5 Assembler Interview Questions and Answers
Assemblers are responsible for putting together parts or components to create finished products according to specifications. They work with tools and machinery, ensuring that each piece is correctly fitted and meets quality standards. Entry-level assemblers focus on learning the assembly process and following instructions, while senior and lead assemblers may oversee assembly lines, ensure quality control, and train new employees. Need to practice for an interview? Try our AI interview practice for free then unlock unlimited access for just $9/month.
Unlimited interview practice for $9 / month
Improve your confidence with an AI mock interviewer.
No credit card required
1. Entry-level Assembler Interview Questions and Answers
1.1. Can you describe a time when you had to follow specific instructions to complete a task?
Introduction
This question is crucial for an assembler as the role requires strict adherence to guidelines and precision in executing tasks.
How to answer
- Start with a brief description of the task you were given
- Explain the instructions and why they were important
- Detail the steps you took to follow those instructions
- Discuss the outcome and how your attention to detail contributed
- Mention any feedback you received from supervisors or colleagues
What not to say
- Vague descriptions of tasks without specific details
- Claiming you didn’t follow instructions and it didn’t matter
- Failing to discuss the importance of accuracy in the role
- Not mentioning any positive outcomes or learning experiences
Example answer
“During my internship at a local manufacturing plant, I was tasked with assembling parts for a new product line. I had to follow a detailed assembly guide that outlined the specific order and method for assembling components. By carefully adhering to these instructions, I successfully completed the task ahead of schedule, which was recognized by my supervisor as a key contribution to the project. This experience taught me the importance of precision and the impact it has on overall productivity.”
Skills tested
Question type
1.2. How do you handle repetitive tasks while maintaining accuracy?
Introduction
This question assesses your ability to focus and maintain quality in a role that often involves repetitive work, which is essential for an assembler.
How to answer
- Explain your strategies for staying focused during repetitive tasks
- Discuss any techniques you use to ensure accuracy
- Mention how you monitor your performance and correct errors
- Share any relevant experiences where your approach was successful
- Emphasize the importance of quality in your work
What not to say
- Expressing frustration with repetitive tasks without a solution
- Ignoring the importance of accuracy in assembly work
- Not providing any techniques or methods to maintain focus
- Failing to acknowledge the potential for errors
Example answer
“In my previous role as a part-time production assistant, I often had to perform the same assembly task for several hours. To stay focused, I set small goals for myself and took short breaks to reset my concentration. I also kept a checklist to ensure that each step was completed accurately. By doing this, I maintained a high level of accuracy and reduced the number of errors in my work, which was noted by my supervisor.”
Skills tested
Question type
2. Assembler Interview Questions and Answers
2.1. Can you describe a time when you had to solve a problem while assembling a product?
Introduction
This question assesses your problem-solving skills and ability to work under pressure, which are crucial for an assembler role where issues can arise unexpectedly during the assembly process.
How to answer
- Use the STAR method to structure your response: Situation, Task, Action, Result.
- Clearly describe the specific problem you encountered during the assembly process.
- Explain the steps you took to diagnose the issue and the reasoning behind your decisions.
- Detail the outcome of your actions and how it affected the final product quality.
- Mention any lessons learned or changes you implemented to avoid similar issues in the future.
What not to say
- Downplaying the significance of the problem or avoiding details.
- Not mentioning how you worked with team members or supervisors.
- Focusing only on the negative aspects without discussing solutions or results.
- Neglecting to show how you learned from the experience.
Example answer
“While working at BMW, I encountered a misalignment issue with a component during assembly. I quickly assessed the situation and found that the parts were labeled incorrectly. I communicated with my supervisor to correct the inventory and adjusted my assembly process to ensure accurate part identification. As a result, we improved assembly efficiency by 20% and reduced errors in subsequent batches. This experience taught me the importance of clear communication and attention to detail.”
Skills tested
Question type
2.2. What safety protocols do you follow when assembling products?
Introduction
This question gauges your awareness and application of safety protocols, which are essential in manufacturing environments to ensure personal safety and that of your colleagues.
How to answer
- Outline the specific safety protocols you are familiar with, such as the use of personal protective equipment (PPE) and machinery safety guidelines.
- Explain how you incorporate these protocols into your daily work routine.
- Provide examples of how you have trained or reminded others about safety practices.
- Discuss any experiences where adherence to safety protocols prevented an accident.
- Mention your willingness to learn and adapt to new safety regulations as they arise.
What not to say
- Claiming that safety protocols are not important or can be overlooked.
- Failing to provide specific examples of safety practices you follow.
- Neglecting to mention your role in promoting safety within your team.
- Being unaware of the safety training required in your previous roles.
Example answer
“In my previous role at Siemens, I strictly followed safety protocols by always wearing PPE such as gloves and goggles when handling machinery. I also conducted regular checks of my work area to ensure it was free from hazards. Once, I noticed a colleague not using their safety gear and reminded them of the rules, which reinforced our team's commitment to safety. I believe that a safe working environment is crucial for productivity and morale.”
Skills tested
Question type
3. Senior Assembler Interview Questions and Answers
3.1. Can you describe a time when you identified a quality issue in the assembly process and how you resolved it?
Introduction
This question assesses your attention to detail and problem-solving skills, which are crucial for ensuring high-quality assembly in manufacturing.
How to answer
- Use the STAR method to structure your response: Situation, Task, Action, Result
- Clearly describe the quality issue you encountered
- Explain the impact of the issue on production and product quality
- Detail the steps you took to investigate and resolve the issue
- Highlight the outcome and any improvements made to prevent future occurrences
What not to say
- Blaming others for the quality issue without taking responsibility
- Providing vague or unclear examples
- Focusing solely on the problem rather than the solution
- Neglecting to mention the importance of quality control
Example answer
“In my previous role at Toyota Australia, I noticed that a specific component was consistently misaligned during assembly, leading to increased rework. I initiated a root cause analysis and discovered that the tools we were using were not calibrated properly. I proposed a recalibration schedule, which was implemented, resulting in a 30% reduction in defects. This experience reinforced my commitment to quality and proactive problem-solving.”
Skills tested
Question type
3.2. What safety protocols do you follow while working on the assembly line?
Introduction
Safety is paramount in assembly operations, and this question evaluates your knowledge of safety practices and your commitment to maintaining a safe work environment.
How to answer
- List specific safety protocols you adhere to, such as wearing PPE and following lockout/tagout procedures
- Explain how you ensure your personal safety and the safety of your colleagues
- Share any experiences where you had to address safety concerns
- Discuss the importance of reporting near misses and safety violations
- Mention any relevant safety training or certifications you have
What not to say
- Ignoring safety protocols or suggesting they are optional
- Failing to recognize the importance of a safety culture
- Providing generic answers without specific examples
- Not mentioning any past safety training or experiences
Example answer
“I strictly follow all safety protocols at my workplace, including wearing appropriate PPE like gloves and safety glasses. I also ensure that all equipment is properly maintained and report any safety hazards immediately. In my previous job at Boeing Australia, I participated in safety training workshops, which emphasized the importance of a proactive approach to safety, leading to a 15% reduction in workplace incidents over the year.”
Skills tested
Question type
4. Lead Assembler Interview Questions and Answers
4.1. Can you describe a time when you identified a process improvement in assembly that enhanced efficiency?
Introduction
This question is important as it evaluates your critical thinking and problem-solving skills in a hands-on assembly environment. Process improvements can lead to significant cost savings and productivity gains.
How to answer
- Provide a specific example of the assembly process you improved.
- Explain how you identified the inefficiency through observation or data analysis.
- Detail the steps you took to implement the improvement.
- Quantify the impact of the improvement on efficiency or output.
- Discuss any team collaboration or training that was involved.
What not to say
- Giving vague examples without measurable outcomes.
- Failing to mention how you involved others in the process.
- Overlooking the challenges you faced during implementation.
- Not discussing the importance of continuous improvement.
Example answer
“At my previous job at Toyota South Africa, I noticed that our assembly line was frequently delayed due to the time taken to fetch tools. I proposed a tool organization system that placed essential tools within arm's reach. After implementation, we reduced assembly time by 20%, which improved our overall productivity and minimized downtime. This experience reinforced my belief in the importance of optimizing processes for efficiency.”
Skills tested
Question type
4.2. How do you ensure quality control in your assembly work?
Introduction
This question assesses your knowledge of quality standards and your commitment to maintaining high-quality output, which is critical in assembly roles.
How to answer
- Discuss the quality control processes you follow during assembly.
- Provide examples of quality checks or metrics you use.
- Explain how you handle defects or issues when they arise.
- Mention any training or protocols you implement for your team.
- Share how you stay updated with industry quality standards.
What not to say
- Claiming to have no formal quality control processes.
- Only mentioning end-of-line checks without discussing in-process checks.
- Neglecting to discuss the importance of teamwork in maintaining quality.
- Avoiding responsibility for addressing quality issues.
Example answer
“In my role at Volkswagen South Africa, I implemented a multi-check system where I conducted quality inspections at every stage of the assembly process. This included visual inspections and functional tests. When defects were identified, I immediately addressed the issue and ensured team members were educated on preventing future occurrences. This proactive approach led to a 15% reduction in defects over six months and enhanced our overall quality rating.”
Skills tested
Question type
5. Assembly Supervisor Interview Questions and Answers
5.1. Can you describe a time when you had to improve assembly line efficiency?
Introduction
This question assesses your ability to identify inefficiencies and implement improvements, which is critical for an Assembly Supervisor role.
How to answer
- Use the STAR method to structure your response, focusing on the Situation, Task, Action, and Result.
- Clearly define the inefficiencies you observed on the assembly line.
- Explain the steps you took to analyze the problems, including data collection or team feedback.
- Detail the specific changes you implemented and how you communicated them to your team.
- Quantify the improvements in efficiency, such as reduced cycle time or increased output.
What not to say
- Mentioning improvements that were not measured or quantified.
- Avoiding responsibility by blaming others for the inefficiencies.
- Describing actions without explaining how they were communicated to the team.
- Focusing only on the problem without discussing the solution.
Example answer
“At Fiat, I noticed our assembly line was experiencing bottlenecks during the quality check phase. I gathered data on cycle times and held discussions with my team to identify pain points. We implemented a new checklist system that allowed for quicker inspections, reducing our quality check time by 20%. This change increased our overall output by 15% within three months. It taught me the importance of team involvement in process improvements.”
Skills tested
Question type
5.2. How do you handle conflicts or disagreements among assembly line workers?
Introduction
This question evaluates your conflict resolution and team management skills, which are essential for maintaining a productive work environment.
How to answer
- Describe your approach to identifying and addressing conflicts early.
- Share specific techniques you use to facilitate communication between team members.
- Explain how you encourage a collaborative atmosphere that minimizes conflict.
- Detail an example of a conflict you successfully resolved, including the outcome.
- Highlight the importance of maintaining team morale and productivity.
What not to say
- Suggesting that conflicts are not a concern in your team.
- Avoiding direct involvement in conflicts.
- Focusing solely on discipline without addressing underlying issues.
- Neglecting to mention follow-up actions to ensure conflicts do not reoccur.
Example answer
“In my previous role at a manufacturing plant, two team members had a disagreement about task responsibilities, impacting productivity. I intervened by facilitating a one-on-one discussion with each of them to understand their perspectives. I then brought them together to clarify roles and set shared goals. By fostering open communication, we resolved the conflict and improved teamwork, resulting in a smoother workflow and a 10% increase in efficiency. This experience reinforced the value of proactive conflict management.”
Skills tested
Question type
Similar Interview Questions and Sample Answers
Simple pricing, powerful features
Upgrade to Himalayas Plus and turbocharge your job search.
Himalayas
Himalayas Plus
Himalayas Max
Find your dream job
Sign up now and join over 100,000 remote workers who receive personalized job alerts, curated job matches, and more for free!
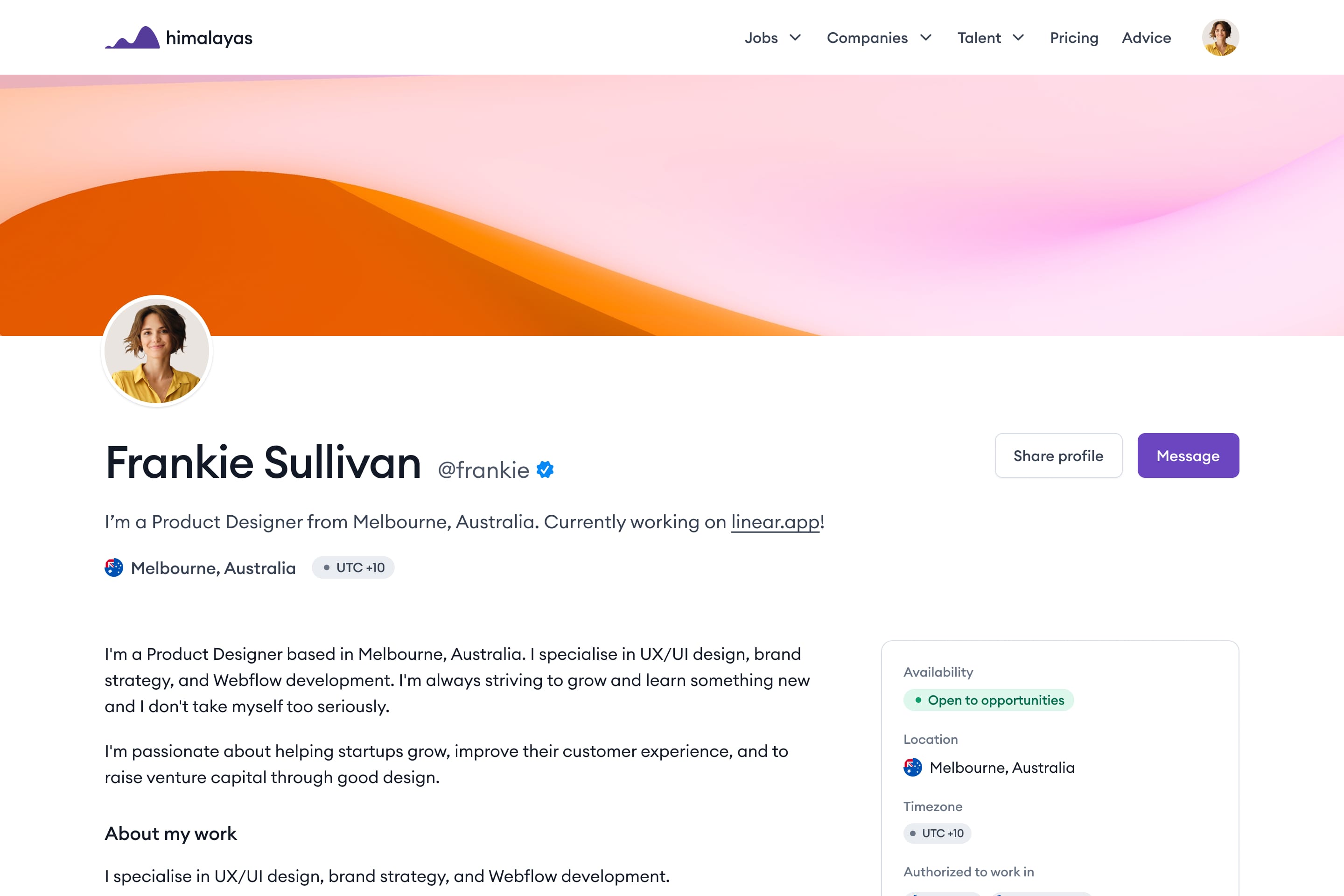