5 Packing Line Operator Interview Questions and Answers
Packing Line Operators are responsible for ensuring products are packaged efficiently and meet quality standards. They operate and monitor machinery, perform quality checks, and maintain a clean and safe work environment. Junior operators focus on learning the equipment and processes, while senior operators may oversee operations, troubleshoot issues, and train new staff. Supervisors and managers take on leadership roles, managing teams and optimizing production workflows. Need to practice for an interview? Try our AI interview practice for free then unlock unlimited access for just $9/month.
Unlimited interview practice for $9 / month
Improve your confidence with an AI mock interviewer.
No credit card required
1. Junior Packing Line Operator Interview Questions and Answers
1.1. Can you describe a time when you had to work under pressure on the packing line? How did you handle it?
Introduction
This question evaluates your ability to perform under pressure, which is crucial in a fast-paced packing environment where efficiency and accuracy are key.
How to answer
- Use the STAR method to structure your response: Situation, Task, Action, Result.
- Describe the specific situation and the pressure you faced, such as tight deadlines or high production demands.
- Explain the actions you took to manage the pressure, including any techniques or strategies you used.
- Share the positive outcome of your actions, highlighting any metrics if possible, such as reduced error rates or meeting deadlines.
- Conclude with what you learned from the experience and how it prepared you for future challenges.
What not to say
- Dismissing the importance of managing pressure in the role.
- Focusing solely on the stress without discussing how you coped.
- Providing vague responses without specific examples or outcomes.
- Blaming external factors for the pressure rather than taking responsibility.
Example answer
“During a peak season at my previous job, we faced a sudden surge in orders that required us to double our output. I took a deep breath, prioritized my tasks, and communicated with my team to streamline our workflow. By maintaining focus and encouraging teamwork, we not only met our deadline but also reduced our error rate by 15%. This experience taught me the importance of clear communication and teamwork during high-pressure situations.”
Skills tested
Question type
1.2. What safety protocols do you think are essential while operating machinery on the packing line?
Introduction
This question assesses your understanding of safety practices, which are vital for maintaining a safe working environment in the packing industry.
How to answer
- List key safety protocols such as wearing appropriate PPE, keeping work areas clean, and following machinery operating procedures.
- Explain the importance of each protocol in preventing accidents and ensuring safety.
- Discuss any training or certifications you have related to safety in the workplace.
- Share examples of how you have followed or enforced safety protocols in past experiences.
- Emphasize your commitment to safety and how you would contribute to a culture of safety in the workplace.
What not to say
- Underestimating the importance of safety protocols.
- Failing to mention specific safety measures.
- Saying that safety protocols can be overlooked if under pressure.
- Not demonstrating knowledge of your responsibilities regarding safety.
Example answer
“I believe essential safety protocols include wearing appropriate personal protective equipment, conducting regular safety checks on machinery, and keeping the work area organized. In my previous role, I was responsible for ensuring our team adhered to these protocols, which helped us maintain a safe work environment. I once identified a potential hazard with a packing machine, reported it immediately, and we resolved the issue before it caused any accidents. Safety is paramount, and I am committed to upholding these standards.”
Skills tested
Question type
2. Packing Line Operator Interview Questions and Answers
2.1. Can you describe a time when you identified a safety hazard on the packing line and how you addressed it?
Introduction
This question is crucial for a Packing Line Operator as safety is a top priority in manufacturing environments. It assesses your awareness of safety protocols and your proactive approach to maintaining a safe work environment.
How to answer
- Use the STAR method to structure your response: Situation, Task, Action, Result.
- Clearly describe the hazard you identified and its potential risks.
- Explain the steps you took to address the hazard and communicate it to your team.
- Highlight any improvements in safety or efficiency resulting from your actions.
- Discuss any follow-up measures to ensure the hazard was permanently resolved.
What not to say
- Ignoring the importance of safety and focusing only on productivity.
- Failing to describe the steps taken to address the hazard.
- Not mentioning team communication or engagement in safety improvements.
- Providing a vague example without specific details or outcomes.
Example answer
“In my previous role at Unilever, I noticed that a box-flattening machine was not properly secured, posing a risk of injury. I immediately reported it to my supervisor and placed warning signs around the area. We halted operations until the issue was resolved and conducted a team meeting to reinforce safety protocols. This action led to a 20% reduction in reported near-miss incidents over the following month.”
Skills tested
Question type
2.2. How do you handle repetitive tasks on the packing line to maintain efficiency and quality?
Introduction
This question assesses your ability to stay focused and motivated while performing repetitive tasks, which is essential for a Packing Line Operator to ensure consistent quality and productivity.
How to answer
- Discuss techniques you use to maintain focus, such as setting personal goals or taking scheduled breaks.
- Explain how you monitor the quality of your work and what checks you perform.
- Share any methods you have implemented to improve efficiency without compromising quality.
- Mention how you stay engaged with your team to foster a positive work environment.
- Highlight any specific metrics or outcomes that demonstrate your effectiveness.
What not to say
- Implying that you find repetitive work boring or unimportant.
- Failing to provide specific strategies for maintaining focus and quality.
- Neglecting to mention teamwork or communication with colleagues.
- Claiming that you never encounter issues with repetitive tasks.
Example answer
“To stay efficient on the packing line, I set small goals for myself, such as completing a certain number of packages within a time frame. I also perform regular quality checks and communicate with my colleagues to share tips on improving our processes. For instance, at Ferrero, I noticed that adjusting the packing speed slightly enhanced our output without increasing errors, leading to a 15% improvement in our daily targets.”
Skills tested
Question type
3. Senior Packing Line Operator Interview Questions and Answers
3.1. Can you describe a time when you identified a problem in the packing process and how you resolved it?
Introduction
This question is crucial for assessing your problem-solving abilities and attention to detail, which are essential for maintaining efficiency and quality in packing operations.
How to answer
- Use the STAR method to structure your response: Situation, Task, Action, Result.
- Clearly describe the specific problem you encountered in the packing line.
- Explain your thought process in identifying the root cause of the issue.
- Detail the actions you took to resolve the problem, including any collaboration with team members.
- Quantify the results of your actions, such as improvements in efficiency or reductions in errors.
What not to say
- Vaguely describing a problem without specific details.
- Taking sole credit without acknowledging teamwork.
- Focusing on problems without discussing solutions.
- Neglecting to mention any metrics or outcomes.
Example answer
“At my previous job with Nestlé, I noticed a recurring issue with packaging misalignment that was causing delays. I conducted a thorough assessment and discovered that the sensors on the packing line were miscalibrated. I worked with the maintenance team to recalibrate the sensors, which reduced misalignment errors by 30% and improved our overall packing speed by 15%. This experience taught me the importance of proactive problem-solving in maintaining productivity.”
Skills tested
Question type
3.2. How do you ensure compliance with safety regulations while operating packing machinery?
Introduction
Safety is paramount in packing operations, making it essential to evaluate your knowledge of safety protocols and your commitment to maintaining a safe working environment.
How to answer
- Discuss specific safety regulations relevant to the packing line.
- Explain your personal practices for ensuring compliance with these regulations.
- Share examples of safety training you've received and how you apply it.
- Describe how you communicate safety protocols to new team members.
- Highlight any initiatives you’ve taken to improve safety in your department.
What not to say
- Suggesting safety regulations are not important.
- Failing to mention specific safety practices.
- Ignoring the importance of team communication regarding safety.
- Neglecting to describe personal accountability in maintaining safety.
Example answer
“In my role at Coca-Cola, I strictly adhered to all safety regulations, including the use of personal protective equipment (PPE) and regular machine maintenance checks. I participated in quarterly safety training and made it a point to share best practices with new operators. When I noticed some new team members were unsure about machine operation, I initiated a buddy system to provide on-the-job training, which significantly improved our safety compliance rates.”
Skills tested
Question type
4. Packing Line Supervisor Interview Questions and Answers
4.1. Describe a situation where you had to manage a conflict between team members on the packing line.
Introduction
This question assesses your conflict resolution skills and ability to maintain a productive work environment, which is crucial for a supervisor.
How to answer
- Use the STAR method to structure your response
- Clearly explain the context of the conflict and the parties involved
- Describe the steps you took to address the conflict
- Highlight the outcomes and any improvements in team dynamics
- Discuss any techniques you used to prevent future conflicts
What not to say
- Avoid blaming team members or making it seem like it was solely their fault
- Don't focus only on the negative aspects of the conflict without showing resolution
- Refrain from saying you don't like dealing with conflicts
- Neglecting to mention the importance of teamwork and communication
Example answer
“In my previous role at a packaging company, two team members had a disagreement over the correct packing procedure, which caused delays. I facilitated a meeting where each could express their viewpoint. We reviewed the standard procedures together and agreed on a solution that combined both ideas. This not only resolved the conflict but also improved our packing efficiency by 15% as everyone was on the same page going forward.”
Skills tested
Question type
4.2. How do you ensure quality control on the packing line?
Introduction
This question helps gauge your attention to detail and understanding of quality assurance processes, which are vital for maintaining product standards.
How to answer
- Outline your quality control processes and protocols
- Discuss any specific metrics or standards you track
- Explain how you train your team to uphold quality standards
- Share examples of how you've improved quality control in the past
- Mention any tools or technologies you use for monitoring quality
What not to say
- Saying that quality control is solely the responsibility of the quality assurance team
- Ignoring the importance of training and team involvement
- Failing to mention any specific metrics or results
- Suggesting you only check quality at the end of the line
Example answer
“At my last job with a food packaging company, I implemented a checklist system for quality checks at each stage of the packing process. I trained my team on the importance of these checks and held weekly reviews to discuss any issues. This proactive approach led to a 30% reduction in packaging errors over six months, ensuring we consistently met our quality standards.”
Skills tested
Question type
5. Packing Line Manager Interview Questions and Answers
5.1. Can you describe a time when you improved the efficiency of a packing line?
Introduction
This question is crucial for understanding your ability to analyze processes and implement improvements, which is essential for a Packing Line Manager.
How to answer
- Start with a specific inefficiency you identified in the packing line
- Explain the steps you took to analyze the problem
- Describe the solutions you implemented and how you engaged your team
- Quantify the improvement in efficiency or productivity as a result
- Discuss any challenges faced during the implementation and how you overcame them
What not to say
- Giving vague answers without specific metrics or outcomes
- Focusing solely on technical aspects without mentioning team involvement
- Not addressing the initial problem clearly
- Failing to mention any follow-up to sustain improvements
Example answer
“At a beverage company, I noticed our packing line was operating at only 70% efficiency. I conducted a time-motion study and identified bottlenecks caused by manual labeling. I implemented an automated labeling system and trained the team on its use. This change increased our efficiency to 90% within three months, leading to a significant reduction in overtime costs.”
Skills tested
Question type
5.2. How do you ensure compliance with safety and quality standards on the packing line?
Introduction
Compliance with safety and quality standards is critical in a packing line environment. This question assesses your understanding and implementation of these standards.
How to answer
- Discuss your knowledge of relevant safety and quality regulations
- Explain how you train and communicate these standards to your team
- Detail the systems you have in place for monitoring compliance
- Provide examples of how you've handled compliance issues in the past
- Mention any certifications or training you have received related to safety and quality
What not to say
- Claiming that compliance is solely the responsibility of another team
- Not providing specific examples of compliance measures taken
- Neglecting to mention ongoing training and updates for staff
- Underestimating the importance of a safety culture
Example answer
“In my previous role at a food packaging plant, I ensured compliance by implementing regular training sessions on safety protocols and quality standards. I established a checklist for daily operations that included safety inspections and quality control measures. When we faced a minor quality issue, I immediately organized a team meeting to address it, leading to improved procedures and zero incidents thereafter.”
Skills tested
Question type
Similar Interview Questions and Sample Answers
Simple pricing, powerful features
Upgrade to Himalayas Plus and turbocharge your job search.
Himalayas
Himalayas Plus
Himalayas Max
Find your dream job
Sign up now and join over 100,000 remote workers who receive personalized job alerts, curated job matches, and more for free!
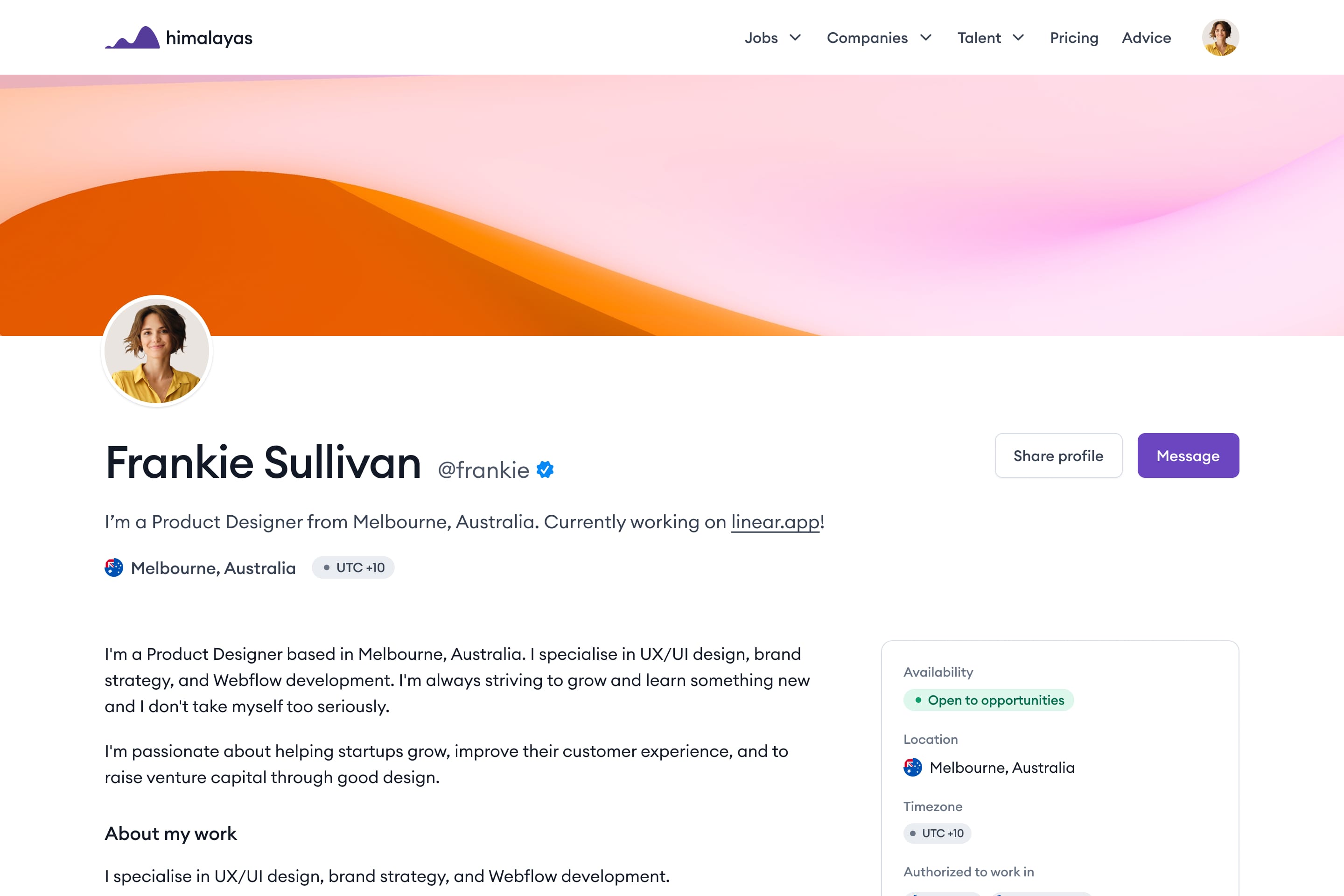