5 Line Operator Interview Questions and Answers
Line Operators are responsible for operating and maintaining machinery on production lines, ensuring the efficient and safe manufacturing of products. They monitor equipment, perform quality checks, and troubleshoot issues to minimize downtime. Junior operators focus on learning the basics of machine operation, while senior operators and leads oversee more complex tasks, mentor team members, and ensure production targets are met. Need to practice for an interview? Try our AI interview practice for free then unlock unlimited access for just $9/month.
Unlimited interview practice for $9 / month
Improve your confidence with an AI mock interviewer.
No credit card required
1. Junior Line Operator Interview Questions and Answers
1.1. Can you describe a time when you identified a problem during the production process and how you resolved it?
Introduction
This question is important for a Junior Line Operator as it assesses your problem-solving skills and ability to act proactively in a production environment.
How to answer
- Use the STAR method (Situation, Task, Action, Result) to structure your response
- Clearly describe the problem you identified, including its context
- Explain the steps you took to investigate and resolve the issue
- Highlight any collaboration with team members or supervisors
- Quantify the results of your actions, such as reduced downtime or improved efficiency
What not to say
- Failing to take responsibility for your role in the problem
- Describing a problem you didn't help to solve
- Focusing too much on blame rather than solution
- Providing vague examples without clear outcomes
Example answer
“During my training at a manufacturing plant, I noticed that a particular machine was frequently jamming, which was slowing down production. I reported it to my supervisor and suggested a minor adjustment to the settings based on my observations. After implementing the change, we saw a 20% reduction in jams, which significantly improved our output for the day.”
Skills tested
Question type
1.2. How do you prioritize your tasks when working on a busy production line?
Introduction
This question evaluates your time management and organizational skills, which are crucial for maintaining efficiency in a production environment.
How to answer
- Discuss your understanding of the workflow and production priorities
- Explain how you assess urgency and importance of tasks
- Describe any tools or methods you use to stay organized
- Mention how you communicate with your team to ensure everyone is aligned
- Share an example of a time when good prioritization led to a successful outcome
What not to say
- Claiming you don't have a method for prioritization
- Suggesting that you only focus on one task at a time
- Not mentioning teamwork or communication with others
- Providing examples that don't demonstrate effective prioritization
Example answer
“In my previous role, I prioritized tasks by first assessing the production schedule and identifying critical deadlines. I used a checklist to keep track of both urgent and important tasks, ensuring I communicated with my team about any changes. For instance, when we had a sudden surge in demand, my prioritization helped us meet our targets without compromising quality.”
Skills tested
Question type
2. Line Operator Interview Questions and Answers
2.1. Can you describe a time when you identified a safety hazard on the production line and how you addressed it?
Introduction
This question is crucial for assessing your awareness of safety protocols and your proactive approach to maintaining a safe working environment, which is vital for a Line Operator.
How to answer
- Use the STAR method to structure your response (Situation, Task, Action, Result)
- Clearly describe the safety hazard you observed
- Detail the steps you took to address the issue, including communication with supervisors or team members
- Highlight the outcomes of your actions, particularly in terms of improved safety or compliance
- Mention any follow-up actions taken to ensure similar issues were avoided in the future
What not to say
- Failing to recognize the importance of safety in the workplace
- Downplaying the significance of the hazard or your response
- Not providing a specific example or being vague about your actions
- Avoiding responsibility or not mentioning how you communicated with others
Example answer
“At a previous job at Coca-Cola, I noticed that a loose guard on a conveyor belt posed a risk to my colleagues. I immediately reported it to my supervisor and stopped the line to prevent any accidents. We conducted a quick team meeting to ensure everyone was aware of the hazard, and I followed up to make sure the guard was fixed. This proactive approach led to a safer working environment and reinforced the importance of vigilance among my team.”
Skills tested
Question type
2.2. How do you handle repetitive tasks and maintain focus on the production line?
Introduction
This question evaluates your ability to maintain productivity and quality in a role that often involves repetitive tasks, which is essential for a Line Operator.
How to answer
- Discuss techniques you use to stay focused and motivated
- Mention any strategies for managing fatigue or monotony
- Explain how you ensure quality standards are met despite the repetitive nature of the job
- Share any personal routines or practices that help you stay engaged
- Highlight the importance of teamwork in maintaining a productive atmosphere
What not to say
- Expressing boredom or dissatisfaction with repetitive work without solutions
- Indicating a lack of strategies to stay focused or engaged
- Avoiding any mention of quality control measures
- Neglecting to recognize the role of teamwork in maintaining focus
Example answer
“In my role at PepsiCo, I found ways to keep my focus during repetitive tasks by setting small goals for myself, like aiming to complete a certain number of units per hour. I also engaged in friendly conversations with my colleagues to break the monotony. To ensure quality, I performed regular checks on my work and encouraged my team to do the same, which fostered a collaborative and attentive environment.”
Skills tested
Question type
3. Senior Line Operator Interview Questions and Answers
3.1. Can you describe a time when you identified a safety hazard in your work environment and how you addressed it?
Introduction
This question is crucial for assessing your commitment to safety protocols and your proactive approach in maintaining a safe work environment, which is vital for a Senior Line Operator.
How to answer
- Use the STAR method (Situation, Task, Action, Result) to structure your response.
- Clearly describe the safety hazard you identified and its potential risks.
- Explain the steps you took to assess and address the hazard.
- Discuss how you communicated the issue to your team or supervisors.
- Highlight the outcome and any changes that were implemented as a result.
What not to say
- Failing to provide a specific example, which could indicate a lack of awareness.
- Downplaying the importance of safety or suggesting that it is not a priority.
- Not mentioning collaboration with others or seeking guidance from supervisors.
- Avoiding discussion on the results or improvements made post-incident.
Example answer
“While working at Nestlé, I noticed that a section of the production line had poor visibility due to clutter. I reported this to my supervisor and proposed a reorganization of the workspace. After clearing the area, we reduced the risk of accidents significantly, and I led a safety training session to reinforce the importance of maintaining clear pathways, which resulted in a 20% decrease in near-miss incidents.”
Skills tested
Question type
3.2. How do you ensure that quality standards are met consistently during production runs?
Introduction
This question assesses your attention to detail and quality control processes, which are critical responsibilities of a Senior Line Operator.
How to answer
- Describe your approach to monitoring quality throughout production.
- Explain the specific quality control measures you implement.
- Detail how you train and guide your team to maintain quality standards.
- Discuss how you handle deviations from quality standards.
- Mention any tools or technologies you use to support quality assurance.
What not to say
- Suggesting that quality checks are someone else's responsibility.
- Focusing solely on the end product without mentioning the process.
- Not providing specific examples of how you ensure quality.
- Ignoring the importance of team involvement in maintaining quality.
Example answer
“In my role at Coca-Cola, I implement a multi-check system where every line operator conducts quality inspections at designated points. I train my team on the standards required and we hold daily briefings to discuss targets. When we faced a consistency issue, I analyzed the production data and modified our processes, resulting in a 15% improvement in product quality metrics over three months.”
Skills tested
Question type
4. Lead Line Operator Interview Questions and Answers
4.1. Can you describe a time when you had to troubleshoot a significant issue during a production run?
Introduction
This question is vital for evaluating your problem-solving skills and ability to maintain production efficiency under pressure, which are critical for a Lead Line Operator.
How to answer
- Use the STAR method (Situation, Task, Action, Result) to structure your response.
- Clearly describe the production issue, including its potential impact on output.
- Explain the steps you took to diagnose and resolve the issue, highlighting teamwork and communication.
- Share the outcome and any improvements made to prevent future occurrences.
- Discuss what you learned from the experience and how it has influenced your approach to operations.
What not to say
- Blaming others without taking responsibility for your role in the situation.
- Providing vague descriptions that lack specific details about the challenge.
- Failing to mention collaboration with team members or other departments.
- Neglecting to discuss the results or improvements stemming from the resolution.
Example answer
“During a production run at Coca-Cola, we experienced a significant malfunction in one of our bottling machines. I quickly gathered my team, assessed the issue, and realized we needed to recalibrate the sensors. By coordinating with maintenance and communicating effectively, we resolved the issue within 30 minutes, minimizing downtime. This taught me the importance of clear communication and proactive maintenance checks, which we implemented afterward, reducing similar incidents by 20%.”
Skills tested
Question type
4.2. How do you ensure that safety standards are met on the production line?
Introduction
This question is crucial for assessing your commitment to safety regulations and your ability to instill a safety culture among your team, which is paramount in manufacturing environments.
How to answer
- Discuss specific safety protocols and regulations relevant to your industry.
- Explain how you communicate and enforce these protocols with your team.
- Share examples of safety training or initiatives you have implemented.
- Describe how you handle safety violations or concerns raised by team members.
- Highlight the importance of reporting and continuous improvement in safety practices.
What not to say
- Implying that safety is not a priority in your operations.
- Providing generic answers without specific examples of safety measures.
- Neglecting to mention team involvement in safety practices.
- Failing to recognize the importance of compliance and regulations.
Example answer
“At PepsiCo, I implemented a weekly safety briefing where we reviewed safety protocols and discussed any near misses. I also initiated an incentive program that rewarded teams for maintaining a clean and safe workspace. As a result, our incident rate decreased by 30% over the year. I believe that safety is everyone's responsibility, and fostering open communication about potential hazards is key to a safe production environment.”
Skills tested
Question type
5. Production Supervisor Interview Questions and Answers
5.1. Can you describe a time when you improved a production process or efficiency in your previous role?
Introduction
This question assesses your ability to identify inefficiencies and implement effective solutions, which is critical for a Production Supervisor.
How to answer
- Use the STAR method to structure your response: Situation, Task, Action, Result.
- Clearly outline the production process that needed improvement.
- Discuss the data or observations that led you to identify the inefficiency.
- Detail the specific actions you took to address the issue.
- Quantify the results to showcase the impact of your improvements.
What not to say
- Not providing a concrete example or being vague about the situation.
- Focusing solely on the problem without detailing your solution.
- Neglecting to mention teamwork or collaboration with other departments.
- Overstating results without providing supporting data.
Example answer
“In my role at Toyota, I noticed that the assembly line was experiencing frequent delays due to equipment downtimes. I conducted a root cause analysis and implemented a proactive maintenance schedule, reducing downtime by 30%. This change improved overall production efficiency by 15% and enhanced team morale, as we could consistently meet our targets.”
Skills tested
Question type
5.2. How do you ensure safety and compliance on the production floor?
Introduction
This question evaluates your understanding of safety regulations and your ability to enforce compliance, which is essential for a Production Supervisor.
How to answer
- Describe your knowledge of relevant safety regulations in Japan.
- Explain how you communicate safety protocols to your team.
- Detail any training or drills you implement to ensure compliance.
- Discuss how you monitor adherence to safety standards and address violations.
- Share an example of a situation where your actions enhanced workplace safety.
What not to say
- Implying that safety compliance is not a priority.
- Failing to mention specific safety regulations or standards.
- Not providing examples of proactive safety measures.
- Overlooking the importance of team involvement in safety culture.
Example answer
“At Panasonic, I took safety compliance very seriously. I developed a quarterly safety training program that included hands-on drills for my team. We also held regular meetings to reinforce the importance of safety protocols. As a result, we reduced safety incidents by 40% over the year, fostering a culture of safety awareness in the production environment.”
Skills tested
Question type
Similar Interview Questions and Sample Answers
Simple pricing, powerful features
Upgrade to Himalayas Plus and turbocharge your job search.
Himalayas
Himalayas Plus
Himalayas Max
Find your dream job
Sign up now and join over 100,000 remote workers who receive personalized job alerts, curated job matches, and more for free!
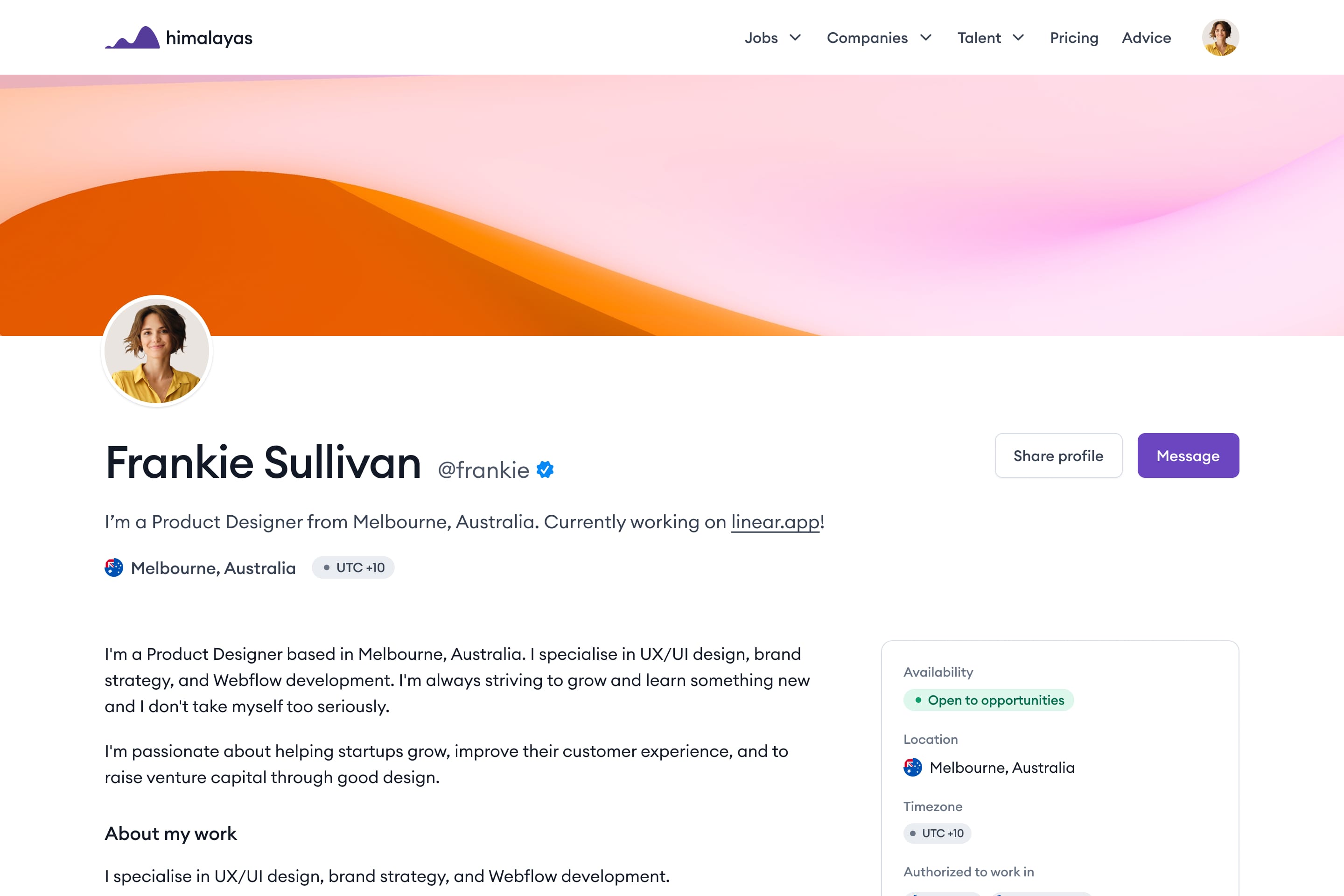