Complete Quality Supervisor Career Guide
Quality supervisors are the frontline leaders ensuring products and services meet rigorous standards, making them indispensable in manufacturing and service industries. They bridge the gap between quality strategy and daily execution, meticulously overseeing processes and teams to prevent defects and drive continuous improvement. This role offers a direct impact on customer satisfaction and brand reputation, providing a clear path for those with an eye for detail and strong leadership skills.
Key Facts & Statistics
Median Salary
$78,570 USD
(U.S. national median, BLS, May 2023)
Range: $50k - $100k+ USD, varying by experience, industry, and location
Growth Outlook
3%
as fast as average (BLS, 2022-2032)
Annual Openings
≈170,000
openings annually (BLS, 2022-2032)
Top Industries
Typical Education
High school diploma or equivalent, with significant work experience in production or operations; some roles prefer an Associate's or Bachelor's degree in a related field, or relevant certifications (e.g., Six Sigma, Lean).
What is a Quality Supervisor?
A Quality Supervisor leads and manages the quality control processes within a manufacturing or production environment. This professional ensures that products, services, or processes consistently meet predefined quality standards, regulatory requirements, and customer expectations. They are critical in maintaining brand reputation and preventing defects before they reach the customer.
Unlike a Quality Inspector who performs specific tests, or a Quality Engineer who designs quality systems, a Quality Supervisor directly oversees the team of inspectors and technicians, implementing the quality plans and reacting to real-time quality challenges on the production floor. They bridge the gap between quality strategy and operational execution, ensuring daily adherence to quality protocols and leading immediate problem-solving efforts related to product quality.
What does a Quality Supervisor do?
Key Responsibilities
- Oversee daily quality control operations to ensure products meet established standards and specifications.
- Train and mentor quality control inspectors on testing procedures, documentation, and compliance protocols.
- Investigate and resolve quality issues, non-conformances, and customer complaints by implementing corrective actions.
- Conduct regular audits of production processes and finished goods to identify areas for improvement and ensure adherence to quality management systems.
- Analyze quality data and metrics to identify trends, report on performance, and recommend process enhancements.
- Collaborate with production, engineering, and supply chain teams to integrate quality requirements throughout the product lifecycle.
- Maintain accurate quality records and documentation, ensuring compliance with industry regulations and internal policies for traceability and audits.
Work Environment
A Quality Supervisor typically works in a manufacturing or production facility, which can range from cleanroom environments to more industrial settings. The role often involves a mix of office work for data analysis and reporting, and significant time on the production floor overseeing operations, conducting inspections, and interacting with staff. Collaboration is constant, working closely with production managers, engineers, and frontline staff. The pace can be fast and dynamic, especially when addressing immediate quality issues or during peak production periods. While primarily on-site, some roles might involve occasional travel to supplier sites or customer locations for quality assurance meetings. The work environment demands a keen eye for detail and a proactive approach to problem-solving.
Tools & Technologies
Quality Supervisors frequently use a variety of tools and technologies to manage and monitor quality. They utilize Statistical Process Control (SPC) software like Minitab or JMP for data analysis and trend identification. Enterprise Resource Planning (ERP) systems such as SAP or Oracle are crucial for tracking production, inventory, and quality data across the organization. They also work with Quality Management Systems (QMS) software like MasterControl or Veeva for document control, non-conformance management, and audit trails. Inspection equipment, including calipers, micrometers, CMMs (Coordinate Measuring Machines), and specialized testing apparatus, are part of their daily routine. Furthermore, they use standard office productivity suites like Microsoft Office (Excel, Word, PowerPoint) for reporting and presentations.
Quality Supervisor Skills & Qualifications
A Quality Supervisor orchestrates the daily operations of quality control, ensuring products or services meet established standards. This role requires a blend of hands-on technical knowledge and strong leadership capabilities. Qualification requirements for this position vary significantly based on the industry, company size, and the complexity of the products or processes involved.
For instance, a Quality Supervisor in manufacturing might need a strong background in lean principles and statistical process control, while one in software development would focus on testing methodologies and agile frameworks. Entry-level supervisory roles often prioritize practical experience and foundational certifications, whereas senior positions demand a deeper understanding of quality management systems and strategic implementation. Formal education, especially a bachelor's degree, provides a strong theoretical base and is often a prerequisite for advancement, but extensive practical experience coupled with relevant certifications can sometimes serve as an alternative pathway.
The skill landscape for Quality Supervisors is evolving, with increasing emphasis on data analytics, automation, and digital quality management tools. Continuous learning through industry-specific certifications, such as those from ASQ (American Society for Quality), significantly enhances a candidate's profile. These certifications validate specialized knowledge and commitment to the field. Understanding the nuances between quality assurance, quality control, and continuous improvement is crucial for this role, as the supervisor often bridges these functions to drive overall quality excellence.
Education Requirements
Technical Skills
- Quality Management Systems (QMS) principles (e.g., ISO 9001, IATF 16949, AS9100) and auditing
- Statistical Process Control (SPC) and data analysis using tools like Minitab or JMP
- Root Cause Analysis methodologies (e.g., 5 Whys, Fishbone diagrams, FMEA)
- Lean Manufacturing and Six Sigma principles (e.g., Kaizen, 5S, Value Stream Mapping)
- Inspection and testing techniques, including proficiency with measurement tools (e.g., calipers, micrometers, CMM)
- Non-conformance management and Corrective and Preventive Actions (CAPA) processes
- Quality control documentation and reporting (e.g., control plans, inspection reports, quality metrics)
- Proficiency with Quality Management Software (QMS) and Enterprise Resource Planning (ERP) systems
- Blueprint reading and Geometric Dimensioning and Tolerancing (GD&T)
- Process validation and qualification (IQ, OQ, PQ) in regulated industries
- Supplier quality management and incoming inspection procedures
- Basic understanding of automation and industry 4.0 concepts in quality
Soft Skills
- Leadership and Team Motivation: Inspiring and guiding quality control teams to achieve high performance and maintain morale, even under pressure.
- Problem-Solving and Root Cause Analysis: Identifying the true causes of quality issues and developing effective, sustainable solutions, not just addressing symptoms.
- Decision-Making: Making timely and informed decisions regarding product acceptance, process adjustments, and corrective actions based on data and established standards.
- Communication and Interpersonal Skills: Effectively conveying quality standards, feedback, and improvement initiatives to team members, management, and other departments.
- Attention to Detail: Meticulously reviewing processes, products, and documentation to ensure compliance with stringent quality specifications and identify subtle deviations.
- Adaptability and Flexibility: Adjusting quickly to changes in production schedules, quality standards, or unexpected issues while maintaining quality oversight.
- Conflict Resolution: Mediating disagreements within the team or with other departments regarding quality concerns, fostering a collaborative environment.
- Mentorship and Coaching: Developing team members' skills and knowledge in quality control techniques and best practices, fostering continuous improvement.
How to Become a Quality Supervisor
Entering the Quality Supervisor field offers multiple pathways, ranging from traditional academic routes to hands-on experience and certifications. While a bachelor's degree in engineering, quality management, or a related technical field is often preferred, many successful Quality Supervisors transition from roles like Quality Inspector, Production Supervisor, or even senior-level manufacturing positions. This field values practical problem-solving skills and leadership abilities as much as formal qualifications.
The timeline to become a Quality Supervisor varies significantly based on your starting point. Someone with a relevant degree and a few years of experience in a quality assurance or manufacturing role might transition within 1-2 years. For individuals starting with no direct experience, building a foundation in manufacturing or quality control, then pursuing certifications, could take 3-5 years. Geographic location also influences opportunities; larger industrial or manufacturing hubs typically have more openings than smaller markets.
Common misconceptions include believing that only engineers can become Quality Supervisors or that the role is purely about inspection. In reality, it involves significant leadership, process improvement, and cross-functional collaboration. Networking within manufacturing and quality associations, seeking mentorship from experienced professionals, and focusing on continuous improvement methodologies are crucial for success in this evolving hiring landscape.
Step 1
Step 2
Step 3
Step 4
Step 5
Education & Training Needed to Become a Quality Supervisor
Becoming a Quality Supervisor involves a blend of formal education and practical experience, with diverse pathways available. Traditional 4-year bachelor's degrees in engineering, business administration, or quality management provide a strong theoretical foundation, typically costing $40,000 to $100,000+ and requiring four years. These programs offer a deep understanding of quality principles, statistical process control, and leadership.
Alternatively, many professionals enter this role through associate degrees or vocational training combined with significant on-the-job experience. Industry-specific certifications, such as those from the American Society for Quality (ASQ), are highly valued and can significantly enhance a candidate's profile. These certifications, like the Certified Quality Supervisor (CQS) or Certified Quality Engineer (CQE), typically cost $300 to $1,500 and require 6-12 months of self-study or focused training. Employers often prefer candidates with a mix of academic credentials and practical, certified expertise.
Continuous learning remains crucial for Quality Supervisors. This includes staying updated on new quality standards (e.g., ISO 9001 revisions), lean manufacturing principles, and Six Sigma methodologies. Online courses and professional development workshops offer flexible learning options, ranging from free resources to programs costing several thousand dollars, with completion times from a few weeks to several months. The specific educational needs for a Quality Supervisor vary by industry, company size, and the complexity of the quality systems involved, emphasizing the need for a tailored educational investment.
Quality Supervisor Salary & Outlook
Compensation for a Quality Supervisor varies significantly based on several factors beyond just base salary. Geographic location plays a crucial role, with higher cost-of-living areas or regions with a strong manufacturing or pharmaceutical presence often commanding higher wages. For instance, supervisors in California or the Northeast generally earn more than those in the Midwest or Southern states, reflecting local market demand and economic conditions.
Experience, specialized industry knowledge (e.g., medical devices, automotive, food safety), and specific skill sets like Lean Six Sigma certifications or advanced statistical process control expertise also dramatically impact earning potential. A supervisor with a deep understanding of complex regulatory frameworks or a proven track record in process optimization can command a premium.
Total compensation packages extend well beyond the base salary. These often include performance-based bonuses, annual incentives, and comprehensive benefits such such as health insurance, paid time off, and retirement contributions like 401(k) matching. Some roles, particularly in larger corporations, may offer profit-sharing or even stock options. Companies investing in professional development, such as certifications or advanced training, further enhance the overall value of the compensation package.
Industry-specific trends also influence compensation. Highly regulated industries like pharmaceuticals or aerospace typically offer more competitive salaries due to the critical nature of quality assurance. Remote work, while less common for this hands-on role, can impact salary ranges, with some companies adjusting pay based on the employee's location. While figures are USD-centric, international markets vary widely, often tied to local economic strength and industry maturity.
Salary by Experience Level
Level | US Median | US Average |
---|---|---|
Quality Coordinator | $52k USD | $55k USD |
Quality Supervisor | $72k USD | $75k USD |
Senior Quality Supervisor | $88k USD | $90k USD |
Quality Manager | $110k USD | $115k USD |
Senior Quality Manager | $135k USD | $140k USD |
Director of Quality Assurance | $168k USD | $175k USD |
VP of Quality | $210k USD | $220k USD |
Market Commentary
The job market for Quality Supervisors remains stable with a steady demand, driven by industries prioritizing product integrity, regulatory compliance, and process efficiency. The Bureau of Labor Statistics projects a modest but consistent growth for related roles, as companies continue to focus on reducing defects, improving customer satisfaction, and adhering to increasingly stringent global standards. Demand is particularly strong in manufacturing, healthcare, and technology sectors, where quality directly impacts safety, reliability, and brand reputation.
Current trends show an increasing emphasis on data analytics, automation, and AI within quality assurance. Quality Supervisors are now expected to not only manage teams and processes but also interpret complex data, implement predictive quality models, and oversee automated inspection systems. This shift creates emerging opportunities for those with strong analytical skills and a willingness to embrace new technologies.
The supply of qualified candidates varies by industry and region. While general quality experience is common, specialized knowledge in areas like ISO 9001, AS9100, or cGMP standards can lead to higher demand. The role is generally recession-resistant as quality control remains essential even during economic downturns, ensuring product consistency and compliance. Geographic hotspots for Quality Supervisors include industrial hubs in states like Michigan, Texas, California, and North Carolina, where manufacturing and R&D activities are concentrated.
Future-proofing this career involves continuous learning in areas such as advanced statistical software, machine learning applications in quality, and evolving regulatory landscapes. As manufacturing moves towards Industry 4.0, the Quality Supervisor's role will evolve from reactive problem-solving to proactive, data-driven prevention, ensuring long-term career viability.
Quality Supervisor Career Path
Career progression for a Quality Supervisor typically involves a blend of technical expertise, process optimization, and leadership development. Professionals in this field can advance through individual contributor (IC) tracks, focusing on specialized quality systems and audits, or transition into management roles, overseeing teams and broader organizational quality initiatives. The path often begins with hands-on quality control and coordination, gradually moving towards strategic planning and systemic improvements.
Advancement speed depends on several factors, including individual performance, the complexity of the manufacturing or service environment, and the company's size and industry. Smaller companies might offer quicker progression to broader roles, while larger corporations provide more specialized, deeper dives into specific quality disciplines. Lateral moves might involve transitioning between different product lines or quality specializations like supplier quality, process quality, or audit management. Networking within professional quality associations and pursuing relevant certifications, such as ASQ certifications (e.g., CQE, CMQ/OE), significantly accelerate career growth and enhance industry reputation.
Continuous learning in areas like Lean Manufacturing, Six Sigma, and ISO standards is crucial. Career paths can also vary by company type; a startup might require a Quality Supervisor to build processes from scratch, while a large corporation might focus on optimizing existing, complex systems. Common career pivots include moving into operations management, regulatory affairs, or continuous improvement roles, leveraging a deep understanding of process and system integrity.
Quality Coordinator
0-2 yearsKey Focus Areas
Quality Supervisor
2-4 yearsKey Focus Areas
Senior Quality Supervisor
4-7 yearsKey Focus Areas
Quality Manager
7-10 yearsKey Focus Areas
Senior Quality Manager
10-15 yearsKey Focus Areas
Director of Quality Assurance
15-20 yearsKey Focus Areas
VP of Quality
20+ yearsKey Focus Areas
Quality Coordinator
0-2 yearsExecutes daily quality checks, collects data, and maintains quality records. Assists in preparing for audits and ensures adherence to established quality procedures. Identifies and reports non-conformances, often escalating issues to higher-level quality personnel. Works under direct supervision, focusing on tactical implementation of quality plans.
Key Focus Areas
Develop foundational knowledge of quality control tools, data collection methods, and documentation standards. Focus on mastering specific quality procedures and understanding product/service specifications. Build strong communication skills for interacting with production teams and identifying non-conformances effectively. Start learning about root cause analysis.
Quality Supervisor
2-4 yearsOversees a team of quality technicians or inspectors, ensuring adherence to quality standards on a specific shift or production line. Troubleshoots immediate quality issues, implements corrective actions, and provides training to team members. Monitors key quality metrics and reports performance to management. Makes operational decisions regarding quality control points.
Key Focus Areas
Enhance problem-solving abilities, particularly in root cause analysis and corrective/preventive actions (CAPA). Develop basic leadership skills, including delegation and performance monitoring for small teams or shifts. Understand statistical process control (SPC) and its application. Focus on process improvement initiatives within their supervised area.
Senior Quality Supervisor
4-7 yearsLeads complex quality projects and initiatives, often across multiple shifts or departments. Develops and refines quality control plans and inspection procedures. Provides expert guidance on root cause analysis and complex CAPA implementation. Acts as a key liaison during internal and external audits, driving compliance efforts.
Key Focus Areas
Master advanced quality methodologies like Six Sigma (Green Belt certification beneficial) and Lean principles. Develop stronger project management skills for leading continuous improvement initiatives. Focus on mentoring junior quality staff and contributing to the development of quality system documentation. Improve analytical skills for trend analysis.
Quality Manager
7-10 yearsManages a team of quality supervisors and specialists, overseeing all quality assurance and control activities for a significant operational area or product line. Develops, implements, and maintains the quality management system. Responsible for achieving departmental quality targets and ensuring regulatory compliance. Represents the quality function in cross-functional strategic meetings.
Key Focus Areas
Cultivate strategic thinking, translating quality objectives into actionable plans. Develop strong leadership and team management skills, including hiring, performance reviews, and talent development. Focus on budget management for the quality department. Gain proficiency in quality management systems (e.g., ISO 9001) implementation and maintenance.
Senior Quality Manager
10-15 yearsDirects multiple quality teams or a broad quality function across several sites or major product lines. Drives continuous improvement strategies and champions a culture of quality throughout the organization. Develops long-term quality roadmaps and allocates resources. Plays a critical role in strategic decision-making impacting product quality and customer satisfaction.
Key Focus Areas
Refine strategic planning and execution skills, aligning quality initiatives with overall business goals. Develop advanced change management capabilities for implementing large-scale quality transformations. Focus on stakeholder management across diverse departments and external entities. Pursue certifications like ASQ Certified Manager of Quality/Organizational Excellence (CMQ/OE).
Director of Quality Assurance
15-20 yearsSets the overall quality vision and strategy for the entire organization, ensuring alignment with corporate objectives. Oversees all quality assurance and regulatory compliance programs across all business units. Leads the quality leadership team and acts as the primary interface with executive leadership on quality performance and risks. Manages the overall quality budget and resource allocation.
Key Focus Areas
Develop enterprise-level strategic leadership, focusing on integrating quality into the core business strategy. Cultivate executive presence and communication skills for board-level presentations. Focus on risk management, regulatory intelligence, and global quality standards. Build a strong external network within the industry and regulatory bodies.
VP of Quality
20+ yearsHolds ultimate accountability for the organization's quality performance, compliance, and culture. Sits on the executive leadership team, influencing overall business strategy and investment decisions related to quality. Drives innovation in quality processes and technologies. Ensures the company maintains a world-class quality reputation and meets all global regulatory requirements. Often responsible for significant P&L impact through quality initiatives.
Key Focus Areas
Master organizational leadership, innovation, and change leadership at the highest level. Focus on global quality trends, emerging technologies, and their impact on the business. Cultivate a strong understanding of market dynamics, competitive landscapes, and customer expectations to drive quality as a competitive advantage. Influence industry standards and best practices.
Job Application Toolkit
Ace your application with our purpose-built resources:
Quality Supervisor Resume Examples
Proven layouts and keywords hiring managers scan for.
View examplesQuality Supervisor Cover Letter Examples
Personalizable templates that showcase your impact.
View examplesTop Quality Supervisor Interview Questions
Practice with the questions asked most often.
View examplesQuality Supervisor Job Description Template
Ready-to-use JD for recruiters and hiring teams.
View examplesGlobal Quality Supervisor Opportunities
Quality Supervisors oversee quality control processes and teams across diverse industries globally. This role translates well internationally, given universal needs for product and process integrity. Global demand for skilled quality professionals remains high, particularly in manufacturing and technology sectors, driven by stricter international standards and consumer expectations. Cultural differences impact quality perceptions and regulatory frameworks, requiring adaptability. International certifications like ISO 9001 are widely recognized, enhancing global mobility for these professionals. Professionals seek international opportunities for career advancement and exposure to varied operational excellence models.
Global Salaries
Salaries for Quality Supervisors vary significantly by region and industry. In North America, particularly the US, annual salaries typically range from $65,000 to $95,000 USD. Canadian supervisors can expect $60,000 to $85,000 CAD (approx. $44,000-$63,000 USD). These figures often include comprehensive benefits packages, health insurance, and retirement plans, which are standard.
European salaries show considerable variation. In Germany, a Quality Supervisor might earn €50,000 to €75,000 (approx. $54,000-$81,000 USD), while in the UK, salaries range from £35,000 to £55,000 (approx. $44,000-$69,000 USD). Southern European countries like Spain offer lower ranges, often €30,000 to €45,000. Purchasing power parity is crucial; higher European salaries often accompany higher costs of living, especially in major cities.
Asia-Pacific markets present diverse compensation. In Australia, salaries range from $70,000 to $95,000 AUD (approx. $46,000-$63,000 USD). Japan offers ¥5,000,000 to ¥7,500,000 JPY (approx. $32,000-$48,000 USD), often with fewer direct benefits but strong social security. China's salaries are lower at ¥150,000 to ¥250,000 CNY (approx. $21,000-$35,000 USD), but cost of living can be significantly lower outside major hubs. Latin American countries like Mexico typically offer $25,000 to $40,000 USD equivalents. Tax rates and take-home pay differ significantly, impacting net compensation. International experience and specialized certifications can positively influence starting salaries in new countries.
Remote Work
International remote work for Quality Supervisors is limited compared to other roles due to the hands-on nature of manufacturing and physical product inspection. However, some aspects, like documentation, compliance audits, and team management, can be performed remotely. Companies increasingly adopt hybrid models, allowing supervisors to manage remote teams or conduct virtual inspections. Legal and tax implications for international remote work require careful navigation, especially concerning permanent establishment rules and local labor laws.
Time zone differences present challenges for global team collaboration. Digital nomad opportunities for this specific role are uncommon, as most countries with remote work visas target highly mobile tech or creative professionals. Employers with international operations might offer intra-company remote roles, but these are rare for direct quality supervision. Salary expectations for remote roles often align with the employer's country of origin, not the employee's location, impacting geographic arbitrage.
Visa & Immigration
Skilled worker visas are the most common pathway for Quality Supervisors seeking international employment. Countries like Canada, Australia, and Germany have points-based or demand-driven immigration systems that often include quality management roles. Specific requirements for these visas, as of 2025, typically involve demonstrating relevant work experience, often 3-5 years, and holding a bachelor's degree in engineering, quality management, or a related field. Professional licensing is generally not required for Quality Supervisors, but industry-specific certifications like Six Sigma or Lean are highly valued.
Visa application timelines vary, ranging from a few months to over a year, depending on the country and applicant's nationality. English language proficiency tests (IELTS, TOEFL) are often mandatory for English-speaking countries. Some countries, like Germany, require basic proficiency in the local language. Pathways to permanent residency often exist after several years of continuous skilled employment. Intra-company transfers are another common route for those already employed by multinational corporations. Family visas are usually available for spouses and dependent children, allowing them to accompany the primary visa holder.
2025 Market Reality for Quality Supervisors
Understanding current market conditions is paramount for Quality Supervisors navigating their careers. The landscape has evolved rapidly, especially between 2023 and 2025, driven by post-pandemic shifts in supply chains and the accelerating AI revolution.
Broader economic factors, such as inflation and consumer demand fluctuations, directly influence production volumes and, consequently, the need for quality oversight. Market realities also vary significantly: larger corporations often seek supervisors with deep regulatory expertise, while smaller firms might prioritize adaptability and broad skill sets. Geographic regions with strong manufacturing or tech hubs typically offer more opportunities. This analysis provides an honest assessment of these dynamics.
Current Challenges
Quality Supervisors face increased competition, particularly from candidates with advanced automation and data analytics skills. Many organizations now seek supervisors who can also manage AI-driven quality tools, leading to a skill gap for those focused solely on traditional methods. Economic uncertainty prompts leaner team structures, often requiring supervisors to manage larger scopes with fewer resources. Job search timelines can extend, especially for roles demanding specialized industry knowledge or advanced tech proficiency.
Growth Opportunities
Despite challenges, strong demand exists for Quality Supervisors proficient in data-driven quality management and automation. Opportunities are emerging in industries adopting Industry 4.0 principles, such as smart manufacturing, aerospace, and medical devices, where quality is critical and highly integrated with digital systems. Specializations in areas like AI-driven defect detection, predictive maintenance quality, or regulatory compliance for emerging technologies (e.g., gene therapy manufacturing) offer significant advantages.
Professionals can position themselves by acquiring certifications in advanced statistical process control (SPC), Six Sigma Black Belt, or specific quality management software platforms. Demonstrating an ability to integrate AI tools into existing quality processes or to lead digital transformation initiatives within quality departments creates a competitive edge. Underserved markets might include regions with new manufacturing investments or niche industries like sustainable packaging. Strategic career moves involve targeting companies investing heavily in automation and data analytics, as these roles promise long-term stability and growth. Even with market corrections, companies prioritize quality to reduce waste and enhance customer satisfaction, making this a resilient function.
Current Market Trends
Hiring for Quality Supervisors in 2025 shows a nuanced demand. While core manufacturing and production sectors maintain steady need, growth areas include biotech, advanced materials, and software development, where quality assurance integrates deeply with product lifecycle management. The integration of AI and machine learning tools for predictive quality analysis and automated inspection is rapidly reshaping the role, shifting focus from reactive problem-solving to proactive prevention.
Economic conditions influence hiring, with some sectors experiencing cautious expansion while others, like automotive, navigate supply chain shifts. Layoffs in tech, for instance, have redirected talent towards more traditional industries, intensifying competition for supervisory roles. Employers increasingly seek Quality Supervisors who understand data visualization, statistical process control software, and can interpret AI-generated quality insights. Traditional auditing and compliance skills remain essential, but now complement a growing need for technological literacy.
Salary trends for Quality Supervisors vary significantly by industry and region. High-tech manufacturing or medical device companies often offer higher compensation due to regulatory complexities and product criticality. Entry-level supervisory roles face some market saturation, but experienced professionals with a proven track record in process improvement and digital transformation remain in demand. Remote work normalization is less prevalent for this hands-on role; most positions require on-site presence, though some corporate quality management roles might offer hybrid options. Seasonal hiring patterns are less pronounced than in production roles, but year-end budgeting cycles can influence hiring timelines.
Emerging Specializations
The landscape of quality management is undergoing significant transformation, driven by rapid advancements in technology and evolving industry standards. This evolution creates new specialization opportunities for Quality Supervisors, extending beyond traditional roles. Early positioning in these emerging areas can provide a substantial advantage for career advancement from 2025 onwards.
Specializing in cutting-edge fields often leads to premium compensation and accelerated career growth. These roles address critical, unmet needs within organizations, making professionals with these skills highly valuable. While established specializations offer stability, emerging areas offer the chance to shape new practices and become a recognized expert in a nascent field.
Many emerging areas, particularly those linked to AI, automation, and sustainability, are quickly moving from niche concepts to mainstream operational necessities. This transition creates a significant number of job opportunities as companies integrate these technologies and principles into their quality frameworks. Understanding the risk and reward of specializing in these areas involves assessing the pace of technological adoption and the specific needs of various industries.
Professionals who proactively develop skills in these forward-looking specializations will find themselves well-prepared for future leadership roles in quality assurance. This strategic focus ensures relevance and competitiveness in a rapidly changing industrial environment.
AI-Driven Quality Systems Supervisor
Global Supply Chain Quality Supervisor
Sustainable Quality & Compliance Supervisor
Robotics Quality Assurance Lead
Cyber-Physical Quality Supervisor
Pros & Cons of Being a Quality Supervisor
Making informed career decisions requires a clear understanding of both the benefits and challenges of a specific role. The experience of a Quality Supervisor can vary significantly based on company culture, industry sector, and the specific products manufactured. What serves as an advantage for one individual might be a disadvantage for another, depending on personal values, work style preferences, and career aspirations. Furthermore, the nature of pros and cons can evolve at different career stages, from entry-level supervision to more senior quality leadership. This assessment provides an honest, balanced perspective to help set realistic expectations for anyone considering a career as a Quality Supervisor.
Pros
- Quality Supervisors play a critical role in ensuring product reliability and customer satisfaction, providing a strong sense of purpose and contribution to the company's success. This role offers excellent opportunities to develop leadership and team management skills by overseeing quality control inspectors and production line staff. The position provides a deep understanding of manufacturing processes and quality systems, which is highly transferable across various industries. Quality Supervisors gain valuable problem-solving expertise by identifying root causes of defects and implementing corrective and preventive actions. Many industries, from automotive to pharmaceuticals, consistently demand skilled Quality Supervisors, leading to stable job security. The role often involves continuous learning about new quality standards, technologies, and production methods, keeping the work intellectually stimulating. Successful Quality Supervisors can advance into Quality Assurance Management, Process Improvement, or even Operations Management roles within an organization.
- Quality Supervisors play a critical role in ensuring product reliability and customer satisfaction, providing a strong sense of purpose and contribution to the company's success. This role offers excellent opportunities to develop leadership and team management skills by overseeing quality control inspectors and production line staff. The position provides a deep understanding of manufacturing processes and quality systems, which is highly transferable across various industries. Quality Supervisors gain valuable problem-solving expertise by identifying root causes of defects and implementing corrective and preventive actions. Many industries, from automotive to pharmaceuticals, consistently demand skilled Quality Supervisors, leading to stable job security. The role often involves continuous learning about new quality standards, technologies, and production methods, keeping the work intellectually stimulating. Successful Quality Supervisors can advance into Quality Assurance Management, Process Improvement, or even Operations Management roles within an organization.
- Quality Supervisors play a critical role in ensuring product reliability and customer satisfaction, providing a strong sense of purpose and contribution to the company's success. This role offers excellent opportunities to develop leadership and team management skills by overseeing quality control inspectors and production line staff. The position provides a deep understanding of manufacturing processes and quality systems, which is highly transferable across various industries. Quality Supervisors gain valuable problem-solving expertise by identifying root causes of defects and implementing corrective and preventive actions. Many industries, from automotive to pharmaceuticals, consistently demand skilled Quality Supervisors, leading to stable job security. The role often involves continuous learning about new quality standards, technologies, and production methods, keeping the work intellectually stimulating. Successful Quality Supervisors can advance into Quality Assurance Management, Process Improvement, or even Operations Management roles within an organization.
- Quality Supervisors play a critical role in ensuring product reliability and customer satisfaction, providing a strong sense of purpose and contribution to the company's success. This role offers excellent opportunities to develop leadership and team management skills by overseeing quality control inspectors and production line staff. The position provides a deep understanding of manufacturing processes and quality systems, which is highly transferable across various industries. Quality Supervisors gain valuable problem-solving expertise by identifying root causes of defects and implementing corrective and preventive actions. Many industries, from automotive to pharmaceuticals, consistently demand skilled Quality Supervisors, leading to stable job security. The role often involves continuous learning about new quality standards, technologies, and production methods, keeping the work intellectually stimulating. Successful Quality Supervisors can advance into Quality Assurance Management, Process Improvement, or even Operations Management roles within an organization.
- Quality Supervisors play a critical role in ensuring product reliability and customer satisfaction, providing a strong sense of purpose and contribution to the company's success. This role offers excellent opportunities to develop leadership and team management skills by overseeing quality control inspectors and production line staff. The position provides a deep understanding of manufacturing processes and quality systems, which is highly transferable across various industries. Quality Supervisors gain valuable problem-solving expertise by identifying root causes of defects and implementing corrective and preventive actions. Many industries, from automotive to pharmaceuticals, consistently demand skilled Quality Supervisors, leading to stable job security. The role often involves continuous learning about new quality standards, technologies, and production methods, keeping the work intellectually stimulating. Successful Quality Supervisors can advance into Quality Assurance Management, Process Improvement, or even Operations Management roles within an organization.
- Quality Supervisors play a critical role in ensuring product reliability and customer satisfaction, providing a strong sense of purpose and contribution to the company's success. This role offers excellent opportunities to develop leadership and team management skills by overseeing quality control inspectors and production line staff. The position provides a deep understanding of manufacturing processes and quality systems, which is highly transferable across various industries. Quality Supervisors gain valuable problem-solving expertise by identifying root causes of defects and implementing corrective and preventive actions. Many industries, from automotive to pharmaceuticals, consistently demand skilled Quality Supervisors, leading to stable job security. The role often involves continuous learning about new quality standards, technologies, and production methods, keeping the work intellectually stimulating. Successful Quality Supervisors can advance into Quality Assurance Management, Process Improvement, or even Operations Management roles within an organization.
- Quality Supervisors play a critical role in ensuring product reliability and customer satisfaction, providing a strong sense of purpose and contribution to the company's success. This role offers excellent opportunities to develop leadership and team management skills by overseeing quality control inspectors and production line staff. The position provides a deep understanding of manufacturing processes and quality systems, which is highly transferable across various industries. Quality Supervisors gain valuable problem-solving expertise by identifying root causes of defects and implementing corrective and preventive actions. Many industries, from automotive to pharmaceuticals, consistently demand skilled Quality Supervisors, leading to stable job security. The role often involves continuous learning about new quality standards, technologies, and production methods, keeping the work intellectually stimulating. Successful Quality Supervisors can advance into Quality Assurance Management, Process Improvement, or even Operations Management roles within an organization.
Cons
- Quality Supervisors often face high pressure to meet production targets while maintaining strict quality standards, leading to stress when balancing speed versus precision. They frequently deal with resistance from production teams who may view quality checks as hindrances to efficiency or blame quality issues on the supervision. Investigating defects and implementing corrective actions can be time-consuming and require meticulous documentation, often extending beyond regular working hours. The role demands constant vigilance and attention to detail, which can be mentally fatiguing over long shifts, especially when monitoring complex processes. Career progression beyond a Quality Supervisor role may be limited without further education or transitioning into broader management or specialized engineering positions. They are often the first point of contact for customer complaints related to product quality, requiring strong problem-solving and communication skills under pressure. Regular exposure to manufacturing environments can involve noise, dust, and other industrial hazards, depending on the specific industry and facility.
- Quality Supervisors often face high pressure to meet production targets while maintaining strict quality standards, leading to stress when balancing speed versus precision. They frequently deal with resistance from production teams who may view quality checks as hindrances to efficiency or blame quality issues on the supervision. Investigating defects and implementing corrective actions can be time-consuming and require meticulous documentation, often extending beyond regular working hours. The role demands constant vigilance and attention to detail, which can be mentally fatiguing over long shifts, especially when monitoring complex processes. Career progression beyond a Quality Supervisor role may be limited without further education or transitioning into broader management or specialized engineering positions. They are often the first point of contact for customer complaints related to product quality, requiring strong problem-solving and communication skills under pressure. Regular exposure to manufacturing environments can involve noise, dust, and other industrial hazards, depending on the specific industry and facility.
- Quality Supervisors often face high pressure to meet production targets while maintaining strict quality standards, leading to stress when balancing speed versus precision. They frequently deal with resistance from production teams who may view quality checks as hindrances to efficiency or blame quality issues on the supervision. Investigating defects and implementing corrective actions can be time-consuming and require meticulous documentation, often extending beyond regular working hours. The role demands constant vigilance and attention to detail, which can be mentally fatiguing over long shifts, especially when monitoring complex processes. Career progression beyond a Quality Supervisor role may be limited without further education or transitioning into broader management or specialized engineering positions. They are often the first point of contact for customer complaints related to product quality, requiring strong problem-solving and communication skills under pressure. Regular exposure to manufacturing environments can involve noise, dust, and other industrial hazards, depending on the specific industry and facility.
- Quality Supervisors often face high pressure to meet production targets while maintaining strict quality standards, leading to stress when balancing speed versus precision. They frequently deal with resistance from production teams who may view quality checks as hindrances to efficiency or blame quality issues on the supervision. Investigating defects and implementing corrective actions can be time-consuming and require meticulous documentation, often extending beyond regular working hours. The role demands constant vigilance and attention to detail, which can be mentally fatiguing over long shifts, especially when monitoring complex processes. Career progression beyond a Quality Supervisor role may be limited without further education or transitioning into broader management or specialized engineering positions. They are often the first point of contact for customer complaints related to product quality, requiring strong problem-solving and communication skills under pressure. Regular exposure to manufacturing environments can involve noise, dust, and other industrial hazards, depending on the specific industry and facility.
- Quality Supervisors often face high pressure to meet production targets while maintaining strict quality standards, leading to stress when balancing speed versus precision. They frequently deal with resistance from production teams who may view quality checks as hindrances to efficiency or blame quality issues on the supervision. Investigating defects and implementing corrective actions can be time-consuming and require meticulous documentation, often extending beyond regular working hours. The role demands constant vigilance and attention to detail, which can be mentally fatiguing over long shifts, especially when monitoring complex processes. Career progression beyond a Quality Supervisor role may be limited without further education or transitioning into broader management or specialized engineering positions. They are often the first point of contact for customer complaints related to product quality, requiring strong problem-solving and communication skills under pressure. Regular exposure to manufacturing environments can involve noise, dust, and other industrial hazards, depending on the specific industry and facility.
- Quality Supervisors often face high pressure to meet production targets while maintaining strict quality standards, leading to stress when balancing speed versus precision. They frequently deal with resistance from production teams who may view quality checks as hindrances to efficiency or blame quality issues on the supervision. Investigating defects and implementing corrective actions can be time-consuming and require meticulous documentation, often extending beyond regular working hours. The role demands constant vigilance and attention to detail, which can be mentally fatiguing over long shifts, especially when monitoring complex processes. Career progression beyond a Quality Supervisor role may be limited without further education or transitioning into broader management or specialized engineering positions. They are often the first point of contact for customer complaints related to product quality, requiring strong problem-solving and communication skills under pressure. Regular exposure to manufacturing environments can involve noise, dust, and other industrial hazards, depending on the specific industry and facility.
- Quality Supervisors often face high pressure to meet production targets while maintaining strict quality standards, leading to stress when balancing speed versus precision. They frequently deal with resistance from production teams who may view quality checks as hindrances to efficiency or blame quality issues on the supervision. Investigating defects and implementing corrective actions can be time-consuming and require meticulous documentation, often extending beyond regular working hours. The role demands constant vigilance and attention to detail, which can be mentally fatiguing over long shifts, especially when monitoring complex processes. Career progression beyond a Quality Supervisor role may be limited without further education or transitioning into broader management or specialized engineering positions. They are often the first point of contact for customer complaints related to product quality, requiring strong problem-solving and communication skills under pressure. Regular exposure to manufacturing environments can involve noise, dust, and other industrial hazards, depending on the specific industry and facility.
Frequently Asked Questions
Quality Supervisors face unique challenges balancing team leadership with strict adherence to quality standards and regulatory compliance. This section addresses the most common questions about entering this role, from the necessary leadership and technical skills to managing team performance and navigating industry-specific regulations.
What are the typical educational and experience requirements for a Quality Supervisor?
To become a Quality Supervisor, you typically need a strong background in quality assurance or a related field, often with several years of experience in a quality control or inspection role. Many employers prefer candidates with an associate's or bachelor's degree in a relevant discipline like engineering, manufacturing, or business management. Certifications such as ASQ's Certified Quality Technician (CQT) or Certified Quality Inspector (CQI) can significantly enhance your qualifications.
What does a typical day look like for a Quality Supervisor?
A Quality Supervisor's day involves a mix of hands-on quality checks, team management, and problem-solving. You will likely spend time overseeing inspection processes, training staff on quality procedures, analyzing data to identify trends, and implementing corrective actions. Communication with production teams, management, and sometimes suppliers is also a significant part of the role to ensure quality standards are met throughout the manufacturing process.
What is the expected salary range and typical benefits for a Quality Supervisor?
The salary for a Quality Supervisor varies significantly based on industry, company size, location, and your level of experience. Entry-level positions might start around $50,000 to $60,000 annually, while experienced supervisors in high-demand industries could earn $75,000 or more. Benefits packages often include health insurance, retirement plans, and paid time off. Researching specific industry salary ranges is helpful for accurate expectations.
What are the career advancement opportunities for a Quality Supervisor?
Career growth for Quality Supervisors can lead to various advanced roles within quality management. You could advance to Quality Manager, Senior Quality Engineer, or even Director of Quality. Some supervisors specialize in certain areas like Six Sigma or Lean Manufacturing, becoming process improvement specialists. Gaining additional certifications and pursuing further education often accelerates this career progression.
What is the typical work-life balance for a Quality Supervisor, including remote work potential?
While some Quality Supervisor roles might offer limited flexibility, many require a consistent on-site presence to oversee production and manage teams directly. The work-life balance largely depends on the industry and specific company culture. Manufacturing environments, for instance, might involve shift work or occasional overtime, especially during peak production periods or when addressing quality issues. It is important to ask about typical work hours during interviews.
What are the biggest challenges a Quality Supervisor faces on the job?
The most significant challenge for a Quality Supervisor is balancing the need for strict quality adherence with production deadlines and cost efficiencies. You must effectively communicate quality requirements, manage and motivate your team, and implement corrective actions under pressure. Handling non-conforming products and resolving disputes between departments regarding quality issues can also be demanding aspects of the job.
What is the job security and market demand for Quality Supervisors?
The job market for Quality Supervisors remains stable, driven by continuous industry demand for high-quality products and services. As companies increasingly prioritize efficiency and customer satisfaction, the need for skilled quality professionals who can lead teams and implement robust quality systems persists. Economic downturns can sometimes impact manufacturing, but the fundamental need for quality control endures across most sectors.
Related Careers
Explore similar roles that might align with your interests and skills:
QA Supervisor
A growing field with similar skill requirements and career progression opportunities.
Explore career guideQuality Assurance Supervisor
A growing field with similar skill requirements and career progression opportunities.
Explore career guideQuality Control Supervisor
A growing field with similar skill requirements and career progression opportunities.
Explore career guideQuality Coordinator
A growing field with similar skill requirements and career progression opportunities.
Explore career guideQuality Inspector
A growing field with similar skill requirements and career progression opportunities.
Explore career guideAssess your Quality Supervisor readiness
Understanding where you stand today is the first step toward your career goals. Our Career Coach helps identify skill gaps and create personalized plans.
Skills Gap Analysis
Get a detailed assessment of your current skills versus Quality Supervisor requirements. Our AI Career Coach identifies specific areas for improvement with personalized recommendations.
See your skills gapCareer Readiness Assessment
Evaluate your overall readiness for Quality Supervisor roles with our AI Career Coach. Receive personalized recommendations for education, projects, and experience to boost your competitiveness.
Assess your readinessSimple pricing, powerful features
Upgrade to Himalayas Plus and turbocharge your job search.
Himalayas
Himalayas Plus
Himalayas Max
Find your dream job
Sign up now and join over 100,000 remote workers who receive personalized job alerts, curated job matches, and more for free!
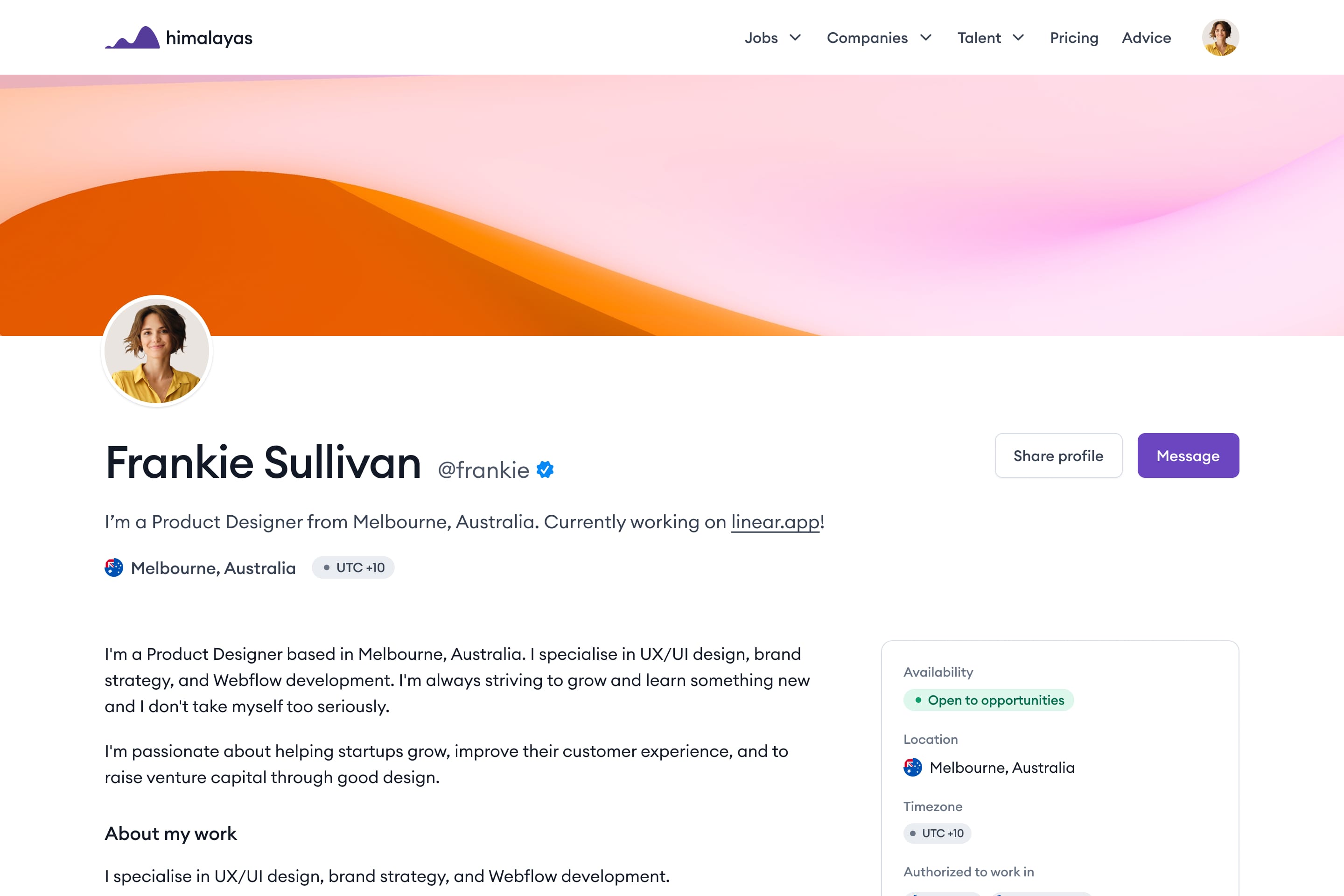