7 Process Development Engineer Interview Questions and Answers
Process Development Engineers focus on designing, optimizing, and implementing manufacturing or production processes to improve efficiency, quality, and cost-effectiveness. They work closely with cross-functional teams, including R&D, production, and quality assurance, to develop scalable and reliable processes. Junior engineers typically assist in process testing and data analysis, while senior and lead engineers take on responsibilities such as process design, troubleshooting, and leading process improvement initiatives. At managerial levels, they oversee teams and drive strategic process development goals. Need to practice for an interview? Try our AI interview practice for free then unlock unlimited access for just $9/month.
Unlimited interview practice for $9 / month
Improve your confidence with an AI mock interviewer.
No credit card required
1. Junior Process Development Engineer Interview Questions and Answers
1.1. Can you describe a project where you had to analyze and improve a manufacturing process?
Introduction
This question assesses your problem-solving abilities and understanding of process development, which are crucial for a Junior Process Development Engineer.
How to answer
- Use the STAR method to outline the situation, task, action, and result.
- Clearly describe the manufacturing process you were analyzing.
- Explain the specific challenges or inefficiencies you identified.
- Detail the steps you took to analyze the process and the tools or methodologies you used.
- Quantify the improvements achieved and discuss how they impacted the overall production.
What not to say
- Avoid vague descriptions without specifics on your role or contributions.
- Don't focus solely on technical jargon without explaining it in simple terms.
- Steer clear of discussing projects where you played a minimal role.
- Neglecting to mention the outcomes or improvements resulting from your actions.
Example answer
“At my internship with a semiconductor manufacturer, I analyzed the wafer fabrication process, which was experiencing high defect rates. I utilized statistical process control charts to identify trends and pinpointed an issue with temperature fluctuations. By collaborating with the engineering team, we adjusted the temperature settings and implemented regular maintenance checks, leading to a 30% reduction in defects and improving yield rates by 15%. This experience reinforced my understanding of process optimization and teamwork.”
Skills tested
Question type
1.2. How do you prioritize tasks when working on multiple projects with tight deadlines?
Introduction
This question evaluates your time management and prioritization skills, which are essential in a fast-paced engineering environment.
How to answer
- Discuss your method for assessing the urgency and importance of tasks.
- Explain how you communicate with team members and stakeholders to align priorities.
- Share a specific example of a time you effectively managed competing deadlines.
- Detail any tools or techniques you use to keep track of your tasks.
- Emphasize your ability to remain flexible and adapt to changing priorities.
What not to say
- Claiming you always prioritize your own tasks without considering team needs.
- Avoiding specific examples, which can make your answer seem generic.
- Neglecting to mention how you deal with unforeseen challenges or changes.
- Implying that you struggle with managing deadlines without showing improvement strategies.
Example answer
“In my previous role as an intern, I was assigned to two projects with overlapping deadlines. I used a priority matrix to assess tasks based on urgency and importance. I communicated with my supervisors to clarify priorities, which helped me focus on delivering critical components first. I also used a project management tool to track progress and ensure nothing fell through the cracks. As a result, both projects were completed on time, with positive feedback from my supervisors on the quality of my work.”
Skills tested
Question type
2. Process Development Engineer Interview Questions and Answers
2.1. Can you describe a project where you improved a manufacturing process? What steps did you take?
Introduction
This question assesses your problem-solving skills and ability to drive process improvements, which are crucial for a Process Development Engineer.
How to answer
- Start with a brief overview of the project and the initial challenges faced.
- Detail the specific methodologies or tools you employed (e.g., Six Sigma, Lean Manufacturing).
- Explain how you gathered data and involved stakeholders in the improvement process.
- Discuss the changes you implemented and their impact on efficiency or quality.
- Quantify your results with specific metrics (e.g., cost savings, time reduction).
What not to say
- Focusing only on technical details without mentioning the project's impact.
- Not addressing the challenges faced during the project.
- Omitting team collaboration or stakeholder involvement.
- Providing vague metrics or results that lack context.
Example answer
“At BHP, I was tasked with improving the ore processing efficiency. I applied Lean Manufacturing principles, mapping the entire process to identify bottlenecks. By redesigning the layout and introducing standard operating procedures, we improved the overall throughput by 30% and reduced waste by 20%. This experience underscored the value of data-driven decision-making and cross-functional teamwork.”
Skills tested
Question type
2.2. How do you ensure compliance with safety and quality standards in process development?
Introduction
This question evaluates your understanding of regulatory requirements and your commitment to safety and quality in engineering processes.
How to answer
- Discuss your knowledge of relevant industry standards (e.g., ISO, AS/NZS standards).
- Explain how you incorporate safety considerations into the design process.
- Share examples of how you have conducted risk assessments and audits.
- Describe how you communicate and enforce compliance standards within your team.
- Mention any training or initiatives you have led to promote safety and quality awareness.
What not to say
- Suggesting that compliance is not a priority in your work.
- Failing to provide specific examples of safety or quality initiatives.
- Overlooking the importance of team communication regarding standards.
- Indicating that you rely solely on others to ensure compliance.
Example answer
“In my role at CSL Limited, I ensured compliance by adhering to ISO 9001 standards. I conducted thorough risk assessments and implemented proactive safety measures during the development phase. I also facilitated regular training workshops to keep the team updated on compliance protocols. As a result, we maintained a 100% compliance record during audits over three consecutive years.”
Skills tested
Question type
3. Senior Process Development Engineer Interview Questions and Answers
3.1. Can you describe a time when you improved a manufacturing process that led to significant cost savings?
Introduction
This question evaluates your ability to identify inefficiencies and implement solutions that enhance productivity and reduce costs, which is a crucial skill for a Senior Process Development Engineer.
How to answer
- Use the STAR method to structure your response: Situation, Task, Action, Result.
- Start by describing the initial state of the manufacturing process and the specific issues you identified.
- Explain the analysis methods you used to determine the root causes of inefficiencies.
- Detail the steps you took to implement improvements, including any innovative techniques or technologies utilized.
- Quantify the cost savings or efficiency gains achieved as a result of your improvements.
What not to say
- Focusing solely on the technical details without discussing the business impact.
- Not providing specific metrics or results related to cost savings.
- Neglecting to mention collaboration with other teams or stakeholders.
- Overstating your role without acknowledging contributions from others.
Example answer
“At Boeing, I noticed our assembly line for a specific aircraft model had a bottleneck that caused delays. I analyzed the workflow and identified that we could optimize the layout and reduce handling time by 30%. By implementing a new tooling strategy and training the team, we achieved a 20% reduction in production costs, saving the company approximately $1 million annually.”
Skills tested
Question type
3.2. How do you ensure the successful implementation of new processes in a cross-functional team environment?
Introduction
This question assesses your ability to work collaboratively across departments, which is essential for a Senior Process Development Engineer tasked with implementing new processes.
How to answer
- Discuss your approach to stakeholder engagement and communication.
- Highlight how you gather input from various functions to understand their needs and concerns.
- Explain the importance of providing training and support during the transition to new processes.
- Share examples of how you have successfully led cross-functional teams through change.
- Mention any tools or methodologies you use to track progress and gather feedback.
What not to say
- Indicating that you work in isolation without collaboration.
- Failing to address the importance of communication and training.
- Overlooking the need for continuous feedback and adjustment.
- Describing a lack of structured approach to implementation.
Example answer
“While working at General Electric, I led a project to implement a new quality control process that required input from engineering, production, and quality assurance teams. I conducted workshops to gather insights from each function and used those insights to tailor the implementation plan. After rolling out the new process, I held training sessions and established a feedback mechanism, which allowed us to refine the process based on real-time experiences. This collaborative approach resulted in a 15% reduction in defects and improved overall team satisfaction.”
Skills tested
Question type
4. Lead Process Development Engineer Interview Questions and Answers
4.1. Can you describe a process improvement project you led that resulted in significant cost savings?
Introduction
This question assesses your ability to identify inefficiencies and implement effective solutions, which is crucial for a Lead Process Development Engineer tasked with optimizing operations.
How to answer
- Outline the initial state of the process and the specific inefficiencies identified
- Describe the approach you took to analyze the process and develop an improvement plan
- Highlight the collaboration with cross-functional teams during the project
- Quantify the cost savings achieved and any other performance improvements
- Reflect on the lessons learned and how they can be applied to future projects
What not to say
- Failing to provide concrete metrics or data to support your claims
- Taking sole credit without acknowledging team contributions
- Focusing too much on the technical details without discussing the business impact
- Neglecting to mention any challenges faced during the project
Example answer
“At a previous role with Repsol, I led a project to streamline our chemical processing line, identifying bottlenecks that increased production costs by 20%. By implementing lean methodologies and enhancing equipment maintenance schedules, we reduced operational costs by €500,000 annually. This experience taught me the importance of cross-departmental collaboration in driving sustainable improvements.”
Skills tested
Question type
4.2. How do you approach developing a new process from scratch? What steps do you take?
Introduction
This question evaluates your systematic thinking and engineering design skills, which are essential for creating efficient and effective processes as a Lead Process Development Engineer.
How to answer
- Start by discussing how you gather requirements and define objectives
- Explain your research and benchmarking process against industry standards
- Detail your approach to designing the process, including selecting technology and equipment
- Describe how you validate the process through testing and iterations
- Mention how you ensure compliance with safety and regulatory standards
What not to say
- Rushing through the design phase without proper analysis
- Neglecting stakeholder input or requirements
- Overlooking the importance of safety and compliance
- Providing a vague answer without a clear step-by-step approach
Example answer
“When developing a new process at Acciona, I start by conducting thorough stakeholder interviews to gather requirements and expectations. I then research best practices, benchmarking against top competitors. After designing the process, I run simulations to validate its efficiency and ensure it meets all safety regulations. This structured approach leads to robust and scalable processes, as evidenced by our successful launch of a new waste processing system that increased throughput by 30%.”
Skills tested
Question type
5. Principal Process Development Engineer Interview Questions and Answers
5.1. Can you describe a complex process development project you led and the challenges you faced?
Introduction
This question is crucial for evaluating your experience with process development, problem-solving abilities, and leadership skills in managing complex engineering projects.
How to answer
- Utilize the STAR method (Situation, Task, Action, Result) for clarity
- Provide context about the project's scope and objectives
- Detail the specific challenges encountered during the project
- Illustrate the actions you took to address these challenges
- Quantify the results or improvements achieved as a result of your leadership
What not to say
- Focusing too much on technical jargon without explaining the project context
- Neglecting to mention your role or contributions
- Overlooking the importance of teamwork and collaboration
- Failing to discuss the impact of your actions on project outcomes
Example answer
“At Bombardier, I led a process development project for a new aircraft component that required innovative material selection. We faced challenges with supplier quality and regulatory compliance. By implementing a rigorous testing protocol and collaborating closely with suppliers, we improved material reliability by 30% and reduced production costs by 15%. This experience taught me the value of cross-functional teamwork and proactive problem-solving.”
Skills tested
Question type
5.2. How do you approach optimization in process development to ensure efficiency and cost-effectiveness?
Introduction
This question assesses your analytical skills and understanding of process optimization techniques, which are vital for a Principal Process Development Engineer.
How to answer
- Outline the optimization methodologies you are familiar with (e.g., Lean, Six Sigma)
- Discuss how you gather data and analyze processes for improvement opportunities
- Provide examples of specific optimization initiatives you've implemented
- Explain how you measure success and ensure continuous improvement
- Highlight your collaboration with other departments to drive optimization
What not to say
- Suggesting that optimization is a one-time effort rather than an ongoing process
- Failing to provide concrete examples of past successes
- Overlooking the importance of team input in optimization efforts
- Neglecting to mention key performance indicators used to measure success
Example answer
“In my role at General Motors, I applied Six Sigma principles to streamline the manufacturing process of a key component, resulting in a 20% reduction in cycle time and a savings of $500,000 annually. I analyzed process data, identified bottlenecks, and collaborated with cross-functional teams to implement solutions. By focusing on continuous improvement, we maintained these gains and fostered a culture of efficiency.”
Skills tested
Question type
6. Process Development Manager Interview Questions and Answers
6.1. Can you describe a process improvement project you led that resulted in significant efficiency gains?
Introduction
This question is crucial as it assesses your ability to identify inefficiencies and implement changes that positively impact operational performance, which is a core responsibility of a Process Development Manager.
How to answer
- Use the STAR (Situation, Task, Action, Result) method to structure your response
- Clearly outline the initial situation and the specific inefficiencies you identified
- Detail the steps you took to analyze the process and develop a solution
- Quantify the results by providing metrics that demonstrate the efficiency gains achieved
- Reflect on the lessons learned and how you would apply them in future projects
What not to say
- Focusing only on the technical aspects without mentioning team involvement
- Providing vague examples without specific metrics or outcomes
- Neglecting to highlight the importance of stakeholder buy-in
- Avoiding discussion of challenges faced during the project
Example answer
“At a manufacturing plant in Brazil, I noticed that our assembly line had excessive downtime due to manual processes. I led a cross-functional team to map out the workflow, identifying key bottlenecks. By implementing automation in the sorting phase, we reduced downtime by 30% and increased production output by 20%. This taught me the importance of engaging the team in process design for better acceptance and implementation.”
Skills tested
Question type
6.2. How do you ensure that process changes are adopted and sustained within an organization?
Introduction
This question evaluates your change management skills and ability to foster a culture of continuous improvement, essential for a Process Development Manager tasked with driving operational changes.
How to answer
- Discuss your approach to communication and training during the change process
- Explain how you engage stakeholders at all levels to gain buy-in
- Describe the methods you use to monitor the adoption of new processes
- Highlight the importance of feedback loops and continuous improvement
- Provide examples of how you have successfully sustained changes in the past
What not to say
- Suggesting that training is unnecessary for successful implementation
- Ignoring the importance of ongoing support and resources
- Failing to mention the need for regular assessments of process effectiveness
- Overlooking the role of leadership in championing change
Example answer
“When implementing a new inventory management system, I ensured all team members received comprehensive training and had access to ongoing support. I held regular check-ins to gather feedback and addressed concerns promptly. By establishing a rewards system for teams that embraced the new processes, we achieved a 95% adoption rate within three months and sustained it through quarterly reviews.”
Skills tested
Question type
7. Director of Process Development Interview Questions and Answers
7.1. Can you describe a project where you successfully improved a process and the impact it had on the organization?
Introduction
This question is crucial for assessing your ability to drive process improvements and measure their impact, which is essential for a role focused on process development.
How to answer
- Use the STAR method (Situation, Task, Action, Result) to structure your response
- Clearly outline the initial process and its limitations
- Detail the analysis you conducted to identify areas for improvement
- Explain the specific changes you implemented and the rationale behind them
- Share measurable outcomes that demonstrate the impact on efficiency, cost savings, or quality
What not to say
- Focusing on the problem without detailing how you resolved it
- Providing vague outcomes without specific metrics or results
- Claiming success without acknowledging team collaboration
- Ignoring the challenges faced during implementation
Example answer
“At Sasol, I led a project to streamline our chemical manufacturing process which was facing significant delays. After mapping the existing process, I identified bottlenecks in material flow and implemented a new scheduling system. This change reduced production lead time by 30% and increased output by 15%, resulting in cost savings of R2 million annually.”
Skills tested
Question type
7.2. How do you ensure that process changes are effectively communicated and implemented across diverse teams?
Introduction
This question assesses your communication and change management skills, which are vital for ensuring successful adoption of new processes within an organization.
How to answer
- Describe your approach to stakeholder engagement and communication
- Explain how you tailor your messaging for different audiences
- Detail any training or support you provide to facilitate implementation
- Discuss how you gather feedback and adjust the process based on team inputs
- Highlight the importance of building a culture of continuous improvement
What not to say
- Suggesting that communication is not your responsibility
- Failing to mention specific strategies for engaging diverse teams
- Overlooking the need for training or support
- Ignoring the role of feedback in the implementation process
Example answer
“I prioritize clear and open communication when implementing process changes. At Vodacom, I held workshops with various teams to explain the changes and gather their input. I also developed a training program to ensure everyone felt confident in the new process. By creating channels for ongoing feedback, we were able to make necessary adjustments, resulting in a smoother implementation and buy-in from all stakeholders.”
Skills tested
Question type
Similar Interview Questions and Sample Answers
Simple pricing, powerful features
Upgrade to Himalayas Plus and turbocharge your job search.
Himalayas
Himalayas Plus
Himalayas Max
Find your dream job
Sign up now and join over 100,000 remote workers who receive personalized job alerts, curated job matches, and more for free!
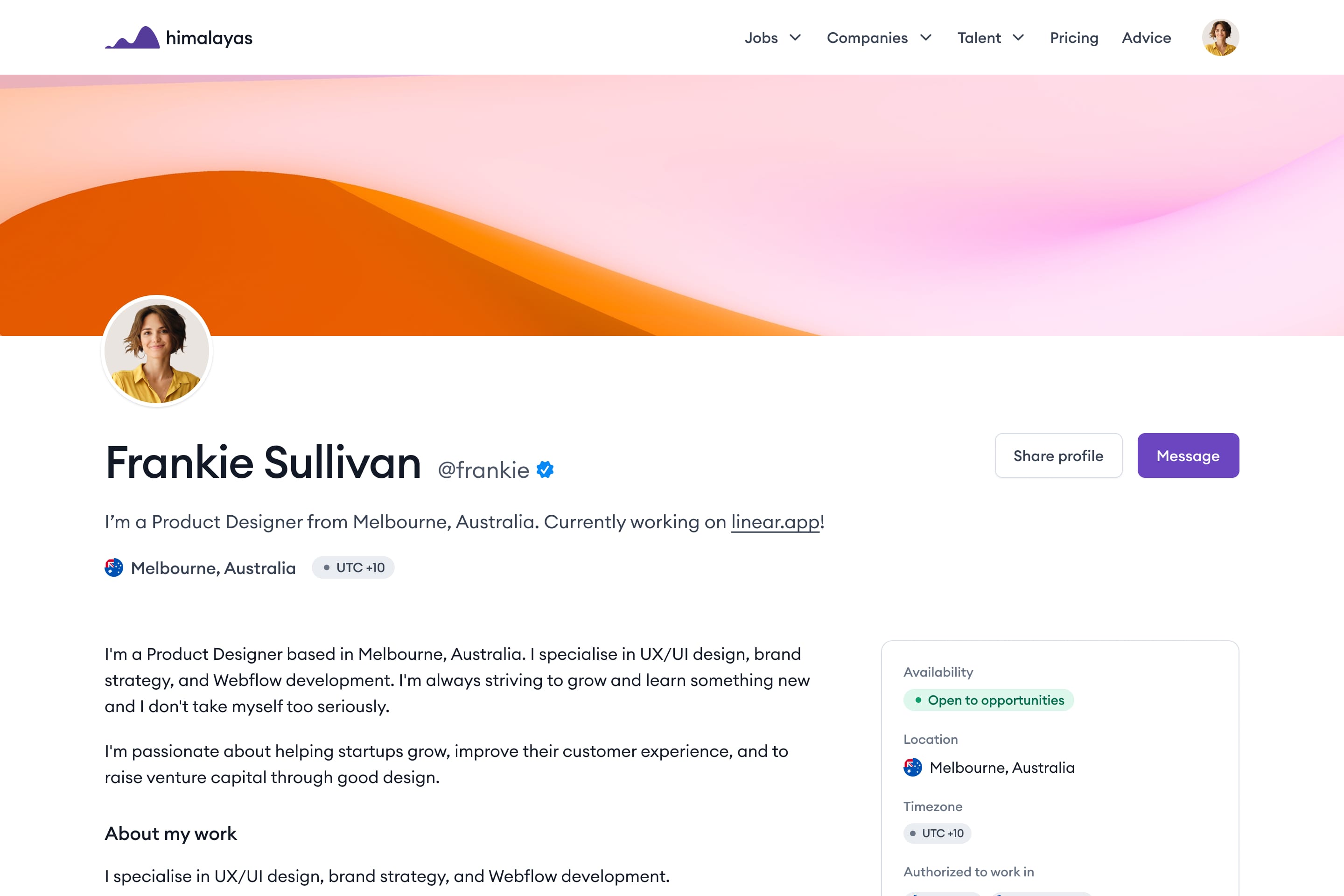