4 Battery Assembler Interview Questions and Answers
Battery Assemblers are responsible for constructing, testing, and assembling battery components and systems. They follow technical specifications and safety protocols to ensure high-quality and reliable battery production. Junior roles focus on basic assembly tasks, while senior and lead positions involve overseeing processes, troubleshooting issues, and mentoring team members. Need to practice for an interview? Try our AI interview practice for free then unlock unlimited access for just $9/month.
Unlimited interview practice for $9 / month
Improve your confidence with an AI mock interviewer.
No credit card required
1. Battery Assembler Interview Questions and Answers
1.1. Can you describe your experience with assembling battery packs and how you ensure quality in your work?
Introduction
This question is crucial for assessing your hands-on experience and attention to detail, which are vital for a battery assembler role.
How to answer
- Begin by discussing your previous roles or training related to battery assembly
- Explain the specific processes you follow to ensure quality, such as testing and inspection methods
- Share any relevant tools or equipment you are proficient with
- Mention any quality standards you adhere to, like ISO or industry regulations
- Highlight any improvements you implemented to enhance quality or efficiency
What not to say
- Focusing solely on your experience without mentioning quality control
- Failing to provide specific examples or details about the battery assembly process
- Overlooking safety protocols or regulations in your answer
- Giving vague responses that lack depth or clarity
Example answer
“In my previous role at a local battery manufacturer, I was responsible for assembling lithium-ion battery packs. I followed strict quality control measures, including visual inspections and electrical testing of each pack before final assembly. I also implemented a new checklist that reduced assembly errors by 15%. Adhering to ISO 9001 standards was crucial to ensuring our products met safety and performance requirements.”
Skills tested
Question type
1.2. How do you handle repetitive tasks and maintain focus during long assembly shifts?
Introduction
This question evaluates your ability to manage monotony and maintain productivity, which is essential in assembly line work.
How to answer
- Discuss techniques you use to stay motivated and focused
- Mention any breaks or routines that help you recharge
- Explain how you maintain a positive attitude and work ethic in repetitive tasks
- Share any strategies for monitoring your performance and efficiency
- Illustrate how you avoid mistakes during long periods of repetition
What not to say
- Expressing frustration with repetitive tasks without solutions
- Suggesting that you lose focus or make mistakes often
- Failing to mention any coping strategies or routines
- Giving a negative perspective on assembly line work
Example answer
“To handle the repetitive nature of assembly work, I set small goals for myself throughout the shift, such as completing a certain number of battery packs before taking a short break. I also find it helpful to listen to music or podcasts during work to keep my mind engaged. This approach allows me to maintain focus and efficiency, and I’ve consistently met or exceeded my production targets.”
Skills tested
Question type
2. Senior Battery Assembler Interview Questions and Answers
2.1. Can you describe a complex battery assembly project you worked on and the specific challenges you faced?
Introduction
This question assesses your technical knowledge and problem-solving abilities in the battery assembly process, which is crucial for a Senior Battery Assembler role.
How to answer
- Use the STAR method (Situation, Task, Action, Result) to structure your response
- Clearly outline the project requirements and objectives
- Detail the specific challenges you encountered during assembly
- Explain the steps you took to overcome those challenges
- Quantify the results achieved and any improvements made to the process
What not to say
- Vague descriptions without specific examples
- Failing to mention personal contributions or leadership
- Overlooking safety protocols or quality standards
- Focusing too much on technical jargon without clarity
Example answer
“In my previous role at Panasonic, I led a project to assemble a new type of lithium-ion battery. We faced challenges with component alignment, which risked product integrity. I implemented a new jig to ensure precise placement, which reduced assembly errors by 30%. This project taught me the importance of continuous improvement and quality assurance in battery assembly.”
Skills tested
Question type
2.2. How do you ensure quality control during the battery assembly process?
Introduction
This question evaluates your understanding of quality assurance practices and your ability to maintain high standards in production, which is vital for a Senior Battery Assembler.
How to answer
- Describe the quality control measures you implement during assembly
- Share specific tools or techniques you use for inspection
- Discuss how you train and guide team members on quality standards
- Explain how you handle quality issues when they arise
- Provide examples of how your approach has improved quality outcomes
What not to say
- Neglecting to mention specific quality control protocols
- Suggesting that quality is solely the responsibility of a separate team
- Providing generic answers without specific examples
- Overlooking the importance of documentation and traceability
Example answer
“At Toyota, I implemented a multi-step quality control process during assembly, including visual inspections and functional testing. I trained my team on identifying defects and maintained a log of quality issues to analyze trends. This proactive approach led to a 20% reduction in defects over six months and improved overall team awareness of quality standards.”
Skills tested
Question type
3. Lead Battery Assembler Interview Questions and Answers
3.1. Can you describe a time when you identified a quality issue in battery assembly and how you addressed it?
Introduction
This question assesses your attention to detail and problem-solving skills, which are critical for maintaining high quality in battery assembly processes.
How to answer
- Use the STAR method to outline the situation, task, action, and result
- Clearly state the quality issue you encountered
- Describe the steps you took to investigate and resolve the issue
- Highlight any collaboration with team members or other departments
- Share the impact of your actions on product quality and safety
What not to say
- Blaming others for the quality issue without taking responsibility
- Providing vague responses that lack specifics or metrics
- Focusing solely on the problem instead of the solution
- Neglecting to mention the importance of teamwork
Example answer
“In my previous role at Johnson Matthey, I noticed a consistent defect rate in the battery cells we were assembling. I conducted a thorough analysis and found that a specific machine was miscalibrated. I collaborated with the maintenance team to recalibrate the machine and implemented additional quality checks. As a result, we reduced the defect rate by 30%, significantly improving our overall product quality.”
Skills tested
Question type
3.2. How would you train new team members on battery assembly best practices?
Introduction
This question evaluates your leadership and training abilities, which are essential for ensuring that all team members adhere to best practices in battery assembly.
How to answer
- Outline a structured training program that includes both theory and practical application
- Emphasize the importance of safety and quality throughout the training
- Mention how you would assess new members' understanding and skills
- Describe how you would encourage questions and feedback during training
- Share any tools or resources you would use to support the training process
What not to say
- Suggesting that training is not important or can be rushed
- Failing to mention safety protocols and quality standards
- Not providing methods for assessing trainee progress
- Overlooking the importance of ongoing support after initial training
Example answer
“I would develop a comprehensive training program that starts with safety protocols and theoretical knowledge of battery assembly. This would be followed by hands-on training where new members would shadow experienced team members. After the training, I would conduct assessments to ensure understanding and encourage ongoing feedback. I believe in a supportive environment where new hires feel comfortable asking questions. At my last job, this approach significantly reduced onboarding time and improved team cohesion.”
Skills tested
Question type
4. Battery Assembly Supervisor Interview Questions and Answers
4.1. Can you describe a time when you improved the efficiency of a battery assembly process?
Introduction
This question assesses your ability to identify inefficiencies and implement process improvements, which are crucial for a supervisory role in battery assembly.
How to answer
- Use the STAR method (Situation, Task, Action, Result) to structure your response.
- Start by outlining the specific inefficiency you identified in the assembly process.
- Describe the steps you took to analyze the issue and develop a solution.
- Detail the actions you implemented and how you involved your team in the process.
- Quantify the results of your improvements, such as increased output or reduced waste.
What not to say
- Focusing on a solution without explaining the problem first.
- Taking sole credit for improvements without acknowledging team contributions.
- Vague responses that lack specific metrics or outcomes.
- Describing improvements without mentioning the sustainability of the changes.
Example answer
“At a previous position in a battery manufacturing plant, I noticed our assembly line was experiencing frequent delays due to manual handling. I initiated a process analysis, which led to the implementation of an automated material handling system. This reduced our assembly time by 30% and improved overall line efficiency, allowing us to meet production targets consistently.”
Skills tested
Question type
4.2. How do you ensure safety compliance and standards are met in the battery assembly area?
Introduction
This question evaluates your knowledge of safety regulations and your ability to enforce compliance, which is critical in a manufacturing environment dealing with batteries.
How to answer
- Describe your understanding of relevant safety regulations in battery assembly.
- Explain the procedures you put in place to ensure compliance among your team.
- Share examples of training programs or safety drills you have conducted.
- Discuss how you handle non-compliance issues or safety violations.
- Highlight the importance of fostering a safety-first culture within the team.
What not to say
- Implying that safety compliance is solely the responsibility of management.
- Neglecting to mention specific safety standards or regulations.
- Providing a generic answer without real examples.
- Underestimating the role of team engagement in safety practices.
Example answer
“In my previous role, I made it a priority to ensure safety compliance by conducting weekly safety audits and monthly training sessions for all assembly staff. I collaborated with the safety officer to implement a comprehensive safety manual tailored to our battery assembly processes. When a minor incident occurred, I led a thorough investigation and revised our protocol, ensuring that all team members understood the importance of adhering to safety standards. This proactive approach resulted in zero accidents over a year.”
Skills tested
Question type
Similar Interview Questions and Sample Answers
Simple pricing, powerful features
Upgrade to Himalayas Plus and turbocharge your job search.
Himalayas
Himalayas Plus
Himalayas Max
Find your dream job
Sign up now and join over 100,000 remote workers who receive personalized job alerts, curated job matches, and more for free!
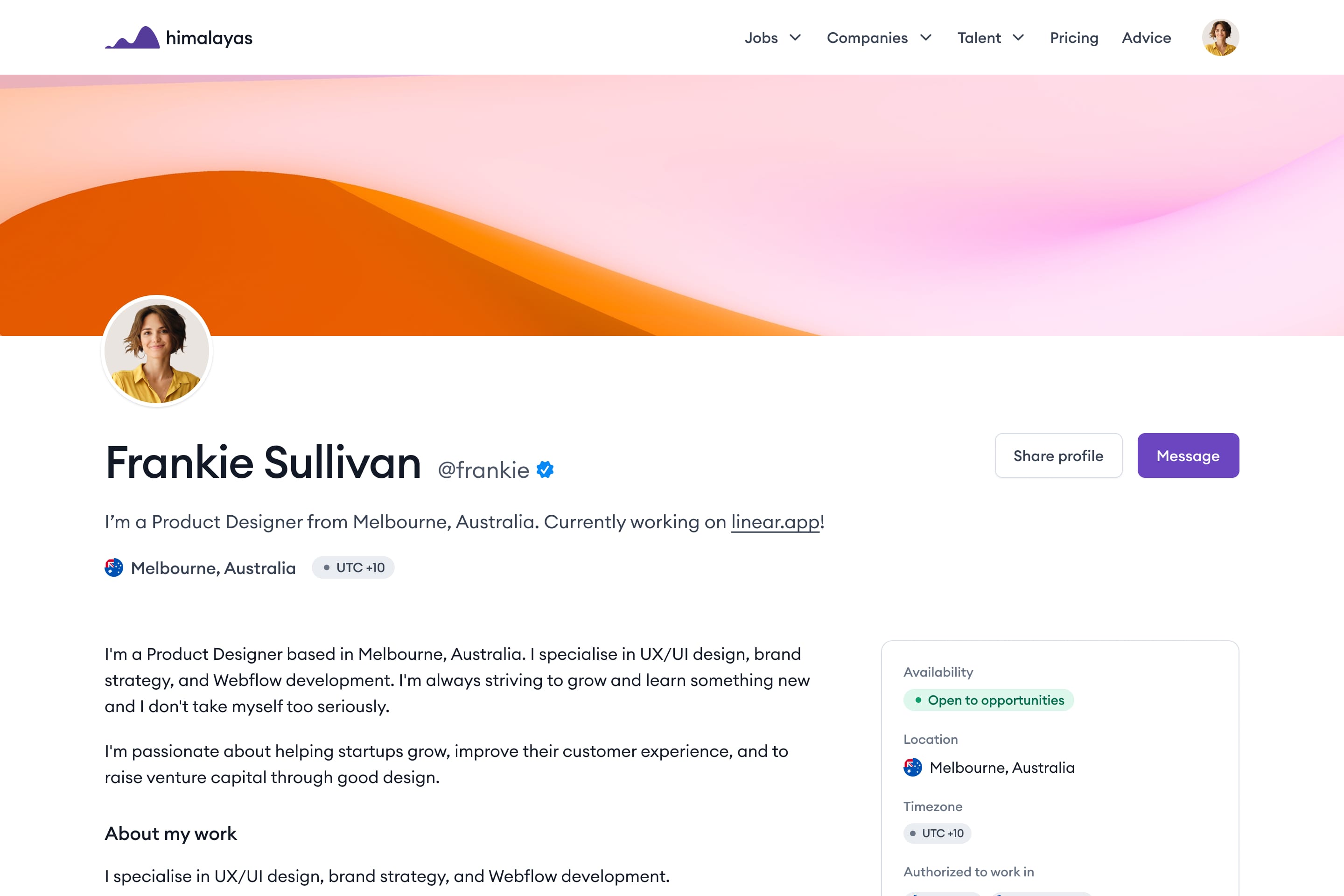