Complete Supply Chain Manager Career Guide
Supply Chain Managers are the strategic architects behind every product reaching its destination, optimizing complex networks of logistics, procurement, and distribution. They are pivotal in ensuring efficiency and resilience, directly impacting a company's profitability and customer satisfaction. This role offers a dynamic career path for problem-solvers who thrive on orchestrating global operations.
Key Facts & Statistics
Median Salary
$106,200 USD
(U.S. national median, BLS, May 2023)
Range: $65k - $160k+ USD (BLS, May 2023)
Growth Outlook
5%
as fast as average (BLS, 2022-2032)
Annual Openings
≈33,700
openings annually (BLS, 2022-2032)
Top Industries
Typical Education
Bachelor's degree in Supply Chain Management, Logistics, Business, or a related field. Some senior roles may prefer an MBA or master's degree.
What is a Supply Chain Manager?
A Supply Chain Manager oversees the entire lifecycle of a product or service, from raw material sourcing to delivery to the end consumer. This role involves strategically planning, implementing, and controlling the efficient, cost-effective flow and storage of goods, services, and related information. They ensure that supply chain operations align with business objectives, focusing on optimizing processes, reducing costs, and enhancing customer satisfaction.
Unlike a Logistics Manager, who primarily focuses on the movement and storage of goods, or a Procurement Manager, who specializes in purchasing, a Supply Chain Manager holds a broader, more strategic view. They integrate all these functions – procurement, production, inventory management, logistics, and distribution – into a cohesive, streamlined system. Their expertise lies in identifying bottlenecks, implementing technological solutions, and building resilient networks to ensure continuous operations and competitive advantage.
What does a Supply Chain Manager do?
Key Responsibilities
- Develop and implement supply chain strategies that optimize efficiency and reduce costs across procurement, production, and distribution.
- Negotiate contracts with suppliers and vendors to secure favorable terms, ensuring timely delivery of materials and services.
- Monitor inventory levels and coordinate with production teams to prevent stockouts or overstock situations, maintaining optimal flow.
- Analyze supply chain data to identify areas for improvement, implementing solutions to enhance logistics and operational performance.
- Manage relationships with key stakeholders, including suppliers, logistics providers, and internal departments, ensuring smooth communication and collaboration.
- Oversee the transportation and warehousing of goods, ensuring compliance with regulations and maintaining high standards of product integrity.
- Implement risk management strategies to mitigate potential disruptions in the supply chain, such as natural disasters or geopolitical events.
Work Environment
Supply Chain Managers typically work in office settings, often within a company's corporate headquarters or a logistics hub. The role involves significant collaboration with cross-functional teams including procurement, manufacturing, sales, and finance. The pace of work is generally fast and dynamic, requiring quick decision-making to address unforeseen issues like supplier delays or sudden demand shifts. While remote work is possible for some planning and analytical tasks, on-site presence is frequently necessary for overseeing operations, warehouse visits, or supplier meetings. Occasional travel to supplier sites, distribution centers, or manufacturing plants may be required. The role demands strong communication and negotiation skills, as it involves constant interaction with both internal and external stakeholders.
Tools & Technologies
Supply Chain Managers regularly use Enterprise Resource Planning (ERP) systems like SAP, Oracle, or Microsoft Dynamics 365 for integrated management of business processes. They also rely on Supply Chain Management (SCM) software such as JDA Software or Manhattan Associates for logistics, inventory, and warehouse optimization. Data analysis tools like Microsoft Excel, Tableau, or Power BI are essential for performance tracking and decision-making. Communication and collaboration platforms like Slack or Microsoft Teams facilitate coordination with internal teams and external partners. Additionally, they may use specialized transportation management systems (TMS) and warehouse management systems (WMS) to streamline operations and ensure efficient material flow.
Supply Chain Manager Skills & Qualifications
A Supply Chain Manager orchestrates the flow of goods and services from raw materials to final consumption. This role demands a holistic understanding of procurement, production, logistics, and distribution. Qualification emphasis shifts significantly with seniority, company size, and industry sector. Entry-level positions may prioritize analytical skills and foundational knowledge, while senior roles demand strategic planning, vendor relationship management, and risk mitigation expertise.
Formal education, practical experience, and certifications all play crucial roles. A bachelor's degree provides a strong theoretical foundation, but extensive practical experience often carries equal or greater weight, especially for mid-career and senior roles. Certifications like CSCP or CPIM demonstrate specialized knowledge and commitment, often becoming 'must-haves' for advancement. Alternative pathways, such as career changers with strong analytical backgrounds or military logistics experience, can succeed by demonstrating relevant transferable skills and a quick learning aptitude.
The supply chain landscape evolves rapidly with technology and global events. Digital transformation, sustainability, and resilience are emerging as critical areas. Managers must balance breadth of understanding across the entire chain with depth in specific areas like demand planning or logistics optimization. Misconceptions often include viewing the role as purely operational; it is increasingly strategic, requiring strong business acumen and the ability to influence cross-functional teams.
Education Requirements
Technical Skills
- Supply Chain Planning Software (e.g., SAP APO, Oracle SCM Cloud, Kinaxis): Proficiency in advanced planning systems for demand forecasting, inventory optimization, and production scheduling.
- Enterprise Resource Planning (ERP) Systems (e.g., SAP, Oracle, Microsoft Dynamics 365): In-depth knowledge of ERP modules related to procurement, inventory, and order management.
- Inventory Management Techniques: Expertise in methodologies like Just-in-Time (JIT), Lean Inventory, ABC analysis, and safety stock calculation to optimize stock levels and reduce carrying costs.
- Logistics and Transportation Management Systems (TMS): Understanding of freight forwarding, customs regulations, carrier selection, and route optimization using TMS platforms.
- Data Analysis and Visualization Tools (e.g., Excel, Tableau, Power BI): Ability to extract, analyze, and present supply chain performance data, identify trends, and support decision-making.
- Procurement and Sourcing Strategies: Knowledge of strategic sourcing, supplier relationship management (SRM), contract negotiation, and risk assessment in the procurement process.
- Process Improvement Methodologies (e.g., Lean, Six Sigma): Application of continuous improvement principles to streamline supply chain operations, reduce waste, and enhance efficiency.
- Demand Forecasting and Planning: Proficiency in statistical forecasting methods, sales and operations planning (S&OP), and collaborative planning, forecasting, and replenishment (CPFR).
- Supply Chain Risk Management: Ability to identify, assess, and mitigate risks across the supply chain, including geopolitical, natural disaster, and cyber risks.
- Sustainability and Ethical Sourcing Practices: Understanding of environmental, social, and governance (ESG) factors in supply chain design and operations.
Soft Skills
- Strategic Thinking: Supply Chain Managers must anticipate market changes, geopolitical shifts, and technological advancements to develop long-term supply chain strategies that align with business objectives.
- Problem-Solving and Decision-Making: Complex issues like unexpected disruptions, supplier failures, or logistical bottlenecks require rapid, data-driven analysis and decisive action to minimize impact.
- Negotiation and Vendor Management: Building and maintaining strong relationships with suppliers, carriers, and partners, often involving complex contract negotiations, is critical for cost efficiency and reliability.
- Cross-functional Collaboration: Success hinges on effective communication and collaboration with internal teams such as sales, marketing, finance, and production to ensure seamless operations.
- Adaptability and Resilience: The global supply chain is prone to disruptions; managers must remain agile, quickly adjust plans, and build resilient systems to navigate unforeseen challenges.
- Leadership and Team Development: Guiding and motivating supply chain teams, fostering a culture of continuous improvement, and developing talent are essential for operational excellence.
- Data-Driven Communication: Translating complex supply chain data and insights into clear, actionable recommendations for stakeholders and senior leadership is vital for influencing decisions.
How to Become a Supply Chain Manager
Breaking into Supply Chain Management offers diverse pathways, moving beyond traditional business degrees to include specialized certifications and practical experience. For a complete beginner, a realistic timeline to land an entry-level role might range from 12 to 24 months, focusing on foundational knowledge and certifications. Career changers with transferable skills from operations or logistics can often transition within 6-12 months by upskilling and leveraging their existing experience.
Entry strategies vary significantly by company size and industry. Large corporations often prefer candidates with formal degrees and certifications, while smaller companies or startups might prioritize practical experience and a demonstrated ability to learn quickly. Geographic location also plays a role; major logistics hubs or manufacturing centers will have more opportunities. Networking, mentorship, and actively participating in industry associations are crucial, as many roles are filled through connections rather than public postings.
A common misconception is that all supply chain roles are highly technical or require extensive travel; many positions focus on planning, analysis, or vendor relations, which are office-based. The hiring landscape values adaptability, analytical skills, and a strong understanding of end-to-end supply chain processes. Overcoming barriers like a lack of direct experience can be achieved through internships, volunteer projects, or roles that involve process improvement and coordination.
Build a foundational understanding of supply chain principles by pursuing a relevant certification or online course. Consider certifications like APICS CSCP or CPIM, or comprehensive Coursera/edX specializations that cover logistics, procurement, and operations. This initial knowledge provides a strong conceptual framework for future learning and practical application.
Gain practical experience through internships, entry-level logistics roles, or volunteer projects that involve inventory management or process optimization. Seek opportunities to work with enterprise resource planning (ERP) systems like SAP or Oracle, even in a limited capacity. Hands-on experience demonstrates your ability to apply theoretical knowledge in a real-world setting.
Develop analytical and technical skills essential for supply chain roles, focusing on data analysis tools and software. Become proficient in Excel, including advanced functions and pivot tables, and consider learning SQL or data visualization tools like Tableau. These skills are critical for interpreting supply chain data, identifying inefficiencies, and making informed decisions.
Create a professional portfolio or resume that highlights your acquired skills, certifications, and project experiences. Quantify your achievements whenever possible, such as "reduced inventory discrepancies by 15%" or "optimized shipping routes, saving 10% on transportation costs." This documentation provides concrete evidence of your capabilities to potential employers.
Actively network with supply chain professionals through LinkedIn, industry events, and professional associations like ASCM (formerly APICS) or CSCMP. Informational interviews can provide insights into specific roles and companies, and often lead to referrals or direct opportunities. Building a strong professional network is vital for discovering hidden job opportunities and gaining mentorship.
Prepare for job applications and interviews by researching common supply chain challenges and solutions. Practice articulating your problem-solving approach and how your skills align with specific job descriptions. Be ready to discuss case studies related to inventory optimization, supplier management, or demand forecasting, demonstrating your strategic thinking.
Target entry-level positions such as Supply Chain Analyst, Logistics Coordinator, or Inventory Specialist to gain initial industry experience. Be open to roles in various industries, as supply chain principles are transferable. Focus on companies that offer growth opportunities and a chance to work with diverse aspects of the supply chain.
Step 1
Build a foundational understanding of supply chain principles by pursuing a relevant certification or online course. Consider certifications like APICS CSCP or CPIM, or comprehensive Coursera/edX specializations that cover logistics, procurement, and operations. This initial knowledge provides a strong conceptual framework for future learning and practical application.
Step 2
Gain practical experience through internships, entry-level logistics roles, or volunteer projects that involve inventory management or process optimization. Seek opportunities to work with enterprise resource planning (ERP) systems like SAP or Oracle, even in a limited capacity. Hands-on experience demonstrates your ability to apply theoretical knowledge in a real-world setting.
Step 3
Develop analytical and technical skills essential for supply chain roles, focusing on data analysis tools and software. Become proficient in Excel, including advanced functions and pivot tables, and consider learning SQL or data visualization tools like Tableau. These skills are critical for interpreting supply chain data, identifying inefficiencies, and making informed decisions.
Step 4
Create a professional portfolio or resume that highlights your acquired skills, certifications, and project experiences. Quantify your achievements whenever possible, such as "reduced inventory discrepancies by 15%" or "optimized shipping routes, saving 10% on transportation costs." This documentation provides concrete evidence of your capabilities to potential employers.
Step 5
Actively network with supply chain professionals through LinkedIn, industry events, and professional associations like ASCM (formerly APICS) or CSCMP. Informational interviews can provide insights into specific roles and companies, and often lead to referrals or direct opportunities. Building a strong professional network is vital for discovering hidden job opportunities and gaining mentorship.
Step 6
Prepare for job applications and interviews by researching common supply chain challenges and solutions. Practice articulating your problem-solving approach and how your skills align with specific job descriptions. Be ready to discuss case studies related to inventory optimization, supplier management, or demand forecasting, demonstrating your strategic thinking.
Step 7
Target entry-level positions such as Supply Chain Analyst, Logistics Coordinator, or Inventory Specialist to gain initial industry experience. Be open to roles in various industries, as supply chain principles are transferable. Focus on companies that offer growth opportunities and a chance to work with diverse aspects of the supply chain.
Education & Training Needed to Become a Supply Chain Manager
The educational landscape for a Supply Chain Manager is diverse, reflecting the role's blend of strategic planning, logistics, and data analysis. Formal university degrees, such as a Bachelor's or Master's in Supply Chain Management, Logistics, or Business Administration with a supply chain specialization, are highly valued. A four-year bachelor's degree typically costs between $40,000 and $100,000 or more, requiring four years of full-time study. Master's programs, often 1-2 years, range from $30,000 to over $80,000.
Alternative learning paths, like professional certifications and specialized online courses, offer flexibility and focused skill development. Certifications such as CSCP or CPIM from APICS (now ASCM) are widely recognized and demonstrate industry-specific expertise. These certifications usually involve 6-18 months of self-study or structured courses, costing $2,000-$5,000 including exam fees. Bootcamps specifically for supply chain are less common but emerging, typically lasting 12-24 weeks and costing $10,000-$20,000. Employers generally perceive formal degrees as foundational, while certifications validate practical, current skills.
Continuous learning is crucial for Supply Chain Managers due to evolving technologies and global market dynamics. Educational needs vary by specialization; for instance, a manager focused on procurement might prioritize different training than one in logistics optimization. Practical experience, often gained through internships or entry-level roles, complements theoretical knowledge from educational programs. Emerging trends include programs focused on supply chain analytics, blockchain, and sustainable practices. Investing in accredited programs or widely recognized certifications offers a strong cost-benefit, enhancing career progression and earning potential.
Supply Chain Manager Salary & Outlook
Compensation for a Supply Chain Manager varies significantly based on several factors. Geographic location plays a crucial role; major logistics hubs and areas with high manufacturing or distribution activity often command higher salaries due to increased demand and cost of living. For instance, a manager in California or New York typically earns more than one in a lower cost-of-living state.
Years of experience, the complexity of supply chain operations managed, and specialized skills in areas like global logistics, supply chain analytics, or sustainable practices directly impact earning potential. Companies managing intricate global networks or those requiring advanced technological integration often pay a premium for specialized expertise.
Total compensation packages extend beyond base salary. They frequently include performance-based bonuses, stock options or equity in larger corporations, and comprehensive benefits such as health insurance, retirement contributions, and professional development allowances. The industry also influences pay; supply chain managers in high-tech, pharmaceutical, or automotive sectors may see higher compensation compared to those in retail or consumer goods.
Negotiation leverage comes from demonstrating a clear track record of cost savings, efficiency improvements, and risk mitigation. Remote work has also introduced new dynamics, allowing some managers to command competitive salaries while residing in lower cost-of-living areas, though some companies adjust pay based on location.
While salary figures are often quoted in USD, it is important to acknowledge that international markets present their own unique compensation structures, influenced by local economic conditions, labor laws, and industry specifics.
Salary by Experience Level
Level | US Median | US Average |
---|---|---|
Junior Supply Chain Manager | $70k USD | $75k USD |
Supply Chain Manager | $100k USD | $105k USD |
Senior Supply Chain Manager | $130k USD | $135k USD |
Supply Chain Director | $165k USD | $175k USD |
VP of Supply Chain | $210k USD | $220k USD |
Chief Supply Chain Officer (CSCO) | $285k USD | $300k USD |
Market Commentary
The job market for Supply Chain Managers remains robust, driven by the increasing complexity of global trade, e-commerce expansion, and the ongoing need for operational efficiency. The Bureau of Labor Statistics projects a steady growth for logisticians, which includes supply chain managers, with an outlook of 4% growth from 2022 to 2032. This translates to approximately 7,100 new jobs over the decade, reflecting a consistent demand across various industries.
Current trends emphasize resilience, sustainability, and digital transformation within supply chains. Companies are actively seeking managers who can implement advanced analytics, AI, and automation to optimize processes and mitigate disruptions. The COVID-19 pandemic highlighted the critical importance of adaptable supply chains, further solidifying the role's strategic value. This has led to a demand for professionals skilled in risk management, supplier diversification, and end-to-end visibility.
Supply and demand dynamics are relatively balanced, but there is a growing need for managers with strong technological acumen and strategic planning capabilities. Geographic hotspots for these roles include major port cities, manufacturing hubs, and large distribution centers. The increasing adoption of remote or hybrid work models also expands the talent pool, though on-site presence remains crucial for certain operational roles.
Future-proofing this career involves continuous learning in areas like blockchain for supply chain transparency, predictive analytics, and green logistics. While automation and AI will handle routine tasks, the strategic oversight, problem-solving, and relationship management aspects of a Supply Chain Manager role are largely recession-resistant and difficult to automate, ensuring long-term viability and growth opportunities within the field.
Supply Chain Manager Career Path
Career progression for a Supply Chain Manager involves a blend of operational excellence, strategic planning, and leadership development. Professionals typically begin by mastering core supply chain functions before transitioning to more complex, strategic roles. Advancement pathways include both individual contributor (IC) tracks, focusing on specialized areas like logistics or procurement, and management tracks, which involve leading teams and entire supply chain operations.
Advancement speed depends on performance, the ability to drive cost efficiencies, and proficiency in adopting new technologies. Specialization in areas such as global logistics, demand planning, or sustainable supply chains can accelerate progression. Company size and industry also shape career paths; startups often offer broader responsibilities earlier, while large corporations provide deeper specialization and more formal leadership pipelines. Economic conditions and global events significantly impact supply chain dynamics, requiring adaptability and continuous learning for professionals in this field.
Networking, mentorship, and building a strong industry reputation through successful project delivery are vital for career advancement. Certifications like CSCP or CPIM mark significant professional milestones. Lateral moves into related fields like operations, finance, or even IT are common, allowing for a broader understanding of business functions and preparing individuals for executive leadership. Continuous skill development, especially in data analytics, automation, and risk management, remains crucial throughout a supply chain career.
Junior Supply Chain Manager
0-2 yearsManage specific operational tasks within the supply chain, such as tracking shipments, processing orders, or managing inventory levels for a particular product line. Support senior managers in data analysis and report generation. Contribute to process improvement initiatives within a limited scope, often under direct supervision.
Key Focus Areas
Develop foundational skills in inventory management, logistics coordination, and procurement processes. Learn to use supply chain software and tools effectively. Focus on understanding internal procedures and cross-functional team dynamics. Building strong communication skills is essential for effective collaboration.
Supply Chain Manager
2-5 yearsOversee a specific segment of the supply chain, such as warehousing operations, transportation, or a key supplier relationship. Make day-to-day operational decisions and implement solutions to logistical challenges. Manage a small team or cross-functional project group. Ensure adherence to budgets and performance metrics for their area of responsibility.
Key Focus Areas
Strengthen analytical and problem-solving skills, particularly in demand forecasting and supply optimization. Develop project management capabilities to lead small to medium-sized initiatives. Focus on stakeholder management and negotiating with suppliers. Begin to understand the financial implications of supply chain decisions.
Senior Supply Chain Manager
5-8 yearsManage complex supply chain projects and lead cross-functional teams to optimize end-to-end processes. Develop and implement strategies for cost reduction, efficiency improvements, and risk mitigation across multiple supply chain functions. Influence key stakeholders and contribute to departmental goal setting. Oversee a larger budget and multiple operational areas.
Key Focus Areas
Cultivate strategic thinking and long-term planning abilities. Develop advanced negotiation and contract management skills. Focus on process re-engineering and implementing new supply chain technologies like AI or blockchain. Mentor junior staff and contribute to talent development within the department.
Supply Chain Director
8-12 yearsDirect the entire supply chain function for a business unit or a significant regional operation. Develop and execute long-term supply chain strategies that align with corporate objectives. Lead large teams of supply chain professionals, including managers and specialists. Responsible for overall supply chain performance, budget, and compliance.
Key Focus Areas
Develop robust leadership and change management skills. Focus on strategic vendor relationships and global supply chain design. Cultivate financial acumen to align supply chain initiatives with overall business profitability. Build a strong external network and stay abreast of industry trends and innovations.
VP of Supply Chain
12-18 yearsOversee the complete supply chain strategy and operations across an entire organization or major division. Drive strategic initiatives related to supply chain resilience, innovation, and competitive advantage. Responsible for the overall performance, P&L, and strategic direction of the supply chain function. Report directly to the C-suite.
Key Focus Areas
Refine executive leadership, strategic foresight, and organizational development skills. Focus on enterprise-wide supply chain transformation and digital initiatives. Develop expertise in global trade compliance, geopolitical risk, and sustainability practices. Represent the supply chain function at the executive level and influence corporate strategy.
Chief Supply Chain Officer (CSCO)
18+ yearsHold ultimate responsibility for the company's entire global supply chain strategy, operations, and performance. Serve as a key member of the executive leadership team, influencing overall business strategy and direction. Drive innovation and digital transformation across the supply chain. Ensure the supply chain supports corporate growth, profitability, and sustainability goals.
Key Focus Areas
Master enterprise-level strategic planning, corporate governance, and investor relations related to supply chain. Develop unparalleled leadership in navigating complex global economic and political landscapes. Focus on integrating supply chain strategy with overall corporate vision and driving sustainable competitive advantage. Cultivate a reputation as a thought leader in the industry.
Junior Supply Chain Manager
0-2 yearsManage specific operational tasks within the supply chain, such as tracking shipments, processing orders, or managing inventory levels for a particular product line. Support senior managers in data analysis and report generation. Contribute to process improvement initiatives within a limited scope, often under direct supervision.
Key Focus Areas
Develop foundational skills in inventory management, logistics coordination, and procurement processes. Learn to use supply chain software and tools effectively. Focus on understanding internal procedures and cross-functional team dynamics. Building strong communication skills is essential for effective collaboration.
Supply Chain Manager
2-5 yearsOversee a specific segment of the supply chain, such as warehousing operations, transportation, or a key supplier relationship. Make day-to-day operational decisions and implement solutions to logistical challenges. Manage a small team or cross-functional project group. Ensure adherence to budgets and performance metrics for their area of responsibility.
Key Focus Areas
Strengthen analytical and problem-solving skills, particularly in demand forecasting and supply optimization. Develop project management capabilities to lead small to medium-sized initiatives. Focus on stakeholder management and negotiating with suppliers. Begin to understand the financial implications of supply chain decisions.
Senior Supply Chain Manager
5-8 yearsManage complex supply chain projects and lead cross-functional teams to optimize end-to-end processes. Develop and implement strategies for cost reduction, efficiency improvements, and risk mitigation across multiple supply chain functions. Influence key stakeholders and contribute to departmental goal setting. Oversee a larger budget and multiple operational areas.
Key Focus Areas
Cultivate strategic thinking and long-term planning abilities. Develop advanced negotiation and contract management skills. Focus on process re-engineering and implementing new supply chain technologies like AI or blockchain. Mentor junior staff and contribute to talent development within the department.
Supply Chain Director
8-12 yearsDirect the entire supply chain function for a business unit or a significant regional operation. Develop and execute long-term supply chain strategies that align with corporate objectives. Lead large teams of supply chain professionals, including managers and specialists. Responsible for overall supply chain performance, budget, and compliance.
Key Focus Areas
Develop robust leadership and change management skills. Focus on strategic vendor relationships and global supply chain design. Cultivate financial acumen to align supply chain initiatives with overall business profitability. Build a strong external network and stay abreast of industry trends and innovations.
VP of Supply Chain
12-18 yearsOversee the complete supply chain strategy and operations across an entire organization or major division. Drive strategic initiatives related to supply chain resilience, innovation, and competitive advantage. Responsible for the overall performance, P&L, and strategic direction of the supply chain function. Report directly to the C-suite.
Key Focus Areas
Refine executive leadership, strategic foresight, and organizational development skills. Focus on enterprise-wide supply chain transformation and digital initiatives. Develop expertise in global trade compliance, geopolitical risk, and sustainability practices. Represent the supply chain function at the executive level and influence corporate strategy.
Chief Supply Chain Officer (CSCO)
18+ yearsHold ultimate responsibility for the company's entire global supply chain strategy, operations, and performance. Serve as a key member of the executive leadership team, influencing overall business strategy and direction. Drive innovation and digital transformation across the supply chain. Ensure the supply chain supports corporate growth, profitability, and sustainability goals.
Key Focus Areas
Master enterprise-level strategic planning, corporate governance, and investor relations related to supply chain. Develop unparalleled leadership in navigating complex global economic and political landscapes. Focus on integrating supply chain strategy with overall corporate vision and driving sustainable competitive advantage. Cultivate a reputation as a thought leader in the industry.
Job Application Toolkit
Ace your application with our purpose-built resources:
Supply Chain Manager Resume Examples
Proven layouts and keywords hiring managers scan for.
View examplesSupply Chain Manager Cover Letter Examples
Personalizable templates that showcase your impact.
View examplesTop Supply Chain Manager Interview Questions
Practice with the questions asked most often.
View examplesSupply Chain Manager Job Description Template
Ready-to-use JD for recruiters and hiring teams.
View examplesGlobal Supply Chain Manager Opportunities
Supply Chain Managers oversee global logistics, procurement, and distribution networks. This role translates directly across borders, with high demand in manufacturing, retail, and e-commerce sectors worldwide. International job market trends for 2025 show robust growth, driven by digitalization and resilience needs. Cultural nuances affect supplier relations and regulatory differences impact compliance. Professionals consider international roles for diverse challenges and market exposure. APICS CSCP or SCOR certifications enhance global mobility.
Global Salaries
Global salaries for Supply Chain Managers vary significantly by region and experience. In North America, particularly the US, annual salaries range from $90,000 to $140,000 USD, often including performance bonuses. Canadian counterparts typically earn $75,000 to $120,000 CAD (approx. $55,000-$90,000 USD).
European markets offer diverse compensation. A Supply Chain Manager in Germany might earn €60,000 to €95,000 (approx. $65,000-$105,000 USD), while in the UK, salaries range from £50,000 to £85,000 (approx. $63,000-$107,000 USD). These figures reflect strong purchasing power in these economies, though higher taxes impact take-home pay.
In Asia-Pacific, salaries range from $45,000 to $80,000 USD in countries like Singapore or Australia, though local currency equivalents are higher, such as AUD 70,000-120,000. China's growing market sees salaries between CNY 250,000-500,000 (approx. $35,000-$70,000 USD), with lower cost of living. Latin America, like Brazil or Mexico, offers $30,000-$60,000 USD equivalents, with benefits often forming a larger part of total compensation.
Experience and education transfer directly impacts compensation. An MBA or specific industry expertise can command higher pay globally. International pay scales are not standardized, but larger multinational corporations often have internal frameworks. Local tax structures and social security contributions significantly alter net income across countries, requiring careful financial planning.
Remote Work
Supply Chain Managers have limited but growing international remote work potential. Many aspects of the role, like site visits and direct team leadership, require physical presence. However, strategic planning, analytics, and vendor management can be performed remotely.
Legal and tax implications for international remote work are complex, involving permanent establishment risks for employers and individual tax residency rules. Time zone differences often pose challenges for global team collaboration, requiring flexible working hours. Digital nomad opportunities for this role are uncommon due to the hands-on nature.
Some global companies offer hybrid models or allow remote work within the same country. Fully international remote roles are rare, primarily limited to very senior strategic or advisory positions. Salary expectations in remote roles may be adjusted based on the employee's location and cost of living. Reliable internet and a dedicated home office setup are essential for any remote arrangement.
Visa & Immigration
Supply Chain Managers often qualify for skilled worker visas in popular destination countries. Nations like Canada, Australia, Germany, and the UK have specific immigration pathways for professionals in demand. Requirements typically include a relevant bachelor's degree, several years of experience, and a job offer from a local employer.
Education credential recognition is crucial; applicants often need their degrees assessed for equivalency. Professional licensing is generally not required for Supply Chain Managers. Visa timelines vary from a few weeks to several months, depending on the country and visa type. The application process usually involves submitting documented qualifications, work experience, and financial stability proofs.
Some countries offer pathways to permanent residency after a few years of skilled employment. Language proficiency, often English or the local language, is a common requirement for immigration. Family visas for spouses and dependents are generally available, allowing them to accompany the primary applicant. There are no specific fast-track programs solely for Supply Chain Managers, but their occupation often appears on national skilled occupation lists.
2025 Market Reality for Supply Chain Managers
Understanding the current market realities for Supply Chain Managers is critical for career progression. The field has evolved significantly from 2023 to 2025, driven by post-pandemic disruptions and the rapid adoption of AI.
Broader economic factors, such as inflation and geopolitical instability, directly impact supply chain resilience and, consequently, the demand for skilled managers. Market conditions vary by experience level, with senior roles often requiring specialized tech integration skills, and by geographic region, depending on industrial concentration. This analysis provides an honest assessment to help you navigate these complex dynamics.
Current Challenges
Supply Chain Managers face increased competition, especially for remote roles. Many companies now expect candidates to manage advanced AI-driven planning tools, creating a skill gap for those without this specific expertise.
Economic uncertainty causes companies to optimize existing operations rather than expand, leading to fewer new positions. Job searches can extend for several months due to these factors and the high demand for specialized skills.
Growth Opportunities
Strong opportunities exist for Supply Chain Managers specializing in AI-driven optimization and sustainable practices. Companies seek professionals who can implement predictive analytics for demand forecasting and automate inventory management.
Emerging roles in 'resilience management' and 'digital supply chain transformation' are gaining traction. Professionals with expertise in integrating IoT, blockchain, and machine learning into logistics operations hold a significant competitive advantage.
Underserved markets in specialized manufacturing or rapidly expanding e-commerce sectors offer promising prospects. Certain skills, like proficiency with advanced planning software (e.g., SAP IBP, Kinaxis) and experience in circular economy models, are highly valued. Strategic career moves now involve upskilling in data science and AI applications to align with future industry needs.
Current Market Trends
Hiring for Supply Chain Managers shows consistent demand, particularly for professionals adept at navigating complex global logistics and integrating advanced technologies. Companies prioritize resilience and efficiency, making managers who can optimize end-to-end processes highly valuable.
The integration of generative AI and automation is reshaping the supply chain landscape. Employers increasingly seek managers capable of implementing AI-powered forecasting, optimizing inventory, and automating routine tasks. This shift means a deeper understanding of data analytics and predictive modeling is now essential, moving beyond traditional operational oversight.
Economic conditions influence hiring, with some sectors experiencing cautious expansion while others focus on cost reduction. Layoffs in certain industries, particularly tech, have increased the pool of available talent, intensifying competition for top roles. Salaries remain strong for experienced managers with specialized tech skills, but entry-level positions face more saturation.
Geographically, demand is robust in major logistics hubs and manufacturing centers. Remote work options, while still present, are becoming less prevalent for senior roles as companies prefer on-site leadership for complex operational oversight. Seasonal patterns often see increased hiring before peak consumer periods, like holidays, to manage anticipated volume surges.
Emerging Specializations
The supply chain landscape undergoes continuous transformation, driven by rapid technological advancements and evolving global dynamics. Understanding these shifts creates new specialization opportunities for Supply Chain Managers. Early positioning in these emerging areas is crucial for career advancement from 2025 onwards. It allows professionals to become pioneers in high-demand fields.
Specializing in cutting-edge areas often commands premium compensation and accelerated career growth. These roles address complex, novel challenges that require unique expertise. While established specializations offer stability, emerging fields promise significant future impact and innovation. The timeline for these emerging areas to become mainstream can vary, but most show significant job opportunities within three to five years.
Pursuing cutting-edge specializations involves a balance of risk and reward. It requires continuous learning and adaptability, but the potential for leadership roles and substantial career gains is high. Strategic choices in specialization can define a Supply Chain Manager's trajectory, positioning them at the forefront of industry evolution rather than merely reacting to it.
AI & Predictive Analytics Supply Chain Manager
This specialization focuses on integrating AI and machine learning models into supply chain operations. It involves optimizing forecasting, inventory management, logistics routing, and predictive maintenance using advanced algorithms. The role ensures that AI solutions enhance efficiency, reduce costs, and improve decision-making across the entire supply network.
Sustainable & Circular Supply Chain Manager
This area addresses the increasing demand for sustainable and ethical supply chain practices. It involves designing and implementing strategies to minimize environmental impact, ensure fair labor practices, and enhance transparency throughout the supply chain. Managers in this role focus on circular economy principles, carbon footprint reduction, and ethical sourcing.
Blockchain & Traceability Supply Chain Manager
This specialization deals with integrating blockchain technology to enhance transparency, traceability, and security within the supply chain. It involves creating immutable records of transactions, product movements, and certifications. The goal is to build trust, reduce fraud, and improve auditability from raw materials to end consumer.
Cybersecurity & Resilience Supply Chain Manager
This role focuses on safeguarding supply chain operations from cyber threats, data breaches, and operational disruptions. It involves implementing robust cybersecurity protocols, developing resilience strategies against attacks, and ensuring data integrity across all digital touchpoints. This specialization is critical as supply chains become increasingly digitized and interconnected.
Robotics & IoT Integration Supply Chain Manager
This specialization involves managing the integration of advanced robotics, automation, and IoT devices within warehouses, factories, and logistics networks. It focuses on optimizing automated processes, deploying smart sensors for real-time data collection, and ensuring seamless communication between physical and digital supply chain components.
Pros & Cons of Being a Supply Chain Manager
Making informed career decisions requires a realistic understanding of both the advantages and challenges of a profession. The experience of a Supply Chain Manager can vary significantly based on the company's size, industry sector, and the specific products or services managed. Pros and cons may also shift as a career progresses, from entry-level roles to senior leadership positions. What one person perceives as a benefit, another might see as a drawback, depending on personal values, work style, and lifestyle preferences. This assessment aims to provide an honest, balanced perspective to help individuals set appropriate expectations for a career in supply chain management.
Pros
Supply Chain Managers are in high demand across nearly all industries, offering strong job security and diverse employment opportunities due to the critical nature of their function in business operations.
The role involves complex problem-solving, requiring strategic thinking to optimize processes, reduce costs, and improve efficiency, which provides significant intellectual stimulation and a sense of accomplishment.
Supply chain management offers clear career progression paths, from analyst roles to senior management or executive positions, with opportunities to specialize in areas like logistics, procurement, or operations.
Professionals gain a holistic understanding of a business, connecting various departments from manufacturing to sales, which provides valuable cross-functional experience and a broad business perspective.
The field embraces technological advancements, such as AI, automation, and data analytics, allowing managers to work with cutting-edge tools and implement innovative solutions to complex logistical challenges.
Supply Chain Managers often have a tangible impact on a company's profitability and customer satisfaction, directly influencing operational success and contributing to the overall business strategy.
Networking opportunities are abundant, as the role requires collaboration with diverse internal teams, external vendors, and international partners, fostering a wide professional network.
Cons
Supply chain disruptions, such as natural disasters, geopolitical events, or sudden demand shifts, often create high-pressure situations requiring rapid problem-solving and extended work hours to mitigate impact.
Balancing cost efficiency with customer service expectations is a constant challenge, as managers must optimize logistics while ensuring timely delivery and product availability, often with conflicting priorities.
Managing a complex network of suppliers, manufacturers, distributors, and retailers requires significant coordination and communication skills, and missteps in one area can cascade throughout the entire chain.
The role demands continuous adaptation to new technologies, global regulations, and evolving consumer behaviors, necessitating ongoing learning and strategic adjustments to maintain competitive advantage.
Supply chain managers frequently face intense pressure to reduce operational costs, which can lead to difficult decisions regarding resource allocation, vendor relationships, and process improvements.
Travel is often required to visit suppliers, distribution centers, or international partners, which can impact work-life balance, especially for those overseeing global supply networks.
The work environment can be highly analytical and data-driven, which might feel isolating for individuals who prefer more creative or less structured roles, as decisions are heavily reliant on metrics and performance indicators.
Frequently Asked Questions
Supply Chain Managers face unique challenges balancing logistics, procurement, and stakeholder communication. This section addresses common questions about entering this dynamic field, from required skills and certifications to managing global disruptions and leveraging technology for efficiency.
How long does it take to become a Supply Chain Manager if I'm starting from scratch?
Becoming an entry-level Supply Chain Manager typically takes 2-4 years, often through a bachelor's degree in supply chain management, logistics, or business. Many professionals start in coordinator or analyst roles for 1-2 years to gain practical experience before moving into management. Certifications like CSCP or CPIM can accelerate career progression by demonstrating specialized knowledge and commitment to the field.
Do I need a specific supply chain degree to become a Supply Chain Manager?
While a specific supply chain degree is beneficial, it is not always mandatory. Many successful Supply Chain Managers hold degrees in business, engineering, economics, or even liberal arts. What matters most is developing strong analytical, problem-solving, and communication skills, often complemented by relevant certifications or practical experience in logistics, operations, or procurement roles.
What are the typical salary expectations for a Supply Chain Manager?
Entry-level Supply Chain Managers can expect a starting salary range of $60,000 to $80,000 annually, depending on location, industry, and company size. With 3-5 years of experience, this can increase to $80,000-$120,000. Senior or specialized roles, especially in large corporations or complex global supply chains, can command salaries exceeding $150,000.
What is the typical work-life balance for a Supply Chain Manager?
The work-life balance for a Supply Chain Manager can vary significantly. During normal operations, it is often a standard 40-50 hour work week, but crises like global disruptions, inventory shortages, or urgent deadlines can demand longer hours. Flexibility is key, as managing a global supply chain may involve early morning or late-night calls to coordinate with international teams and suppliers.
Is the Supply Chain Manager role in high demand, and what is the job security like?
The demand for skilled Supply Chain Managers remains strong and is projected to grow. Globalization, e-commerce expansion, and the increasing complexity of logistics networks ensure a steady need for professionals who can optimize operations and mitigate risks. Companies across almost every industry rely on efficient supply chains, making this a stable and forward-looking career choice.
What are the career advancement opportunities for a Supply Chain Manager?
Yes, the Supply Chain Manager role offers significant career growth. You can advance to Senior Supply Chain Manager, Director of Logistics, or Vice President of Global Supply Chain. Specialization in areas like procurement, demand planning, or supply chain analytics also opens doors to expert roles. Many also transition into consulting or executive leadership positions within operations.
What are the biggest challenges or frustrations that Supply Chain Managers typically face?
The biggest challenges include managing unexpected disruptions like natural disasters or geopolitical events, dealing with rising transportation costs, and ensuring ethical sourcing across complex global networks. Supply Chain Managers must also adapt to rapid technological advancements, integrate new software, and effectively manage diverse teams and demanding stakeholders.
Can Supply Chain Managers work remotely, or is it primarily an in-office role?
Remote work flexibility for Supply Chain Managers depends heavily on the company and the specific responsibilities. Roles focused on strategic planning, data analysis, or supplier relationship management might offer more remote options. However, positions requiring hands-on oversight of warehouses, manufacturing, or direct logistics coordination often necessitate significant on-site presence or travel.
Related Careers
Explore similar roles that might align with your interests and skills:
Logistics Manager
A growing field with similar skill requirements and career progression opportunities.
Explore career guideSupply Chain
A growing field with similar skill requirements and career progression opportunities.
Explore career guideSupply Chain Coordinator
A growing field with similar skill requirements and career progression opportunities.
Explore career guideSupply Chain Specialist
A growing field with similar skill requirements and career progression opportunities.
Explore career guideSupply Manager
A growing field with similar skill requirements and career progression opportunities.
Explore career guideAssess your Supply Chain Manager readiness
Understanding where you stand today is the first step toward your career goals. Our Career Coach helps identify skill gaps and create personalized plans.
Skills Gap Analysis
Get a detailed assessment of your current skills versus Supply Chain Manager requirements. Our AI Career Coach identifies specific areas for improvement with personalized recommendations.
See your skills gapCareer Readiness Assessment
Evaluate your overall readiness for Supply Chain Manager roles with our AI Career Coach. Receive personalized recommendations for education, projects, and experience to boost your competitiveness.
Assess your readinessLand your dream job with Himalayas Plus
Upgrade to unlock Himalayas' premium features and turbocharge your job search.
Himalayas
Himalayas Plus
Himalayas Max
Find your dream job
Sign up now and join over 100,000 remote workers who receive personalized job alerts, curated job matches, and more for free!
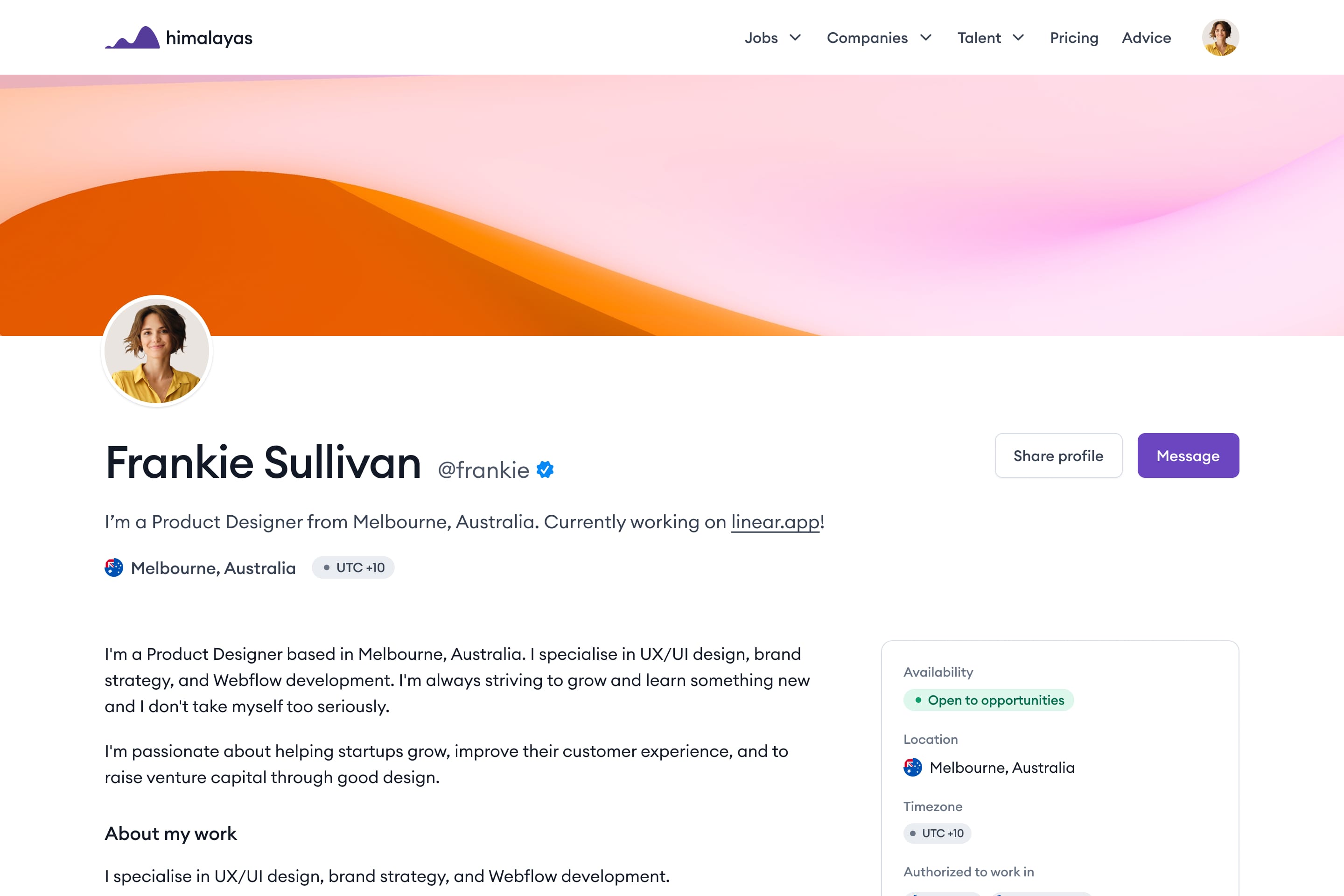