Complete Sub Arc Operator Career Guide
Sub Arc Operators are highly skilled welding professionals who specialize in Submerged Arc Welding (SAW), a high-deposition process crucial for heavy fabrication and structural integrity. You'll operate advanced machinery to create exceptionally strong, high-quality welds on thick materials, often for critical infrastructure and large-scale projects. This role demands precision and a deep understanding of metallurgy, offering a stable career path in industries vital to modern society.
Key Facts & Statistics
Median Salary
$48,290 USD
(U.S. national median for welders, cutters, solderers, and brazers, BLS May 2023)
Range: $36,000 - $70,000+ USD (Varies significantly by experience, industry, and location)
Growth Outlook
2%
slower than average (for welders, cutters, solderers, and brazers, BLS)
Annual Openings
≈44,300
openings annually (for welders, cutters, solderers, and brazers, BLS)
Top Industries
Typical Education
High school diploma or equivalent, often with vocational training or an associate's degree in welding technology; certifications (e.g., AWS Certified Welder) are highly valued
What is a Sub Arc Operator?
A Sub Arc Operator specializes in operating and maintaining Submerged Arc Welding (SAW) equipment, a highly efficient welding process used for joining thick sections of metal. Unlike manual welding, SAW uses a continuously fed consumable electrode and a blanket of granular flux that completely covers the arc, protecting it from atmospheric contamination and allowing for very high deposition rates and deep penetration.
This role differs significantly from a traditional manual welder or MIG/TIG welder. While manual welders control the arc directly, a Sub Arc Operator focuses on setting up, programming, and monitoring automated or semi-automated machinery. Their expertise lies in understanding complex weld parameters, material science, and machine mechanics to ensure consistent, high-quality welds on large-scale projects like pressure vessels, structural beams, and large pipes. They are essential for precision and efficiency in heavy fabrication industries where strong, defect-free welds are critical.
What does a Sub Arc Operator do?
Key Responsibilities
- Set up and adjust Submerged Arc Welding (SAW) equipment, including wire feed speed, voltage, amperage, and travel speed, according to specified welding procedures and blueprints.
- Load and position workpieces onto welding fixtures, ensuring proper alignment and fit-up to achieve accurate weld dimensions and quality.
- Monitor the welding process continuously, observing the arc, molten puddle, and overall weld bead for consistency and defects such as porosity or lack of fusion.
- Perform routine maintenance and troubleshooting on SAW machinery, including cleaning nozzles, replacing contact tips, and addressing minor mechanical or electrical issues.
- Interpret engineering drawings, welding symbols, and written specifications to determine the correct welding sequence, joint preparation, and material requirements.
- Operate overhead cranes or forklifts to move large and heavy metal components safely within the fabrication area.
- Conduct quality checks on completed welds using visual inspection, measuring tools, and sometimes non-destructive testing methods to ensure compliance with quality standards and customer specifications.
Work Environment
Sub Arc Operators typically work in manufacturing plants, fabrication shops, or heavy industrial settings. The environment is often noisy due to machinery and grinding operations, and can be dusty. Safety is paramount, requiring strict adherence to protocols and the use of personal protective equipment at all times.
The role involves standing for extended periods, lifting heavy components, and performing repetitive tasks. Collaboration occurs with other welders, fitters, and quality control personnel. While largely independent during the welding process, operators coordinate closely with team members on project timelines and material flow. Work schedules are usually full-time, often including shifts, and may involve overtime to meet production deadlines. The pace of work is steady and production-focused, requiring careful attention to detail.
Tools & Technologies
Sub Arc Operators primarily use specialized Submerged Arc Welding (SAW) machines, which can range from automated gantry systems to robotic welding cells. They work with various types of welding wire, such as solid or flux-cored, and granular flux materials, which protect the weld from atmospheric contamination.
Essential tools include calipers, micrometers, and other measuring devices for precise component fit-up and weld inspection. They also utilize grinding equipment for surface preparation, and material handling equipment like overhead cranes, jib cranes, and forklifts to position heavy workpieces. Knowledge of control panels for programming weld parameters and basic computer interfaces for data logging is also important. Safety equipment, including welding helmets, gloves, and flame-retardant clothing, is critical for daily operations.
Sub Arc Operator Skills & Qualifications
A Submerged Arc Welding (SAW) Operator possesses a specialized skill set focused on this high-deposition welding process. Qualifications for this role primarily emphasize practical experience and certifications over formal academic degrees. Companies prioritize candidates who demonstrate a strong understanding of SAW principles, machine setup, and troubleshooting.
Requirements vary significantly based on the industry and the complexity of the weldments. For instance, operators in heavy fabrication, such as pressure vessel or structural steel manufacturing, need extensive experience with thick materials and critical joint designs. In contrast, those in pipe manufacturing might focus more on consistent circumferential welding. Seniority often dictates the level of autonomy and problem-solving expected; entry-level operators might assist, while experienced operators manage complex setups and quality control.
Formal education, like a welding technology diploma, provides a strong foundation, but industry-recognized certifications, particularly from organizations like the American Welding Society (AWS), carry more weight. These certifications validate specific process knowledge and practical skills. Alternative pathways, such as vocational training, apprenticeships, or on-the-job training, are common and highly valued. The skill landscape is evolving with automation and robotics integrating into SAW operations, requiring operators to adapt to programming and monitoring automated systems alongside manual proficiency. Balancing deep expertise in SAW with an understanding of related processes and quality standards is crucial for career advancement.
Education Requirements
Technical Skills
- Submerged Arc Welding (SAW) process setup and operation (single and multi-wire)
- Parameter control (voltage, amperage, travel speed, wire feed speed) and adjustment
- Knowledge of SAW flux types and their applications (neutral, active, basic)
- Material preparation (joint fit-up, cleaning, preheating) for various base metals (carbon steel, stainless steel)
- Interpretation of welding blueprints, symbols, and specifications (AWS D1.1, ASME Section IX)
- Use of measuring tools (calipers, micrometers, gauges) for quality control and dimensional accuracy
- Troubleshooting common SAW defects (porosity, undercut, lack of fusion) and corrective actions
- Maintenance and calibration of SAW equipment (power sources, wire feeders, manipulators)
- Knowledge of welding metallurgy fundamentals and heat input effects on materials
- Post-weld inspection techniques (visual inspection, basic NDT principles like dye penetrant)
Soft Skills
- Attention to Detail: Critical for setting precise parameters, inspecting welds for defects, and ensuring adherence to specifications, which directly impacts weld quality and structural integrity.
- Problem-Solving: Essential for diagnosing issues with equipment, materials, or weld quality, and implementing effective corrective actions to maintain production efficiency and product standards.
- Mechanical Aptitude: Important for understanding and operating complex SAW machinery, performing routine maintenance, and making necessary adjustments to achieve optimal weld results.
- Safety Consciousness: Paramount for adhering to strict safety protocols, handling hazardous materials, and operating heavy machinery to prevent accidents and ensure a safe working environment.
- Team Collaboration: Often works within a fabrication team, requiring effective communication and coordination with fitters, quality control inspectors, and supervisors to ensure smooth workflow and project completion.
- Adaptability: Necessary to adjust to changing production demands, material specifications, or equipment configurations, ensuring continuous productivity and quality output.
- Precision and Consistency: Crucial for maintaining tight tolerances and producing uniform welds over long runs, which is a hallmark of the SAW process and vital for structural reliability.
How to Become a Sub Arc Operator
Becoming a Submerged Arc Welding (SAW) Operator offers a stable and specialized career path within manufacturing and heavy industries. Entry routes vary significantly, from vocational training and apprenticeships to on-the-job learning. A complete beginner might spend 6-12 months gaining foundational welding skills before specializing, while someone with prior welding experience could transition in 3-6 months. The timeline depends heavily on the chosen learning path and commitment.
Traditional entry often involves completing a welding program at a technical school or community college, which provides a strong theoretical and practical base. Alternatively, many enter through apprenticeships with manufacturing companies or unions, offering paid on-the-job training and mentorship. This path often takes longer, perhaps 2-4 years, but provides immediate income and invaluable real-world experience. For those with some welding background, direct entry into entry-level operator roles is possible, often requiring a few months of internal training.
Geographic considerations also play a role; areas with heavy manufacturing, shipbuilding, or structural steel fabrication will have more opportunities. Company size matters too; larger corporations may offer more structured training programs, while smaller shops might provide quicker hands-on experience. Misconceptions include believing that only a degree is necessary; practical skills and certifications often outweigh formal education. Networking within the local industrial community and attending industry events significantly boosts job prospects, as many positions are filled through referrals.
Step 1
Step 2
Step 3
Step 4
Step 5
Step 6
Education & Training Needed to Become a Sub Arc Operator
Becoming a Sub Arc Operator primarily involves hands-on training and certification, rather than traditional academic degrees. While a high school diploma or GED is typically a prerequisite, employers prioritize practical welding skills over formal university education. Vocational schools, community colleges, and dedicated welding academies offer specialized programs ranging from 6 weeks to 12 months. These programs often cost between $5,000 and $15,000, focusing heavily on shielded metal arc welding (SMAW), gas metal arc welding (GMAW), flux-cored arc welding (FCAW), and specifically, submerged arc welding (SAW) techniques.
Alternative learning paths include apprenticeships, which combine paid on-the-job training with classroom instruction. Apprenticeships can last 3-5 years, providing comprehensive skills development and industry-recognized credentials without upfront tuition costs. Self-study is less common for this hands-on role; however, some operators might supplement their practical training with online courses on welding theory, blueprint reading, or safety standards, often costing under $500. Employers highly value certifications from organizations like the American Welding Society (AWS), such as the Certified Welder (CW) or Certified Welding Inspector (CWI) credentials, which demonstrate proficiency and adherence to industry standards. These certifications require passing practical and written exams, with costs ranging from $200-$1,000 per exam.
The market perception of a Sub Arc Operator emphasizes proven skill and experience. While a four-year degree is unnecessary, continuous learning through advanced welding certifications or specialized training in automated welding systems enhances career progression. The educational needs vary based on the complexity of the projects and the specific industry; for instance, aerospace or nuclear applications demand more stringent certifications and specialized training. Practical experience, especially with large-scale or automated SAW equipment, often outweighs theoretical knowledge for this role. Investing in quality vocational training and industry certifications provides a strong return, leading to well-paying positions in manufacturing, construction, and heavy industry.
Sub Arc Operator Salary & Outlook
Compensation for a Sub Arc Operator depends on many factors. Geographic location significantly affects earnings, with higher cost of living areas and regions with strong industrial demand typically offering higher wages. For example, salaries in bustling manufacturing hubs or states with extensive infrastructure projects often exceed those in less industrialized areas.
Experience levels, specialized certifications, and the ability to operate advanced Sub Arc welding equipment also create dramatic salary variations. Total compensation packages frequently extend beyond base salary. These can include overtime pay, production bonuses, and comprehensive benefits such as health insurance, retirement contributions, and paid time off. Some companies also offer allowances for professional development and specialized training.
Industry-specific trends, particularly in shipbuilding, heavy machinery manufacturing, and large-scale construction, drive salary growth for skilled Sub Arc Operators. Negotiation leverage comes from demonstrating a proven track record of high-quality work, efficiency, and adherence to safety protocols. Specialized skills, such as working with exotic materials or complex weld procedures, command premium compensation.
While remote work is not applicable to this hands-on role, demand varies internationally. The salary figures provided are in USD and reflect the United States market. International markets, particularly those with significant heavy industry, may offer different compensation structures and rates.
Salary by Experience Level
Level | US Median | US Average |
---|---|---|
Junior Sub Arc Operator | $45k USD | $48k USD |
Sub Arc Operator | $55k USD | $58k USD |
Senior Sub Arc Operator | $68k USD | $70k USD |
Lead Sub Arc Operator | $80k USD | $82k USD |
Market Commentary
The job market for Sub Arc Operators remains steady, driven by ongoing demand in heavy fabrication industries. These include shipbuilding, pipeline construction, structural steel, and the manufacturing of large industrial components. Infrastructure projects, particularly in energy and transportation, continue to be significant demand drivers. The growth outlook is stable, supported by consistent investment in these sectors.
Emerging opportunities for Sub Arc Operators often involve working with advanced materials and automated welding systems. While automation is increasing, the need for skilled operators to set up, monitor, and troubleshoot these complex machines persists. This evolving role requires adaptability and a willingness to learn new technologies. The supply of highly skilled Sub Arc Operators can sometimes lag behind demand, creating favorable conditions for experienced professionals.
This profession is relatively recession-resistant due to its foundational role in critical infrastructure and manufacturing. However, it can be cyclical, tied to large project pipelines. Geographic hotspots for Sub Arc Operators include coastal regions with shipyards, states with extensive oil and gas infrastructure, and areas with strong heavy manufacturing bases. Future-proofing involves continuous training in new welding techniques and automation technologies. The ability to perform complex, high-quality welds consistently will remain paramount.
Sub Arc Operator Career Path
Career progression for a Sub Arc Operator centers on mastering specialized welding techniques, equipment operation, and quality assurance. Advancement hinges on demonstrated proficiency, the ability to handle complex welds, and a commitment to safety and efficiency. This field offers both individual contributor (IC) growth, focusing on deeper technical expertise, and a leadership track, which emphasizes team oversight and process improvement.
Advancement speed depends on several factors, including an operator's consistent performance, the complexity of projects undertaken, and the specific industry. For example, working in aerospace or pressure vessel manufacturing often demands higher precision and offers more specialized advancement opportunities than general fabrication. Company size also plays a role; larger corporations may have more defined multi-level progression paths, while smaller shops might offer quicker transitions to lead roles based on merit.
Lateral moves might involve specializing in different welding processes, becoming a welding inspector, or moving into a welding engineering support role. Continuous learning, often through certifications in advanced welding procedures or specific materials, is crucial. Networking within the fabrication and manufacturing sectors helps identify new opportunities. Mentorship from experienced operators accelerates skill acquisition and problem-solving abilities, which are key markers of progression in this specialized trade.
Junior Sub Arc Operator
0-2 yearsKey Focus Areas
Sub Arc Operator
2-5 yearsKey Focus Areas
Senior Sub Arc Operator
5-8 yearsKey Focus Areas
Lead Sub Arc Operator
8+ years total experienceKey Focus Areas
Junior Sub Arc Operator
0-2 yearsA Junior Sub Arc Operator learns to set up and operate submerged arc welding (SAW) equipment under direct supervision. This role involves basic machine adjustments, material handling, and ensuring proper fit-up for simple welding tasks. They contribute to production by performing routine, repetitive welds, focusing on achieving acceptable quality standards.
Key Focus Areas
Develop foundational knowledge of submerged arc welding principles, including wire feed speeds, voltage settings, and flux types. Focus on consistent bead placement and understanding basic weld defects. Emphasize shop safety protocols and proper equipment maintenance. Seek mentorship from experienced operators to accelerate learning.
Sub Arc Operator
2-5 yearsA Sub Arc Operator independently sets up, operates, and monitors SAW equipment for a range of projects, including complex or critical welds. This individual makes independent adjustments to welding parameters to meet specific quality and efficiency targets. They are responsible for inspecting their own welds for defects and performing minor equipment maintenance.
Key Focus Areas
Master advanced SAW techniques for various joint configurations and material thicknesses. Develop strong troubleshooting skills for equipment and weld quality issues. Focus on optimizing welding parameters for efficiency and minimizing rework. Begin understanding blueprint reading and interpreting welding symbols accurately.
Senior Sub Arc Operator
5-8 yearsA Senior Sub Arc Operator handles the most challenging and critical welding projects, often involving high-value materials or strict quality requirements. This role provides technical guidance to other operators and acts as a subject matter expert for complex SAW applications. They contribute to process optimization and quality control initiatives, minimizing defects and maximizing throughput.
Key Focus Areas
Cultivate expertise in specialized welding procedures and exotic materials, such as stainless steel or nickel alloys. Develop advanced problem-solving abilities for complex metallurgical challenges. Focus on process improvement, identifying opportunities to enhance efficiency and reduce waste. Begin mentoring junior operators and contributing to training programs.
Lead Sub Arc Operator
8+ years total experienceA Lead Sub Arc Operator oversees a team of Sub Arc Operators, ensuring production schedules are met and quality standards are maintained across multiple projects. This role involves assigning tasks, providing on-the-job training, and troubleshooting complex operational issues. They collaborate with engineering and quality assurance teams to optimize welding processes and implement new procedures. Lead operators are critical in maintaining a safe and productive work environment.
Key Focus Areas
Develop strong leadership and communication skills, effectively delegating tasks and providing constructive feedback. Focus on project management, including scheduling, resource allocation, and meeting production deadlines. Master advanced quality control techniques and ensure compliance with industry standards. Participate in the selection and implementation of new welding technologies.
Job Application Toolkit
Ace your application with our purpose-built resources:
Sub Arc Operator Cover Letter Examples
Personalizable templates that showcase your impact.
View examplesSub Arc Operator Job Description Template
Ready-to-use JD for recruiters and hiring teams.
View examplesGlobal Sub Arc Operator Opportunities
A Sub Arc Operator specializes in Submerged Arc Welding (SAW), a high-deposition welding process crucial for heavy fabrication across industries like shipbuilding, construction, and oil and gas. This role is globally in demand, particularly in countries with robust industrial infrastructure projects. International opportunities arise from large-scale manufacturing and infrastructure developments. Cultural and regulatory differences impact safety standards and equipment certifications. Professionals pursue international roles for specialized project involvement and higher earning potential. International certifications like AWS or EWF enhance global mobility.
Global Salaries
Salaries for Sub Arc Operators vary significantly by region and experience. In North America, particularly the United States and Canada, annual salaries range from $60,000 to $90,000 USD. Experienced operators in high-demand areas like Texas or Alberta might earn closer to $100,000 USD, often with overtime. European countries, such as Germany or the Netherlands, offer salaries between €45,000 and €70,000 (approximately $48,000 to $75,000 USD), reflecting strong industrial sectors. These figures often include comprehensive benefits like health insurance and generous vacation time.
In the Asia-Pacific region, countries like Australia and South Korea present competitive packages. Australian operators can expect AUD 70,000 to AUD 100,000 (around $47,000 to $67,000 USD), while South Korea offers KRW 40,000,000 to KRW 60,000,000 (approximately $30,000 to $45,000 USD). These figures must be considered against the local cost of living. For instance, while Australian salaries might appear lower in USD, purchasing power for daily expenses can be comparable due to different pricing structures. Latin American countries, like Brazil or Mexico, offer lower nominal salaries, typically $15,000 to $30,000 USD, but cost of living is also significantly lower.
Salary structures also differ in terms of benefits. European packages often include robust social security contributions, affecting take-home pay but providing extensive healthcare and pension benefits. North American compensation might feature higher base pay but with more variable benefits. International experience and specialized certifications directly influence compensation, enabling operators to command higher rates, especially for complex projects. Some international projects might offer per diem allowances in addition to base pay, enhancing overall compensation.
Remote Work
Sub Arc Operators primarily perform hands-on work with heavy machinery, making traditional remote work largely impractical. The core duties involve operating specific welding equipment in a manufacturing or construction setting. Therefore, the direct operational aspect of this role requires physical presence at the job site.
However, some peripheral activities might support remote work. These include remote monitoring of welding parameters, data analysis of weld quality, or virtual training sessions. Digital nomad opportunities do not typically apply to this profession due to the hands-on nature of the job. Companies hiring in this field prioritize on-site presence. International remote work policies from employers in this sector are rare for operational roles. Salary expectations are tied to on-site work, and geographic arbitrage is not a factor for the core Sub Arc Operator duties.
Visa & Immigration
Sub Arc Operators typically pursue skilled worker visas for international employment. Popular destinations include Canada, Australia, Germany, and the United States, all with established immigration pathways for skilled trades. Canada's Express Entry system or Provincial Nominee Programs often consider welders. Australia's Skilled Migration program lists welding as a demanded occupation, requiring skill assessments through bodies like Trades Recognition Australia (TRA).
For the US, an H-2B visa for temporary non-agricultural workers can be an option if an employer sponsors. Germany offers the Skilled Immigration Act, facilitating visas for recognized qualifications. Educational credential recognition is crucial; professional licensing or certification from the destination country or international bodies like AWS or EWF is often required. The typical visa timeline varies from a few months to over a year, depending on the country and visa type. Application processes involve submitting skill assessments, educational documents, and proof of work experience.
Some countries offer pathways to permanent residency after several years of skilled employment. Language requirements, such as English for Anglophone countries or German for Germany, might be necessary for visa applications and professional integration. Family visas for dependents are usually available alongside the primary applicant's work visa. Specific project visas can also exist for large infrastructure developments, offering temporary but direct employment opportunities.
2025 Market Reality for Sub Arc Operators
Understanding current market conditions is paramount for Sub Arc Operators navigating their careers. This specialized welding field has seen significant evolution from 2023 to 2025, influenced by post-pandemic economic shifts and the accelerating integration of automation.
Broader economic factors, particularly in construction and heavy industry, directly impact project pipelines and, consequently, job availability for these highly skilled professionals. Market realities for Sub Arc Operators vary significantly by experience level, the specific industry (e.g., oil and gas, shipbuilding), and regional industrial activity. This analysis provides an honest assessment of current hiring landscapes, helping operators set realistic expectations and strategic career plans.
Current Challenges
Sub Arc Operators face increased competition for specialized roles, often requiring specific certifications or experience with automated systems. Economic slowdowns impact large-scale infrastructure projects, directly reducing demand for this role.
The integration of advanced welding robotics also means fewer purely manual operator positions, shifting demand towards those who can program and oversee automated equipment. Job search timelines can extend, especially for those lacking the most current automation skills.
Growth Opportunities
Despite market shifts, strong opportunities for Sub Arc Operators exist in energy infrastructure, including pipeline construction and renewable energy component fabrication. These sectors consistently require high-integrity, large-scale welds that SAW excels at.
Emerging opportunities also lie in roles that combine traditional SAW expertise with proficiency in robotic welding systems. Operators who can program, maintain, and troubleshoot automated SAW cells are in high demand, positioning themselves as indispensable assets.
Underserved markets often include regions with new industrial developments or expansions in manufacturing hubs that require significant fabrication capabilities. Certifications in advanced materials or specialized welding codes (e.g., API, ASME) provide a significant competitive advantage.
Strategic career moves might involve pursuing roles in companies investing heavily in automation, allowing operators to gain experience with cutting-edge technology. Industries like offshore wind turbine manufacturing and modular construction are also growing, creating new niches for skilled SAW professionals.
Current Market Trends
Hiring for Sub Arc Operators shows steady demand in sectors like heavy manufacturing, shipbuilding, and infrastructure development as of 2025. This specialized welding process remains critical for thick-plate, high-integrity welds in large structural components. However, recent trends emphasize operators with experience in automated or semi-automated SAW systems, moving beyond purely manual operations.
Post-pandemic, supply chain disruptions initially impacted project timelines, but a rebound in construction and energy sectors is now driving consistent, though not explosive, demand. Economic factors, particularly interest rates affecting large capital projects, influence the pipeline of work available. Layoffs have been minimal in this specific niche, given the specialized skill set required.
Technology, especially advanced robotics and AI-driven quality control, is reshaping the operator's role. Operators must increasingly monitor sophisticated equipment, troubleshoot automated processes, and interpret digital schematics. This shift raises the bar for technical proficiency beyond traditional welding skills.
Employer requirements now frequently include certifications for specific materials or joint configurations, alongside a proven track record with automated submerged arc welding. Salary trends for experienced operators remain strong, reflecting the specialized nature of the work, but market saturation exists at entry levels if candidates lack direct SAW experience. Geographic demand concentrates in industrial hubs, with limited remote work possibilities due to the hands-on nature of the job.
Emerging Specializations
The field of welding, particularly specialized areas like Submerged Arc Welding (SAW), is experiencing significant transformation. New technological advancements and evolving industry demands constantly create novel specialization opportunities. Understanding these emerging areas allows Sub Arc Operators to strategically position themselves for future career growth.
Early positioning in these nascent specializations offers a distinct advantage, often leading to premium compensation and accelerated career progression. As industries adopt more advanced manufacturing techniques and automation, operators who master these emerging skills become indispensable. While established welding specializations remain vital, focusing on cutting-edge areas ensures relevance and opens doors to next-generation projects.
Emerging specializations typically gain significant traction and create widespread job opportunities within three to five years. This timeline allows dedicated professionals to acquire necessary skills and experience. Pursuing these advanced paths involves a calculated risk, as some areas may evolve differently than expected. However, the potential for substantial reward in terms of compensation and career impact often outweighs these considerations, making it a strategic choice for forward-thinking Sub Arc Operators.
Robotic SAW Systems Operator
As manufacturing processes become increasingly automated, Sub Arc Operators with expertise in robotic SAW systems are in high demand. This specialization involves programming, calibrating, and overseeing robotic arms that perform precise submerged arc welds, ensuring consistent quality and efficiency. Operators must understand complex automation software and integrate welding parameters with robotic movements.
Advanced Material SAW Specialist
The demand for high-integrity welds in critical infrastructure, such as pipelines and structural components, is driving a need for specialized operators in advanced material SAW. This area focuses on welding exotic alloys, high-strength steels, and dissimilar metals that require precise control of heat input and shielding. Operators must understand metallurgical properties and their impact on weld integrity.
Smart Welding Data Analyst (SAW Focus)
Data-driven welding, also known as Industry 4.0 welding, is emerging as a critical specialization. Sub Arc Operators in this field utilize real-time data from welding processes—such as voltage, current, travel speed, and temperature—to optimize parameters, predict defects, and improve overall operational efficiency. This involves working with sensors, data analytics platforms, and cloud-based systems to enhance weld quality and reduce waste.
Sustainable SAW Process Operator
With increasing emphasis on environmental sustainability, a specialization in low-emission and energy-efficient SAW processes is gaining traction. This involves optimizing welding parameters and consumables to reduce fume generation, minimize energy consumption, and manage waste effectively. Operators in this area contribute to greener manufacturing practices and compliance with environmental regulations.
WAAM (Wire Arc Additive Manufacturing) Operator
Specialization in additive manufacturing, particularly wire arc additive manufacturing (WAAM) using SAW principles, represents a significant future opportunity. This technique involves building 3D metal structures layer by layer using welding. Sub Arc Operators can transition into operating WAAM systems, requiring an understanding of digital design, material deposition, and post-processing for complex geometries.
Pros & Cons of Being a Sub Arc Operator
Making informed career decisions requires a clear understanding of both the benefits and challenges associated with a specific profession. A career as a Sub Arc Operator offers distinct advantages, but it also comes with genuine difficulties that prospective individuals should consider.
Career experiences can vary significantly based on the company's industry, the specific projects undertaken, and the individual's personality and preferences. What one person views as a challenge, another might see as an opportunity for growth. Furthermore, the nature of pros and cons can shift at different stages of a career, from entry-level positions to more experienced roles. This assessment aims to provide a realistic and balanced perspective on the Sub Arc Operator role.
Pros
- Sub Arc Operators are highly specialized, and this niche skill often commands competitive wages, especially for experienced professionals in industries like shipbuilding, heavy manufacturing, and pressure vessel fabrication.
- There is consistent demand for skilled Sub Arc Operators in industries that require high-quality, high-deposition welds, offering good job security in sectors focused on large-scale construction and manufacturing.
- Working with advanced automated welding equipment provides an opportunity to develop expertise in sophisticated machinery and process control, which can be intellectually stimulating for those interested in industrial technology.
- Sub arc welding is known for its high efficiency and ability to produce strong, consistent welds on thick materials, offering a sense of accomplishment in contributing to robust and critical structures.
- Many sub arc welding operations occur in controlled shop environments, which can offer more stable working conditions compared to field welding, with less exposure to extreme weather.
- The role often involves working as part of a team with engineers and quality control personnel, fostering a collaborative environment where operators can learn from diverse perspectives and contribute to large projects.
- Developing proficiency as a Sub Arc Operator provides a solid foundation for career advancement into roles such as welding lead, supervisor, quality control inspector, or even welding technician, leveraging specialized knowledge.
Cons
- The work environment can be physically demanding, requiring prolonged standing, lifting heavy components, and working in noisy conditions, which can lead to fatigue and potential long-term physical strain.
- Exposure to welding fumes and intense light requires strict adherence to safety protocols and the consistent use of personal protective equipment, as improper precautions can pose health risks.
- Repetitive tasks are common in sub arc welding, as operators often perform similar welds on large batches of components, which can lead to monotony and reduced job satisfaction for some individuals.
- The specialized nature of sub arc welding means that while demand exists, the number of available positions may be less diverse compared to more general welding roles, potentially limiting geographical flexibility.
- Requires a high degree of precision and attention to detail; even minor errors can lead to costly rework or structural integrity issues, placing constant pressure on the operator to maintain quality.
- Maintaining and troubleshooting complex sub arc welding equipment requires mechanical aptitude and problem-solving skills, adding to the operator's responsibilities beyond just welding.
- Career progression for a Sub Arc Operator often involves moving into supervisory roles or becoming a welding inspector rather than directly advancing within the operator position itself, which might not appeal to everyone looking for technical growth in welding operations itself.
Frequently Asked Questions
Sub Arc Operators face unique challenges balancing precision welding with large-scale fabrication demands. This section addresses key questions about entering this specialized role, from mastering the equipment to understanding the physical demands and career progression in heavy industries.
What are the typical entry requirements and how long does it take to become a Sub Arc Operator?
Becoming a Sub Arc Operator typically requires a combination of formal training and practical experience. Many start with a welding certificate or associate's degree, which can take 6-24 months. After initial training, accumulating experience with various welding processes, including manual welding, is crucial before specializing in submerged arc welding. Most operators need 2-5 years of general welding experience before transitioning into a dedicated Sub Arc role.
What are the salary expectations for a Sub Arc Operator, and do benefits vary?
The salary for Sub Arc Operators varies based on experience, location, and the industry. Entry-level operators might earn $40,000-$55,000 annually, while experienced operators with specialized certifications can command $60,000-$80,000 or more. Overtime opportunities are often available in this field, which can significantly boost overall earnings. Benefits packages typically include health insurance, retirement plans, and paid time off.
What is the typical work-life balance and work environment like for a Sub Arc Operator?
The work-life balance for Sub Arc Operators can vary. Many roles involve standard 40-hour work weeks, but project-based work or industries with high demand, like oil and gas or infrastructure, may require overtime, night shifts, or weekend work. The job often involves working in industrial environments, which can be physically demanding and require adherence to strict safety protocols. Travel might be necessary for field-based projects.
Is there good job security and demand for Sub Arc Operators in the current market?
Job security for skilled Sub Arc Operators is generally strong, particularly in industries requiring large-scale, high-quality welds such as shipbuilding, heavy machinery manufacturing, and structural steel fabrication. While economic downturns can impact demand, the specialized nature of submerged arc welding means that skilled operators are consistently sought after. Automation is increasing, but the need for human oversight and specialized setup ensures continued demand for experienced operators.
What are the typical career growth opportunities for a Sub Arc Operator?
Career growth for Sub Arc Operators can lead to various advanced roles. Experienced operators might move into supervisory positions, becoming welding foremen or lead operators. Further specialization in advanced welding techniques, quality control, or welding inspection is also possible. Some operators transition into welding instruction, equipment maintenance, or even sales roles for welding equipment manufacturers. Continuous learning and certification are key for advancement.
What are the biggest challenges or downsides of being a Sub Arc Operator?
The most significant challenges for Sub Arc Operators include maintaining high precision and quality on large-scale projects, troubleshooting complex equipment, and adapting to new materials or specifications. The work can be physically demanding, requiring standing for long periods and operating heavy machinery in varying industrial conditions. Adhering to strict safety regulations and managing fumes and heat are also constant considerations.
Can Sub Arc Operators work remotely, or is location flexibility common?
While some remote monitoring or programming of welding robots exists, the Sub Arc Operator role itself is inherently hands-on and requires physical presence at the machine. It is not a remote-friendly position. Work typically takes place in fabrication shops, industrial sites, or manufacturing facilities. Location flexibility is limited to where these types of operations are located, often in industrial hubs or near major construction projects.
What are the most important skills for a Sub Arc Operator to master?
The skills most critical for success as a Sub Arc Operator include a strong understanding of welding metallurgy, blueprint reading, and precision measurement. Attention to detail, problem-solving abilities for machine calibration and troubleshooting, and adherence to strict safety protocols are paramount. Physical dexterity, good hand-eye coordination, and the ability to work effectively in a team environment are also highly valued.
Related Careers
Explore similar roles that might align with your interests and skills:
Welder
A growing field with similar skill requirements and career progression opportunities.
Explore career guideArc Welder
A growing field with similar skill requirements and career progression opportunities.
Explore career guideElectric Arc Furnace Operator
A growing field with similar skill requirements and career progression opportunities.
Explore career guideMachine Welder
A growing field with similar skill requirements and career progression opportunities.
Explore career guideWelding Machine Operator
A growing field with similar skill requirements and career progression opportunities.
Explore career guideAssess your Sub Arc Operator readiness
Understanding where you stand today is the first step toward your career goals. Our Career Coach helps identify skill gaps and create personalized plans.
Skills Gap Analysis
Get a detailed assessment of your current skills versus Sub Arc Operator requirements. Our AI Career Coach identifies specific areas for improvement with personalized recommendations.
See your skills gapCareer Readiness Assessment
Evaluate your overall readiness for Sub Arc Operator roles with our AI Career Coach. Receive personalized recommendations for education, projects, and experience to boost your competitiveness.
Assess your readinessSimple pricing, powerful features
Upgrade to Himalayas Plus and turbocharge your job search.
Himalayas
Himalayas Plus
Himalayas Max
Find your dream job
Sign up now and join over 100,000 remote workers who receive personalized job alerts, curated job matches, and more for free!
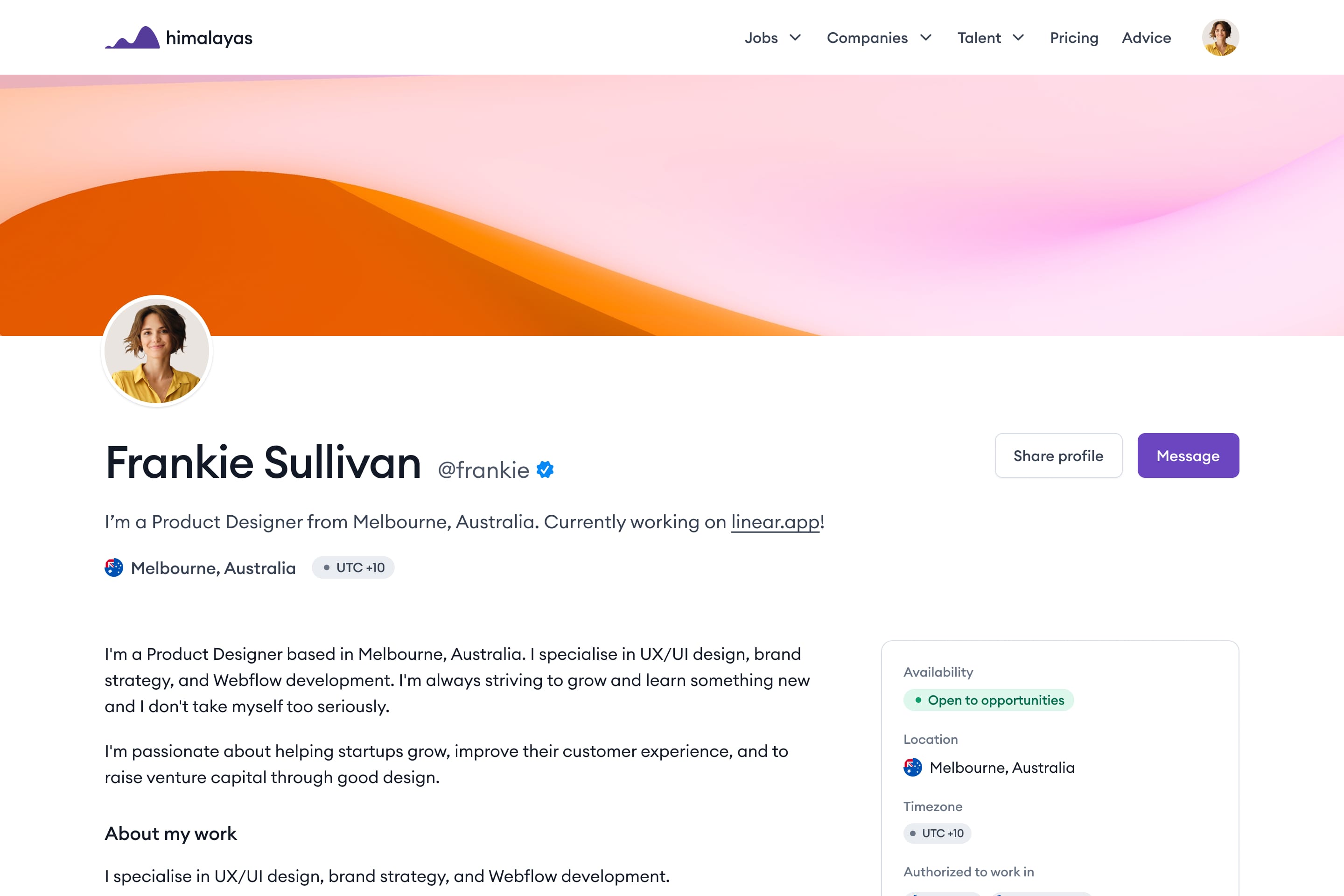