5 Process Engineering Manager Interview Questions and Answers
Process Engineering Managers oversee the design, implementation, and optimization of manufacturing and operational processes within an organization. They lead teams of engineers to ensure efficiency, cost-effectiveness, and compliance with safety and quality standards. At junior levels, responsibilities may focus on assisting with process improvements and team coordination, while senior roles involve strategic planning, cross-departmental collaboration, and leadership of large-scale process initiatives. Need to practice for an interview? Try our AI interview practice for free then unlock unlimited access for just $9/month.
Unlimited interview practice for $9 / month
Improve your confidence with an AI mock interviewer.
No credit card required
1. Associate Process Engineering Manager Interview Questions and Answers
1.1. Describe a time when you implemented a process improvement that significantly enhanced operational efficiency.
Introduction
This question assesses your ability to identify areas for improvement and implement effective solutions, which is crucial for a Process Engineering Manager role.
How to answer
- Use the STAR method to structure your response: Situation, Task, Action, Result.
- Clearly define the process you improved and its initial inefficiencies.
- Explain the steps you took to analyze the process and identify improvements.
- Detail the implementation of the new process, including any challenges faced and how you overcame them.
- Quantify the impact of your improvement on operational efficiency, such as time saved or cost reduced.
What not to say
- Focusing solely on the technical aspects without discussing the broader impact on the team or company.
- Failing to provide measurable results or data to back up your claims.
- Neglecting to mention collaboration with other teams or stakeholders.
- Being vague about the steps taken or challenges faced during implementation.
Example answer
“At a manufacturing plant in Mexico, I led a project to streamline the assembly line process, which was facing delays. By conducting a thorough analysis, I identified unnecessary steps that could be eliminated. After collaborating with the team to implement a leaner process, we reduced assembly time by 25% and improved output quality. This experience taught me the importance of cross-functional collaboration and data-driven decision-making.”
Skills tested
Question type
1.2. How do you approach managing a team during a complex engineering project?
Introduction
This question evaluates your leadership and team management skills, essential for successfully guiding engineering teams through complex projects.
How to answer
- Discuss your leadership style and how it adapts to different team dynamics.
- Explain your approach to setting clear goals and expectations for the team.
- Detail how you foster collaboration and communication among team members.
- Share examples of how you address conflicts or challenges within the team.
- Highlight any tools or methodologies you use to track progress and maintain alignment.
What not to say
- Indicating that you prefer to work alone without leveraging your team's strengths.
- Failing to provide specific examples of past experiences with team management.
- Being overly authoritative without showing a collaborative approach.
- Neglecting to mention the importance of team morale and motivation.
Example answer
“In my previous role at a chemical processing company, I managed a team of engineers during a critical project to upgrade our production line. I conducted regular check-ins to ensure everyone was aligned on goals and encouraged open communication. When conflicts arose, I facilitated discussions to find common ground and solutions. By using project management tools like Asana, we tracked progress effectively, leading to successful project completion on time and within budget. This experience reinforced my belief in the power of teamwork and open dialogue.”
Skills tested
Question type
2. Process Engineering Manager Interview Questions and Answers
2.1. Can you describe a process improvement project you led and its results?
Introduction
This question is crucial for assessing your experience in process optimization, a key responsibility for a Process Engineering Manager. It illustrates your ability to lead initiatives that improve efficiency and effectiveness.
How to answer
- Use the STAR method (Situation, Task, Action, Result) to structure your response.
- Clearly define the process that needed improvement and the metrics involved.
- Detail the specific strategies you implemented to enhance the process.
- Quantify the results, such as time saved, cost reductions, or quality improvements.
- Discuss any challenges faced and how you overcame them.
What not to say
- Vague descriptions of the project without specific metrics.
- Taking sole credit for a team effort.
- Focusing too much on the problems without showcasing solutions.
- Neglecting to mention the impact on stakeholders or the broader organization.
Example answer
“At Renault, I led a project to streamline the production line for our electric vehicle components. We identified bottlenecks causing a 20% delay in output. By implementing a lean methodology and reorganizing workflows, we improved cycle time by 30% and reduced waste by 15%. This not only boosted our production capacity but also saved €200,000 annually.”
Skills tested
Question type
2.2. How do you ensure that your team remains compliant with industry regulations during process changes?
Introduction
This question evaluates your understanding of compliance and regulatory frameworks, which are vital in process engineering, especially in highly regulated industries.
How to answer
- Discuss your knowledge of relevant regulations and standards.
- Explain how you communicate these requirements to your team.
- Detail the processes you implement to monitor compliance during changes.
- Mention any tools or software you use to track compliance.
- Share examples of how you've successfully navigated compliance challenges in the past.
What not to say
- Implying that compliance is secondary to process improvement.
- Not demonstrating knowledge of specific regulations relevant to the industry.
- Failing to mention any proactive measures for compliance.
- Ignoring the importance of team training on compliance issues.
Example answer
“In my role at TotalEnergies, I regularly updated my team on ISO 9001 and environmental regulations. During a recent process change, I established a compliance checklist and scheduled training sessions to ensure everyone understood their responsibilities. I also utilized compliance management software to track adherence, which helped us maintain a 100% compliance rate throughout the transition.”
Skills tested
Question type
3. Senior Process Engineering Manager Interview Questions and Answers
3.1. Describe a time when you implemented a process improvement that significantly enhanced productivity.
Introduction
This question is crucial for assessing your ability to identify inefficiencies and implement effective solutions, which is essential for a Senior Process Engineering Manager.
How to answer
- Use the STAR method to structure your response: Situation, Task, Action, Result.
- Clearly describe the initial process and its limitations.
- Detail the analysis conducted to identify improvement opportunities.
- Explain the specific changes you implemented and the rationale behind them.
- Quantify the impact of the improvements on productivity metrics.
What not to say
- Providing vague examples without specific metrics or results.
- Focusing too much on the technical aspects without explaining the business impact.
- Taking sole credit without acknowledging team contributions.
- Not discussing the challenges faced during implementation.
Example answer
“At a manufacturing facility in Guadalajara, I identified that our assembly line had a 20% downtime due to inefficient scheduling. I led a cross-functional team to analyze the workflow, and we implemented a new scheduling software that optimized machine usage. As a result, we saw a 30% increase in productivity over six months, which saved the company 15% in operational costs. This project taught me the importance of data-driven decision-making and teamwork.”
Skills tested
Question type
3.2. How do you ensure that your engineering team adheres to safety and quality standards during process changes?
Introduction
This question evaluates your leadership and commitment to safety and quality, which are vital aspects of process engineering management.
How to answer
- Discuss your approach to integrating safety and quality checks within the engineering process.
- Mention specific frameworks or standards you follow (e.g., ISO, Six Sigma).
- Explain how you communicate these standards to your team.
- Share examples of training or resources you provide to ensure compliance.
- Describe how you monitor adherence and address any deviations.
What not to say
- Neglecting to mention any specific safety or quality standards.
- Implying that safety and quality are secondary to productivity.
- Avoiding the discussion of how to handle non-compliance.
- Failing to provide examples of how you've implemented these practices.
Example answer
“In my previous role at a food processing plant, I implemented the Six Sigma methodology to enhance our quality assurance processes. I ensured that each team member received training on safety protocols and quality standards. We conducted regular audits and established a feedback loop to address any issues promptly. This approach not only improved compliance rates by 40% but also fostered a culture of safety and quality among the team.”
Skills tested
Question type
4. Director of Process Engineering Interview Questions and Answers
4.1. Can you describe a specific process improvement project you led and its impact on the organization?
Introduction
This question assesses your ability to drive process improvements, a crucial skill for a Director of Process Engineering. It highlights your strategic thinking, leadership, and measurable outcomes.
How to answer
- Use the STAR method to structure your response: Situation, Task, Action, Result.
- Clearly define the process that needed improvement and the reasons behind it.
- Detail your specific role and actions taken to implement the changes.
- Quantify the impact of the improvements using metrics such as time saved, cost reduction, or quality enhancements.
- Discuss any challenges faced during implementation and how you overcame them.
What not to say
- Providing vague descriptions without specific metrics or outcomes.
- Failing to mention the team or stakeholders involved in the project.
- Avoiding discussion of challenges or resistance encountered.
- Simply stating a process was improved without explaining how or why.
Example answer
“At Rolls-Royce, I led a project to revamp the supply chain process that reduced lead times by 25%. The situation involved high delays in sourcing materials. I initiated a cross-functional team to map the existing process, identify bottlenecks, and implemented lean methodologies. As a result, we achieved a 30% cost reduction and improved supplier relationships, which was reflected in a 15% increase in on-time delivery rates.”
Skills tested
Question type
4.2. How do you approach change management when implementing new processes?
Introduction
This question evaluates your understanding of change management principles, which are essential for successfully implementing new processes and ensuring team buy-in.
How to answer
- Outline your change management strategy, including stakeholder engagement and communication.
- Discuss how you assess the impact of the change on various teams and processes.
- Explain your methods for training and supporting staff during the transition.
- Describe how you measure the success of the change and gather feedback for continuous improvement.
- Share examples of past experiences where your change management approach led to successful outcomes.
What not to say
- Suggesting that change can be implemented without communication or stakeholder buy-in.
- Failing to acknowledge potential resistance from team members.
- Overlooking the importance of training and support during transitions.
- Describing a rigid approach without flexibility to adapt based on feedback.
Example answer
“In my role at BAE Systems, I implemented a new quality assurance process that required significant changes in team workflows. I started by conducting stakeholder meetings to understand concerns and gather input. I provided training sessions and created a feedback loop to address issues as they arose. This approach led to 90% team acceptance and a smoother transition, ultimately increasing our quality compliance rate by 20%.”
Skills tested
Question type
5. VP of Process Engineering Interview Questions and Answers
5.1. Can you describe a major process improvement initiative you led and the results it achieved?
Introduction
This question is crucial for assessing your ability to identify inefficiencies and implement effective process improvements, a key responsibility for a VP of Process Engineering.
How to answer
- Use the STAR method to structure your answer: Situation, Task, Action, Result.
- Clearly describe the initial situation and why the improvement was necessary.
- Explain your role in leading the initiative and the specific strategies you employed.
- Quantify the results achieved, such as cost savings, time reductions, or quality improvements.
- Discuss any challenges faced during the implementation and how you overcame them.
What not to say
- Providing vague descriptions without specific metrics or outcomes.
- Taking sole credit for a team effort without acknowledging contributions from others.
- Focusing too much on the problem rather than the solution and results.
- Neglecting to mention how you measured the success of the initiative.
Example answer
“At Renault, I led a cross-departmental initiative to streamline our manufacturing process. We identified bottlenecks in the assembly line and implemented a lean methodology, reducing cycle time by 20% and saving the company €1.5 million annually. The success of this project not only improved productivity but also enhanced team collaboration across departments.”
Skills tested
Question type
5.2. How do you ensure that process engineering initiatives align with overall business goals and objectives?
Introduction
This question evaluates your strategic thinking and ability to align engineering processes with broader organizational goals, which is essential for a VP role.
How to answer
- Discuss your approach to understanding business objectives and how they inform process engineering decisions.
- Explain how you engage with other departments to ensure alignment.
- Describe how you measure the impact of process initiatives on business outcomes.
- Share examples of past experiences where you successfully aligned process initiatives with business goals.
- Highlight your communication strategies for keeping stakeholders informed.
What not to say
- Suggesting that process engineering is separate from business strategy.
- Failing to mention collaboration with other departments.
- Providing generic answers without specific examples.
- Overlooking the importance of measuring outcomes against business objectives.
Example answer
“I prioritize alignment by regularly collaborating with senior leadership to understand strategic goals. For instance, at Airbus, I initiated quarterly reviews of our process initiatives against business metrics. This resulted in the development of a new supply chain process that improved delivery timelines by 15%, directly supporting our goal of enhancing customer satisfaction.”
Skills tested
Question type
Similar Interview Questions and Sample Answers
Simple pricing, powerful features
Upgrade to Himalayas Plus and turbocharge your job search.
Himalayas
Himalayas Plus
Himalayas Max
Find your dream job
Sign up now and join over 100,000 remote workers who receive personalized job alerts, curated job matches, and more for free!
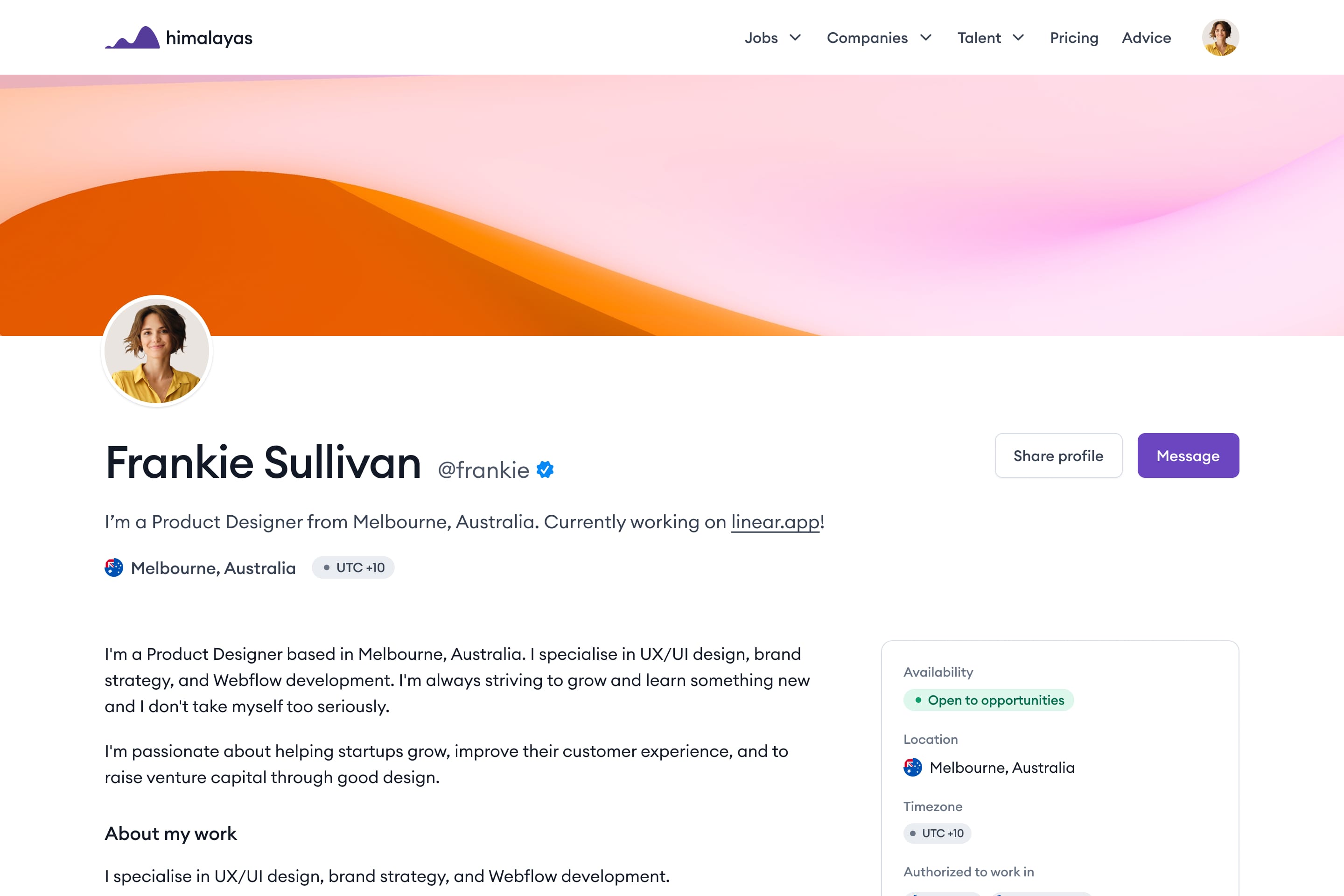