5 Factory Worker Interview Questions and Answers
Factory Workers are responsible for operating machinery, assembling products, and ensuring the production process runs smoothly. They play a critical role in maintaining efficiency and quality in manufacturing. Junior workers focus on specific tasks under supervision, while senior workers may take on additional responsibilities such as training new employees, overseeing production lines, or managing teams. Need to practice for an interview? Try our AI interview practice for free then unlock unlimited access for just $9/month.
Unlimited interview practice for $9 / month
Improve your confidence with an AI mock interviewer.
No credit card required
1. Factory Worker Interview Questions and Answers
1.1. Can you describe a situation where you identified a safety hazard in the workplace and how you addressed it?
Introduction
This question evaluates your awareness of workplace safety and your initiative in creating a safer work environment, which is crucial in factory settings.
How to answer
- Clearly describe the safety hazard you identified and its potential risks
- Explain the steps you took to address the hazard, including any communication with supervisors or colleagues
- Highlight any protocols you followed or suggestions you made to improve safety
- Discuss the outcomes of your actions and any feedback received
- Emphasize the importance of safety in the workplace and your commitment to it
What not to say
- Minimizing the importance of safety issues
- Failing to provide a specific example or being vague
- Claiming you didn't take any action despite knowing about a hazard
- Not showing an understanding of safety protocols
Example answer
“At my previous job at a manufacturing plant, I noticed that some equipment was not properly secured, which could have led to accidents. I immediately reported it to my supervisor and suggested a review of the equipment maintenance schedule. As a result, we implemented a more rigorous inspection protocol, and I received positive feedback for my proactive approach. Ensuring a safe working environment is a priority for me.”
Skills tested
Question type
1.2. How do you handle repetitive tasks while maintaining productivity and quality?
Introduction
This question assesses your ability to stay focused and efficient in a factory environment, where tasks can often be repetitive.
How to answer
- Share techniques you use to stay engaged during repetitive tasks, such as breaking tasks into smaller goals
- Discuss any methods you employ to ensure quality control amid routine work
- Explain how you manage your time effectively to meet production targets
- Provide an example of a time you improved your efficiency or quality on the job
- Highlight your commitment to maintaining high standards despite the nature of the work
What not to say
- Expressing boredom or disinterest in repetitive tasks
- Claiming you don't have any strategies to maintain productivity
- Failing to mention quality control measures
- Not providing any examples of past experiences
Example answer
“In my role at a packaging facility, I often performed repetitive tasks. To maintain my focus and productivity, I set small goals for myself, such as completing a certain number of items before taking a short break. I also regularly checked my work to ensure it met quality standards. This approach allowed me to stay productive while achieving a 98% quality assurance rate during my shifts.”
Skills tested
Question type
2. Senior Factory Worker Interview Questions and Answers
2.1. Can you describe a time when you identified a safety hazard in the workplace and how you addressed it?
Introduction
This question assesses your awareness of safety protocols and your proactive approach to maintaining a safe working environment, which is crucial in a factory setting.
How to answer
- Start by briefly describing the specific safety hazard you encountered.
- Explain the steps you took to investigate and confirm the hazard.
- Detail how you communicated the issue to your supervisor or team.
- Discuss any actions you implemented to mitigate the hazard.
- Conclude with the outcome and how it improved workplace safety.
What not to say
- Failing to mention specific actions taken to address the hazard.
- Blaming others for the hazard without taking responsibility.
- Describing a situation without any follow-up actions.
- Neglecting to highlight the importance of safety in the workplace.
Example answer
“At a previous job with Jaguar Land Rover, I noticed a loose guard on a machine that posed a risk. I immediately reported it to my supervisor and suggested a temporary halt in operations until it was fixed. I also assisted in securing the area to prevent access until repairs were made. This proactive approach not only addressed the immediate hazard but also led to a review of our safety checks, ultimately enhancing our workplace safety standards.”
Skills tested
Question type
2.2. How do you handle repetitive tasks while maintaining quality and efficiency?
Introduction
This question evaluates your ability to focus on quality and productivity, which are essential in a factory environment where tasks can become monotonous.
How to answer
- Discuss your strategies for maintaining focus during repetitive tasks.
- Explain how you monitor and ensure the quality of your work.
- Share any techniques you use to stay engaged and motivated.
- Provide an example of how you balanced quality and efficiency in your previous roles.
- Mention any feedback you received from supervisors or peers regarding your work.
What not to say
- Claiming that repetition leads to a drop in quality without any solutions.
- Suggesting that you do not find any methods to stay engaged.
- Failing to provide specific examples or metrics related to quality.
- Ignoring the importance of teamwork and collaboration in quality control.
Example answer
“In my role at BAE Systems, I handled assembly tasks that were highly repetitive. To maintain my focus, I set small goals for myself throughout the shift, such as completing a certain number of units within a timeframe. I also double-checked my work at regular intervals to ensure quality. By doing this, I was able to maintain a consistent output while achieving a 98% quality rating in my work. My supervisors appreciated my dedication to both efficiency and quality.”
Skills tested
Question type
3. Team Lead (Factory) Interview Questions and Answers
3.1. Can you describe a situation where you had to manage a conflict within your team?
Introduction
This question is crucial for assessing your conflict resolution skills and ability to maintain team cohesion, which are essential for a Team Lead in a factory setting.
How to answer
- Use the STAR method (Situation, Task, Action, Result) to structure your response
- Clearly outline the context of the conflict and the individuals involved
- Detail the steps you took to address the conflict and facilitate communication
- Highlight the resolution and any positive outcomes for team dynamics
- Reflect on what you learned from the experience and how it improved your leadership
What not to say
- Avoid blaming team members without taking responsibility for your leadership role
- Do not provide vague situations without clear actions taken
- Refrain from discussing conflicts without a resolution
- Avoid showing a lack of empathy or understanding in conflict situations
Example answer
“In my previous role at Toyota, we faced a conflict between two team members regarding task responsibilities. I arranged a meeting to allow both parties to express their concerns. By facilitating open communication, we identified overlapping responsibilities and clarified each person's role. This not only resolved the conflict but also strengthened team collaboration. I learned that proactive communication is key to preventing conflicts in the future.”
Skills tested
Question type
3.2. How do you ensure safety compliance among your team members in the factory?
Introduction
Safety is paramount in a factory environment, and this question assesses your commitment to safety standards and your ability to enforce compliance effectively.
How to answer
- Describe your approach to training and educating team members on safety protocols
- Discuss regular safety audits and how you address any issues that arise
- Explain how you foster a culture of safety and encourage team members to speak up about safety concerns
- Provide examples of specific safety initiatives you have implemented
- Mention how you keep yourself updated with safety regulations and best practices
What not to say
- Avoid suggesting that safety training is a one-time event
- Do not ignore the role of accountability in safety compliance
- Refrain from downplaying the importance of safety in production
- Avoid discussing safety solely as a regulatory requirement without a culture of safety
Example answer
“At Honda, I implemented a comprehensive safety training program for new hires and conducted regular refreshers for the whole team. We also held monthly safety audits, where team members could report hazards without fear of reprisal. This initiative not only reduced workplace incidents by 30% but also fostered a culture where safety became everyone's responsibility. I stay informed about safety regulations through continuous education and networking with industry safety experts.”
Skills tested
Question type
4. Shift Supervisor Interview Questions and Answers
4.1. Can you describe a time when you had to handle a conflict between team members during a shift?
Introduction
This question assesses your conflict resolution skills, which are crucial for maintaining a productive work environment as a Shift Supervisor.
How to answer
- Use the STAR method to structure your response: Situation, Task, Action, Result.
- Clearly describe the conflict and the individuals involved.
- Explain your role in resolving the conflict and the steps you took.
- Highlight the outcome and any positive changes that resulted from your intervention.
- Discuss any lessons learned that you applied to future situations.
What not to say
- Avoid placing blame solely on one party without acknowledging all sides.
- Don't minimize the conflict or suggest it was unimportant.
- Refrain from stating that you would avoid conflict rather than manage it.
- Avoid vague responses that don't detail your actions or results.
Example answer
“During my time at Starbucks, two baristas had a disagreement over shift responsibilities that was affecting team morale. I called a quick meeting to address the issue, allowing each person to express their concerns. I facilitated a discussion to help them find common ground and agree on a plan moving forward. As a result, not only did their working relationship improve, but the entire team reported higher morale in our next survey.”
Skills tested
Question type
4.2. How do you ensure that all team members are meeting performance standards during your shift?
Introduction
This question evaluates your ability to monitor, manage, and motivate team performance, which is essential for a Shift Supervisor.
How to answer
- Describe your approach to setting clear performance expectations.
- Explain how you monitor performance throughout the shift.
- Discuss techniques you use to provide constructive feedback.
- Mention how you celebrate successes and encourage improvement.
- Provide an example of how you addressed performance issues in the past.
What not to say
- Saying you don't monitor performance closely or leave it to others.
- Avoiding direct accountability for team performance.
- Neglecting to mention feedback mechanisms or follow-up processes.
- Failing to recognize the importance of motivation and team morale.
Example answer
“At Target, I set clear performance standards at the beginning of each shift. I use a checklist to monitor tasks and provide immediate feedback when necessary. During a particularly busy holiday season, I recognized a team member struggling to keep up. I offered support and shared effective time management techniques, which not only helped them but also improved overall team efficiency. I believe in celebrating small wins as well, which helps to keep morale high.”
Skills tested
Question type
5. Production Manager Interview Questions and Answers
5.1. Can you describe a time when you improved a production process? What steps did you take and what was the outcome?
Introduction
This question assesses your ability to analyze and enhance production processes, which is vital for a Production Manager to ensure efficiency and reduce costs.
How to answer
- Begin with a specific production process you identified as needing improvement.
- Explain the analysis you conducted to pinpoint inefficiencies.
- Detail the steps you took to implement changes, including any collaborative efforts with your team.
- Quantify the results with metrics, such as reduced production time or cost savings.
- Reflect on what you learned from the experience and how it has influenced your approach to production management.
What not to say
- Providing vague details without clear metrics or outcomes.
- Focusing solely on the problem instead of the solution.
- Claiming improvements without evidence or data.
- Neglecting to mention teamwork or collaboration in the process.
Example answer
“At XYZ Manufacturing, I noticed our assembly line was facing delays due to unnecessary manual handling. I conducted a time-motion study, which revealed that we could automate certain tasks. I worked with the engineering team to implement a new conveyor system that reduced manual handling by 30%. As a result, we increased our production output by 20% in just three months, significantly lowering labor costs. This experience taught me the importance of data-driven decision-making.”
Skills tested
Question type
5.2. How do you ensure safety and compliance in a production environment?
Introduction
Safety and compliance are critical responsibilities for a Production Manager, and this question evaluates your approach to maintaining a safe workplace.
How to answer
- Discuss the specific safety standards and regulations relevant to the industry.
- Explain your process for conducting regular safety audits and training.
- Share examples of how you have addressed safety violations or risks in the past.
- Highlight your communication methods to ensure staff are aware of safety practices.
- Mention any certifications or training you have that enhance your safety management skills.
What not to say
- Suggesting safety is the sole responsibility of the safety officer.
- Failing to provide specific examples of your safety practices.
- Underestimating the importance of compliance training.
- Neglecting to mention the involvement of staff in safety initiatives.
Example answer
“In my role at ABC Manufacturing, I prioritized safety by implementing a comprehensive training program for all employees focused on compliance with Australian safety standards. I conducted monthly safety audits and encouraged open communication regarding safety concerns. When we identified an issue with machine guards, I led a team to redesign the guards and retrain staff, resulting in a 50% reduction in safety incidents over a year. Safety is a shared responsibility, and I believe in empowering my team to take ownership.”
Skills tested
Question type
Similar Interview Questions and Sample Answers
Simple pricing, powerful features
Upgrade to Himalayas Plus and turbocharge your job search.
Himalayas
Himalayas Plus
Himalayas Max
Find your dream job
Sign up now and join over 100,000 remote workers who receive personalized job alerts, curated job matches, and more for free!
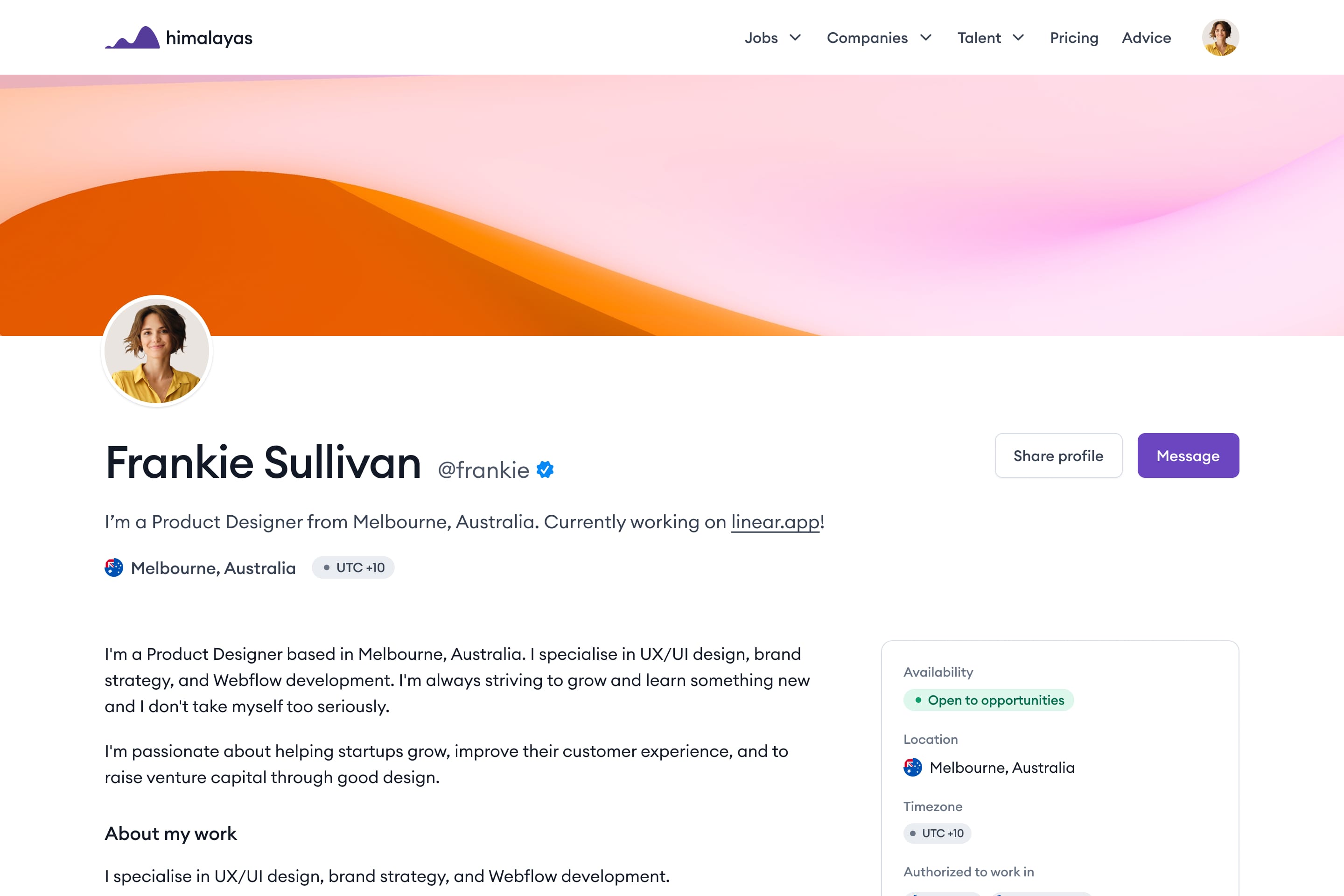