Complete Tool and Die Designer Career Guide
Tool and die designers are the architects behind precision manufacturing, translating product designs into the specialized tools, dies, and molds that shape everything from automotive parts to medical devices. This role demands a unique blend of engineering principles, advanced CAD software proficiency, and an acute understanding of material properties to create the essential components that enable mass production. It’s a rewarding career for those who enjoy meticulous problem-solving and seeing their designs bring complex products to life.
Key Facts & Statistics
Median Salary
$66,970 USD
(U.S. national median, U.S. Bureau of Labor Statistics, May 2023)
Range: $45k - $95k+ USD, varying significantly by experience, industry, and geographic location.
Growth Outlook
0%
as fast as average (U.S. Bureau of Labor Statistics, 2022-2032)
Annual Openings
≈3,200
openings annually (U.S. Bureau of Labor Statistics, 2022-2032)
Top Industries
Typical Education
Associate's degree in tool and die design, mechanical engineering technology, or a related field. Apprenticeships and significant on-the-job training are also common and highly valued.
What is a Tool and Die Designer?
A Tool and Die Designer is a specialized engineer or technician who creates the blueprints and specifications for the tools, dies, jigs, and fixtures used in manufacturing. These precision instruments shape raw materials into finished products, particularly in metal stamping, plastic injection molding, and forging processes. Their work ensures that components are produced efficiently, accurately, and consistently.
This role differs significantly from a general Mechanical Designer, who might design end products. Tool and Die Designers focus exclusively on the specialized equipment that makes those products. They must possess a deep understanding of material science, manufacturing processes, and machine capabilities to translate product designs into effective and durable tooling solutions. Their expertise directly impacts production cost, quality, and speed.
What does a Tool and Die Designer do?
Key Responsibilities
- Interpret engineering blueprints and specifications to conceptualize precise tool and die designs for manufacturing processes.
- Develop detailed 2D and 3D CAD models of stamping dies, molds, jigs, and fixtures using specialized design software.
- Calculate material stresses, clearances, and tolerances to ensure the structural integrity and functional accuracy of designed tools.
- Collaborate with manufacturing engineers and machinists to refine designs, addressing manufacturability concerns and optimizing production efficiency.
- Perform simulations and analyses on tool designs to predict performance, identify potential failure points, and reduce prototyping costs.
- Prepare comprehensive documentation, including bill of materials, assembly instructions, and operational procedures for tool fabrication and use.
- Review and modify existing tool designs to improve performance, extend lifespan, or adapt to new product requirements.
Work Environment
Tool and Die Designers typically work in office settings, often co-located with manufacturing facilities or engineering departments. The work involves significant time at a computer workstation, creating and refining designs. Collaboration with engineers, machinists, and production staff is frequent, requiring strong communication skills. The pace can be project-driven, with deadlines for new product launches or design revisions. While primarily office-based, occasional visits to the shop floor are necessary to observe tool performance or troubleshoot issues. Remote work possibilities exist but are less common due to the need for direct interaction with physical manufacturing processes.
Tools & Technologies
Tool and Die Designers primarily utilize specialized CAD/CAM software suites such as SolidWorks, AutoCAD, CATIA, and Siemens NX for 2D drafting and 3D modeling. They also work with simulation and analysis tools like FEA (Finite Element Analysis) software to test designs virtually. Knowledge of manufacturing execution systems (MES) and enterprise resource planning (ERP) software is beneficial for integrating designs into production workflows. Common shop floor tools and measurement devices, including calipers and micrometers, are also relevant for understanding design implications. Familiarity with programming languages for automation, such as macro scripting within CAD software, is increasingly valuable.
Tool and Die Designer Skills & Qualifications
A Tool and Die Designer creates detailed blueprints and specifications for tools, dies, jigs, and fixtures used in manufacturing processes. This role demands a blend of engineering principles, material science, and practical manufacturing knowledge. The qualification landscape prioritizes a strong foundation in mechanical design, often gained through formal education or extensive practical experience.
Requirements vary significantly by seniority and industry. Entry-level positions may accept associate's degrees or vocational training, while senior roles often require bachelor's degrees and several years of specialized experience. Companies producing complex components for aerospace or automotive industries typically demand higher academic qualifications and advanced CAD/CAM proficiency than those in general manufacturing. Geographic location also influences requirements; regions with strong manufacturing hubs may have more structured apprenticeship programs.
Formal education, practical experience, and certifications each contribute to a designer's profile. Practical experience, particularly hands-on work with machining and toolmaking, holds significant weight. Certifications in specific CAD software, GD&T, or specialized manufacturing processes enhance a candidate's marketability. The skill landscape evolves with new materials, additive manufacturing techniques, and advanced automation, requiring continuous learning in areas like simulation software and smart tooling design.
Education Requirements
Technical Skills
- Advanced CAD software proficiency (e.g., SolidWorks, CATIA, PTC Creo, NX) for 3D modeling and assembly design
- Geometric Dimensioning and Tolerancing (GD&T) application and interpretation
- Die design principles (progressive, compound, transfer dies) and stamping processes
- Jig and fixture design for machining, assembly, and inspection operations
- Material science knowledge (metals, alloys, plastics) and their properties under stress
- CAM software understanding for manufacturing process simulation and optimization
- CNC machining principles and capabilities relevant to tool fabrication
- Blueprint reading and technical drawing creation following industry standards
- Feasibility analysis and cost estimation for tool and die production
- Finite Element Analysis (FEA) software for stress, strain, and deformation analysis (for complex designs)
- Tool steel selection and heat treatment processes
- Automation and robotics integration considerations in tooling design
Soft Skills
- Problem-solving and analytical thinking: Tool and Die Designers must diagnose complex manufacturing challenges and develop innovative solutions for tool functionality and efficiency.
- Attention to detail: Precision is paramount in tool design; even minor errors can lead to costly manufacturing defects or failures.
- Spatial reasoning: Visualizing complex 3D forms and how they interact within a manufacturing process is crucial for effective design.
- Communication and collaboration: Designers frequently work with engineers, machinists, and production teams, requiring clear articulation of design intent and active listening.
- Adaptability and continuous learning: The manufacturing landscape changes rapidly, demanding a willingness to learn new software, materials, and production techniques.
- Time management and project organization: Designers often manage multiple projects simultaneously, requiring strong organizational skills to meet deadlines and prioritize tasks.
- Creativity and innovation: Developing novel tool designs that improve efficiency, reduce costs, or enable new product features requires creative thinking.
- Persistence and resilience: Design challenges can be complex and require iterative refinement; designers must persevere through setbacks to achieve optimal solutions.
How to Become a Tool and Die Designer
Becoming a Tool and Die Designer involves a blend of traditional education and practical, hands-on experience. While a formal engineering degree offers a strong theoretical foundation, many successful designers enter the field through vocational training, apprenticeships, or by progressing from a tool and die maker role. The timeline for entry varies significantly; a complete beginner might spend 2-4 years in a technical program or apprenticeship, while someone transitioning from a related manufacturing role could pivot in 6-12 months with focused CAD training.
Entry routes differ by company size and geographic location. Larger manufacturing firms often prefer candidates with a degree or extensive apprenticeship experience, valuing a deep understanding of manufacturing processes and materials. Smaller job shops, however, might prioritize practical design skills and experience with specific CAD/CAM software, sometimes offering on-the-job training. Misconceptions include believing a four-year degree is always mandatory or that design is purely theoretical; practical shop floor experience is invaluable for understanding manufacturability.
Networking within the manufacturing community, attending industry trade shows, and seeking mentorship from experienced designers provides critical insights and opportunities. The hiring landscape values demonstrable design proficiency, often shown through a portfolio of conceptual or completed tool designs. Overcoming barriers like a lack of direct experience often means starting in a related role, such as a drafter or a toolmaker, to gain foundational knowledge before moving into design.
Obtain foundational knowledge in mechanical design and manufacturing processes. Enroll in a vocational program, an associate's degree in mechanical design, or an apprenticeship focusing on tool and die making. This phase typically takes 1-2 years and provides essential theoretical understanding of materials, machining, and engineering principles.
Master industry-standard CAD software relevant to tool and die design, such as SolidWorks, AutoCAD, CATIA, or NX. Complete online courses, workshops, or certifications to build proficiency. Focus on creating precise 2D drawings and complex 3D models of components, assemblies, and tooling fixtures, which is critical for future design work.
Gain practical experience in a manufacturing environment, ideally as a machinist, toolmaker, or manufacturing technician. This hands-on experience, which can take 1-3 years, provides invaluable insight into the challenges of manufacturing, material behavior, and assembly processes, directly informing better tool designs.
Develop a professional portfolio showcasing your design capabilities. Include a range of projects, from simple jigs and fixtures to more complex stamping dies or molds. For each project, detail the design problem, your solution, the software used, and any manufacturing considerations, demonstrating your problem-solving approach.
Network with professionals in the manufacturing and tooling industries by attending trade shows, joining professional organizations like SME (Society of Manufacturing Engineers), and connecting with local machine shops. Informational interviews can provide insights into specific company needs and potential job openings, often leading to referrals.
Prepare for job applications by tailoring your resume to highlight relevant coursework, software proficiency, and practical experience. Practice explaining your portfolio projects and design thought process. Be ready to discuss your understanding of manufacturing tolerances, material selection, and cost-effective design principles during interviews.
Step 1
Obtain foundational knowledge in mechanical design and manufacturing processes. Enroll in a vocational program, an associate's degree in mechanical design, or an apprenticeship focusing on tool and die making. This phase typically takes 1-2 years and provides essential theoretical understanding of materials, machining, and engineering principles.
Step 2
Master industry-standard CAD software relevant to tool and die design, such as SolidWorks, AutoCAD, CATIA, or NX. Complete online courses, workshops, or certifications to build proficiency. Focus on creating precise 2D drawings and complex 3D models of components, assemblies, and tooling fixtures, which is critical for future design work.
Step 3
Gain practical experience in a manufacturing environment, ideally as a machinist, toolmaker, or manufacturing technician. This hands-on experience, which can take 1-3 years, provides invaluable insight into the challenges of manufacturing, material behavior, and assembly processes, directly informing better tool designs.
Step 4
Develop a professional portfolio showcasing your design capabilities. Include a range of projects, from simple jigs and fixtures to more complex stamping dies or molds. For each project, detail the design problem, your solution, the software used, and any manufacturing considerations, demonstrating your problem-solving approach.
Step 5
Network with professionals in the manufacturing and tooling industries by attending trade shows, joining professional organizations like SME (Society of Manufacturing Engineers), and connecting with local machine shops. Informational interviews can provide insights into specific company needs and potential job openings, often leading to referrals.
Step 6
Prepare for job applications by tailoring your resume to highlight relevant coursework, software proficiency, and practical experience. Practice explaining your portfolio projects and design thought process. Be ready to discuss your understanding of manufacturing tolerances, material selection, and cost-effective design principles during interviews.
Education & Training Needed to Become a Tool and Die Designer
Becoming a Tool and Die Designer requires a blend of theoretical knowledge and practical application, with several educational pathways available. Formal associate's or bachelor's degrees in mechanical engineering technology, manufacturing engineering, or industrial design provide a strong foundation, typically costing $20,000-$60,000 for an associate's and $40,000-$100,000+ for a bachelor's, with completion times of two and four years respectively. These programs often include extensive CAD/CAM training and material science, which are critical for the role.
Alternatively, many successful Tool and Die Designers begin with apprenticeships or vocational training programs, which are often more hands-on and can range from 1-5 years. These pathways typically focus on practical skills, machine operation, and toolroom experience, often with a lower direct cost as they may be employer-sponsored or involve paid on-the-job training. Employers often value this practical experience highly, sometimes even more than a four-year degree, especially for roles focused on production and problem-solving.
Continuous learning is essential due to evolving manufacturing technologies and software. Specialized certifications in CAD/CAM software (like SolidWorks, AutoCAD, or CATIA) or specific tooling processes (e.g., progressive dies, injection molds) enhance a designer's marketability. These certifications can range from a few hundred to several thousand dollars and take weeks to months to complete. The most effective educational strategy often combines formal education with hands-on experience and ongoing professional development in new design software and manufacturing techniques.
Tool and Die Designer Salary & Outlook
Compensation for a Tool and Die Designer varies significantly based on several key factors. Geographic location plays a crucial role; regions with a high concentration of manufacturing, such as the Midwest or parts of the Southeast in the U.S., often offer higher salaries due to demand and cost of living. International markets also show variation, with U.S. figures typically reflecting a strong market for specialized design skills.
Experience levels directly impact earning potential. Entry-level designers start lower, while those with extensive experience, specialized knowledge in complex tooling, or expertise in advanced CAD/CAM software command higher salaries. Total compensation extends beyond base pay, including performance bonuses, profit-sharing, and comprehensive benefits packages like health insurance, retirement plans, and professional development allowances for certifications.
Industry-specific trends, such as the growth in automotive, aerospace, or medical device manufacturing, influence salary growth. Companies utilizing cutting-edge design software or additive manufacturing techniques may offer premium compensation for designers skilled in these areas. Negotiating leverage comes from a strong portfolio, specialized skills, and a proven track record of efficient, accurate designs that reduce production costs. Remote work opportunities, while less common for this hands-on field, can still influence salary expectations based on the employer's location and the designer's ability to work effectively off-site.
Salary by Experience Level
Level | US Median | US Average |
---|---|---|
Junior Tool and Die Designer | $55k USD | $58k USD |
Tool and Die Designer | $70k USD | $72k USD |
Senior Tool and Die Designer | $85k USD | $88k USD |
Lead Tool and Die Designer | $102k USD | $105k USD |
Tool and Die Design Manager | $120k USD | $125k USD |
Market Commentary
The job market for Tool and Die Designers remains stable, driven by the ongoing need for precision manufacturing across various industries. While some manufacturing processes evolve, the fundamental requirement for custom tooling and dies persists. The U.S. Bureau of Labor Statistics projects a modest growth outlook for industrial designers, which includes tool and die specialists, indicating consistent demand rather than rapid expansion.
Emerging opportunities in this field are increasingly tied to advanced manufacturing technologies. Designers proficient in generative design, simulation software, and integrating designs for additive manufacturing (3D printing) are highly sought after. The automotive, aerospace, and medical device sectors continue to be significant employers, requiring innovative tooling for new product development and efficiency improvements.
Supply and demand dynamics show a consistent need for skilled designers, particularly those with strong foundational knowledge combined with modern software proficiency. An aging workforce in traditional manufacturing also creates openings for newer talent. Future-proofing this career involves continuous learning in new design software, materials science, and automation integration. While automation handles repetitive tasks, the creative and problem-solving aspects of complex tool and die design remain highly human-centric and recession-resistant due to their critical role in production. Geographic hotspots for this role align with major manufacturing hubs, though remote collaboration tools are slowly expanding possibilities.
Tool and Die Designer Career Path
Career progression for a Tool and Die Designer involves a clear path from fundamental design tasks to advanced engineering, leadership, and management. Professionals typically begin by mastering design software and manufacturing principles. As expertise grows, individuals choose between an individual contributor (IC) track, focusing on complex technical challenges, or a management track, leading teams and projects.
Advancement speed depends on several factors: the complexity of projects undertaken, continuous skill development in new technologies like additive manufacturing, and the industry served (e.g., automotive, aerospace, medical devices). Company size also plays a role; larger corporations might offer more structured advancement paths, while smaller shops could provide broader experience but fewer formal titles. Lateral moves into related fields like manufacturing engineering or product design are common.
Networking within professional organizations, pursuing certifications in CAD/CAM software, and gaining a reputation for precision and innovation significantly aid progression. Mentorship from experienced designers is invaluable for skill transfer and understanding industry nuances. Common career pivots include moving into quality control, supply chain management for tooling, or even entrepreneurship, starting their own design or fabrication services.
Junior Tool and Die Designer
0-2 yearsAssist senior designers with drafting, detailing, and minor design modifications for dies, molds, jigs, and fixtures. Work under direct supervision, primarily focusing on executing specific tasks within larger projects. Learn company standards and documentation procedures. Impact is limited to accuracy of assigned components.
Key Focus Areas
Develop strong proficiency in CAD software (e.g., SolidWorks, AutoCAD, CATIA). Understand basic machining processes, material properties, and GD&T principles. Focus on accuracy, attention to detail, and following established design standards. Begin to build problem-solving skills for simple design challenges.
Tool and Die Designer
2-5 yearsDesign and develop various tools, dies, molds, and fixtures from concept to production with moderate supervision. Create detailed 2D and 3D models, assembly drawings, and bill of materials. Collaborate with manufacturing engineers to ensure design feasibility. Responsible for accuracy and functionality of individual tooling components.
Key Focus Areas
Master advanced CAD modeling techniques, including surface modeling and complex assembly design. Deepen understanding of manufacturing processes, including stamping, forging, and injection molding. Develop problem-solving skills for complex design issues and optimize designs for manufacturability and cost. Cultivate effective communication with machinists and fabricators.
Senior Tool and Die Designer
5-8 yearsLead the design of highly complex and innovative tooling solutions, often for new product lines or challenging applications. Provide technical leadership and mentorship to junior designers. Make independent design decisions, often involving intricate mechanisms and tight tolerances. Influence project outcomes through design optimization and problem resolution.
Key Focus Areas
Develop expertise in design for automation, robotics, and advanced manufacturing technologies. Lead design reviews and provide technical guidance to junior designers. Cultivate project management skills, including scheduling, budgeting, and risk assessment. Contribute to process improvement initiatives and standardization efforts.
Lead Tool and Die Designer
8-12 yearsOversee multiple concurrent tool and die design projects, ensuring technical excellence and adherence to project timelines and budgets. Act as the primary technical authority for complex design challenges. Responsible for setting design standards and best practices. Directly impacts the efficiency and quality of the entire tooling department's output.
Key Focus Areas
Drive innovation in tooling design, exploring new materials and manufacturing techniques. Develop strategic planning skills related to tooling development and lifecycle management. Mentor and develop a team of designers, fostering their technical growth. Build strong relationships with cross-functional teams and external vendors.
Tool and Die Design Manager
12+ years total experience, 3+ years in a lead roleManage a team of Tool and Die Designers, overseeing all design projects and departmental operations. Develop and implement design strategies, allocate resources, and ensure quality standards. Responsible for departmental budget, performance, and talent development. Influences overall manufacturing capability and product launch success through effective tooling design management.
Key Focus Areas
Develop strong leadership and people management skills, including performance reviews, hiring, and team development. Master strategic planning for departmental resources, technology adoption, and long-term tooling needs. Cultivate business acumen to align design initiatives with company goals and profitability. Engage in industry trends and technological advancements.
Junior Tool and Die Designer
0-2 yearsAssist senior designers with drafting, detailing, and minor design modifications for dies, molds, jigs, and fixtures. Work under direct supervision, primarily focusing on executing specific tasks within larger projects. Learn company standards and documentation procedures. Impact is limited to accuracy of assigned components.
Key Focus Areas
Develop strong proficiency in CAD software (e.g., SolidWorks, AutoCAD, CATIA). Understand basic machining processes, material properties, and GD&T principles. Focus on accuracy, attention to detail, and following established design standards. Begin to build problem-solving skills for simple design challenges.
Tool and Die Designer
2-5 yearsDesign and develop various tools, dies, molds, and fixtures from concept to production with moderate supervision. Create detailed 2D and 3D models, assembly drawings, and bill of materials. Collaborate with manufacturing engineers to ensure design feasibility. Responsible for accuracy and functionality of individual tooling components.
Key Focus Areas
Master advanced CAD modeling techniques, including surface modeling and complex assembly design. Deepen understanding of manufacturing processes, including stamping, forging, and injection molding. Develop problem-solving skills for complex design issues and optimize designs for manufacturability and cost. Cultivate effective communication with machinists and fabricators.
Senior Tool and Die Designer
5-8 yearsLead the design of highly complex and innovative tooling solutions, often for new product lines or challenging applications. Provide technical leadership and mentorship to junior designers. Make independent design decisions, often involving intricate mechanisms and tight tolerances. Influence project outcomes through design optimization and problem resolution.
Key Focus Areas
Develop expertise in design for automation, robotics, and advanced manufacturing technologies. Lead design reviews and provide technical guidance to junior designers. Cultivate project management skills, including scheduling, budgeting, and risk assessment. Contribute to process improvement initiatives and standardization efforts.
Lead Tool and Die Designer
8-12 yearsOversee multiple concurrent tool and die design projects, ensuring technical excellence and adherence to project timelines and budgets. Act as the primary technical authority for complex design challenges. Responsible for setting design standards and best practices. Directly impacts the efficiency and quality of the entire tooling department's output.
Key Focus Areas
Drive innovation in tooling design, exploring new materials and manufacturing techniques. Develop strategic planning skills related to tooling development and lifecycle management. Mentor and develop a team of designers, fostering their technical growth. Build strong relationships with cross-functional teams and external vendors.
Tool and Die Design Manager
12+ years total experience, 3+ years in a lead roleManage a team of Tool and Die Designers, overseeing all design projects and departmental operations. Develop and implement design strategies, allocate resources, and ensure quality standards. Responsible for departmental budget, performance, and talent development. Influences overall manufacturing capability and product launch success through effective tooling design management.
Key Focus Areas
Develop strong leadership and people management skills, including performance reviews, hiring, and team development. Master strategic planning for departmental resources, technology adoption, and long-term tooling needs. Cultivate business acumen to align design initiatives with company goals and profitability. Engage in industry trends and technological advancements.
Job Application Toolkit
Ace your application with our purpose-built resources:
Tool and Die Designer Resume Examples
Proven layouts and keywords hiring managers scan for.
View examplesTool and Die Designer Cover Letter Examples
Personalizable templates that showcase your impact.
View examplesTop Tool and Die Designer Interview Questions
Practice with the questions asked most often.
View examplesTool and Die Designer Job Description Template
Ready-to-use JD for recruiters and hiring teams.
View examplesGlobal Tool and Die Designer Opportunities
Tool and Die Designers are crucial globally, creating precision tools, dies, and molds for manufacturing across diverse industries. Demand remains strong in industrialized nations, especially in automotive, aerospace, and medical device sectors. Regulatory standards and material specifications vary by region, impacting design practices. Professionals often seek international roles for advanced projects or specialized manufacturing hubs. International certifications in CAD/CAM software or specific industry standards enhance global mobility.
Global Salaries
Tool and Die Designer salaries vary significantly by region, reflecting economic conditions and industry demand. In North America, a designer in the United States typically earns between $60,000 and $95,000 USD annually, with Canadian counterparts seeing $55,000 to $85,000 CAD ($40,000-$62,000 USD). These figures often include comprehensive benefits like health insurance and retirement plans.
Europe presents diverse salary landscapes. Germany, a manufacturing powerhouse, offers €50,000 to €80,000 ($54,000-$87,000 USD), often with robust social security and generous vacation. The UK ranges from £35,000 to £55,000 ($44,000-$69,000 USD). Eastern European countries like Poland offer lower nominal salaries, around €25,000 to €40,000 ($27,000-$44,000 USD), but purchasing power can be comparable due to lower living costs.
Asia-Pacific markets also differ. Australia’s salaries range from AUD 70,000 to AUD 100,000 ($46,000-$66,000 USD). Japan offers JPY 5,000,000 to JPY 8,000,000 ($33,000-$53,000 USD), while South Korea is similar. China’s compensation is highly variable, often starting lower but increasing significantly with experience and for specialized skills. These regions often have less extensive benefit packages than North America or Western Europe.
Latin America sees lower nominal wages, with Mexico offering MXN 250,000 to MXN 500,000 ($14,000-$28,000 USD). Cost of living adjustments are crucial for understanding true compensation. Experience and specialized software proficiency significantly impact earning potential globally. Tax implications and net take-home pay differ greatly, with some European countries having higher tax burdens but more social benefits.
Remote Work
International remote work for Tool and Die Designers is possible but often limited to specific project phases. Conceptual design, CAD modeling, and simulation can be performed remotely. However, the role frequently requires on-site collaboration with manufacturing teams for prototyping, testing, and troubleshooting physical tools.
Legal and tax implications for international remote work require careful consideration. Designers must understand their tax residency and potential double taxation. Some countries, like Portugal or Estonia, offer digital nomad visas, which can facilitate long-term remote stays. Employers may have specific policies on global hiring, impacting where a designer can be officially employed.
Time zone differences can challenge international team collaboration, especially when working with manufacturing facilities. Companies hiring remotely in this field often seek designers who can manage asynchronous communication effectively. Salary expectations for remote roles may vary, with some employers adjusting pay based on the designer's location and its cost of living.
Practical considerations include a stable internet connection, appropriate design software licenses, and a secure workspace. While fully remote global opportunities are less common than in software development, hybrid models or project-based remote contracts are increasing, allowing designers flexibility during initial design phases.
Visa & Immigration
Tool and Die Designers often qualify for skilled worker visas in many industrialized nations. Popular destinations include Germany, Canada, Australia, and the United States, all with established manufacturing sectors. These countries typically require proof of relevant education, professional experience, and sometimes, a job offer from a local employer.
Education credential recognition is crucial; designers need to ensure their diplomas and certifications meet the standards of the destination country. Professional licensing is generally not required for designers, but industry-specific certifications, such as those in CAD/CAM software (e.g., SolidWorks, AutoCAD), are highly valued. Visa timelines vary, ranging from a few months to over a year, depending on the country and visa type.
Common visa categories include employer-sponsored work permits or points-based immigration systems. Canada's Express Entry and Australia's Skilled Migration programs often list engineering and technical design roles as in-demand. Language requirements, such as English proficiency for Anglophone countries or basic German for Germany, are frequently part of the application process. Some countries offer faster processing for highly skilled workers in critical sectors.
Pathways to permanent residency or citizenship exist in many countries after several years of continuous skilled employment. Dependents, including spouses and children, can typically accompany the primary visa holder. Intracompany transfers are also an option for designers moving within multinational corporations. Researching specific country requirements is essential, as regulations can change.
2025 Market Reality for Tool and Die Designers
Understanding the current market realities for Tool and Die Designers is essential for career success. This field has seen significant evolution, particularly from 2023 to 2025, influenced by post-pandemic shifts in supply chains and the rapid integration of AI into design processes. Broader economic factors, such as industrial output and investment in new product development, directly impact job availability.
Market conditions for designers vary considerably by experience level, geographic region, and the size of the manufacturing firm. Entry-level roles face different dynamics than senior positions, and opportunities in, for example, automotive tooling differ from those in medical device manufacturing. This analysis provides an honest assessment to help designers strategically navigate today's landscape.
Current Challenges
Tool and Die Designers face significant competition, especially for entry-level roles. Automation and AI tools impact the demand for certain traditional design tasks, increasing productivity expectations for designers. Economic uncertainty causes some manufacturing sectors to delay investments in new tooling, directly affecting job availability.
A notable skill gap exists where employers seek designers proficient in advanced CAD/CAM software and simulation tools, but many candidates lack these specific, updated proficiencies. Job searches can extend for several months, particularly for roles requiring specialized industry experience.
Growth Opportunities
Despite challenges, strong demand persists for Tool and Die Designers specializing in complex, high-precision tooling. Industries like aerospace, defense, and medical device manufacturing continue to invest heavily in advanced manufacturing capabilities, creating consistent opportunities. Designers with expertise in designing for additive manufacturing (3D printing) or those proficient in simulating manufacturing processes (e.g., injection molding, stamping) are highly sought after.
Emerging roles often involve integrating AI-driven generative design tools to optimize part performance and manufacturability. Professionals who can leverage these technologies to reduce design iterations and improve efficiency gain a significant competitive edge. Underserved markets might include smaller, specialized fabrication shops that require custom tooling solutions but lack in-house advanced design capabilities, or regions with a growing need for localized manufacturing.
Developing expertise in specific materials, such as composites or advanced alloys, and their unique tooling requirements, also presents a distinct advantage. Strategic career moves involve upskilling in advanced simulation software, data-driven design, and understanding the full product lifecycle from concept to production. Focusing on sectors resilient to economic fluctuations, such as essential medical equipment or high-tech defense components, can provide more stable career paths.
Current Market Trends
The demand for Tool and Die Designers remains steady in specialized manufacturing sectors, especially where precision and custom tooling are critical. Hiring patterns show a strong preference for designers experienced with complex geometries and advanced materials. Industries like aerospace, medical devices, and electric vehicle component manufacturing are actively seeking skilled designers.
Recent industry changes emphasize digital integration. Companies increasingly adopt advanced CAD/CAM software, generative design tools, and simulation platforms. This shift means designers must not only conceptualize but also validate designs virtually, often before physical prototyping. The integration of AI in design optimization is beginning to influence workflows, automating repetitive design tasks and allowing designers to focus on innovation and problem-solving.
Economic conditions present a mixed picture. While some sectors show robust growth, others experience caution, leading to project delays. This affects the overall volume of new tooling projects. Employer requirements now frequently include proficiency in specific software suites like SolidWorks, CATIA, or NX, alongside a deep understanding of manufacturing processes and material science. There is a growing need for designers who can bridge the gap between design and additive manufacturing capabilities.
Salary trends for experienced Tool and Die Designers remain stable, reflecting the specialized skill set required. However, market saturation at the basic drafting level pushes salaries down for less experienced candidates. Geographic variations are significant; areas with strong manufacturing hubs, like the Midwest in the U.S. or automotive centers in Europe, exhibit higher demand. Remote work for these roles is less common due to the need for direct interaction with manufacturing processes and physical prototypes, though some conceptual design work can be performed remotely.
Emerging Specializations
Technological advancements and evolving manufacturing demands consistently reshape the landscape for tool and die designers. These shifts create novel specialization opportunities, particularly as industries adopt more sophisticated production methods and materials. Positioning oneself early in these emerging areas provides a significant advantage for career progression beyond 2025.
Specializing in cutting-edge fields often leads to premium compensation and accelerated career growth. These roles address critical industry needs that established specializations may not fully cover. While foundational tool and die design skills remain crucial, integrating new expertise allows designers to command higher value.
Emerging specializations typically take a few years to become mainstream and generate a substantial volume of job opportunities. Early adoption involves a balance of risk and reward; it requires investing in new skills before widespread demand. However, those who do so are well-placed to lead in future industry developments, securing roles at the forefront of innovation.
Understanding these strategic implications helps professionals make informed choices about their career trajectory. It is about anticipating where the industry is heading and aligning one's skills to meet those future demands effectively.
Additive Manufacturing Tooling Designer
Advanced Composites Tooling Specialist
Smart Tooling and Sensor Integration Designer
Micro-Tooling Designer
Sustainable Tool and Die Design Engineer
Pros & Cons of Being a Tool and Die Designer
Understanding both the advantages and challenges of a career is crucial before making a commitment. The experience in any field, including tool and die design, can vary significantly based on the company culture, the specific industry sector, and the individual's specialization within the role. Factors like the size of the company, the type of products manufactured, and the level of technological adoption all influence daily work life. Additionally, what one person considers a pro, another might view as a con, depending on their personal values, work style, and career aspirations. For instance, a fast-paced environment might be exciting for some, while stressful for others. These assessments aim to provide a realistic overview, helping aspiring designers set appropriate expectations for a career that evolves at different stages, from entry-level to senior positions.
Pros
- Tool and die designers enjoy strong job security due to the critical need for custom tooling in manufacturing across various industries, ensuring consistent demand for their specialized skills.
- The role offers significant intellectual stimulation, as designers are constantly solving complex engineering problems to create precise and efficient manufacturing tools and dies.
- Designers see tangible results of their work, as they transform concepts into physical tools that directly contribute to the production of consumer goods and industrial components.
- There are opportunities for continuous professional development through learning new software, advanced materials, and innovative manufacturing processes, keeping the work engaging and current.
- The specialized nature of the work often commands competitive salaries, reflecting the high level of skill and technical expertise required to design intricate and durable tools.
- Tool and die designers often collaborate with engineers, machinists, and production teams, providing a dynamic work environment with diverse interactions and shared problem-solving.
- The skills acquired are highly transferable within the manufacturing sector, allowing designers to work in various industries such as automotive, aerospace, medical devices, and consumer electronics.
Cons
- The work environment can sometimes be noisy and dusty due to proximity to manufacturing operations, which might not suit everyone's preference for a quiet office setting.
- There is a constant need for precision and attention to detail, as even minor errors in design can lead to costly manufacturing mistakes and project delays.
- The job often involves working with complex CAD/CAM software and specialized machinery, requiring continuous learning and adaptation to new technologies and design tools.
- Meeting tight production deadlines can lead to periods of high pressure and extended hours, especially when new products are being developed or existing tools need urgent modifications.
- Finding entry-level positions can be challenging, as many companies prefer candidates with direct experience in tool and die design or related manufacturing fields.
- The work can be physically demanding, requiring occasional visits to the shop floor to inspect tools, troubleshoot issues, or oversee testing, which involves standing and moving around heavy machinery.
- Career progression might be limited to senior design roles or management positions within a specific company, as the specialization can make transitioning to entirely different engineering fields more difficult without further education or retraining opportunities.
Frequently Asked Questions
Tool and Die Designers combine precision engineering with practical manufacturing knowledge. This role requires understanding complex machinery and material properties, leading to unique questions about specialized software, hands-on experience requirements, and the industry's future amidst automation trends.
What are the typical educational and experience requirements to become a Tool and Die Designer?
Becoming a Tool and Die Designer typically requires a combination of formal education and practical experience. Many professionals pursue an Associate's degree in Tool and Die Design, Mechanical Engineering Technology, or a related field. Some also complete apprenticeships that provide comprehensive on-the-job training, which can be highly valuable for developing hands-on skills.
How long does it realistically take to become a proficient Tool and Die Designer from a beginner level?
The timeline to become job-ready can vary significantly. An Associate's degree usually takes two years, while an apprenticeship can range from three to five years, combining classroom instruction with extensive practical work. If you are starting from scratch, expect a minimum of two to three years to acquire the necessary foundational knowledge and entry-level skills.
What specific software and technical skills are most critical for a Tool and Die Designer?
Tool and Die Designers work with specialized CAD/CAM software like SolidWorks, AutoCAD, CATIA, and Mastercam. Proficiency in these programs is crucial for creating detailed blueprints, 3D models, and machining instructions. Employers often look for candidates who can demonstrate hands-on experience with these industry-standard tools.
What are the typical salary expectations for an entry-level Tool and Die Designer, and how does it progress with experience?
Entry-level salaries for Tool and Die Designers can range from $45,000 to $60,000 annually, depending on location, company size, and specific responsibilities. With several years of experience and specialized skills, salaries can increase significantly, often reaching $70,000 to $90,000 or more for senior designers. Overtime opportunities might also affect overall earnings.
Is the job market for Tool and Die Designers growing, or is it being impacted by automation?
The job market for Tool and Die Designers remains stable, driven by the ongoing need for custom manufacturing and specialized tooling across various industries. While automation impacts some aspects of manufacturing, the demand for skilled designers who can create and optimize complex tools and dies persists. Companies consistently need experts to innovate and maintain production efficiency.
What is the typical work-life balance and work environment like for a Tool and Die Designer?
Work-life balance for Tool and Die Designers generally involves standard business hours, but project deadlines or urgent production needs can sometimes require extended hours. The work environment is typically in an office setting, often near a manufacturing floor, requiring attention to detail and occasional collaboration with machinists and engineers.
What are the potential career advancement opportunities for a Tool and Die Designer?
Career growth for Tool and Die Designers can lead to various advanced roles. You might specialize in specific types of tooling, move into project management, or transition into engineering or manufacturing management positions. Some designers also pursue roles in research and development, contributing to new material and manufacturing process innovations.
Related Careers
Explore similar roles that might align with your interests and skills:
Die Maker
A growing field with similar skill requirements and career progression opportunities.
Explore career guideTool Designer
A growing field with similar skill requirements and career progression opportunities.
Explore career guideTooling Engineer
A growing field with similar skill requirements and career progression opportunities.
Explore career guideDie Designer
A growing field with similar skill requirements and career progression opportunities.
Explore career guideTool and Die Engineer
A growing field with similar skill requirements and career progression opportunities.
Explore career guideAssess your Tool and Die Designer readiness
Understanding where you stand today is the first step toward your career goals. Our Career Coach helps identify skill gaps and create personalized plans.
Skills Gap Analysis
Get a detailed assessment of your current skills versus Tool and Die Designer requirements. Our AI Career Coach identifies specific areas for improvement with personalized recommendations.
See your skills gapCareer Readiness Assessment
Evaluate your overall readiness for Tool and Die Designer roles with our AI Career Coach. Receive personalized recommendations for education, projects, and experience to boost your competitiveness.
Assess your readinessLand your dream job with Himalayas Plus
Upgrade to unlock Himalayas' premium features and turbocharge your job search.
Himalayas
Himalayas Plus
Himalayas Max
Find your dream job
Sign up now and join over 100,000 remote workers who receive personalized job alerts, curated job matches, and more for free!
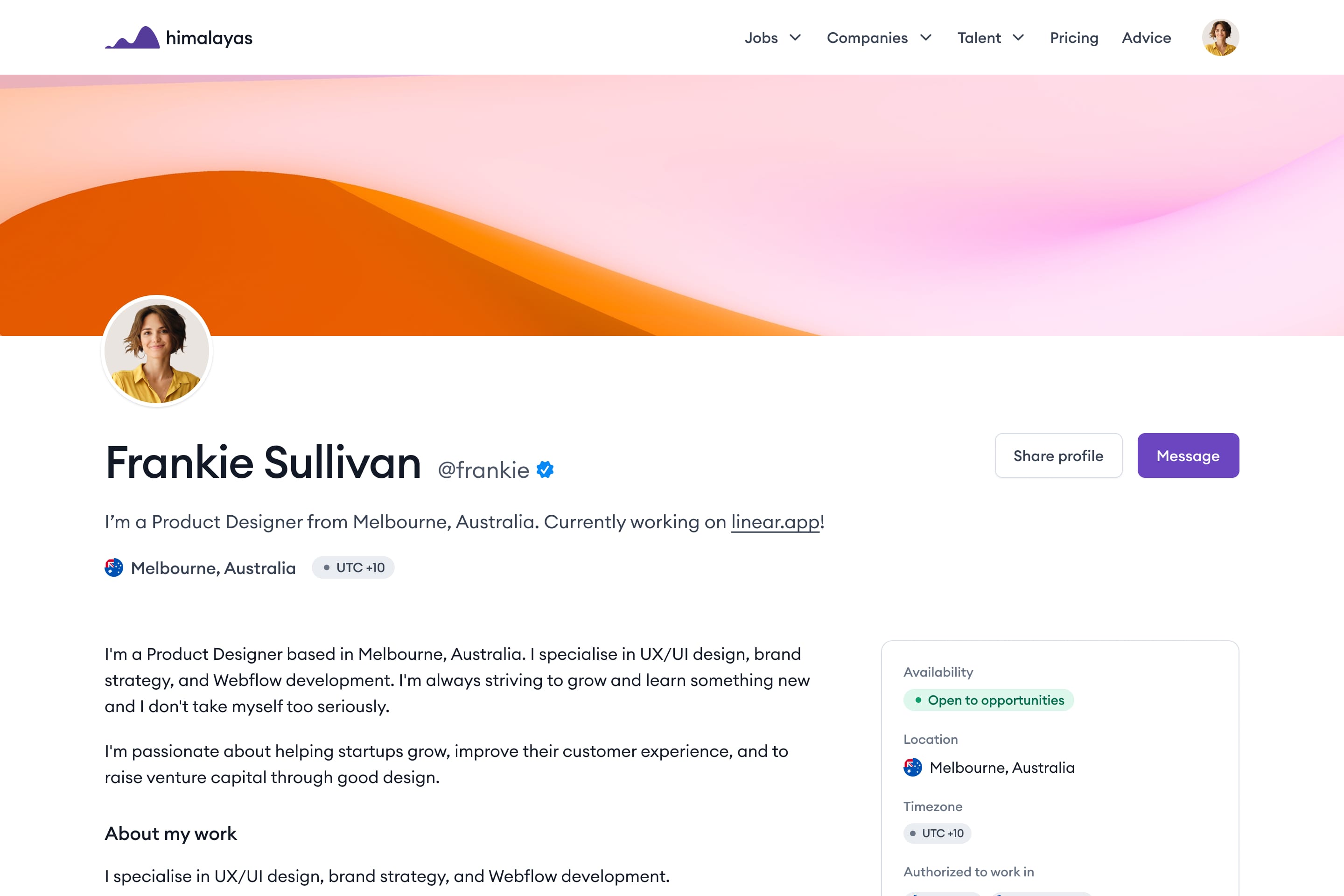