5 Production Line Worker Interview Questions and Answers
Production Line Workers are responsible for assembling, packaging, or inspecting products on a production line. They ensure that manufacturing processes run smoothly and efficiently, adhering to quality standards and safety protocols. Entry-level workers focus on basic tasks and learning the processes, while senior workers may take on more complex responsibilities or assist in training others. Supervisors and managers oversee the entire production line, ensuring productivity and resolving any operational issues. Need to practice for an interview? Try our AI interview practice for free then unlock unlimited access for just $9/month.
Unlimited interview practice for $9 / month
Improve your confidence with an AI mock interviewer.
No credit card required
1. Entry-Level Production Line Worker Interview Questions and Answers
1.1. Can you describe a time when you had to work as part of a team to complete a task on the production line?
Introduction
This question is important for assessing your teamwork and collaboration skills, which are essential in a production environment where tasks are often interdependent.
How to answer
- Use the STAR method (Situation, Task, Action, Result) to structure your response.
- Clearly describe the specific task and your role within the team.
- Highlight how you communicated and collaborated with your teammates.
- Discuss any challenges you faced and how you overcame them as a team.
- Quantify the outcome if possible, such as improvements in efficiency or quality.
What not to say
- Focusing solely on your individual contributions without acknowledging the team.
- Describing a situation where you did not work well with others.
- Failing to mention specific actions taken to support teammates.
- Being vague about the results or impact of the teamwork.
Example answer
“In my previous role at a local factory, our team was tasked with increasing output during a peak season. I collaborated closely with my colleagues, ensuring clear communication about our progress and any issues we encountered. By sharing our strengths, we managed to increase our production by 20% over three weeks, helping the company meet its sales targets. This experience taught me the value of teamwork and communication in achieving common goals.”
Skills tested
Question type
1.2. How do you ensure that you follow safety protocols while working on the production line?
Introduction
Safety is paramount in a production environment, and this question assesses your awareness and commitment to maintaining a safe workplace.
How to answer
- Discuss your understanding of the safety protocols relevant to the position.
- Mention any specific training or experience you have had regarding workplace safety.
- Explain how you apply these safety protocols in your daily work.
- Share an example of a time you identified a safety concern and how you addressed it.
- Emphasize the importance of safety both for yourself and your colleagues.
What not to say
- Indicating a lack of knowledge about safety protocols.
- Saying that safety is not a priority for you.
- Neglecting to provide specific examples of how you ensure safety.
- Offering vague answers that do not demonstrate a proactive safety attitude.
Example answer
“Safety is a top priority for me while working on the production line. I always follow the established protocols, such as wearing protective gear and being mindful of my surroundings. In my last job at a packaging facility, I noticed a co-worker not wearing their gloves while handling hazardous materials. I immediately spoke up and reminded them of the safety guidelines, which helped prevent potential injuries. I believe that maintaining a safe work environment is crucial for everyone’s well-being.”
Skills tested
Question type
2. Production Line Worker Interview Questions and Answers
2.1. Can you describe a time when you identified a safety hazard on the production line and how you addressed it?
Introduction
This question is crucial for evaluating your awareness of safety protocols and your proactive approach to maintaining a safe working environment, which is vital in manufacturing settings.
How to answer
- Begin with a brief description of the production line environment to set context.
- Clearly outline the safety hazard you identified and why it was a concern.
- Detail the steps you took to address the hazard, including reporting it and any immediate actions taken.
- Discuss the outcome of your actions, including any changes made to safety protocols.
- Emphasize the importance of safety in your work and how it impacts team morale and productivity.
What not to say
- Failing to mention the specific hazard or its implications.
- Downplaying safety concerns by suggesting they were not significant.
- Not discussing the steps taken to resolve the issue.
- Avoiding responsibility by stating it was someone else's job to manage safety.
Example answer
“While working at a manufacturing facility in Melbourne, I noticed that a conveyor belt was not properly guarded, creating a risk for operators. I immediately reported it to my supervisor and suggested we implement temporary barriers until a permanent fix could be made. This led to an audit of our safety measures and a new training session for staff on equipment safety, reinforcing our commitment to a safe workplace.”
Skills tested
Question type
2.2. How do you handle repetitive tasks on the production line to maintain your efficiency and focus?
Introduction
This question assesses your ability to manage monotony effectively, which is important in roles that involve repetitive tasks, ensuring both productivity and quality.
How to answer
- Share specific techniques you use to stay focused, such as time management strategies or breaks.
- Discuss any methods you implement to ensure quality control while working on repetitive tasks.
- Explain how you maintain motivation and energy levels during long shifts.
- Mention any tools or practices you use to track your productivity.
- Highlight the importance of teamwork and communication in maintaining a positive work environment.
What not to say
- Expressing boredom or dissatisfaction without offering solutions.
- Suggesting that you do not have any techniques to handle repetition.
- Neglecting to mention the importance of quality in repetitive tasks.
- Focusing solely on personal strategies without considering team dynamics.
Example answer
“To stay focused during repetitive tasks on the production line, I set small, achievable goals for each hour, which helps me manage my time effectively. I also take short breaks to stretch and reset my focus. I always double-check my work for quality, as I believe consistency is key. Additionally, I communicate with my teammates to ensure we are all on track and support each other in maintaining productivity.”
Skills tested
Question type
3. Senior Production Line Worker Interview Questions and Answers
3.1. Can you describe a time when you identified a safety hazard on the production line and how you addressed it?
Introduction
Safety is crucial in a production environment, and this question assesses your awareness of safety protocols and your ability to take initiative when it comes to workplace safety.
How to answer
- Use the STAR method to structure your response: Situation, Task, Action, Result.
- Clearly describe the safety hazard you identified.
- Explain the potential risks associated with the hazard.
- Detail the steps you took to address it, including notifying supervisors or implementing changes.
- Highlight any positive outcomes resulting from your actions, like improved safety records or team awareness.
What not to say
- Ignoring safety protocols or downplaying the importance of safety.
- Failing to mention specific actions taken to resolve the issue.
- Describing a situation without a clear resolution.
- Avoiding personal accountability or responsibility.
Example answer
“At my previous job at a manufacturing plant, I noticed that the floor near the assembly line was often slippery due to spilled materials. I reported this to my supervisor and proposed that we implement a more regular cleaning schedule. After making these changes, we saw a 30% reduction in near-miss incidents related to slips and falls over the next quarter.”
Skills tested
Question type
3.2. How do you ensure quality control in your work on the production line?
Introduction
This question evaluates your understanding of quality assurance processes and your commitment to maintaining high production standards.
How to answer
- Describe specific quality control measures you implement during production.
- Explain how you monitor your work and that of your team.
- Discuss your familiarity with quality standards relevant to your industry.
- Provide examples of how you’ve contributed to improving quality on the line.
- Mention any tools or technologies you utilize for quality control.
What not to say
- Suggesting that quality control is solely the responsibility of a different team.
- Failing to provide concrete examples of quality control practices.
- Overlooking the importance of continuous improvement.
- Indicating a disregard for quality standards.
Example answer
“In my role at a food processing facility, I always double-check my work against the quality checklist we have in place. I also trained my colleagues on the importance of these checks. When I noticed some inconsistencies in product weight, I initiated a review of our measuring tools, which led to adjustments and a 15% improvement in consistency across the production line.”
Skills tested
Question type
4. Production Line Supervisor Interview Questions and Answers
4.1. Can you describe a time when you had to deal with a significant production delay? What actions did you take to resolve it?
Introduction
This question assesses your problem-solving skills and ability to manage production challenges, which are critical for a Production Line Supervisor.
How to answer
- Use the STAR method to structure your response: Situation, Task, Action, Result.
- Clearly articulate the nature of the delay and its impact on production.
- Detail the steps you took to investigate and address the issue.
- Discuss any collaboration with team members or other departments.
- Share the outcome and any lessons learned that improved future processes.
What not to say
- Blaming others for the delay without taking responsibility.
- Providing vague details that don't demonstrate your role in the resolution.
- Failing to discuss measurable results or changes implemented.
- Overlooking the importance of teamwork and communication.
Example answer
“At Coca-Cola Australia, we faced a major delay due to equipment failure that halted production for several hours. I quickly gathered the team to assess the situation and communicated with maintenance to expedite repairs. We implemented a temporary workflow to redistribute tasks and minimize downtime. As a result, we recovered lost production within the week and conducted a review to improve our maintenance schedule, reducing future risks by 30%.”
Skills tested
Question type
4.2. How do you ensure that safety protocols are followed on the production line?
Introduction
This question evaluates your commitment to safety standards, which is a vital aspect of a Production Line Supervisor's role.
How to answer
- Discuss your approach to training staff on safety protocols.
- Explain how you monitor compliance and address violations.
- Share examples of safety improvements you have implemented.
- Detail how you foster a culture of safety within the team.
- Describe how you handle safety incidents and reporting.
What not to say
- Suggesting safety is someone else's responsibility.
- Failing to provide specific examples of safety measures taken.
- Ignoring the importance of training and continuous improvement.
- Overlooking the need for regular safety audits.
Example answer
“In my role at Nestlé Australia, I prioritized safety by conducting weekly training sessions and maintaining open communication about safety concerns. I implemented a buddy system for new employees, ensuring they had guidance. After identifying a compliance gap in PPE usage, I instituted mandatory checks and increased awareness through posters and reminders. This led to a 40% reduction in safety incidents over six months.”
Skills tested
Question type
5. Production Line Manager Interview Questions and Answers
5.1. Can you describe a time when you improved production efficiency on your line?
Introduction
This question is crucial as it evaluates your ability to identify inefficiencies and implement effective solutions, a key responsibility of a Production Line Manager.
How to answer
- Use the STAR method to structure your response: Situation, Task, Action, Result.
- Clearly outline the inefficiency you identified and its impact on production.
- Detail the specific actions you took to address the issue.
- Quantify the results of your actions, such as reduced downtime or increased output.
- Highlight any collaboration with team members or other departments.
What not to say
- Vaguely describing problems without concrete examples.
- Focusing solely on technical aspects without mentioning team involvement.
- Failing to provide measurable outcomes from your actions.
- Blaming others for inefficiencies instead of taking responsibility.
Example answer
“At Fiat, I noticed our assembly line was frequently halted due to equipment failures. I initiated a preventive maintenance program and trained the team on basic troubleshooting. As a result, we decreased downtime by 30% and increased overall production output by 15% over six months. This experience taught me the importance of proactive management and teamwork.”
Skills tested
Question type
5.2. How do you handle conflicts between team members on the production line?
Introduction
This question assesses your conflict resolution skills and ability to maintain a positive working environment, which is critical in a high-pressure production setting.
How to answer
- Describe your approach to actively listening to both sides of the conflict.
- Explain how you facilitate open communication among team members.
- Detail any strategies you employ to mediate and resolve conflicts.
- Share examples of successful conflict resolution and its impact on team dynamics.
- Emphasize the importance of maintaining morale and productivity.
What not to say
- Ignoring the importance of addressing conflicts promptly.
- Taking sides without understanding the full context of the issue.
- Describing a hands-off approach that allows conflicts to fester.
- Failing to mention the positive outcomes of resolved conflicts.
Example answer
“When two team members at a Nestlé production line had a disagreement over task responsibilities, I arranged a meeting to listen to both perspectives. I facilitated a discussion where they could express their concerns and collaboratively find a resolution. This not only resolved the conflict but also improved their working relationship, leading to a more cohesive team environment. I learned that open communication is key to conflict resolution.”
Skills tested
Question type
Similar Interview Questions and Sample Answers
Simple pricing, powerful features
Upgrade to Himalayas Plus and turbocharge your job search.
Himalayas
Himalayas Plus
Himalayas Max
Find your dream job
Sign up now and join over 100,000 remote workers who receive personalized job alerts, curated job matches, and more for free!
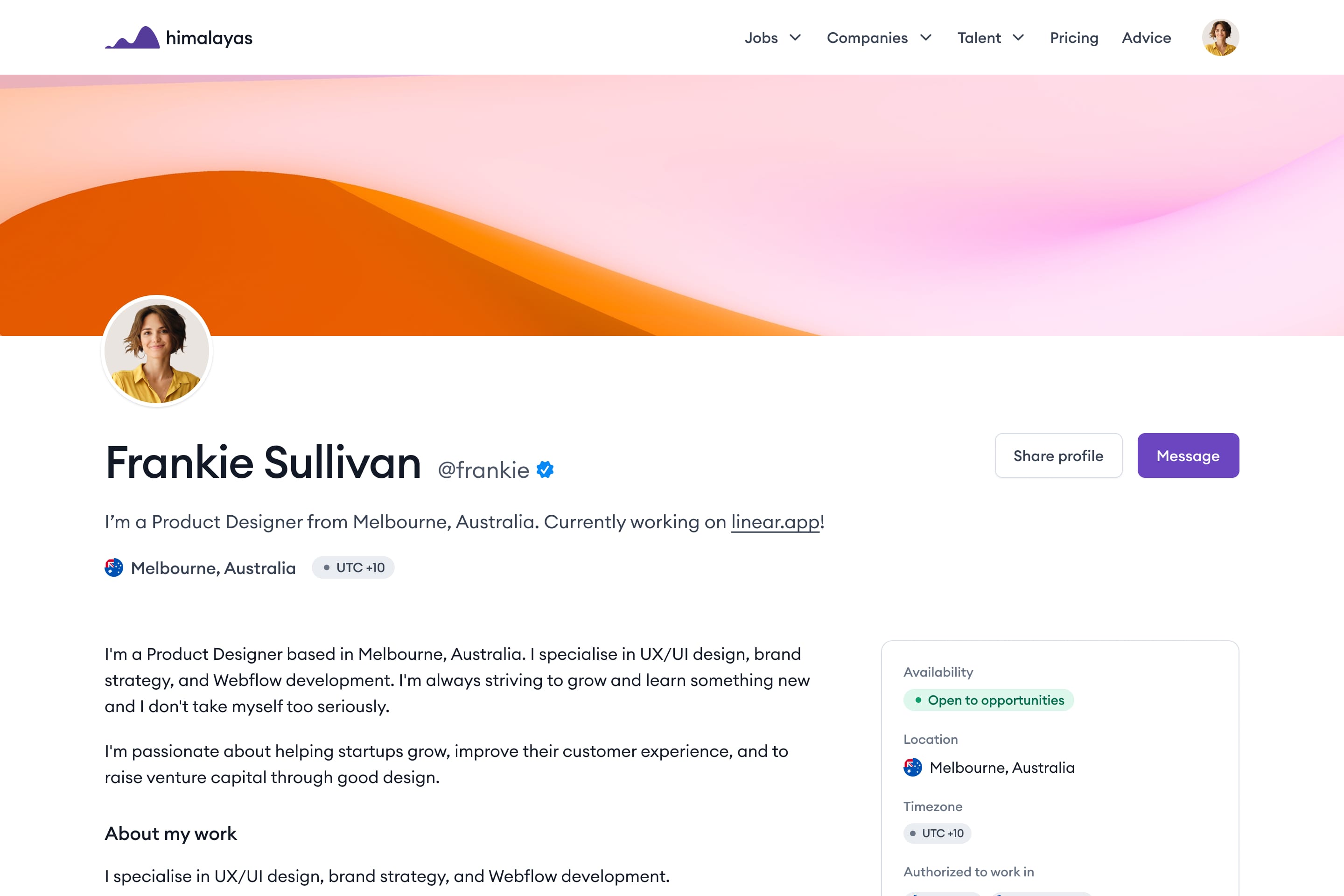