4 Air Bag Builder Interview Questions and Answers
Air Bag Builders are responsible for assembling and manufacturing airbag systems used in vehicles to ensure passenger safety. They work with precision machinery, follow strict safety protocols, and adhere to quality standards. Junior roles focus on basic assembly tasks, while senior and lead positions involve overseeing production processes, ensuring quality control, and training team members. Need to practice for an interview? Try our AI interview practice for free then unlock unlimited access for just $9/month.
Unlimited interview practice for $9 / month
Improve your confidence with an AI mock interviewer.
No credit card required
1. Air Bag Builder Interview Questions and Answers
1.1. Can you describe your experience with the assembly of airbag systems and the safety protocols you follow?
Introduction
This question is crucial for assessing your technical expertise in airbag assembly and your commitment to safety, which are paramount in this role.
How to answer
- Start by detailing your specific experience with airbag assembly, including types of airbags you've worked with.
- Highlight the safety protocols you adhere to during assembly to ensure quality and prevent accidents.
- Mention any relevant certifications or training you've received related to airbag systems.
- Emphasize your understanding of the importance of precision and attention to detail in this line of work.
- Discuss how you handle quality checks and testing procedures post-assembly.
What not to say
- Vaguely discussing assembly without mentioning specific protocols or systems.
- Underestimating the importance of safety in the assembly process.
- Failing to mention any quality control measures taken during or after assembly.
- Claiming to have experience without providing concrete examples or details.
Example answer
“In my previous role at Bosch, I assembled various types of airbags, including driver and passenger airbags. I strictly followed safety protocols, such as wearing protective gear and conducting thorough inspections before and after assembly. I was trained in the ISO 9001 standards, which reinforced my commitment to quality. After assembly, I also performed functional tests on the airbags to ensure they met safety specifications, which ensured that our products were reliable.”
Skills tested
Question type
1.2. Describe a time when you identified a problem during the assembly process. How did you handle it?
Introduction
This question evaluates your problem-solving skills and ability to maintain quality control in a manufacturing environment.
How to answer
- Use the STAR method to structure your answer: Situation, Task, Action, Result.
- Clearly describe the problem you encountered during the assembly process.
- Detail the steps you took to resolve the issue, including teamwork or communication with supervisors.
- Highlight the outcome and any improvements that resulted from your actions.
- Discuss any lessons learned that you applied to future assembly tasks.
What not to say
- Failing to take responsibility for the problem or blaming others.
- Describing a problem without detailing how you resolved it.
- Neglecting to mention the outcome or the impact of your resolution.
- Being vague about the steps taken to address the issue.
Example answer
“During my time at ZF Friedrichshafen, I noticed that some airbag inflators were not fitting correctly during assembly. I immediately reported the issue to my supervisor and suggested we halt production to investigate. We discovered that a batch of inflators was faulty due to a manufacturing error. I helped implement a quality check for incoming parts, which reduced similar issues by 30%. This experience taught me the importance of vigilance and proactive problem-solving.”
Skills tested
Question type
2. Senior Air Bag Builder Interview Questions and Answers
2.1. Can you describe a time when you identified a safety issue during the airbag assembly process and how you addressed it?
Introduction
This question is critical for assessing your attention to detail and commitment to safety, which are paramount in the automotive industry, particularly in airbag manufacturing.
How to answer
- Use the STAR method (Situation, Task, Action, Result) to structure your response.
- Clearly describe the safety issue you identified and the potential risks involved.
- Explain the steps you took to investigate and address the issue.
- Highlight any collaboration with team members or supervisors to implement the solution.
- Share the positive outcomes, including any improvements in safety protocols or production efficiency.
What not to say
- Downplaying the significance of safety issues.
- Failing to provide a specific example of a safety concern.
- Not mentioning collaboration with others or seeking input.
- Not discussing the lessons learned from the experience.
Example answer
“In my previous role at Toyota, I noticed that a specific batch of airbag inflators showed inconsistent pressure levels during testing. Realizing the potential danger, I immediately halted the assembly line and reported it to my supervisor. We conducted a thorough review and found a calibration error in our testing equipment. I collaborated with the engineering team to recalibrate the equipment and retrain staff on inspection protocols, leading to a 30% decrease in defects and enhanced overall safety in production.”
Skills tested
Question type
2.2. How do you ensure quality control in your work when building airbags?
Introduction
This question assesses your understanding of quality assurance processes and your ability to maintain high standards in production, which is crucial in airbag manufacturing.
How to answer
- Explain your approach to following standard operating procedures (SOPs).
- Discuss the quality control measures you implement during the assembly process.
- Mention any specific tools or technologies you use for quality inspection.
- Share how you train or mentor others to uphold quality standards.
- Provide examples of how your quality control efforts have positively impacted production outcomes.
What not to say
- Claiming to rely solely on others for quality checks.
- Failing to mention any specific quality measures or tools.
- Suggesting that quality control is not a priority in your work.
- Not providing evidence of the results of your quality efforts.
Example answer
“At Honda, I strictly adhere to our SOPs, conducting visual inspections at each stage of the airbag assembly process. I also use a digital gauge to measure inflator dimensions and ensure they meet specifications. I regularly conduct training sessions with new team members to instill a culture of quality. My focus on quality control resulted in a 15% reduction in rework and enhanced our reputation for reliability in airbag systems.”
Skills tested
Question type
3. Lead Air Bag Builder Interview Questions and Answers
3.1. Can you describe a time when you identified a safety hazard in the airbag production line and how you addressed it?
Introduction
This question assesses your attention to detail and commitment to safety standards, which are crucial in the manufacturing of airbags where safety is paramount.
How to answer
- Use the STAR method (Situation, Task, Action, Result) to structure your response.
- Describe the specific safety hazard you identified and its potential impact.
- Explain the steps you took to address the hazard, including any collaboration with team members.
- Highlight any changes implemented in the production process as a result of your actions.
- Share the outcomes, focusing on improvements in safety metrics or employee awareness.
What not to say
- Downplaying the importance of safety in manufacturing processes.
- Not providing a specific example or being vague about the situation.
- Failing to mention teamwork or collaboration in addressing the hazard.
- Suggesting that safety hazards are someone else's responsibility.
Example answer
“In my role at Takata, I noticed that some raw materials were not being stored correctly, leading to potential contamination risks. I immediately reported this to my supervisor and conducted a risk assessment with my team. We reorganized the storage area and implemented a checklist for material handling. As a result, we improved our safety audit scores and reduced incidents related to material contamination by 30%.”
Skills tested
Question type
3.2. How do you ensure quality control in the airbag assembly process?
Introduction
This question evaluates your understanding of quality assurance practices and your ability to maintain high standards in production.
How to answer
- Outline your approach to quality control in airbag assembly.
- Discuss specific techniques or tools you use to monitor and improve quality.
- Mention any quality standards or frameworks you are familiar with (e.g., ISO, Six Sigma).
- Share examples of how you or your team have successfully improved quality metrics.
- Emphasize the importance of continuous improvement and training for team members.
What not to say
- Ignoring the importance of quality control altogether.
- Providing vague answers without specific examples or metrics.
- Suggesting that quality control is solely the responsibility of quality inspectors.
- Failing to mention employee training or engagement in quality processes.
Example answer
“At Autoliv, I implemented a quality assurance checklist for each assembly line. We used statistical process control (SPC) to monitor key metrics and identify variations in real-time. By training my team on these practices, we decreased defects by 20% within six months. I believe that fostering a culture of quality is essential, and I regularly hold workshops to discuss quality improvements.”
Skills tested
Question type
4. Air Bag Assembly Supervisor Interview Questions and Answers
4.1. Can you describe a time when you had to resolve a conflict among team members on the assembly line?
Introduction
This question is vital as it assesses your conflict resolution and leadership skills, which are critical for maintaining a productive assembly environment.
How to answer
- Use the STAR method to structure your response: Situation, Task, Action, Result.
- Clearly describe the conflict and its impact on productivity or morale.
- Explain the steps you took to address the conflict, including communication strategies.
- Outline the resolution and its positive impact on the team and assembly line performance.
- Share any lessons learned to improve future conflict management.
What not to say
- Avoid blaming team members without acknowledging your role.
- Don't provide vague or unclear examples without specific outcomes.
- Steer clear of suggesting that conflict is not a concern in a team setting.
- Avoid mentioning unresolved conflicts or negative consequences.
Example answer
“In my previous role at Toyota Australia, there was a disagreement between two team members over the assembly process, leading to delays. I facilitated a meeting where both could express their views. By encouraging open communication, we agreed on a combined approach that utilized the strengths of both methods. This not only resolved the conflict but also improved our efficiency by 15%. I learned the importance of addressing conflicts promptly and fostering a collaborative environment.”
Skills tested
Question type
4.2. What steps would you take to ensure quality control in the airbag assembly process?
Introduction
This question evaluates your understanding of quality control processes and your ability to implement effective measures to ensure product safety.
How to answer
- Outline a quality control framework relevant to the assembly process.
- Discuss specific metrics or checks you would implement at various stages of assembly.
- Explain how you would train your team to adhere to quality standards.
- Describe the importance of documentation and feedback loops in quality control.
- Mention how you would address any quality issues that arise.
What not to say
- Avoid vague statements about quality without specific examples.
- Don't dismiss the importance of team training and engagement.
- Steer clear of suggesting that quality control is solely the responsibility of management.
- Avoid focusing only on the final product without mentioning the assembly process.
Example answer
“To ensure quality control, I would implement a multi-tiered approach that includes pre-assembly inspections, in-process checks, and final product audits. Each assembler would receive training on quality standards and how to recognize defects. For instance, during my time at Audi, I introduced a checklist for each assembly station which decreased defects by 30%. Documentation of any issues and the implementation of corrective actions would be key to continuous improvement.”
Skills tested
Question type
Similar Interview Questions and Sample Answers
Simple pricing, powerful features
Upgrade to Himalayas Plus and turbocharge your job search.
Himalayas
Himalayas Plus
Himalayas Max
Find your dream job
Sign up now and join over 100,000 remote workers who receive personalized job alerts, curated job matches, and more for free!
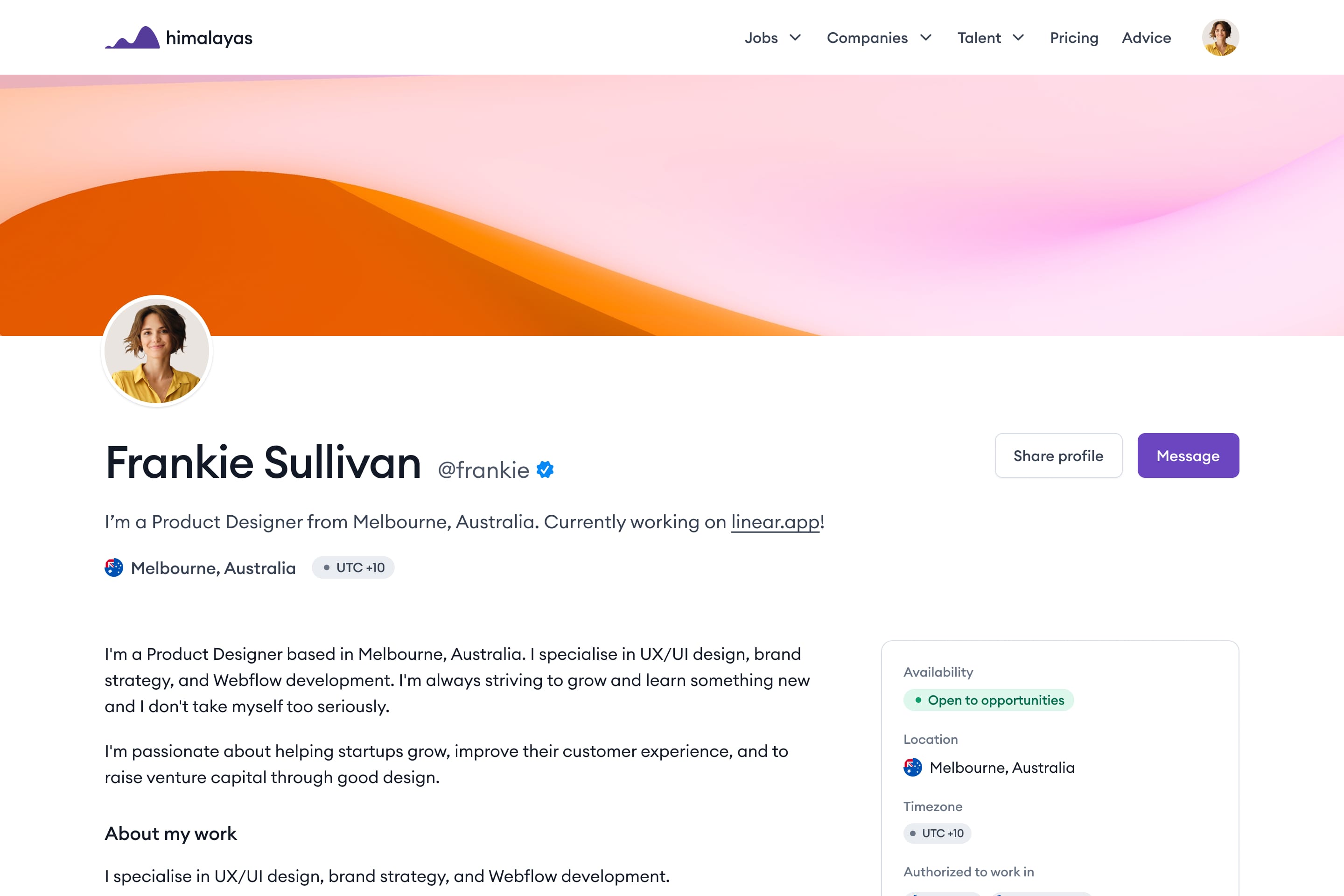