6 Manufacturing Process Engineer Interview Questions and Answers
Manufacturing Process Engineers are responsible for designing, implementing, and optimizing manufacturing processes to improve efficiency, quality, and cost-effectiveness. They work closely with production teams, quality assurance, and design engineers to ensure smooth operations and continuous improvement. Junior engineers focus on learning and supporting process improvements, while senior engineers lead projects, mentor teams, and drive strategic initiatives in manufacturing operations. Need to practice for an interview? Try our AI interview practice for free then unlock unlimited access for just $9/month.
Unlimited interview practice for $9 / month
Improve your confidence with an AI mock interviewer.
No credit card required
1. Junior Manufacturing Process Engineer Interview Questions and Answers
1.1. Can you describe a project where you improved a manufacturing process? What steps did you take?
Introduction
This question is important as it assesses your practical experience with process improvement, which is a key responsibility for a Junior Manufacturing Process Engineer.
How to answer
- Start with a brief overview of the project and its objectives.
- Detail the specific steps you took to identify and analyze the process.
- Explain the methodologies you applied, such as Lean or Six Sigma.
- Discuss the challenges you faced and how you overcame them.
- Quantify the results of your improvements, such as reduced cycle time or cost savings.
What not to say
- Describing a project without detailing your specific contributions.
- Focusing only on theoretical knowledge without practical applications.
- Failing to mention measurable outcomes from your improvements.
- Not addressing any challenges faced during the project.
Example answer
“During my internship at General Motors, I worked on a project to streamline the assembly line process for a specific vehicle model. I conducted a thorough analysis using Lean principles, identifying bottlenecks that delayed production. By implementing a new layout and training staff on efficient practices, we reduced assembly time by 15%, which translated to significant cost savings. This experience taught me the value of data-driven decision-making in manufacturing.”
Skills tested
Question type
1.2. How would you handle a situation where a manufacturing process is consistently producing defects?
Introduction
This question evaluates your analytical skills, problem-solving abilities, and your approach to quality control in manufacturing processes.
How to answer
- Describe your approach to identifying the root cause of the defects.
- Discuss the tools and techniques you would use, such as process mapping or statistical analysis.
- Explain how you would collaborate with team members to implement corrective actions.
- Mention how you would monitor the process post-implementation to ensure defects are reduced.
- Highlight the importance of documentation and reporting in this scenario.
What not to say
- Suggesting to ignore the problem or wait for it to resolve itself.
- Failing to mention a systematic approach to identify defects.
- Overlooking the need for teamwork in solving the issue.
- Not emphasizing the importance of continuous monitoring.
Example answer
“If faced with a consistent defect issue, I would first gather data to analyze the defect patterns. Using tools like Pareto analysis, I would identify the most common defects and their causes. I would collaborate with quality assurance and production teams to brainstorm corrective actions, such as adjusting machine settings or revising work instructions. Post-implementation, I’d monitor defect rates closely for a few weeks to ensure the issue is resolved before documenting the findings for future reference. This systematic approach not only addresses the immediate issue but also contributes to long-term quality improvements.”
Skills tested
Question type
2. Manufacturing Process Engineer Interview Questions and Answers
2.1. Can you describe a time when you improved the efficiency of a manufacturing process?
Introduction
This question is critical for a Manufacturing Process Engineer as it highlights your ability to identify inefficiencies and implement solutions that enhance productivity and reduce costs.
How to answer
- Use the STAR method (Situation, Task, Action, Result) to structure your response.
- Clearly outline the specific process and its inefficiencies that you encountered.
- Detail the steps you took to analyze the process and identify improvement opportunities.
- Explain the solutions you implemented and how you measured their effectiveness.
- Share quantifiable results, such as percentage increases in efficiency or cost savings.
What not to say
- Focusing only on theoretical knowledge without practical application.
- Vague descriptions that do not provide clear actions taken.
- Failing to mention collaboration with team members or other departments.
- Overlooking the importance of safety and quality standards in the process.
Example answer
“At a manufacturing facility in São Paulo, I identified that our assembly line was experiencing a 20% downtime due to equipment failures. I conducted a root cause analysis and implemented a predictive maintenance program, which involved regular inspections and using IoT sensors. This initiative reduced downtime by 40% and increased overall production efficiency by 15%, significantly decreasing costs.”
Skills tested
Question type
2.2. How do you ensure compliance with safety and quality standards in manufacturing processes?
Introduction
This question assesses your approach to maintaining safety and quality, which are paramount in manufacturing environments to protect employees and ensure product integrity.
How to answer
- Discuss specific safety and quality standards relevant to the industry, such as ISO or Six Sigma.
- Describe your methods for training team members on these standards.
- Explain your approach to conducting regular audits and inspections.
- Share examples of how you responded to safety or quality issues in the past.
- Highlight any certifications or training you have in quality assurance or safety management.
What not to say
- Indicating that safety and quality are not priorities.
- Providing a generic answer without specific examples.
- Failing to describe how you involve team members in these processes.
- Overlooking the importance of continuous improvement in safety and quality.
Example answer
“I prioritize safety and quality by implementing ISO 9001 standards in our processes. I conduct regular training sessions for the team to ensure everyone understands the protocols. I also perform monthly audits to identify potential risks and areas for improvement. For instance, when I noticed an increase in defect rates, I initiated a quality control program that reduced defects by 30% over six months, ensuring we consistently meet industry standards.”
Skills tested
Question type
3. Senior Manufacturing Process Engineer Interview Questions and Answers
3.1. Can you describe a time when you implemented a significant process improvement in a manufacturing setting?
Introduction
This question assesses your ability to identify inefficiencies and implement improvements, which is critical in a Senior Manufacturing Process Engineer role.
How to answer
- Use the STAR method (Situation, Task, Action, Result) to structure your answer.
- Clearly outline the initial situation and the specific problem you faced.
- Describe the process improvement you implemented, including your rationale and the steps taken.
- Quantify the results of your actions (e.g., cost savings, reduced cycle time, increased output).
- Discuss any challenges you faced during implementation and how you overcame them.
What not to say
- Focusing solely on technical details without explaining the business impact.
- Providing vague descriptions of improvements without specific metrics.
- Failing to mention teamwork or collaboration with other departments.
- Neglecting to address how you managed resistance to change.
Example answer
“At a manufacturing plant for Bosch in Mexico, I noticed that our assembly line was experiencing a 20% delay due to inefficient layout. I led a team to redesign the workflow, optimizing equipment placement and introducing a lean methodology. As a result, we reduced cycle time by 30%, which boosted overall productivity by 15%. This experience taught me the importance of data-driven decision-making and collaboration across teams.”
Skills tested
Question type
3.2. How do you ensure compliance with safety and quality standards in manufacturing processes?
Introduction
This question evaluates your knowledge of safety and quality standards, which are crucial in manufacturing environments.
How to answer
- Describe your understanding of relevant safety and quality standards (e.g., ISO, Six Sigma).
- Explain how you integrate these standards into process design and execution.
- Share specific examples of how you have monitored compliance in past roles.
- Discuss methods you use to train and educate staff on these standards.
- Highlight any tools or technologies you utilize for compliance tracking.
What not to say
- Implying that compliance is someone else's responsibility.
- Failing to mention proactive measures taken to prevent non-compliance.
- Providing generic answers without specific examples or standards.
- Neglecting to discuss the importance of a safety culture within the team.
Example answer
“In my previous role at General Electric in Mexico, I implemented a comprehensive training program on ISO 9001 standards for all staff. I regularly conducted audits and used real-time data analytics to track compliance. As a result, we achieved a 98% compliance rate and significantly reduced safety incidents, fostering a culture of quality and safety throughout the organization.”
Skills tested
Question type
4. Lead Manufacturing Process Engineer Interview Questions and Answers
4.1. Can you describe a time when you improved a manufacturing process and what impact it had on production efficiency?
Introduction
This question is crucial for assessing your ability to identify inefficiencies and implement effective solutions, which is a key responsibility for a Lead Manufacturing Process Engineer.
How to answer
- Use the STAR method (Situation, Task, Action, Result) to structure your response
- Clearly define the manufacturing process you focused on and the specific inefficiencies
- Describe the analysis you conducted to identify the root cause of the inefficiency
- Explain the steps you took to implement changes, including collaboration with cross-functional teams
- Highlight the measurable outcomes of your improvements, such as increased efficiency or reduced waste
What not to say
- Vaguely describing improvements without specific details or metrics
- Taking sole credit without acknowledging team contributions
- Focusing only on theoretical knowledge without real-world applications
- Neglecting to mention any challenges encountered during the process
Example answer
“At Bombardier, I identified a bottleneck in the assembly line that was causing a 15% delay in production. After analyzing the workflow, I reorganized the layout and introduced a new scheduling system. This change improved production efficiency by 20% and reduced waste by 10%. The project taught me the value of hands-on analysis and team collaboration.”
Skills tested
Question type
4.2. How do you approach training and mentoring junior engineers in manufacturing processes?
Introduction
This question evaluates your leadership and mentoring skills, which are vital for a Lead Manufacturing Process Engineer to ensure knowledge transfer and skill development within the team.
How to answer
- Describe your philosophy on mentorship and knowledge sharing
- Provide specific examples of how you have successfully trained junior engineers
- Discuss how you tailor your training approach to different learning styles
- Mention any structured training programs or materials you have developed or used
- Highlight the positive impacts of your mentorship on team performance
What not to say
- Implying that mentoring is not part of your job responsibilities
- Providing vague examples without measurable outcomes
- Focusing solely on technical training without addressing soft skills
- Describing a rigid training approach that doesn't accommodate individual differences
Example answer
“In my role at Magna International, I developed a mentorship program for junior engineers that included weekly hands-on training sessions and shadowing opportunities. I tailored the content based on individual learning styles, which led to a 30% faster onboarding process. My mentees reported feeling more confident in their roles and contributed to team projects more effectively.”
Skills tested
Question type
5. Principal Manufacturing Process Engineer Interview Questions and Answers
5.1. Can you describe a process improvement project you led that resulted in significant cost savings?
Introduction
This question assesses your ability to identify inefficiencies and implement solutions that drive cost savings, a crucial skill for a Principal Manufacturing Process Engineer.
How to answer
- Begin with a brief overview of the initial process and its challenges
- Detail the specific changes you proposed or implemented
- Quantify the cost savings achieved and describe how you measured success
- Discuss any tools or methodologies you used, such as Lean or Six Sigma
- Highlight how you engaged stakeholders and ensured team buy-in
What not to say
- Focusing too much on the technical details without mentioning the impact
- Providing vague descriptions without quantifiable results
- Neglecting to discuss the involvement of your team or stakeholders
- Claiming credit for a project without acknowledging team contributions
Example answer
“At my previous role with a semiconductor manufacturer, I identified inefficiencies in our wafer fabrication process that led to excessive scrap rates. By implementing a Lean Six Sigma project, I streamlined the workflow and reduced cycle time by 15%. This resulted in annual cost savings of over SGD 500,000. Engaging with cross-functional teams was critical to achieving these results, as it ensured everyone understood the changes and their benefits.”
Skills tested
Question type
5.2. How do you ensure compliance with safety and environmental regulations in manufacturing processes?
Introduction
This question evaluates your knowledge of regulatory compliance and your ability to implement safety measures, which are critical in manufacturing environments.
How to answer
- Discuss your understanding of relevant regulations in Singapore, such as OSHA or NEA guidelines
- Explain how you integrate compliance into the design and operation of manufacturing processes
- Share examples of audits or assessments you have conducted
- Detail your approach to training staff on safety protocols
- Mention any continuous improvement initiatives you’ve implemented to enhance compliance
What not to say
- Suggesting that compliance is not a priority in manufacturing
- Ignoring specific local regulations and frameworks
- Focusing solely on past experiences without discussing proactive measures
- Neglecting the importance of staff training and awareness
Example answer
“To ensure compliance with safety and environmental regulations, I regularly review Singapore's regulations and conduct internal audits to assess adherence. At my last company, I developed a training program for staff that emphasized the importance of safety protocols and environmental stewardship. This initiative led to a 30% reduction in safety incidents over a year. I also implemented a continuous feedback loop to stay updated on regulatory changes and adjust our processes accordingly.”
Skills tested
Question type
6. Manufacturing Engineering Manager Interview Questions and Answers
6.1. Can you describe a time when you implemented a process improvement in a manufacturing setting? What was the impact?
Introduction
This question evaluates your ability to identify inefficiencies and apply engineering principles to improve manufacturing processes, which is crucial for a Manufacturing Engineering Manager.
How to answer
- Use the STAR method to structure your answer: Situation, Task, Action, Result.
- Clearly describe the specific process that needed improvement.
- Explain the analysis you conducted to identify the root cause of inefficiencies.
- Detail the steps you took to implement the improvement, including any collaboration with teams.
- Quantify the impact of the improvement on production efficiency, costs, or quality.
What not to say
- Providing vague examples without specific metrics.
- Focusing too much on the problem and not on the solution.
- Neglecting to mention teamwork or collaboration aspects.
- Avoiding responsibility for the outcome of the initiative.
Example answer
“At Huawei, I identified that our assembly line had a bottleneck due to manual inspection processes. I led a cross-functional team to implement automated inspection systems, which reduced handling time by 30%. This improvement not only increased production throughput by 20% but also enhanced product quality, leading to a 15% decrease in return rates.”
Skills tested
Question type
6.2. How do you ensure your engineering team stays up-to-date with the latest manufacturing technologies?
Introduction
This question assesses your approach to continuous learning and development in a rapidly evolving field, which is essential for maintaining a competitive edge in manufacturing.
How to answer
- Discuss your strategies for fostering a culture of learning within your team.
- Mention specific training programs, workshops, or conferences you encourage attendance at.
- Explain how you share knowledge and best practices within the team.
- Describe your approach to evaluating new technologies and their applicability to your operations.
- Highlight any partnerships with educational institutions or industry groups.
What not to say
- Implying that staying updated is not a priority.
- Providing generic responses without specific examples.
- Failing to mention team involvement in learning initiatives.
- Ignoring the importance of adapting to industry trends.
Example answer
“I prioritize continuous learning by organizing monthly knowledge-sharing sessions where team members present on new technologies or processes they’ve researched. Additionally, I provide opportunities for my team to attend key industry conferences, such as the China International Industry Fair. This approach keeps us informed and encourages innovation. Recently, we adopted a new robotics technology that improved our production efficiency by 25%.”
Skills tested
Question type
Similar Interview Questions and Sample Answers
Simple pricing, powerful features
Upgrade to Himalayas Plus and turbocharge your job search.
Himalayas
Himalayas Plus
Himalayas Max
Find your dream job
Sign up now and join over 100,000 remote workers who receive personalized job alerts, curated job matches, and more for free!
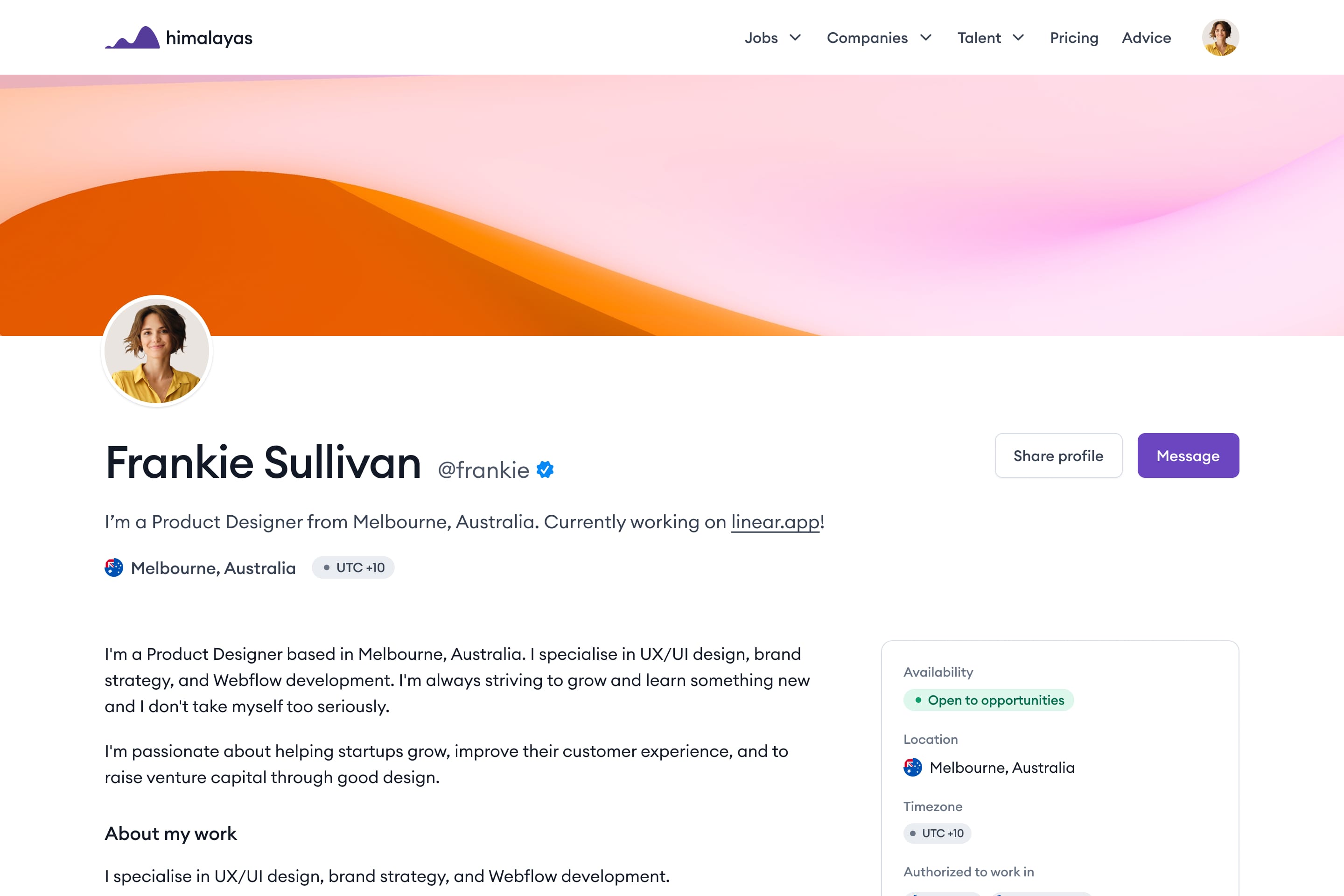