Complete Supplier Quality Manager Career Guide
A Supplier Quality Manager ensures that all purchased components and services meet stringent quality standards, directly impacting a company's product reliability and brand reputation. This critical role involves auditing, problem-solving, and continuous improvement across the supply chain, making you indispensable to operational excellence and cost efficiency. It's a challenging yet rewarding path for those who thrive on precision and strategic vendor relationships.
Key Facts & Statistics
Median Salary
$106,780 USD
(U.S. national median, BLS, May 2023)
Range: $70k - $150k+ USD, varying significantly by industry and location
Growth Outlook
3%
as fast as average (BLS, 2022-2032)
Annual Openings
≈17,000
openings annually (BLS, 2022-2032)
Top Industries
Typical Education
Bachelor's degree in Engineering, Supply Chain Management, or a related technical field; certifications like ASQ Certified Quality Engineer (CQE) or Certified Manager of Quality/Organizational Excellence (CMQ/OE) are highly valued.
What is a Supplier Quality Manager?
A Supplier Quality Manager is a critical professional who ensures that the materials, components, and services provided by external suppliers meet an organization's stringent quality standards. This role bridges the gap between a company's internal quality requirements and its supply chain, safeguarding product integrity and operational efficiency. They proactively identify, assess, and mitigate risks associated with supplier performance, directly impacting product reliability and customer satisfaction.
Unlike a general Quality Manager who focuses on internal processes, or a Procurement Manager who emphasizes cost and delivery, the Supplier Quality Manager specializes in the external supply base. Their primary objective is to build a robust, high-performing supplier network by implementing rigorous quality controls, conducting audits, and driving continuous improvement initiatives with external partners. They are instrumental in preventing defects before they reach the production line, thereby reducing costs and enhancing overall product quality.
What does a Supplier Quality Manager do?
Key Responsibilities
- Conduct regular audits of supplier facilities and processes to ensure compliance with quality standards and regulatory requirements.
- Collaborate with procurement and engineering teams to qualify new suppliers and assess their capabilities before onboarding.
- Develop and implement supplier quality agreements, establishing clear expectations for performance, documentation, and corrective actions.
- Analyze supplier performance data, including defect rates, on-time delivery, and audit findings, to identify areas for improvement.
- Lead root cause analysis and corrective action initiatives for supplier-related quality issues, ensuring timely resolution and preventing recurrence.
- Manage the supplier corrective action request (SCAR) process, tracking progress and verifying the effectiveness of implemented solutions.
- Provide technical guidance and training to suppliers on quality methodologies, process controls, and product specifications to foster continuous improvement.
Work Environment
Supplier Quality Managers typically work in a hybrid environment, splitting their time between a corporate office and supplier sites. The role involves frequent travel, often both domestically and internationally, to conduct audits, resolve issues, and build relationships with suppliers. They collaborate extensively with internal teams such as procurement, engineering, manufacturing, and legal. The pace of work can be dynamic, balancing proactive quality assurance activities with reactive problem-solving when issues arise. While some roles offer remote flexibility for administrative tasks, on-site supplier visits are a fundamental component of the job, ensuring direct oversight and effective problem resolution.
Tools & Technologies
Supplier Quality Managers frequently utilize Enterprise Resource Planning (ERP) systems like SAP or Oracle to track supplier data, orders, and performance metrics. They also use Quality Management Software (QMS) such as MasterControl or EtQ Reliance for document control, non-conformance management, and audit scheduling. Data analysis tools like Microsoft Excel, Minitab, or specialized statistical software are essential for evaluating supplier performance and identifying trends. Communication and collaboration platforms like Microsoft Teams or Slack facilitate interaction with internal teams and external suppliers. Additionally, they work with various industry-specific quality standards and frameworks, including ISO 9001, AS9100, IATF 16949, or FDA regulations, depending on the industry.
Supplier Quality Manager Skills & Qualifications
A Supplier Quality Manager ensures that an organization's suppliers deliver products and services meeting established quality standards. This role bridges supply chain management, quality assurance, and engineering, focusing on preventing defects rather than just detecting them. Qualification requirements for this position vary significantly based on the industry, company size, and the complexity of the supply chain.
For instance, a Supplier Quality Manager in the automotive or aerospace industry typically requires a strong engineering background due to stringent regulatory compliance and high-reliability components. In contrast, roles in consumer goods or retail might prioritize supply chain management experience and process improvement. Larger corporations often demand extensive experience and formal certifications, while smaller companies might value a broader skill set and adaptability. Practical experience often holds more weight than formal education alone, especially for senior roles, but a relevant degree provides a crucial foundational understanding.
Certifications like ASQ's Certified Quality Engineer (CQE), Certified Quality Auditor (CQA), or Certified Manager of Quality/Organizational Excellence (CMQ/OE) significantly enhance a candidate's profile. These credentials validate specialized knowledge and commitment to quality principles. The skill landscape evolves with global supply chain complexities, emphasizing digital tools for supplier monitoring, data analytics for performance prediction, and robust risk management. Balancing deep technical knowledge with strong interpersonal skills is critical for effective supplier collaboration and continuous improvement.
Education Requirements
Technical Skills
- Quality Management Systems (e.g., ISO 9001, IATF 16949, AS9100, ISO 13485 depending on industry)
- Supplier Audit and Assessment Methodologies (e.g., VDA 6.3, process audits, product audits)
- Statistical Process Control (SPC) and Statistical Quality Control (SQC)
- Root Cause Analysis Tools (e.g., 8D, 5 Whys, Fishbone diagrams, FMEA - Failure Mode and Effects Analysis)
- Measurement Systems Analysis (MSA) and Gage R&R studies
- Lean Manufacturing and Six Sigma principles (e.g., DMAIC methodology)
- Supplier Performance Management and Scorecard Development
- Contract Review and Specification Interpretation
- Non-Conformance Management and Corrective Action/Preventive Action (CAPA) Processes
- Enterprise Resource Planning (ERP) and Quality Management Software (QMS) proficiency for supplier data management
- Technical Drawing and Blueprint Reading (GD&T - Geometric Dimensioning and Tolerancing)
- Global Supply Chain Dynamics and Risk Management
Soft Skills
- Negotiation and Persuasion: Essential for establishing clear quality agreements, resolving non-conformances, and driving continuous improvement with suppliers.
- Problem-Solving and Root Cause Analysis: Crucial for identifying the underlying issues of supplier quality failures and implementing effective corrective actions.
- Cross-functional Collaboration: Necessary to work effectively with internal teams (e.g., R&D, Procurement, Manufacturing) and external suppliers to achieve quality goals.
- Communication and Presentation: Important for clearly articulating quality requirements, audit findings, and performance metrics to diverse audiences, both internal and external.
- Stakeholder Management: Vital for balancing the needs and expectations of various internal departments, suppliers, and regulatory bodies.
- Analytical Thinking and Data Interpretation: Key for interpreting complex supplier performance data, identifying trends, and making data-driven decisions.
- Adaptability and Resilience: Important for navigating unforeseen supply chain disruptions, changing supplier capabilities, and evolving quality standards.
- Ethical Judgment and Integrity: Crucial for maintaining fair and transparent relationships with suppliers while upholding the organization's quality standards.
How to Become a Supplier Quality Manager
Breaking into the Supplier Quality Manager role involves diverse pathways, far beyond a single traditional route. Many individuals transition from engineering, manufacturing operations, or quality assurance roles, leveraging their existing process knowledge. The timeline for entry varies significantly; a complete beginner might need 2-3 years to build foundational skills and gain relevant experience, while a seasoned professional from a related field could transition in 6-12 months.
Entry strategies often depend on company size and industry. Large corporations may prefer candidates with formal quality certifications and a proven track record, whereas smaller companies or startups might value practical problem-solving skills and adaptability more. Geographic location also influences opportunities; industrial hubs typically offer more roles. Understanding these nuances helps candidates tailor their approach, whether focusing on certifications, hands-on experience, or specific industry knowledge.
Networking and mentorship play crucial roles in this field. Connecting with professionals can reveal unadvertised opportunities and provide insights into industry-specific challenges. Overcoming barriers like a lack of direct supplier management experience often means highlighting transferable skills in process improvement, auditing, and root cause analysis from previous roles. The hiring landscape values a blend of technical acumen, soft skills like negotiation, and a proactive approach to risk mitigation.
Develop a strong foundation in quality management principles by studying ISO 9001 and other relevant quality standards such as IATF 16949 for automotive or AS9100 for aerospace. Consider pursuing foundational certifications like ASQ Certified Quality Inspector (CQI) or Certified Quality Technician (CQT) to validate your understanding.
Gain practical experience in manufacturing, operations, or quality assurance roles for 1-3 years. Focus on tasks involving process control, root cause analysis, corrective actions, and internal auditing, as these directly transfer to supplier quality management.
Acquire specialized knowledge in supplier auditing and supply chain management. Complete courses on lead auditor training for ISO standards and learn about supplier selection, performance monitoring, and risk assessment techniques. Many professional organizations offer relevant workshops.
Build a professional network within the supply chain and quality communities by attending industry conferences, webinars, and local chapter meetings of organizations like ASQ or ISM. Seek out mentors who are experienced Supplier Quality Managers to gain insights and guidance.
Create a targeted resume and cover letter that highlights your relevant experience in quality, manufacturing, or operations, emphasizing achievements related to process improvement, problem-solving, and collaboration. Prepare for interviews by practicing responses to questions about supplier audits, non-conformance management, and relationship building.
Apply for entry-level or junior Supplier Quality Engineer/Specialist roles, or positions with similar responsibilities such as Quality Engineer with supplier interaction. Be prepared to discuss specific examples of how you have improved processes or resolved issues in previous roles, even if not directly with external suppliers.
Continuously learn and adapt by staying updated on industry best practices, new technologies in quality management, and evolving supply chain regulations. Pursue advanced certifications like ASQ Certified Quality Engineer (CQE) or Certified Quality Auditor (CQA) to enhance your credentials and career progression.
Step 1
Develop a strong foundation in quality management principles by studying ISO 9001 and other relevant quality standards such as IATF 16949 for automotive or AS9100 for aerospace. Consider pursuing foundational certifications like ASQ Certified Quality Inspector (CQI) or Certified Quality Technician (CQT) to validate your understanding.
Step 2
Gain practical experience in manufacturing, operations, or quality assurance roles for 1-3 years. Focus on tasks involving process control, root cause analysis, corrective actions, and internal auditing, as these directly transfer to supplier quality management.
Step 3
Acquire specialized knowledge in supplier auditing and supply chain management. Complete courses on lead auditor training for ISO standards and learn about supplier selection, performance monitoring, and risk assessment techniques. Many professional organizations offer relevant workshops.
Step 4
Build a professional network within the supply chain and quality communities by attending industry conferences, webinars, and local chapter meetings of organizations like ASQ or ISM. Seek out mentors who are experienced Supplier Quality Managers to gain insights and guidance.
Step 5
Create a targeted resume and cover letter that highlights your relevant experience in quality, manufacturing, or operations, emphasizing achievements related to process improvement, problem-solving, and collaboration. Prepare for interviews by practicing responses to questions about supplier audits, non-conformance management, and relationship building.
Step 6
Apply for entry-level or junior Supplier Quality Engineer/Specialist roles, or positions with similar responsibilities such as Quality Engineer with supplier interaction. Be prepared to discuss specific examples of how you have improved processes or resolved issues in previous roles, even if not directly with external suppliers.
Step 7
Continuously learn and adapt by staying updated on industry best practices, new technologies in quality management, and evolving supply chain regulations. Pursue advanced certifications like ASQ Certified Quality Engineer (CQE) or Certified Quality Auditor (CQA) to enhance your credentials and career progression.
Education & Training Needed to Become a Supplier Quality Manager
Becoming a Supplier Quality Manager involves a blend of formal education and practical experience, with diverse pathways available. Traditional four-year bachelor's degrees in engineering, supply chain management, or business administration often serve as foundational credentials. These degrees typically cost between $40,000 and $100,000+ for in-state tuition and take four years to complete. They provide a strong theoretical base in quality systems, manufacturing processes, and supply chain dynamics, which employers value for strategic roles.
Alternatively, professionals can pursue certifications and specialized training programs, which offer more focused and time-efficient learning. Certifications like ASQ's Certified Quality Manager/Organizational Excellence (CMQ/OE) or Certified Quality Engineer (CQE) are highly recognized industry standards, costing $500-$1,500 and requiring 6-12 months of self-study or short courses. These options enhance specific skill sets and demonstrate a commitment to quality principles. Online courses and professional development workshops further bridge knowledge gaps, often ranging from free to a few thousand dollars, with completion times from weeks to a few months.
Employer perception varies; while large corporations often prefer candidates with bachelor's or master's degrees, practical experience combined with relevant certifications can open doors in many companies. Continuous learning remains crucial for Supplier Quality Managers due to evolving global supply chains and quality standards. This includes staying current with new regulations, quality tools (e.g., Lean Six Sigma), and technologies. The cost-benefit analysis favors a foundational degree followed by targeted certifications and ongoing professional development to maximize career progression and earning potential in this specialized field.
Supplier Quality Manager Salary & Outlook
Compensation for a Supplier Quality Manager varies significantly based on several factors. Geographic location plays a crucial role, with higher salaries often found in major industrial hubs or regions with a high cost of living, such as California, New York, or Massachusetts. Conversely, areas with lower living costs may offer more modest base salaries, although purchasing power can be similar. International markets also present diverse compensation structures, typically benchmarked against local economic conditions, with USD figures serving as a common reference point.
Years of experience, the complexity of supply chains managed, and specific industry knowledge (e.g., aerospace, automotive, medical devices) dramatically influence earning potential. Professionals with expertise in niche quality standards or global supplier networks command higher compensation. Total compensation packages extend beyond base salary, often including performance-based bonuses, company equity or stock options, comprehensive health benefits, and robust retirement contributions. Companies also frequently provide professional development allowances for certifications like ASQ or Six Sigma, enhancing long-term earning capacity.
Industry-specific trends, such as increased regulatory scrutiny or globalization of supply chains, can drive salary growth for skilled Supplier Quality Managers. Negotiation leverage comes from a proven track record of cost savings, risk mitigation, and successful supplier development programs. Remote work has introduced geographic arbitrage opportunities, allowing some professionals to earn salaries benchmarked to higher-cost regions while residing in lower-cost areas. Understanding these components is key to maximizing earning potential in this field.
Salary by Experience Level
Level | US Median | US Average |
---|---|---|
Associate Supplier Quality Manager | $70k USD | $75k USD |
Supplier Quality Manager | $100k USD | $105k USD |
Senior Supplier Quality Manager | $130k USD | $135k USD |
Supplier Quality Lead | $150k USD | $155k USD |
Supplier Quality Director | $180k USD | $185k USD |
VP of Supplier Quality | $220k USD | $230k USD |
Market Commentary
The job market for Supplier Quality Managers shows stable demand, driven by globalized supply chains and increasing emphasis on product reliability and regulatory compliance. Industries like manufacturing, automotive, aerospace, and medical devices consistently seek these professionals. Projections indicate a steady growth outlook, often tied to overall manufacturing output and the complexity of global sourcing. Companies are investing more in resilient supply chains, which directly translates to a need for skilled quality oversight.
Emerging opportunities include roles focused on supply chain digitalization, sustainable sourcing practices, and risk management related to geopolitical events. The integration of AI and advanced analytics is beginning to reshape the role, shifting some routine tasks and enhancing predictive quality management. This evolution requires Supplier Quality Managers to develop stronger data analysis and technological proficiency to remain competitive.
The supply of qualified candidates can be tight, particularly for those with specialized industry experience or international supplier management expertise. This imbalance often results in competitive salaries and strong hiring incentives. While not entirely recession-proof, the role is relatively resilient because maintaining quality and mitigating supply chain risks remains critical even during economic downturns. Geographic hotspots for these roles align with manufacturing corridors and innovation centers, though remote work options are expanding the talent pool. Continuous learning in areas like lean manufacturing, quality systems, and digital tools is essential for career advancement.
Supplier Quality Manager Career Path
Career progression for a Supplier Quality Manager involves a blend of technical expertise, relationship management, and strategic leadership. Professionals typically advance by demonstrating consistent success in ensuring product quality, managing supplier relationships, and implementing robust quality systems. Progression can follow an individual contributor (IC) track, focusing on deep technical specialization and complex problem-solving, or a management/leadership track, emphasizing team oversight, strategic direction, and broader organizational impact.
Advancement speed depends on several factors: an individual's performance in improving supplier quality, the complexity of the supply chain, and the industry's regulatory environment. Specialization in areas like advanced quality planning, auditing, or specific material categories can accelerate growth. Company size also affects career paths; larger corporations may offer more defined vertical paths, while startups or smaller firms might provide broader exposure and faster assumption of leadership roles. Lateral moves into roles like Supply Chain Management, Procurement, or Manufacturing Quality are common, leveraging a deep understanding of supplier dynamics and quality assurance.
Networking within industry groups, pursuing relevant certifications (e.g., ASQ certifications), and continuous learning in areas like lean manufacturing, Six Sigma, and global quality standards are crucial for sustained progression. Mentorship plays a significant role in developing the strategic and leadership competencies needed for senior roles. Building a strong reputation for problem-solving and fostering collaborative supplier relationships unlocks higher-level opportunities and prepares individuals for executive leadership in quality or supply chain functions.
Associate Supplier Quality Manager
0-2 yearsSupport senior team members in managing supplier quality issues, conducting basic audits, and tracking supplier performance metrics. Assist with corrective action follow-up and data collection. Work under direct supervision, focusing on specific tasks within established quality processes.
Key Focus Areas
Develop foundational knowledge of quality systems, auditing principles, and data analysis. Focus on mastering root cause analysis tools and corrective action processes. Build communication skills for effective supplier interaction and internal reporting. Understand relevant industry standards and regulations.
Supplier Quality Manager
2-5 yearsManage a portfolio of suppliers, ensuring adherence to quality standards and specifications. Drive corrective and preventive actions for identified non-conformances. Conduct supplier audits and assess quality management systems. Influence supplier performance through direct engagement and data-driven feedback.
Key Focus Areas
Enhance problem-solving abilities, particularly for complex quality deviations. Develop stronger negotiation and conflict resolution skills for supplier interactions. Focus on proactive quality planning (APQP) and risk mitigation. Begin to mentor junior associates and take ownership of process improvements.
Senior Supplier Quality Manager
5-8 yearsOversee critical or high-risk suppliers, implementing strategic quality improvement initiatives. Lead complex problem-solving efforts and drive significant cost-of-poor-quality reductions. Provide technical guidance and mentorship to other quality professionals. Contribute to the development of departmental policies and procedures.
Key Focus Areas
Master advanced quality tools like Six Sigma and Lean methodologies. Develop strategic thinking to align supplier quality with business objectives. Cultivate strong cross-functional leadership and stakeholder management skills. Focus on developing new supplier onboarding processes and risk assessment frameworks.
Supplier Quality Lead
8-12 yearsLead a team of Supplier Quality Managers and Associates, setting performance objectives and providing technical direction. Manage supplier quality programs for new product introductions or major product lines. Act as the primary interface for complex supplier quality issues with internal stakeholders and executive leadership. Drive continuous improvement across the entire supply base.
Key Focus Areas
Develop formal leadership and team management skills, including performance management and talent development. Focus on program management for large-scale quality initiatives. Enhance strategic planning and execution capabilities. Build a reputation as an internal subject matter expert and external industry liaison.
Supplier Quality Director
12-18 yearsDefine and implement the overall supplier quality strategy for a business unit or major division. Lead large-scale quality improvement programs impacting multiple product categories or regions. Manage a significant budget and resource allocation for the supplier quality function. Influence cross-functional leadership decisions related to supplier selection and performance.
Key Focus Areas
Cultivate executive presence and strategic communication skills. Focus on global supply chain quality strategy and risk management. Develop expertise in supplier relationship management at a strategic level. Drive organizational change and innovation in quality processes.
VP of Supplier Quality
18+ yearsEstablish the vision and strategic direction for all aspects of supplier quality across the entire organization. Oversee global supplier quality operations, ensuring alignment with corporate objectives and regulatory requirements. Serve as a key member of the executive leadership team, influencing business strategy and major investment decisions related to the supply chain. Represent the company in external quality forums and industry associations.
Key Focus Areas
Master enterprise-level quality strategy and governance. Develop expertise in global regulatory compliance and geopolitical risk assessment for supply chains. Focus on executive leadership, talent acquisition, and strategic partnerships. Drive a culture of quality excellence throughout the organization and its supply network.
Associate Supplier Quality Manager
0-2 yearsSupport senior team members in managing supplier quality issues, conducting basic audits, and tracking supplier performance metrics. Assist with corrective action follow-up and data collection. Work under direct supervision, focusing on specific tasks within established quality processes.
Key Focus Areas
Develop foundational knowledge of quality systems, auditing principles, and data analysis. Focus on mastering root cause analysis tools and corrective action processes. Build communication skills for effective supplier interaction and internal reporting. Understand relevant industry standards and regulations.
Supplier Quality Manager
2-5 yearsManage a portfolio of suppliers, ensuring adherence to quality standards and specifications. Drive corrective and preventive actions for identified non-conformances. Conduct supplier audits and assess quality management systems. Influence supplier performance through direct engagement and data-driven feedback.
Key Focus Areas
Enhance problem-solving abilities, particularly for complex quality deviations. Develop stronger negotiation and conflict resolution skills for supplier interactions. Focus on proactive quality planning (APQP) and risk mitigation. Begin to mentor junior associates and take ownership of process improvements.
Senior Supplier Quality Manager
5-8 yearsOversee critical or high-risk suppliers, implementing strategic quality improvement initiatives. Lead complex problem-solving efforts and drive significant cost-of-poor-quality reductions. Provide technical guidance and mentorship to other quality professionals. Contribute to the development of departmental policies and procedures.
Key Focus Areas
Master advanced quality tools like Six Sigma and Lean methodologies. Develop strategic thinking to align supplier quality with business objectives. Cultivate strong cross-functional leadership and stakeholder management skills. Focus on developing new supplier onboarding processes and risk assessment frameworks.
Supplier Quality Lead
8-12 yearsLead a team of Supplier Quality Managers and Associates, setting performance objectives and providing technical direction. Manage supplier quality programs for new product introductions or major product lines. Act as the primary interface for complex supplier quality issues with internal stakeholders and executive leadership. Drive continuous improvement across the entire supply base.
Key Focus Areas
Develop formal leadership and team management skills, including performance management and talent development. Focus on program management for large-scale quality initiatives. Enhance strategic planning and execution capabilities. Build a reputation as an internal subject matter expert and external industry liaison.
Supplier Quality Director
12-18 yearsDefine and implement the overall supplier quality strategy for a business unit or major division. Lead large-scale quality improvement programs impacting multiple product categories or regions. Manage a significant budget and resource allocation for the supplier quality function. Influence cross-functional leadership decisions related to supplier selection and performance.
Key Focus Areas
Cultivate executive presence and strategic communication skills. Focus on global supply chain quality strategy and risk management. Develop expertise in supplier relationship management at a strategic level. Drive organizational change and innovation in quality processes.
VP of Supplier Quality
18+ yearsEstablish the vision and strategic direction for all aspects of supplier quality across the entire organization. Oversee global supplier quality operations, ensuring alignment with corporate objectives and regulatory requirements. Serve as a key member of the executive leadership team, influencing business strategy and major investment decisions related to the supply chain. Represent the company in external quality forums and industry associations.
Key Focus Areas
Master enterprise-level quality strategy and governance. Develop expertise in global regulatory compliance and geopolitical risk assessment for supply chains. Focus on executive leadership, talent acquisition, and strategic partnerships. Drive a culture of quality excellence throughout the organization and its supply network.
Job Application Toolkit
Ace your application with our purpose-built resources:
Supplier Quality Manager Resume Examples
Proven layouts and keywords hiring managers scan for.
View examplesSupplier Quality Manager Cover Letter Examples
Personalizable templates that showcase your impact.
View examplesTop Supplier Quality Manager Interview Questions
Practice with the questions asked most often.
View examplesSupplier Quality Manager Job Description Template
Ready-to-use JD for recruiters and hiring teams.
View examplesGlobal Supplier Quality Manager Opportunities
A Supplier Quality Manager ensures suppliers meet quality standards, a critical role in global supply chains. This profession translates across industries worldwide, from manufacturing to technology, with high demand in regions focused on robust production and regulatory compliance. International opportunities exist due to dispersed supply networks and the need for consistent quality assurance. Professionals often seek global roles for diverse industry exposure and career advancement. Certifications like ASQ CMQ/OE or ISO 9001 lead auditor enhance global mobility.
Global Salaries
Supplier Quality Manager salaries vary significantly by region and industry. In North America, a typical range for an experienced manager is USD 90,000 to USD 140,000 annually. For instance, in the US, it might be USD 100,000-130,000, while in Canada, CAD 95,000-125,000 (approx. USD 70,000-92,000).
Europe offers diverse ranges. In Germany, salaries are often EUR 65,000-95,000 (approx. USD 70,000-103,000), reflecting a higher cost of living. The UK sees GBP 55,000-80,000 (approx. USD 70,000-101,000). Southern and Eastern Europe generally have lower nominal salaries but higher purchasing power due to lower living costs.
Asia-Pacific markets present different structures. In China, a Supplier Quality Manager might earn CNY 250,000-450,000 (approx. USD 35,000-63,000), which provides substantial local purchasing power. Japan offers JPY 7,000,000-11,000,000 (approx. USD 47,000-74,000). These figures often include comprehensive benefits packages that differ from Western norms, such as housing allowances or performance bonuses.
Latin America typically has lower nominal salaries; for example, in Mexico, MXN 500,000-900,000 (approx. USD 29,000-52,000). Compensation structures also differ, with varied vacation time, healthcare provisions, and pension contributions across countries. Tax implications significantly affect take-home pay, with some European countries having higher income tax rates than North America. International experience and advanced degrees often lead to higher compensation globally, particularly in multinational corporations with standardized global pay scales.
Remote Work
International remote work for a Supplier Quality Manager is less common than for purely digital roles, but it is growing. This role often requires on-site supplier audits and direct interaction, limiting full remote potential. Hybrid models are more prevalent, allowing some remote work balanced with necessary travel.
Legal and tax implications for international remote work are complex. Professionals must understand their tax residency status and potential double taxation agreements. Time zone differences can pose challenges for global team collaboration, requiring flexible working hours.
Some companies, especially those with established global supply chains, may allow Supplier Quality Managers to be based in a central hub while managing suppliers remotely, traveling as needed. Digital nomad visas are emerging in countries like Portugal or Spain, but their applicability for roles requiring frequent physical presence is limited. Equipment needs include reliable internet and secure access to company systems. Salary expectations for remote roles might see adjustments based on the employee's location and the employer's global compensation policies.
Visa & Immigration
Supplier Quality Managers often qualify for skilled worker visas in many countries. Popular destinations include Germany (EU Blue Card), Canada (Express Entry), and Australia (Skilled Nominated Visa Subclass 190). These visas typically require a job offer, relevant education, and professional experience.
Education credential recognition is crucial; applicants often need their degrees assessed by a national authority. Professional licensing is generally not required for this role, but industry-specific certifications are beneficial. Typical visa timelines range from a few months to over a year, depending on the country and visa type. The application process involves submitting documents, background checks, and sometimes interviews.
Pathways to permanent residency often exist after several years of skilled employment. Language requirements vary; some countries like Canada or Germany require proof of language proficiency (English or German, respectively). Intra-company transfers are common for multinational corporations moving existing employees. Practical considerations include securing family visas for dependents, which are usually tied to the primary applicant's work visa.
2025 Market Reality for Supplier Quality Managers
Understanding current market realities is crucial for Supplier Quality Managers navigating a rapidly evolving professional landscape. The period from 2023 to 2025 brought significant shifts, including post-pandemic supply chain reconfigurations and the accelerating impact of AI on quality processes.
Broader economic factors, such as inflation and global trade policies, directly influence manufacturing output and, consequently, the demand for quality oversight within supply chains. Market realities vary considerably; entry-level positions often face higher competition than specialized senior roles, and opportunities differ between regions with strong industrial bases versus those focused on services. This analysis provides an honest assessment to help professionals strategically plan their careers.
Current Challenges
Supplier Quality Managers face increased competition, especially for remote roles, as companies consolidate operations and demand higher productivity from AI-augmented teams. Economic uncertainty causes hiring freezes, particularly impacting roles in non-critical supply chain areas. Mismatches exist between traditional quality assurance skills and the growing need for data analytics and AI-driven risk assessment.
Moreover, the normalization of remote work expands the talent pool, intensifying competition. Job search timelines have lengthened, often requiring several months to secure a suitable position in the current climate.
Growth Opportunities
Despite challenges, strong opportunities exist for Supplier Quality Managers specializing in AI-driven quality assurance, sustainable sourcing, and risk management. Companies increasingly seek professionals who can leverage AI tools for predictive defect analysis and automated supplier assessments, transforming traditional quality control into proactive risk mitigation.
Emerging roles focus on supply chain digitization, where managers oversee the integration of IoT sensors for real-time quality monitoring or blockchain for traceability. Professionals with certifications in advanced analytics, cybersecurity for supply chain data, or specific industry compliance (e.g., aerospace AS9100, medical ISO 13485) gain a significant competitive edge.
Underserved markets include small to medium-sized enterprises (SMEs) that lack sophisticated quality infrastructure but face increasing regulatory pressure, creating consulting or fractional management opportunities. Additionally, sectors undergoing rapid innovation, such as electric vehicles or renewable energy, consistently seek skilled quality managers to establish robust supplier ecosystems from the ground up.
Strategic career moves involve upskilling in data science, artificial intelligence applications, or advanced negotiation tactics. Investing in these areas now positions professionals for leadership roles in future-proof supply chains, ensuring long-term career resilience and growth.
Current Market Trends
Hiring for Supplier Quality Managers in 2025 shows steady demand, particularly in manufacturing, automotive, and aerospace sectors focusing on supply chain resilience and regulatory compliance. Companies prioritize candidates who can implement robust quality management systems and mitigate risks across complex global networks. Industry shifts towards localized supply chains and enhanced scrutiny on ethical sourcing drive demand for skilled managers.
The integration of AI and automation tools significantly impacts this profession. AI-powered platforms for supplier auditing, predictive quality analytics, and performance monitoring become standard, requiring managers to adapt to data-driven decision-making. This technology reduces the need for manual oversight but elevates the importance of strategic vendor relationship management and root cause analysis expertise.
Economic conditions, while showing signs of stabilization, continue to influence hiring. Some companies maintain leaner operational models post-2023, leading to fewer new permanent positions and more demand for consultants or project-based roles. Employer requirements increasingly emphasize a blend of technical quality skills, such as Lean Six Sigma, with strong communication, negotiation, and digital literacy.
Salary trends for experienced Supplier Quality Managers remain stable, with slight increases for those demonstrating proficiency in advanced analytics or niche industry standards. However, market saturation at entry and mid-levels means more competition for less experienced candidates. Geographically, areas with strong manufacturing bases, like the Midwest and Southeast US, show consistent demand, while remote opportunities are highly competitive due to increased applicant pools.
Emerging Specializations
The role of a Supplier Quality Manager is evolving rapidly, driven by advancements in digital technologies, global supply chain complexities, and increasing demands for sustainability and resilience. Understanding these shifts helps professionals identify future-oriented career paths. Early positioning in emerging areas like AI-driven quality assurance or circular economy principles can significantly enhance career prospects and compensation in 2025 and beyond.
Specializing in these cutting-edge fields often leads to premium compensation and accelerated career growth compared to established specializations. While traditional supplier quality management remains crucial, integrating new technological and strategic competencies creates distinct advantages. These emerging areas typically take 3-5 years to become mainstream and generate a significant volume of job opportunities, making early adoption a strategic advantage.
Pursuing emerging specializations involves a balance of risk and reward. While the demand is high and competition is lower initially, the exact trajectory of these fields can vary. Professionals who proactively develop skills in these nascent areas are better equipped to lead future initiatives, mitigate supply chain risks, and drive innovation within their organizations.
AI-Driven Predictive Quality Manager
This specialization focuses on integrating AI and machine learning tools to predict and prevent supplier quality issues. It involves developing algorithms to analyze vast datasets from supplier performance, IoT sensors, and production lines, identifying patterns that indicate potential quality deviations before they occur. This proactive approach minimizes defects, reduces waste, and improves overall supply chain efficiency by shifting from reactive problem-solving to predictive intelligence.
Sustainable Supply Chain Quality Specialist
This area focuses on ensuring suppliers adhere to environmental, social, and governance (ESG) standards throughout their operations. It involves auditing supplier practices for sustainable sourcing, labor ethics, carbon footprint reduction, and waste management. Supplier Quality Managers in this role drive the adoption of circular economy principles, ensuring materials are reused and recycled, and promoting ethical labor practices across the supply chain, which is increasingly vital for corporate reputation and regulatory compliance.
Cyber-Physical Supply Chain Security Manager
This specialization addresses the critical need for robust cybersecurity measures within the supplier ecosystem. It involves assessing suppliers' cybersecurity postures, ensuring data integrity, protecting intellectual property, and preventing cyber-physical attacks that could compromise product quality or operational continuity. As supply chains become more interconnected, managing cyber risks from third-party vendors is paramount to maintaining product reliability and customer trust.
Digital Supply Network Quality Integrator
This role focuses on optimizing supplier relationships and performance through advanced digital platforms and real-time data. It involves implementing and managing digital twins of supplier processes, leveraging blockchain for traceability, and using IoT devices for continuous monitoring of quality metrics. The goal is to create a transparent, interconnected, and highly responsive supplier network, enhancing collaboration and enabling immediate identification and resolution of quality issues.
Supply Chain Resilience & Risk Quality Manager
This specialization focuses on building highly resilient supplier networks capable of withstanding global disruptions, from pandemics to geopolitical events. It involves developing strategies for multi-sourcing, regionalization, and dynamic risk assessment to ensure continuous supply of critical components while maintaining quality standards. Supplier Quality Managers in this area design and implement contingency plans, evaluate supplier financial health, and establish robust communication protocols to navigate unforeseen challenges.
Pros & Cons of Being a Supplier Quality Manager
Understanding both the advantages and challenges of a career is crucial before making a commitment. A Supplier Quality Manager role, for instance, offers unique experiences that can vary greatly based on the company's industry, its supply chain complexity, and the specific products involved. What one person finds rewarding, another might find challenging, largely depending on their personality, values, and career aspirations.
The career journey also impacts perception; an early career professional might focus on learning opportunities, while a senior manager might prioritize strategic impact. This assessment provides an honest, balanced view of the realistic benefits and genuine difficulties associated with being a Supplier Quality Manager, helping to set appropriate expectations.
Pros
Plays a critical role in ensuring product quality and customer satisfaction, directly impacting the company's reputation and bottom line by preventing defects.
Offers opportunities for global travel and exposure to diverse manufacturing processes and cultures, as suppliers are often located internationally.
Involves a blend of technical problem-solving, interpersonal negotiation, and strategic planning, providing a varied and intellectually stimulating work environment.
Develops strong project management and analytical skills through root cause analysis, corrective action implementation, and supplier performance monitoring.
Provides significant career advancement opportunities into senior quality roles, supply chain management, or operational leadership positions due to the cross-functional nature of the role.
Builds a wide professional network by interacting with various internal departments (engineering, procurement, manufacturing) and external supplier organizations.
Offers a sense of accomplishment by driving continuous improvement initiatives and seeing tangible results in supplier performance and product reliability.
Cons
Frequent travel to supplier sites is often required, which can lead to significant time away from home and disrupt personal life, especially for global supply chains.
Managing difficult supplier relationships and resolving quality issues can be highly stressful and require significant negotiation skills, as conflicts may arise frequently.
Requires deep technical knowledge across various manufacturing processes and quality standards, demanding continuous learning and adaptation to new technologies and industry regulations.
Accountability for supplier performance can be high, meaning a critical quality failure from a supplier directly reflects on the Supplier Quality Manager, leading to pressure and scrutiny.
Work often involves reactive problem-solving for unexpected quality defects, which can disrupt planned activities and require immediate attention and long hours to resolve.
Balancing cost pressures with quality requirements is a constant challenge, as suppliers may resist investments in quality improvements if they increase their costs, leading to difficult trade-offs.
Limited direct control over supplier operations means influencing change often relies on persuasion, audits, and contractual agreements rather than direct authority, which can be frustrating.
Frequently Asked Questions
Supplier Quality Managers face unique challenges balancing technical expertise with strong interpersonal skills to ensure supplier compliance and performance. This section addresses common questions about entering this role, from required qualifications and managing complex global supply chains to navigating difficult supplier relationships and career growth.
What are the essential educational and experience requirements to become a Supplier Quality Manager?
Most Supplier Quality Manager roles require a bachelor's degree in engineering, supply chain management, or a related technical field. Many employers also prefer or require certifications like ASQ Certified Quality Engineer (CQE) or Certified Quality Auditor (CQA). Practical experience in manufacturing, quality control, or procurement is crucial, often spanning 3-7 years in a relevant industry.
How long does it typically take to become a Supplier Quality Manager if I'm starting my career or making a transition?
Transitioning into this role often takes 2-4 years of dedicated experience after your initial degree, assuming you start in a related quality or engineering position. If you are shifting from a non-technical background, obtaining relevant certifications and gaining hands-on experience through entry-level quality assurance or manufacturing roles can extend this timeline to 4-6 years. Building a strong network in the industry helps identify opportunities.
What are the typical salary expectations for a Supplier Quality Manager at different experience levels?
Salaries for Supplier Quality Managers vary significantly based on industry, company size, location, and experience. Entry-level positions might start around $70,000-$90,000 annually. Experienced professionals in large corporations or high-tech industries can earn $100,000-$150,000 or more, especially with advanced certifications or specialized product knowledge. Performance bonuses and benefits are often part of the total compensation package.
What is the typical work-life balance like for a Supplier Quality Manager, considering travel and demands?
The work-life balance for a Supplier Quality Manager can vary, often depending on the company's global footprint and specific industry. It frequently involves domestic and international travel for supplier audits, performance reviews, and issue resolution, which can impact personal time. During critical projects or supplier issues, workload can be intense, but generally, it offers a manageable balance once established processes are in place. Remote work flexibility depends heavily on the need for on-site supplier visits.
What is the job security and future outlook for the Supplier Quality Manager role?
The job market for Supplier Quality Managers remains stable and generally strong, driven by increasing global supply chain complexities and regulatory demands. Companies continuously seek to mitigate risks and ensure product quality, making this role essential. While economic downturns can impact hiring in some sectors, the fundamental need for robust supplier quality management ensures consistent demand across manufacturing, automotive, aerospace, and medical device industries.
What are the typical career advancement opportunities for a Supplier Quality Manager?
Career growth paths for Supplier Quality Managers are diverse. You can advance to Senior Supplier Quality Manager, Director of Quality, or even Vice President of Supply Chain or Operations. Many also transition into roles like Supply Chain Consultant, Procurement Manager, or specialize in areas like Lean Manufacturing or Six Sigma. Continuous learning, leadership development, and cross-functional project experience are key to upward mobility.
What are the most common challenges and difficult situations a Supplier Quality Manager faces?
A significant challenge is managing diverse suppliers across different cultures and regulatory environments, requiring strong communication and negotiation skills. You will often balance cost pressures with quality standards and deal with non-compliant suppliers, demanding diplomacy and firm corrective action planning. The ability to influence without direct authority and resolve complex technical issues remotely are also common hurdles.
Can a Supplier Quality Manager role realistically be performed remotely, or is significant travel always required?
While some administrative tasks can be done remotely, the Supplier Quality Manager role often requires significant on-site presence at supplier facilities for audits, inspections, and problem-solving. Travel can range from 25% to 75%, depending on the company's supply chain geography. Therefore, it is rarely a fully remote position, though hybrid models with reduced office time are becoming more common for non-travel days.
Related Careers
Explore similar roles that might align with your interests and skills:
Quality Assurance Manager
A growing field with similar skill requirements and career progression opportunities.
Explore career guideQuality Control Manager
A growing field with similar skill requirements and career progression opportunities.
Explore career guideQuality Manager
A growing field with similar skill requirements and career progression opportunities.
Explore career guideQuality Supervisor
A growing field with similar skill requirements and career progression opportunities.
Explore career guideSupply Chain Manager
A growing field with similar skill requirements and career progression opportunities.
Explore career guideAssess your Supplier Quality Manager readiness
Understanding where you stand today is the first step toward your career goals. Our Career Coach helps identify skill gaps and create personalized plans.
Skills Gap Analysis
Get a detailed assessment of your current skills versus Supplier Quality Manager requirements. Our AI Career Coach identifies specific areas for improvement with personalized recommendations.
See your skills gapCareer Readiness Assessment
Evaluate your overall readiness for Supplier Quality Manager roles with our AI Career Coach. Receive personalized recommendations for education, projects, and experience to boost your competitiveness.
Assess your readinessLand your dream job with Himalayas Plus
Upgrade to unlock Himalayas' premium features and turbocharge your job search.
Himalayas
Himalayas Plus
Himalayas is trusted by hundreds of thousands of job seekers every month
Get started for freeNo credit card required
Find your dream job
Sign up now and join over 100,000 remote workers who receive personalized job alerts, curated job matches, and more for free!
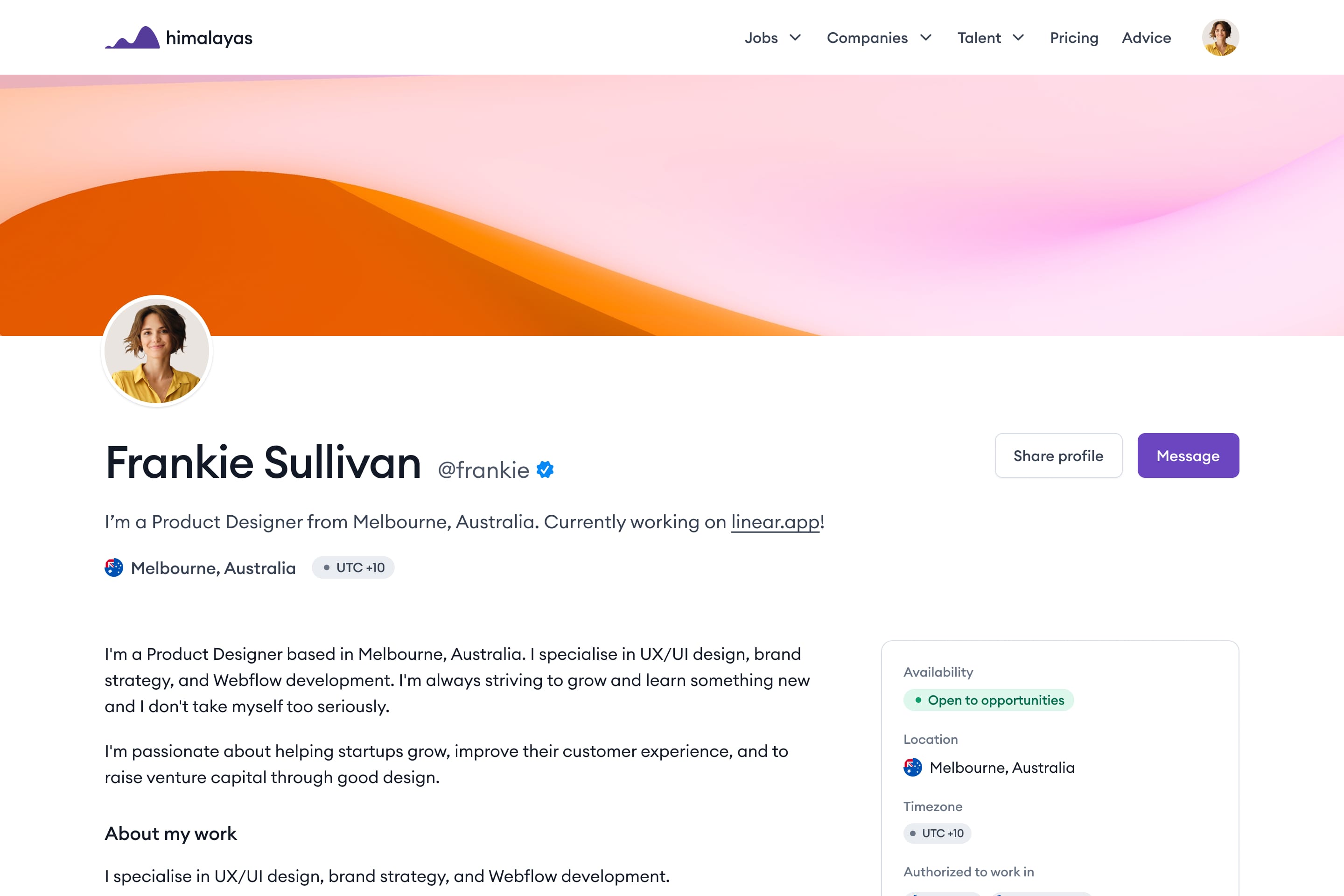