5 Manufacturing Operator Interview Questions and Answers
Manufacturing Operators are responsible for operating and maintaining machinery used in the production process. They ensure that production runs smoothly, efficiently, and safely, adhering to quality standards and safety protocols. Junior operators focus on learning equipment operation and performing basic tasks, while senior operators and leads take on more complex responsibilities, such as troubleshooting, training team members, and overseeing production lines. Need to practice for an interview? Try our AI interview practice for free then unlock unlimited access for just $9/month.
Unlimited interview practice for $9 / month
Improve your confidence with an AI mock interviewer.
No credit card required
1. Junior Manufacturing Operator Interview Questions and Answers
1.1. Can you describe a time when you identified a problem during the manufacturing process and how you addressed it?
Introduction
This question is critical for assessing your problem-solving skills and attention to detail, which are essential for a Junior Manufacturing Operator to ensure production efficiency and quality.
How to answer
- Use the STAR method (Situation, Task, Action, Result) to structure your response.
- Clearly describe the specific problem you identified in the manufacturing process.
- Explain your thought process in analyzing the problem and determining the best course of action.
- Detail the steps you took to address the issue, including collaboration with team members if applicable.
- Share the outcome of your actions and any measurable improvements in the process.
What not to say
- Avoid vague descriptions that lack specific details about the problem.
- Do not take sole credit if it was a team effort; acknowledge others' contributions.
- Refrain from blaming others for the problem without discussing your role in the solution.
- Avoid discussing problems that are not relevant to manufacturing processes.
Example answer
“During my internship at a local manufacturing plant in Barcelona, I noticed that a machine was frequently jamming, causing delays in production. I gathered data on the frequency of jams and worked with my supervisor to analyze the issue. Together, we adjusted the machine settings and conducted training sessions for the team on proper loading techniques. As a result, we reduced machine downtime by 30%, significantly improving our production efficiency.”
Skills tested
Question type
1.2. How do you ensure that you adhere to safety protocols while working in a manufacturing environment?
Introduction
Safety is a top priority in manufacturing. This question assesses your awareness of safety protocols and your ability to follow them diligently.
How to answer
- Discuss your understanding of safety protocols specific to the manufacturing environment.
- Explain how you have applied these protocols in previous roles or training.
- Share examples of how you actively promote safety among your colleagues.
- Describe any safety training or certifications you have completed.
- Convey your commitment to maintaining a safe work environment.
What not to say
- Do not minimize the importance of safety protocols.
- Avoid saying you have never had to deal with safety issues.
- Do not provide generic answers that lack personal experience.
- Refrain from discussing safety protocols you do not fully understand.
Example answer
“In my previous role at a packaging facility, I was trained on safety protocols such as proper machine operation and personal protective equipment (PPE) usage. I always double-check that my workstation is free of hazards before starting my shift. I also encourage my peers to follow safety procedures by leading by example. Safety is paramount, and I believe that fostering a culture of safety helps prevent accidents and ensures a smooth workflow.”
Skills tested
Question type
2. Manufacturing Operator Interview Questions and Answers
2.1. Can you describe a time when you identified a safety issue in the manufacturing process and what actions you took?
Introduction
This question is crucial for assessing your commitment to workplace safety and your proactive problem-solving abilities, which are vital in a manufacturing environment.
How to answer
- Use the STAR method (Situation, Task, Action, Result) to structure your response.
- Clearly outline the safety issue you identified and its potential impact on operations.
- Detail the steps you took to address the issue, including any collaboration with colleagues or management.
- Explain the outcome of your actions and any long-term improvements that were made.
- Emphasize the importance of safety and continuous improvement in manufacturing.
What not to say
- Downplaying the importance of safety protocols.
- Failing to provide a specific example or being vague.
- Not mentioning any follow-up actions taken after addressing the issue.
- Blaming others without taking personal responsibility.
Example answer
“While working at Fiat, I noticed that a machine in the assembly line was frequently overheating, posing a risk of fire. I immediately reported the issue to my supervisor and stopped the line to prevent any accidents. We collaborated with the maintenance team to implement regular checks and an upgrade to the cooling system. As a result, we not only improved safety but also enhanced production efficiency by reducing downtime from overheating by 30%.”
Skills tested
Question type
2.2. How do you ensure quality control in your daily tasks as a manufacturing operator?
Introduction
Quality control is essential in manufacturing to maintain standards and reduce waste. This question tests your understanding of quality assurance processes.
How to answer
- Describe the specific quality control measures you follow in your role.
- Explain how you monitor and report any deviations from quality standards.
- Share examples of how you have contributed to improving quality in previous positions.
- Discuss your familiarity with quality management systems or tools used in manufacturing.
- Highlight the importance of teamwork in maintaining quality across the production line.
What not to say
- Suggesting that quality control is not your responsibility.
- Failing to provide concrete examples of quality assurance practices.
- Ignoring the role of feedback and continuous improvement.
- Being dismissive about the importance of quality in manufacturing.
Example answer
“In my role at Maserati, I followed a strict protocol for quality checks at each stage of production. I routinely used calipers and gauges to measure components, ensuring they met specifications. I documented any discrepancies and worked closely with the quality assurance team to investigate issues and implement corrective actions. This proactive approach helped us maintain a 95% first-pass yield rate over the past year, significantly reducing rework costs.”
Skills tested
Question type
3. Senior Manufacturing Operator Interview Questions and Answers
3.1. Can you describe a time when you identified a process inefficiency in the manufacturing line and how you addressed it?
Introduction
This question is crucial as it assesses your analytical skills and ability to improve manufacturing processes, which are key responsibilities for a Senior Manufacturing Operator.
How to answer
- Use the STAR method (Situation, Task, Action, Result) to structure your response
- Begin by describing the specific inefficiency you encountered
- Explain your role in addressing the issue and the steps you took
- Provide data or metrics to quantify the improvement achieved
- Share any feedback received from team members or management about your solution
What not to say
- Blaming others for the inefficiency without offering a solution
- Providing vague examples without specific outcomes
- Focusing solely on the problem rather than the resolution
- Neglecting to mention teamwork or collaboration
Example answer
“At Coca-Cola Amatil, I noticed that our bottling line had a recurring delay due to manual inspections. I proposed implementing an automated quality check system. After conducting a trial, we reduced inspection time by 30%, leading to a 15% increase in overall line efficiency. The management praised the initiative, and it was rolled out across other lines.”
Skills tested
Question type
3.2. How do you ensure adherence to safety protocols in the manufacturing environment?
Introduction
This question evaluates your commitment to safety standards, which is vital in manufacturing roles to prevent accidents and ensure compliance.
How to answer
- Discuss your understanding of relevant safety regulations and protocols
- Describe specific methods you use to promote safety in the workplace
- Share examples of training or initiatives you have led or participated in
- Explain how you monitor compliance and address violations
- Emphasize the importance of a safety-first culture in manufacturing
What not to say
- Implying that safety is not a priority
- Failing to provide specific examples of safety measures you’ve implemented
- Neglecting to mention the role of teamwork in maintaining safety
- Overlooking personal accountability for safety practices
Example answer
“At BHP, I led a safety initiative that included weekly safety briefings and hands-on training sessions for new operators. I also implemented a buddy system for new hires to ensure they understood safety protocols. As a result, we achieved a 25% reduction in safety incidents over six months, fostering a culture of safety among our team.”
Skills tested
Question type
4. Lead Manufacturing Operator Interview Questions and Answers
4.1. Can you describe a time when you identified a safety risk in the manufacturing process and how you addressed it?
Introduction
This question is crucial for assessing your commitment to workplace safety, which is a top priority in manufacturing roles. It also evaluates your proactive problem-solving skills.
How to answer
- Use the STAR method (Situation, Task, Action, Result) to structure your response
- Clearly outline the safety risk you identified and its potential impact
- Detail the steps you took to mitigate the risk, including team involvement
- Highlight any changes or improvements made as a result of your actions
- Mention any positive feedback received from management or peers
What not to say
- Downplaying the importance of safety risks
- Failing to provide a specific example
- Not involving team members in the solution process
- Neglecting to mention outcomes or follow-up actions
Example answer
“While working at Siemens, I noticed that the lifting equipment in our assembly line was frequently overloaded. I conducted a risk assessment and proposed a new weight limit policy, which I presented to management. After implementation, we saw a 30% reduction in near-miss incidents over six months, and my team appreciated the increased safety focus.”
Skills tested
Question type
4.2. How do you ensure that production targets are met while maintaining high-quality standards?
Introduction
This question evaluates your ability to balance efficiency and quality in manufacturing, a critical competency for a Lead Manufacturing Operator.
How to answer
- Discuss your approach to setting realistic production targets
- Explain how you monitor production processes to ensure quality standards
- Detail any tools or metrics you use to track performance
- Share an example of how you addressed a quality issue without sacrificing productivity
- Highlight your communication strategies with team members
What not to say
- Suggesting that quality can be compromised for speed
- Providing vague answers without specific metrics
- Not mentioning any teamwork or collaboration
- Ignoring the importance of continuous improvement
Example answer
“At Rolls-Royce, I implemented a new quality control checklist that integrated seamlessly into our production workflow. By conducting regular training sessions, we maintained a 98% quality compliance rate while meeting our production targets consistently. This dual focus on quality and efficiency helped foster a culture of pride among the team.”
Skills tested
Question type
5. Manufacturing Supervisor Interview Questions and Answers
5.1. Can you describe a time when you successfully improved a manufacturing process?
Introduction
This question helps assess your problem-solving skills and ability to drive continuous improvement, which are crucial for a Manufacturing Supervisor role.
How to answer
- Use the STAR method (Situation, Task, Action, Result) to structure your response
- Clearly outline the process you aimed to improve, including its initial inefficiencies
- Describe the specific changes you implemented and the rationale behind them
- Quantify the results, such as improved efficiency, reduced waste, or cost savings
- Highlight any challenges faced during the implementation and how you overcame them
What not to say
- Focusing on minor adjustments rather than significant process improvements
- Neglecting to mention team involvement in the improvement efforts
- Providing vague results without specific metrics or outcomes
- Avoiding discussion of any challenges or setbacks faced
Example answer
“At Tata Steel, I led a project to improve the assembly line process for our new product line. We identified bottlenecks that caused delays, so I implemented a just-in-time inventory system. This change reduced our processing time by 20% and cut material waste by 15%. The key challenge was training the team on the new system, but through workshops and hands-on support, we achieved a smooth transition.”
Skills tested
Question type
5.2. How do you handle conflicts within your team during production?
Introduction
This question evaluates your leadership and conflict resolution skills, which are essential for maintaining a productive work environment in manufacturing.
How to answer
- Describe your approach to identifying the root cause of conflicts
- Explain how you facilitate open communication among team members
- Share a specific example of a conflict you resolved and the outcome
- Highlight your ability to remain impartial and focus on solutions
- Discuss how you ensure that conflicts do not hinder team performance
What not to say
- Avoiding confrontation or letting conflicts escalate
- Taking sides without understanding all perspectives
- Ignoring the emotional aspects of conflicts
- Failing to implement follow-up measures to prevent future issues
Example answer
“In my previous role at Mahindra & Mahindra, I encountered a conflict between two team members over responsibility for a production error. I arranged a meeting where both could share their viewpoints. After facilitating the discussion, we identified that the issue stemmed from unclear roles. By clarifying responsibilities and enhancing communication, we not only resolved the conflict but also improved overall team dynamics and performance.”
Skills tested
Question type
Similar Interview Questions and Sample Answers
Simple pricing, powerful features
Upgrade to Himalayas Plus and turbocharge your job search.
Himalayas
Himalayas Plus
Himalayas Max
Find your dream job
Sign up now and join over 100,000 remote workers who receive personalized job alerts, curated job matches, and more for free!
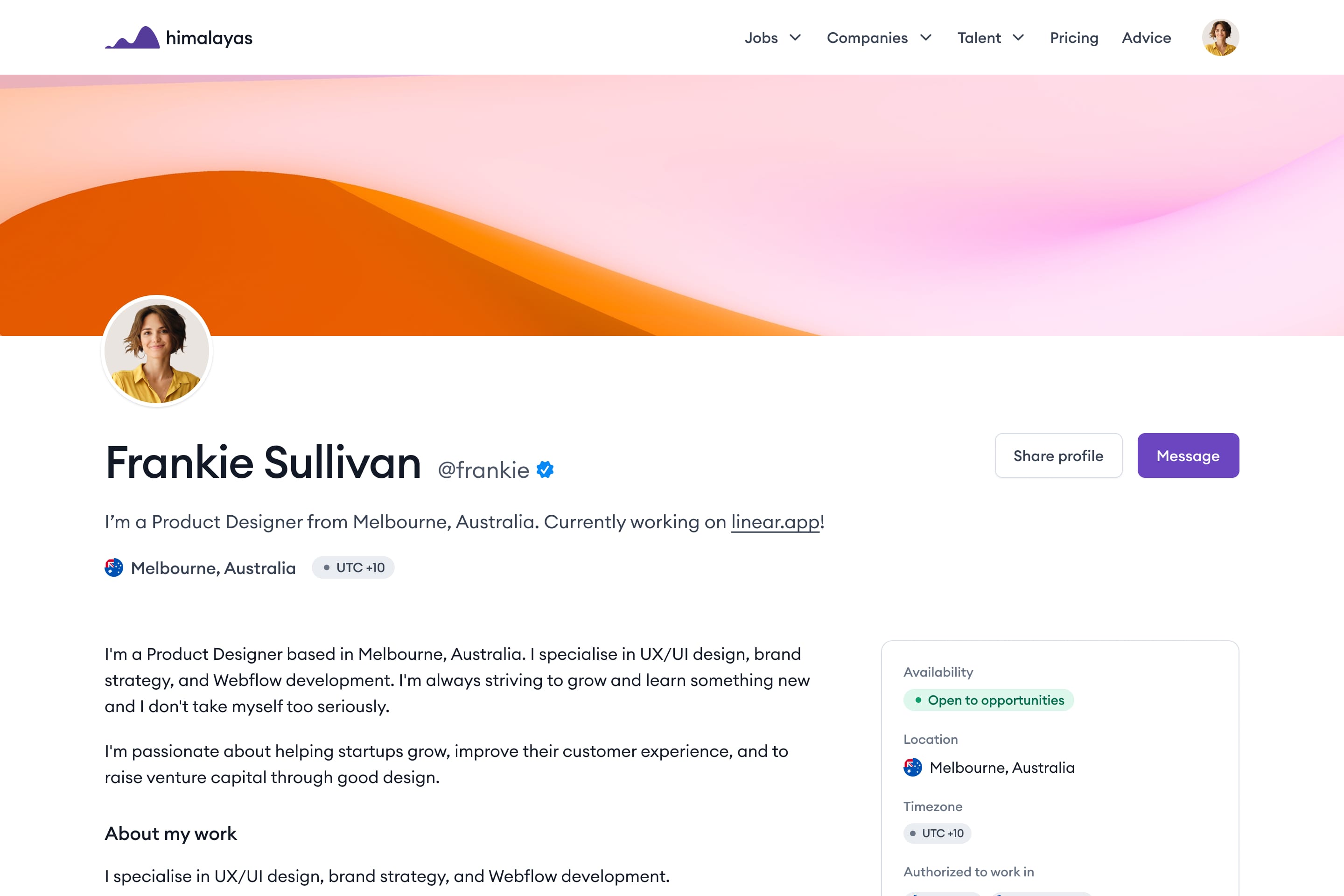