Complete Quality Control Manager Career Guide
Quality Control Managers ensure products and services meet rigorous standards, safeguarding brand reputation and customer satisfaction. They are pivotal in identifying flaws, streamlining processes, and implementing corrective actions to prevent costly errors before they impact the market. This role demands sharp analytical skills and a meticulous eye for detail, offering a career path where you directly influence a company's success and product integrity.
Key Facts & Statistics
Median Salary
$99,300 USD
(U.S. national median, May 2023, BLS)
Range: $60k - $150k+ USD, varying significantly by industry, experience, and location
Growth Outlook
5%
as fast as average (2022-2032)
Annual Openings
≈23,000
openings annually
Top Industries
Typical Education
Bachelor's degree in a relevant field like engineering, business, or quality management; certifications (e.g., ASQ Certified Quality Manager) are highly valued
What is a Quality Control Manager?
A Quality Control Manager is a specialized professional responsible for ensuring that products or services consistently meet established quality standards and regulatory requirements. This role focuses on the inspection and testing phases of production, identifying defects, and preventing faulty goods from reaching the customer. They implement and oversee the systems and procedures that verify product quality at various stages of development and manufacturing.
Unlike a Quality Assurance (QA) Manager, who focuses on preventing defects by improving processes and systems from the outset, a Quality Control Manager concentrates on identifying defects after they occur. They are critical in industries like manufacturing, pharmaceuticals, and food production, where product integrity directly impacts consumer safety and brand reputation. Their primary goal is to maintain high product reliability and customer satisfaction through rigorous testing and inspection protocols.
What does a Quality Control Manager do?
Key Responsibilities
- Develop and implement quality control processes and procedures to ensure products meet established standards and specifications.
- Oversee daily inspection activities, including raw materials, in-process production, and finished goods, to identify non-conformities.
- Analyze quality data and metrics to identify trends, root causes of defects, and areas for continuous improvement.
- Lead and manage a team of quality control inspectors, providing training, performance evaluations, and mentorship.
- Collaborate with production, engineering, and supply chain teams to resolve quality issues and implement corrective and preventive actions.
- Conduct internal and external audits to ensure compliance with industry regulations, quality management systems, and customer requirements.
- Prepare detailed quality reports for management, highlighting performance, challenges, and proposed improvements to quality systems and products.
Work Environment
Quality Control Managers typically work in a hybrid environment, splitting their time between an office setting and the production floor or laboratory. The work environment can be fast-paced, especially in manufacturing, requiring quick decision-making to address immediate quality issues. They collaborate extensively with production, engineering, and supply chain teams, often participating in cross-functional meetings. The role usually involves regular business hours, but occasional evening or weekend work may be necessary to resolve critical quality problems or oversee production shifts.
Travel is generally minimal, primarily for supplier audits or industry conferences. The culture emphasizes meticulous attention to detail, adherence to standards, and continuous improvement. It is a role that balances analytical work with hands-on problem-solving and team leadership.
Tools & Technologies
Quality Control Managers utilize a range of tools and technologies to monitor and improve product quality. They frequently work with Quality Management Systems (QMS) software like ISO 9001-certified platforms to document processes, manage audits, and track non-conformances. Statistical Process Control (SPC) software is essential for analyzing data, identifying trends, and predicting potential issues in manufacturing processes.
They also use various inspection equipment such as calipers, micrometers, CMM (Coordinate Measuring Machine) systems, and specialized testing apparatus relevant to their industry (e.g., tensile testers, spectrometers). Spreadsheet software like Microsoft Excel and data visualization tools such as Tableau or Power BI are critical for data analysis and reporting. Communication and project management tools like Microsoft Teams, Slack, and Jira facilitate collaboration with cross-functional teams.
Quality Control Manager Skills & Qualifications
A Quality Control Manager oversees product or service quality, ensuring adherence to established standards and regulatory compliance. This role focuses on implementing and maintaining quality systems, not just inspecting individual products. Understanding how qualifications are structured in this field is crucial for career progression.
Requirements vary significantly by industry. For instance, a Quality Control Manager in pharmaceuticals faces stringent regulatory demands, often requiring specific certifications like Six Sigma Black Belt or ISO 13485 auditor. In manufacturing, a strong background in lean principles and statistical process control is essential. Company size also plays a role; smaller companies may expect a broader skillset, while larger organizations allow for more specialization within quality management. Seniority levels demand increasing leadership, strategic planning, and complex problem-solving abilities.
Formal education provides a strong foundation, particularly degrees in engineering, quality management, or a relevant scientific field. However, practical experience often outweighs a degree alone, especially for mid-career professionals. Certifications from bodies like the American Society for Quality (ASQ) significantly enhance marketability and demonstrate specialized knowledge. Alternative pathways, such as vocational training in quality assurance coupled with extensive on-the-job experience, are viable. The skill landscape is evolving with the integration of AI for predictive quality and advanced data analytics, making these emerging skills increasingly valuable. Balancing broad quality management knowledge with deep expertise in specific tools or methodologies is key for career advancement.
Education Requirements
Technical Skills
- Quality Management Systems (QMS) implementation and maintenance (e.g., ISO 9001, AS9100, ISO 13485, IATF 16949)
- Statistical Process Control (SPC) and Statistical Data Analysis (e.g., Minitab, JMP)
- Root Cause Analysis methodologies (e.g., 5 Whys, Fishbone diagrams, FMEA, 8D)
- Lean Manufacturing and Six Sigma principles and tools (e.g., DMAIC, Value Stream Mapping)
- Audit management and execution (internal and external audits)
- Metrology and calibration principles, including measurement system analysis (MSA)
- Data analysis and visualization tools (e.g., Excel, Tableau, Power BI) for quality metrics reporting
- Non-conformance management and Corrective and Preventive Actions (CAPA) systems
- Supplier Quality Management and incoming inspection processes
- Risk management principles and application in quality control
- Regulatory compliance specific to industry (e.g., FDA, GMP, CE Mark, UL)
- Technical documentation and report writing for quality assurance
Soft Skills
- Leadership and Team Management: A Quality Control Manager guides quality teams, sets performance expectations, and fosters a culture of quality. This skill is vital for driving continuous improvement initiatives and motivating staff.
- Problem-Solving and Root Cause Analysis: Identifying the true cause of quality issues and developing effective corrective actions is central to this role. Managers must apply structured methodologies to complex problems.
- Communication and Presentation: Explaining complex quality data, presenting audit findings to stakeholders, and training staff on quality procedures requires clear, concise communication. This includes written reports and verbal presentations.
- Attention to Detail and Accuracy: Meticulousness is paramount in ensuring product specifications, documentation, and regulatory requirements are met without error. Overlooking small details can lead to significant quality failures.
- Strategic Thinking and Planning: Developing and implementing long-term quality strategies, integrating quality objectives with business goals, and anticipating future quality challenges are critical for effective quality control.
- Negotiation and Influence: Managers often need to negotiate quality standards with suppliers, influence cross-functional teams to adopt quality best practices, and resolve conflicts related to quality deviations.
- Adaptability and Continuous Improvement Mindset: The quality landscape constantly evolves with new technologies and regulations. A manager must adapt to changes and champion a culture of ongoing process enhancement.
How to Become a Quality Control Manager
Breaking into Quality Control Management involves various pathways, each with distinct timelines and requirements. Traditional routes often include a bachelor's degree in a relevant scientific or engineering discipline, followed by several years in a quality assurance or control role. Non-traditional paths might leverage extensive technical experience from manufacturing or laboratory settings, often supplemented by certifications rather than a formal degree.
Timeline expectations vary significantly; a complete beginner might need 3-5 years to gain foundational experience and then move into management, while someone transitioning from a related technical role could achieve this in 1-2 years with focused effort. Entry strategies also depend on the industry—pharmaceuticals and medical devices often demand stricter academic backgrounds, whereas food processing or general manufacturing might prioritize practical experience. Large corporations often prefer formal qualifications and structured career progression, while smaller companies or startups might value a diverse skill set and adaptability.
A common misconception is that quality control is purely about inspection; in reality, it's about implementing robust systems, continuous improvement, and risk management. Networking within industry associations and seeking mentorship can significantly accelerate career progression by opening doors to opportunities and insights not publicly advertised. The current hiring landscape increasingly values candidates with strong analytical skills, a deep understanding of regulatory compliance, and the ability to lead cross-functional teams, moving beyond just technical expertise.
Step 1
Step 2
Step 3
Step 4
Step 5
Step 6
Step 7
Education & Training Needed to Become a Quality Control Manager
Becoming a Quality Control Manager involves a blend of formal education and practical experience. Traditional four-year bachelor's degrees in fields like Engineering, Business Administration, or Quality Management provide a strong theoretical foundation, often costing between $40,000 and $100,000+ for tuition and taking four years to complete. These programs are highly valued by larger organizations and those in regulated industries, as they demonstrate a comprehensive understanding of underlying principles and methodologies.
Alternatively, professionals can pursue specialized certifications and online courses, which focus on practical skills and industry standards. These options range from a few hundred dollars to $5,000-$10,000 and can be completed in 6 to 18 months. While not a direct substitute for a degree in all cases, certifications from reputable bodies like ASQ (American Society for Quality) are highly recognized and can significantly boost a candidate's profile, especially for those with existing industry experience. Employers often prefer candidates with a mix of credentials, valuing both theoretical knowledge and demonstrated practical application.
Continuous learning is crucial in quality control, as regulations and technologies evolve. Advanced certifications, Six Sigma belts, and specialized training in areas like Lean Manufacturing or ISO standards are vital for career progression and staying competitive. The investment in these can range from $1,000 to $10,000 for a Black Belt certification. The most effective educational path balances formal academic grounding with practical, industry-specific certifications, ensuring a candidate possesses both the strategic oversight and the tactical tools required for effective quality management.
Quality Control Manager Salary & Outlook
Compensation for a Quality Control Manager varies significantly based on multiple factors. Geographic location plays a crucial role, with higher salaries often found in major industrial hubs or regions with a higher cost of living, such as California or the Northeast United States. Local market demand and the presence of specific industries like pharmaceuticals or manufacturing also influence earning potential.
Years of experience, specialized certifications (e.g., Six Sigma, ASQ), and the complexity of products or processes managed create dramatic salary variations. Total compensation packages extend beyond base salary, often including performance-based bonuses, stock options in larger corporations, and comprehensive benefits. These benefits typically cover health insurance, retirement contributions like 401(k) matching, and professional development allowances for continuous learning.
Industry-specific trends, such as increased regulatory scrutiny or demand for higher precision manufacturing, drive salary growth for skilled Quality Control Managers. Professionals with strong negotiation skills and a proven track record of implementing effective quality systems command premium compensation. While remote work is less common for hands-on quality control roles, some strategic or oversight positions may offer location flexibility, impacting salary ranges based on the company's compensation philosophy for remote talent. Salaries provided are in USD, acknowledging international market variations.
Salary by Experience Level
Level | US Median | US Average |
---|---|---|
Assistant Quality Control Manager | $65k USD | $70k USD |
Quality Control Manager | $90k USD | $95k USD |
Senior Quality Control Manager | $115k USD | $120k USD |
Quality Assurance Manager | $130k USD | $135k USD |
Director of Quality Control | $155k USD | $165k USD |
VP of Quality Assurance | $190k USD | $205k USD |
Market Commentary
The job market for Quality Control Managers remains stable with a projected growth outlook, driven by increasing regulatory requirements and consumer demand for higher quality products across various industries. The Bureau of Labor Statistics projects a steady demand for quality control professionals. Industries such as manufacturing, pharmaceuticals, food and beverage, and medical devices consistently seek skilled managers to ensure compliance and product excellence.
Emerging opportunities for Quality Control Managers include specializations in data analytics for quality assurance, automation of inspection processes, and the integration of AI in quality monitoring. The role is evolving to require more proficiency in digital tools and statistical software, moving beyond traditional manual inspections. Supply and demand dynamics are relatively balanced, with a consistent need for experienced professionals who can navigate complex quality systems and lead teams effectively.
Future-proofing considerations for this role involve continuous learning in areas like lean manufacturing, advanced statistical process control, and cybersecurity for industrial control systems. While some routine quality checks might be automated, the strategic oversight, problem-solving, and leadership aspects of the Quality Control Manager role are largely resistant to automation. This profession is generally considered recession-resistant, as quality assurance remains critical even during economic downturns. Geographic hotspots include industrial corridors in the Midwest, technology manufacturing centers, and pharmaceutical hubs, though skilled professionals are needed nationwide.
Quality Control Manager Career Path
Career progression for a Quality Control Manager typically involves a clear path from hands-on operational oversight to strategic leadership. Professionals often begin by mastering specific testing protocols and quality standards within a particular industry. Advancement hinges on a deep understanding of process improvement, risk management, and regulatory compliance.
Progression can follow an individual contributor (IC) track, focusing on deep technical expertise and complex problem-solving, or a management track, emphasizing team leadership and strategic program development. The size and type of company significantly influence this. Startups might offer faster advancement but broader responsibilities, while large corporations have more structured, often slower, paths with opportunities for specialization. Agencies or consulting firms often prioritize diverse client experience and project management skills.
Key factors influencing advancement speed include demonstrated success in reducing defects, improving efficiency, and ensuring compliance. Specialization in areas like Six Sigma, Lean Manufacturing, or specific industry regulations (e.g., ISO, FDA) can accelerate growth. Networking within industry associations, continuous learning in quality methodologies, and effective mentorship are crucial for identifying opportunities and developing leadership capabilities. Lateral moves into related areas like process engineering or supply chain management are also common alternative pathways.
Assistant Quality Control Manager
2-4 yearsKey Focus Areas
Quality Control Manager
4-7 yearsKey Focus Areas
Senior Quality Control Manager
7-10 yearsKey Focus Areas
Quality Assurance Manager
10-14 yearsKey Focus Areas
Director of Quality Control
14-18 yearsKey Focus Areas
VP of Quality Assurance
18+ yearsKey Focus Areas
Assistant Quality Control Manager
2-4 yearsOversees daily quality checks and inspections on production lines or incoming materials. Ensures adherence to established quality standards and specifications. Manages a small team of quality technicians or inspectors, providing direct supervision and training. Reports non-conformances and assists in initial investigations.
Key Focus Areas
Mastering quality inspection techniques and documentation. Understanding standard operating procedures and regulatory requirements. Developing strong communication skills for reporting non-conformances. Beginning to identify root causes of quality issues. Acquiring foundational knowledge of quality management systems.
Quality Control Manager
4-7 yearsManages the overall quality control function for a specific product line or department. Develops and implements quality control procedures and sampling plans. Analyzes quality data to identify trends and areas for improvement. Leads investigations into significant quality failures and ensures compliance with internal and external standards.
Key Focus Areas
Implementing corrective and preventive actions (CAPA). Driving continuous improvement initiatives using methodologies like Lean or Six Sigma. Enhancing data analysis skills for trend identification and predictive quality. Developing conflict resolution and team leadership abilities. Expanding knowledge of industry-specific regulations.
Senior Quality Control Manager
7-10 yearsOversees multiple quality control teams or an entire facility's quality operations. Designs and implements advanced quality assurance programs and systems. Acts as a subject matter expert for complex quality issues and regulatory audits. Drives significant process improvements and cost reduction initiatives through quality enhancements.
Key Focus Areas
Developing strategic quality planning skills. Mentoring and developing junior quality professionals. Leading cross-functional teams for complex problem-solving. Enhancing risk assessment and mitigation strategies. Building strong stakeholder management and negotiation skills.
Quality Assurance Manager
10-14 yearsResponsible for the overall quality assurance strategy and system across an organization or major business unit. Establishes quality policies, procedures, and standards. Ensures compliance with all relevant industry regulations and certifications. Oversees audit programs and drives continuous improvement throughout the entire product lifecycle.
Key Focus Areas
Designing and implementing enterprise-wide quality management systems (QMS). Developing and executing quality strategies aligned with business objectives. Leading major certification efforts (e.g., ISO). Cultivating strong relationships with regulatory bodies and external auditors. Mastering change management principles.
Director of Quality Control
14-18 yearsProvides strategic leadership and direction for all quality control operations across an organization. Develops and implements the overarching quality control vision and long-term objectives. Manages significant budgets and resources, ensuring alignment with corporate goals. Represents the company on quality matters with external stakeholders and regulatory agencies.
Key Focus Areas
Shaping organizational quality culture and governance. Driving innovation in quality methodologies and technologies. Developing talent pipelines for quality leadership roles. Influencing executive leadership on quality-related investments and strategic direction. Managing global quality initiatives and supply chain quality.
VP of Quality Assurance
18+ yearsHolds ultimate accountability for the entire organization's quality assurance function and performance. Sets global quality strategy, policies, and standards. Oversees all quality management systems, regulatory compliance, and customer satisfaction related to quality. Provides executive-level guidance on quality risks and opportunities, directly influencing business outcomes.
Key Focus Areas
Defining and championing the enterprise-wide quality vision and strategy. Driving a culture of excellence and continuous improvement across all business functions. Leading global quality initiatives and ensuring competitive advantage through superior quality. Developing and nurturing strategic partnerships.
Job Application Toolkit
Ace your application with our purpose-built resources:
Quality Control Manager Resume Examples
Proven layouts and keywords hiring managers scan for.
View examplesQuality Control Manager Cover Letter Examples
Personalizable templates that showcase your impact.
View examplesTop Quality Control Manager Interview Questions
Practice with the questions asked most often.
View examplesQuality Control Manager Job Description Template
Ready-to-use JD for recruiters and hiring teams.
View examplesGlobal Quality Control Manager Opportunities
A Quality Control Manager's role translates universally across manufacturing, pharmaceuticals, and technology, focusing on product or service integrity. Global demand remains strong as industries prioritize compliance and excellence. Regulatory frameworks, like ISO standards, are largely consistent, but national specificities exist. Professionals seek international roles for diverse industry exposure and career advancement. Certifications like ASQ CMQ/OE enhance global mobility significantly.
Global Salaries
Salaries for Quality Control Managers vary significantly by region and industry. In North America, particularly the US, annual salaries range from $80,000 to $130,000 USD, influenced by industry (e.g., medical devices offer higher pay) and company size. Canada sees ranges of CAD 75,000 to CAD 110,000, roughly $55,000 to $80,000 USD, with a lower cost of living.
Europe presents diverse compensation. Germany offers €60,000 to €95,000 ($65,000-$105,000 USD), while the UK ranges from £50,000 to £80,000 ($63,000-$100,000 USD). Scandinavian countries provide similar ranges but with higher taxation. Southern European nations like Spain or Italy might offer €40,000 to €60,000 ($43,000-$65,000 USD), reflecting lower living costs.
Asia-Pacific markets are competitive. Australia's salaries are AUD 90,000 to AUD 130,000 ($60,000-$85,000 USD). In developed Asian economies like Singapore, managers earn SGD 70,000 to SGD 120,000 ($52,000-$89,000 USD). China, particularly in manufacturing hubs, offers RMB 200,000 to RMB 400,000 ($28,000-$56,000 USD), often with local benefits. Latin America's ranges are lower, often $25,000-$50,000 USD, but purchasing power can be higher.
International salary structures often include varying benefits, such as private healthcare, pension contributions, and vacation days, which impact total compensation. Tax implications differ greatly; for instance, high-tax European nations might result in lower take-home pay compared to the US. Experience, specialized industry knowledge, and advanced degrees significantly influence compensation globally.
Remote Work
International remote work for Quality Control Managers is limited, as the role often requires direct oversight of production processes or physical products. However, some aspects, like documentation, process analysis, and supplier quality management, can be performed remotely. Industry trends show a slight increase in hybrid models for this role, blending on-site presence with remote tasks.
Legal and tax implications for international remote work involve navigating host country labor laws and tax residency rules. Time zone differences can pose challenges for global team collaboration. Digital nomad visas are generally not suitable for this role due to its on-site demands. Employers typically require a local entity to hire internationally.
The impact of remote work on salary expectations for Quality Control Managers is minimal. Companies usually base compensation on the cost of labor in the employee's location, not the employer's. Platforms for international hiring in this field are less common due to the hands-on nature of the job. Essential requirements include reliable internet and a dedicated workspace for the remote components of the role.
Visa & Immigration
Quality Control Managers typically qualify for skilled worker visas in popular destination countries. Common visa categories include the H-1B in the US, Tier 2 (Skilled Worker) visa in the UK, and Blue Card in the EU. Requirements often include a relevant bachelor's degree, several years of experience, and a job offer from a sponsoring employer.
For the UK, the Skilled Worker visa requires a Certificate of Sponsorship and meeting salary thresholds, usually processed within weeks. Germany's Blue Card demands a recognized degree and a specific salary level, offering a pathway to permanent residency. Canada's Express Entry system prioritizes skilled workers, including Quality Control Managers, based on a points system for age, education, language proficiency, and work experience.
Education credential recognition is crucial; applicants often need evaluations to ensure their degrees meet local standards. Professional licensing is generally not required for this role, but industry-specific certifications, like ISO lead auditor, are beneficial. English language proficiency tests, such as IELTS or TOEFL, are often mandatory for non-native speakers. Some countries offer fast-track processing for highly skilled roles, but this is not common for Quality Control Managers. Family members typically receive dependent visas.
2025 Market Reality for Quality Control Managers
Understanding current market realities is critical for Quality Control Managers navigating career paths. The landscape has evolved significantly from 2023 to 2025, driven by post-pandemic supply chain shifts and the accelerating AI revolution.
Broader economic factors, such as inflation and consumer spending trends, directly impact production volumes and, consequently, the demand for quality oversight. Market realities for this role vary considerably by industry—highly regulated fields like medical devices or aerospace have different needs than, for instance, consumer electronics. Experience levels and company size also dictate expectations, with larger corporations often seeking managers capable of overseeing complex global quality systems. This analysis offers an honest assessment of current conditions.
Current Challenges
Quality Control Managers face increased competition, especially as companies consolidate roles and AI tools automate some oversight tasks. Market saturation appears at mid-level positions due to fewer senior roles opening up. Economic uncertainty leads companies to delay hiring or freeze budgets for quality departments, impacting job availability. The rapid pace of technological change creates skill gaps, as managers need expertise in new automation and data analytics platforms. Remote work means competition extends globally, further intensifying the search.
Growth Opportunities
Despite market challenges, strong demand persists for Quality Control Managers proficient in specific areas. Opportunities are robust in industries undergoing significant digital transformation, such as advanced manufacturing, biotech, and specialized electronics. Companies in these sectors seek leaders who can implement Industry 4.0 principles, including IoT-driven quality monitoring and machine learning for defect prediction.
Emerging roles include 'AI Quality Assurance Lead' or 'Data-Driven Quality Manager,' focusing on leveraging large datasets to enhance product reliability and process efficiency. Professionals who can demonstrate a proven track record in reducing waste through automation or improving compliance using digital tools gain a significant competitive edge. Underserved markets often appear in regions with growing niche manufacturing or specialized R&D facilities that require stringent quality protocols.
Certifications in AI ethics, data governance, or advanced statistical process control (SPC) provide strong advantages. Market corrections might create opportunities for strategic moves into companies prioritizing long-term quality investments over short-term cost-cutting. Sectors like medical device manufacturing, defense, and high-tech automotive remain resilient, offering stable career paths. Investing in continuous learning, particularly in AI and automation, is a smart career move for Quality Control Managers.
Current Market Trends
Hiring for Quality Control Managers remains steady but selective as of 2025. Demand focuses on candidates who can integrate advanced data analytics and automation into existing quality processes. Companies are increasingly looking for managers who can leverage AI-powered predictive quality tools, moving from reactive defect detection to proactive prevention. This shift demands a blend of traditional quality assurance principles with strong technological acumen.
Economic conditions, particularly in manufacturing and consumer goods, influence hiring. While essential, some sectors face pressure to reduce overhead, leading to leaner quality teams. This means fewer roles but higher expectations for those hired. Generative AI impacts document control, standard operating procedure generation, and initial anomaly detection, requiring managers to oversee sophisticated automated systems rather than just manual checks. Employers prioritize candidates with experience in digital transformation projects within quality departments.
Salary growth for Quality Control Managers shows moderation, with significant increases reserved for those possessing specialized skills in AI integration, Six Sigma Black Belt certification, and regulatory compliance in highly regulated industries like pharmaceuticals or aerospace. Market saturation is evident at the entry-to-mid level, making differentiation through advanced certifications or niche industry experience crucial. Geographically, demand remains strong in industrial hubs and areas with robust manufacturing or biotech sectors. Remote opportunities exist but are less common for roles requiring direct oversight of physical production lines.
Emerging Specializations
Technological advancements and evolving industry standards consistently reshape the landscape for quality control professionals. These shifts create novel specialization opportunities, moving beyond traditional inspection and assurance roles into more analytical and proactive domains. Early positioning in these emerging areas is crucial for career advancement, especially looking towards 2025 and beyond.
Specializing in cutting-edge fields often commands premium compensation and offers accelerated career growth. These roles address complex challenges that established specializations may not cover, making them highly valuable. While established quality control practices remain essential, integrating emerging expertise allows professionals to lead future quality initiatives.
Many emerging areas, particularly those driven by data science, artificial intelligence, or advanced automation, are currently gaining significant traction. They are poised to become mainstream within the next three to five years, generating substantial job opportunities. Professionals embracing these specializations early can shape best practices and define new industry benchmarks.
Pursuing cutting-edge specializations involves balancing risk and reward. While the potential for impact and growth is high, these fields may require continuous learning and adapting to rapid changes. However, the strategic advantage of being at the forefront of quality innovation often outweighs these challenges, positioning individuals as indispensable assets within their organizations.
Predictive Quality Analytics Specialist
Automated Quality Systems Integrator
Additive Manufacturing Quality Assurance Lead
Embedded Systems Quality & Functional Safety Manager
Sustainable Product Quality Specialist
Pros & Cons of Being a Quality Control Manager
Making informed career decisions requires a clear understanding of both the benefits and challenges associated with a profession. The experience in a career like Quality Control Manager can vary significantly based on the industry, company culture, specific products, and the manager's individual personality and leadership style. What one person views as a pro, another might see as a con, depending on their values and work preferences. Furthermore, the daily realities and strategic demands of this role can shift as one moves from an early career stage to more senior or leadership positions. This assessment offers an honest, balanced perspective to help set realistic expectations for anyone considering a career as a Quality Control Manager.
Pros
- Quality Control Managers play a critical role in ensuring product safety and reliability, directly impacting customer satisfaction and company reputation. This provides a strong sense of purpose and contribution to product excellence.
- The role offers significant intellectual stimulation as it involves problem-solving, root cause analysis, and implementing continuous improvement initiatives. Managers constantly analyze data and processes to enhance quality systems.
- There is high demand for skilled Quality Control Managers across various industries, including manufacturing, pharmaceuticals, food and beverage, and technology. This offers strong job security and diverse employment opportunities.
- Quality Control Managers develop a comprehensive understanding of an organization's entire production process, from raw materials to finished goods. This broad knowledge can open doors to other operational or leadership roles.
- The position often commands a competitive salary due to its specialized nature and the critical responsibility of maintaining quality standards and regulatory compliance. This reflects the value placed on preventing defects and ensuring product integrity.
- Quality Control Managers are empowered to implement changes and drive improvements in processes and products. This autonomy allows for significant influence over operational efficiency and overall business success.
- This role requires strong analytical, organizational, and leadership skills, which are highly transferable across different industries and management positions. The skills acquired are valuable for career advancement in many fields.
Cons
- Quality Control Managers often face high pressure, especially when production issues arise or deadlines loom. This can lead to stressful periods and long hours to ensure compliance and prevent product recalls.
- The role requires meticulous attention to detail and adherence to strict regulations, which can be repetitive and mentally taxing over time. Missing even minor discrepancies can have significant consequences.
- Dealing with non-conforming products or processes often involves difficult conversations with production teams, suppliers, or even customers. This can be challenging and require strong conflict resolution skills.
- Career progression can sometimes be limited within a single organization, as the Quality Control Manager role is often a senior, specialized position. Advancement may require moving to a larger company or into broader operations management.
- The work environment can sometimes be isolated, as the Quality Control Manager is often seen as the enforcer of standards. This can lead to less collaborative interaction compared to other roles in manufacturing or production.
- Continuous learning is essential to keep up with evolving industry standards, regulations, and technological advancements in quality assurance. This requires ongoing professional development outside of regular work hours.
- Budget constraints can limit access to new quality control technologies or sufficient staffing, forcing managers to achieve high standards with limited resources, which adds to the operational challenge and potential for burnout.
Frequently Asked Questions
Quality Control Managers face distinct challenges ensuring product or service excellence while managing teams and processes. This section addresses common questions about entry requirements, daily responsibilities, and career growth, helping you understand the precision and leadership required in this vital role.
What educational background and certifications are essential to become a Quality Control Manager?
You typically need a bachelor's degree in a relevant field like engineering, quality management, business administration, or a related science. Many employers also prefer or require certifications such as ASQ Certified Quality Manager (CQM/OE) or Six Sigma Black Belt. Practical experience in a quality assurance or manufacturing role is crucial for advancement.
How long does it typically take to advance into a Quality Control Manager position?
Transitioning into this role usually takes 3-7 years, depending on your starting point and the industry. If you have a relevant degree, you might start as a Quality Control Inspector or Technician, then progress to a Quality Engineer before reaching a management position. Gaining leadership experience and specialized certifications can accelerate this timeline.
What are the typical salary expectations for a Quality Control Manager?
Starting salaries for Quality Control Managers vary significantly by industry, location, and experience, but generally range from $70,000 to $95,000 annually. With extensive experience, specialized certifications, and in senior roles or high-demand industries, salaries can exceed $120,000. Researching specific industry salary guides for your region provides the most accurate picture.
What is the typical work-life balance like for a Quality Control Manager?
The work-life balance can fluctuate, often depending on the industry and company culture. During peak production periods, audits, or issue resolution, you might work longer hours. However, many roles offer standard business hours. It's important to clarify the expected demands during the interview process, especially regarding on-call duties or travel.
Is the Quality Control Manager role secure, and what is the market demand like?
Job security for Quality Control Managers is generally strong, as quality assurance remains critical across all industries. Companies continuously seek to improve efficiency and reduce defects, making this role indispensable. The demand for skilled professionals who can implement robust quality systems and lead teams effectively continues to grow.
What are the typical career growth opportunities for a Quality Control Manager?
You can advance to Senior Quality Control Manager, Director of Quality, or even Vice President of Operations or Manufacturing. Many also transition into consulting, specializing in quality system implementation or process improvement. Continuous learning, gaining expertise in lean manufacturing or Six Sigma, and developing strong leadership skills open these doors.
What are the most significant challenges a Quality Control Manager faces daily?
The biggest challenges often involve balancing cost reduction with quality standards, managing complex regulatory compliance, and leading a team to consistently meet targets. You also face pressure to implement continuous improvement initiatives while troubleshooting existing issues. Effective communication and problem-solving skills are essential to navigate these demands.
Can a Quality Control Manager work remotely, or is it primarily an on-site role?
While some administrative tasks might be performed remotely, the Quality Control Manager role often requires a significant on-site presence. You need to be physically present to oversee production lines, conduct inspections, manage teams directly, and interact with various departments. Fully remote opportunities for this specific role are rare, but hybrid models are becoming more common.
Related Careers
Explore similar roles that might align with your interests and skills:
Quality Assurance Manager
A growing field with similar skill requirements and career progression opportunities.
Explore career guideQuality Control
A growing field with similar skill requirements and career progression opportunities.
Explore career guideQuality Control Coordinator
A growing field with similar skill requirements and career progression opportunities.
Explore career guideQuality Control Specialist
A growing field with similar skill requirements and career progression opportunities.
Explore career guideQuality Manager
A growing field with similar skill requirements and career progression opportunities.
Explore career guideAssess your Quality Control Manager readiness
Understanding where you stand today is the first step toward your career goals. Our Career Coach helps identify skill gaps and create personalized plans.
Skills Gap Analysis
Get a detailed assessment of your current skills versus Quality Control Manager requirements. Our AI Career Coach identifies specific areas for improvement with personalized recommendations.
See your skills gapCareer Readiness Assessment
Evaluate your overall readiness for Quality Control Manager roles with our AI Career Coach. Receive personalized recommendations for education, projects, and experience to boost your competitiveness.
Assess your readinessSimple pricing, powerful features
Upgrade to Himalayas Plus and turbocharge your job search.
Himalayas
Himalayas Plus
Himalayas Max
Find your dream job
Sign up now and join over 100,000 remote workers who receive personalized job alerts, curated job matches, and more for free!
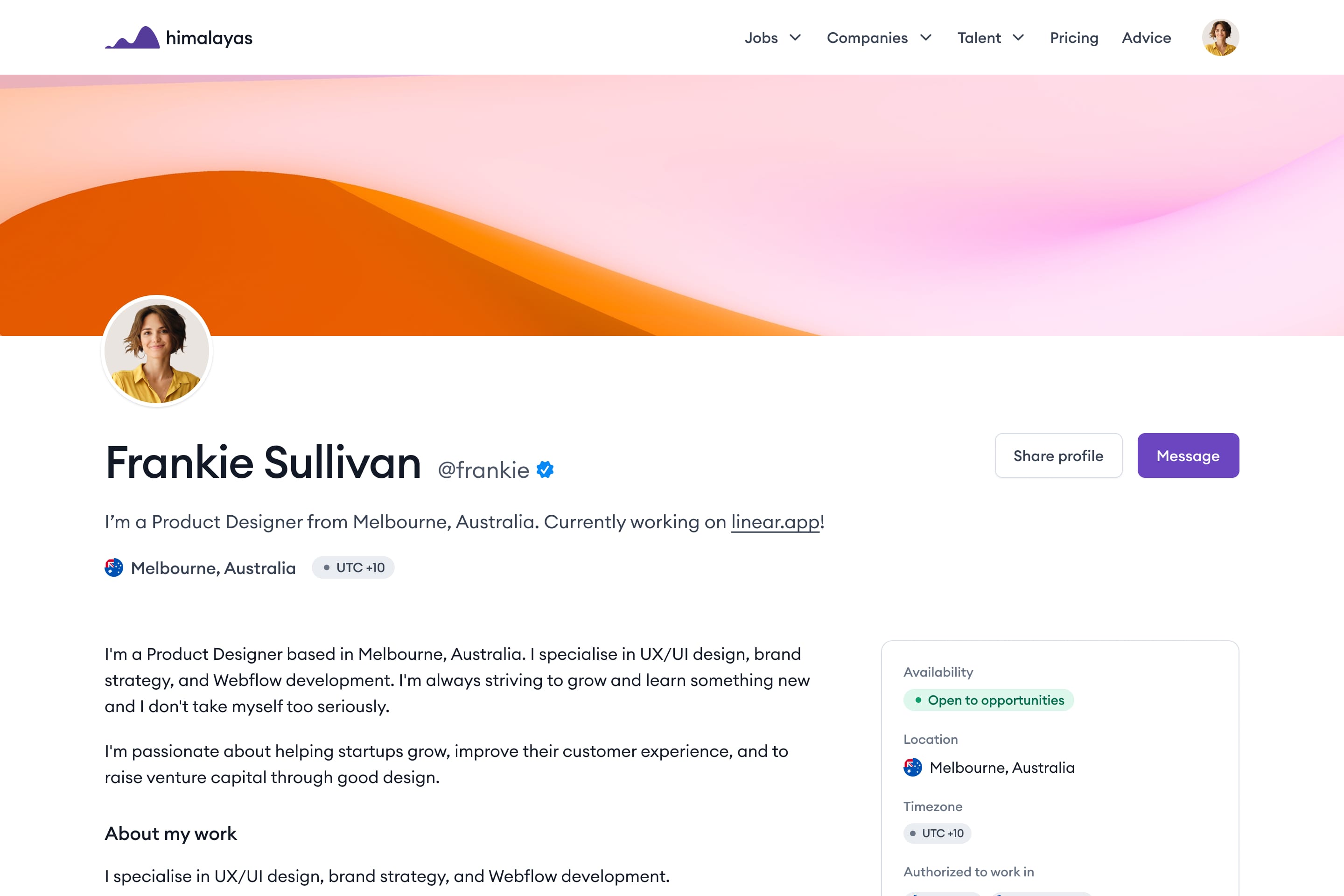