4 Assembly Line Worker Interview Questions and Answers
Assembly Line Workers are essential to the manufacturing process, responsible for assembling parts and products in a systematic and efficient manner. They ensure that production targets are met while maintaining quality standards. At entry levels, workers focus on specific tasks within the assembly process, while senior workers may take on more complex tasks and troubleshooting. Supervisors and managers oversee the entire assembly line, ensuring smooth operations and addressing any issues that arise. Need to practice for an interview? Try our AI interview practice for free then unlock unlimited access for just $9/month.
Unlimited interview practice for $9 / month
Improve your confidence with an AI mock interviewer.
No credit card required
1. Assembly Line Worker Interview Questions and Answers
1.1. Can you describe a time when you identified a safety hazard on the assembly line and how you addressed it?
Introduction
This question is crucial for evaluating your awareness of safety protocols and your proactive approach to maintaining a safe work environment, which is essential in manufacturing roles.
How to answer
- Use the STAR method: describe the Situation, Task, Action, and Result.
- Clearly explain the safety hazard you identified and its potential risks.
- Detail the steps you took to address the hazard, including communication with supervisors or colleagues.
- Highlight the positive outcomes of your actions, such as improved safety or compliance with regulations.
- Mention any follow-up measures taken to prevent future occurrences.
What not to say
- Ignoring safety protocols or suggesting they are unimportant.
- Describing a situation without taking any action.
- Failing to acknowledge the importance of teamwork in safety.
- Overlooking the importance of reporting hazards to management.
Example answer
“While working at Renault, I noticed that a section of the assembly line had insufficient lighting, which made it difficult to see clearly. I reported the issue to my supervisor and suggested installing additional lights. As a result, not only did we improve visibility, but it also reduced the number of near-misses by 30%. This experience reinforced my commitment to safety on the job.”
Skills tested
Question type
1.2. How do you ensure quality control in your work on the assembly line?
Introduction
This question assesses your attention to detail and commitment to maintaining high-quality standards, which are critical in assembly line roles.
How to answer
- Explain your understanding of quality control processes.
- Describe the specific methods you use to check your work for quality.
- Provide examples of how you have contributed to quality improvements in past roles.
- Discuss how you handle mistakes when they occur.
- Emphasize the importance of collaboration with quality assurance teams.
What not to say
- Claiming that quality control is not part of your responsibility.
- Using vague or non-specific examples.
- Failing to acknowledge past mistakes without learning from them.
- Suggesting that speed is more important than quality.
Example answer
“At Peugeot, I always double-check my work by reviewing each assembly step against the checklist provided. If I notice any discrepancies, I immediately report them to my supervisor. For example, I identified a recurring issue with a specific component not fitting correctly, which led to a team discussion that improved our fitting process by 15%. Quality is crucial, and I strive to uphold it in every task.”
Skills tested
Question type
2. Senior Assembly Line Worker Interview Questions and Answers
2.1. Can you describe a time when you identified and resolved a safety issue on the assembly line?
Introduction
This question is crucial as safety is a top priority in manufacturing environments. It assesses your ability to recognize hazards and take proactive measures to ensure a safe workplace.
How to answer
- Use the STAR method to structure your response, focusing on the Situation, Task, Action, and Result.
- Clearly outline the safety issue you encountered and its potential risks.
- Detail the steps you took to address the issue, including any collaboration with team members or management.
- Explain the outcome of your actions and any changes implemented as a result.
- Emphasize the importance of safety culture within the workplace.
What not to say
- Downplaying the importance of safety procedures.
- Avoiding personal responsibility by blaming others.
- Failing to provide a clear example or resolution.
- Not discussing the impact of your actions on team safety.
Example answer
“At Volkswagen, I noticed that a machine was leaking hydraulic fluid, creating a slip hazard. I immediately reported it to my supervisor and worked with maintenance to address the leak. As a result, we implemented more frequent equipment inspections, reducing safety incidents by 30%. This experience reinforced my belief in proactive safety management.”
Skills tested
Question type
2.2. How do you maintain quality control while working under tight deadlines on the assembly line?
Introduction
This question evaluates your ability to balance productivity and quality, which is essential in a fast-paced manufacturing environment.
How to answer
- Describe your quality control processes and any standards you adhere to.
- Share specific techniques you use to ensure product quality despite time pressures.
- Explain how you communicate with team members about quality expectations.
- Discuss any tools or technology you utilize to assist in maintaining quality.
- Provide examples of how you have successfully met deadlines without compromising quality.
What not to say
- Suggesting that quality is secondary to meeting deadlines.
- Failing to mention any specific methods for quality control.
- Not providing concrete examples of past experiences.
- Overlooking the importance of teamwork in maintaining quality.
Example answer
“While working at Daimler, we faced tight production schedules. I implemented a checklist system to ensure each assembly step met quality standards. By communicating regularly with my team about potential issues, we maintained a defect rate of less than 1% even during peak times. This taught me that effective communication and process adherence are key to balancing quality and speed.”
Skills tested
Question type
2.3. What motivates you to excel in your role as an assembly line worker?
Introduction
Understanding your motivations can help gauge your commitment to the role and the organization, which is vital for team morale and productivity.
How to answer
- Share personal values that drive you in your work, such as teamwork, craftsmanship, or safety.
- Relate your motivation to the broader goals of the company.
- Discuss how your contributions impact the team's success.
- Provide examples of accomplishments that fueled your motivation.
- Express your enthusiasm for the industry and your role within it.
What not to say
- Focusing solely on monetary rewards.
- Indicating a lack of interest in personal or team development.
- Providing vague or generic answers.
- Not connecting your motivation to the specific role or company.
Example answer
“I am motivated by the satisfaction of producing high-quality products that make a difference in people's lives. At BMW, knowing that my work contributes to vehicles that are both safe and enjoyable to drive inspires me. I take pride in my craftsmanship and value the teamwork that drives our success as a production line.”
Skills tested
Question type
3. Assembly Line Supervisor Interview Questions and Answers
3.1. Can you describe a time when you had to improve the efficiency of an assembly line?
Introduction
This question evaluates your problem-solving skills and ability to enhance operational efficiency, which are critical in the role of an Assembly Line Supervisor.
How to answer
- Use the STAR method (Situation, Task, Action, Result) to structure your response
- Clearly define the inefficiency issue you faced and its impact on production
- Describe the steps you took to analyze the problem and implement changes
- Highlight any collaboration with team members or other departments
- Provide measurable outcomes that demonstrate the success of your initiatives
What not to say
- Focusing on blame rather than solutions
- Giving vague examples without specific actions or results
- Neglecting to mention teamwork or collaboration
- Failing to quantify improvements or impact
Example answer
“At Fiat, we noticed a bottleneck in our assembly line that was causing delays. I led a team to analyze the workflow and identified that we needed to rearrange the stations for better efficiency. By implementing a new layout and introducing standardized work procedures, we improved our output by 20% over three months. This experience taught me the value of teamwork in driving operational improvements.”
Skills tested
Question type
3.2. How do you handle conflicts or disagreements among assembly line workers?
Introduction
This question assesses your conflict resolution skills and ability to maintain a productive work environment, which is crucial for team dynamics on the assembly line.
How to answer
- Discuss your approach to conflict resolution, emphasizing communication and understanding
- Provide a specific example of a conflict you managed successfully
- Highlight the importance of fairness and maintaining morale
- Explain how you ensure that conflicts do not affect overall productivity
- Share any follow-up actions taken to prevent future conflicts
What not to say
- Ignoring the importance of addressing conflicts
- Describing a situation where you took sides rather than remaining neutral
- Focusing only on the conflict without discussing resolution
- Failing to mention the impact on team dynamics
Example answer
“In my previous role at Bosch, I encountered a situation where two team members had a disagreement over responsibilities that was affecting the workflow. I facilitated a meeting with both individuals to discuss their perspectives. By encouraging open communication, we reached a compromise that allowed them to collaborate effectively. Afterward, I conducted a team meeting to set clearer expectations, which helped improve overall morale and productivity.”
Skills tested
Question type
4. Assembly Line Manager Interview Questions and Answers
4.1. Can you describe a time when you had to improve the efficiency of an assembly line?
Introduction
This question is important for assessing your problem-solving abilities and understanding of operational efficiency, which are critical for an Assembly Line Manager.
How to answer
- Use the STAR method to frame your response
- Start by explaining the initial challenges the assembly line faced
- Detail the specific steps you took to analyze and improve the process
- Quantify the improvements achieved in terms of efficiency or output
- Discuss any changes you made to team dynamics or training
What not to say
- Focusing only on the problems without discussing solutions
- Making vague claims without concrete metrics or outcomes
- Ignoring the importance of teamwork and collaboration
- Overlooking safety considerations in your improvements
Example answer
“At Fiat, our assembly line was experiencing a 20% backlog due to bottlenecks in the painting section. I implemented a time-motion study that highlighted inefficiencies in the workflow. By reorganizing the layout and introducing cross-training for employees, we improved our output by 30% and decreased the backlog significantly. This experience taught me the value of data-driven decisions and team involvement.”
Skills tested
Question type
4.2. How do you handle conflicts among team members on the assembly line?
Introduction
This question evaluates your conflict resolution and interpersonal skills, which are essential for maintaining a harmonious and productive work environment.
How to answer
- Describe your approach to identifying conflict early
- Explain your strategies for facilitating open communication
- Share an example of a specific conflict you resolved
- Discuss how you ensure that all voices are heard
- Highlight any follow-up actions taken to prevent future conflicts
What not to say
- Ignoring the importance of addressing conflicts promptly
- Suggesting that conflicts are not a concern in the workplace
- Failing to provide a concrete example from your experience
- Overemphasizing authority instead of collaboration
Example answer
“In my role at Lamborghini, two team members had a disagreement over task responsibilities, which affected morale. I organized a mediation session where each person could express their concerns. By facilitating a constructive dialogue, we clarified roles and responsibilities. As a result, not only did we resolve the conflict, but we also improved team cohesion, leading to a 15% increase in productivity.”
Skills tested
Question type
Similar Interview Questions and Sample Answers
Simple pricing, powerful features
Upgrade to Himalayas Plus and turbocharge your job search.
Himalayas
Himalayas Plus
Himalayas Max
Find your dream job
Sign up now and join over 100,000 remote workers who receive personalized job alerts, curated job matches, and more for free!
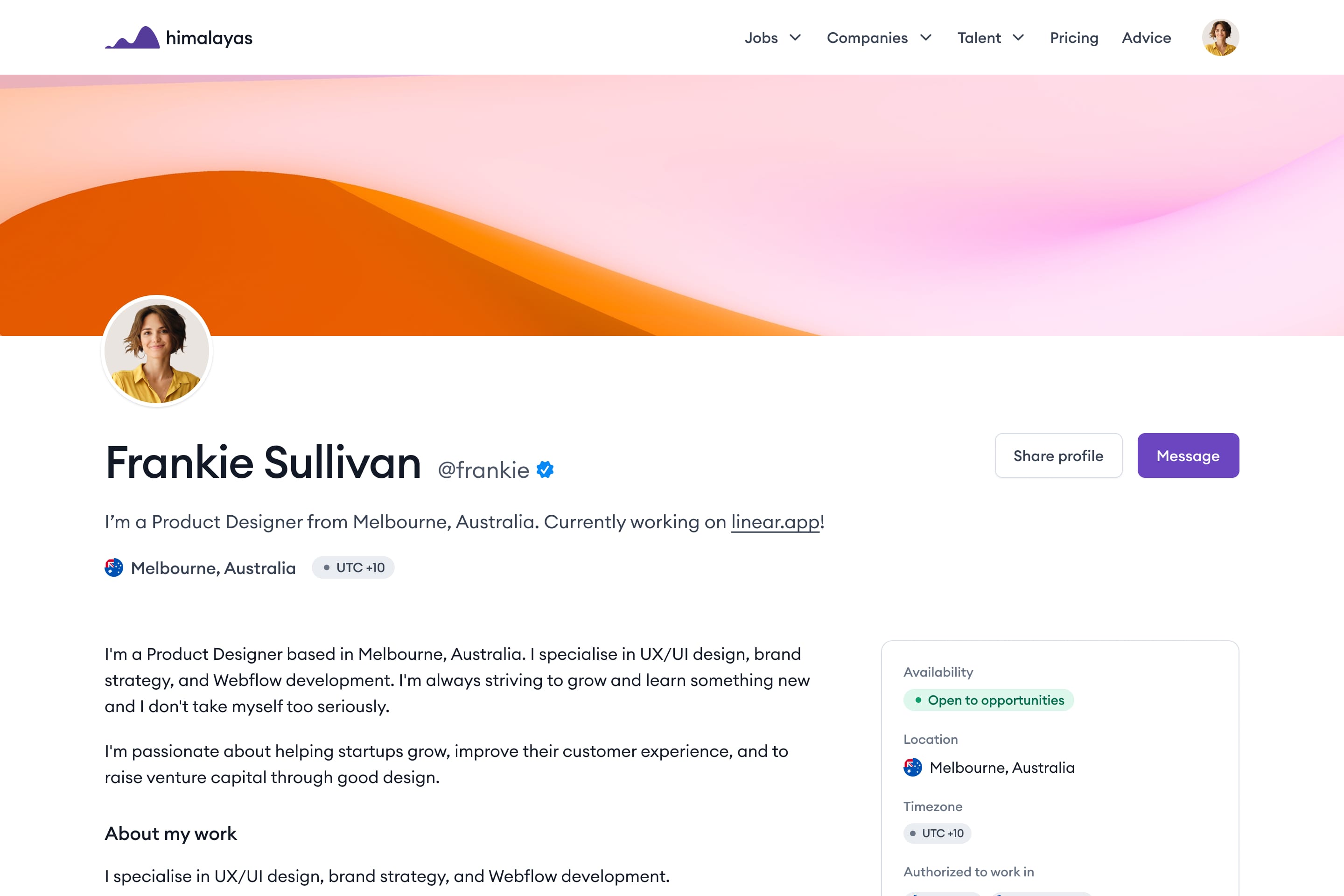