6 Auto Battery Builder Interview Questions and Answers
Auto Battery Builders are responsible for assembling, testing, and ensuring the quality of automotive batteries. They work with specialized tools and machinery to construct batteries that meet industry standards. Junior roles focus on basic assembly tasks and learning processes, while senior and lead roles involve overseeing production, ensuring quality control, and mentoring team members. Need to practice for an interview? Try our AI interview practice for free then unlock unlimited access for just $9/month.
Unlimited interview practice for $9 / month
Improve your confidence with an AI mock interviewer.
No credit card required
1. Auto Battery Assembler Interview Questions and Answers
1.1. Can you describe a time when you identified a quality issue in the assembly process and how you addressed it?
Introduction
This question evaluates your attention to detail and problem-solving skills, which are critical in ensuring high-quality assembly of auto batteries.
How to answer
- Use the STAR method (Situation, Task, Action, Result) to structure your response.
- Clearly articulate the quality issue you encountered.
- Explain your thought process in identifying the root cause.
- Detail the steps you took to resolve the issue and any collaboration with team members.
- Quantify the results of your actions, such as improved defect rates or enhanced safety.
What not to say
- Blaming others for the quality issue without taking responsibility.
- Providing vague descriptions without specific details.
- Not mentioning any follow-up actions to prevent recurrence.
- Ignoring the impact on production timelines or team dynamics.
Example answer
“In my previous position at Bosch, I noticed an increase in battery failures during quality checks. I investigated and found that a specific component was being incorrectly assembled. I collaborated with my team to implement a more rigorous training session on proper assembly techniques, which reduced defects by 30% in the following month. This experience taught me the importance of proactive quality management.”
Skills tested
Question type
1.2. What safety protocols do you believe are essential when assembling auto batteries?
Introduction
This question assesses your knowledge of safety practices, which are crucial for protecting yourself and your coworkers in manufacturing environments.
How to answer
- List specific safety protocols related to battery assembly, such as protective equipment and handling procedures.
- Explain why each protocol is important for safety.
- Share any relevant training or experiences that have informed your understanding of these protocols.
- Discuss how you ensure compliance with safety standards in your work.
- Highlight your commitment to fostering a safe work environment.
What not to say
- Overlooking the importance of safety training.
- Providing generic safety answers without specific relevance to battery assembly.
- Downplaying the risks associated with battery components.
- Failing to demonstrate a proactive approach to safety.
Example answer
“I believe that wearing appropriate personal protective equipment, such as gloves and goggles, is essential when working with auto batteries. Additionally, following proper procedures for handling and disposing of hazardous materials is crucial. In my previous role at Varta, I consistently conducted safety audits and trained new team members on these protocols, which contributed to a safe working environment and zero accidents during my tenure.”
Skills tested
Question type
2. Junior Auto Battery Builder Interview Questions and Answers
2.1. Can you describe your experience working with tools and equipment in a manufacturing environment?
Introduction
This question is crucial as it evaluates your hands-on experience and comfort level with the specific tools and machinery used in battery assembly, which is vital for ensuring quality and safety.
How to answer
- Start by outlining the tools and equipment you've used in previous roles or training.
- Highlight specific tasks you performed with these tools, emphasizing your ability to follow safety protocols.
- Discuss any training or certifications you have related to equipment operation.
- Mention how you ensured quality in your work and any improvements you made in efficiency or safety.
- If applicable, share examples of troubleshooting or resolving issues with the equipment.
What not to say
- Claiming to have experience with tools you are unfamiliar with.
- Ignoring safety practices and protocols.
- Being vague about your hands-on experience and specific tasks.
- Not mentioning any teamwork or collaboration when using equipment.
Example answer
“In my previous internship at a local manufacturing plant, I regularly used hand tools like torque wrenches and power drills for assembling battery components. I completed a safety training course that taught me how to operate equipment safely and efficiently. I also implemented a checklist system to ensure all components were assembled correctly, reducing errors by 20%.”
Skills tested
Question type
2.2. Describe a time when you had to work as part of a team to achieve a goal. What was your role?
Introduction
This question assesses your teamwork and collaboration skills, which are essential in a manufacturing environment where tasks are often interdependent.
How to answer
- Use the STAR method to structure your response (Situation, Task, Action, Result).
- Clearly outline your specific role within the team.
- Describe the goal the team was working towards and the importance of collaboration.
- Highlight any challenges faced and how you contributed to overcoming them.
- Conclude with the outcome and what you learned from the experience.
What not to say
- Taking sole credit for the team's success without acknowledging others.
- Describing a negative team experience without sharing what you learned.
- Being unclear about your specific contributions.
- Failing to express how you can work with diverse team members.
Example answer
“While working on a group project in my manufacturing class, our team needed to assemble a model of an electric vehicle battery. I was responsible for coordinating the assembly process. We faced a challenge when one component arrived damaged, but I helped organize a brainstorming session to find a solution. We managed to source a replacement in time, and our project received top marks. This experience taught me the value of clear communication and teamwork.”
Skills tested
Question type
3. Auto Battery Builder Interview Questions and Answers
3.1. Can you describe your experience working with battery assembly and the specific techniques you used?
Introduction
This question is important as it assesses your technical skills and hands-on experience in battery assembly, which are crucial for an Auto Battery Builder role.
How to answer
- Start by discussing your previous roles related to battery assembly or similar manufacturing processes.
- Detail specific techniques you have used, such as welding, soldering, or automated assembly processes.
- Explain any safety protocols you followed to ensure a safe working environment.
- Mention any relevant machinery or tools you are proficient with.
- Share any metrics or results that demonstrate your efficiency or quality in assembly.
What not to say
- Providing vague descriptions without specific techniques or tools.
- Focusing only on theoretical knowledge without practical experience.
- Neglecting to mention safety protocols or procedures.
- Failing to highlight your contributions to team goals or quality outcomes.
Example answer
“In my previous role at Tesla, I was responsible for assembling battery packs using both manual and automated processes. I utilized precision soldering techniques to connect cells and adhered strictly to safety protocols, which helped reduce workplace incidents by 20%. Additionally, I implemented a quality check procedure that improved our defect rate by 15%.”
Skills tested
Question type
3.2. Describe a time when you faced a challenge during the battery assembly process. How did you resolve it?
Introduction
This question evaluates your problem-solving abilities and how you deal with challenges in a manufacturing environment.
How to answer
- Use the STAR method (Situation, Task, Action, Result) to structure your response.
- Clearly outline the challenge you faced during assembly.
- Discuss the steps you took to identify and resolve the issue.
- Detail any collaboration with team members or supervisors to find a solution.
- Share the positive outcome and what you learned from the experience.
What not to say
- Blaming others for the challenge without taking responsibility.
- Describing a situation without clearly stating the resolution.
- Failing to emphasize teamwork or communication as part of the solution.
- Neglecting to mention any personal growth or learning from the challenge.
Example answer
“During my time at Ford, we encountered a significant delay in battery assembly due to a faulty component from a supplier. I took the initiative to collaborate with our supply chain team to source a temporary alternative while we addressed the root cause. This quick action allowed us to maintain production schedules and ultimately led to a long-term partnership with a more reliable supplier. This experience taught me the importance of proactive problem-solving and effective communication.”
Skills tested
Question type
4. Senior Auto Battery Builder Interview Questions and Answers
4.1. Can you describe a time when you had to troubleshoot a battery assembly issue on the production line?
Introduction
This question evaluates your technical problem-solving skills and your ability to handle production challenges, which are crucial in the battery manufacturing industry.
How to answer
- Use the STAR method to structure your response: Situation, Task, Action, Result.
- Clearly describe the specific issue you encountered and the impact it had on production.
- Detail the steps you took to diagnose the problem and the tools or techniques you used.
- Explain how you collaborated with team members or other departments to resolve the issue.
- Quantify the outcome, such as reduced downtime or improved product quality.
What not to say
- Failing to mention specific actions taken to resolve the issue.
- Blaming others without taking responsibility for your part.
- Providing vague or unclear details about the problem.
- Not emphasizing the importance of teamwork in solving the issue.
Example answer
“In my previous role at Tesla, we faced a recurring issue with battery cells not seating properly in the assembly process, which caused production delays. I led an investigation using root cause analysis, discovering a misalignment in our assembly jig. I collaborated with the engineering team to redesign the jig, resulting in a 30% reduction in assembly errors and a 15% increase in overall production efficiency.”
Skills tested
Question type
4.2. What safety protocols do you follow when working with battery components?
Introduction
This question assesses your knowledge of safety practices, which are critical in the battery assembly process due to the hazardous materials involved.
How to answer
- Discuss specific safety protocols you adhere to, such as PPE requirements and handling procedures.
- Explain how you stay updated with safety regulations and best practices.
- Share examples of how you’ve contributed to a safe working environment, such as training others or reporting hazards.
- Mention any safety certifications or training you have completed.
- Highlight the importance of safety in preventing accidents and ensuring product integrity.
What not to say
- Underestimating the importance of safety protocols.
- Providing generic answers that lack specificity.
- Failing to mention personal responsibility for safety.
- Ignoring the importance of continuous safety education.
Example answer
“At my previous job at LG Chem, I strictly adhered to all OSHA regulations and company safety protocols. I always wore appropriate PPE, such as gloves and goggles, when handling battery components. I also participated in quarterly safety training sessions to keep my knowledge current. Additionally, I conducted a safety workshop for my team, which resulted in a 20% reduction in safety incidents over six months.”
Skills tested
Question type
5. Lead Auto Battery Builder Interview Questions and Answers
5.1. Can you describe a specific project where you improved the production process of auto batteries?
Introduction
This question evaluates your ability to identify inefficiencies and implement improvements in a production environment, which is crucial for a lead role in battery assembly.
How to answer
- Start by outlining the initial challenges faced in the production process
- Detail the steps you took to analyze and identify inefficiencies
- Explain the specific changes or innovations you implemented
- Quantify the outcomes in terms of production speed, quality, or cost savings
- Share any feedback from team members or management on your improvements
What not to say
- Focusing only on technical details without discussing the impact
- Neglecting to mention teamwork or collaboration
- Providing vague examples without measurable results
- Avoiding discussion of challenges faced during the project
Example answer
“At my previous position with a battery manufacturing company in Melbourne, I noticed our assembly line was experiencing delays due to inefficient material handling. I led a project to redesign the workflow, implementing a just-in-time inventory system that reduced material waiting time by 30%. As a result, our production output increased by 20% without compromising quality, which was praised in our quarterly review.”
Skills tested
Question type
5.2. How do you ensure quality control in the battery assembly process?
Introduction
Quality control is critical in battery production to ensure safety and reliability. This question assesses your understanding of quality assurance processes and your ability to enforce them.
How to answer
- Outline the quality control measures you have implemented in past roles
- Describe any specific tools or techniques you use for monitoring quality
- Explain how you train your team on quality standards and procedures
- Discuss how you handle quality issues when they arise
- Mention any relevant metrics you track to ensure compliance with quality standards
What not to say
- Indicating that quality control is not a priority
- Failing to mention specific methods or tools used for quality assurance
- Not discussing team involvement in quality processes
- Ignoring the importance of continuous improvement in quality control
Example answer
“In my role at a battery manufacturing facility, I implemented a comprehensive quality control program that included regular inspections at each stage of production. I trained my team on using statistical process control tools to monitor key quality metrics. When we identified a batch with defects, I led a root cause analysis that resulted in a 50% reduction in defects over the next quarter. This proactive approach not only improved product quality but also boosted team morale as everyone felt involved in the process.”
Skills tested
Question type
6. Auto Battery Production Supervisor Interview Questions and Answers
6.1. Can you describe a time when you improved the efficiency of a production line in your previous role?
Introduction
This question is crucial for assessing your ability to optimize production processes, which is key in a supervisory role in auto battery production.
How to answer
- Explain the specific production process you focused on and identify the inefficiencies.
- Describe the steps you took to analyze the production workflow.
- Detail the solutions you implemented and how you involved your team.
- Quantify the improvements in terms of efficiency, cost savings, or output.
- Discuss the long-term impact of your changes on production quality and safety.
What not to say
- Vaguely describing improvements without specific metrics or outcomes.
- Claiming success without mentioning team involvement or collaboration.
- Focusing only on technical solutions without considering employee input.
- Failing to address how you measured the effectiveness of your changes.
Example answer
“At my previous role with a leading battery manufacturer in Australia, I identified that our assembly line was experiencing bottlenecks due to inefficient workstation layout. I conducted a time-motion study and proposed a new layout that streamlined the workflow. After implementing these changes, we saw a 20% increase in output and reduced assembly time by 15%. This not only improved our efficiency but also boosted team morale as they found the new layout more ergonomic.”
Skills tested
Question type
6.2. How do you ensure compliance with safety and quality standards in production?
Introduction
This question evaluates your understanding of safety regulations and quality control, which are critical in the auto battery production industry.
How to answer
- Describe your knowledge of relevant safety and quality standards (e.g., ISO, AS/NZS).
- Explain your approach to training team members on these standards.
- Discuss how you monitor compliance and address non-compliance issues.
- Share examples of how you have improved safety or quality in past roles.
- Highlight the importance of fostering a culture of safety and quality within the team.
What not to say
- Neglecting to mention specific safety standards or regulations.
- Claiming that safety is someone else's responsibility.
- Overshadowing quality control with production speed.
- Failing to provide concrete examples of compliance initiatives.
Example answer
“In my previous position, I ensured compliance with AS/NZS standards by implementing a rigorous safety training program for all team members. I conducted monthly audits and established a feedback loop for reporting safety concerns. As a result, our facility achieved a 30% reduction in safety incidents over the year. I believe that prioritizing safety not only protects staff but also enhances overall production quality.”
Skills tested
Question type
Similar Interview Questions and Sample Answers
Simple pricing, powerful features
Upgrade to Himalayas Plus and turbocharge your job search.
Himalayas
Himalayas Plus
Himalayas Max
Find your dream job
Sign up now and join over 100,000 remote workers who receive personalized job alerts, curated job matches, and more for free!
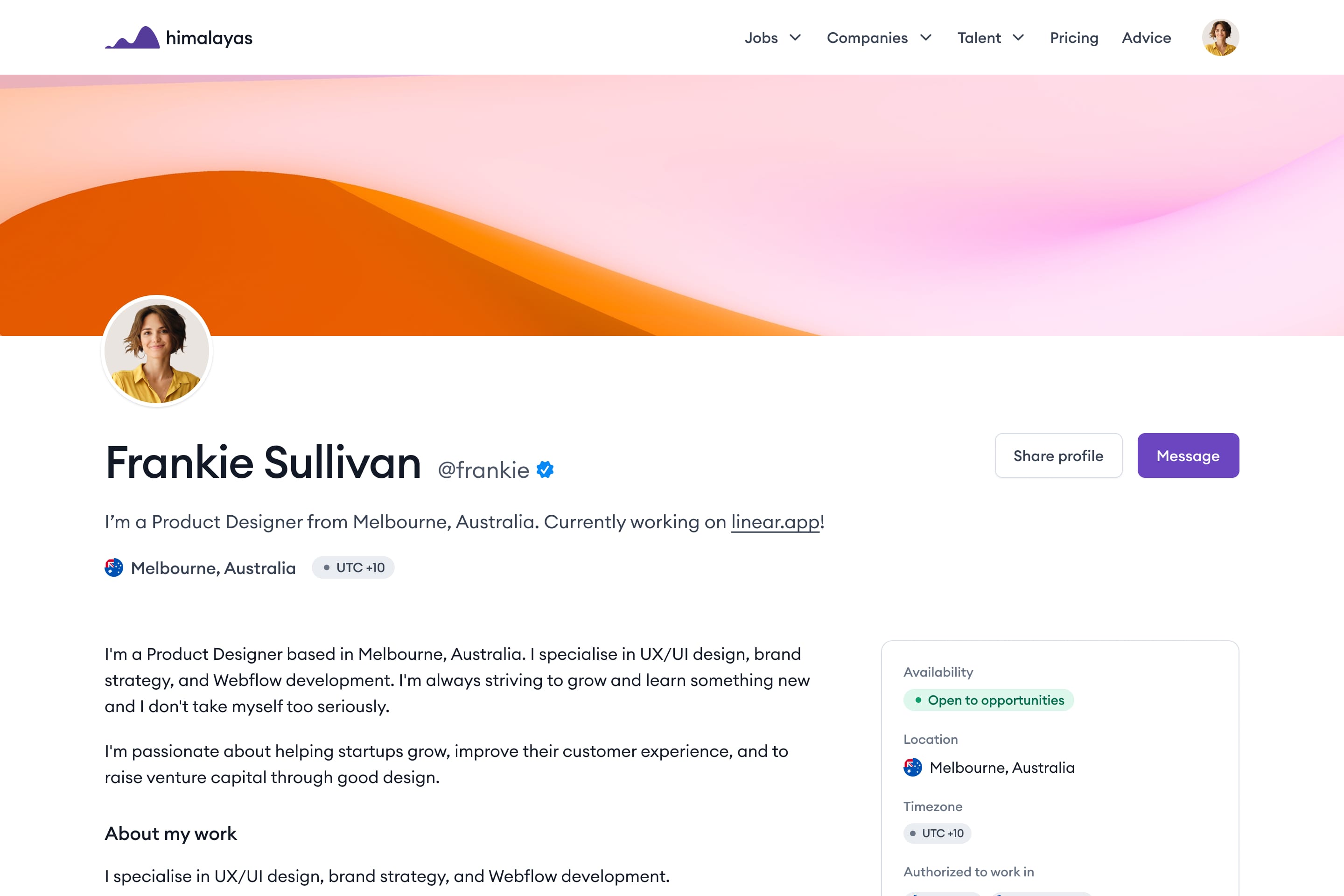