6 Die Maker Interview Questions and Answers
Die Makers are skilled tradespeople who design, construct, and repair dies used in manufacturing processes. They work with precision tools and machinery to create molds and dies that shape materials into specific forms. Junior roles focus on learning and assisting with basic tasks, while senior and lead roles involve overseeing projects, mentoring apprentices, and ensuring the quality and efficiency of die-making operations. Need to practice for an interview? Try our AI interview practice for free then unlock unlimited access for just $9/month.
Unlimited interview practice for $9 / month
Improve your confidence with an AI mock interviewer.
No credit card required
1. Apprentice Die Maker Interview Questions and Answers
1.1. Can you explain the process you follow to create a die from the initial design to the final product?
Introduction
This question is crucial for assessing your technical knowledge and understanding of the die-making process, which is essential for an Apprentice Die Maker.
How to answer
- Start by outlining the steps in the die-making process, from design interpretation to fabrication
- Mention the tools and machinery you would use at each stage
- Explain how you ensure precision and quality throughout the process
- Discuss any safety protocols you follow while operating machinery
- If applicable, reference any past experiences or projects related to die making
What not to say
- Providing vague or incomplete descriptions of the die-making process
- Failing to mention tools or machinery relevant to the role
- Neglecting the importance of safety measures
- Avoiding discussion of quality control practices
Example answer
“When creating a die, I start by analyzing the design specifications to ensure I understand the requirements. I then proceed to select appropriate materials before moving to the machining phase, where I use CNC machines to shape the die. Throughout this process, I maintain close attention to detail, checking tolerances regularly. Safety is paramount, so I always wear protective gear and follow operational guidelines. This methodical approach ensures a high-quality final product.”
Skills tested
Question type
1.2. Describe a challenging situation you encountered in a previous project or apprenticeship, and how you handled it.
Introduction
This question evaluates your problem-solving abilities and resilience, which are vital traits for an Apprentice Die Maker who may face challenges in the workshop.
How to answer
- Use the STAR method to structure your response (Situation, Task, Action, Result)
- Clearly describe the challenge you faced and its context
- Explain the actions you took to address the issue
- Highlight any collaboration with team members or supervisors
- Detail the outcomes and what you learned from the experience
What not to say
- Blaming others for the challenge without taking responsibility
- Providing unclear or overly simplistic solutions
- Failing to demonstrate learning or growth from the experience
- Neglecting the importance of teamwork or support
Example answer
“During my apprenticeship, I was tasked with fabricating a die for a complex component. Halfway through, I realized I had misinterpreted the design. I immediately consulted with my supervisor to reassess the situation and we devised a plan to correct the misalignment. By reworking the die, we not only met the deadline but also improved the design's functionality. This experience taught me the importance of clear communication and verifying information early on.”
Skills tested
Question type
2. Junior Die Maker Interview Questions and Answers
2.1. Can you describe your experience with operating and maintaining die-making machinery?
Introduction
This question assesses your technical skills and familiarity with machinery, which are crucial for a Junior Die Maker role.
How to answer
- Begin by specifying the types of machinery you have worked with.
- Discuss any formal training or apprenticeships you have completed.
- Explain your daily responsibilities regarding machine operation and maintenance.
- Highlight any troubleshooting experiences you have had with machinery.
- Mention any safety protocols you follow while operating equipment.
What not to say
- Claiming to have experience with machinery you have not operated.
- Being vague about your responsibilities and tasks.
- Not mentioning safety practices or protocols.
- Failing to discuss your approach to maintenance and troubleshooting.
Example answer
“In my apprenticeship at a local manufacturing firm, I operated CNC milling machines and hydraulic presses. I was responsible for daily checks and routine maintenance, which included lubricating parts and replacing worn tools. I also learned to troubleshoot minor issues, which improved my understanding of machine operation. Safety was paramount; I always followed the established protocols to ensure a safe working environment.”
Skills tested
Question type
2.2. Describe a time when you faced a challenge while working on a die-making project. What was the issue, and how did you resolve it?
Introduction
This question evaluates your problem-solving abilities and how you respond to challenges, which are essential in a production environment.
How to answer
- Use the STAR method (Situation, Task, Action, Result) to structure your response.
- Clearly outline the challenge you faced and its impact on the project.
- Describe the steps you took to resolve the issue.
- Highlight the outcome of your actions and any lessons learned.
- Emphasize collaboration with team members if applicable.
What not to say
- Focusing only on the problem without discussing your resolution.
- Blaming others for the challenge without taking responsibility.
- Providing a vague answer without specific details.
- Neglecting to mention teamwork or collaboration.
Example answer
“During my internship, I worked on a project where a die was not producing parts to the required specifications. I identified that the problem was due to incorrect alignment. I gathered the team to discuss the issue and we re-evaluated the setup. After realigning the die, we conducted tests and achieved the desired precision. This experience taught me the importance of quick assessment and teamwork in overcoming production challenges.”
Skills tested
Question type
2.3. What steps do you take to ensure the quality of the dies you produce?
Introduction
This question is crucial because quality assurance is vital in die-making to prevent defects and ensure customer satisfaction.
How to answer
- Discuss your understanding of quality standards in die-making.
- Explain the processes you follow to check quality during and after production.
- Mention any measurement tools or techniques you use.
- Highlight your commitment to continuous improvement and feedback.
- Provide examples of how you've implemented quality checks in past projects.
What not to say
- Suggesting quality checks are not important.
- Failing to provide specific examples or processes.
- Indicating that you rely solely on others for quality assurance.
- Neglecting to mention any tools or techniques used.
Example answer
“I believe quality starts with understanding the specifications for each die. I regularly perform in-process inspections using calipers and gauges to ensure dimensions are within tolerance. After production, I conduct a final quality check before any dies leave the workshop. I also encourage feedback from my supervisors to identify areas for improvement. In my previous role, implementing these checks helped reduce defects by 15%.”
Skills tested
Question type
3. Die Maker Interview Questions and Answers
3.1. Can you describe a challenging die-making project you worked on and how you overcame the obstacles?
Introduction
This question assesses your problem-solving skills and technical expertise in die making, which are critical for ensuring precision and quality in manufacturing.
How to answer
- Use the STAR method to structure your response (Situation, Task, Action, Result)
- Clearly outline the specific challenges you faced during the project
- Explain the steps you took to address these challenges, highlighting your technical skills
- Discuss the outcome of your efforts and any lessons learned
- Mention how you ensured quality and adherence to specifications
What not to say
- Failing to provide specific details about the project or challenges
- Blaming others for the difficulties faced without taking responsibility
- Overemphasizing the challenges without discussing solutions
- Neglecting to mention the importance of teamwork and collaboration
Example answer
“In my previous role at a local manufacturing company, I faced a significant challenge with a die that was not producing parts to the required tolerances. The initial design had flaws that led to misalignment during production. I conducted a thorough analysis to identify the root cause and collaborated with my team to redesign the die. We implemented new machining techniques which improved precision by 30%. This experience taught me the importance of attention to detail and proactive problem-solving in die making.”
Skills tested
Question type
3.2. What measures do you take to ensure the quality and precision of your dies?
Introduction
This question evaluates your understanding of quality control processes and your commitment to producing high-quality dies, which is crucial in the manufacturing industry.
How to answer
- Discuss specific quality control measures you implement during the die-making process
- Mention any tools or technologies you use for quality assurance
- Explain how you document and track quality metrics
- Share examples of how you have improved quality in past projects
- Describe your approach to continuous improvement in die making
What not to say
- Providing vague answers without specific quality measures
- Ignoring the importance of documentation and tracking
- Overlooking the role of teamwork in maintaining quality
- Focusing solely on end results without mentioning the process
Example answer
“I ensure quality by implementing a multi-step quality control process. During the machining phase, I utilize precision measuring tools like micrometers and calipers to verify dimensions frequently. I also conduct visual inspections at critical stages and maintain detailed records of all measurements to track any deviations. For instance, in a project for a major automotive client, this rigorous process helped us achieve a 99% first-pass yield, significantly reducing rework and costs.”
Skills tested
Question type
4. Senior Die Maker Interview Questions and Answers
4.1. Can you describe a challenging die-making project you've worked on and how you overcame the obstacles?
Introduction
This question is crucial for assessing your problem-solving skills and technical expertise in die-making, which are essential for a Senior Die Maker role.
How to answer
- Use the STAR method to structure your response: Situation, Task, Action, Result.
- Clearly explain the specific project and the challenges faced, such as tight deadlines or complex designs.
- Detail the steps you took to address these challenges, including any innovative techniques or tools you used.
- Discuss the outcome, quantifying success with metrics if possible, such as reduced production time or increased quality.
- Reflect on what you learned from the experience and how it has shaped your approach to die-making.
What not to say
- Avoid vague descriptions of the project without detailing specific challenges.
- Do not take sole credit; acknowledge team collaboration if applicable.
- Refrain from focusing too much on the technical aspects without discussing problem-solving.
- Avoid negative tones; instead, focus on solutions and learning from the experience.
Example answer
“In my previous role at a leading automotive parts manufacturer, I worked on a die for a complex body panel that had a very tight tolerance requirement. We faced significant issues with material flow and die wear. I led a brainstorming session with the team to explore alternative materials and cooling methods. We decided to use a new alloy that improved durability and introduced a more effective cooling channel design. This not only reduced the defect rate by 30% but also increased our production rate by 20%. This experience taught me the importance of collaboration and innovation in overcoming challenges.”
Skills tested
Question type
4.2. How do you ensure quality control throughout the die-making process?
Introduction
This question assesses your understanding of quality assurance processes, which are critical in die-making to ensure precision and reliability.
How to answer
- Describe specific quality control measures you implement during the die-making process.
- Explain how you use tools and technology for inspections and measurements.
- Discuss the role of documentation and standards in maintaining quality.
- Share examples of how you handled quality issues in the past and the outcomes.
- Emphasize your commitment to continuous improvement and feedback loops.
What not to say
- Avoid overly simplistic answers that don’t demonstrate depth of knowledge.
- Do not suggest that quality checks are an afterthought; emphasize they are integral to the process.
- Refrain from mentioning only personal methods without discussing team and company standards.
- Avoid downplaying the importance of quality by suggesting that issues are inevitable.
Example answer
“At my previous company, I implemented a multi-tiered quality control process that included initial inspections during the design phase, in-process checks at each stage of production, and final inspections before shipping. I utilized CMM (Coordinate Measuring Machine) technology for precision measurements and maintained a quality control log for tracking defects. This proactive approach helped reduce defects by 25% and ensured that our dies consistently met customer specifications. I believe that quality is everyone’s responsibility, and I encourage team members to take ownership of their work.”
Skills tested
Question type
5. Lead Die Maker Interview Questions and Answers
5.1. Can you describe a challenging project where you had to design a die under tight deadlines?
Introduction
This question is crucial for evaluating your technical expertise and time management skills, especially given the fast-paced nature of die-making in manufacturing.
How to answer
- Use the STAR method to outline the situation, task, action, and result.
- Clearly define the project requirements and constraints you faced.
- Explain your design process, including software or tools used.
- Detail how you collaborated with other team members or departments.
- Quantify the impact of your work—such as production efficiency or reduced costs.
What not to say
- Vague descriptions without clear outcomes.
- Neglecting to mention the role of teamwork in success.
- Focusing solely on technical details without mentioning time management.
- Not addressing any challenges faced during the project.
Example answer
“In my role at Alfa Romeo, I was tasked with designing a die for a new automotive part with a three-week deadline. I initiated a design brainstorming session with my team and utilized CAD software to create prototypes quickly. We faced limitations in materials, but I proposed an alternative that resulted in a 20% reduction in production time. The collaboration led to a successful launch ahead of schedule and a 15% cost saving.”
Skills tested
Question type
5.2. How do you ensure quality and precision in your die-making process?
Introduction
This question assesses your commitment to quality and your methods for maintaining high standards in production, which are essential in the die-making industry.
How to answer
- Describe your quality control procedures and tools used.
- Explain how you integrate feedback and continuous improvement into your workflow.
- Provide examples of how you've handled quality issues in the past.
- Discuss training or mentoring others on quality standards.
- Mention certifications or standards you follow, like ISO.
What not to say
- Failing to mention specific quality control measures.
- Assuming that quality is solely the responsibility of the QC department.
- Describing a lack of follow-up on quality issues.
- Overlooking the importance of documentation and traceability.
Example answer
“At Fiat, I implemented a rigorous quality control system where each die was tested for precision before production. I utilized measurement tools like calipers and micrometers, and I trained my team on interpreting the results. When we encountered a defect in a die, I led a root cause analysis that not only resolved the issue but also improved our overall process by 30%. This commitment to quality ensured that we consistently met client specifications.”
Skills tested
Question type
6. Tool and Die Supervisor Interview Questions and Answers
6.1. Can you describe a time when you had to resolve a conflict between team members on the shop floor?
Introduction
This question is crucial for assessing your leadership and conflict resolution skills, which are essential for maintaining a harmonious and productive work environment as a Tool and Die Supervisor.
How to answer
- Use the STAR method to structure your response: Situation, Task, Action, Result.
- Clearly describe the conflict and its impact on the team's performance.
- Explain the steps you took to address the conflict, including communication and mediation strategies.
- Discuss the outcome and how it improved team dynamics or productivity.
- Reflect on what you learned and how you apply this knowledge in future situations.
What not to say
- Avoid blaming team members without taking responsibility for the situation.
- Don't provide vague answers without specific examples.
- Refrain from suggesting that conflicts are unimportant or should be ignored.
- Avoid discussing conflicts that were not resolved or resulted in negative outcomes.
Example answer
“In my previous role at Magna International, I encountered a conflict between two machinists regarding the proper setup of a die. The disagreement was affecting their productivity and the workflow. I facilitated a meeting where each could express their concerns and viewpoints. After listening, we collaboratively identified a solution that incorporated both of their ideas. This not only resolved the conflict but also improved the die setup process, resulting in a 15% increase in efficiency. I learned that active listening and collaboration are key in conflict resolution.”
Skills tested
Question type
6.2. How do you ensure the quality and precision of tools and dies produced by your team?
Introduction
Quality control is vital in tool and die manufacturing, and this question helps assess your knowledge of quality assurance processes and your ability to implement them effectively.
How to answer
- Discuss specific quality control measures you implement in the production process.
- Explain how you train and guide your team to adhere to quality standards.
- Share examples of tools or techniques you use for quality assurance, such as statistical process control or inspection routines.
- Highlight any experiences where you improved quality outcomes in your previous roles.
- Mention how you handle deviations from quality standards.
What not to say
- Avoid saying that quality control is not a priority for your team.
- Don't provide generic answers without specific methodologies.
- Refrain from blaming quality issues solely on team members without acknowledging process improvements.
- Avoid discussing quality assurance as an afterthought rather than an integral part of the production process.
Example answer
“At my previous position with Linamar, I implemented a rigorous quality assurance protocol that included daily inspections and the use of calibration tools for precision measurements. I trained my team on the importance of adhering to these standards and introduced a peer review system where team members checked each other's work. This approach led to a 20% reduction in rework and ensured that our tools met all specifications consistently. I believe that quality is everyone's responsibility, and fostering a culture of accountability is essential.”
Skills tested
Question type
Similar Interview Questions and Sample Answers
Simple pricing, powerful features
Upgrade to Himalayas Plus and turbocharge your job search.
Himalayas
Himalayas Plus
Himalayas Max
Find your dream job
Sign up now and join over 100,000 remote workers who receive personalized job alerts, curated job matches, and more for free!
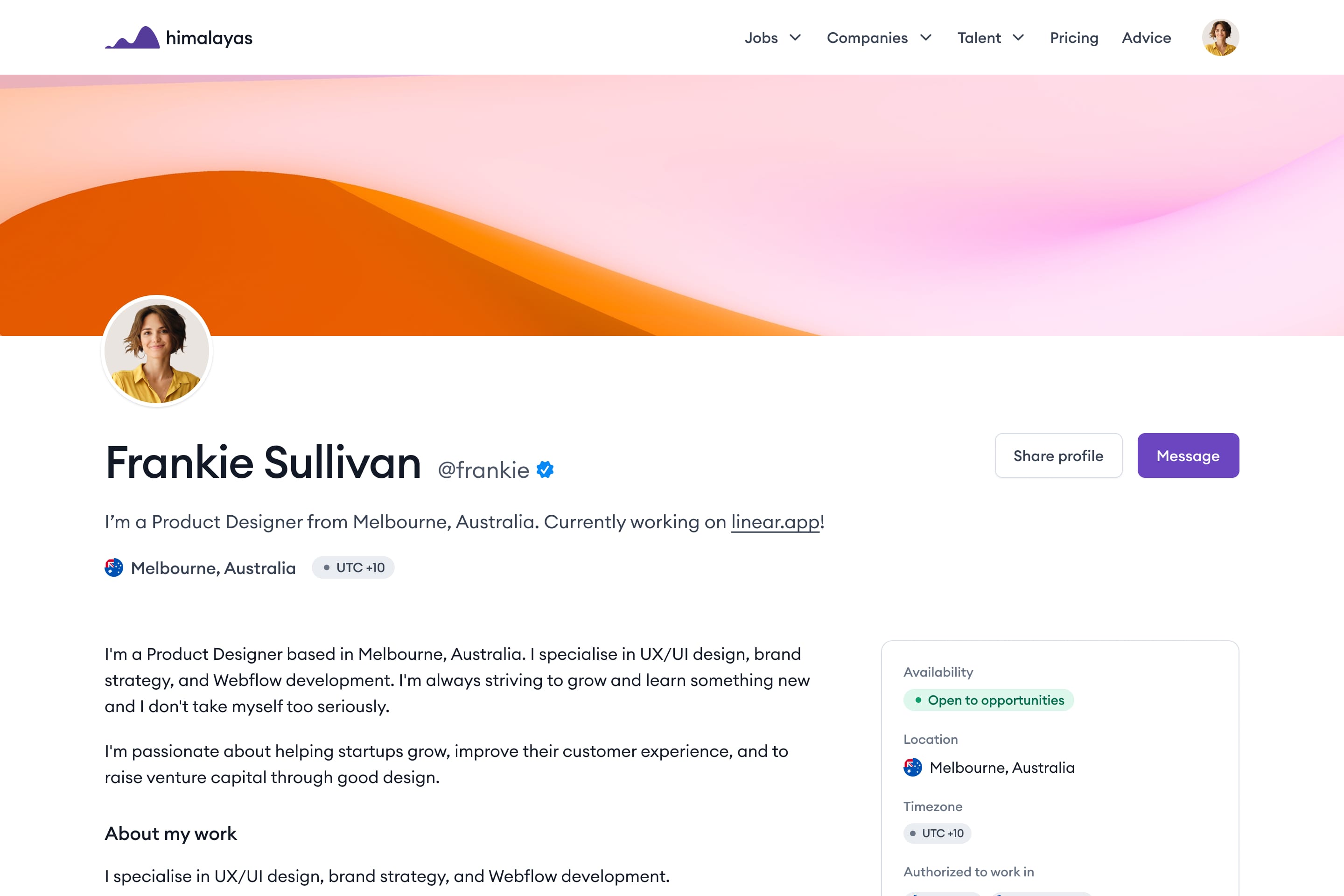