications and assembly standards.
- Material Handling Equipment Operation: Basic operation of pallet jacks, carts, or other equipment for moving materials on the assembly line.
- Basic Robotics Operation (Human-Robot Collaboration): Interacting safely with and assisting collaborative robots in automated assembly tasks.
- Lean Manufacturing Principles: Understanding concepts like 5S, Kaizen, and waste reduction to optimize efficiency and quality.
- Measurement Tools Usage: Accurately using calipers, micrometers, and other measuring devices for quality verification.
- Computerized Work Instruction Systems: Navigating digital work instructions and data entry for tracking progress and issues.
- Preventive Maintenance (Basic): Performing routine checks and minor adjustments to tools and equipment to ensure functionality.
- Ergonomics and Body Mechanics: Applying proper techniques to prevent strain and injury during repetitive tasks.
Soft Skills
- Attention to Detail: Essential for ensuring each component is correctly placed and secured, preventing defects that can lead to costly rework or safety issues.
- Adherence to Procedures: Critical for following strict assembly sequences, safety protocols, and quality standards on a fast-paced production line.
- Teamwork and Collaboration: Vital for coordinating actions with fellow assemblers and other line personnel to maintain production flow and meet daily targets.
- Problem-Solving Skills: Important for identifying minor issues on the line, troubleshooting basic malfunctions, and suggesting improvements to processes.
- Adaptability and Flexibility: Necessary for adjusting to changes in production schedules, component specifications, or assembly techniques.
- Physical Stamina and Endurance: Required for performing repetitive tasks, often standing for long periods, and handling various tools and components.
- Safety Consciousness: Paramount for recognizing and mitigating hazards, following lockout/tagout procedures, and ensuring a safe working environment for everyone.
- Time Management: Crucial for completing assigned tasks efficiently and maintaining the pace of the assembly line to avoid bottlenecks.
How to Become a Team Automobile Assembler
Becoming a Team Automobile Assembler offers a direct entry into the manufacturing sector, often without requiring a four-year degree. Pathways typically involve vocational training, community college programs, or direct entry-level positions within a plant. The timeline can vary; some roles offer immediate training for entry-level hires, while others prefer candidates with a certificate or diploma, which might take 6-18 months.
Entry strategies often differ by company size and location. Large automotive manufacturers might have structured apprenticeship programs or require specific technical certifications. Smaller component suppliers or specialized vehicle builders may offer more on-the-job training. Geographic regions with established automotive industries, like the Midwest in the U.S. or specific industrial zones globally, will have more opportunities. Misconceptions exist that this work is entirely automated; human assemblers remain crucial for precision, quality control, and complex tasks.
The hiring landscape favors individuals who demonstrate reliability, a strong work ethic, and a willingness to learn. While formal education is a plus, practical aptitude and a commitment to safety are highly valued. Networking through trade schools, local manufacturing associations, or even directly approaching plant HR departments can open doors. Overcoming barriers often involves proving a consistent attendance record and an ability to follow detailed instructions, which are critical in a high-volume production environment.
Step 1
Step 2
Step 3
Step 4
Step 5
Step 6
Step 7
Education & Training Needed to Become a Team Automobile Assembler
Becoming a Team Automobile Assembler primarily relies on vocational training and practical experience, rather than traditional four-year degrees. While a high school diploma or GED is usually a prerequisite, specialized technical training offers a significant advantage. Formal degree programs, like a Bachelor's in Mechanical Engineering, provide theoretical depth but are typically overqualified and costly for this role, ranging from $40,000 to $100,000+ over four years.
Alternative learning paths, such as vocational school programs, community college certificates, and manufacturer-specific training, are far more relevant and cost-effective. These programs usually cost between $3,000 and $15,000 and can be completed in 6 to 18 months. Employer acceptance for these credentials is high, as they demonstrate direct hands-on skills. Self-study, while possible for foundational knowledge, does not replace the practical experience gained in structured programs or apprenticeships.
Continuous learning is crucial for Team Automobile Assemblers due to evolving vehicle technologies, especially with electric and autonomous vehicles. Employers often provide on-the-job training for new models or specialized assembly techniques. Practical experience gained through internships, apprenticeships, or entry-level positions is highly valued, often outweighing theoretical knowledge from broad academic degrees. The cost-benefit analysis strongly favors vocational training and direct industry experience for this specific role, as they offer a direct path to employment without the significant time and financial investment of a university degree.
Team Automobile Assembler Salary & Outlook
Compensation for an Automobile Assembler varies significantly based on several factors beyond just the base hourly wage. Geographic location plays a crucial role; areas with major automotive manufacturing hubs, such as Michigan, Ohio, and parts of the South, often offer higher wages due to concentrated industry demand and a higher cost of living. Conversely, regions with fewer manufacturing plants may see lower pay rates.
Experience directly correlates with earning potential. Entry-level assemblers typically start at lower hourly rates, while those with years of experience, specialized skills like robotics operation or advanced welding, or certifications in specific assembly processes can command significantly higher pay. Total compensation packages often include more than just base salary; they can feature overtime pay, production bonuses based on efficiency or quality metrics, and comprehensive benefits. These benefits typically include health insurance, paid time off, and retirement plans like 401(k) contributions.
Industry-specific trends, such as the shift towards electric vehicle (EV) production, also influence salary growth. Assemblers trained in EV manufacturing processes or battery assembly may see premium compensation. Union representation, common in the automotive sector, also impacts wages and benefits, often leading to standardized pay scales and robust benefits packages. Negotiation leverage comes from demonstrating a strong work ethic, a commitment to quality, and adaptability to new technologies. While remote work is not applicable for this hands-on role, the domestic market sets the primary salary benchmarks, though international automotive hubs may have different compensation structures.
Salary by Experience Level
Level | US Median | US Average |
---|---|---|
Junior Automobile Assembler | $38k USD | $40k USD |
Automobile Assembler | $46k USD | $48k USD |
Senior Automobile Assembler | $54k USD | $56k USD |
Lead Automobile Assembler | $62k USD | $65k USD |
Assembly Line Supervisor | $75k USD | $78k USD |
Market Commentary
The job market for Automobile Assemblers is currently stable, with moderate growth driven by consistent vehicle demand and the ongoing transition to electric vehicles. The U.S. Bureau of Labor Statistics projects a modest growth rate for assembly line workers, including automobile assemblers, indicating a steady demand for skilled labor in manufacturing. This growth is particularly concentrated in states with established automotive manufacturing footprints.
Emerging opportunities for Automobile Assemblers are increasingly tied to the electric vehicle sector. New EV manufacturing plants are opening, creating demand for assemblers trained in battery module integration, electric motor assembly, and specific EV chassis construction. This shift requires assemblers to adapt to new technologies and processes, making continuous learning vital for career longevity. Automation and advanced robotics are also becoming more prevalent on assembly lines. While robots handle repetitive tasks, human assemblers are needed for complex operations, quality control, maintenance, and programming these automated systems. This evolution means the role is becoming more technical, requiring problem-solving skills alongside manual dexterity.
Supply and demand dynamics vary by region; some areas experience a shortage of skilled manufacturing workers, while others have a more balanced market. The automotive assembly profession is somewhat cyclical, tied to consumer spending and economic health, but remains essential for vehicle production. Future-proofing involves acquiring skills in new manufacturing techniques, digital literacy, and understanding automation interfaces. Geographic hotspots for employment include the traditional Midwest automotive belt and emerging manufacturing zones in the Southern states, which are attracting new investment in EV production.
Team Automobile Assembler Career Path
Career progression for a Team Automobile Assembler typically follows a structured path, emphasizing the development of precision, efficiency, and adherence to safety protocols. Individuals advance by consistently demonstrating high-quality work, increasing their speed, and mastering complex assembly tasks. This field offers distinct pathways: remaining on the individual contributor (IC) track to become a highly specialized expert or transitioning into a management/leadership track to oversee teams and operations.
Advancement speed depends on several factors, including individual performance, the willingness to specialize in critical areas like robotics or advanced welding, and the specific company's growth trajectory. Larger automotive manufacturers often provide more defined progression paths and training opportunities compared to smaller custom shops. Lateral movement can occur between different assembly lines or departments, such as quality control or logistics, offering broader experience within the manufacturing environment.
Continuous learning, especially through company-sponsored training on new technologies and lean manufacturing principles, is crucial for progression. Networking within the plant, seeking mentorship from experienced assemblers or supervisors, and building a reputation for reliability and problem-solving accelerate career growth. Certifications in specific assembly techniques or safety protocols also mark significant milestones. Some assemblers may pivot into roles like production planning, industrial engineering, or even technical training, leveraging their deep understanding of the assembly process.
Junior Automobile Assembler
0-2 yearsKey Focus Areas
Automobile Assembler
2-4 years total experienceKey Focus Areas
Senior Automobile Assembler
4-7 years total experienceKey Focus Areas
Lead Automobile Assembler
7-10 years total experienceKey Focus Areas
Assembly Line Supervisor
10+ years total experienceKey Focus Areas
Junior Automobile Assembler
0-2 yearsPerforms entry-level assembly tasks under close supervision, focusing on a limited set of components or a specific station on the assembly line. Responsibilities include attaching parts, tightening fasteners, and performing basic quality checks. Works as part of a team, contributing to the overall production flow. Decisions are typically pre-defined by standard operating procedures.
Key Focus Areas
Develop foundational skills in tool usage, part identification, and basic assembly techniques. Focus on understanding and strictly following safety procedures and quality standards. Practice precise movements and efficient work habits under direct supervision. Learn to identify common defects and report them promptly. Build familiarity with different components and their placement within the vehicle.
Automobile Assembler
2-4 years total experienceExecutes a variety of complex assembly operations independently, often rotating through several workstations on the line. Responsibilities include fitting, aligning, and securing components, operating specialized machinery, and performing detailed quality inspections. Makes routine decisions based on established procedures and escalates more complex issues to senior personnel. Contributes significantly to daily production targets.
Key Focus Areas
Master a wider range of assembly tasks and become proficient across multiple stations. Focus on increasing speed and efficiency while maintaining high quality standards. Develop problem-solving skills for minor assembly issues and learn to interpret complex blueprints or work instructions. Take initiative in identifying process improvements and participate in team problem-solving sessions.
Senior Automobile Assembler
4-7 years total experienceServes as a highly skilled and experienced assembler, often specializing in critical or technically challenging areas of vehicle assembly. Responsibilities include performing intricate tasks, resolving complex assembly defects, and assisting with equipment calibration or minor maintenance. Provides guidance and on-the-job training to less experienced team members. Operates with significant autonomy, making decisions to maintain production quality and flow.
Key Focus Areas
Achieve expert-level proficiency in all assembly operations within a specific area or across multiple product lines. Develop advanced troubleshooting skills for complex assembly problems and machinery malfunctions. Begin mentoring junior assemblers and share best practices. Focus on optimizing workflow, reducing waste, and improving overall line efficiency. Participate in continuous improvement initiatives and pilot new assembly techniques.
Lead Automobile Assembler
7-10 years total experienceActs as a working team leader, directing the efforts of a small group of assemblers at a specific section of the assembly line. Responsibilities include assigning tasks, monitoring progress, ensuring quality control, and providing immediate technical assistance. Troubleshoots minor equipment issues and ensures the team meets production targets. Facilitates communication between the assembly team and supervisors.
Key Focus Areas
Develop strong leadership and communication skills, effectively guiding a small team of assemblers. Focus on coordinating tasks, ensuring adherence to production schedules, and resolving immediate operational issues. Learn to interpret production metrics and contribute to performance reporting. Enhance problem-solving capabilities, particularly concerning team dynamics and process bottlenecks. Actively participate in training and onboarding new team members.
Assembly Line Supervisor
10+ years total experienceManages and oversees a larger section of the assembly line or an entire shift, responsible for the performance, safety, and morale of a team of assemblers. Responsibilities include scheduling, performance reviews, training, and implementing continuous improvement initiatives. Ensures adherence to production goals, quality standards, and safety regulations. Makes critical operational decisions, allocates resources, and collaborates with other departments to optimize the manufacturing process.
Key Focus Areas
Cultivate comprehensive leadership, team management, and operational planning skills. Focus on maximizing team productivity, managing performance, and fostering a positive work environment. Develop expertise in lean manufacturing principles, safety regulations, and quality management systems. Gain proficiency in data analysis for production reporting and strategic decision-making. Build strong interpersonal skills for conflict resolution and effective communication across departments.
Job Application Toolkit
Ace your application with our purpose-built resources:
Team Automobile Assembler Resume Examples
Proven layouts and keywords hiring managers scan for.
View examplesTeam Automobile Assembler Cover Letter Examples
Personalizable templates that showcase your impact.
View examplesTop Team Automobile Assembler Interview Questions
Practice with the questions asked most often.
View examplesTeam Automobile Assembler Job Description Template
Ready-to-use JD for recruiters and hiring teams.
View examplesGlobal Team Automobile Assembler Opportunities
The Team Automobile Assembler role is globally standardized, focusing on efficiency and quality in vehicle production lines. Demand for skilled assemblers remains consistent in major automotive manufacturing hubs worldwide, driven by evolving production technologies and new model launches. Cultural differences affect workplace communication and safety protocols, while regulatory frameworks dictate labor standards. Professionals consider international roles for higher wages or specialized training. No specific international certifications exist; on-the-job training and experience are primary qualifications.
Global Salaries
Team Automobile Assembler salaries vary significantly by region, reflecting economic conditions and unionization. In North America, a typical assembler earns $45,000-$70,000 USD annually, particularly in the US and Canada, often with strong benefits and overtime pay. This range reflects higher purchasing power in these countries, despite higher living costs in manufacturing centers.
European salaries range from €30,000-€55,000 EUR (approx. $32,000-$60,000 USD) in Germany and France, with lower ranges in Eastern Europe, such as €15,000-€25,000 EUR (approx. $16,000-$27,000 USD) in countries like Poland or Hungary. These figures include comprehensive social security benefits and ample vacation time, which are common in Europe. Take-home pay is influenced by higher tax rates in Western Europe.
In Asia-Pacific, Japan and South Korea offer competitive wages from ¥3,500,000-¥6,000,000 JPY (approx. $23,000-$40,000 USD) and ₩40,000,000-₩65,000,000 KRW (approx. $29,000-$48,000 USD) respectively, often including performance bonuses. China's assemblers earn ¥60,000-¥120,000 CNY (approx. $8,500-$17,000 USD), but with a lower cost of living. Experience and specialized skills, like robotics operation, significantly impact compensation across all regions.
Latin American salaries are typically lower, ranging from $10,000-$25,000 USD in Mexico or Brazil, reflecting lower purchasing power. Benefits packages often include basic healthcare and limited vacation. International pay scales are not standardized for this role; compensation reflects local labor market conditions and cost of living. Education beyond a high school diploma is less critical than practical experience for salary progression.
Remote Work
Remote work for a Team Automobile Assembler is generally not possible. This role requires hands-on physical presence on the factory floor, directly interacting with vehicles, tools, and assembly lines. The nature of the work, involving manual dexterity and specialized equipment, prohibits off-site operations.
Digital nomad opportunities or remote work policies are not applicable to this profession. Employers globally require assemblers to be physically present at the manufacturing plant. Therefore, tax implications or time zone considerations for international remote work do not apply to this specific job title.
Some related roles, such as design or quality control, might offer limited hybrid or remote options. However, the core function of a Team Automobile Assembler remains entirely on-site. Equipment requirements include factory-specific tools and safety gear, which are only accessible within the plant environment.
Visa & Immigration
Immigration pathways for Team Automobile Assemblers typically involve skilled worker visas. Popular destinations include Germany, Canada, the US, and Japan, all with significant automotive industries. Requirements often include a job offer from a local employer, relevant work experience, and sometimes vocational training or certification. Education credential recognition is less critical than practical experience in this field.
For example, Germany's Skilled Immigration Act allows non-EU skilled workers with a job offer to apply for a visa. Canada's Express Entry system may consider assemblers under specific provincial nominee programs if demand exists. US H-2B visas are for temporary non-agricultural workers, potentially including assemblers, but require employer sponsorship. Japan offers specific visas for skilled trades, often requiring Japanese language proficiency.
Visa timelines vary, typically ranging from a few months to over a year. Professional licensing is not common for assemblers, but specific safety certifications may be required. Language requirements depend on the country; English is often sufficient in Canada, while local language skills are crucial in Germany or Japan. Pathways to permanent residency exist in many countries after several years of continuous employment. Family visas are usually available for spouses and dependents.
2025 Market Reality for Team Automobile Assemblers
Understanding the current market realities for team automobile assemblers is vital for career planning. The automotive industry is in a significant transition, driven by post-pandemic recovery efforts and the accelerating shift towards electric vehicles.
These shifts, combined with broader economic factors like inflation and supply chain adjustments, directly influence hiring volumes and skill requirements. The impact varies considerably by plant location, company size, and the specific vehicle segments being produced. This analysis provides an honest assessment to help assemblers navigate their career paths effectively.
Current Challenges
Automobile assemblers face intensified competition, particularly from automation. Many entry-level roles see saturation as companies optimize production lines. Economic slowdowns directly affect vehicle demand, leading to hiring freezes. Adapting to new vehicle technologies also requires continuous training, a challenge for some.
Growth Opportunities
Despite challenges, specific opportunities exist for team automobile assemblers. Plants producing electric vehicles or advanced driver-assistance systems (ADAS) components are experiencing strong demand for skilled assemblers. These roles often require specialized training in battery integration or sensor calibration.
Assemblers who proactively acquire certifications in robotics operation, advanced manufacturing techniques, or EV-specific assembly processes gain a significant competitive edge. Companies are willing to invest in training for individuals demonstrating high aptitude and a commitment to continuous learning. Exploring opportunities in regions with newer assembly plants or those expanding EV production lines often yields better prospects.
Furthermore, the industry's focus on quality and efficiency means that assemblers with strong problem-solving skills and a meticulous approach to their work are highly valued. Internal promotions to team lead or quality control roles are common for experienced, reliable assemblers. Strategic career moves now involve aligning skills with the industry's technological evolution, particularly in automation and electrification.
Current Market Trends
Hiring for team automobile assemblers shows mixed signals as of 2025. Demand remains steady in plants producing popular, high-volume models, but overall growth has slowed. The industry is heavily investing in automation and robotics, which streamlines assembly lines but also shifts labor needs towards oversight and maintenance rather than direct assembly tasks.
Economic conditions, including fluctuating consumer confidence and interest rates, directly impact vehicle sales and, consequently, production volumes. This creates a cyclical hiring pattern, with periods of strong demand followed by adjustments. The transition to electric vehicles (EVs) also introduces new assembly processes and material handling requirements, necessitating updated skills for assemblers.
Employers increasingly seek assemblers with foundational technical aptitude and adaptability. Familiarity with basic robotic operation, quality control software, and data input systems is becoming more valuable. While wages have seen some upward pressure due to union negotiations and skilled labor shortages in specific areas, market saturation exists in regions with multiple assembly plants, potentially capping entry-level salaries. Remote work is not applicable to this hands-on role; job availability is strictly tied to factory locations.
Emerging Specializations
Technological advancements and evolving manufacturing paradigms are continuously reshaping the landscape for team automobile assemblers. New specialization opportunities arise from the integration of advanced robotics, artificial intelligence, and sustainable manufacturing practices into automotive production lines. Understanding these future-oriented paths allows assemblers to strategically position themselves for career advancement.
Early positioning in emerging areas often commands premium compensation and enhanced career growth beyond 2025. While established assembly specializations remain vital, focusing on next-generation skills provides a distinct advantage. This strategic choice balances the stability of current roles with the significant upside of cutting-edge expertise.
Emerging specializations typically take 3-5 years to become mainstream and create a substantial number of job opportunities. Investing in these areas now prepares professionals for the significant demand that will follow. Pursuing cutting-edge specializations involves a calculated risk, but the potential for higher earnings and leadership roles in a transforming industry often outweighs the initial investment in new skill acquisition.
Autonomous Systems Integration Assembler
Electric Vehicle Powertrain Assembler
Robotics & Cobot Interaction Specialist
Sustainable Manufacturing Assembler
Advanced Materials & Additive Manufacturing Assembler
Pros & Cons of Being a Team Automobile Assembler
Understanding the full scope of a career, including both its benefits and challenges, is crucial for making informed decisions. Experiences in any profession, such as a Team Automobile Assembler, can vary significantly based on the specific company culture, the level of automation in the plant, and individual team dynamics. What one person perceives as an advantage, another might see as a challenge, reflecting diverse personal values and lifestyle preferences.
Moreover, the demands and rewards of an assembler role can evolve at different career stages, from initial training to becoming a seasoned expert. This assessment provides an honest, balanced view to help set realistic expectations for anyone considering this hands-on career path.
Pros
- Stable employment with consistent demand often exists in the automotive manufacturing sector, providing good job security, especially with major manufacturers.
- Direct contribution to a tangible product provides a sense of accomplishment, as assemblers see a vehicle come together through their direct efforts.
- Team-oriented environment fosters camaraderie and collaboration, as individuals work closely with colleagues to meet production goals and solve immediate issues.
- Opportunities for skill development in specialized assembly techniques, tool operation, and quality control are common, enhancing a worker's practical expertise.
- Competitive wages and comprehensive benefits packages, including health insurance, retirement plans, and paid time off, are typically offered by large automotive companies.
- Clear training pathways are often available, allowing new assemblers to quickly learn the required skills through structured programs and on-the-job instruction.
- Predictable work routines mean a consistent schedule and set tasks each day, which can be appealing for those who prefer structured environments.
Cons
- Repetitive tasks can lead to monotony and boredom over long periods, as the same set of actions are performed repeatedly on each vehicle.
- Physically demanding work often involves standing for extended periods, bending, lifting, and performing precise movements, which can cause strain and fatigue.
- Risk of injury from power tools, heavy components, and fast-paced assembly lines is present, requiring constant vigilance and adherence to safety protocols.
- Exposure to noise, fumes, and vibrations from machinery and ongoing production processes can be an environmental challenge in the workspace.
- Strict production quotas and tight deadlines create constant pressure to maintain speed and accuracy, which can be stressful for some individuals.
- Limited opportunities for immediate career advancement often exist within the assembler role itself, with progression typically requiring additional training or moving into supervisory positions.
- Work schedules may include night shifts, rotating shifts, or mandatory overtime, impacting personal life and work-life balance.
Frequently Asked Questions
Team Automobile Assemblers face distinct challenges around the physical demands of the job, the precision required, and the integration into a fast-paced production line. This section addresses the most common questions about entering this role, from training requirements to career progression within an automotive plant.
What are the basic educational or training requirements to become a Team Automobile Assembler?
Most entry-level Team Automobile Assembler positions require a high school diploma or GED. Some employers prefer vocational training or certifications in manufacturing, welding, or automotive technology, but often provide on-the-job training for specific assembly tasks. Demonstrating a strong work ethic, attention to detail, and ability to follow instructions is crucial for securing a role.
How long does it typically take to become job-ready as a Team Automobile Assembler from scratch?
The timeline to become job-ready for an entry-level assembler position is relatively short. If you have the basic qualifications, you can often start with on-the-job training provided by the manufacturer, which can last from a few weeks to a couple of months. Some vocational programs might add 3-6 months of focused training, but direct entry is common.
What are the typical salary expectations for an entry-level Team Automobile Assembler?
Entry-level Team Automobile Assemblers typically earn competitive hourly wages, often ranging from $18 to $25 per hour, depending on the manufacturer, location, and union agreements. With experience, specialized skills, and tenure, wages can increase significantly. Many positions also offer comprehensive benefits packages, including health insurance, retirement plans, and paid time off.
What is the typical work-life balance like for an Automobile Assembler, considering shift work and demands?
The work-life balance for Team Automobile Assemblers often involves working shifts, including nights and weekends, especially in plants with 24/7 operations. Overtime can be common during peak production. While the work can be physically demanding and repetitive, most employers adhere to strict safety standards and provide regular breaks, offering a predictable schedule once you adapt to the shift rotation.
Is the job of a Team Automobile Assembler secure, given industry changes like automation and EVs?
The job security for Team Automobile Assemblers is generally stable, though it can fluctuate with automotive market demand and economic cycles. The industry continues to evolve with electric vehicles and automation, creating new roles and requiring adaptability. Skilled assemblers who are open to learning new processes and technologies often find long-term stability.
What are the potential career growth opportunities for a Team Automobile Assembler?
Team Automobile Assemblers have several avenues for career growth. You can advance to lead assembler, team leader, or supervisor roles, taking on more responsibility for production quality and team management. Opportunities also exist in quality control, maintenance, or specialized technical roles within the plant, often requiring additional training or certifications. Some even transition into engineering support roles.
What are the biggest challenges or downsides to working as a Team Automobile Assembler?
The primary challenges include the physical demands of repetitive tasks, working in a fast-paced environment, and adhering to strict quality standards. Assemblers must maintain focus and precision for extended periods. Adapting to new vehicle models and manufacturing processes also requires continuous learning and flexibility. Safety protocols are paramount, and adherence is non-negotiable.
Can Team Automobile Assemblers work remotely, or is it strictly an on-site role?
Team Automobile Assembler roles are almost exclusively on-site within manufacturing plants. The nature of the work requires direct interaction with the assembly line, machinery, and physical components, making remote work infeasible. Therefore, you must be prepared to commute to a specific plant location for employment.
Related Careers
Explore similar roles that might align with your interests and skills:
Assembler
A growing field with similar skill requirements and career progression opportunities.
Explore career guideAssembly Mechanic
A growing field with similar skill requirements and career progression opportunities.
Explore career guideAssembly Operator
A growing field with similar skill requirements and career progression opportunities.
Explore career guideMechanical Assembler
A growing field with similar skill requirements and career progression opportunities.
Explore career guideTeam Assembly Line Machine Operator
A growing field with similar skill requirements and career progression opportunities.
Explore career guideAssess your Team Automobile Assembler readiness
Understanding where you stand today is the first step toward your career goals. Our Career Coach helps identify skill gaps and create personalized plans.
Skills Gap Analysis
Get a detailed assessment of your current skills versus Team Automobile Assembler requirements. Our AI Career Coach identifies specific areas for improvement with personalized recommendations.
See your skills gapCareer Readiness Assessment
Evaluate your overall readiness for Team Automobile Assembler roles with our AI Career Coach. Receive personalized recommendations for education, projects, and experience to boost your competitiveness.
Assess your readinessSimple pricing, powerful features
Upgrade to Himalayas Plus and turbocharge your job search.
Himalayas
Himalayas Plus
Himalayas Max
Find your dream job
Sign up now and join over 100,000 remote workers who receive personalized job alerts, curated job matches, and more for free!
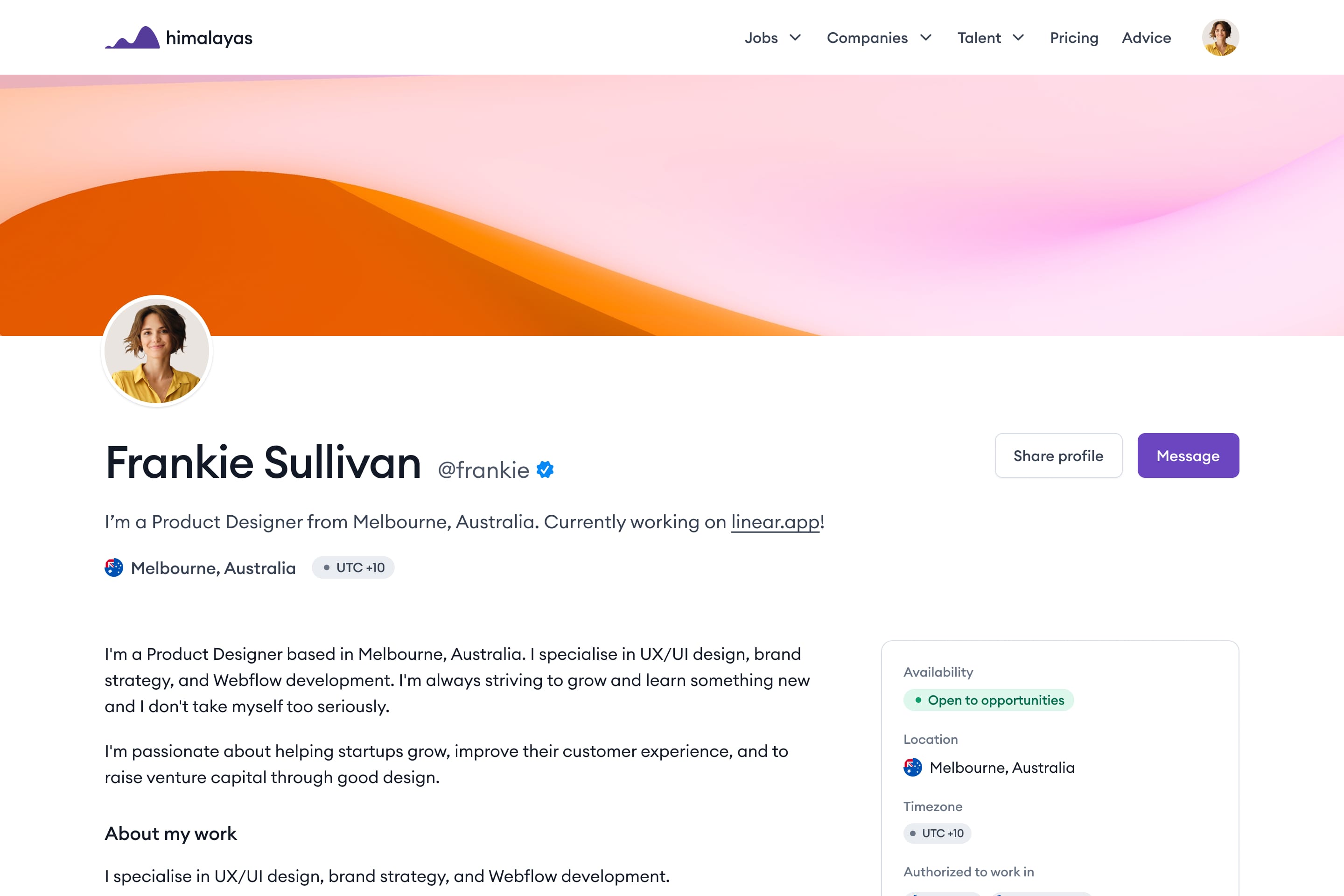