Complete Die Designer Career Guide
Die Designers are the masterminds behind the precision tools that shape everything from automotive parts to electronic components. They translate complex product designs into manufacturing blueprints, creating the specialized dies and molds essential for mass production. This role demands a blend of engineering acumen and artistic vision, offering a rewarding path for those who thrive on problem-solving and seeing their creations come to life in tangible products.
Key Facts & Statistics
Median Salary
$64,280 USD
(U.S. national median, BLS, May 2023)
Range: $40k - $90k+ USD (BLS, May 2023)
Growth Outlook
0%
as fast as average (BLS, 2022-2032)
Annual Openings
≈1,300
openings annually (BLS, 2022-2032)
Top Industries
Typical Education
High school diploma or equivalent, often followed by an apprenticeship or associate's degree in tool and die making or a related field.
What is a Die Designer?
A Die Designer specializes in creating the precise tools, known as dies, used to cut, shape, or form materials, primarily metals, in manufacturing processes such as stamping, forging, or extrusion. They translate product blueprints into detailed designs for these complex tools, ensuring that the dies can produce components accurately, efficiently, and cost-effectively.
This role differs significantly from a general Mechanical Designer or Product Designer. While a Product Designer focuses on the end product's form and function, and a Mechanical Designer might design various machinery components, a Die Designer's expertise is specifically in the intricate mechanics of the die itself, understanding material behavior under stress, and optimizing designs for high-volume production and longevity. They are crucial for bridging the gap between product concept and mass production.
What does a Die Designer do?
Key Responsibilities
- Interpret product specifications and engineering drawings to conceptualize optimal die designs for manufacturing components.
- Develop detailed 2D and 3D CAD models of dies, including individual die components, using specialized design software.
- Perform stress analysis and simulation on die designs to predict material flow, potential defects, and ensure structural integrity.
- Collaborate with manufacturing engineers and toolmakers to refine designs, ensuring manufacturability and adherence to production capabilities.
- Create comprehensive documentation, including blueprints, material specifications, and assembly instructions for die fabrication.
- Participate in design reviews, presenting concepts and incorporating feedback to optimize die performance and cost-efficiency.
- Troubleshoot and analyze issues with existing dies, implementing design modifications to improve operational efficiency or product quality.
Work Environment
Die Designers typically work in office settings, often within manufacturing plants or engineering firms. Their work is largely computer-based, involving extensive time at a workstation. The role requires significant collaboration with manufacturing teams, tool and die makers, and product engineers, often involving meetings and shop floor visits to observe die performance.
The pace can vary; some projects involve long-term design cycles, while others require rapid problem-solving for production issues. Deadlines are common, especially when supporting new product launches or resolving manufacturing bottlenecks. While primarily an individual contributor in design tasks, the role is highly interconnected with production schedules and quality control.
Tools & Technologies
Die Designers regularly use advanced CAD/CAM software suites such as SolidWorks, AutoCAD, CATIA, and NX for creating precise 2D and 3D models. They also utilize specialized simulation software like AutoForm, LS-DYNA, or DEFORM to analyze material deformation and predict stamping process outcomes. Knowledge of CAM software is important for preparing designs for CNC machining.
Beyond design tools, they work with product lifecycle management (PLM) systems for document control and versioning. Understanding of GD&T (Geometric Dimensioning and Tolerancing) is critical for specifying part tolerances. Basic measurement tools and access to prototyping equipment may also be part of their daily environment.
Die Designer Skills & Qualifications
A Die Designer crafts the intricate blueprints for tools that shape metal or other materials. This role demands a unique blend of engineering principles, material science knowledge, and practical manufacturing insight. Qualification priorities vary significantly based on the industry, company size, and the complexity of the dies being designed.
For entry-level positions, a strong foundation in CAD software and mechanical design principles is crucial. As designers advance, practical experience on the shop floor, understanding of stamping presses, and expertise in simulation software become increasingly important. Larger companies or those in aerospace and automotive sectors often prefer candidates with formal engineering degrees, while smaller custom shops may value extensive hands-on experience and a strong portfolio. Certifications in specific CAD/CAM software or specialized tooling design can significantly enhance a candidate's profile, sometimes even serving as an alternative pathway to a degree.
The skill landscape for Die Designers is evolving with the adoption of advanced simulation tools, generative design, and automation. Designers must continuously update their knowledge of new materials, manufacturing processes, and software advancements. The balance between theoretical knowledge and practical application is critical; a designer must understand not just how to draw a die, but how it will perform under real-world conditions. This role requires precision, attention to detail, and a deep understanding of manufacturing tolerances.
Education Requirements
Technical Skills
- 3D CAD software proficiency (e.g., SolidWorks, Siemens NX, CATIA, AutoCAD Inventor)
- 2D CAD drafting and dimensioning standards (GD&T)
- Die kinematics and material flow analysis
- Press mechanics and tonnage calculation
- Tool steel selection and heat treatment principles
- Sheet metal forming processes (bending, drawing, piercing, blanking)
- Progressive die design principles and strip layout optimization
- Fixture and jig design
- Stamping simulation software (e.g., AutoForm, LS-DYNA, Pam-Stamp)
- Tolerance stack-up analysis
- Manufacturing process knowledge (CNC machining, EDM, grinding)
- Tooling cost estimation and optimization
Soft Skills
- Problem-solving: Die designers frequently encounter complex challenges related to material flow, part ejection, and structural integrity, requiring innovative solutions.
- Attention to detail: Precision is paramount in die design; even minor errors can lead to costly manufacturing defects and production delays.
- Spatial reasoning: The ability to visualize complex 3D structures and their interaction with materials and machinery is fundamental to effective design.
- Communication: Clear communication with toolmakers, machinists, and production teams is essential to ensure designs are accurately interpreted and implemented.
- Adaptability: Designers must adapt to new materials, evolving manufacturing processes, and changes in project specifications or client requirements.
- Time management: Efficiently managing multiple design projects, meeting deadlines, and prioritizing tasks are crucial for timely product development.
- Collaboration: Working effectively with cross-functional teams, including engineers, manufacturing personnel, and quality control, ensures optimal die performance.
- Critical thinking: Evaluating design choices, predicting potential failure modes, and optimizing for manufacturability and cost efficiency requires strong analytical skills and sound judgment, especially when dealing with complex progressive dies or transfer dies where sequencing is critical and material properties need to be considered.
How to Become a Die Designer
Breaking into die design involves a blend of technical education and practical experience, with various entry points depending on your background. Traditional paths often include vocational training or an associate's degree in mechanical design or engineering technology. Some individuals transition from skilled trades like tool and die making, bringing invaluable hands-on experience, while others enter through a bachelor's degree in mechanical engineering, focusing on design principles and materials science.
Timeline expectations vary; a complete beginner might spend 2-4 years on education and another 1-2 years in an entry-level or apprentice role to gain proficiency. Career changers with transferable skills, such as drafting or CAD experience, may accelerate this by 1-2 years. The hiring landscape also shifts; larger manufacturing hubs or specialized industries like automotive and aerospace offer more opportunities. Smaller companies or regional shops might prioritize practical experience over formal degrees.
A common misconception is that die design is purely theoretical; it heavily relies on understanding manufacturing processes and material behavior. Networking within the manufacturing community, attending industry trade shows, and seeking mentorship from experienced designers are crucial. Building a portfolio of design projects, even conceptual ones, demonstrates your problem-solving abilities and understanding of tooling principles, often outweighing a lack of direct experience for entry-level roles.
Develop foundational knowledge in mechanical design and manufacturing processes. Pursue an Associate's Degree in Mechanical Design, Engineering Technology, or complete a vocational program in tool and die making. This foundational education provides crucial understanding of materials, mechanics, and drafting standards, typically taking 1-2 years.
Master Computer-Aided Design (CAD) software relevant to die design. Become proficient in tools like SolidWorks, Inventor, or CATIA, which are industry standards for creating and analyzing die designs. Complete online courses, workshops, or certifications to build a strong portfolio of 3D models and assemblies, focusing on part design and tooling components.
Gain practical experience through internships or entry-level manufacturing roles. Seek opportunities as a design intern, junior drafter, or even a machine shop assistant to understand the manufacturing floor, material properties, and machining limitations firsthand. This practical insight is invaluable for designing tools that are both effective and manufacturable, typically requiring 6-12 months.
Build a portfolio showcasing your die design projects and problem-solving skills. Include 3-5 detailed projects, such as stamping dies, forming dies, or injection molds, even if they are conceptual or academic. Document your design process, material choices, and any simulations or analyses performed to demonstrate your technical understanding and attention to detail.
Network with professionals in the manufacturing and tooling industry. Attend local manufacturing trade shows, join professional organizations like SME (Society of Manufacturing Engineers), and connect with experienced die designers on LinkedIn. Informational interviews can provide insights into industry trends and open doors to potential mentorships or job opportunities.
Prepare for job applications and technical interviews by refining your resume and practicing design challenges. Tailor your resume to highlight your CAD proficiency, design projects, and any relevant manufacturing experience. Be ready to discuss your design choices, problem-solving methodologies, and understanding of manufacturing constraints during interviews, potentially including a CAD skills test.
Step 1
Develop foundational knowledge in mechanical design and manufacturing processes. Pursue an Associate's Degree in Mechanical Design, Engineering Technology, or complete a vocational program in tool and die making. This foundational education provides crucial understanding of materials, mechanics, and drafting standards, typically taking 1-2 years.
Step 2
Master Computer-Aided Design (CAD) software relevant to die design. Become proficient in tools like SolidWorks, Inventor, or CATIA, which are industry standards for creating and analyzing die designs. Complete online courses, workshops, or certifications to build a strong portfolio of 3D models and assemblies, focusing on part design and tooling components.
Step 3
Gain practical experience through internships or entry-level manufacturing roles. Seek opportunities as a design intern, junior drafter, or even a machine shop assistant to understand the manufacturing floor, material properties, and machining limitations firsthand. This practical insight is invaluable for designing tools that are both effective and manufacturable, typically requiring 6-12 months.
Step 4
Build a portfolio showcasing your die design projects and problem-solving skills. Include 3-5 detailed projects, such as stamping dies, forming dies, or injection molds, even if they are conceptual or academic. Document your design process, material choices, and any simulations or analyses performed to demonstrate your technical understanding and attention to detail.
Step 5
Network with professionals in the manufacturing and tooling industry. Attend local manufacturing trade shows, join professional organizations like SME (Society of Manufacturing Engineers), and connect with experienced die designers on LinkedIn. Informational interviews can provide insights into industry trends and open doors to potential mentorships or job opportunities.
Step 6
Prepare for job applications and technical interviews by refining your resume and practicing design challenges. Tailor your resume to highlight your CAD proficiency, design projects, and any relevant manufacturing experience. Be ready to discuss your design choices, problem-solving methodologies, and understanding of manufacturing constraints during interviews, potentially including a CAD skills test.
Education & Training Needed to Become a Die Designer
Becoming a Die Designer involves a blend of theoretical knowledge and practical application, with several educational pathways available. Formal degree programs, such as a Bachelor's in Mechanical Engineering or Manufacturing Engineering Technology, provide a strong theoretical foundation in materials science, CAD/CAM, and mechanical principles. These 4-year degrees typically cost between $40,000 and $120,000+, depending on the institution, and are often preferred for senior or R&D focused die design roles. Graduates from these programs usually spend 1-2 years in junior design roles before advancing.
Alternative paths include associate degrees in Tool & Die Design or Drafting, which are often 2-year programs costing $10,000-$30,000. These programs focus more directly on design software and manufacturing processes. Vocational schools and specialized certification programs, sometimes lasting 6-18 months and costing $3,000-$15,000, offer intensive training in specific CAD/CAM software and die types. Many employers value a combination of formal education and hands-on experience, often gained through apprenticeships or entry-level positions where mentorship is available. Continuous learning is vital in this field, as new materials, manufacturing techniques, and design software emerge regularly.
Market perception varies; larger corporations often favor candidates with bachelor's degrees, while smaller custom shops may prioritize practical experience and a strong portfolio. Self-study, through online courses and tutorials, can supplement formal education but rarely replaces it entirely for this role due to the need for complex problem-solving and industry-specific knowledge. The cost-benefit analysis favors a structured program that includes practical application and exposure to industry-standard software. Professional certifications in specific CAD software, like SolidWorks or CATIA, significantly enhance a designer's resume. The educational needs also depend on the type of die design, whether it's stamping, forging, casting, or plastic injection, each requiring specialized knowledge.
Die Designer Salary & Outlook
Die Designer compensation varies significantly based on several factors, reflecting the specialized skills and critical nature of the role within manufacturing. Geographic location plays a major role; areas with a high concentration of automotive, aerospace, or heavy machinery industries often offer higher wages due to demand and cost of living. For instance, salaries in Michigan or Ohio, key manufacturing hubs, typically exceed those in regions with less industrial presence. International markets also present variations, though figures here are benchmarked against USD.
Years of experience and specific expertise in progressive dies, transfer dies, or complex tooling designs dramatically influence earning potential. Designers proficient in advanced CAD/CAM software, simulation tools, and lean manufacturing principles command premium compensation. Total compensation packages extend beyond base salary to include performance bonuses tied to project completion or efficiency improvements, health benefits, and retirement plans. Some companies may offer profit-sharing or professional development allowances for certifications in areas like GD&T or specific software suites.
Industry-specific trends, such as the shift towards electric vehicle manufacturing or advanced materials, drive salary growth for designers with relevant expertise. Larger companies or those with highly complex product lines often offer more competitive salaries and benefits compared to smaller shops. Negotiating leverage comes from a proven track record of successful die designs, problem-solving capabilities, and the ability to reduce material waste or production time. While remote work is less common for hands-on design roles, some conceptual design or simulation tasks may offer location flexibility, potentially impacting geographic arbitrage opportunities for specific skill sets.
Salary by Experience Level
Level | US Median | US Average |
---|---|---|
Junior Die Designer | $62k USD | $65k USD |
Die Designer | $75k USD | $78k USD |
Senior Die Designer | $92k USD | $95k USD |
Lead Die Designer | $105k USD | $110k USD |
Tooling Engineer | $115k USD | $118k USD |
Die Design Manager | $130k USD | $135k USD |
Market Commentary
The job market for Die Designers shows a stable outlook, driven by the continuous need for new tooling in manufacturing sectors like automotive, aerospace, and consumer goods. The U.S. Bureau of Labor Statistics projects consistent demand for industrial engineers and related occupations, which includes die designers, though specific projections for this niche are not isolated. Growth is particularly strong in industries adopting advanced manufacturing techniques and automation. The push towards electric vehicles and lightweight materials necessitates constant innovation in die design, creating new opportunities for specialists in these areas.
Emerging opportunities for Die Designers include roles focused on additive manufacturing tooling, smart dies with integrated sensors, and designs optimized for robotic handling. The increasing integration of AI and machine learning in design optimization and simulation software is evolving the role, requiring designers to adapt to new digital tools. This shift emphasizes the need for continuous learning in areas like generative design and digital twin technology. The supply of highly skilled Die Designers is often tight, especially for those proficient in complex multi-stage progressive dies, creating a favorable market for experienced professionals.
While some manufacturing jobs face automation threats, the creative and problem-solving aspects of die design are resistant to full automation, ensuring long-term viability. However, designers must embrace new software and simulation tools to remain competitive. Geographic hotspots for Die Designers include established manufacturing regions in the Midwest and Southeast U.S., where large-scale production facilities are concentrated. The cyclical nature of manufacturing industries means demand can fluctuate with economic conditions, though the foundational need for new product development provides a degree of recession resistance for skilled designers.
Die Designer Career Path
Career progression for a Die Designer typically follows a well-defined path, emphasizing technical mastery, problem-solving, and eventually, leadership. Professionals advance through increasing complexity in design challenges and greater responsibility for project outcomes. An individual contributor (IC) track focuses on deep technical specialization and complex design work, while a management track shifts towards overseeing design teams and strategic planning.
Advancement speed depends on several factors, including an individual's performance, the willingness to specialize in specific die types (e.g., progressive, transfer, line dies), and the size and type of manufacturing company. Larger corporations may offer more structured advancement paths, while smaller shops might provide broader exposure but less formal progression. Lateral moves can involve specializing in different materials, manufacturing processes, or transitioning into related roles like manufacturing engineering or quality assurance.
Continuous learning is crucial for Die Designers. Staying updated on new software, materials, and manufacturing technologies directly impacts career growth. Networking within the tooling industry, participating in professional organizations, and seeking mentorship from experienced designers or engineers also accelerate progression and open doors to new opportunities. Achieving certifications in CAD/CAM software or specific manufacturing processes marks significant milestones.
Junior Die Designer
0-2 yearsAssists senior designers with drafting, detailing, and minor design modifications for simpler dies. Primarily focuses on learning and executing tasks under direct supervision. Checks existing drawings for accuracy and contributes to documentation. Does not typically make independent design decisions.
Key Focus Areas
Develop foundational CAD skills, understand material properties, and learn manufacturing processes. Focus on drafting standards, basic die components, and safety protocols. Begin to grasp the relationship between die design and stamping press capabilities. Seek guidance from senior designers consistently.
Die Designer
2-5 yearsDesigns components and assemblies for moderately complex dies, including progressive and transfer dies. Works with engineers to integrate design requirements and specifications. Creates detailed drawings and bills of material. Provides input on design feasibility and manufacturability, with some independent decision-making on design details.
Key Focus Areas
Master advanced CAD techniques, including surface modeling and assembly design. Develop strong problem-solving skills for common die design challenges. Understand tool steel selection, heat treatment, and wear considerations. Improve communication with manufacturing and production teams.
Senior Die Designer
5-8 yearsLeads the design of highly complex and critical dies, often involving innovative solutions or new manufacturing processes. Responsible for entire die design projects from concept through production support. Collaborates extensively with product design, manufacturing, and quality teams. Makes significant design decisions with considerable autonomy.
Key Focus Areas
Specialize in complex die types or materials, such as high-strength steels or aluminum. Develop expertise in simulation software for formability analysis. Enhance project management skills, including scheduling and resource allocation. Mentor junior designers and review their work for quality and adherence to standards.
Lead Die Designer
8-12 yearsOversees a team of Die Designers, providing technical guidance, design review, and project allocation. Ensures designs meet project timelines, budget constraints, and quality standards. Acts as the primary technical expert for complex design challenges. Participates in strategic planning related to tooling development and innovation.
Key Focus Areas
Develop strong leadership and team coordination abilities. Focus on optimizing design workflows, implementing best practices, and standardizing design processes. Understand cost analysis related to tooling and design for manufacturing efficiency. Cultivate strong stakeholder management and negotiation skills.
Tooling Engineer
10-15 years total experience, with 2-5 years in a lead design roleWorks across the entire tooling lifecycle, from design and development to manufacturing, implementation, and maintenance. Optimizes tooling processes for efficiency, cost reduction, and quality improvement. Troubleshoots production issues related to tooling and machinery. May manage specific tooling programs or lead continuous improvement initiatives.
Key Focus Areas
Acquire deep knowledge of manufacturing processes beyond die design, including machining, assembly, and testing. Focus on process optimization, lean manufacturing principles, and automation integration. Develop strong analytical skills for root cause analysis and continuous improvement. Understand overall factory operations and production flow.
Die Design Manager
12-18 years total experience, with 3-6 years in a lead or engineering roleManages the entire die design department, including budget, personnel, and strategic direction. Responsible for departmental goals, technology adoption, and innovation. Collaborates with executive leadership on long-term tooling strategy and capital investment. Represents the design function in cross-functional leadership meetings.
Key Focus Areas
Develop strategic leadership, financial management, and business development skills. Focus on talent management, team building, and performance evaluation. Understand market trends, competitive analysis, and long-term technology roadmaps for tooling. Cultivate executive presence and strong cross-functional communication.
Junior Die Designer
0-2 yearsAssists senior designers with drafting, detailing, and minor design modifications for simpler dies. Primarily focuses on learning and executing tasks under direct supervision. Checks existing drawings for accuracy and contributes to documentation. Does not typically make independent design decisions.
Key Focus Areas
Develop foundational CAD skills, understand material properties, and learn manufacturing processes. Focus on drafting standards, basic die components, and safety protocols. Begin to grasp the relationship between die design and stamping press capabilities. Seek guidance from senior designers consistently.
Die Designer
2-5 yearsDesigns components and assemblies for moderately complex dies, including progressive and transfer dies. Works with engineers to integrate design requirements and specifications. Creates detailed drawings and bills of material. Provides input on design feasibility and manufacturability, with some independent decision-making on design details.
Key Focus Areas
Master advanced CAD techniques, including surface modeling and assembly design. Develop strong problem-solving skills for common die design challenges. Understand tool steel selection, heat treatment, and wear considerations. Improve communication with manufacturing and production teams.
Senior Die Designer
5-8 yearsLeads the design of highly complex and critical dies, often involving innovative solutions or new manufacturing processes. Responsible for entire die design projects from concept through production support. Collaborates extensively with product design, manufacturing, and quality teams. Makes significant design decisions with considerable autonomy.
Key Focus Areas
Specialize in complex die types or materials, such as high-strength steels or aluminum. Develop expertise in simulation software for formability analysis. Enhance project management skills, including scheduling and resource allocation. Mentor junior designers and review their work for quality and adherence to standards.
Lead Die Designer
8-12 yearsOversees a team of Die Designers, providing technical guidance, design review, and project allocation. Ensures designs meet project timelines, budget constraints, and quality standards. Acts as the primary technical expert for complex design challenges. Participates in strategic planning related to tooling development and innovation.
Key Focus Areas
Develop strong leadership and team coordination abilities. Focus on optimizing design workflows, implementing best practices, and standardizing design processes. Understand cost analysis related to tooling and design for manufacturing efficiency. Cultivate strong stakeholder management and negotiation skills.
Tooling Engineer
10-15 years total experience, with 2-5 years in a lead design roleWorks across the entire tooling lifecycle, from design and development to manufacturing, implementation, and maintenance. Optimizes tooling processes for efficiency, cost reduction, and quality improvement. Troubleshoots production issues related to tooling and machinery. May manage specific tooling programs or lead continuous improvement initiatives.
Key Focus Areas
Acquire deep knowledge of manufacturing processes beyond die design, including machining, assembly, and testing. Focus on process optimization, lean manufacturing principles, and automation integration. Develop strong analytical skills for root cause analysis and continuous improvement. Understand overall factory operations and production flow.
Die Design Manager
12-18 years total experience, with 3-6 years in a lead or engineering roleManages the entire die design department, including budget, personnel, and strategic direction. Responsible for departmental goals, technology adoption, and innovation. Collaborates with executive leadership on long-term tooling strategy and capital investment. Represents the design function in cross-functional leadership meetings.
Key Focus Areas
Develop strategic leadership, financial management, and business development skills. Focus on talent management, team building, and performance evaluation. Understand market trends, competitive analysis, and long-term technology roadmaps for tooling. Cultivate executive presence and strong cross-functional communication.
Job Application Toolkit
Ace your application with our purpose-built resources:
Global Die Designer Opportunities
Die Designers translate product specifications into precise manufacturing tools. This profession sees consistent global demand, particularly in automotive, aerospace, and consumer goods industries. International job market trends for 2025 show growth in Asia and Central Europe for skilled designers. Cultural differences impact design aesthetics, while regulatory standards vary for tooling safety and material specifications. International opportunities offer diverse project experiences and exposure to advanced manufacturing technologies. Certifications like Six Sigma or specific CAD software proficiencies enhance global mobility.
Global Salaries
Salaries for Die Designers vary significantly across global markets. In North America, a Die Designer can expect to earn between $60,000 and $95,000 USD annually. For instance, in the US, salaries average around $75,000 USD, while in Canada, they range from CAD 65,000 to CAD 90,000 ($48,000 - $67,000 USD). These figures reflect higher purchasing power in many US regions due to lower living costs compared to major European cities.
In Europe, salaries typically range from €40,000 to €70,000 ($43,000 - $75,000 USD). Germany, a manufacturing hub, offers €50,000 to €75,000 (around $54,000 - $81,000 USD), while in the UK, it is £35,000 to £55,000 ($44,000 - $69,000 USD). Scandinavian countries might offer similar nominal wages but with higher tax burdens, affecting take-home pay. Benefits packages in Europe often include more generous vacation time and comprehensive public healthcare.
Asia-Pacific markets present diverse compensation. In South Korea, Die Designers can earn KRW 45,000,000 to KRW 70,000,000 ($33,000 - $51,000 USD), while in Japan, it is JPY 5,000,000 to JPY 8,000,000 ($32,000 - $51,000 USD). China's industrial centers offer RMB 180,000 to RMB 350,000 ($25,000 - $48,000 USD). While nominal salaries may seem lower, the cost of living in many Asian cities is also considerably less, stretching purchasing power further. Experience and specialized software skills directly influence compensation globally.
Remote Work
International remote work for Die Designers is possible but often limited due to the collaborative and often hands-on nature of the role. Some design phases, like conceptualization and CAD modeling, can be done remotely. However, final adjustments and testing often require on-site presence or close coordination with manufacturing teams. Industry trends show an increase in hybrid models for this role.
Legal and tax implications for international remote work are complex. Designers must understand their tax residency and potential double taxation agreements. Time zone differences require flexible working hours for effective international team collaboration. Digital nomad visas are emerging in countries like Portugal and Estonia, offering pathways for remote professionals, but specific Die Designer roles might not fully qualify due to occasional on-site needs.
Employer policies on international remote work vary significantly; some global manufacturers have robust remote infrastructure. Remote work can impact salary expectations, with some companies adjusting pay based on the employee's location and local cost of living. Platforms like Upwork or specialized engineering job boards sometimes list freelance die design projects, but full-time international remote roles are less common for this specific profession.
Visa & Immigration
Die Designers seeking international work typically apply for skilled worker visas. Popular destinations include Germany, Canada, and Australia due to their robust manufacturing sectors and points-based immigration systems. Requirements for these visas often include a recognized engineering or design qualification, relevant work experience, and a job offer from an employer in the destination country.
Credential recognition is crucial; applicants may need their educational qualifications assessed by official bodies in the target country. Professional licensing is generally not required for Die Designers but may be for related engineering roles. The typical visa timeline ranges from 3 to 12 months, depending on the country and visa type, with application processes involving online submissions, document verification, and interviews.
Some countries, like Canada and Australia, offer pathways to permanent residency for skilled workers after a few years of employment. Language requirements vary; English proficiency tests (IELTS, TOEFL) are common for Anglophone countries, while German language skills are beneficial for Germany. Family visas allow spouses and dependents to accompany the primary applicant, often with work or study rights. Specific fast-track programs for manufacturing specialists are rare, but general skilled occupation lists may include this role.
2025 Market Reality for Die Designers
Understanding current market conditions is crucial for Die Designers to navigate career paths effectively. The landscape for this specialization has evolved significantly since 2023, influenced by post-pandemic supply chain adjustments and the accelerating integration of AI into design and manufacturing.
Broader economic factors, such as industrial output and investment in new product development, directly shape demand for die design expertise. Market realities vary based on experience level, with senior designers finding more stability, and by geographic region, concentrating opportunities where manufacturing thrives. Company size also plays a role; smaller shops might seek versatile designers, while larger corporations need specialists. This analysis provides an honest assessment of these dynamics.
Current Challenges
Die Designers face significant competition, especially for roles requiring traditional drafting skills. Automation and AI tools, while boosting productivity, also raise expectations for designers to handle more complex projects faster, potentially increasing pressure. Economic slowdowns directly impact manufacturing, leading to fewer new die projects and extended job search timelines, sometimes up to six months.
Growth Opportunities
Despite challenges, strong demand exists for Die Designers specializing in additive manufacturing and advanced composite tooling. Emerging roles focus on optimizing designs for 3D printing and integrating smart manufacturing concepts, requiring a blend of traditional design principles with digital fabrication expertise.
Professionals who master generative design tools and AI-driven optimization software gain a significant competitive advantage. Underserved markets include niche industries requiring highly customized, low-volume production, or regions with a resurgence in specialized manufacturing. Expertise in materials science, particularly in lightweight alloys and advanced polymers, also opens doors.
Strategic career moves might involve transitioning into roles focused on R&D for new manufacturing processes or consulting for automation integration. The aerospace, medical device, and renewable energy sectors remain strong, consistently seeking innovative die design solutions. Investing in certifications for specific CAD/CAM platforms or advanced manufacturing techniques provides a clear path to higher-demand roles.
Current Market Trends
Hiring for Die Designers in 2025 shows a split market. Demand remains steady for highly specialized roles in precision industries like aerospace and medical devices, where custom tooling is critical. However, roles focused on high-volume, standardized parts face reduced demand due to increased automation in manufacturing and the adoption of off-the-shelf tooling solutions.
The integration of generative AI and advanced CAD/CAM software is reshaping design workflows. Employers now prioritize designers proficient in simulation software, DFM (Design for Manufacturability), and FEA (Finite Element Analysis) over pure drafting skills. This shift means designers must understand material science and manufacturing processes deeply to optimize designs for automated production lines.
Salary trends for Die Designers are stable for experienced professionals with advanced software skills, but stagnant or declining for those with only traditional expertise. Market saturation is evident at entry levels, as fewer apprenticeship programs exist, and companies prefer experienced hires. Remote work is less common in this field due to the need for hands-on interaction with manufacturing processes and equipment, keeping opportunities largely tied to geographic manufacturing hubs.
Economic conditions, particularly in the automotive and general manufacturing sectors, directly influence job availability. Layoffs have occurred in companies streamlining operations or shifting production overseas. Seasonal hiring is minimal; demand typically aligns with capital expenditure cycles in manufacturing.
Emerging Specializations
The manufacturing landscape is undergoing a profound transformation, driven by advancements in materials science, automation, and digital technologies. This evolution creates exciting new specialization opportunities for Die Designers, moving beyond traditional approaches to embrace cutting-edge methodologies.
Early positioning in these emerging areas is crucial for career advancement from 2025 onwards. Professionals who proactively develop skills in these future-oriented niches will find themselves highly sought after, commanding premium compensation and experiencing accelerated career growth. While established die design specializations remain vital, future opportunities often lie at the intersection of traditional expertise and new technological frontiers.
Many emerging areas, particularly those tied to AI and advanced manufacturing, are rapidly moving from niche concepts to mainstream adoption. This shift will create significant job opportunities within the next 3-5 years. Specializing in these cutting-edge fields involves a balance of risk and reward; while initial demand might be lower, the long-term career trajectory and impact potential are substantial for those who commit to continuous learning and adaptation.
Additive Manufacturing-Optimized Die Design
This specialization focuses on designing dies optimized for additive manufacturing processes, particularly for creating prototypes or complex tooling inserts. It involves understanding how 3D printing affects material properties, thermal management within the die, and geometric constraints. Designers must integrate additive manufacturing's benefits, like conformal cooling channels, directly into the die design process, leading to improved part quality and cycle times.
Composite Material Die Design
This area involves designing dies for advanced composite materials, including carbon fiber, thermoplastics, and thermosets, which are increasingly used in aerospace, automotive, and consumer goods. It requires a deep understanding of anisotropic material behavior, fiber orientation, and curing processes. Designers must account for unique challenges like spring-back, delamination, and complex material flow during forming, ensuring structural integrity and performance.
AI-Driven Generative Die Design
This specialization applies artificial intelligence and machine learning algorithms to optimize die design parameters, predict material behavior, and automate design iterations. It moves beyond traditional simulation by using AI to analyze vast datasets from past designs and production runs, identifying optimal geometries, material choices, and process settings. This leads to faster design cycles, reduced material waste, and higher first-pass success rates for new dies.
Micro/Nano-Forming Die Design
This emerging field focuses on designing dies for micro-forming and nano-forming applications, producing components with features at the micron or nanometer scale. Such dies are critical for medical devices, microelectronics, and advanced sensors. It demands extreme precision, an understanding of size effects on material behavior, and the ability to work with advanced fabrication techniques for the die itself, such as LIGA or focused ion beam machining.
Smart Die Design with Integrated Sensors
This specialization involves designing dies that are integrated with real-time sensing and feedback systems to optimize the forming process on the fly. These 'smart dies' can monitor parameters like temperature, pressure, and strain during production, adjusting settings to prevent defects and ensure consistent part quality. It requires an understanding of sensor technology, data acquisition, and control systems, alongside traditional die design principles.
Pros & Cons of Being a Die Designer
Understanding the advantages and challenges of any career is crucial before committing. The experience of a die designer, for instance, can vary significantly depending on the company's size, the industry it serves, and the specific types of products being manufactured. Factors such as company culture, the level of automation, and individual personality can also influence how one perceives these aspects.
Some pros might be cons for others; for example, a fast-paced environment might energize one designer while overwhelming another. These dynamics can also shift throughout a career, with early-stage challenges potentially becoming mid-career strengths. This assessment offers an honest look at the realistic benefits and genuine difficulties inherent in a die designer role, helping you set appropriate expectations.
Pros
- Die designers engage in complex problem-solving daily, translating product specifications into intricate tooling designs. This provides constant intellectual stimulation and a sense of accomplishment when a challenging design is successfully implemented.
- There is a strong demand for skilled die designers across various manufacturing sectors, including automotive, aerospace, and consumer goods, leading to good job security and diverse employment opportunities.
- The role offers competitive salaries, especially for experienced professionals with specialized knowledge in complex progressive dies or advanced materials. This earning potential reflects the specialized skills required.
- Die designers work at the intersection of engineering and manufacturing, seeing their conceptual designs come to life on the production floor. This tangible outcome provides a high level of job satisfaction and a direct impact on product quality.
- The profession allows for continuous skill development in CAD/CAM software, material science, and manufacturing processes. This keeps the work engaging and ensures designers remain valuable assets in an evolving industry.
- Many die designers work standard day shifts, providing a predictable work schedule that supports a good work-life balance, although project deadlines can occasionally require extended hours.
Cons
- The work environment can be physically demanding, often requiring prolonged standing, bending, and lifting of heavy die components or tools, which can lead to fatigue or strain over time.
- Die designers frequently face tight deadlines, especially when new products are being launched or production issues arise, leading to periods of high pressure and potential overtime to meet schedules.
- The role requires continuous learning and adaptation to new materials, manufacturing processes, and software technologies. Staying current demands ongoing professional development outside of regular work hours.
- Errors in die design can be costly, leading to significant material waste, production delays, and potential damage to machinery. This places a high degree of responsibility and stress on the designer.
- Career progression within die design can sometimes be limited to senior designer or lead roles, and moving into management often requires acquiring additional business or project management skills.
- Finding entry-level positions can be challenging without prior hands-on experience in tool and die making or a strong portfolio demonstrating design proficiency, as many employers prefer seasoned professionals.
Frequently Asked Questions
Die Designers face unique challenges in translating complex product specifications into precise manufacturing tools. This section addresses the most common questions about entering this specialized field, from mastering CAD software and material science to understanding the job market and career progression.
What educational background or certifications do I need to become a Die Designer?
Becoming a Die Designer typically requires a combination of formal education and practical experience. Many successful designers hold an associate's or bachelor's degree in mechanical engineering, manufacturing engineering, or a related field. Vocational training in tool and die making or specialized CAD courses can also provide a strong foundation. Hands-on experience with machining and metalworking is highly beneficial.
How long does it take to become proficient enough to work as a Die Designer?
The timeline to become job-ready as an entry-level Die Designer varies. If you're starting with a relevant degree, it might take 1-2 years of internships or junior roles to gain practical experience. Without a degree, vocational programs can last 1-3 years, followed by an apprenticeship which can extend for another 3-5 years. The key is gaining proficiency in specialized CAD software and understanding manufacturing processes.
What are the typical salary expectations for an entry-level Die Designer versus an experienced one?
Entry-level Die Designers can expect a starting salary that varies by region, industry, and company size, typically ranging from $45,000 to $60,000 annually. With 5-10 years of experience and specialized skills, salaries can increase significantly, often reaching $70,000 to $90,000 or more. Factors like expertise in complex tooling or niche materials greatly influence earning potential.
What does the typical work-life balance look like for a Die Designer, and is remote work common?
The work-life balance for Die Designers is generally stable, often involving standard weekday hours. However, project deadlines can sometimes require extended hours, especially during critical design phases or when troubleshooting issues. The role is primarily office-based, focused on computer-aided design, though some roles may involve time on the manufacturing floor for collaboration or problem-solving.
Is the Die Designer role secure in the long term, considering advancements in automation and manufacturing technology?
Job security for Die Designers is generally strong because their specialized skills are crucial for manufacturing industries. While automation impacts some aspects of manufacturing, the creative and problem-solving elements of die design still require human expertise. Demand remains consistent in sectors like automotive, aerospace, and consumer goods manufacturing, which rely heavily on custom tooling.
What are the typical career growth opportunities and advancement paths for a Die Designer?
Career growth for a Die Designer often involves specializing in complex tooling, advanced materials, or specific manufacturing processes. You can progress into lead designer roles, engineering management, or project management positions. Some designers transition into consulting, technical sales, or R&D roles. Continuous learning in new design software and manufacturing techniques is essential for advancement.
What are the biggest challenges or frustrations that Die Designers commonly face in their day-to-day work?
The most significant challenge for Die Designers is balancing design precision with manufacturing feasibility and cost-effectiveness. You must create designs that are not only accurate but also manufacturable efficiently and within budget. Staying updated with evolving materials, manufacturing techniques, and CAD software is another continuous challenge that requires ongoing professional development.
Related Careers
Explore similar roles that might align with your interests and skills:
Die Maker
A growing field with similar skill requirements and career progression opportunities.
Explore career guideTool Designer
A growing field with similar skill requirements and career progression opportunities.
Explore career guideTooling Engineer
A growing field with similar skill requirements and career progression opportunities.
Explore career guideTool and Die Designer
A growing field with similar skill requirements and career progression opportunities.
Explore career guideTool and Die Engineer
A growing field with similar skill requirements and career progression opportunities.
Explore career guideAssess your Die Designer readiness
Understanding where you stand today is the first step toward your career goals. Our Career Coach helps identify skill gaps and create personalized plans.
Skills Gap Analysis
Get a detailed assessment of your current skills versus Die Designer requirements. Our AI Career Coach identifies specific areas for improvement with personalized recommendations.
See your skills gapCareer Readiness Assessment
Evaluate your overall readiness for Die Designer roles with our AI Career Coach. Receive personalized recommendations for education, projects, and experience to boost your competitiveness.
Assess your readinessLand your dream job with Himalayas Plus
Upgrade to unlock Himalayas' premium features and turbocharge your job search.
Himalayas
Himalayas Plus
Himalayas Max
Find your dream job
Sign up now and join over 100,000 remote workers who receive personalized job alerts, curated job matches, and more for free!
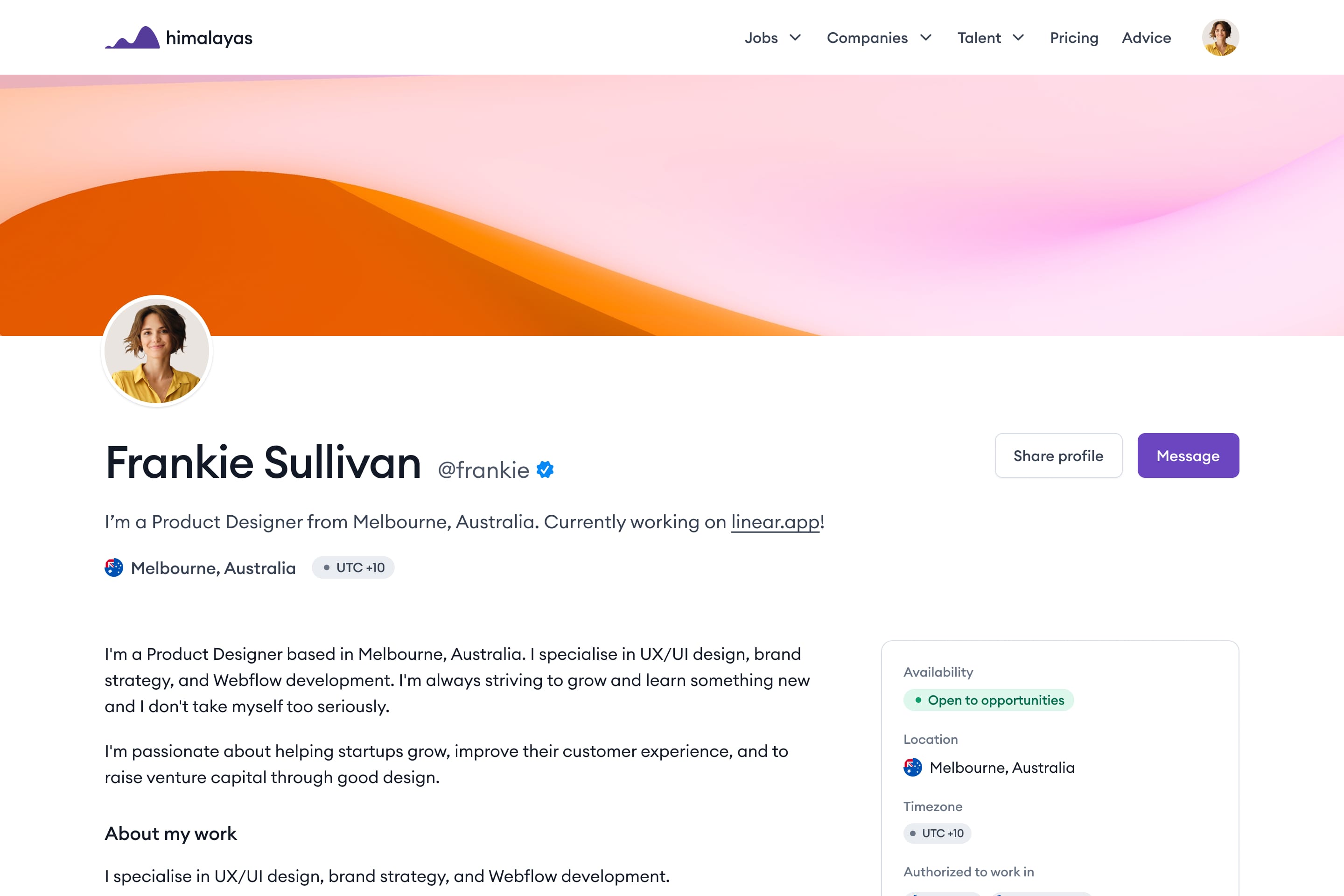