5 Packaging Technician Interview Questions and Answers
Packaging Technicians are responsible for operating and maintaining machinery used in the packaging process, ensuring products are packaged efficiently and meet quality standards. They monitor equipment, troubleshoot issues, and adhere to safety and regulatory guidelines. Junior technicians focus on basic tasks and learning the equipment, while senior technicians and leads take on more complex troubleshooting, process optimization, and team supervision. Need to practice for an interview? Try our AI interview practice for free then unlock unlimited access for just $9/month.
Unlimited interview practice for $9 / month
Improve your confidence with an AI mock interviewer.
No credit card required
1. Junior Packaging Technician Interview Questions and Answers
1.1. Can you describe a time when you identified a packaging issue and how you resolved it?
Introduction
This question assesses your problem-solving skills and attention to detail, which are crucial for a Junior Packaging Technician responsible for ensuring product integrity.
How to answer
- Use the STAR method to structure your response: Situation, Task, Action, Result.
- Clearly define the packaging issue you encountered.
- Explain your thought process in identifying the root cause of the problem.
- Describe the actions you took to resolve the issue, including any collaboration with team members.
- Quantify the results of your actions, such as reduced waste or improved product quality.
What not to say
- Failing to provide a specific example and giving vague responses.
- Blaming others for the issue without taking responsibility.
- Not mentioning the outcome or results of your actions.
- Overlooking the importance of teamwork in your resolution.
Example answer
“At my previous internship with a local food manufacturer, I noticed that some packaging was not sealing properly, risking contamination. I investigated and found that the sealing machine was not calibrated correctly. I collaborated with the maintenance team to recalibrate the machine, resulting in a 20% reduction in defective packages and ensuring food safety standards were met.”
Skills tested
Question type
1.2. How do you ensure compliance with packaging regulations and standards?
Introduction
This question evaluates your understanding of industry regulations and your ability to maintain compliance, which is vital in packaging roles.
How to answer
- Discuss your knowledge of relevant packaging regulations (e.g., food safety, labeling requirements).
- Explain how you stay updated on any changes in regulations.
- Describe processes or tools you use to ensure compliance in your work.
- Share an example of how you applied regulations in a past role or project.
- Highlight your attention to detail in documenting compliance.
What not to say
- Claiming that you are not familiar with packaging regulations.
- Ignoring the importance of staying updated on industry standards.
- Providing a response that lacks specific examples or processes.
- Failing to acknowledge the consequences of non-compliance.
Example answer
“I am familiar with the South African food packaging regulations, including the requirements for labeling and material safety. I regularly review updates from the Department of Health and utilize checklists to ensure all packaging complies before production. During my internship at a dairy company, I ensured that all products were labeled accurately, which helped us avoid a potential recall due to incorrect information.”
Skills tested
Question type
2. Packaging Technician Interview Questions and Answers
2.1. Can you describe a time when you identified a quality issue in the packaging process and how you addressed it?
Introduction
This question is crucial for assessing your attention to detail and problem-solving skills, which are vital in ensuring product integrity and compliance in packaging.
How to answer
- Use the STAR method to structure your response: Situation, Task, Action, Result.
- Clearly explain the quality issue you encountered and its potential impact on the product.
- Detail the steps you took to investigate the issue, including any tools or methods used.
- Describe how you communicated the issue to your team and any actions taken to rectify it.
- Share the outcome, including any improvements made to the process as a result.
What not to say
- Ignoring the importance of quality control in packaging.
- Giving vague examples without specific details or metrics.
- Failing to mention teamwork or collaboration in resolving the issue.
- Not discussing what you learned from the experience.
Example answer
“At Nestlé, I noticed discrepancies in the sealing of our snack packaging, which could lead to spoilage. I conducted a thorough analysis and discovered that the sealing machine was miscalibrated. I reported this to my supervisor and collaborated with the maintenance team to recalibrate the machine. As a result, we improved our sealing accuracy by 20%, ensuring product quality and reducing waste.”
Skills tested
Question type
2.2. What steps do you take to ensure compliance with packaging regulations and standards?
Introduction
This question evaluates your knowledge of industry regulations and your ability to implement compliance measures, which are essential for a packaging technician.
How to answer
- Discuss your understanding of relevant regulations (e.g., EU packaging regulations).
- Explain how you stay updated on changes in regulations.
- Detail your process for checking compliance during the packaging process.
- Share an example of how you handled a compliance issue in the past.
- Highlight your collaboration with quality assurance and regulatory teams.
What not to say
- Implying that compliance is not your responsibility.
- Providing outdated or incorrect information about regulations.
- Neglecting to mention proactive measures you take.
- Focusing solely on compliance without discussing quality.
Example answer
“I regularly review the latest EU packaging regulations and participate in training sessions. During my time at Unilever, I implemented a compliance checklist for each packaging line, ensuring that all materials and labels met the necessary standards. This proactive approach helped us avoid compliance issues during audits and increased our overall efficiency.”
Skills tested
Question type
3. Senior Packaging Technician Interview Questions and Answers
3.1. Can you describe a time when you identified a flaw in a packaging process and how you resolved it?
Introduction
This question assesses your attention to detail and problem-solving skills, which are critical for ensuring packaging quality and compliance in manufacturing.
How to answer
- Use the STAR method (Situation, Task, Action, Result) to structure your response.
- Clearly describe the packaging process and the specific flaw you identified.
- Explain the steps you took to investigate and analyze the issue.
- Detail the solution you implemented and its impact on the packaging quality.
- Mention any follow-up actions to prevent similar issues in the future.
What not to say
- Vague descriptions without specific details about the flaw.
- Focusing solely on the problem without discussing the resolution.
- Neglecting to mention collaboration with team members or other departments.
- Omitting the impact of your actions on the overall process.
Example answer
“While working at Grupo Bimbo, I noticed that certain packages were not sealing properly during the production run, leading to potential product spoilage. I conducted a thorough analysis and discovered that the temperature settings on the sealing machine were incorrect. I recalibrated the machine and retrained the team on proper sealing techniques. As a result, we reduced the defect rate by 30% and improved overall product quality, ensuring customer satisfaction.”
Skills tested
Question type
3.2. How do you ensure that your packaging meets industry standards and regulations?
Introduction
This question evaluates your knowledge of industry standards and your commitment to compliance, which are essential in the packaging sector.
How to answer
- Discuss your familiarity with relevant packaging regulations and standards, such as ISO or local requirements.
- Explain your process for staying updated on changes in regulations.
- Describe how you conduct quality checks to ensure compliance.
- Mention any training or certifications you have regarding packaging standards.
- Provide examples of how you have implemented compliance measures in your previous roles.
What not to say
- Claiming to know all standards without acknowledging the need for continuous learning.
- Providing generic answers without specific examples of compliance measures.
- Failing to mention collaboration with quality assurance teams.
- Overlooking the importance of documentation in compliance.
Example answer
“At Nestlé, I regularly reviewed packaging materials against the latest food safety regulations. I attended industry workshops to stay informed about updates and ensured compliance by conducting routine audits of our packaging processes. By implementing a checklist system for our materials, we achieved a 100% compliance rate during our last inspection, which was crucial for maintaining our brand reputation.”
Skills tested
Question type
4. Lead Packaging Technician Interview Questions and Answers
4.1. Can you describe your experience with implementing new packaging processes or technologies?
Introduction
This question assesses your ability to innovate and improve operational efficiency in packaging, which is crucial for a lead technician role.
How to answer
- Start by providing a specific example of a packaging process or technology you implemented.
- Explain the rationale behind the implementation and the problems it aimed to solve.
- Detail the steps you took to roll out the new process or technology, including team involvement.
- Discuss any challenges faced during implementation and how you overcame them.
- Highlight the measurable outcomes and improvements resulting from the change.
What not to say
- Being vague about your experience or not providing specific examples.
- Focusing solely on the technology without discussing the process and team impact.
- Failing to acknowledge challenges or lessons learned during implementation.
- Not providing quantifiable results to demonstrate success.
Example answer
“At my previous role with a manufacturing company, I led the implementation of an automated packing line that reduced packaging time by 30%. I first conducted a thorough analysis of our existing process and identified bottlenecks. After researching suitable technology, I collaborated with the IT team and trained my staff on the new system. Although we faced some initial resistance, we held training sessions to address concerns. Ultimately, we improved our overall productivity and reduced labor costs significantly.”
Skills tested
Question type
4.2. Describe a time when you had to troubleshoot a packaging issue on the production line.
Introduction
This question evaluates your problem-solving skills and ability to work under pressure, which are vital for a lead technician managing packaging processes.
How to answer
- Use the STAR method to structure your response.
- Clearly explain the situation and the specific packaging issue encountered.
- Detail the steps you took to diagnose the problem and the resources you utilized.
- Describe how you collaborated with your team to resolve the issue.
- Discuss the outcome and any changes made to prevent similar issues in the future.
What not to say
- Avoid blaming others or external factors for the issue.
- Failing to provide specific steps taken to resolve the problem.
- Not discussing the outcome or any preventive measures implemented.
- Being overly technical without connecting it to team collaboration.
Example answer
“While working at a beverage packaging facility, we faced a sudden malfunction in one of our bottling machines during peak production. I quickly assessed the situation, identifying that the issue was due to a faulty sensor. I coordinated with the maintenance team to replace the sensor and temporarily rerouted production to another line. We managed to minimize downtime to only 30 minutes. Afterward, I initiated a review of our equipment maintenance schedule to ensure better monitoring and prevent future occurrences.”
Skills tested
Question type
5. Packaging Supervisor Interview Questions and Answers
5.1. Can you describe a time when you improved a packaging process in your previous role?
Introduction
This question is vital as it assesses your ability to identify inefficiencies and implement improvements within packaging processes, which is crucial for a Packaging Supervisor.
How to answer
- Start by outlining the specific packaging process you focused on.
- Explain the challenges or inefficiencies you identified.
- Detail the solution you implemented, including any tools or methodologies used.
- Quantify the results of your improvement, such as cost savings or increased efficiency.
- Reflect on what you learned from the experience and how it can apply to future processes.
What not to say
- Providing vague answers without specific examples.
- Focusing only on the problem without discussing the solution.
- Neglecting to mention measurable outcomes or results.
- Claiming improvements without evidence or data to back it up.
Example answer
“At my previous job at Coca-Cola Beverages South Africa, I noticed that our bottle labeling process was causing delays. I initiated a review and introduced a new labeling machine that reduced our labeling time by 30%. This change saved the company about R150,000 annually in labor costs and significantly improved our production line efficiency. This experience taught me the importance of continuous improvement and being proactive in identifying challenges.”
Skills tested
Question type
5.2. How do you ensure compliance with safety and quality standards in packaging operations?
Introduction
This question evaluates your understanding of safety and quality regulations, which are critical in packaging to ensure product integrity and compliance with industry standards.
How to answer
- Explain your knowledge of relevant safety and quality standards (e.g., ISO, HACCP).
- Detail the procedures and checks you implement to ensure compliance.
- Discuss how you train and inform your team about these standards.
- Provide examples of how you've addressed compliance issues in the past.
- Mention any tools or software you use for monitoring compliance.
What not to say
- Indicating that compliance is not a priority.
- Failing to mention specific standards or regulations.
- Not discussing team involvement in compliance training.
- Ignoring the importance of documentation and record-keeping.
Example answer
“In my role at Nestlé, I ensured compliance with ISO 22000 standards by implementing a rigorous training program for my team on food safety practices. We conducted weekly audits of our packaging processes and had a checklist to ensure every step adhered to safety protocols. This proactive approach helped us pass our external audits without any issues and improved our overall product quality. I believe that a strong culture of safety and quality is essential in packaging operations.”
Skills tested
Question type
Similar Interview Questions and Sample Answers
Simple pricing, powerful features
Upgrade to Himalayas Plus and turbocharge your job search.
Himalayas
Himalayas Plus
Himalayas Max
Find your dream job
Sign up now and join over 100,000 remote workers who receive personalized job alerts, curated job matches, and more for free!
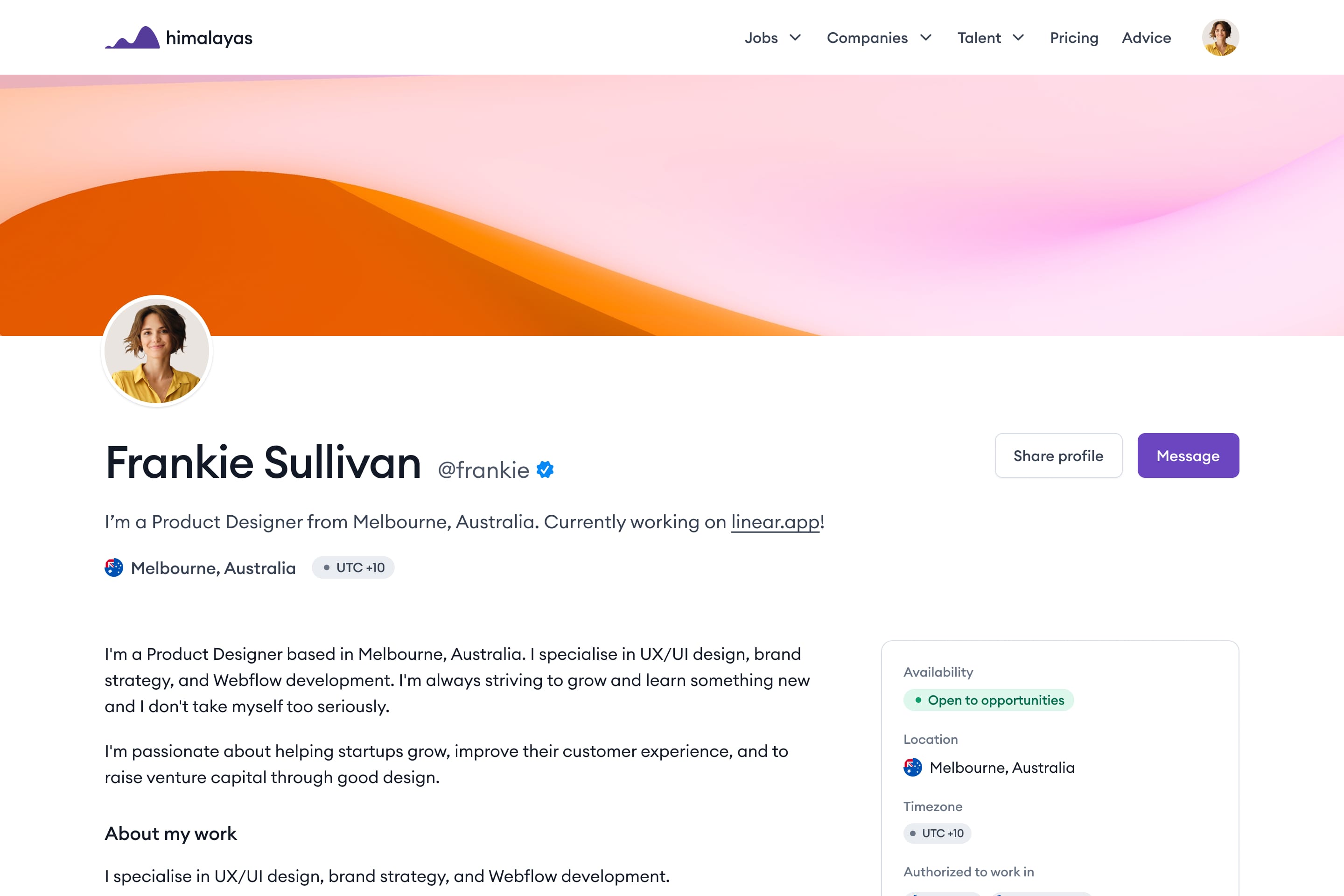