5 Packaging Machine Operator Interview Questions and Answers
Packaging Machine Operators are responsible for operating and maintaining machinery used in the packaging process. They ensure products are packaged efficiently, safely, and according to quality standards. Junior operators focus on basic machine operation and learning processes, while senior operators handle complex tasks, troubleshoot issues, and may oversee other operators. Supervisory roles involve managing teams and optimizing packaging workflows. Need to practice for an interview? Try our AI interview practice for free then unlock unlimited access for just $9/month.
Unlimited interview practice for $9 / month
Improve your confidence with an AI mock interviewer.
No credit card required
1. Junior Packaging Machine Operator Interview Questions and Answers
1.1. Can you describe a time when you identified a problem with a packaging machine and how you resolved it?
Introduction
This question assesses your problem-solving skills and technical understanding of packaging machinery, which are crucial for a Junior Packaging Machine Operator.
How to answer
- Use the STAR method to structure your response: Situation, Task, Action, Result.
- Clearly describe the specific issue you encountered with the machine.
- Explain the steps you took to diagnose and resolve the problem.
- Mention any tools or techniques you used during the troubleshooting process.
- Highlight the outcome and any improvements made as a result of your actions.
What not to say
- Avoid vague descriptions of problems without a clear resolution.
- Don't take credit for team efforts; focus on your contributions.
- Steering away from technical jargon that may confuse the interviewer.
- Neglecting to mention safety protocols during the troubleshooting process.
Example answer
“At my previous position at Müller, I noticed the packaging machine was frequently jamming during the sealing process. I investigated and discovered that a worn-out blade was causing the issue. I reported it to my supervisor, replaced the blade, and adjusted the machine settings. This reduced downtime by 30% and improved our packaging efficiency significantly, ensuring we met our production targets.”
Skills tested
Question type
1.2. What safety protocols do you follow when operating packaging machines?
Introduction
This question is vital as it assesses your understanding of safety regulations and procedures, which are critical in the packaging industry to prevent accidents.
How to answer
- Outline specific safety protocols you follow, such as wearing personal protective equipment (PPE).
- Discuss the importance of regular machine maintenance and safety checks.
- Explain how you ensure your workspace is clear and organized to prevent accidents.
- Mention your understanding of emergency procedures and how you would react in case of an emergency.
- Show your commitment to safety by discussing any relevant training you've received.
What not to say
- Suggesting that safety protocols are optional or can be ignored.
- Focusing solely on operational efficiency without mentioning safety.
- Failing to acknowledge the importance of teamwork in maintaining a safe environment.
- Not providing concrete examples of safety practices.
Example answer
“I always wear the necessary PPE, including gloves and goggles, while operating machinery. I conduct daily safety checks to ensure that all emergency stops are functional and that there are no obstructions around the machine. I also follow the lockout/tagout procedures to ensure machines are properly shut down during maintenance. Safety is a top priority, and I believe that maintaining a safe workplace is crucial for everyone’s well-being.”
Skills tested
Question type
2. Packaging Machine Operator Interview Questions and Answers
2.1. Can you describe a time when you identified a malfunction in a packaging machine and how you resolved it?
Introduction
This question assesses your technical skills and problem-solving abilities, which are crucial for a Packaging Machine Operator in ensuring production efficiency and minimizing downtime.
How to answer
- Start with a clear description of the malfunction you encountered.
- Explain the steps you took to diagnose the issue.
- Discuss how you resolved the malfunction, including any tools or techniques you used.
- Quantify the impact of your solution on production efficiency or downtime.
- Conclude with what you learned from the experience to prevent future issues.
What not to say
- Avoid vague descriptions that lack specific details.
- Don't blame others for the malfunction without acknowledging your role in the solution.
- Refrain from discussing unrelated technical issues.
- Do not neglect to mention the importance of safety protocols during the resolution.
Example answer
“At Nestlé, I noticed that our flow wrapping machine was producing packages with inconsistent seals. I immediately shut down the line and inspected the machine, discovering a misalignment in the sealing jaws. After recalibrating the machine, I ran a series of tests to ensure proper sealing. This proactive approach reduced our defect rate by 20%, and I shared the calibration process with the team, which helped us avoid future misalignments.”
Skills tested
Question type
2.2. How do you ensure quality control during the packaging process?
Introduction
This question evaluates your understanding of quality control measures and your commitment to maintaining high standards in packaging operations.
How to answer
- Discuss your familiarity with quality control standards in packaging.
- Describe specific methods you use to monitor quality during production.
- Explain how you document quality checks and report discrepancies.
- Share an example of how you contributed to improving quality in a previous role.
- Mention how you collaborate with other departments to ensure quality.
What not to say
- Avoid stating that quality control is solely the responsibility of supervisors.
- Do not mention a lack of experience with quality control processes.
- Refrain from discussing quality checks that are too vague or generic.
- Do not neglect to mention the importance of compliance with safety and regulatory standards.
Example answer
“In my role at Coca-Cola, I implemented a checklist for quality control that included checks for seal integrity, package weight, and visual defects. I conducted hourly inspections and documented the findings in our quality management system. When I noticed an increase in weight discrepancies, I collaborated with the production team to identify the cause and adjusted the filling process. This led to a 15% reduction in weight-related complaints from our clients.”
Skills tested
Question type
3. Senior Packaging Machine Operator Interview Questions and Answers
3.1. Can you describe a time when you identified a malfunction in a packaging machine, and how you handled it?
Introduction
This question evaluates your technical troubleshooting skills and ability to maintain operational efficiency, which are crucial for a Senior Packaging Machine Operator.
How to answer
- Use the STAR method to structure your response: Situation, Task, Action, Result.
- Clearly describe the malfunction and its impact on production.
- Detail the steps you took to diagnose the issue, including any tools or methods used.
- Explain how you communicated with your team and management during the process.
- Share the outcome and any preventive measures you implemented to avoid future issues.
What not to say
- Failing to take responsibility for the situation.
- Not detailing the specific actions you took.
- Overlooking the importance of teamwork and communication.
- Describing a situation without a clear resolution or learning outcome.
Example answer
“At a Coca-Cola bottling plant, I noticed our packaging machine was producing misaligned labels, which could lead to wastage. I immediately halted production and used diagnostic tools to identify that a sensor had malfunctioned. I communicated with my supervisor and together we replaced the faulty part. After resolving the issue, I trained the team on regular maintenance checks to prevent recurrence, which improved our output quality by 15%.”
Skills tested
Question type
3.2. How do you ensure adherence to safety protocols while operating packaging machinery?
Introduction
This question assesses your knowledge of safety standards and your commitment to maintaining a safe working environment, which is essential in manufacturing roles.
How to answer
- Explain the safety protocols specific to packaging machinery.
- Discuss how you keep yourself and your team accountable to these protocols.
- Share examples of safety training or initiatives you have been involved in.
- Describe how you handle safety violations or near-misses in the workplace.
- Highlight the importance of continuous safety improvement and training.
What not to say
- Suggesting safety protocols are optional or unimportant.
- Failing to provide specific examples of how you prioritize safety.
- Ignoring the role of teamwork in maintaining safety standards.
- Downplaying the consequences of safety violations.
Example answer
“I prioritize safety by strictly adhering to our company's safety protocols, such as wearing personal protective equipment and conducting regular safety audits on our machines. I also lead monthly safety training sessions for my team, emphasizing the importance of reporting any safety concerns immediately. Last year, I identified a potential hazard related to machine maintenance and suggested a new lockout/tagout procedure that has since reduced our near-miss incidents by 30%.”
Skills tested
Question type
4. Lead Packaging Machine Operator Interview Questions and Answers
4.1. Can you describe a time when you identified a recurring issue with a packaging machine and how you resolved it?
Introduction
This question assesses your problem-solving abilities and technical expertise in operating and maintaining packaging machinery, which is critical for ensuring production efficiency.
How to answer
- Use the STAR method to structure your response (Situation, Task, Action, Result)
- Clearly state the issue you encountered and its impact on production
- Explain the steps you took to diagnose and resolve the issue
- Highlight any tools or techniques you used to fix the problem
- Mention the positive outcomes resulting from your actions, such as reduced downtime or improved efficiency
What not to say
- Describing a situation where you didn't take any action to resolve the issue
- Focusing solely on technical details without mentioning the team or communication aspects
- Failing to provide measurable results or outcomes
- Blaming others for the issue without demonstrating personal accountability
Example answer
“At a beverage manufacturing plant, I noticed that our bottling line frequently jammed, causing significant downtime. I took the initiative to analyze the conveyor system and found that a misaligned sensor was the culprit. I recalibrated the sensor and implemented a weekly maintenance schedule, which reduced machine jams by 60% and improved overall production efficiency by 15%.”
Skills tested
Question type
4.2. How do you ensure quality control during the packaging process?
Introduction
This question evaluates your understanding of quality assurance practices and your role in maintaining product standards, which are vital for customer satisfaction and compliance.
How to answer
- Discuss the specific quality control measures you implement during packaging
- Explain how you train and communicate these measures to your team
- Describe any tools or technologies you use for monitoring quality
- Provide examples of how you address quality issues and ensure compliance with safety regulations
- Mention the importance of documentation for quality control in packaging
What not to say
- Claiming quality control isn't part of your responsibility
- Giving vague answers without specific examples or methods
- Neglecting to discuss teamwork or collaboration in maintaining quality
- Failing to mention industry standards or regulations
Example answer
“In my role at a food packaging facility, I established a quality control checklist that included visual inspections and weight measurements for every batch. I trained my team on these protocols, ensuring everyone understood the importance of compliance. I also implemented a digital tracking system to document any deviations, which led to a 25% reduction in packaging errors over six months.”
Skills tested
Question type
5. Packaging Supervisor Interview Questions and Answers
5.1. Can you describe a time when you improved the efficiency of a packaging process?
Introduction
This question evaluates your ability to analyze and enhance operational processes, a critical skill for a Packaging Supervisor responsible for maximizing productivity and minimizing waste.
How to answer
- Use the STAR method (Situation, Task, Action, Result) to structure your answer
- Clearly outline the initial inefficiencies you identified
- Discuss the specific measures you implemented to improve the process
- Quantify the results, such as increased output or reduced costs
- Reflect on any challenges faced during the implementation and how you overcame them
What not to say
- Focusing on solutions that didn't yield measurable results
- Neglecting to mention teamwork or collaboration with other departments
- Overlooking safety or quality considerations in the process
- Failing to describe the specific actions taken
Example answer
“At my previous job at a food packaging plant, I noticed that our packing line had frequent slowdowns due to manual handling. I initiated a project to automate part of the process by introducing semi-automated packing machines. This change increased our packing speed by 30% and reduced labor costs by 20%. It was a significant improvement, and we also maintained safety and quality throughout the transition.”
Skills tested
Question type
5.2. How do you ensure compliance with safety and quality standards in packaging operations?
Introduction
This question is crucial for understanding your commitment to maintaining industry standards, which is vital in the packaging sector to ensure product integrity and safety.
How to answer
- Outline your knowledge of relevant safety and quality regulations
- Describe your approach to training and informing team members about compliance
- Discuss regular audits or quality checks you implement
- Explain how you handle non-compliance issues when they arise
- Share examples of how you have previously improved compliance measures
What not to say
- Implying that compliance is not a priority
- Failing to provide specific examples of compliance measures
- Overlooking the importance of ongoing training and awareness
- Neglecting to mention how you monitor compliance
Example answer
“In my role at a beverage packaging company, I prioritized compliance by conducting regular training sessions on safety standards and quality protocols. I implemented a checklist system for daily operations that helped our team adhere to regulations. Additionally, I conducted surprise audits and addressed any issues immediately. As a result, we achieved a 95% compliance rate during our last external audit.”
Skills tested
Question type
Similar Interview Questions and Sample Answers
Simple pricing, powerful features
Upgrade to Himalayas Plus and turbocharge your job search.
Himalayas
Himalayas Plus
Himalayas Max
Find your dream job
Sign up now and join over 100,000 remote workers who receive personalized job alerts, curated job matches, and more for free!
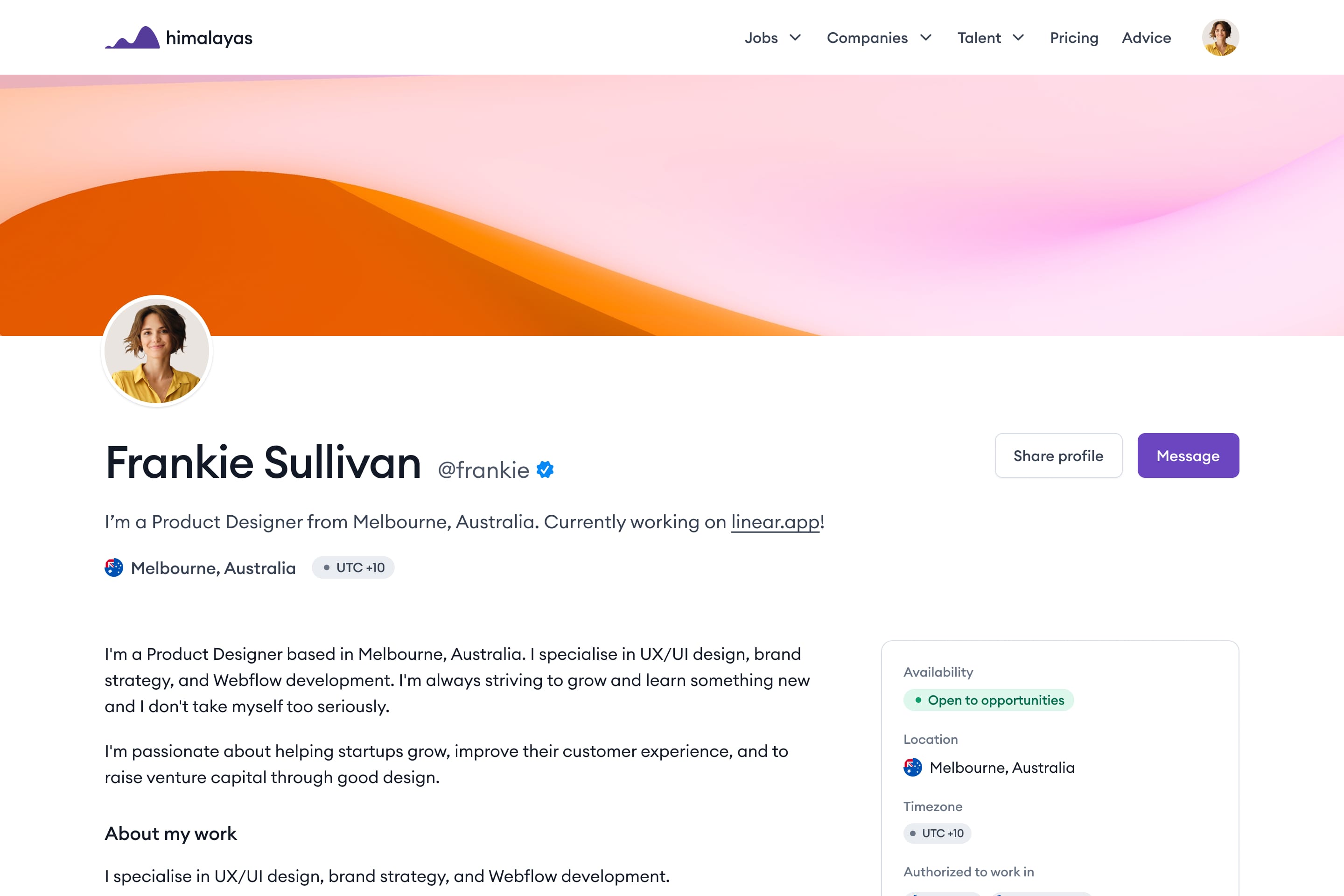