Complete Factory Worker Career Guide
Factory workers are the backbone of modern production, transforming raw materials into finished goods that power our economy and daily lives. They operate and maintain the machinery that manufactures everything from automobiles to electronics, ensuring quality and efficiency in high-volume environments.
This role offers tangible results and a clear path for skill development, making it an accessible entry point into the manufacturing sector with opportunities for advancement into specialized or supervisory positions.
Key Facts & Statistics
Median Salary
$39,830 USD
(U.S. national median, BLS May 2023)
Range: $29k - $55k+ USD
Growth Outlook
1%
slower than average
Annual Openings
≈340k
openings annually
Top Industries
Typical Education
High school diploma or equivalent; on-the-job training is common, with some roles benefiting from vocational training or certifications in specific machinery operation or safety protocols.
What is a Factory Worker?
A factory worker is an essential part of the manufacturing process, responsible for the hands-on production, assembly, and inspection of goods within a factory or plant. These professionals operate and maintain machinery, assemble products, and ensure that items meet quality standards before they are distributed. Their work directly contributes to the output and efficiency of industrial production.
Unlike skilled tradespeople who might design or repair complex systems, a factory worker focuses on the execution of production tasks, often repetitive, to create a consistent flow of finished products. They are distinct from warehouse workers who primarily focus on storage, picking, and shipping, as factory workers are directly involved in the creation or modification of the product itself. Their role is critical in transforming raw materials into consumer-ready goods.
What does a Factory Worker do?
Key Responsibilities
- Operate and monitor machinery to produce goods according to specifications, ensuring proper settings and continuous function.
- Assemble products or components by hand or using power tools, following detailed instructions and blueprints.
- Inspect finished products for defects, ensuring they meet quality standards and discarding or reprocessing substandard items.
- Load and unload materials from production lines, ensuring a steady supply of raw materials and efficient removal of finished goods.
- Package completed products for shipment, labeling them accurately and preparing them for transport.
- Perform routine maintenance and cleaning of equipment and work areas to maintain a safe and efficient production environment.
- Adhere strictly to all safety protocols and regulations, including wearing personal protective equipment and reporting hazards immediately.
Work Environment
Factory workers typically operate within a manufacturing plant or warehouse setting, which can be noisy, dusty, and may involve exposure to various temperatures depending on the products being made. Work is often physically demanding, requiring standing for long periods, repetitive motions, and lifting heavy objects.
Collaboration occurs within small teams or alongside other machine operators on a production line. Schedules often involve fixed shifts, including day, night, or rotating patterns, with overtime frequently available. The pace of work is usually fast and consistent, driven by production targets. While most work occurs on-site, some specialized roles might involve occasional travel for training or equipment setup.
Tools & Technologies
Factory workers utilize a range of tools and technologies depending on the industry and specific tasks. They commonly operate various types of machinery, such as conveyor belts, automated assembly machines, presses, and packaging equipment. Hand tools like wrenches, screwdrivers, and hammers are essential for assembly and minor adjustments.
Personal protective equipment (PPE), including safety glasses, gloves, hard hats, and ear protection, is mandatory. They also interact with basic computer systems or control panels for machine operation and monitoring. Some roles may involve forklifts or pallet jacks for material handling, requiring specific certifications. Inventory management systems or handheld scanners might be used for tracking materials and finished goods.
Factory Worker Skills & Qualifications
Qualifications for a Factory Worker focus heavily on practical skills, reliability, and adherence to safety protocols. Formal education often takes a backseat to demonstrated mechanical aptitude, a strong work ethic, and the ability to follow instructions precisely. Entry-level positions typically require a high school diploma or equivalent, with many employers offering on-the-job training for specific machinery and processes.
Requirements vary significantly based on the industry sector and the type of manufacturing. For instance, a factory worker in an automotive plant might need specialized knowledge of robotics or assembly lines, while someone in food processing requires strict adherence to hygiene and sanitation standards. Company size also plays a role; larger factories might have more specialized roles and advanced equipment, whereas smaller operations might expect workers to handle a wider range of tasks.
Certifications like OSHA safety training or forklift operation licenses add significant value, often making candidates more competitive. Practical experience, even in unrelated manual labor roles, is highly valued as it demonstrates reliability and a foundational understanding of physical work environments. The skill landscape is evolving with increasing automation; workers who can monitor automated systems or perform basic maintenance on them are becoming more desirable. Focusing on foundational safety, quality control, and efficiency skills is crucial for anyone entering or advancing in this field.
Education Requirements
Technical Skills
- Operating basic production machinery (e.g., presses, drills, conveyors)
- Performing quality checks and inspections using gauges or visual assessment
- Basic hand and power tool operation (e.g., wrenches, screwdrivers, drills)
- Material handling and loading/unloading procedures
- Reading and interpreting work orders and production schedules
- Maintaining a clean and organized work area (5S methodology)
- Troubleshooting minor equipment malfunctions (e.g., clearing jams, restarting machines)
- Forklift operation (certification often required)
- Inventory management basics (counting, labeling, tracking parts)
- Understanding of Lean Manufacturing principles (e.g., waste reduction, continuous improvement)
Soft Skills
- Attention to Detail: Essential for quality control and ensuring products meet specifications.
- Adherence to Safety Protocols: Crucial for preventing accidents and maintaining a safe work environment.
- Reliability and Punctuality: Factory operations depend on consistent attendance and timely task completion.
- Teamwork and Collaboration: Many tasks require coordinated effort with colleagues on assembly lines or production teams.
- Problem-Solving: Ability to identify minor issues with machinery or product quality and report them effectively.
- Adaptability: Readiness to switch tasks, learn new processes, or operate different machinery as production needs change.
- Stamina and Physical Endurance: Ability to perform repetitive tasks, stand for long periods, and lift materials.
- Following Instructions: Capacity to understand and precisely execute verbal and written operational guidelines and procedures from supervisors and engineers to ensure product quality and safety standards are met consistently, which is fundamental to efficient factory output and minimizing errors or defects.
How to Become a Factory Worker
Entering the factory worker field offers various pathways, depending on the industry and specific role. Many positions, especially in manufacturing or assembly, do not require a college degree, making them accessible entry points for individuals with a strong work ethic. Some roles might prefer a high school diploma or GED, while others prioritize physical stamina and the ability to follow safety protocols.
The timeline for securing a factory worker position can be relatively quick, often within a few weeks to a few months, especially for entry-level roles. This contrasts with fields requiring extensive education or specialized certifications. Opportunities are often abundant in industrial zones and areas with a strong manufacturing base, with different company sizes, from small local plants to large multinational corporations, offering varied work environments.
A common misconception is that factory work is unskilled labor; however, many modern factories integrate advanced machinery and require workers to have strong problem-solving skills and technical aptitude. Networking, even in this field, can open doors, as current employees often refer reliable candidates. Focus on demonstrating reliability, a willingness to learn, and adherence to safety guidelines, as these attributes are highly valued by employers.
Step 1
Step 2
Step 3
Step 4
Step 5
Step 6
Education & Training Needed to Become a Factory Worker
Becoming a factory worker primarily involves practical training and certifications rather than traditional university degrees. High school diplomas or GEDs are often prerequisites, but specialized vocational training and safety certifications hold more weight for employers. Four-year degrees typically cost $40,000-$100,000+, while vocational programs range from $2,000-$15,000. These programs usually take 3 months to 2 years to complete, contrasting sharply with the 4-year commitment for a bachelor's degree.
Employers value hands-on skills, safety compliance, and the ability to operate specific machinery. Vocational schools, community colleges, and industry-specific training centers offer focused programs that directly teach these skills. While self-study can provide foundational knowledge, practical experience gained through apprenticeships or on-the-job training is crucial for securing and advancing in factory roles. The market perception favors candidates with demonstrable skills and a strong safety record.
Continuous learning in this field focuses on new equipment operation, advanced manufacturing techniques, and updated safety protocols. Certifications in areas like Lean Manufacturing or Six Sigma can enhance career prospects and lead to supervisory roles. Cost-benefit considerations favor shorter, targeted training programs that offer immediate employability over lengthy academic paths. Programs with industry accreditation or strong local employer partnerships often provide the best return on investment for aspiring factory workers.
Factory Worker Salary & Outlook
Compensation for a Factory Worker varies significantly, influenced by numerous factors beyond just base pay. Geographic location plays a crucial role; areas with higher costs of living or strong manufacturing sectors often offer higher wages. For example, salaries in metropolitan industrial hubs typically exceed those in rural areas, even within the same state.
Experience, specialization, and the specific industry dramatically impact earning potential. A Factory Worker with specialized skills like operating complex machinery or certifications in quality control can command a premium. Performance bonuses tied to production targets or safety records are common, along with overtime pay, which can significantly boost total earnings.
Total compensation packages extend beyond hourly wages to include health insurance, paid time off, and retirement contributions like 401(k) plans. Some companies offer tuition reimbursement for skills development or profit-sharing. Union membership often provides additional benefits and standardized wage scales.
Larger manufacturing companies generally offer more competitive salaries and comprehensive benefits compared to smaller operations. While remote work is not applicable for this role, the stability of the manufacturing sector within a region can influence salary growth. International variations exist, with these figures representing typical U.S. Dollar compensation.
Salary by Experience Level
Level | US Median | US Average |
---|---|---|
Factory Worker | $36k USD | $38k USD |
Senior Factory Worker | $43k USD | $45k USD |
Team Lead (Factory) | $52k USD | $55k USD |
Shift Supervisor | $65k USD | $68k USD |
Production Manager | $82k USD | $85k USD |
Market Commentary
The job market for Factory Workers remains robust, driven by steady demand in various manufacturing sectors. Industries such as automotive, food processing, and consumer goods continue to require a consistent workforce for production lines. The reshoring of manufacturing and investments in domestic production facilities are creating new opportunities.
Automation and AI are impacting the nature of factory work, but they are not eliminating the need for human workers. Instead, these technologies are shifting roles towards monitoring, maintenance, and operating advanced machinery. This transition creates a demand for Factory Workers with stronger technical and problem-solving skills.
The supply and demand dynamics for skilled Factory Workers can be tight in some regions, leading companies to offer competitive wages and training programs. Future growth is projected at about 2-3% over the next decade, aligning with overall manufacturing output trends. This growth is stable rather than explosive.
Geographic hotspots for Factory Worker roles include states with strong manufacturing bases, such as Michigan, Ohio, Texas, and the Carolinas. The profession is generally recession-resistant for essential goods production, though cyclical for durable goods. Continuous learning in areas like lean manufacturing, robotics operation, and safety protocols is essential for career advancement.
Factory Worker Career Path
Career progression for Factory Workers typically unfolds through a combination of demonstrated proficiency, consistent reliability, and a willingness to take on greater responsibility. Advancement often involves mastering a specific production line or machine, then moving into roles that oversee processes or teams.
Individuals can pursue an individual contributor (IC) track by becoming highly specialized experts in complex machinery or quality control, or they can transition to a management track by leading teams and shifts. Factors influencing advancement include performance metrics, adherence to safety protocols, and the ability to train new hires. Company size and industry also play a role; larger corporations may offer more structured paths, while smaller operations might provide quicker opportunities for cross-training and broader responsibilities.
Lateral movement might involve shifting between different production departments to gain a wider understanding of the manufacturing process. Continuous learning, often through internal training on new equipment or safety standards, is vital. Networking within the plant and demonstrating leadership potential through initiative and problem-solving are also crucial for upward mobility.
Factory Worker
0-2 yearsKey Focus Areas
Senior Factory Worker
2-5 yearsKey Focus Areas
Team Lead (Factory)
5-8 years total experience, 1-3 years in team leadershipKey Focus Areas
Shift Supervisor
8-12 years total experience, 3-5 years in supervisory rolesKey Focus Areas
Production Manager
12+ years total experience, 5+ years in managementKey Focus Areas
Factory Worker
0-2 yearsPerforms routine tasks on the production line, operating specific machines or assembling components according to established procedures. Responsible for individual output and maintaining product quality within their assigned workstation. Follows instructions from supervisors and team leads. Has minimal decision-making authority, focusing on execution.
Key Focus Areas
Mastering basic machinery operation, assembly techniques, and quality checks. Adhering strictly to all safety procedures and plant regulations. Developing reliability, punctuality, and the ability to work effectively in a team environment. Understanding production goals.
Senior Factory Worker
2-5 yearsOperates more complex machinery or handles specialized tasks requiring a higher skill level and attention to detail. Acts as a subject matter expert for particular processes or equipment. May assist with quality control inspections or material handling. Provides informal guidance to less experienced workers and proactively identifies production bottlenecks.
Key Focus Areas
Optimizing personal efficiency and output. Troubleshooting minor equipment issues and performing basic maintenance. Contributing to process improvement suggestions. Training new Factory Workers on specific tasks and safety protocols. Building knowledge of lean manufacturing principles.
Team Lead (Factory)
5-8 years total experience, 1-3 years in team leadershipDirects a small team of Factory Workers, assigning tasks, monitoring progress, and ensuring production targets are met for their specific line or area. Provides on-the-job training and guidance to team members. Responsible for maintaining workflow, addressing immediate operational issues, and reporting team performance to supervisors. Ensures adherence to safety and quality standards.
Key Focus Areas
Developing leadership skills, including delegation, motivation, and conflict resolution. Improving communication skills for instructing team members and reporting to supervisors. Understanding production schedules and resource allocation. Focusing on team safety and efficiency metrics.
Shift Supervisor
8-12 years total experience, 3-5 years in supervisory rolesManages the entire factory shift, overseeing multiple production lines and teams. Responsible for shift-level production planning, staff deployment, and managing unexpected operational disruptions. Ensures all safety protocols are followed and production quotas are achieved. Conducts performance reviews for Team Leads and addresses escalated issues. Reports directly to the Production Manager.
Key Focus Areas
Mastering shift-wide planning, resource management, and problem-solving under pressure. Enhancing leadership and motivational skills for larger groups. Developing proficiency in production scheduling software and reporting tools. Focusing on overall shift productivity, safety, and quality objectives.
Production Manager
12+ years total experience, 5+ years in managementOversees all aspects of factory operations, including production planning, inventory management, quality control, and maintenance. Develops and implements production strategies to meet company goals and customer demands. Manages the factory budget, optimizes resource allocation, and leads continuous improvement projects. Responsible for overall plant safety, efficiency, and profitability. Collaborates with other departments like logistics, sales, and HR.
Key Focus Areas
Developing strategic planning, budget management, and cross-departmental coordination skills. Enhancing analytical abilities to identify efficiency improvements and cost-saving opportunities. Building strong communication and negotiation skills for vendor and stakeholder interaction. Focusing on long-term operational excellence and continuous improvement initiatives.
Job Application Toolkit
Ace your application with our purpose-built resources:
Factory Worker Cover Letter Examples
Personalizable templates that showcase your impact.
View examplesFactory Worker Job Description Template
Ready-to-use JD for recruiters and hiring teams.
View examplesGlobal Factory Worker Opportunities
Factory workers find opportunities globally, particularly in manufacturing hubs across Asia, Europe, and North America. This profession involves operating machinery, assembling products, and quality control, translating consistently across international industrial settings. Global demand for factory workers remains steady, driven by production needs in automotive, electronics, and consumer goods. Cultural nuances affect workplace safety and labor practices, but the core tasks are universal. Many consider international work for better wages or living conditions. No specific international certifications are typically required, but vocational training is beneficial.
Global Salaries
Salaries for factory workers vary significantly by region and industry. In North America, entry-level positions might range from $30,000 to $45,000 USD annually in the US, and $40,000 to $55,000 CAD in Canada. Experienced workers can earn more, up to $60,000 USD or $70,000 CAD. These figures reflect a higher cost of living. In Western Europe, such as Germany, annual salaries range from €28,000 to €40,000 ($30,000-$43,000 USD equivalent), while in Eastern Europe, like Poland, it might be €10,000 to €18,000 ($10,800-$19,500 USD equivalent). Asian manufacturing centers like China or Vietnam offer lower nominal wages, often $5,000 to $15,000 USD annually, but these often provide a higher purchasing power locally due to much lower living costs. Latin American countries, such as Mexico, typically see salaries from $6,000 to $12,000 USD annually.
Salary structures also differ. European countries often include robust social benefits, like extensive vacation time, healthcare, and pension contributions, which might not be explicitly reflected in the base salary. North American packages often feature health insurance and 401k matching. Tax implications vary; some countries have higher income taxes but offer more public services. Experience and specific skill sets, such as operating specialized CNC machinery, can lead to higher compensation globally. There are no standardized international pay scales, but multinational corporations sometimes offer consistent benefits packages across their global factories, adjusting wages for local conditions.
Remote Work
International remote work opportunities for factory workers are extremely limited. The nature of factory work requires physical presence to operate machinery, assemble products, and manage inventory on a production line. Therefore, this role is not suitable for digital nomad lifestyles or traditional work-from-home setups. Some administrative or supervisory roles within a factory might offer hybrid options, but the core factory worker position remains on-site.
Companies do not typically hire factory workers internationally for remote roles due to the inherent need for on-site presence. Any compensation models like geographic arbitrage do not apply here. Practical considerations for a factory worker always involve commuting to a physical location, adhering to safety protocols, and using specialized equipment provided on-site. Internet requirements or home workspace setup are irrelevant for this role.
Visa & Immigration
Common visa categories for factory workers typically fall under skilled or semi-skilled worker programs. Countries like Germany, Canada, and Australia offer pathways for specific industrial trades. Requirements usually include a job offer from an employer, proof of relevant experience or vocational training, and sometimes language proficiency. For instance, Canada's Express Entry system or Provincial Nominee Programs occasionally include industrial occupations. German work visas often require a recognized vocational qualification and a valid employment contract.
The application process generally involves submitting an application, providing documentation, and attending an interview. Processing times vary from a few months to over a year. Education credential recognition is less stringent than for professional roles, but specific certifications for machinery operation might be necessary. Pathways to permanent residency can exist after several years of continuous employment, depending on the country's immigration policies. Language tests, like IELTS for English-speaking countries or Goethe-Zertifikat for Germany, are often required. Some countries may offer specific labor shortage programs that benefit certain industrial roles, potentially fast-tracking visa processing. Family reunification visas are often available for dependents once the primary worker secures their status.
2025 Market Reality for Factory Workers
Understanding the current market reality for factory workers is crucial for career planning today. The landscape for these roles has significantly evolved from 2023 to 2025, driven by post-pandemic supply chain adjustments and the accelerating integration of automation and AI.
Broader economic factors, such as inflation and consumer demand, directly impact factory output and, consequently, job security. Market realities also vary by experience level, with specialized skills commanding more stability, and by geographic region, as manufacturing centers shift. This analysis provides an honest assessment to help factory workers navigate these changes effectively.
Current Challenges
Factory workers face increasing competition due to automation and a shrinking manufacturing base in some regions. Economic shifts impact production volumes, directly affecting job stability. Skill gaps arise as companies adopt new technologies, requiring workers to adapt quickly or face displacement.
Growth Opportunities
Despite challenges, significant opportunities exist for factory workers who adapt to evolving demands. Roles in advanced manufacturing, particularly those involving oversight of automated lines or quality assurance for AI-driven processes, show strong growth. Specializations in robotics maintenance, industrial IoT monitoring, or data collection from production lines are emerging areas.
Workers can gain an advantage by pursuing certifications in areas like mechatronics, industrial control systems, or lean manufacturing principles. These skills are highly valued and reduce the gap between traditional manual labor and modern factory requirements. Underserved markets often appear in new industrial parks focused on high-tech component production or in regions experiencing manufacturing reshoring initiatives.
Strategic career moves involve targeting companies investing in factory modernization or those producing goods with consistent demand, such as medical devices or specialized electronics. Investing in vocational training or apprenticeships focused on Industry 4.0 technologies can open doors to more stable and higher-paying positions, positioning workers for long-term success in an automated environment.
Current Market Trends
Hiring for factory workers shows a nuanced picture in 2025. While some sectors like specialized manufacturing or essential goods production maintain steady demand, others face pressure from automation and global supply chain shifts. Companies seek workers who can operate increasingly sophisticated machinery and adapt to digitalized workflows.
The integration of AI and advanced robotics is transforming factory floors. This leads to a demand for workers with hybrid skills, combining manual dexterity with technical understanding of automated systems. Traditional, purely manual roles are diminishing, replaced by positions requiring oversight of machines or quality control for automated processes.
Economic conditions directly influence production levels; slowdowns can lead to reduced shifts or temporary layoffs, impacting job availability. Salary trends for basic factory roles remain stable but show moderate growth for workers with specialized technical skills or certifications in automation. Market saturation is evident in areas with legacy manufacturing, while regions with high-tech production or reshoring initiatives offer better prospects.
Geographically, opportunities concentrate in industrial hubs with advanced manufacturing facilities. Remote work is not applicable here, as these roles require on-site presence. Seasonal hiring patterns exist in industries like food processing or automotive assembly, tied to production cycles.
Emerging Specializations
The landscape of factory work is undergoing a profound transformation, driven by advancements in automation, artificial intelligence, and digital manufacturing. These technological shifts are not eliminating roles but rather reshaping them, creating new specialization opportunities that demand advanced skills. Early positioning in these emerging areas is crucial for factory workers aiming to secure long-term career growth and command premium compensation in 2025 and beyond.
Understanding these future-oriented paths allows professionals to strategically invest in their skill development, moving beyond traditional manual tasks to more analytical, supervisory, and technical roles. While established specializations remain vital, the highest growth potential and salary increases often reside in these cutting-edge fields. These emerging areas typically take 3-5 years to become mainstream and create a significant volume of job opportunities, making proactive skill acquisition essential now.
Specializing in cutting-edge areas involves a balance of risk and reward. It requires adaptability and a willingness to learn new technologies. However, the reward includes enhanced job security, increased earning potential, and the opportunity to be at the forefront of industrial innovation. Factory workers who embrace these changes will find themselves indispensable assets in the factories of the future.
Robotics & Automation Technician
Production Data Monitor
Additive Manufacturing Operator
AR/VR Factory Support Specialist
Factory Cybersecurity Guardian
Pros & Cons of Being a Factory Worker
Making a career choice requires understanding both the benefits and challenges of a profession. This is particularly true for a factory worker role, where daily experiences can vary significantly based on the specific industry, company culture, and production line. What one person considers an advantage, like routine tasks, another might find monotonous. Factors such as a company's commitment to safety, the level of automation, and the type of product being manufactured all influence the day-to-day reality. Furthermore, the physical and mental demands can shift at different career stages or with different specializations within a factory. This assessment provides a realistic look at the common advantages and challenges to help individuals set appropriate expectations.
Pros
- Entry-level accessibility is high, as many factory positions do not require advanced degrees or specialized certifications, making it a viable option for individuals seeking immediate employment.
- Consistent work schedules are often in place once a shift is assigned, providing a predictable routine that can help with personal planning and childcare arrangements.
- Opportunities for overtime pay are frequently available, allowing workers to significantly increase their earnings, especially during peak production periods or to meet demanding deadlines.
- On-the-job training is common, enabling workers to learn new skills and processes directly from experienced colleagues or supervisors without needing prior formal education in manufacturing.
- Team-based work environments foster camaraderie and collaboration among colleagues, as many tasks require coordinated effort, building a strong sense of teamwork.
- Tangible results are visible daily, as workers directly contribute to the production of physical goods, providing a clear sense of accomplishment and impact from their labor.
Cons
- Repetitive tasks are common, leading to monotony and mental fatigue over long shifts. This can make the workday feel longer and less engaging.
- Physical demands are high, often involving heavy lifting, standing for extended periods, and repetitive motions, which can lead to musculoskeletal issues or injuries over time.
- Work environments in factories can be noisy, dusty, or involve exposure to chemicals, requiring strict adherence to safety protocols and potentially impacting long-term health if not properly managed.
- Shift work is frequently required, including nights, weekends, and holidays, which can disrupt personal life, sleep patterns, and social engagements.
- Career advancement opportunities are often limited, with many roles offering little upward mobility beyond supervisory positions without additional education or specialized training.
- Job security can be unstable due to automation, outsourcing, or economic downturns, as factory production is often sensitive to market fluctuations and technological advancements.
Frequently Asked Questions
Factory workers face distinct challenges around physical demands, safety, and adapting to production cycles. This section addresses common questions about entering this role, from understanding the daily routine and safety protocols to navigating shift work and career progression within manufacturing environments.
What are the typical educational or experience requirements to become a factory worker?
Most factory worker positions do not require a specific degree; a high school diploma or GED is often sufficient. Employers prioritize reliability, a strong work ethic, and the ability to follow instructions. Some specialized roles might benefit from vocational training or certifications in areas like machine operation or welding, but many entry-level positions offer on-the-job training.
How long does it take to become job-ready as a factory worker, especially if I have no prior experience?
The time it takes to become job-ready depends on the specific role and factory. For general assembly or production line work, you can often start within weeks after hiring, as most training occurs on-site. For roles requiring specialized machinery operation or technical skills, a few months of vocational training or a longer apprenticeship might be necessary before you are fully proficient.
What are the typical salary expectations for factory workers, and how does it vary by experience or industry?
Salaries for factory workers vary widely by industry, location, and skill level. Entry-level positions typically start around minimum wage or slightly above, while experienced operators or those in specialized roles can earn significantly more. Overtime pay can also substantially increase earnings, as factory work often involves extended hours or shift differentials.
What is the typical work-life balance like for a factory worker, considering shift schedules and demands?
Work-life balance can be challenging due to common shift work, including nights, weekends, and holidays. Many factories operate 24/7, requiring workers to rotate shifts or commit to fixed non-traditional hours. This can impact personal life and social schedules. However, some facilities offer more predictable daytime schedules, and understanding the specific shift requirements before accepting a role is crucial.
Is the factory worker role stable, or is it at high risk due to automation and economic changes?
Job security for factory workers depends on the industry, company stability, and automation trends. While some manufacturing sectors face challenges from offshoring or automation, others are stable and even growing, especially those producing essential goods or requiring specialized human oversight. Developing adaptable skills and a willingness to learn new technologies can enhance long-term job security.
What are the common career advancement opportunities or growth paths for factory workers?
Career growth paths for factory workers often include moving into supervisory roles, becoming a team leader, or specializing in machine operation, quality control, or maintenance. Many companies offer internal training programs or tuition reimbursement for certifications that can lead to higher-skilled, better-paying positions. Gaining diverse experience across different production lines can also open doors to new opportunities.
What are the main safety concerns for factory workers, and how are they addressed?
Safety is a primary concern in factory environments due to heavy machinery, repetitive motions, and potential exposure to chemicals or noise. Factories must adhere to strict safety regulations, and proper training, protective equipment, and adherence to protocols are crucial to prevent injuries. Companies with strong safety cultures prioritize worker well-being and invest in ongoing training and hazard mitigation.
Can factory workers work remotely, or is it strictly an on-site position?
Remote work is generally not an option for most factory worker roles because the job requires direct interaction with machinery, products, and the physical production line. Factory work is inherently hands-on and location-dependent. Therefore, you must be physically present at the manufacturing facility to perform your duties effectively.
Related Careers
Explore similar roles that might align with your interests and skills:
Assembly Line Worker
A growing field with similar skill requirements and career progression opportunities.
Explore career guideManufacturing Operator
A growing field with similar skill requirements and career progression opportunities.
Explore career guidePlant Worker
A growing field with similar skill requirements and career progression opportunities.
Explore career guideProduction Line Worker
A growing field with similar skill requirements and career progression opportunities.
Explore career guideProduction Worker
A growing field with similar skill requirements and career progression opportunities.
Explore career guideAssess your Factory Worker readiness
Understanding where you stand today is the first step toward your career goals. Our Career Coach helps identify skill gaps and create personalized plans.
Skills Gap Analysis
Get a detailed assessment of your current skills versus Factory Worker requirements. Our AI Career Coach identifies specific areas for improvement with personalized recommendations.
See your skills gapCareer Readiness Assessment
Evaluate your overall readiness for Factory Worker roles with our AI Career Coach. Receive personalized recommendations for education, projects, and experience to boost your competitiveness.
Assess your readinessSimple pricing, powerful features
Upgrade to Himalayas Plus and turbocharge your job search.
Himalayas
Himalayas Plus
Himalayas Max
Find your dream job
Sign up now and join over 100,000 remote workers who receive personalized job alerts, curated job matches, and more for free!
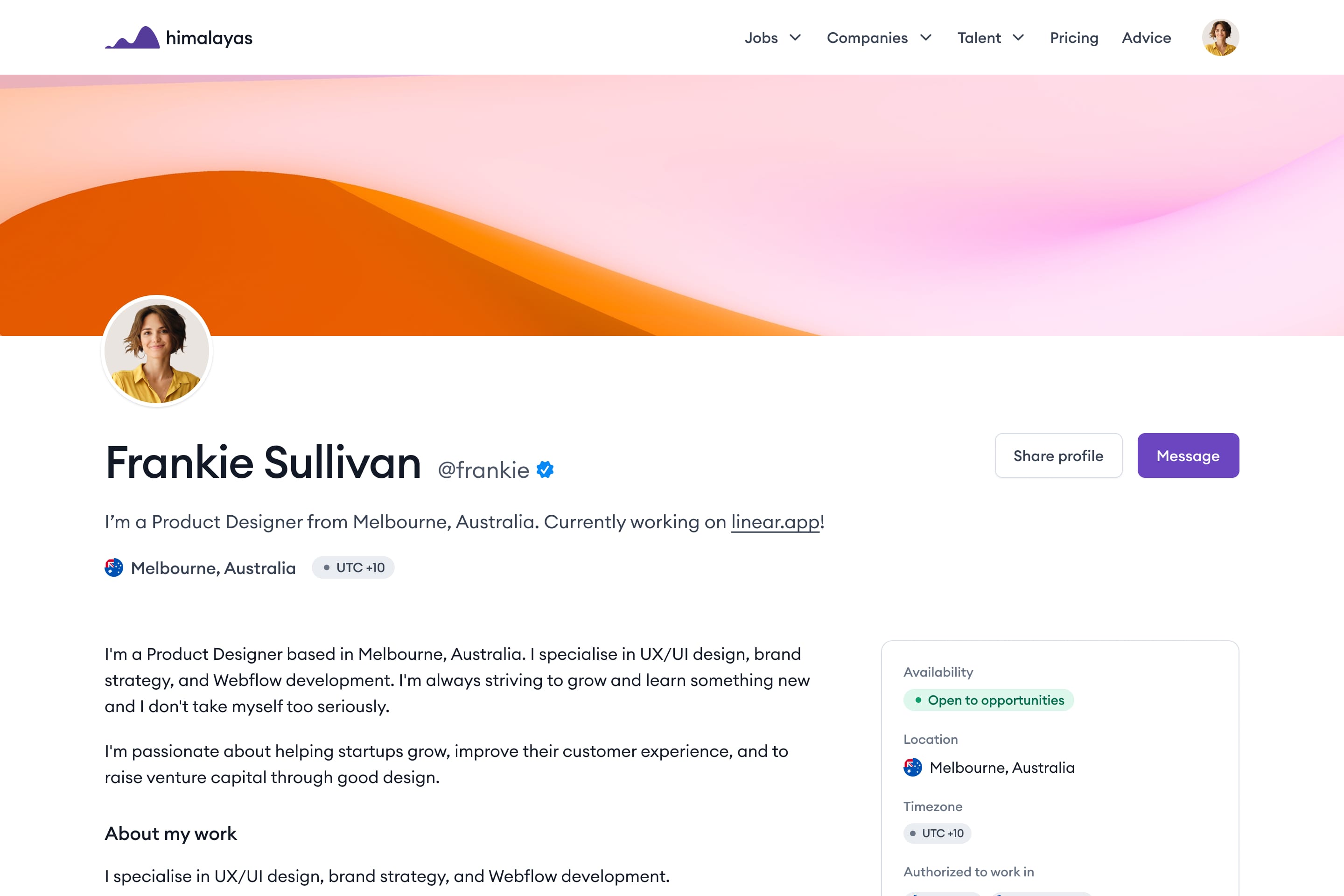