5 Doughnut Machine Operator Interview Questions and Answers
Doughnut Machine Operators are responsible for operating and maintaining machinery used in the production of doughnuts. They ensure the machines run efficiently, troubleshoot issues, and maintain quality standards for the final product. Junior operators focus on basic tasks and learning machine operations, while senior and lead operators oversee production, train team members, and ensure compliance with safety and quality protocols. Need to practice for an interview? Try our AI interview practice for free then unlock unlimited access for just $9/month.
Unlimited interview practice for $9 / month
Improve your confidence with an AI mock interviewer.
No credit card required
1. Junior Doughnut Machine Operator Interview Questions and Answers
1.1. Can you describe a time when you identified a problem with the doughnut machine during production?
Introduction
This question is important for assessing your problem-solving skills and attention to detail, which are crucial for maintaining the efficiency of the production line.
How to answer
- Use the STAR method to structure your response (Situation, Task, Action, Result)
- Clearly describe the context in which the problem occurred
- Explain how you identified the issue and its impact on production
- Detail the steps you took to resolve the problem
- Highlight the outcome and any improvements made to processes
What not to say
- Avoid blaming others for the issue without taking responsibility
- Neglecting to mention the steps taken to address the problem
- Focusing solely on the problem without discussing resolutions
- Not quantifying the results or improvements from your action
Example answer
“During my internship at a local bakery, I noticed the doughnut machine was not heating properly, which resulted in undercooked doughnuts. I immediately reported it to my supervisor and suggested checking the thermostat. After recalibrating it, we were able to resume production, and the quality of the doughnuts improved significantly. This experience taught me the importance of vigilance and proactive problem-solving in a manufacturing setting.”
Skills tested
Question type
1.2. How do you ensure that doughnut production meets quality standards?
Introduction
This question evaluates your understanding of quality control processes and your commitment to maintaining high production standards.
How to answer
- Discuss specific quality control measures you are familiar with
- Explain how you monitor the production process for consistency
- Share your approach to handling quality issues when they arise
- Mention any training or protocols you follow for quality assurance
- Highlight the importance of feedback in improving quality
What not to say
- Suggesting that quality is not important in doughnut production
- Failing to mention any specific quality control measures
- Ignoring the role of teamwork in maintaining quality standards
- Providing vague answers without concrete examples
Example answer
“I believe quality control starts from the very first step of making the dough. At my previous role in a bakery, I ensured that the ingredients were fresh and measured accurately. During production, I regularly checked the consistency of the dough and the temperature of the oil. If I noticed any discrepancies, I would alert my supervisor immediately. This proactive approach helped us maintain a high quality of doughnuts and minimize waste.”
Skills tested
Question type
2. Doughnut Machine Operator Interview Questions and Answers
2.1. Can you describe a time when you had to troubleshoot a malfunction in the doughnut machine?
Introduction
This question evaluates your technical problem-solving skills and ability to respond to equipment issues, which are crucial for a Doughnut Machine Operator.
How to answer
- Begin by outlining the specific issue you faced with the machine
- Describe the troubleshooting steps you took to diagnose the problem
- Explain how you resolved the issue and any adjustments made
- Highlight the outcome and any improvements in efficiency or product quality
- Mention any additional support or resources you utilized during the process
What not to say
- Giving vague descriptions of the problem without specific details
- Failing to mention any proactive measures taken to prevent future issues
- Not acknowledging the importance of safety protocols during troubleshooting
- Blaming others or external factors without taking responsibility
Example answer
“At my previous job at a local bakery, the doughnut machine suddenly stopped operating during peak hours. I quickly assessed the situation and found that a sensor had malfunctioned. I followed the troubleshooting manual, replaced the sensor, and recalibrated the machine. As a result, we were able to resume production in under an hour, minimizing downtime significantly. This experience taught me the importance of staying calm and methodical under pressure.”
Skills tested
Question type
2.2. How do you ensure the quality and consistency of the doughnuts produced?
Introduction
This question assesses your understanding of quality control processes and your commitment to maintaining high production standards, which are vital in food manufacturing.
How to answer
- Describe your approach to monitoring the doughnut-making process
- Explain specific quality control measures you implement at various stages
- Share examples of how you have addressed quality issues in the past
- Discuss any relevant training or certifications related to food safety
- Highlight your collaboration with team members to uphold quality standards
What not to say
- Neglecting to mention any quality checks or standards
- Suggesting that quality is not a priority in the production process
- Failing to provide specific examples of quality improvements
- Overlooking the importance of feedback from customers or team members
Example answer
“I maintain the quality of our doughnuts by implementing a strict quality control process. This includes regularly checking the dough consistency, temperature of the frying oil, and the final product appearance. For example, when I noticed inconsistencies in size, I adjusted the portioning machine, which improved our uniformity and reduced waste. Collaborating with my team to share feedback helps us continuously improve our processes.”
Skills tested
Question type
3. Senior Doughnut Machine Operator Interview Questions and Answers
3.1. Can you describe a time when you had to troubleshoot a malfunctioning doughnut machine during production?
Introduction
This question is crucial for understanding your technical skills and problem-solving abilities in a fast-paced production environment. As a Senior Doughnut Machine Operator, your ability to quickly identify and resolve issues is vital to maintaining production efficiency.
How to answer
- Start by outlining the situation and the specific malfunction that occurred.
- Explain the steps you took to diagnose the problem, including any tools or resources you used.
- Detail the solution you implemented and how you ensured it was effective.
- Discuss the impact your actions had on production, including minimizing downtime.
- Reflect on the lessons learned and how it improved your troubleshooting skills.
What not to say
- Blaming others for the malfunction without taking responsibility.
- Providing vague descriptions of the problem without specifics.
- Failing to mention the importance of teamwork in resolving the issue.
- Neglecting to discuss the results of your troubleshooting efforts.
Example answer
“At my previous job at a large bakery in Tokyo, our doughnut fryer suddenly stopped working during the morning rush. I quickly assessed the situation, identified a faulty thermostat, and replaced it with a spare part from our inventory. This allowed us to resume production within 30 minutes, saving the bakery from significant losses in revenue. This experience taught me the importance of having a well-stocked inventory and always being prepared for equipment issues.”
Skills tested
Question type
3.2. How do you ensure quality control in the doughnut production process?
Introduction
Quality control is essential in food production to ensure product consistency and safety. This question examines your understanding of quality standards and your methods for maintaining them.
How to answer
- Explain the specific quality control measures you implement during production.
- Discuss how you train and supervise junior operators to adhere to quality standards.
- Provide examples of how you monitor doughnut quality throughout the process.
- Share how you respond to quality issues and implement corrective actions.
- Mention any relevant certifications or training in food safety or quality control.
What not to say
- Ignoring the importance of quality in the production process.
- Failing to mention any proactive measures you take.
- Concentrating only on the final product without discussing in-process quality checks.
- Giving generic answers that do not showcase specific practices.
Example answer
“In my role at a confectionery plant, I implement a quality control checklist that includes measuring doughnut size, checking frying temperatures, and conducting taste tests. I also train new operators on these standards to ensure consistency. If a batch does not meet quality standards, I immediately collaborate with the team to analyze the process and determine the cause, often leading to adjustments in frying time or ingredient ratios. This commitment to quality has helped us maintain a 98% customer satisfaction rate.”
Skills tested
Question type
4. Lead Doughnut Machine Operator Interview Questions and Answers
4.1. Can you describe a time when you had to troubleshoot a malfunctioning doughnut machine during production?
Introduction
This question assesses your technical problem-solving skills and ability to work under pressure, which are critical for a lead operator responsible for maintaining production efficiency.
How to answer
- Begin with the context of the production process and the specific malfunction encountered
- Explain the troubleshooting steps you took to identify the issue
- Detail how you communicated with your team during the process
- Describe any adjustments made to minimize downtime
- Conclude with the outcome and what you learned from the experience
What not to say
- Avoid sounding overly reliant on maintenance personnel without taking initiative
- Do not focus solely on technical jargon without explaining the process
- Refrain from blaming other team members or the equipment without showing accountability
- Avoid vague responses that do not provide specific details or outcomes
Example answer
“In my previous role at Tim Hortons, during a morning rush, our doughnut fryer suddenly stopped heating. I quickly assessed the machine, determined it was a faulty temperature sensor, and communicated with my team to switch to a backup fryer. I then contacted maintenance while we continued production. After resolving the issue, we were back on track within 30 minutes, which minimized customer impact. This taught me the importance of quick thinking and communication under pressure.”
Skills tested
Question type
4.2. What safety protocols do you believe are critical in operating a doughnut machine, and how do you ensure compliance?
Introduction
This question evaluates your understanding of safety standards in food production and your leadership in enforcing these protocols among team members.
How to answer
- List key safety protocols relevant to doughnut machine operation
- Explain how you train and reinforce these protocols with your team
- Discuss any past experiences where safety protocols prevented incidents
- Describe how you monitor compliance and handle violations
- Highlight the importance of safety in maintaining a productive work environment
What not to say
- Neglecting to mention specific safety protocols or standards
- Downplaying the importance of safety in production
- Avoiding responsibility for team training on safety measures
- Providing vague answers without examples of compliance monitoring
Example answer
“I believe critical safety protocols include ensuring proper personal protective equipment (PPE) is worn, conducting regular inspections of the machinery, and maintaining clear emergency procedures. At my previous job at a local bakery, I implemented weekly safety training sessions, which not only improved compliance but also fostered a culture of safety. I regularly monitored adherence to these protocols, which resulted in zero accidents during my tenure.”
Skills tested
Question type
5. Doughnut Production Supervisor Interview Questions and Answers
5.1. Can you describe a time when you had to manage a production issue during a high-demand period?
Introduction
This question assesses your problem-solving skills and ability to handle pressure, which are critical for a production supervisor in a fast-paced environment like doughnut production.
How to answer
- Use the STAR method (Situation, Task, Action, Result) to structure your response
- Clearly outline the production issue you faced and its implications on output
- Describe the steps you took to address the issue promptly
- Detail how you communicated with your team and other stakeholders
- Share the outcome and any lessons learned from the experience
What not to say
- Blaming others without taking responsibility
- Focusing too much on the problem rather than the solution
- Not mentioning how you supported your team during the issue
- Providing vague details without a clear resolution
Example answer
“During a peak holiday season at Krispy Kreme, we faced a machinery breakdown that threatened our production targets. I quickly assessed the situation, coordinated with maintenance, and implemented a temporary workflow to shift production to another line. I kept the team informed throughout the process, which maintained morale. As a result, we only experienced a 10% dip in output instead of a potential 30%, and we fulfilled all customer orders on time.”
Skills tested
Question type
5.2. How do you ensure quality control in doughnut production?
Introduction
This question evaluates your understanding of quality assurance processes, which are vital in food production to maintain standards and customer satisfaction.
How to answer
- Explain your approach to establishing quality control measures
- Discuss the importance of regular inspections and audits
- Detail how you train staff on quality standards and procedures
- Include any specific metrics you track to monitor quality
- Describe how you handle deviations from quality standards
What not to say
- Suggesting that quality checks are not important or optional
- Overlooking the importance of staff training and engagement
- Failing to mention any specific quality metrics
- Not addressing how to handle quality issues when they arise
Example answer
“In my previous role at Dunkin', I implemented a rigorous quality control system that involved regular inspections at every stage of production. We trained staff on our quality standards and conducted weekly audits. I tracked metrics such as doughnut weight and glaze consistency, which allowed us to identify and address issues quickly. If we found a deviation, I ensured we had corrective actions in place, which helped us maintain a 98% customer satisfaction rate.”
Skills tested
Question type
Similar Interview Questions and Sample Answers
Simple pricing, powerful features
Upgrade to Himalayas Plus and turbocharge your job search.
Himalayas
Himalayas Plus
Himalayas Max
Find your dream job
Sign up now and join over 100,000 remote workers who receive personalized job alerts, curated job matches, and more for free!
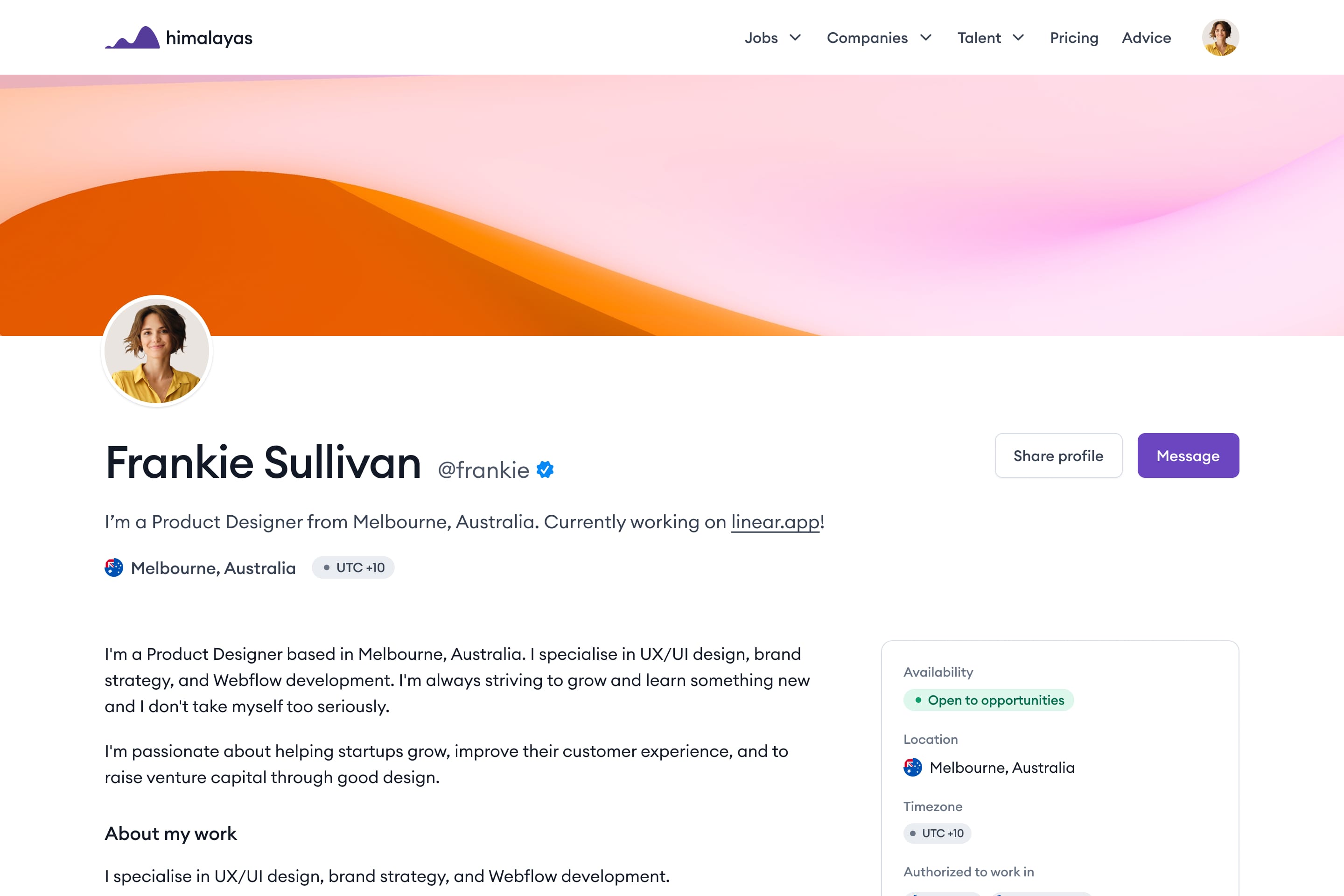