5 Dumpling Machine Operator Interview Questions and Answers
Dumpling Machine Operators are responsible for operating and maintaining machinery used in the production of dumplings. They ensure the equipment runs efficiently, monitor the quality of the output, and troubleshoot any mechanical issues. Junior operators focus on basic machine operations and learning processes, while senior operators take on more complex tasks, including overseeing production lines and mentoring junior staff. Supervisory roles involve managing teams and ensuring production goals are met. Need to practice for an interview? Try our AI interview practice for free then unlock unlimited access for just $9/month.
Unlimited interview practice for $9 / month
Improve your confidence with an AI mock interviewer.
No credit card required
1. Junior Dumpling Machine Operator Interview Questions and Answers
1.1. Can you describe your experience with operating machinery, specifically in a food production setting?
Introduction
This question is essential for understanding your familiarity with operating equipment, as well as your ability to ensure quality and safety in food production.
How to answer
- Start by outlining any relevant experience with machinery in food production or similar environments.
- Emphasize your understanding of machine operation, maintenance, and safety protocols.
- Discuss any training or certifications you have received related to machinery operation.
- Mention specific tasks you performed and how they relate to operating a dumpling machine.
- Conclude with any improvements or efficiencies you contributed to in past roles.
What not to say
- Claiming to have no experience operating machinery at all.
- Focusing solely on unrelated experiences without connecting them to this role.
- Neglecting safety protocols or procedures, as this is critical in food production.
- Being vague about your responsibilities and contributions.
Example answer
“In my previous role at a local bakery, I operated various food production machines, including dough mixers and filling machines. I was responsible for daily maintenance checks to ensure everything was running smoothly. My training in food safety and machine operation allowed me to identify and resolve minor issues before they became significant problems, which helped maintain high production standards and prevent downtime.”
Skills tested
Question type
1.2. Describe a time when you had to troubleshoot a problem with a machine during production.
Introduction
This question assesses your problem-solving skills and your ability to remain calm under pressure in a production environment.
How to answer
- Use the STAR method to structure your response: Situation, Task, Action, Result.
- Clearly describe the specific problem you encountered with the machine.
- Explain the steps you took to diagnose and fix the issue.
- Discuss the outcome, including any impact on production efficiency.
- Highlight any lessons learned or improvements made as a result.
What not to say
- Dismissing the issue as someone else's problem.
- Failing to take responsibility for resolving the situation.
- Providing vague or irrelevant examples that do not relate to machine operation.
- Not discussing the results or impact of your actions.
Example answer
“At my previous job at a small food factory, the dumpling machine jammed during a busy shift. First, I assessed the situation and found that the dough was too thick. I adjusted the settings and removed the excess dough. This quick action allowed us to resume production within 20 minutes, minimizing downtime. I also suggested a review of our dough consistency to avoid future jams, which improved our production flow.”
Skills tested
Question type
2. Dumpling Machine Operator Interview Questions and Answers
2.1. Can you describe your experience operating a dumpling machine and the types of dumplings you've produced?
Introduction
This question is crucial for understanding your hands-on experience with the machinery and your familiarity with different dumpling varieties, which is vital for quality control and production efficiency.
How to answer
- Start by detailing your specific experience with dumpling machines, including brands and models if applicable.
- Mention the types of dumplings you have produced, such as steamed, boiled, or fried, and any variations.
- Explain your role in the production process, including setup, operation, and maintenance of the machine.
- Highlight any relevant safety protocols you followed.
- Discuss how you ensured product quality and consistency during production.
What not to say
- Providing vague answers without detailing specific machines or dumpling types.
- Ignoring the importance of safety and quality control.
- Focusing solely on machine operation without mentioning teamwork or communication with others.
- Failing to mention any troubleshooting or problem-solving experiences.
Example answer
“At a local dumpling factory in São Paulo, I operated a KX-100 dumpling machine, producing various types of dumplings, including pork and vegetable variants. My responsibilities included setting up the machine, monitoring the dough consistency, and ensuring that each dumpling was filled properly. I strictly adhered to safety protocols and performed routine maintenance to keep the machine in optimal condition. This experience taught me the importance of quality checks, and I consistently achieved a 98% quality rate in our production runs.”
Skills tested
Question type
2.2. Have you ever encountered a problem while operating the dumpling machine? How did you resolve it?
Introduction
This question assesses your problem-solving abilities and how you handle issues on the production floor, which is key in a fast-paced manufacturing environment.
How to answer
- Describe the specific problem you encountered, providing enough context.
- Explain the steps you took to diagnose the issue.
- Detail the actions you implemented to resolve the problem.
- Discuss any collaboration with team members or supervisors in finding a solution.
- Share the outcome and any lessons learned from the experience.
What not to say
- Avoiding responsibility or blaming others for the machinery issues.
- Providing overly technical jargon that may not be understood.
- Failing to demonstrate a clear problem-solving process.
- Not mentioning any follow-up actions to prevent future issues.
Example answer
“While operating the dumpling machine, I once noticed that the dough was not feeding properly, causing inconsistencies in the size of the dumplings. I quickly stopped the machine and checked for any blockages. After identifying a minor jam in the feeding mechanism, I cleared it and adjusted the settings to ensure a smoother dough flow. I communicated with my supervisor about the issue and implemented a regular check every hour to prevent recurrence. This proactive approach improved our production line's efficiency significantly.”
Skills tested
Question type
3. Senior Dumpling Machine Operator Interview Questions and Answers
3.1. Can you describe a time when you identified and solved a problem with the dumpling machine during production?
Introduction
This question assesses your troubleshooting skills and ability to maintain production quality, which are critical for a Senior Dumpling Machine Operator.
How to answer
- Use the STAR method to structure your response: Situation, Task, Action, Result.
- Clearly describe the specific issue with the dumpling machine, including its impact on production.
- Detail the steps you took to diagnose and resolve the problem.
- Explain any collaboration with team members or management during the process.
- Quantify the results achieved, such as reduced downtime or improved product quality.
What not to say
- Blaming the machine or other team members without taking ownership.
- Vaguely describing a problem without detailing your specific actions.
- Failing to mention the importance of team communication.
- Ignoring the results or metrics related to your solution.
Example answer
“At my previous job with a major dumpling manufacturer, I noticed that the machine was not sealing properly, causing a significant waste of product. I stopped production and performed a thorough inspection, discovering a misalignment in the sealing mechanism. After realigning and calibrating the machine, we resumed production, reducing waste by 30% and increasing overall efficiency. This reinforced the importance of proactive maintenance and attention to detail.”
Skills tested
Question type
3.2. What safety protocols do you follow while operating the dumpling machine?
Introduction
This question evaluates your knowledge of safety practices essential for operating machinery and ensuring a safe work environment.
How to answer
- List specific safety protocols you adhere to, such as machine lockout/tagout procedures.
- Explain how you ensure both personal safety and the safety of your coworkers.
- Discuss any training or certifications you have received related to safety.
- Mention how you stay updated on safety regulations and best practices.
- Provide an example of how you've promoted safety within your team.
What not to say
- Minimizing the importance of safety protocols.
- Providing vague or generic responses without specifics.
- Failing to mention personal accountability for safety.
- Neglecting to discuss teamwork in maintaining a safe environment.
Example answer
“I strictly adhere to safety protocols, including wearing personal protective equipment and following lockout/tagout procedures before performing any maintenance on the machine. I also conduct daily safety checks to ensure that all guards and safety devices are in place. Recently, I conducted a safety briefing for new operators, emphasizing the importance of reporting any safety hazards immediately. This proactive approach helps prevent accidents and ensures a safe workplace for everyone.”
Skills tested
Question type
4. Lead Dumpling Machine Operator Interview Questions and Answers
4.1. Can you describe a time when you had to troubleshoot a malfunction in the dumpling machine during production?
Introduction
This question is important because it evaluates your technical problem-solving skills and ability to maintain production efficiency under pressure.
How to answer
- Use the STAR method to structure your response (Situation, Task, Action, Result)
- Clearly explain the specific malfunction and its impact on production
- Detail the steps you took to diagnose and resolve the issue
- Highlight any collaboration with team members or maintenance staff
- Quantify the outcome, such as reduced downtime or increased output
What not to say
- Blaming the machine or external factors without taking ownership
- Providing vague examples without clear steps taken to resolve issues
- Focusing only on the negative outcome without highlighting your role in solving the problem
- Neglecting to mention any preventative measures you implemented afterward
Example answer
“During my time at a local dumpling factory, we experienced an unexpected jam in the dumpling machine that halted production. I quickly assessed the situation and identified a misalignment in the feeding mechanism. Collaborating with my team, I shut down the machine and realigned the feeder within 20 minutes, which minimized downtime. This incident not only improved our response time for future issues but also led to a 15% increase in overall production efficiency.”
Skills tested
Question type
4.2. How do you ensure quality control while operating the dumpling machine?
Introduction
This question assesses your attention to detail and commitment to quality standards in food production, which is critical in maintaining product integrity.
How to answer
- Describe specific quality control measures you implement during operation
- Discuss how you monitor the machine and product output
- Explain how you train and guide team members on quality standards
- Share examples of how you’ve addressed quality issues in the past
- Mention any relevant certifications or standards you adhere to
What not to say
- Claiming that quality control is solely the responsibility of supervisors
- Providing generic answers without specific examples from experience
- Ignoring the importance of regular machine maintenance
- Failing to mention the importance of hygiene and safety standards
Example answer
“I ensure quality control by regularly checking the dumpling machine settings and conducting visual inspections of the dumplings every hour. I train my team to identify any inconsistencies in size or sealing and encourage immediate reporting. Once, I noticed a batch of dumplings was not sealing properly, which I traced back to incorrect settings. After adjusting the machine and retraining the team on proper sealing techniques, we maintained our quality standards without any further issues.”
Skills tested
Question type
5. Dumpling Production Supervisor Interview Questions and Answers
5.1. Can you describe a time when you had to improve the efficiency of the dumpling production process?
Introduction
This question is important for understanding your ability to optimize production processes, which is a key responsibility for a supervisor in a food production environment.
How to answer
- Use the STAR method to structure your response: Situation, Task, Action, Result.
- Clearly explain the initial efficiency issues and their impact on production.
- Detail the specific changes or strategies you implemented to enhance efficiency.
- Quantify the improvements in terms of output, cost savings, or time reduction.
- Share any challenges faced during implementation and how you overcame them.
What not to say
- Focusing only on the problem without discussing your actions.
- Providing vague or general statements without specific metrics.
- Neglecting to mention the involvement of your team in the process.
- Failing to address the long-term sustainability of the improvements.
Example answer
“At a previous role in a dumpling factory, we faced a slowdown in our production line due to outdated equipment. I led a project to assess our process, and we introduced a new steam cooking system that reduced cooking time by 20%. This change not only increased our output by 30% but also improved the quality of the dumplings. The team was initially resistant, but I involved them in training sessions to ease the transition, which resulted in a smooth implementation.”
Skills tested
Question type
5.2. How do you ensure quality control in the dumpling production process?
Introduction
Quality control is critical in food production to maintain safety and customer satisfaction. This question assesses your approach to maintaining high standards.
How to answer
- Describe your quality control processes and standards you follow.
- Share specific examples of how you detect and address quality issues.
- Explain how you train and involve your team in quality assurance.
- Discuss the importance of compliance with food safety regulations.
- Mention any metrics you use to track quality performance.
What not to say
- Ignoring the importance of quality control in production.
- Focusing only on end-product inspections rather than in-process checks.
- Failing to mention team training or involvement.
- Providing examples without clear outcomes or improvements.
Example answer
“In my previous role at a dumpling production facility, I established a comprehensive quality control system that included regular checks at each stage of production, from ingredient sourcing to final product inspection. I trained my team on quality standards and implemented a feedback loop where they could report issues. This proactive approach reduced our defect rate by 15% over six months and ensured compliance with HACCP standards.”
Skills tested
Question type
Similar Interview Questions and Sample Answers
Simple pricing, powerful features
Upgrade to Himalayas Plus and turbocharge your job search.
Himalayas
Himalayas Plus
Himalayas Max
Find your dream job
Sign up now and join over 100,000 remote workers who receive personalized job alerts, curated job matches, and more for free!
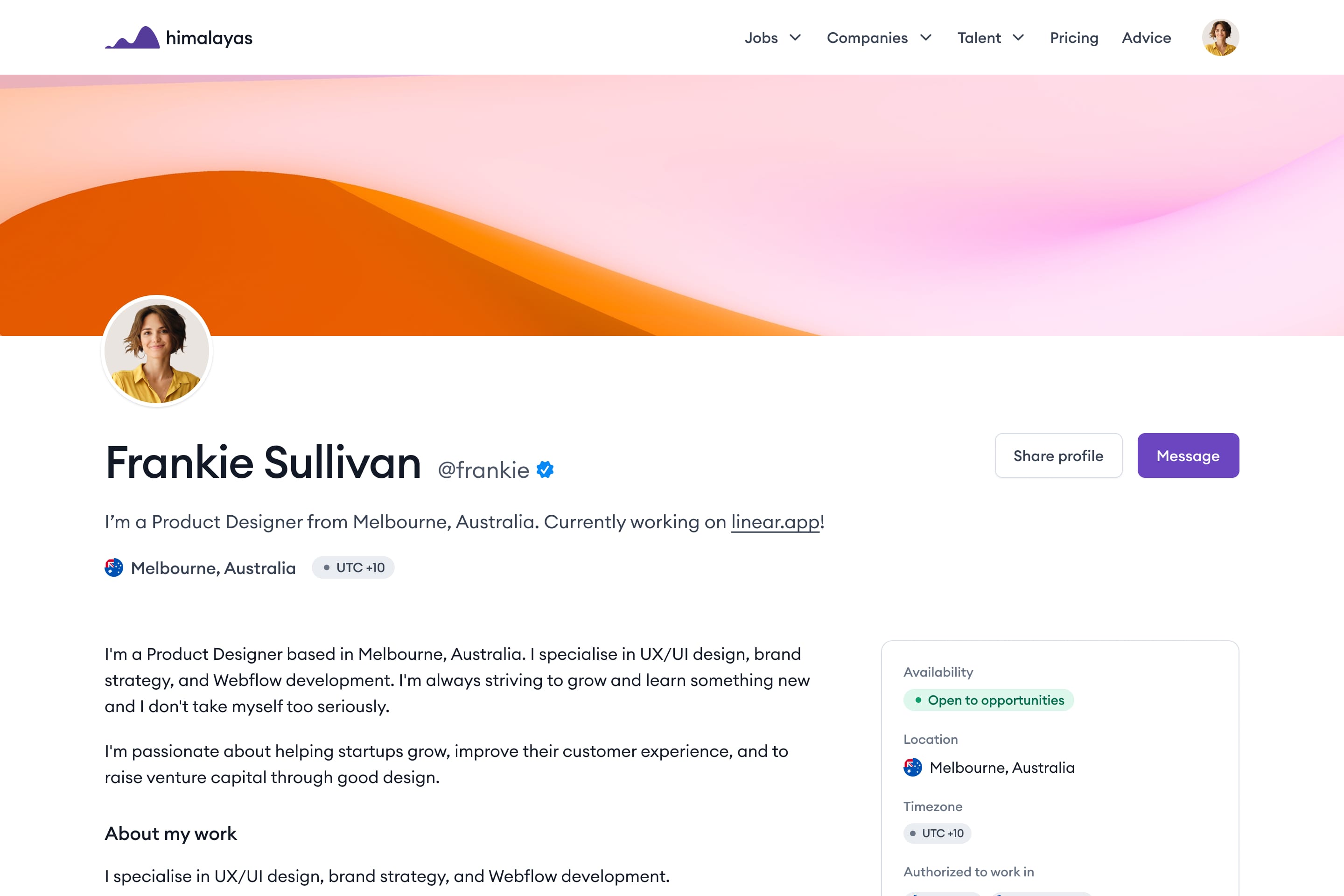