5 Aircraft Part Assembler Interview Questions and Answers
Aircraft Part Assemblers are responsible for constructing and assembling components used in aircraft manufacturing. They follow detailed blueprints and specifications to ensure precision and safety standards are met. Junior assemblers typically focus on basic tasks and learning assembly techniques, while senior and lead assemblers oversee complex assemblies, ensure quality control, and may mentor junior team members. Supervisors manage assembly teams and coordinate production schedules. Need to practice for an interview? Try our AI interview practice for free then unlock unlimited access for just $9/month.
Unlimited interview practice for $9 / month
Improve your confidence with an AI mock interviewer.
No credit card required
1. Junior Aircraft Part Assembler Interview Questions and Answers
1.1. Can you describe a time when you had to follow detailed assembly instructions closely? What was the outcome?
Introduction
This question assesses your attention to detail and ability to follow complex procedures, which are critical in aircraft assembly to ensure safety and quality.
How to answer
- Select a specific instance from your experience where following instructions was crucial.
- Explain the complexity of the instructions and why they were important.
- Detail the steps you took to ensure accuracy during the assembly process.
- Discuss the outcome and any positive feedback received or issues avoided due to your diligence.
- Reflect on any lessons learned that could improve future performance.
What not to say
- Vague responses without specific examples.
- Overlooking the importance of the instructions or implying they were not necessary.
- Focusing only on the outcome, without explaining the process.
- Failing to acknowledge any mistakes or how they were handled.
Example answer
“During my internship at Bombardier, I was tasked with assembling the fuselage of a regional jet. The assembly manual was complex and required precision in following each step. I double-checked each instruction and used a checklist to ensure I didn’t miss any components. As a result, my section passed inspection without any issues, and the project was completed ahead of schedule. This experience taught me the value of meticulousness and the importance of adhering to safety protocols.”
Skills tested
Question type
1.2. How do you handle repetitive tasks, and what strategies do you use to maintain focus and motivation?
Introduction
This question evaluates your ability to manage monotony, which is common in assembly roles, while maintaining high standards of quality and efficiency.
How to answer
- Acknowledge the nature of repetitive tasks in assembly work.
- Discuss specific techniques you use to stay focused, such as setting personal goals or taking structured breaks.
- Share examples of how you stay motivated during long periods of repetitive work.
- Mention any tools or methods that help you track your progress.
- Emphasize the importance of quality and safety in every task.
What not to say
- Expressing boredom or negativity towards repetitive tasks.
- Indicating that you have no strategies for maintaining focus.
- Failing to recognize the importance of quality in repetitive tasks.
- Suggesting that you might cut corners to finish faster.
Example answer
“In my previous role at a manufacturing plant, I often performed the same assembly task for hours. To maintain focus, I would set small goals for myself, such as completing a certain number of assemblies before taking a brief break. I also kept a checklist to track my progress, which gave me a sense of accomplishment. This approach helped me stay motivated and ensured that I maintained high-quality work throughout my shifts, ultimately contributing to the team’s overall efficiency.”
Skills tested
Question type
2. Aircraft Part Assembler Interview Questions and Answers
2.1. Can you describe a time when you had to troubleshoot an issue during the assembly process?
Introduction
This question is crucial for understanding your problem-solving skills and ability to maintain quality standards in aircraft assembly, which can have serious safety implications.
How to answer
- Begin with a brief overview of the assembly task you were working on.
- Clearly describe the issue that arose during the process.
- Explain your thought process and the steps you took to identify the root cause.
- Detail the solution you implemented to resolve the issue.
- Share the outcome and any lessons learned that improved future assembly processes.
What not to say
- Claiming you have never faced any issues during assembly.
- Providing a vague answer without specific details about the problem or solution.
- Blaming others for the issue instead of focusing on your actions.
- Failing to mention the importance of quality and safety in your response.
Example answer
“While assembling a wing component at Boeing, I noticed that a part didn't fit as expected. I paused the assembly line and investigated, discovering that a previous part had been incorrectly installed. I coordinated with my team to rectify the issue and implemented a double-check system for critical components. This not only resolved the immediate problem but reduced similar errors by 20% in future assemblies.”
Skills tested
Question type
2.2. How do you ensure that the parts you assemble meet quality standards and specifications?
Introduction
This question assesses your understanding of quality control processes and your commitment to maintaining high standards in aircraft assembly.
How to answer
- Discuss the specific quality standards and regulations applicable to aircraft assembly.
- Describe your personal checklist or guidelines for verifying parts during assembly.
- Explain how you document and report any deviations from quality standards.
- Share any experience you have with tools or technologies that assist in quality assurance.
- Mention the importance of teamwork and communication in maintaining quality.
What not to say
- Suggesting that quality checks are not your responsibility.
- Failing to reference any industry standards or regulations.
- Providing a general answer without specifics about your processes.
- Neglecting to mention teamwork or communication in ensuring quality.
Example answer
“At Airbus, I follow the established quality standards like AS9100 and use a detailed checklist for each assembly task. I verify each component against technical drawings and perform visual inspections for defects. If I notice any discrepancies, I document them and notify my supervisor immediately. This process has helped maintain our team's quality rate of over 98% consistently.”
Skills tested
Question type
3. Senior Aircraft Part Assembler Interview Questions and Answers
3.1. Can you describe a specific instance where you identified a quality issue during assembly, and how you addressed it?
Introduction
This question assesses your attention to detail and problem-solving skills, which are crucial in ensuring the safety and reliability of aircraft components.
How to answer
- Use the STAR method to structure your response: Situation, Task, Action, Result.
- Clearly explain the quality issue you encountered and its potential impact.
- Detail the steps you took to investigate and resolve the issue.
- Discuss any collaboration with team members or superiors to rectify the problem.
- Highlight the outcomes of your actions, including any improvements in the assembly process.
What not to say
- Failing to take responsibility for identifying issues.
- Describing a quality issue without a resolution or learning outcome.
- Overemphasizing individual contributions without mentioning teamwork.
- Neglecting to mention the importance of quality control in your role.
Example answer
“While assembling a series of wing components, I noticed discrepancies in the dimensions of several parts. Understanding the potential safety implications, I halted the assembly process and reported the issue to my supervisor. Together, we conducted an inspection that revealed a calibration error in our equipment. We corrected the calibration and implemented a more rigorous inspection procedure moving forward. As a result, we reduced rework by 30% and enhanced overall quality control.”
Skills tested
Question type
3.2. How do you ensure compliance with safety regulations and standards during the assembly process?
Introduction
This question evaluates your knowledge of safety protocols and your commitment to maintaining a safe working environment, which is vital in the aviation industry.
How to answer
- Discuss your familiarity with relevant safety regulations and standards, such as those from Transport Canada or the FAA.
- Explain your personal practices for maintaining safety during assembly.
- Share examples of safety training you've undergone or conducted.
- Describe how you communicate safety protocols to team members.
- Mention any contributions you've made to improving safety procedures.
What not to say
- Implying that safety is not a priority in your work.
- Providing vague or generic responses without specific examples.
- Failing to demonstrate an understanding of current safety regulations.
- Neglecting to mention the importance of continuous safety education.
Example answer
“I prioritize safety by staying up-to-date with Transport Canada's regulations and ensuring all assembly procedures comply with these standards. In my previous role, I conducted monthly safety briefings for the team to reinforce safe practices. Additionally, I initiated a peer review system for complex assembly tasks, which not only enhanced compliance but also fostered a culture of safety awareness. This initiative led to zero safety incidents during my tenure.”
Skills tested
Question type
4. Lead Aircraft Part Assembler Interview Questions and Answers
4.1. Can you describe your experience with assembling complex aircraft parts and the tools you used?
Introduction
This question assesses your technical skills and familiarity with the tools and processes involved in aircraft assembly, which are critical for ensuring safety and quality.
How to answer
- Begin by outlining your relevant experience in aircraft assembly, focusing on specific parts or components.
- Mention the tools and technologies you're proficient with, explaining their significance in the assembly process.
- Discuss any quality control measures you've implemented or followed during assembly.
- Highlight any certifications or training you've received that relate to aircraft assembly.
- Provide examples of how your work contributed to the overall success of a project or operation.
What not to say
- Avoid vague descriptions of your experience without specific details.
- Don't focus solely on tools without explaining how you used them in context.
- Refrain from mentioning any experience that does not relate directly to aircraft assembly.
- Avoid downplaying the importance of safety and quality in your assembly work.
Example answer
“In my previous role at Airbus South Africa, I was responsible for assembling wing components using advanced pneumatic tools and precision measuring equipment. I ensured that each assembly met stringent quality control standards, which were vital for the aircraft's performance and safety. I completed a specialized training course on composite materials, which helped me improve my assembly techniques, resulting in a 15% reduction in assembly time while maintaining quality.”
Skills tested
Question type
4.2. Describe a challenging assembly project you worked on and how you overcame the obstacles.
Introduction
This question evaluates your problem-solving skills and ability to work under pressure, which are essential in the fast-paced environment of aircraft assembly.
How to answer
- Use the STAR method (Situation, Task, Action, Result) to structure your response.
- Clearly define the challenge you faced and the stakes involved.
- Detail the specific actions you took to address the challenge, including any teamwork or collaboration.
- Highlight the outcome of your actions, particularly any improvements in efficiency, quality, or safety.
- Reflect on what you learned from the experience and how it impacted your approach to future projects.
What not to say
- Avoid blaming others for the challenges encountered.
- Don't focus too much on the problem without providing a solution.
- Refrain from giving examples that lack measurable outcomes.
- Avoid vague statements that do not clearly outline your role in overcoming the challenge.
Example answer
“During a critical phase of assembling aircraft fuselage sections at Boeing South Africa, we faced a delay due to a shortage of specialized rivets. I organized a team meeting to brainstorm solutions, which led us to source alternative rivet suppliers locally. This collaboration not only resolved the delay but also strengthened our relationships with local vendors. As a result, we completed the project on time, and I learned the importance of resourcefulness and teamwork in overcoming obstacles.”
Skills tested
Question type
5. Assembly Supervisor (Aircraft Parts) Interview Questions and Answers
5.1. Can you describe a time when you had to ensure quality control during the assembly process?
Introduction
This question evaluates your attention to detail and ability to enforce quality standards, which are critical in the aircraft parts assembly industry.
How to answer
- Use the STAR method to structure your response, focusing on the Situation, Task, Action, and Result.
- Clearly describe the quality control measures you implemented during assembly.
- Explain how you identified potential quality issues and the steps you took to address them.
- Discuss how you communicated these standards to your team and ensured compliance.
- Highlight the impact of your efforts on product quality and team performance.
What not to say
- Neglecting to mention specific quality control measures or tools used.
- Focusing solely on the problem without discussing your solution.
- Taking credit for team efforts without acknowledging contributions.
- Failing to provide measurable outcomes or results.
Example answer
“At Airbus, I noticed that a particular assembly line was experiencing a higher rate of defects. I initiated a thorough review of our quality control process, which led to the implementation of a double-check system at critical points of assembly. By training my team on these new standards, we reduced defects by 30% within three months, significantly improving our output quality.”
Skills tested
Question type
5.2. How do you motivate your team to meet assembly deadlines without compromising quality?
Introduction
This question assesses your leadership and motivational skills, which are essential for managing a team in a high-stakes environment like aircraft assembly.
How to answer
- Discuss your leadership style and how it fosters a positive work environment.
- Share specific strategies you use to motivate your team, such as recognition, incentives, or team-building activities.
- Explain how you balance the urgency of deadlines with the importance of maintaining quality standards.
- Include examples of successful outcomes resulting from your motivational techniques.
- Mention any tools or methods you use to track progress and celebrate achievements.
What not to say
- Indicating that deadlines are the only priority with no regard for quality.
- Failing to mention your team’s role in achieving goals.
- Using vague statements without concrete examples.
- Describing a one-size-fits-all approach to motivation.
Example answer
“In my role at Lufthansa Technik, I prioritize open communication and team recognition. I set clear expectations and involve my team in the goal-setting process, which fosters ownership. I also celebrate small wins weekly, which keeps morale high. This approach allowed us to consistently meet deadlines while maintaining a defect rate below 1% during peak production times.”
Skills tested
Question type
Similar Interview Questions and Sample Answers
Simple pricing, powerful features
Upgrade to Himalayas Plus and turbocharge your job search.
Himalayas
Himalayas Plus
Himalayas Max
Find your dream job
Sign up now and join over 100,000 remote workers who receive personalized job alerts, curated job matches, and more for free!
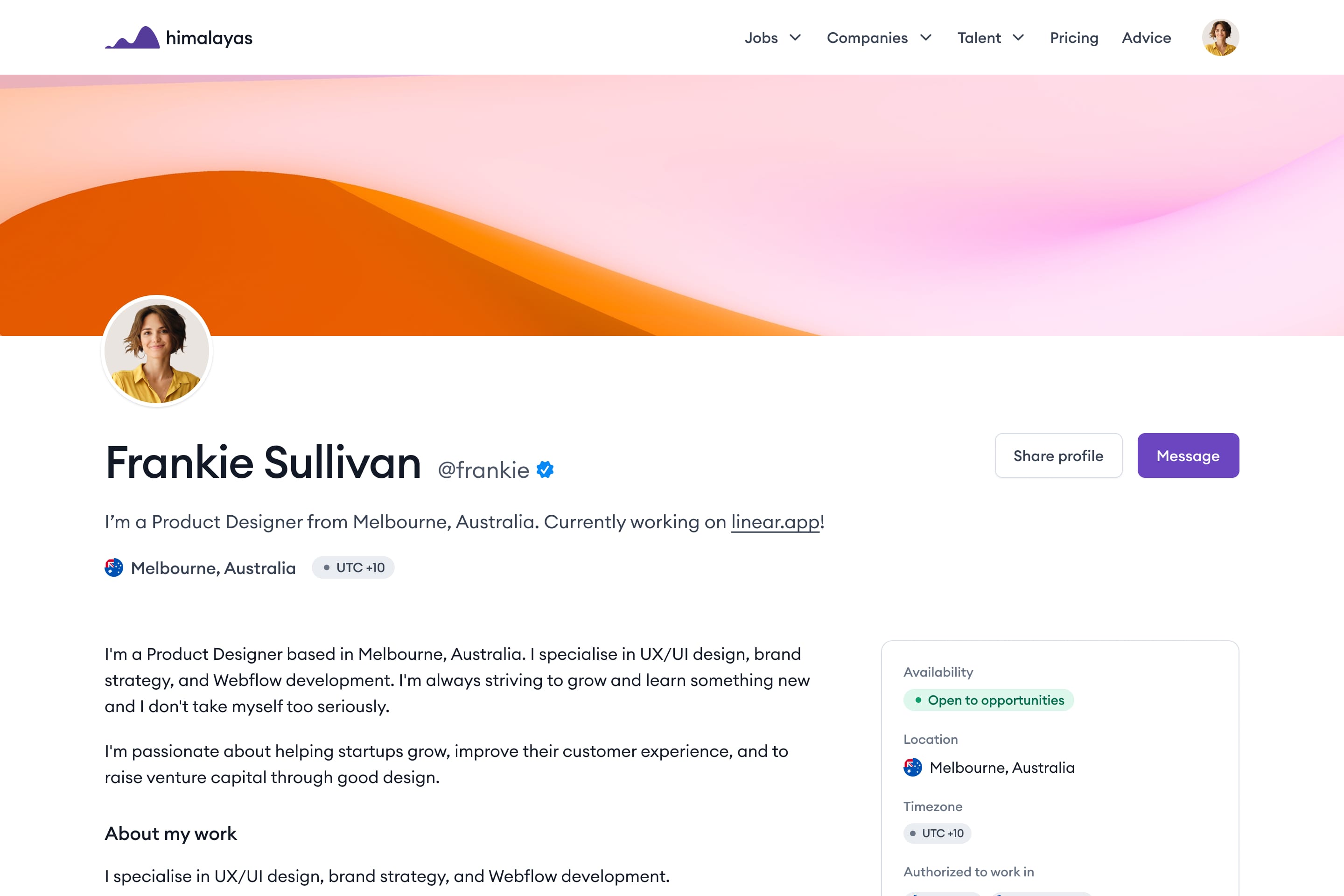