Complete Manufacturing Process Engineer Career Guide
Manufacturing Process Engineers are the architects of efficiency, optimizing production lines to reduce costs and boost quality across diverse industries. You'll solve complex operational challenges, ensuring products move seamlessly from raw materials to finished goods, making this a critical role for any company aiming for peak performance. This career offers a dynamic blend of technical problem-solving and hands-on implementation, driving tangible improvements in real-world production environments.
Key Facts & Statistics
Median Salary
$104,780 USD
(U.S. Bureau of Labor Statistics, May 2023)
Range: $65k - $150k+ USD, varying by experience, industry, and location
Growth Outlook
10%
faster than average (U.S. Bureau of Labor Statistics, 2022-2032)
Annual Openings
≈20,200
openings annually (U.S. Bureau of Labor Statistics, 2022-2032)
Top Industries
Typical Education
Bachelor's degree in engineering (e.g., Industrial, Mechanical, Chemical, or Manufacturing Engineering) is typically required; certifications in Six Sigma or Lean Manufacturing are highly valued.
What is a Manufacturing Process Engineer?
A Manufacturing Process Engineer defines, optimizes, and scales the methods and systems used to produce goods. This role focuses on translating product designs into efficient, repeatable, and high-quality production processes. They are the architects of the factory floor, ensuring that raw materials are transformed into finished products in the most effective way possible.
Unlike a Manufacturing Engineer who might focus more broadly on equipment and factory layout, or a Production Supervisor who manages daily output and personnel, the Process Engineer specifically hones in on the sequence of operations, the parameters of each step, and the flow of materials. They ensure that processes are robust, cost-effective, and capable of meeting production targets and quality standards, making them critical to a company's operational excellence and competitive edge.
What does a Manufacturing Process Engineer do?
Key Responsibilities
- Design and optimize manufacturing processes to improve efficiency, reduce waste, and enhance product quality.
- Conduct root cause analysis for production issues, implementing corrective actions to prevent recurrence.
- Develop and maintain process documentation, including standard operating procedures (SOPs), work instructions, and process flow diagrams.
- Collaborate with product design and R&D teams to ensure new products are manufacturable and meet production requirements.
- Implement automation solutions and new technologies to streamline production lines and increase output.
- Monitor key performance indicators (KPIs) such as yield, cycle time, and machine uptime, reporting on performance and proposing improvements.
- Train production staff on new processes, equipment, and safety protocols to ensure compliance and operational effectiveness.
Work Environment
Manufacturing Process Engineers typically split their time between an office setting and the factory floor. They spend significant time in manufacturing plants, observing production lines, troubleshooting equipment, and interacting with operators and technicians. The work environment can be dynamic, sometimes noisy, and requires adherence to safety protocols. Collaboration with cross-functional teams, including production, quality, design, and maintenance, is constant.
The pace of work can be fast, especially when addressing production bottlenecks or implementing new processes. While a standard work week is common, engineers may need to respond to urgent production issues or work extended hours during critical project phases. Travel is generally minimal, primarily within the local manufacturing facilities, but could involve visits to suppliers or other company sites.
Tools & Technologies
Manufacturing Process Engineers utilize a variety of tools and technologies to analyze, design, and optimize production systems. They frequently work with CAD/CAM software like AutoCAD, SolidWorks, or CATIA for process layout and fixture design. For data analysis and statistical process control (SPC), they use software such as Minitab, JMP, or Microsoft Excel, often integrated with enterprise resource planning (ERP) systems like SAP or Oracle for production data. Simulation software like Arena or FlexSim helps model and optimize production flows.
They also work with programmable logic controllers (PLCs) and human-machine interfaces (HMIs) for automation, alongside various sensors and control systems. Familiarity with robotics, vision systems, and additive manufacturing technologies is increasingly important. Project management software like Jira or Asana helps track improvement initiatives.
Manufacturing Process Engineer Skills & Qualifications
Manufacturing Process Engineers focus on optimizing production methods to improve efficiency, quality, and cost-effectiveness. The qualification landscape for this role emphasizes a blend of formal engineering education and practical experience. Entry-level positions typically require a bachelor's degree, while senior roles often benefit from a master's degree or extensive industry experience.
Requirements vary significantly based on the industry sector and company size. In highly regulated industries like aerospace or medical devices, deep knowledge of specific quality standards (e.g., ISO, FDA regulations) is crucial. Larger companies may prioritize candidates with experience in complex, automated systems, whereas smaller firms might value adaptability and broad problem-solving skills. Geographic location also plays a role, with some regions having a higher demand for specific industry specializations.
While formal education provides foundational principles, practical experience gained through internships, co-op programs, or prior roles is often more valued than theoretical knowledge alone. Certifications in lean manufacturing, Six Sigma, or specific software tools can significantly enhance a candidate's profile, demonstrating a commitment to continuous improvement methodologies. The skill landscape is continuously evolving, with increasing emphasis on automation, data analytics, and digital manufacturing technologies. Engineers must balance a deep understanding of core manufacturing principles with the ability to integrate new technologies. Prioritizing hands-on experience and continuous learning in emerging areas is essential for career progression.
Education Requirements
Technical Skills
- Lean Manufacturing principles (Value Stream Mapping, 5S, Kaizen)
- Six Sigma methodologies (DMAIC, statistical process control, Minitab)
- Process mapping and flow diagramming (Visio, BPMN)
- CAD/CAM software proficiency (SolidWorks, AutoCAD, CATIA)
- Simulation and modeling software (Arena, FlexSim, AnyLogic)
- Manufacturing Execution Systems (MES) and Enterprise Resource Planning (ERP) integration
- Automation and robotics fundamentals (PLC programming, industrial control systems)
- Statistical analysis and data interpretation for process optimization
- Quality Management Systems (ISO 9001, AS9100, ISO 13485)
- Design of Experiments (DoE) for process optimization and troubleshooting
- Root Cause Analysis techniques (5 Whys, Fishbone diagrams, FMEA)
- Material science and manufacturing processes (machining, welding, molding, assembly)
Soft Skills
- Problem-Solving: Identifying root causes of production issues and developing effective, sustainable solutions.
- Analytical Thinking: Interpreting complex data sets, identifying trends, and making data-driven decisions to optimize processes.
- Communication: Clearly articulating technical concepts, process improvements, and project statuses to diverse audiences, including operators, management, and cross-functional teams.
- Collaboration: Working effectively with production teams, quality control, R&D, and supply chain to implement changes and achieve common goals.
- Attention to Detail: Ensuring precise process documentation, accurate data collection, and adherence to strict quality and safety standards.
- Adaptability: Quickly adjusting to new technologies, changing production demands, and unexpected challenges in a dynamic manufacturing environment.
- Project Management: Planning, executing, and monitoring process improvement initiatives from inception to completion.
- Continuous Improvement Mindset: Proactively seeking opportunities to enhance efficiency, reduce waste, and improve product quality.
How to Become a Manufacturing Process Engineer
Becoming a Manufacturing Process Engineer involves optimizing production lines and improving efficiency, a role crucial across various industries. While a traditional engineering degree, specifically in Mechanical, Industrial, Chemical, or Manufacturing Engineering, is a common entry point, non-traditional paths are becoming more viable. Individuals with a strong technical background from vocational schools or military experience can transition, often by acquiring specific certifications or through apprenticeships.
The timeline for entry varies significantly. A recent graduate with a relevant degree might secure a role within 3-6 months. For career changers, especially those needing to build foundational knowledge, this journey could extend to 1-2 years, involving further education or intensive self-study. Geographic location plays a role; manufacturing hubs in the Midwest or Southeast United States, or industrial regions in Europe and Asia, often have more opportunities than smaller markets. Companies range from large corporations with structured graduate programs to smaller startups needing versatile engineers.
A common misconception is that this role is purely theoretical; in reality, it demands hands-on problem-solving and collaboration. While academic knowledge is essential, practical experience gained through internships, co-ops, or personal projects is often more critical for securing a position. Networking within professional organizations like SME or IIE, attending industry conferences, and connecting with mentors can open doors to unadvertised positions and provide invaluable insights into industry needs and current market conditions. Overcoming barriers often means demonstrating a strong aptitude for continuous improvement and a willingness to learn on the job.
Step 1
Step 2
Step 3
Step 4
Step 5
Step 6
Step 7
Education & Training Needed to Become a Manufacturing Process Engineer
Becoming a Manufacturing Process Engineer involves a blend of theoretical knowledge and practical application. Formal bachelor's degrees in engineering, typically Industrial, Mechanical, Chemical, or Manufacturing Engineering, form the traditional foundation. These 4-year programs can cost between $40,000 and $100,000+ for public universities and significantly more for private institutions. They provide a deep understanding of core engineering principles, materials science, and system optimization. Employers widely accept and often prefer these degrees, especially for entry-level positions requiring a strong analytical base.
Alternative learning paths, while less common for direct entry, can supplement or enhance a formal degree. Online courses and specialized certifications, ranging from a few hundred to a few thousand dollars, can focus on specific tools like Lean Six Sigma, CAD software, or automation systems. These typically take weeks to months to complete. While they do not replace a degree, they are excellent for continuous professional development and for engineers looking to specialize or upskill. Self-study, often through industry journals and open-source materials, offers flexibility but lacks formal credentialing.
Practical experience is crucial in this field. Internships during degree programs, co-op experiences, or entry-level roles as a junior engineer build valuable hands-on skills. Continuous learning is essential, as manufacturing processes and technologies evolve rapidly. Master's degrees, costing $20,000 to $60,000 and taking 1-2 years, are often pursued by engineers aiming for senior roles or specialized areas like advanced robotics or supply chain optimization. Industry-specific accreditations, such as Professional Engineer (PE) licensure, are vital for certain responsibilities and enhance credibility. The market values a blend of strong academic fundamentals and demonstrable problem-solving abilities in a manufacturing environment.
Manufacturing Process Engineer Salary & Outlook
Compensation for a Manufacturing Process Engineer varies significantly based on several factors. Geographic location plays a crucial role, with higher salaries typically found in regions with a high concentration of manufacturing industries and a higher cost of living, such as California, Texas, and Michigan. Conversely, areas with lower living expenses may offer more modest salaries. Experience level directly correlates with earning potential; entry-level engineers command starting salaries, while seasoned professionals with specialized expertise or leadership responsibilities earn substantially more.
Total compensation packages extend beyond base salary. They often include performance bonuses, which can be tied to production efficiency, cost savings, or project milestones. Equity options are less common in traditional manufacturing but can be a component in highly innovative or startup environments. Comprehensive benefits packages, including health insurance, retirement contributions like 401(k) matching, and paid time off, significantly enhance overall compensation. Many companies also offer professional development allowances for certifications or advanced degrees, reflecting an investment in employee growth.
Industry-specific trends also influence compensation. High-growth sectors like advanced manufacturing, aerospace, or medical devices often offer more competitive salaries compared to more mature industries. Companies with complex or highly automated processes may also pay a premium for specialized engineering talent. Effective salary negotiation, highlighting unique skills, proven project success, and in-demand expertise, can significantly increase earning potential. Remote work opportunities, while less prevalent for hands-on process engineering roles, can impact geographic arbitrage, allowing engineers to command higher salaries while residing in lower-cost areas, though on-site presence is often required for direct process oversight. International markets present their own distinct salary scales, typically benchmarked against local economic conditions rather than direct USD equivalents.
Salary by Experience Level
Level | US Median | US Average |
---|---|---|
Junior Manufacturing Process Engineer | $70k USD | $75k USD |
Manufacturing Process Engineer | $90k USD | $95k USD |
Senior Manufacturing Process Engineer | $110k USD | $115k USD |
Lead Manufacturing Process Engineer | $130k USD | $135k USD |
Principal Manufacturing Process Engineer | $150k USD | $155k USD |
Manufacturing Engineering Manager | $170k USD | $175k USD |
Market Commentary
The job market for Manufacturing Process Engineers shows steady demand, driven by the ongoing need for operational efficiency, cost reduction, and quality improvement across various industries. Current trends emphasize smart manufacturing, Industry 4.0 adoption, and automation, increasing the demand for engineers proficient in these areas. The U.S. Bureau of Labor Statistics projects a stable outlook for industrial engineers, a category that includes process engineers, with growth expected to remain consistent with the average for all occupations. This growth is fueled by companies investing in new technologies and optimizing existing production lines to remain competitive globally.
Emerging opportunities for Manufacturing Process Engineers are found in advanced materials, additive manufacturing, and sustainable production processes. As companies strive for carbon neutrality and circular economy models, engineers with expertise in waste reduction, energy efficiency, and eco-friendly manufacturing methods are becoming highly sought after. There is a strong supply of qualified candidates, but a persistent demand for those with specialized skills in automation, data analytics for process optimization, and specific industry experience (e.g., automotive, aerospace, pharmaceuticals).
The profession is relatively recession-resistant, as manufacturing companies continuously seek efficiency improvements regardless of economic cycles. However, economic downturns can slow down new capital expenditure projects, which might temporarily affect job growth in certain sectors. Geographic hotspots for these roles include traditional manufacturing hubs in the Midwest and Southeast U.S., as well as areas with burgeoning tech manufacturing like parts of California and Texas. Future-proofing this career involves continuous learning in areas like AI-driven process control, robotics, and lean manufacturing methodologies, ensuring engineers remain adaptable to technological advancements and evolving industry demands.
Manufacturing Process Engineer Career Path
Career progression for a Manufacturing Process Engineer involves a clear path from hands-on optimization to strategic leadership. Professionals typically begin by mastering specific production lines and gradually expand their influence to broader systems. This field offers distinct individual contributor (IC) tracks, focusing on deep technical expertise and innovation, and management tracks, which involve leading teams and overseeing engineering operations. Advancement speed depends on demonstrated impact, continuous learning, and adapting to new manufacturing technologies.
Factors influencing career velocity include specialization in areas like automation, lean manufacturing, or Six Sigma, and the type of company. Startups might offer faster progression and broader exposure, while large corporations provide structured paths and opportunities for deep specialization. Agencies or consulting firms allow engineers to gain diverse experience across multiple industries. Building a strong professional network and seeking mentorship are crucial for identifying opportunities and gaining insights into industry best practices. Certifications in lean manufacturing, Six Sigma, or specific automation platforms often mark significant milestones.
Lateral moves are common, allowing engineers to transition between different product lines, facility types, or even into related fields like quality assurance, supply chain, or product development. Some engineers pivot into project management or even entrepreneurship, leveraging their process optimization skills. Continuous skill development, particularly in data analytics, advanced materials, and digital manufacturing, is essential for sustained growth and opens doors to leadership and principal-level roles within the field.
Junior Manufacturing Process Engineer
0-2 yearsKey Focus Areas
Manufacturing Process Engineer
2-5 yearsKey Focus Areas
Senior Manufacturing Process Engineer
5-8 yearsKey Focus Areas
Lead Manufacturing Process Engineer
8-12 yearsKey Focus Areas
Principal Manufacturing Process Engineer
12+ yearsKey Focus Areas
Manufacturing Engineering Manager
8+ years total experience, with 2+ years in a Senior or Lead Engineering roleKey Focus Areas
Junior Manufacturing Process Engineer
0-2 yearsResponsible for supporting process improvement initiatives on a single production line or specific equipment. Collects data, assists with root cause analysis of production issues, and helps implement minor process adjustments under direct supervision. Executes defined experiments and documents findings. Decisions are typically reviewed by a senior engineer.
Key Focus Areas
Develop foundational skills in process documentation, data collection, and basic statistical analysis. Learn to use CAD software and simulation tools. Focus on understanding safety protocols and quality standards. Build communication skills to interact with production teams and supervisors effectively. Seek mentorship from senior engineers to understand practical applications.
Manufacturing Process Engineer
2-5 yearsManages and optimizes processes for one or more production lines. Identifies inefficiencies, designs and implements process improvements, and conducts detailed analyses of production data. Leads small to medium-sized projects aimed at reducing waste, improving quality, or increasing output. Provides technical support to production teams and helps troubleshoot complex issues independently. Makes recommendations on equipment and process changes.
Key Focus Areas
Master process mapping, value stream mapping, and advanced statistical process control. Develop proficiency in lean manufacturing principles and Six Sigma methodologies. Improve problem-solving skills and the ability to propose data-driven solutions. Begin to lead small-scale improvement projects. Cultivate cross-functional collaboration with maintenance, quality, and production teams.
Senior Manufacturing Process Engineer
5-8 yearsLeads significant process engineering projects, often spanning multiple production lines or departments. Develops and implements new manufacturing processes, equipment, and technologies. Provides technical leadership and guidance to other engineers. Conducts complex root cause analysis for major production challenges. Plays a key role in capital expenditure planning and new product introduction processes. Makes critical technical decisions with broad impact.
Key Focus Areas
Develop expertise in complex system optimization, advanced automation, and industry 4.0 technologies. Enhance project management skills, including budgeting and resource allocation. Mentor junior engineers and contribute to their development. Begin to influence departmental strategy and technology roadmaps. Pursue specialized certifications in areas like robotics or advanced analytics.
Lead Manufacturing Process Engineer
8-12 yearsActs as the primary technical expert and strategic leader for major manufacturing process initiatives. Oversees the design, development, and implementation of highly complex or novel manufacturing processes. Provides technical direction and mentorship to a team of engineers, often without direct reporting lines. Drives standardization and best practices across the organization. Influences long-term manufacturing strategy and technology adoption. Decisions have significant impact on production capabilities and costs.
Key Focus Areas
Focus on driving innovation and strategic initiatives across multiple manufacturing areas. Develop strong leadership and communication skills to influence stakeholders at various levels. Cultivate expertise in emerging manufacturing technologies and their strategic application. Contribute to intellectual property development and industry best practices. Begin to take on cross-organizational leadership roles.
Principal Manufacturing Process Engineer
12+ yearsServes as a top-tier technical authority and strategic advisor on all aspects of manufacturing processes across the entire organization or business unit. Drives enterprise-wide process excellence initiatives, influencing global manufacturing strategies and technology investments. Identifies breakthrough opportunities for process innovation and competitive advantage. Provides expert consultation on complex technical challenges. Decisions shape the company's long-term manufacturing capabilities and competitive position.
Key Focus Areas
Develop deep expertise in advanced manufacturing systems, global supply chain integration, and corporate-level strategic planning. Master the ability to translate business objectives into manufacturing solutions. Focus on thought leadership through publications, patents, or industry presentations. Cultivate executive-level communication and negotiation skills. Drive enterprise-wide innovation and continuous improvement culture.
Manufacturing Engineering Manager
8+ years total experience, with 2+ years in a Senior or Lead Engineering roleLeads and manages a team of Manufacturing Process Engineers, overseeing their projects, performance, and professional development. Responsible for setting departmental goals, managing budgets, and allocating resources effectively. Ensures alignment of engineering activities with overall manufacturing objectives. Represents the engineering function in cross-functional leadership meetings. Drives the implementation of best practices and continuous improvement initiatives within the team and across the manufacturing facility.
Key Focus Areas
Cultivate strong people management, coaching, and performance evaluation skills. Develop expertise in budget management, resource planning, and strategic workforce development. Focus on creating a high-performing engineering team and fostering a culture of continuous improvement. Enhance strategic planning and cross-functional leadership capabilities. Participate in talent acquisition and development programs.
Job Application Toolkit
Ace your application with our purpose-built resources:
Manufacturing Process Engineer Resume Examples
Proven layouts and keywords hiring managers scan for.
View examplesManufacturing Process Engineer Cover Letter Examples
Personalizable templates that showcase your impact.
View examplesTop Manufacturing Process Engineer Interview Questions
Practice with the questions asked most often.
View examplesManufacturing Process Engineer Job Description Template
Ready-to-use JD for recruiters and hiring teams.
View examplesGlobal Manufacturing Process Engineer Opportunities
Manufacturing Process Engineers find strong global demand across diverse industries, from automotive to semiconductors. This role translates well internationally, focusing on optimizing production lines and improving efficiency worldwide. Regulatory differences impact process design, especially in environmental or safety standards. Professionals seek international roles for exposure to advanced manufacturing techniques or specialized industry hubs. Certifications like Six Sigma or Lean Manufacturing hold global recognition, boosting mobility.
Global Salaries
Salaries for Manufacturing Process Engineers vary significantly by region and industry. In North America, particularly the US, entry-level engineers earn $65,000-$80,000 USD, while experienced professionals command $90,000-$130,000 USD. Canada offers similar ranges, though often slightly lower. Europe sees ranges of €45,000-€75,000 in Germany and Switzerland, but €35,000-€60,000 in countries like Spain or Italy. These figures reflect higher purchasing power in Germany and Switzerland due to stronger economies.
Asia-Pacific markets present diverse compensation. In Japan, salaries range from ¥5,000,000-¥9,000,000 (approx. $34,000-$61,000 USD), while in Singapore, they are S$60,000-S$100,000 (approx. $44,000-$74,000 USD). Cost of living adjustments are crucial; a higher nominal salary in Zurich might offer less purchasing power than a lower one in Berlin. Tax implications also differ, with some European countries having higher income tax rates than the US or Singapore, affecting take-home pay.
Latin America's salaries are generally lower, with Brazil offering R$80,000-R$150,000 (approx. $16,000-$30,000 USD) for experienced engineers. Middle Eastern countries like UAE provide tax-free salaries, ranging from AED 180,000-AED 300,000 (approx. $49,000-$82,000 USD). International experience and advanced degrees often increase compensation, especially in multinational corporations. Benefits packages also vary, with comprehensive healthcare and pension plans being common in Western Europe, while some Asian countries might offer more performance-based bonuses.
Remote Work
International remote work for Manufacturing Process Engineers is limited due to the hands-on nature of the role. Most tasks involve on-site observation, machinery interaction, and direct collaboration on factory floors. However, some aspects, like data analysis, process simulation, and documentation, can be performed remotely. This often applies to roles within corporate R&D or global optimization teams, where engineers support multiple sites from a central location.
Digital nomad opportunities are rare for core process engineering tasks, but a few companies hire for remote analytical or consulting roles. Legal and tax implications for international remote work require careful consideration, as engineers must comply with both their home country's and the employer's country's regulations. Time zone differences can pose collaboration challenges for global teams. Employer policies on international remote work vary; some large corporations may offer hybrid models or occasional remote work for specific projects.
Visa & Immigration
Manufacturing Process Engineers commonly use skilled worker visas for international assignments. Popular destinations include Germany (EU Blue Card), Canada (Express Entry), Australia (Skilled Nominated Visa), and the United States (H-1B visa, though highly competitive). Requirements typically include a relevant engineering degree, several years of experience, and a job offer from an employer in the target country. Education credential recognition is vital; engineers must often have their degrees assessed for equivalency.
Professional licensing might be necessary in some countries, like Canada or the US, before practicing independently. Visa timelines vary, from a few months for some EU countries to over a year for the US H-1B lottery. Language requirements are essential for non-English speaking countries, often requiring proficiency tests. Pathways to permanent residency often exist after several years of skilled employment, particularly in Canada and Australia. Some countries, like Germany, offer fast-track visas for highly skilled professionals in demand. Family visas usually accompany the primary applicant's visa, allowing dependents to join. Intra-company transfers are also common for multinational firms.
2025 Market Reality for Manufacturing Process Engineers
Understanding current market conditions for Manufacturing Process Engineers is crucial for career success. This role has seen significant evolution from 2023 to 2025, driven by post-pandemic reshoring efforts and the accelerating AI revolution.
Broader economic factors, such as inflation and supply chain stability, directly influence manufacturing investment and, consequently, demand for process engineers. Market realities vary considerably by experience level—entry-level roles face more competition—and by geographic region, depending on the concentration of manufacturing industries. Company size also plays a role, with larger corporations often having more structured hiring processes. This analysis provides an honest assessment to help engineers navigate these complex dynamics.
Current Challenges
Manufacturing Process Engineers face increased competition, especially at entry levels, as companies seek experienced talent. Economic uncertainty and supply chain volatility cause some firms to delay hiring. Additionally, the rapid integration of AI and automation demands new skills, creating a gap for engineers without recent training.
Job searches can extend, requiring persistence and targeted skill development.
Growth Opportunities
Despite challenges, strong opportunities exist for Manufacturing Process Engineers, particularly in high-tech manufacturing sectors and those adopting Industry 4.0 principles. Companies in electric vehicle production, advanced materials, and sustainable manufacturing are actively seeking engineers who can design and optimize next-generation processes.
Emerging roles include AI Integration Engineers, Robotics Process Specialists, and Digital Manufacturing Architects. Professionals can gain a competitive advantage by focusing on certifications in AI, machine learning, and industrial automation platforms. Expertise in data visualization, predictive analytics, and simulation software is highly valued.
Underserved markets often include regions with new factory builds or specialized production needs. Engineers who combine traditional process optimization with a deep understanding of AI-driven tools are uniquely positioned. Market corrections might open doors for strategic career moves into companies investing in long-term efficiency. Sectors like medical device manufacturing and defense remain resilient, offering stable opportunities. Investing in continuous learning, especially in AI applications for manufacturing, significantly boosts career prospects and helps time career moves effectively.
Current Market Trends
Hiring for Manufacturing Process Engineers in 2025 shows a nuanced picture, with strong demand in specific sectors like automotive, aerospace, and medical devices. These industries prioritize efficiency and advanced production methods. Many companies seek engineers who can optimize existing lines and integrate new technologies.
The integration of generative AI and advanced automation is profoundly reshaping the role. Employers now prioritize engineers who can not only manage traditional processes but also design, implement, and troubleshoot AI-driven systems. This includes predictive maintenance, smart quality control, and robotic process automation. Traditional manufacturing skills remain vital, but the emphasis shifts toward data analytics, machine learning fundamentals, and digital twin technology. Companies increasingly look for candidates who understand how to leverage AI to reduce waste, improve throughput, and enhance product quality.
Economic conditions, while stable in some manufacturing segments, lead to cautious hiring in others. Some larger firms might downsize or restructure, but mid-sized and specialized manufacturers continue to invest in process optimization. Salary trends are generally stable to slightly increasing for highly skilled engineers, particularly those proficient in AI and automation. Market saturation exists at generalist entry levels, but specialized roles with advanced tech skills see strong demand. Remote work is less common for this hands-on role, though some design and analysis tasks can be done off-site. Geographic variations are significant; areas with strong manufacturing bases, like the Midwest and Southeast U.S., show more robust markets. Cyclical trends tied to industrial output and capital expenditure also influence hiring.
Emerging Specializations
Technological advancement and industry evolution consistently generate new specialization opportunities across various fields. For manufacturing process engineers, this means a shift towards highly integrated, data-driven, and sustainable production paradigms. Early positioning in these emerging areas is crucial for career advancement in 2025 and beyond, allowing professionals to become indispensable leaders in next-generation manufacturing.
Specializing in cutting-edge fields often commands premium compensation and accelerated career growth. These roles address critical industry needs that traditional specializations may not fully encompass. While established specializations remain vital, exploring emerging areas offers a strategic advantage, balancing foundational expertise with future-oriented skills.
Many emerging areas begin as niche fields, gaining momentum over several years before becoming mainstream and creating significant job opportunities. This timeline allows proactive engineers to develop deep expertise before the market becomes saturated. Pursuing these cutting-edge specializations involves a calculated risk, as not all emerging trends achieve widespread adoption. However, the potential for high reward, including pioneering new methodologies and shaping industry standards, often outweighs this uncertainty for ambitious professionals.
Smart Factory Integration Specialist
Additive Manufacturing Process Engineer
Sustainable Manufacturing Process Engineer
AI/ML Process Optimization Engineer
Advanced Robotics & Automation Engineer
Pros & Cons of Being a Manufacturing Process Engineer
Making an informed career decision requires a thorough understanding of both the benefits and challenges associated with a particular profession. The experience of a Manufacturing Process Engineer can vary significantly based on the industry, company culture, specific products manufactured, and the engineer's individual specialization. Factors like company size, technological maturity, and geographic location also play a crucial role in shaping the day-to-day realities. Moreover, the pros and cons may shift at different career stages; for instance, early-career engineers might focus more on learning and technical challenges, while senior engineers might deal more with strategic and leadership aspects. What one person considers an advantage, like a fast-paced environment, another might view as a disadvantage. This assessment aims to provide a realistic and balanced perspective to help set appropriate expectations for this vital role.
Pros
- Manufacturing Process Engineers play a critical role in optimizing production, directly impacting a company's bottom line by improving efficiency, reducing waste, and cutting costs. This direct contribution provides a strong sense of purpose and tangible impact within the organization.
- There is significant demand for skilled Manufacturing Process Engineers across diverse industries, including automotive, aerospace, pharmaceuticals, consumer goods, and electronics, ensuring strong job security and diverse career paths. This broad applicability makes the skill set highly transferable.
- The role offers continuous intellectual stimulation through problem-solving and process optimization, as engineers constantly analyze complex systems, identify bottlenecks, and develop innovative solutions. Each day presents new technical challenges to overcome.
- Manufacturing Process Engineers gain hands-on experience with cutting-edge technologies, automation, and lean manufacturing principles, which are highly valued skills in today's industrial landscape. This exposure ensures continuous professional development and marketability.
- The position offers a clear career progression path, from entry-level roles to senior engineer, lead engineer, and eventually management or specialized consulting positions within manufacturing or operations. There are ample opportunities for growth and specialization.
- Engineers frequently work on diverse projects, from designing new production lines to implementing quality control systems or troubleshooting existing processes, preventing monotony and offering varied learning experiences. This project-based work keeps the role dynamic and engaging.
- This role provides opportunities to travel to different manufacturing sites, suppliers, or customer locations, which can be a significant advantage for those who enjoy variety and gaining exposure to different operational environments and cultures.
Cons
- Manufacturing Process Engineers often face high-pressure environments during production issues or new product introductions, which can lead to extended hours and significant stress to maintain output and quality. The role frequently involves troubleshooting complex problems on the factory floor, demanding quick thinking and effective solutions under tight deadlines.
- The work environment can be physically demanding, requiring time spent in noisy, hot, or otherwise challenging factory settings. Exposure to various industrial hazards, even with safety protocols, remains a consistent factor in this profession.
- Career progression can sometimes feel limited within a single plant, as promotions to senior engineering or management roles may require relocating or gaining experience across different manufacturing sites or product lines. Opportunities for advancement are often tied to specific organizational structures.
- Continuous learning is essential, as new technologies, materials, and production methods emerge regularly, requiring engineers to constantly update their skills and knowledge outside of regular work hours. Staying current demands significant personal investment.
- The role often involves extensive cross-functional collaboration with production, quality, maintenance, and design teams, which can lead to conflicting priorities and the need for constant negotiation and compromise. Managing these diverse expectations can be a significant challenge.
- Process engineers are directly responsible for efficiency and cost reduction, meaning their performance is under constant scrutiny and tied to tangible financial metrics. This pressure for continuous improvement can create a demanding work climate.
- Implementing changes can be slow and bureaucratic in large organizations, as new processes often require extensive validation, approvals, and buy-in from multiple departments. This can be frustrating for engineers eager to see their improvements realized quickly, leading to perceived stagnation or delays in project execution.
Frequently Asked Questions
Manufacturing Process Engineers face distinct challenges balancing efficiency improvements with quality control and safety. This section addresses common questions about entering this role, from required technical skills and problem-solving approaches to career progression and the impact of new technologies on the profession.
What educational background and specific skills are essential to become a Manufacturing Process Engineer?
A bachelor's degree in engineering, typically industrial, mechanical, chemical, or manufacturing engineering, is the standard entry requirement. Some roles may prefer or require a master's degree, especially for senior positions or specialized industries. Strong analytical skills, a solid understanding of manufacturing principles, and experience with CAD software are also highly valued.
How long does it typically take to become job-ready as a Manufacturing Process Engineer, especially if I'm transitioning from a related field?
Transitioning into this role often involves gaining practical experience through internships or entry-level positions like manufacturing technician or junior engineer. Many professionals find that securing an internship during their engineering studies provides a direct pathway. For those changing careers, a relevant engineering degree combined with project-based learning or certifications in lean manufacturing or Six Sigma can accelerate the process.
What are the realistic salary expectations for a Manufacturing Process Engineer at different career stages?
Entry-level salaries for Manufacturing Process Engineers typically range from $60,000 to $75,000 annually, varying by industry, location, and company size. Mid-career professionals with 5-10 years of experience can expect to earn $80,000 to $110,000. Senior or specialized roles can command salaries well over $120,000, particularly in high-demand sectors like aerospace or pharmaceuticals.
What kind of work-life balance can I expect in this role, and how demanding are the hours?
The work-life balance for a Manufacturing Process Engineer can vary significantly depending on the industry and specific company. While standard 40-hour weeks are common, project deadlines, production issues, or new equipment installations can sometimes require longer hours or weekend work. Roles in continuous production environments might involve on-call duties. Generally, it's a demanding but manageable career.
Is the job market for Manufacturing Process Engineers growing, or is it at risk from automation?
The job market for Manufacturing Process Engineers remains stable and is expected to grow, driven by advancements in automation, smart manufacturing, and the continuous need for efficiency improvements across various industries. While some manufacturing jobs face automation risks, the role of a Process Engineer, which involves designing, optimizing, and troubleshooting complex systems, is highly resilient and in demand.
What are the typical career growth opportunities and advancement paths for a Manufacturing Process Engineer?
Career growth paths for a Manufacturing Process Engineer are diverse. You can advance to senior process engineer, lead engineer, or engineering manager roles. Specialization in areas like lean manufacturing, Six Sigma, or specific manufacturing technologies (e.g., additive manufacturing, robotics) also opens doors. Opportunities exist to move into R&D, project management, or even executive leadership within manufacturing operations.
What are the biggest day-to-day challenges or common frustrations that Manufacturing Process Engineers face?
The most common challenges include balancing quality control with production speed, troubleshooting complex machinery or process failures under pressure, and implementing changes that require significant stakeholder buy-in. Adapting to new technologies and continuous learning about advanced manufacturing techniques are also ongoing challenges. Effective communication and problem-solving skills are crucial for navigating these hurdles.
Is remote work a realistic option for Manufacturing Process Engineers, or is it primarily an on-site role?
While some administrative or design tasks can be done remotely, the core function of a Manufacturing Process Engineer involves hands-on work with production lines, equipment, and on-site teams. Therefore, this role is primarily on-site. Hybrid models might be possible for certain aspects, but frequent presence on the factory floor is generally required to observe processes, conduct tests, and implement improvements directly.
Related Careers
Explore similar roles that might align with your interests and skills:
Manufacturing Engineer
A growing field with similar skill requirements and career progression opportunities.
Explore career guideProcess Development Engineer
A growing field with similar skill requirements and career progression opportunities.
Explore career guideProcess Engineer
A growing field with similar skill requirements and career progression opportunities.
Explore career guideProduction Engineer
A growing field with similar skill requirements and career progression opportunities.
Explore career guideProcess Engineering Manager
A growing field with similar skill requirements and career progression opportunities.
Explore career guideAssess your Manufacturing Process Engineer readiness
Understanding where you stand today is the first step toward your career goals. Our Career Coach helps identify skill gaps and create personalized plans.
Skills Gap Analysis
Get a detailed assessment of your current skills versus Manufacturing Process Engineer requirements. Our AI Career Coach identifies specific areas for improvement with personalized recommendations.
See your skills gapCareer Readiness Assessment
Evaluate your overall readiness for Manufacturing Process Engineer roles with our AI Career Coach. Receive personalized recommendations for education, projects, and experience to boost your competitiveness.
Assess your readinessSimple pricing, powerful features
Upgrade to Himalayas Plus and turbocharge your job search.
Himalayas
Himalayas Plus
Himalayas Max
Find your dream job
Sign up now and join over 100,000 remote workers who receive personalized job alerts, curated job matches, and more for free!
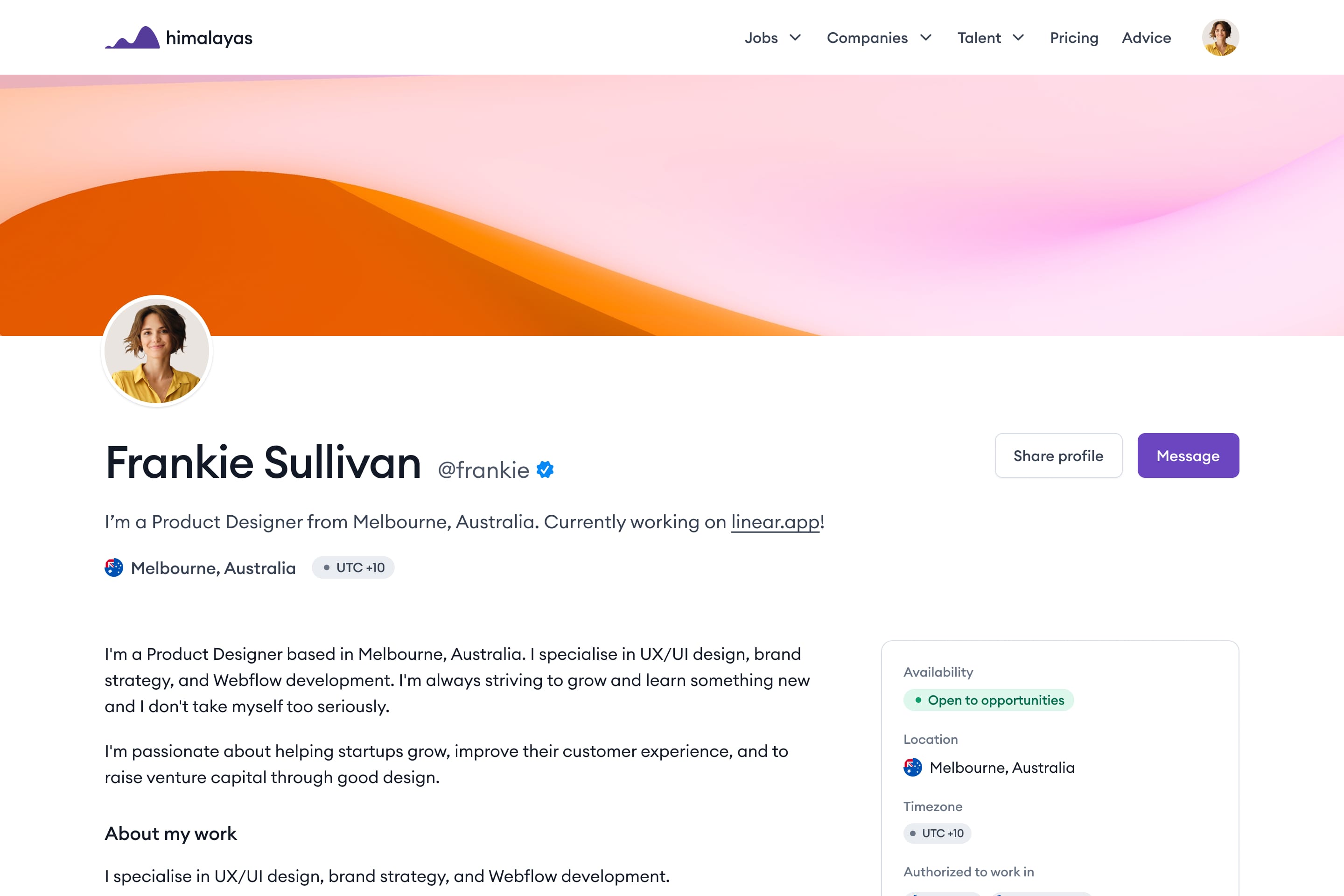