5 Assembly Mechanic Interview Questions and Answers
Assembly Mechanics are skilled professionals responsible for assembling mechanical components and systems according to specifications. They work with tools and machinery to ensure that parts fit correctly and function as intended. Junior Assembly Mechanics focus on learning the basics and assisting in assembly tasks, while Senior and Lead Assembly Mechanics take on more complex projects, oversee quality control, and may supervise teams. They play a critical role in manufacturing and production environments, ensuring that products are built to high standards of quality and safety. Need to practice for an interview? Try our AI interview practice for free then unlock unlimited access for just $9/month.
Unlimited interview practice for $9 / month
Improve your confidence with an AI mock interviewer.
No credit card required
1. Junior Assembly Mechanic Interview Questions and Answers
1.1. Can you describe a time when you had to troubleshoot a mechanical issue during assembly?
Introduction
This question is important as it assesses your problem-solving skills and your ability to work under pressure, which are critical for a Junior Assembly Mechanic.
How to answer
- Use the STAR method to structure your response
- Begin by clearly describing the mechanical issue you encountered
- Explain the steps you took to diagnose the problem
- Describe how you resolved the issue and any tools or techniques used
- Quantify the outcome, if possible, to demonstrate the impact of your solution
What not to say
- Avoid vague descriptions of the problem without specific details
- Don't focus only on the tools without explaining your thought process
- Refrain from blaming others for the issue without taking responsibility
- Avoid discussing unresolved issues as they do not showcase your problem-solving skills
Example answer
“During my internship at Fiat, I encountered a situation where the assembly line was halted due to a malfunctioning part. I quickly diagnosed the issue as a misalignment in the assembly jigs. I recalibrated the jigs and re-assembled the parts, which restored the line's functionality. This experience taught me the importance of attention to detail and effective troubleshooting under pressure.”
Skills tested
Question type
1.2. How do you ensure quality and precision in your assembly work?
Introduction
This question evaluates your understanding of quality control processes and your commitment to maintaining high standards in mechanical assembly.
How to answer
- Outline your understanding of quality standards relevant to assembly work
- Describe specific techniques or processes you use to ensure accuracy
- Discuss any tools or equipment you utilize for quality checks
- Provide examples of how you have maintained or improved quality in past roles
- Emphasize the importance of following protocols and guidelines
What not to say
- Suggesting that quality is not a priority in assembly work
- Failing to provide specific examples or techniques
- Ignoring the importance of following guidelines and protocols
- Discussing quality control only in relation to other people's work
Example answer
“I believe that maintaining quality is crucial in assembly work. I always double-check my work against the assembly specifications and use calipers and gauges to ensure precision. In my previous role, I implemented a peer review process where we checked each other’s work, which reduced errors by 20%. This focus on quality not only enhanced the final product but also improved team collaboration.”
Skills tested
Question type
2. Assembly Mechanic Interview Questions and Answers
2.1. Can you describe a time when you identified a defect during the assembly process and how you addressed it?
Introduction
This question is crucial for assessing your attention to detail, problem-solving abilities, and commitment to quality in the assembly process.
How to answer
- Begin with a specific example using the STAR method (Situation, Task, Action, Result)
- Clearly outline the defect you identified and the potential impact it could have had on the final product
- Explain the steps you took to address the defect, including any collaboration with team members or supervisors
- Discuss the outcome of your actions, including any improvements in quality or efficiency
- Emphasize the importance of quality control in assembly work
What not to say
- Avoid vague answers that lack a specific example or context
- Don't focus solely on the defect without discussing your response or resolution
- Refrain from blaming others for the defect without taking personal responsibility
- Steer clear of mentioning defects you ignored or overlooked
Example answer
“During my time at Bombardier, I noticed a misalignment in the components of an aircraft wing assembly. Recognizing the potential safety impact, I immediately halted the assembly line and notified my supervisor. We conducted a thorough inspection and corrected the misalignment before proceeding. This proactive approach not only ensured safety but also improved our team's efficiency by reducing rework time by 15%.”
Skills tested
Question type
2.2. How do you stay organized and manage your time when working on multiple assembly projects?
Introduction
This question evaluates your organizational skills and ability to prioritize tasks effectively in a fast-paced assembly environment.
How to answer
- Describe your methods for prioritizing tasks based on deadlines and project importance
- Explain any tools or techniques you use to keep track of your work (e.g., checklists, scheduling software)
- Share an example of a time when you successfully managed multiple projects simultaneously
- Discuss how you communicate with team members to coordinate efforts and avoid bottlenecks
- Mention any adjustments you make to improve efficiency or address challenges
What not to say
- Avoid saying you don’t have a specific method for organization
- Don't mention being overwhelmed or unable to manage multiple tasks
- Refrain from neglecting to highlight teamwork or communication aspects
- Steer clear of generic answers that don’t provide specific examples
Example answer
“At Toyota, I often handled multiple assembly projects. I use a digital task manager to prioritize my daily tasks based on deadlines and project complexity. For instance, while working on two different vehicle models, I scheduled specific times for each project, ensuring I maintained focus. Regular check-ins with my team helped us coordinate our efforts effectively, which led to a 20% increase in our overall productivity during that period.”
Skills tested
Question type
3. Senior Assembly Mechanic Interview Questions and Answers
3.1. Can you describe a complex assembly project you worked on and the challenges you faced?
Introduction
This question assesses your technical expertise and problem-solving ability in real-world assembly situations, which are crucial for a Senior Assembly Mechanic.
How to answer
- Clearly outline the project scope and objectives.
- Discuss specific challenges encountered during the assembly process.
- Explain the steps you took to overcome these challenges.
- Highlight any teamwork or collaboration involved.
- Mention the successful outcome and any metrics that demonstrate success.
What not to say
- Focusing too much on minor technical details without context.
- Not acknowledging the role of the team or others involved.
- Failing to mention the impact of the project on the organization.
- Avoiding discussion of challenges, which may indicate a lack of experience.
Example answer
“In my previous role at Fiat, I worked on assembling a prototype for a new vehicle. One significant challenge was integrating a new electronic system into the assembly line. I coordinated closely with the engineering team to troubleshoot connectivity issues, which involved re-evaluating our assembly process. Ultimately, we successfully integrated the system ahead of schedule, improving production efficiency by 20%.”
Skills tested
Question type
3.2. How do you ensure quality in your assembly work?
Introduction
This question evaluates your understanding of quality assurance practices and your commitment to maintaining high standards in assembly tasks.
How to answer
- Discuss specific quality control methods you use.
- Explain how you incorporate feedback and continuous improvement.
- Describe any relevant certifications or training in quality assurance.
- Provide examples of how you’ve caught and corrected errors in the past.
- Mention your approach to training others on quality standards.
What not to say
- Suggesting that quality checks are not necessary.
- Failing to provide concrete examples of quality assurance.
- Neglecting to mention any ongoing education or training.
- Overlooking the importance of documenting quality issues.
Example answer
“I ensure quality by implementing rigorous checks at each phase of the assembly process. For instance, I use visual inspections and measurement tools to verify tolerances. At my last job with Lamborghini, I identified a recurring issue with part misalignment early on, leading to a redesign of the assembly fixture, which reduced defects by 30%. I also conduct training sessions to share best practices with junior mechanics.”
Skills tested
Question type
4. Lead Assembly Mechanic Interview Questions and Answers
4.1. Can you describe a complex assembly project you worked on and the challenges you faced during the process?
Introduction
This question assesses your technical expertise and problem-solving skills, which are vital for a Lead Assembly Mechanic responsible for overseeing complex projects.
How to answer
- Use the STAR method (Situation, Task, Action, Result) to structure your response
- Provide specific details about the assembly project, including the components involved
- Discuss the particular challenges you encountered, whether technical or team-related
- Explain the solutions you implemented to overcome these challenges
- Highlight the successful outcomes and any lessons learned
What not to say
- Vaguely describing the project without specific details
- Focusing solely on the challenges without discussing solutions
- Taking full credit without acknowledging teamwork
- Ignoring safety considerations or protocols
Example answer
“In my role at Boeing Australia, I led a team assembling a new aircraft model which faced unexpected delays due to parts shortages. We quickly adapted by developing strong relationships with suppliers to expedite deliveries. This proactive approach not only kept the project on schedule but also resulted in a 15% reduction in assembly time. The experience taught me the importance of supplier collaboration and adaptability in project management.”
Skills tested
Question type
4.2. How do you ensure quality control in the assembly process, and can you give an example of a time when you identified a quality issue?
Introduction
This question evaluates your understanding of quality control processes and your attention to detail, both critical for a Lead Assembly Mechanic.
How to answer
- Discuss your approach to quality assurance during assembly
- Provide a specific example of a quality issue you encountered
- Explain how you identified the issue and the steps you took to rectify it
- Highlight the impact of your actions on the final product and team morale
- Mention any preventive measures you implemented to avoid future issues
What not to say
- Claiming that quality control is not a significant part of your role
- Focusing on the problem without demonstrating how you resolved it
- Neglecting to mention team involvement or collaboration
- Providing a generic answer without specific examples
Example answer
“At Thales Australia, I noticed a recurring issue with misaligned components during final assembly checks. I initiated a review of our assembly processes and discovered a lack of alignment in the initial setup. By implementing a standardized checklist and additional training for the team, we reduced alignment errors by 30%. This not only improved product quality but also boosted team confidence in our assembly processes.”
Skills tested
Question type
5. Assembly Supervisor Interview Questions and Answers
5.1. Can you describe a time when you had to resolve a conflict between team members on the assembly line?
Introduction
This question assesses your conflict resolution skills and ability to maintain a harmonious working environment, which is crucial for team productivity and morale.
How to answer
- Use the STAR method to structure your response: Situation, Task, Action, Result.
- Explain the context of the conflict and the parties involved.
- Detail the steps you took to mediate the situation and facilitate communication.
- Share the outcome of your intervention and how it improved team dynamics.
- Highlight any lessons learned and how it influenced your approach to team management.
What not to say
- Blaming team members for the conflict without taking responsibility.
- Ignoring the importance of resolving conflicts for team productivity.
- Failing to describe specific actions taken to resolve the issue.
- Giving vague or generic responses without concrete examples.
Example answer
“In my previous role at General Motors, I noticed two assembly line workers were arguing over task responsibilities, which affected their performance. I arranged a private meeting with both individuals to discuss their concerns. I encouraged them to express their viewpoints and facilitated a dialogue to find common ground. As a result, they agreed on a shared approach to their tasks, leading to a more cohesive working relationship and a 15% increase in their output over the next month.”
Skills tested
Question type
5.2. How do you ensure quality control on the assembly line while meeting production deadlines?
Introduction
This question evaluates your ability to balance quality assurance with productivity, which is essential for maintaining standards in manufacturing environments.
How to answer
- Describe your approach to implementing quality control measures.
- Explain how you monitor compliance with these standards during production.
- Detail any tools or techniques you use to track quality metrics.
- Share examples of how you've successfully maintained quality while meeting deadlines.
- Discuss the importance of training and empowering team members to uphold quality standards.
What not to say
- Neglecting the importance of quality in favor of speed.
- Failing to provide specific methods or tools used for quality assurance.
- Claiming that quality control is solely the responsibility of a separate department.
- Ignoring previous experiences where quality was compromised.
Example answer
“At Ford, I implemented a quality control checklist that each team member completed at the end of their shift. During peak production times, I ensured that necessary resources were allocated for additional quality checks without slowing down the line. This approach not only maintained our quality standards but also allowed us to meet our production targets consistently, reducing defects by 20% over three months.”
Skills tested
Question type
Similar Interview Questions and Sample Answers
Simple pricing, powerful features
Upgrade to Himalayas Plus and turbocharge your job search.
Himalayas
Himalayas Plus
Himalayas Max
Find your dream job
Sign up now and join over 100,000 remote workers who receive personalized job alerts, curated job matches, and more for free!
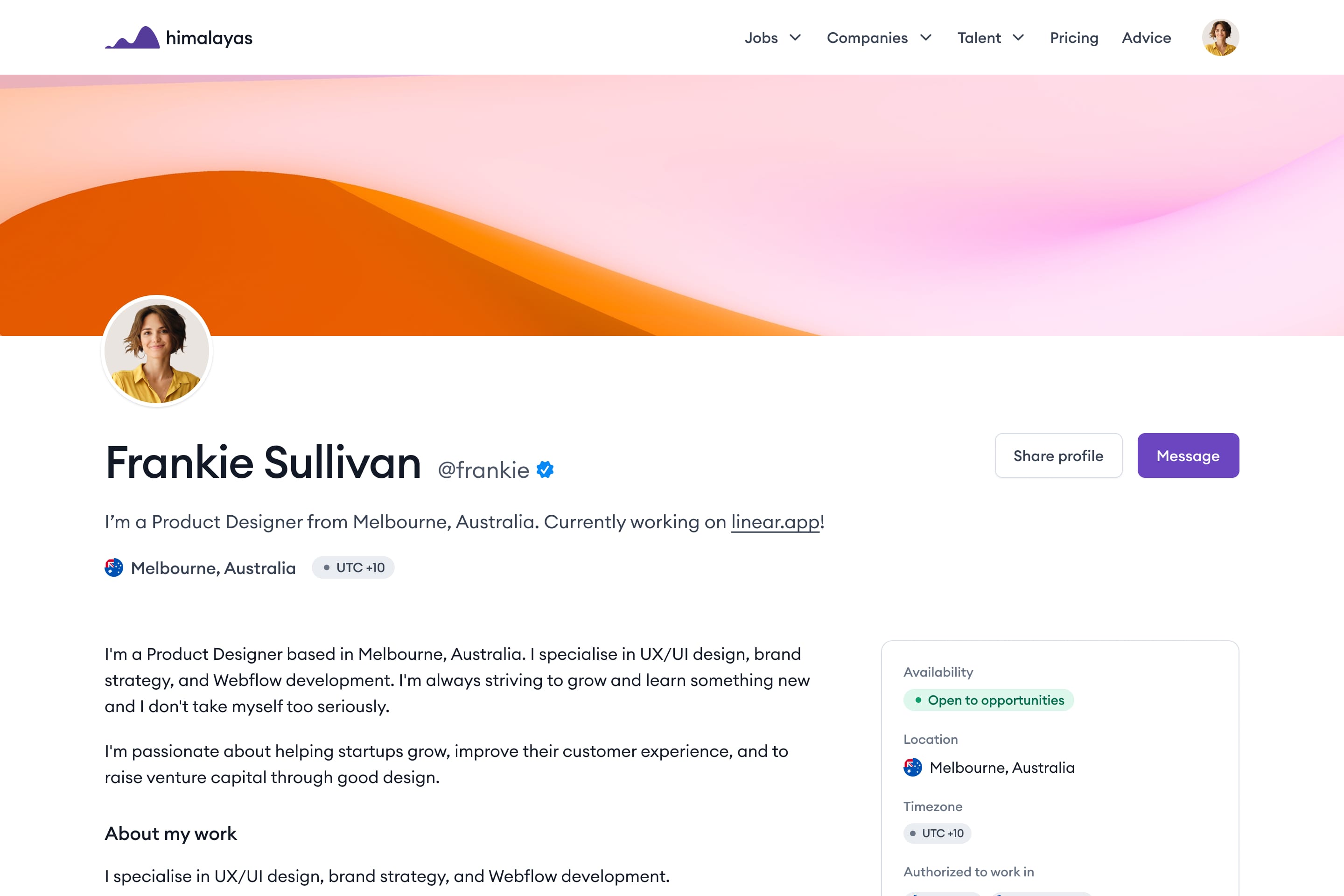