Complete Tool and Die Engineer Career Guide
Tool and Die Engineers are the unsung heroes of modern manufacturing, designing and creating the precision tooling that makes mass production possible. They translate product designs into the molds, dies, and fixtures essential for everything from automotive parts to medical devices, ensuring accuracy and efficiency. This critical role combines advanced engineering principles with hands-on fabrication skills, offering a stable and impactful career path in industries relying on highly precise component creation.
Key Facts & Statistics
Median Salary
$62,940 USD
(U.S. national median, BLS, May 2023)
Range: $40k - $85k+ USD
Growth Outlook
Annual Openings
≈1700
openings annually (BLS, 2022-2032)
Top Industries
Typical Education
Associate's degree in Tool and Die Technology or a related field; some positions may require a Bachelor's degree in Mechanical Engineering or Manufacturing Engineering, often combined with extensive on-the-job training or apprenticeship.
What is a Tool and Die Engineer?
A Tool and Die Engineer is a specialized mechanical engineer who designs, develops, and optimizes the precision tools, molds, dies, jigs, and fixtures essential for high-volume manufacturing processes. These engineers are the backbone of industries producing anything from automotive parts and consumer electronics to medical devices and plastic components. They translate product designs into tangible manufacturing solutions.
Unlike a general mechanical engineer who might design the product itself, a Tool and Die Engineer focuses specifically on the 'how' - creating the intricate machinery that enables mass production. They combine advanced engineering principles with practical knowledge of materials and manufacturing processes to ensure that products can be made efficiently, accurately, and cost-effectively. They differ from toolmakers, who are skilled craftspeople that build and repair tools; the engineer designs and validates the concepts, providing the blueprint for the toolmaker's work.
What does a Tool and Die Engineer do?
Key Responsibilities
- Design complex molds, dies, jigs, and fixtures using CAD/CAM software to meet product specifications and manufacturing requirements.
- Analyze part designs and material properties to determine the most effective tooling methods and identify potential manufacturing challenges.
- Oversee the fabrication and assembly of tools and dies, working closely with toolmakers and machinists to ensure precision and quality.
- Conduct thorough testing and validation of newly manufactured tools, making necessary adjustments and improvements to optimize performance.
- Develop and implement preventative maintenance programs for existing tooling to extend lifespan and minimize downtime.
- Troubleshoot and resolve issues related to tool performance, material flow, and product defects, often requiring on-the-spot adjustments.
- Collaborate with product design teams to provide DFM (Design for Manufacturability) input, ensuring that new products are feasible for tooling and production at an early stage of development.
Work Environment
Tool and Die Engineers typically work in manufacturing facilities, machine shops, or dedicated tooling departments. The environment often combines office work, where designs are created and analyzed, with shop floor presence, where they oversee fabrication and troubleshoot issues. Collaboration is frequent, working closely with toolmakers, machinists, production teams, and product designers. The pace can be fast, especially when responding to production line issues or urgent project deadlines. While primarily an on-site role, some larger companies may offer hybrid options for design-focused tasks. The work requires a strong attention to detail and a hands-on approach to problem-solving.
Tools & Technologies
Tool and Die Engineers rely heavily on advanced CAD/CAM software suites, such as SolidWorks, AutoCAD, CATIA, and Mastercam, for designing and simulating tooling. They also use CAE (Computer-Aided Engineering) tools for stress analysis and mold flow simulation to predict material behavior. Precision measurement instruments, including calipers, micrometers, CMMs (Coordinate Measuring Machines), and optical comparators, are essential for verifying tool dimensions and product quality. Knowledge of CNC machining centers, EDM (Electrical Discharge Machining) equipment, and various manual machining tools is crucial for understanding the fabrication process. Furthermore, they utilize enterprise resource planning (ERP) systems for project management and material tracking, and often work with specialized programming languages for automation and machine control.
Tool and Die Engineer Skills & Qualifications
A Tool and Die Engineer combines precision engineering principles with hands-on manufacturing expertise. This role focuses on designing, building, and maintaining the specialized tools, dies, jigs, and fixtures used in various manufacturing processes, particularly stamping, forging, and molding operations. Success in this field requires a deep understanding of materials science, mechanical design, and production methodologies.
Qualification requirements for Tool and Die Engineers vary significantly based on the industry, company size, and seniority level. Entry-level positions may accept candidates with an Associate's degree or vocational training coupled with practical experience, while senior roles often demand a Bachelor's degree in Mechanical Engineering or a related field. Practical experience, especially apprenticeships, holds substantial weight in this profession. Certifications in specific CAD/CAM software or specialized manufacturing processes, such as advanced stamping die design or injection mold design, significantly enhance a candidate's profile.
The skill landscape for Tool and Die Engineers constantly evolves with advancements in automation, additive manufacturing, and smart factory initiatives. Traditional machining skills remain fundamental, but proficiency in CAD/CAM software, simulation tools, and even basic programming for CNC machines becomes increasingly vital. Companies seek individuals who can integrate new technologies to optimize tool performance and manufacturing efficiency. The balance between theoretical knowledge and practical application is crucial; a strong portfolio demonstrating successful tool designs and problem-solving capabilities often outweighs extensive formal education alone. Misconceptions sometimes arise that this role is purely manual; however, it increasingly involves complex analytical and design work.
Education Requirements
Technical Skills
- CAD software proficiency (e.g., SolidWorks, AutoCAD, CATIA, Siemens NX) for 3D modeling and design
- CAM software operation (e.g., Mastercam, GibbsCAM) for generating CNC machine code
- Precision machining techniques (milling, turning, grinding, EDM) for tool fabrication
- Geometric Dimensioning and Tolerancing (GD&T) interpretation and application
- Materials science knowledge (metals, plastics, composites) and heat treatment processes
- Tool and die design principles (progressive dies, transfer dies, injection molds, stamping dies)
- CNC programming (G-code, M-code) and machine operation
- Press operation and setup knowledge (stamping presses, injection molding machines)
- Fixture and jig design for manufacturing processes
- Metrology and inspection techniques (CMM, optical comparators, micrometers)
- Failure analysis and root cause identification for tool and die components
- FEA (Finite Element Analysis) or simulation software for design validation and optimization
Soft Skills
- Problem Solving: Essential for diagnosing tool failures, optimizing designs, and developing innovative solutions to manufacturing challenges.
- Attention to Detail: Critical for ensuring precise measurements, tight tolerances, and flawless operation of complex tools and dies.
- Spatial Reasoning: Necessary for visualizing complex 3D designs, understanding material flow, and anticipating potential manufacturing issues.
- Communication: Important for collaborating with machinists, production teams, and product designers to ensure tool designs meet production needs and specifications.
- Adaptability: Valuable for integrating new technologies, adjusting to evolving manufacturing processes, and responding to design changes or production demands.
- Time Management: Key for prioritizing tasks, meeting project deadlines, and managing multiple tool design or repair projects concurrently.
- Continuous Learning: Vital for staying current with advancements in materials, manufacturing techniques, and software tools within the industry.
- Patience and Persistence: Required when troubleshooting complex tool issues or refining designs over multiple iterations to achieve optimal performance and longevity for the tool and die components.
How to Become a Tool and Die Engineer
Entering the Tool and Die Engineer field offers several pathways, from traditional apprenticeships to engineering degrees. A complete beginner might spend 3-5 years acquiring the necessary skills and certifications, while someone transitioning from a related manufacturing role could achieve entry in 1-2 years. The timeline depends heavily on prior experience and the chosen educational route.
Traditional entry often involves vocational training or an apprenticeship, providing hands-on experience alongside theoretical knowledge. Alternatively, a Mechanical Engineering or Manufacturing Engineering degree can lead to this role, especially in companies focused on advanced manufacturing and design. Geographic location also plays a role; regions with strong manufacturing bases, like the Midwest in the USA or industrial zones in Germany, will have more opportunities and established pathways.
Many believe a four-year engineering degree is essential, but practical skills gained through apprenticeships or associate degrees are equally valued, especially for hands-on roles. Companies often prioritize a strong understanding of machining, CAD/CAM, and material science, alongside problem-solving abilities. Building a portfolio of design projects or practical fabrication experience significantly enhances a candidate's appeal, often more so than academic credentials alone.
Step 1
Step 2
Step 3
Step 4
Step 5
Step 6
Education & Training Needed to Become a Tool and Die Engineer
The educational landscape for Tool and Die Engineers blends traditional academic learning with hands-on vocational training. Formal four-year bachelor's degrees in Mechanical Engineering or Manufacturing Engineering Technology provide a strong theoretical foundation, typically costing $40,000-$100,000+ and taking four years to complete. These programs emphasize design principles, material science, and manufacturing processes. They prepare engineers for complex problem-solving and R&D roles.
Alternatively, two-year associate's degrees in Tool and Die Making or Machine Tool Technology, often found at community colleges, offer a more direct path. These programs focus on practical skills like CAD/CAM, CNC machining, and precision measurement. They typically cost $5,000-$20,000 and take two years. Vocational schools and apprenticeships, ranging from 6 months to 4 years, provide intensive hands-on training with minimal upfront cost, often leading directly to employment. Employers highly value practical experience and a proven ability to work with precision machinery. These paths range from $0 (apprenticeship) to $15,000 (vocational certificate).
While formal degrees provide theoretical depth, practical experience gained through apprenticeships or on-the-job training is crucial for Tool and Die Engineers. Many employers prioritize candidates with a blend of theoretical knowledge and hands-on proficiency, especially in precision machining and CAD/CAM software. Continuous learning through industry certifications in areas like GD&T or specific software platforms is essential for staying current with evolving manufacturing technologies. The choice of educational path depends on career aspirations, with higher-level design and management roles often requiring a bachelor's degree, while hands-on production roles might favor vocational training and apprenticeships.
Tool and Die Engineer Salary & Outlook
Compensation for a Tool and Die Engineer varies significantly based on several factors. Geographic location plays a crucial role; areas with a high concentration of manufacturing, particularly in automotive or aerospace industries, typically offer higher salaries due to increased demand and cost of living. Conversely, regions with fewer specialized manufacturing operations may see lower pay scales.
Years of experience dramatically impact earning potential. Entry-level engineers command starting salaries, while those with specialized skills in areas like progressive dies, complex mold design, or advanced machining technologies can secure premium compensation. Total compensation extends beyond base salary to include performance bonuses, profit-sharing, and comprehensive benefits packages. These often encompass health insurance, retirement contributions like 401(k) matching, and allowances for continuous professional development.
Industry-specific trends also influence salaries. The automotive sector, for instance, often drives higher compensation due to the complexity and volume of tooling required. Company size can also matter, with larger corporations sometimes offering more structured pay scales and benefit programs. Remote work is less common for this hands-on role, but companies might offer relocation incentives for skilled professionals to specific manufacturing hubs. Salary negotiation leverage increases with proven expertise in optimizing production processes and reducing manufacturing costs, demonstrating a direct impact on profitability.
Salary by Experience Level
Level | US Median | US Average |
---|---|---|
Junior Tool and Die Engineer | $65k USD | $68k USD |
Tool and Die Engineer | $82k USD | $85k USD |
Senior Tool and Die Engineer | $102k USD | $105k USD |
Lead Tool and Die Engineer | $120k USD | $125k USD |
Tool and Die Engineering Manager | $140k USD | $145k USD |
Market Commentary
The job market for Tool and Die Engineers shows a stable demand, driven by the ongoing need for precision manufacturing across various industries. While some traditional manufacturing jobs have shifted, the specialized skill set of a Tool and Die Engineer remains critical for developing and maintaining the intricate tooling required for modern production lines. The Bureau of Labor Statistics projects a modest growth for industrial engineers, a category that often includes specialized roles like this, reflecting the continued importance of optimizing manufacturing processes.
Emerging opportunities lie in the adoption of advanced manufacturing technologies. This includes integrating additive manufacturing (3D printing) into tooling processes, utilizing simulation software for design validation, and leveraging automation. Engineers proficient in these areas, along with traditional machining and design principles, will find themselves in high demand. The supply of highly skilled Tool and Die Engineers can be tight, particularly for those with expertise in complex, high-precision tooling, creating a favorable market for experienced professionals.
Future-proofing this career involves continuous learning in areas like CAD/CAM software advancements, material science, and automation integration. While automation may change some aspects of the job, the core functions of design, problem-solving, and precision craftsmanship remain essential and are resistant to full automation. Geographic hotspots for these roles include the Midwest and Southeast United States, driven by automotive, aerospace, and general manufacturing sectors. The profession is generally stable, though economic downturns can temporarily slow new tooling projects.
Tool and Die Engineer Career Path
Career progression for a Tool and Die Engineer typically involves a deep specialization in manufacturing processes and materials science. Professionals advance by mastering complex tooling design, fabrication, and maintenance, moving from executing tasks to leading intricate projects and teams. This field offers distinct pathways: an individual contributor (IC) track focused on technical mastery and innovation, and a management track centered on leading engineering teams and operations.
Advancement speed depends on several factors, including an individual's performance, the complexity of projects undertaken, and the specific industry (e.g., automotive, aerospace, medical devices). Larger companies often provide more structured progression paths and opportunities for specialization, while smaller firms or startups might offer broader responsibilities earlier. Lateral moves can involve specializing in particular die types (e.g., progressive dies, transfer dies) or transitioning into related fields like manufacturing engineering or product design.
Continuous learning is critical, encompassing new materials, advanced machining techniques, and automation. Networking within the industry and seeking mentorship from experienced engineers significantly aids progression. Certifications in specific software (e.g., CAD/CAM) or manufacturing methodologies (e.g., Lean, Six Sigma) can also mark significant milestones. Some engineers pivot into consulting roles or specialized training positions, leveraging their deep technical expertise across various organizations.
Junior Tool and Die Engineer
0-2 yearsKey Focus Areas
Tool and Die Engineer
2-5 yearsKey Focus Areas
Senior Tool and Die Engineer
5-8 yearsKey Focus Areas
Lead Tool and Die Engineer
8-12 yearsKey Focus Areas
Tool and Die Engineering Manager
12+ yearsKey Focus Areas
Junior Tool and Die Engineer
0-2 yearsAssists senior engineers with tool and die design, fabrication, and maintenance tasks. Executes specific instructions for machining, assembly, and testing. Supports troubleshooting efforts under direct supervision. Responsibilities are primarily task-oriented with limited independent decision-making.
Key Focus Areas
Develop foundational knowledge in tool and die making principles, including blueprint reading, basic machining, and material properties. Focus on learning CAD software for design and simulation. Cultivate strong problem-solving skills and attention to detail. Begin understanding manufacturing process flows and quality control standards.
Tool and Die Engineer
2-5 yearsDesigns, develops, and optimizes various types of tools and dies, including progressive, forming, and stamping dies. Conducts detailed analysis of part specifications and material flow. Participates in prototyping and testing phases, identifying and resolving design flaws. Works with moderate autonomy on assigned projects.
Key Focus Areas
Master advanced CAD/CAM techniques for complex tool and die designs. Develop expertise in selecting appropriate materials and heat treatments for specific applications. Improve troubleshooting and root cause analysis skills for production issues. Begin understanding cost implications of design choices and manufacturing efficiency.
Senior Tool and Die Engineer
5-8 yearsLeads complex tool and die projects from concept to production, ensuring designs meet performance, cost, and timeline objectives. Provides technical leadership and guidance to junior engineers. Collaborates with cross-functional teams, including production, quality, and R&D. Makes independent technical decisions and validates design integrity.
Key Focus Areas
Acquire expertise in DFM (Design for Manufacturability) and DFA (Design for Assembly) principles. Develop strong project management skills, including planning, scheduling, and resource allocation. Mentor junior engineers and provide technical guidance. Focus on continuous process improvement and implementing Lean manufacturing principles.
Lead Tool and Die Engineer
8-12 yearsOversees multiple tool and die engineering projects, ensuring alignment with organizational goals and strategic objectives. Acts as a primary technical expert, providing high-level guidance and resolving critical engineering challenges. Drives continuous improvement initiatives across the tool and die department. Mentors and develops the technical capabilities of the engineering team.
Key Focus Areas
Develop strategic thinking regarding tooling investments and long-term manufacturing capabilities. Cultivate advanced leadership and team coordination skills. Focus on optimizing overall tooling operations for efficiency and innovation. Engage in industry best practices and emerging technologies like additive manufacturing for tooling.
Tool and Die Engineering Manager
12+ yearsManages a team of Tool and Die Engineers, overseeing their projects, professional development, and performance. Responsible for departmental budget, resource allocation, and strategic planning for tooling needs. Collaborates with senior leadership to integrate tooling strategies with overall manufacturing and product development plans. Drives departmental goals and ensures operational excellence.
Key Focus Areas
Master personnel management, budgeting, and departmental strategic planning. Develop strong communication and stakeholder management skills. Focus on fostering a culture of innovation, safety, and continuous improvement within the engineering team. Understand business development aspects related to tooling services.
Job Application Toolkit
Ace your application with our purpose-built resources:
Tool and Die Engineer Resume Examples
Proven layouts and keywords hiring managers scan for.
View examplesTool and Die Engineer Cover Letter Examples
Personalizable templates that showcase your impact.
View examplesTop Tool and Die Engineer Interview Questions
Practice with the questions asked most often.
View examplesTool and Die Engineer Job Description Template
Ready-to-use JD for recruiters and hiring teams.
View examplesGlobal Tool and Die Engineer Opportunities
Tool and Die Engineers are globally essential, designing and fabricating precision tools, dies, and molds for manufacturing across industries. Demand remains strong in industrialized nations like Germany, Japan, and the USA, driven by advanced manufacturing and automation needs. Regulatory differences impact design standards and safety protocols, requiring engineers to adapt to diverse international specifications. Professionals consider international roles for specialized projects, higher compensation, or exposure to cutting-edge technologies. Global mobility is aided by certifications in CAD/CAM software and lean manufacturing principles.
Global Salaries
Salaries for Tool and Die Engineers vary significantly by region. In North America, particularly the USA, an engineer can expect to earn between $70,000 and $110,000 USD annually. Canadian salaries typically range from $65,000 to $95,000 CAD (approximately $48,000-$70,000 USD). These figures reflect competitive markets with high manufacturing output.
European salaries show a wide range. In Germany, a leading manufacturing hub, engineers might earn €55,000 to €85,000 per year (around $60,000-$92,000 USD). The UK offers £40,000 to £65,000 (about $50,000-$82,000 USD). Cost of living adjustments are crucial; for instance, while German salaries appear higher, living costs in major cities can reduce purchasing power compared to some US regions.
Asia-Pacific markets present different compensation structures. In Japan, salaries for experienced engineers range from ¥6,000,000 to ¥9,000,000 annually (roughly $40,000-$60,000 USD), often complemented by robust benefits packages. Australia offers AUD 75,000 to AUD 110,000 (about $50,000-$73,000 USD). Latin American countries like Mexico, a growing manufacturing center, offer lower direct salaries, typically $25,000-$45,000 USD, but with significantly lower living expenses. Tax implications and social security contributions vary by country, affecting net take-home pay. Experience and specialized skills, such as advanced CNC programming or additive manufacturing knowledge, enhance international compensation.
Remote Work
Purely remote work for Tool and Die Engineers is limited due to the hands-on nature of the role, which requires physical presence in a workshop or factory. However, aspects like design, simulation, and project management can be performed remotely. Industry trends show a shift towards hybrid models, where engineers might spend part of their week on-site and part working from home.
Legal and tax implications of international remote work are complex. An engineer working remotely from a different country than their employer may face challenges regarding permanent establishment rules and dual taxation. Time zone differences also impact international team collaboration, requiring flexible working hours.
Digital nomad opportunities are rare for this profession as most tasks are tied to specific machinery. Some companies might hire for remote design roles, but these are often project-based or require periodic on-site visits. Employers are generally cautious about global hiring for roles demanding physical presence, impacting salary expectations. Equipment needs include high-performance CAD workstations and specialized software licenses.
Visa & Immigration
Tool and Die Engineers often qualify for skilled worker visas in many countries, including Canada (Express Entry), Australia (Skilled Migration Program), and Germany (EU Blue Card). Requirements typically include a relevant engineering degree, professional experience, and sometimes a job offer. Popular destinations like the USA require an H-1B visa, which is quota-limited and lottery-based. Credential recognition is vital; engineers may need to have their degrees assessed by local professional bodies.
Visa timelines vary, from a few months for intra-company transfers to over a year for some skilled migration pathways. English language proficiency tests like IELTS or TOEFL are often required for English-speaking countries. German and other European countries may require basic language proficiency for integration. Pathways to permanent residency exist, often after several years of continuous skilled employment.
Some countries offer fast-track processing for highly skilled professionals in demand occupations. Family visas for spouses and dependents are generally available once the primary applicant secures their work visa. Professional licensing or registration might be required in some jurisdictions before commencing work, adding a layer to the immigration process.
2025 Market Reality for Tool and Die Engineers
Understanding the current market realities for Tool and Die Engineers is essential for career longevity and strategic planning. The landscape for this specialization has transformed significantly from 2023 to 2025, moving beyond traditional craftsmanship. Post-pandemic supply chain recalibrations and the rapid integration of AI into design processes have redefined the core competencies employers seek.
Broader economic factors, including manufacturing output and investment in new product development, directly influence job availability. Market realities also vary by experience level; entry-level roles often require more foundational technical skills, while senior positions demand advanced design and problem-solving expertise. Geographic location and the size of manufacturing operations further dictate specific opportunities. This analysis provides an honest assessment of current conditions, helping you navigate the evolving demands of this engineering field.
Current Challenges
Tool and Die Engineers face significant hurdles. Automation and advanced CNC machinery reduce demand for manual intervention, increasing competition for fewer roles. Economic slowdowns impact manufacturing sectors directly, leading to fewer new projects and hiring freezes. Companies seek engineers with advanced CAD/CAM and simulation software proficiency, creating a skill gap for those focused solely on traditional methods. Finding roles requiring a blend of hands-on and high-tech skills can take six to twelve months in a cautious hiring environment.
Growth Opportunities
Despite challenges, significant opportunities exist for Tool and Die Engineers. Strong demand persists in industries requiring high-precision, low-volume, or custom tooling, such as medical device manufacturing, specialized automotive components, and aerospace. These sectors value engineers who can innovate and optimize complex designs for specific applications.
Emerging specializations in high demand include engineers proficient in DfAM (Design for Additive Manufacturing) for tooling, those skilled in integrating AI-driven generative design into mold and die creation, and experts in multi-axis CNC programming and automation cell integration. Engineers who combine traditional toolmaking knowledge with advanced digital simulation and data analytics skills possess a significant competitive advantage. Underserved markets often appear in regions with growing advanced manufacturing hubs that lack a deep pool of digitally proficient tooling engineers. Strategic career moves involve upskilling in simulation software, automation systems, and understanding new materials. Investing in certifications for specific CAD/CAM platforms or additive manufacturing processes can open new doors. The market correction currently underway, while slowing some hiring, also emphasizes efficiency and innovation, creating roles for engineers who can deliver these outcomes.
Current Market Trends
Hiring for Tool and Die Engineers shows a nuanced pattern as of 2025. While demand for traditional, hands-on die makers has softened due to increased automation, there is a strong, unmet need for engineers who can design, optimize, and troubleshoot complex tooling systems using advanced software. The integration of generative AI in design and simulation tools is rapidly changing project timelines and increasing efficiency expectations. This shift means fewer roles for those without strong digital skills.
Economic conditions, marked by cautious investment in new manufacturing lines, influence the number of new tool development projects. This leads to a stable but not rapidly expanding job market in many regions. However, sectors like aerospace, medical devices, and custom high-precision manufacturing continue to seek skilled engineers. These industries often require specialized, low-volume tooling, where human expertise in design and problem-solving remains critical.
Employer requirements now heavily emphasize proficiency in CAD/CAM software (e.g., SolidWorks, CATIA, Mastercam), FEA simulation, and an understanding of additive manufacturing processes for prototyping and short-run tooling. Salaries for engineers with these digital skills and a strong understanding of manufacturing principles are trending upward, reflecting their value. Conversely, market saturation exists for candidates whose skills are limited to conventional machining and design without modern software capabilities. Geographic variations are notable; states with strong automotive, aerospace, or advanced manufacturing bases (e.g., Michigan, Ohio, California, Texas) show stronger market activity. Remote work is rare for this role, given the need for direct interaction with physical tools and machinery.
Emerging Specializations
The field of tool and die engineering is undergoing significant transformation, driven by advancements in materials science, automation, and digital manufacturing. These technological shifts are creating new specialization opportunities that demand forward-thinking skills. Professionals who proactively position themselves in these emerging areas can secure a competitive edge, ensuring career advancement and often commanding premium compensation in 2025 and beyond.
Early adoption of these specialized skills allows engineers to shape the future of manufacturing, rather than merely reacting to changes. While established specializations remain vital, focusing on emerging niches can unlock greater growth potential and innovative roles. Many cutting-edge areas, initially niche, become mainstream within five to seven years, creating a surge in demand for early experts.
Investing in these nascent fields involves a calculated risk, as not all emerging trends achieve widespread adoption. However, the potential for significant career trajectory acceleration and becoming an industry leader often outweighs this risk. Strategic upskilling in these areas provides a strong foundation for long-term career resilience and success.
AI-Driven Tooling Optimization Engineer
The integration of artificial intelligence and machine learning into the design and manufacturing of tools and dies is rapidly expanding. This specialization focuses on developing AI-driven algorithms for optimizing die design, predicting material behavior during stamping or molding, and automating quality control processes. It involves leveraging data analytics to enhance precision, reduce material waste, and significantly shorten development cycles for complex tooling.
Additive Manufacturing for Tooling Specialist
Additive manufacturing, particularly industrial 3D printing of metal components, is revolutionizing tool and die production. This specialization involves designing and optimizing tools, dies, and molds specifically for additive manufacturing processes, such as DMLS or SLM. It focuses on creating intricate internal cooling channels, lightweight structures, and rapid prototyping of complex geometries that are impossible with traditional subtractive methods, leading to improved tool performance and lifespan.
Sustainable Tooling Design Engineer
The demand for sustainable manufacturing practices is driving a need for tool and die engineers who can specialize in designing environmentally conscious tooling. This involves optimizing die designs to reduce material consumption, extend tool life through advanced coatings, and enable easier recycling or refurbishment of tooling components. It also includes developing tooling for manufacturing products from sustainable or recycled materials, minimizing environmental impact throughout the product lifecycle.
Robotics and Automation Integration Engineer
Advanced robotics are increasingly integrated into tool and die shops for automated material handling, precision machining, and assembly of complex dies. This specialization focuses on programming, calibrating, and integrating robotic systems for tasks like automated die polishing, precision assembly of die components, or robotic inspection. It requires a deep understanding of robot kinematics and collaborative robot applications within a manufacturing environment.
Industrial Cybersecurity for Tooling Systems Specialist
As manufacturing processes become more interconnected, cybersecurity for industrial control systems (ICS) and operational technology (OT) in tool and die shops is critical. This specialization involves securing the digital infrastructure of tool and die production, including CNC machines, robotic cells, and networked design systems, from cyber threats. It focuses on implementing robust security protocols, identifying vulnerabilities, and ensuring the integrity of intellectual property and operational data.
Pros & Cons of Being a Tool and Die Engineer
Making informed career decisions requires a clear understanding of both the benefits and challenges associated with a specific profession. A career's experience can vary significantly based on the company culture, the industry sector, the specific specialization within the field, and an individual's personal preferences and personality.
Pros and cons may also shift at different career stages; for instance, the demands of an entry-level position might differ greatly from those of a senior leadership role. What one person considers a significant advantage, another might view as a drawback, underscoring the subjective nature of career satisfaction. This assessment provides an honest, balanced perspective on the tool and die engineer role, helping readers set realistic expectations.
Pros
- Tool and die engineers enjoy strong job security and consistent demand across various manufacturing sectors, as their specialized skills are essential for producing precision components and products.
- The role offers significant intellectual stimulation through problem-solving and design, as engineers constantly optimize tool performance, troubleshoot production issues, and innovate manufacturing processes.
- Tool and die engineers often experience a tangible sense of accomplishment by seeing their designs and repairs directly impact product quality and production efficiency.
- The specialized nature of tool and die engineering commands competitive salaries, reflecting the high level of skill, precision, and expertise required for the role.
- There are clear paths for career advancement, allowing engineers to move into senior engineering roles, management positions, or specialize further in areas like automation or advanced materials.
- The work provides a blend of hands-on technical work and theoretical design, appealing to individuals who enjoy both practical application and analytical challenges.
- Tool and die engineers develop highly transferable skills in precision machining, material science, CAD/CAM software, and problem-solving, which are valuable across many industries beyond traditional manufacturing.
Cons
- The work environment often involves exposure to loud machinery, metal dust, and various lubricants or coolants, which requires strict adherence to safety protocols and can be physically demanding.
- Troubleshooting complex tooling issues can be mentally exhausting and time-consuming, especially when production lines are halted and pressure to resolve problems quickly is high.
- The role often requires irregular hours, including overtime, weekend work, or being on-call, particularly during urgent repairs, new tool try-outs, or critical production periods.
- Tool and die engineers must continuously update their skills to keep pace with advancements in materials, machining technologies like CNC, and CAD/CAM software, requiring ongoing learning outside of work hours.
- While stable, the demand for tool and die engineers can fluctuate with manufacturing cycles and economic downturns, potentially affecting job availability in some regions or industries.
- Entry into the field often requires significant hands-on experience in machining or apprenticeship programs, which can be a longer and more specialized path compared to some other engineering disciplines.
- The work can be repetitive at times, especially when performing routine maintenance, making minor adjustments, or producing large batches of similar components, which may not appeal to those seeking constant novelty and innovation.
Frequently Asked Questions
Tool and Die Engineers face unique challenges in precision manufacturing, bridging design with hands-on production. This section addresses crucial questions about entering this specialized field, from required technical skills and educational paths to career growth and the evolving impact of automation on the role.
What educational background or certifications are essential to become a Tool and Die Engineer?
Becoming a Tool and Die Engineer typically requires a combination of formal education and practical experience. Many start with an associate's degree in tool and die making, manufacturing engineering technology, or a related field. Some pursue a bachelor's degree in mechanical engineering or manufacturing engineering, which provides a stronger theoretical foundation for design and analysis. Apprenticeships are also a common and highly effective path, offering hands-on training alongside experienced professionals.
Can I become a Tool and Die Engineer without a four-year engineering degree?
While a bachelor's degree provides a strong foundation in engineering principles, it is not always strictly necessary. Many successful Tool and Die Engineers gain their expertise through associate's degrees combined with extensive on-the-job training or structured apprenticeships. Practical skills, problem-solving ability, and experience with CAD/CAM software and various machining processes often outweigh formal degree requirements for entry-level positions. However, a bachelor's degree can open doors to more advanced design or management roles.
How long does it typically take to become a proficient Tool and Die Engineer from scratch?
The timeline to become a fully qualified Tool and Die Engineer varies significantly. An associate's degree takes about two years, followed by several years of practical experience. Apprenticeships typically last 3-5 years, providing comprehensive hands-on training and theoretical knowledge. If pursuing a bachelor's degree, it is a four-year program, often complemented by internships to gain practical exposure. Overall, expect a commitment of 4-7 years to achieve professional competency in this field.
What is the job security and future outlook for Tool and Die Engineers, especially with increasing automation?
Job security for Tool and Die Engineers remains strong due to the critical need for custom tooling in manufacturing. While some production processes automate, the design, maintenance, and complex problem-solving involved in tool and die work still require human expertise. The demand for skilled professionals who can create intricate molds, dies, and fixtures for various industries, including automotive, aerospace, and medical devices, ensures consistent opportunities. Embracing new technologies like additive manufacturing and advanced CAD/CAM further enhances job stability.
What is the typical work-life balance like for a Tool and Die Engineer?
The work-life balance for Tool and Die Engineers can vary depending on the industry and specific company. While a standard 40-hour work week is common, project deadlines or urgent repairs can sometimes require extended hours, especially during peak production periods or critical breakdowns. However, many roles offer predictable schedules once projects are stable. The hands-on nature of the work means less remote flexibility compared to purely design-based engineering roles, but it provides a tangible connection to the manufacturing process.
What are the common career progression paths for a Tool and Die Engineer?
Career advancement for Tool and Die Engineers can lead to several specialized or leadership roles. Many progress to become senior tool designers, lead engineers, or project managers overseeing tooling development. Opportunities also exist in quality control, process improvement, or research and development. Some experienced professionals transition into teaching or consulting roles, sharing their specialized knowledge. Continuous learning in new materials, machining technologies, and CAD/CAM software is crucial for career progression.
What are the typical salary expectations for a Tool and Die Engineer at different experience levels?
The salary for Tool and Die Engineers depends on experience, location, industry, and specific skill sets. Entry-level positions typically start in the mid-$40,000s to low-$60,000s annually. With several years of experience and specialized skills, salaries can range from $60,000 to $90,000. Highly experienced or lead engineers, particularly in specialized sectors like aerospace or medical, can earn upwards of $100,000 or more. Benefits packages often include health insurance, retirement plans, and paid time off.
Related Careers
Explore similar roles that might align with your interests and skills:
Tool Designer
A growing field with similar skill requirements and career progression opportunities.
Explore career guideTooling Engineer
A growing field with similar skill requirements and career progression opportunities.
Explore career guideDie Designer
A growing field with similar skill requirements and career progression opportunities.
Explore career guideTool Engineer
A growing field with similar skill requirements and career progression opportunities.
Explore career guideTool and Die Designer
A growing field with similar skill requirements and career progression opportunities.
Explore career guideAssess your Tool and Die Engineer readiness
Understanding where you stand today is the first step toward your career goals. Our Career Coach helps identify skill gaps and create personalized plans.
Skills Gap Analysis
Get a detailed assessment of your current skills versus Tool and Die Engineer requirements. Our AI Career Coach identifies specific areas for improvement with personalized recommendations.
See your skills gapCareer Readiness Assessment
Evaluate your overall readiness for Tool and Die Engineer roles with our AI Career Coach. Receive personalized recommendations for education, projects, and experience to boost your competitiveness.
Assess your readinessSimple pricing, powerful features
Upgrade to Himalayas Plus and turbocharge your job search.
Himalayas
Himalayas Plus
Himalayas Max
Find your dream job
Sign up now and join over 100,000 remote workers who receive personalized job alerts, curated job matches, and more for free!
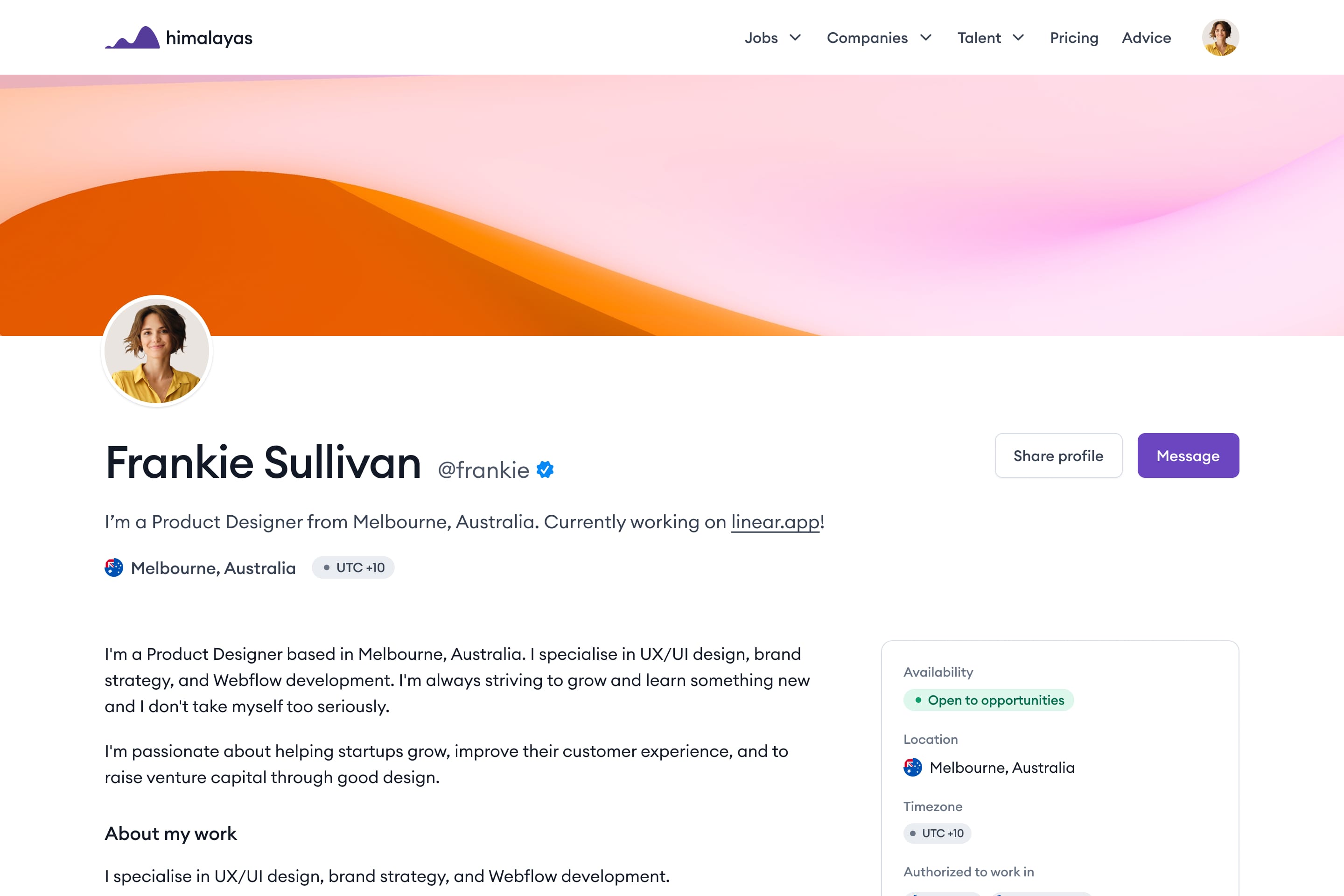