Complete Machine Welder Career Guide
Machine welders operate sophisticated robotic or automated welding equipment, precisely joining metal components for everything from automotive parts to heavy machinery. This role merges skilled trades with advanced technology, demanding an understanding of both metallurgy and automation systems. You'll ensure consistent, high-quality welds at speed, playing a critical role in manufacturing and infrastructure development across various industries.
Key Facts & Statistics
Median Salary
$48,270 USD
(U.S. national median, BLS May 2023)
Range: $38k - $70k+ USD
Growth Outlook
2%
slower than average (BLS)
Annual Openings
≈44,000
openings annually (BLS)
Top Industries
Typical Education
High school diploma or equivalent; vocational training, an associate's degree, or apprenticeship highly preferred
What is a Machine Welder?
A machine welder specializes in operating and monitoring automated or semi-automated welding equipment to join metal components. Unlike a manual welder who uses hand-held tools to perform welds, a machine welder's primary responsibility involves setting up, programming, and overseeing sophisticated machinery that executes the welding process. They ensure the machines produce consistent, high-quality welds according to precise specifications.
This role focuses on precision, repeatability, and efficiency in large-scale production. Machine welders often work in industries like automotive, heavy machinery manufacturing, and aerospace, where consistent quality and high throughput are critical. Their expertise lies in understanding machine capabilities, material properties, and welding parameters to optimize automated processes rather than the intricate manual dexterity required by traditional welders.
What does a Machine Welder do?
Key Responsibilities
- Set up and operate automated or semi-automated welding machines according to blueprints and welding procedure specifications (WPS).
- Load and unload components into welding jigs and fixtures, ensuring proper alignment and clamping for consistent weld quality.
- Monitor machine operations, adjusting parameters like voltage, wire feed speed, and travel speed to maintain optimal weld penetration and bead formation.
- Perform routine maintenance on welding equipment, including cleaning nozzles, replacing worn contact tips, and troubleshooting minor mechanical issues.
- Inspect finished welds for defects such as porosity, cracks, or excessive spatter, using visual inspection and basic measurement tools.
- Maintain accurate production records, including part counts, machine settings, and any observed anomalies or quality control issues.
- Collaborate with engineers and quality control personnel to refine welding processes and improve efficiency and weld integrity for various materials and designs.
Work Environment
Machine welders typically work in manufacturing plants, fabrication shops, or industrial settings. The environment can be noisy, with machinery operating constantly, and often requires personal protective equipment like safety glasses, ear protection, and welding helmets. This role involves more stationary work at a machine workstation compared to manual welding, but still requires physical dexterity and standing for extended periods. Collaboration is often with production supervisors, quality inspectors, and maintenance teams. Work schedules are usually standard shifts, but overtime can be common during peak production times. The pace is steady and driven by production quotas, with a strong emphasis on precision and efficiency.
Tools & Technologies
Machine welders primarily use a range of automated and semi-automated welding equipment, including robotic welding cells, orbital welding machines, and CNC welding systems. They work with various welding processes such as Gas Metal Arc Welding (GMAW/MIG), Flux-Cored Arc Welding (FCAW), and Gas Tungsten Arc Welding (GTAW/TIG), adapted for machine operation. Their toolkit includes precision measurement devices like calipers, micrometers, and gauges for quality checks, alongside hand tools for setup and maintenance. They also interpret blueprints, technical drawings, and Welding Procedure Specifications (WPS). Increasingly, they interact with control panels, programming interfaces, and sometimes even basic CAD/CAM software for machine setup and adjustment.
Machine Welder Skills & Qualifications
A Machine Welder's qualification landscape emphasizes practical proficiency and safety above all else. Employers prioritize demonstrated ability to operate automated or semi-automated welding equipment accurately and efficiently. While formal education provides a strong foundation, hands-on experience and specific certifications often carry more weight, especially for entry-level positions.
Requirements for Machine Welders vary significantly by industry sector. The aerospace or medical device industries demand extremely high precision and specific material knowledge, often requiring extensive certification and a longer apprenticeship. In contrast, general fabrication or construction might accept a broader skill set with less stringent certification. Company size also plays a role; larger manufacturing facilities often have more specialized machine welding roles, while smaller shops might expect a welder to handle both machine and manual tasks.
The skill landscape for Machine Welders is evolving with increased automation and robotics. Welders increasingly need to understand programming basic machine movements, troubleshooting automated systems, and interpreting digital schematics. Certifications from organizations like the American Welding Society (AWS) are crucial, often a 'must-have' for employment, validating specific process expertise (e.g., robotic welding, laser welding). Alternative pathways like vocational school programs or apprenticeships are highly valued, providing the practical experience employers seek.
Education Requirements
Technical Skills
- Machine Setup and Calibration: Ability to configure automated welding machines, including wire feed speed, voltage, amperage, and gas flow rates.
- Robotic Welding Operation: Proficiency in operating and monitoring robotic welding cells, including basic programming and teach pendant use.
- Interpretation of Blueprints and Schematics: Skill in reading and understanding technical drawings, welding symbols, and work instructions.
- Material Science Knowledge: Understanding of various metal properties (e.g., steel, aluminum, stainless steel) and their behavior during welding.
- Welding Processes (Automated): Expertise in automated GMAW (MIG), GTAW (TIG), FCAW, and potentially laser or resistance welding.
- Quality Control and Inspection: Ability to perform visual inspections of machine welds, identify defects (e.g., porosity, undercut), and use basic measuring tools.
- Preventative Maintenance: Performing routine cleaning, maintenance, and minor repairs on welding equipment to ensure optimal performance.
- Tooling and Fixturing: Knowledge of designing or setting up jigs, fixtures, and workholding devices for automated welding processes.
- Computer Numerical Control (CNC) Operation: Basic understanding of CNC principles for automated manufacturing environments.
- Non-Destructive Testing (NDT) Principles: Familiarity with NDT methods like dye penetrant or magnetic particle inspection to verify weld integrity.
Soft Skills
- Attention to Detail: Critical for ensuring weld quality, detecting flaws, and maintaining precise machine settings for consistent output.
- Problem-Solving: Essential for troubleshooting machine malfunctions, identifying root causes of weld defects, and optimizing machine parameters.
- Safety Consciousness: Paramount for operating heavy machinery and high-heat processes safely, adhering to strict protocols to prevent accidents.
- Mechanical Aptitude: Important for understanding how welding machines operate, performing basic maintenance, and making necessary adjustments.
- Adaptability: Necessary for switching between different welding processes, materials, or machine setups as production demands change.
- Work Ethic: Machine welders often work in fast-paced production environments, requiring diligence, reliability, and commitment to meeting output targets.
How to Become a Machine Welder
Becoming a Machine Welder offers various entry points, depending on your prior experience and educational background. For a complete beginner, a vocational school or community college program provides a structured pathway, typically taking 6-12 months to earn a certificate. Career changers with some mechanical aptitude might accelerate this process through intensive bootcamps or apprenticeships, which combine classroom learning with on-the-job training.
Entry strategies also vary significantly by industry and company size. Large manufacturing plants often prefer candidates with formal certifications and a clean safety record, while smaller fabrication shops might prioritize hands-on experience and a strong work ethic. Geographic location also plays a role; industrial hubs will have more opportunities and potentially higher competition. Understand that a portfolio of your weld samples, even from practice, is crucial.
A common misconception is that machine welding is simply pushing a button. In reality, it requires a deep understanding of metallurgy, machine calibration, and precise quality control. Networking with experienced welders and instructors can provide invaluable insights into specific industry needs and job openings. The hiring landscape values demonstrable skill and a commitment to continuous learning over just a degree.
Complete foundational training in welding processes and safety. Enroll in a vocational program, community college, or a recognized welding academy. This training should cover various welding methods like MIG, TIG, and Stick, along with essential safety protocols and blueprint reading. Expect this foundational phase to take 3-12 months, depending on program intensity.
Gain hands-on experience operating different welding machines. Practice extensively with both manual and automated welding equipment, focusing on consistent bead quality, penetration, and material integrity. Seek opportunities for practical application through school projects, personal projects, or volunteer work to build muscle memory and problem-solving skills.
Obtain industry certifications relevant to machine welding. Pursue certifications from recognized bodies like the American Welding Society (AWS), which validate your proficiency in specific welding processes and materials. These certifications are often a prerequisite for employment and demonstrate your commitment to professional standards.
Develop a portfolio of your best weld samples and project documentation. Photograph your completed welds from various angles, highlighting quality, consistency, and any complex joints or materials you have worked with. Include brief descriptions of the welding process used, machine settings, and the challenges overcome, as this showcases your technical understanding.
Network with professionals in the manufacturing and fabrication industries. Attend local industry events, job fairs, or connect with instructors and alumni from your training program. Informational interviews with current machine welders can provide insights into specific job requirements and potential openings, helping you tailor your application.
Prepare a targeted resume and practice interview skills. Highlight your technical skills, certifications, and any practical experience, even if it is from a training environment. Be ready to discuss your understanding of machine operation, safety procedures, and quality control during interviews, and be prepared for a hands-on welding test.
Step 1
Complete foundational training in welding processes and safety. Enroll in a vocational program, community college, or a recognized welding academy. This training should cover various welding methods like MIG, TIG, and Stick, along with essential safety protocols and blueprint reading. Expect this foundational phase to take 3-12 months, depending on program intensity.
Step 2
Gain hands-on experience operating different welding machines. Practice extensively with both manual and automated welding equipment, focusing on consistent bead quality, penetration, and material integrity. Seek opportunities for practical application through school projects, personal projects, or volunteer work to build muscle memory and problem-solving skills.
Step 3
Obtain industry certifications relevant to machine welding. Pursue certifications from recognized bodies like the American Welding Society (AWS), which validate your proficiency in specific welding processes and materials. These certifications are often a prerequisite for employment and demonstrate your commitment to professional standards.
Step 4
Develop a portfolio of your best weld samples and project documentation. Photograph your completed welds from various angles, highlighting quality, consistency, and any complex joints or materials you have worked with. Include brief descriptions of the welding process used, machine settings, and the challenges overcome, as this showcases your technical understanding.
Step 5
Network with professionals in the manufacturing and fabrication industries. Attend local industry events, job fairs, or connect with instructors and alumni from your training program. Informational interviews with current machine welders can provide insights into specific job requirements and potential openings, helping you tailor your application.
Step 6
Prepare a targeted resume and practice interview skills. Highlight your technical skills, certifications, and any practical experience, even if it is from a training environment. Be ready to discuss your understanding of machine operation, safety procedures, and quality control during interviews, and be prepared for a hands-on welding test.
Education & Training Needed to Become a Machine Welder
A Machine Welder operates automated or semi-automated welding equipment to join metal components. This role differs from a manual welder, focusing on precision machine operation, programming, and quality control rather than hands-on torch work. Educational pathways for this specialized field primarily involve vocational training, certifications, and apprenticeships, with less emphasis on traditional four-year degrees.
Vocational programs and technical schools offer focused training, typically ranging from 6 to 18 months, with costs from $5,000 to $20,000. These programs often lead to industry-recognized certifications, such as those from the American Welding Society (AWS), which are highly valued by employers. Apprenticeships combine on-the-job training with classroom instruction, usually lasting 3-5 years, providing paid experience while learning. Self-study for specific machine operation or programming aspects is possible, but practical, hands-on experience with equipment remains crucial. Employers prioritize demonstrated skill and relevant certifications over academic degrees for machine welders.
Continuous learning is vital due to evolving welding technologies and automation. Machine welders often pursue advanced certifications in robotic welding, laser welding, or specific programming languages. These specialized courses can cost $1,000 to $5,000 and take weeks to months. The cost-benefit analysis for machine welders strongly favors vocational training and certifications, as they offer a direct path to employment without the higher cost and time commitment of a bachelor's degree. Practical experience and a portfolio of successful welds are as important as formal credentials.
Machine Welder Salary & Outlook
Compensation for a Machine Welder varies significantly based on several key factors. Geographic location plays a crucial role, with higher wages typically found in areas with a strong manufacturing base or high cost of living. For instance, states with significant automotive, aerospace, or heavy machinery industries often offer better pay.
Years of experience and specialized skills directly impact earning potential. A Machine Welder with certifications in advanced techniques, such as robotic welding or specialized material fabrication, can command premium compensation. Performance and efficiency also enhance a welder's value, particularly in production environments.
Total compensation packages extend beyond base salary. They often include overtime pay, production bonuses, and comprehensive benefits like health insurance, retirement plans, and paid time off. Some companies also offer allowances for professional development or tool acquisition.
Industry-specific trends also influence salaries; for example, the oil and gas or defense sectors may offer higher pay compared to general manufacturing. Remote work is not typically applicable for this hands-on role, so geographic location remains a primary driver of salary differences. While these figures are in USD, international markets will have their own distinct wage structures driven by local demand and economic conditions.
Salary by Experience Level
Level | US Median | US Average |
---|---|---|
Junior Machine Welder | $42k USD | $45k USD |
Machine Welder | $52k USD | $55k USD |
Senior Machine Welder | $65k USD | $68k USD |
Lead Machine Welder | $75k USD | $78k USD |
Welding Supervisor | $85k USD | $88k USD |
Market Commentary
The job market for Machine Welders shows steady demand, driven by the ongoing need for fabricated metal products across various industries. Manufacturing, construction, and infrastructure projects consistently require skilled welders. The aging workforce also contributes to a consistent need for new talent entering the field.
Growth in this sector is projected to remain stable, with the U.S. Bureau of Labor Statistics forecasting a modest increase in welding jobs over the next decade. Automation and advanced welding technologies, including robotic welding, are transforming the role. This shift creates opportunities for Machine Welders who can program, operate, and maintain these sophisticated systems.
The supply and demand dynamics for skilled Machine Welders often show a shortage of qualified candidates, especially those proficient in modern techniques. This imbalance can lead to competitive wages and job security. Emerging specializations in advanced materials and precision welding are creating new career paths.
While automation handles repetitive tasks, the need for human expertise in complex setups, quality control, and custom fabrication remains strong. This profession is relatively recession-resistant as essential infrastructure and manufacturing continue even during economic downturns. Geographic hotspots for Machine Welders include industrial belts in the Midwest, Southeast, and certain coastal regions with shipbuilding or heavy industry.
Machine Welder Career Path
Career progression for a Machine Welder involves a clear path from foundational skills to advanced technical expertise and leadership. This path typically emphasizes hands-on proficiency, continuous learning, and adherence to safety and quality standards. Professionals advance by mastering diverse welding techniques, operating complex machinery, and consistently producing high-quality welds.
Advancement speed depends on individual performance, the ability to learn new technologies, and the specific industry. For example, welders in highly specialized fields like aerospace or medical device manufacturing may see faster progression due to the demand for precision and advanced certifications. Company size also plays a role; larger corporations often have more structured advancement programs and diverse project opportunities compared to smaller fabrication shops.
Progression can lead to individual contributor roles focused on technical excellence, or supervisory roles managing welding teams. Lateral moves often involve specializing in a particular welding process, material, or machine type, such as robotic welding or exotic alloy welding. Networking within professional welding associations and pursuing advanced certifications, like Certified Welding Inspector (CWI), are crucial for opening new opportunities and demonstrating expertise.
Junior Machine Welder
0-2 yearsOperate welding machines under direct supervision to produce simple components. Perform repetitive welding tasks following established procedures and quality checks. Responsible for basic machine maintenance and ensuring a clean and safe work area. Initial impact is on individual task completion and adherence to production schedules.
Key Focus Areas
Develop foundational welding skills, including setting up and operating basic welding machines, understanding different joint types, and basic blueprint reading. Focus on safety protocols, proper material handling, and achieving consistent, clean welds. Build proficiency in common welding processes like MIG, TIG, or Stick welding.
Machine Welder
2-5 yearsOperate various welding machines independently to fabricate and repair components according to specifications. Work on moderately complex projects with minimal supervision. Conduct self-inspections of welds to ensure quality standards are met. Collaborate with team members to optimize workflow and resolve minor production issues.
Key Focus Areas
Master multiple welding processes and machine types, including more complex setups and troubleshooting. Enhance blueprint interpretation skills for intricate assemblies. Focus on improving weld quality, reducing defects, and increasing production efficiency. Begin to understand material science and how different metals react to welding.
Senior Machine Welder
5-8 yearsHandle complex welding tasks and operate sophisticated welding machinery, often involving robotic or automated systems. Independently troubleshoot machine malfunctions and implement effective solutions. Take responsibility for critical welds and ensure adherence to stringent quality and safety standards. Provide technical guidance to peers.
Key Focus Areas
Develop expertise in advanced welding techniques, complex machine programming, and quality control. Focus on problem-solving for challenging welding applications and optimizing machine performance. Mentor junior welders and contribute to process improvement initiatives. Pursue specialized certifications in advanced welding methods or materials.
Lead Machine Welder
8-12 yearsLead a small team of machine welders on specific projects or production lines. Oversee machine setups, process parameters, and quality assurance for complex assemblies. Act as a primary point of contact for technical issues and provide on-the-job training. Contribute to scheduling and resource allocation for welding tasks.
Key Focus Areas
Cultivate leadership skills, including project planning, team coordination, and advanced problem-solving. Focus on optimizing overall welding operations, implementing new technologies, and ensuring compliance with industry codes. Develop strong communication skills for effective collaboration with engineering and production teams.
Welding Supervisor
12+ yearsManage the entire welding department or a significant section of it, overseeing multiple teams and complex welding operations. Responsible for departmental output, quality control, safety compliance, and personnel development. Make strategic decisions regarding equipment upgrades, process improvements, and training programs. Collaborate cross-functionally with other departments.
Key Focus Areas
Develop comprehensive management and supervisory skills, including team leadership, performance management, and strategic planning for the welding department. Focus on budget management, continuous improvement methodologies, and fostering a culture of safety and quality. Pursue certifications in lean manufacturing or project management.
Junior Machine Welder
0-2 yearsOperate welding machines under direct supervision to produce simple components. Perform repetitive welding tasks following established procedures and quality checks. Responsible for basic machine maintenance and ensuring a clean and safe work area. Initial impact is on individual task completion and adherence to production schedules.
Key Focus Areas
Develop foundational welding skills, including setting up and operating basic welding machines, understanding different joint types, and basic blueprint reading. Focus on safety protocols, proper material handling, and achieving consistent, clean welds. Build proficiency in common welding processes like MIG, TIG, or Stick welding.
Machine Welder
2-5 yearsOperate various welding machines independently to fabricate and repair components according to specifications. Work on moderately complex projects with minimal supervision. Conduct self-inspections of welds to ensure quality standards are met. Collaborate with team members to optimize workflow and resolve minor production issues.
Key Focus Areas
Master multiple welding processes and machine types, including more complex setups and troubleshooting. Enhance blueprint interpretation skills for intricate assemblies. Focus on improving weld quality, reducing defects, and increasing production efficiency. Begin to understand material science and how different metals react to welding.
Senior Machine Welder
5-8 yearsHandle complex welding tasks and operate sophisticated welding machinery, often involving robotic or automated systems. Independently troubleshoot machine malfunctions and implement effective solutions. Take responsibility for critical welds and ensure adherence to stringent quality and safety standards. Provide technical guidance to peers.
Key Focus Areas
Develop expertise in advanced welding techniques, complex machine programming, and quality control. Focus on problem-solving for challenging welding applications and optimizing machine performance. Mentor junior welders and contribute to process improvement initiatives. Pursue specialized certifications in advanced welding methods or materials.
Lead Machine Welder
8-12 yearsLead a small team of machine welders on specific projects or production lines. Oversee machine setups, process parameters, and quality assurance for complex assemblies. Act as a primary point of contact for technical issues and provide on-the-job training. Contribute to scheduling and resource allocation for welding tasks.
Key Focus Areas
Cultivate leadership skills, including project planning, team coordination, and advanced problem-solving. Focus on optimizing overall welding operations, implementing new technologies, and ensuring compliance with industry codes. Develop strong communication skills for effective collaboration with engineering and production teams.
Welding Supervisor
12+ yearsManage the entire welding department or a significant section of it, overseeing multiple teams and complex welding operations. Responsible for departmental output, quality control, safety compliance, and personnel development. Make strategic decisions regarding equipment upgrades, process improvements, and training programs. Collaborate cross-functionally with other departments.
Key Focus Areas
Develop comprehensive management and supervisory skills, including team leadership, performance management, and strategic planning for the welding department. Focus on budget management, continuous improvement methodologies, and fostering a culture of safety and quality. Pursue certifications in lean manufacturing or project management.
Job Application Toolkit
Ace your application with our purpose-built resources:
Machine Welder Cover Letter Examples
Personalizable templates that showcase your impact.
View examplesMachine Welder Job Description Template
Ready-to-use JD for recruiters and hiring teams.
View examplesGlobal Machine Welder Opportunities
Machine welders operate automated or semi-automated welding equipment, a skill in demand across global manufacturing, construction, and energy sectors. This profession translates consistently worldwide, focusing on precision and efficiency in production environments. Global demand for skilled machine welders remains strong as industries automate, requiring expertise in robotic and advanced welding systems. Regulatory standards and safety protocols for welding vary slightly by region, influencing operational practices. Professionals seek international opportunities for higher wages, advanced training, or specialized projects, often benefiting from certifications like AWS or EWF which enhance global mobility.
Global Salaries
Machine welder salaries vary significantly by region and industrial demand. In North America, particularly the United States and Canada, annual salaries range from $45,000 to $75,000 USD, with higher figures for specialized or certified welders. Cost of living in major industrial hubs like the Midwest US or Alberta, Canada, is moderate, offering good purchasing power.
European salaries differ by country. In Germany, machine welders earn €35,000 to €55,000 (approx. $38,000 - $60,000 USD), while in the UK, it ranges from £28,000 to £45,000 (approx. $35,000 - $56,000 USD). Northern European countries like Norway or Switzerland offer higher nominal wages but also have a much higher cost of living. Benefits often include robust social security, healthcare, and generous vacation time, which can significantly impact overall compensation.
Asia-Pacific markets like Australia and New Zealand offer competitive salaries, typically between AUD $60,000 and $90,000 (approx. $40,000 - $60,000 USD), driven by mining and construction sectors. In some Middle Eastern countries, salaries can reach $30,000 to $50,000 USD tax-free, but often with fewer social benefits. Latin American countries generally have lower nominal salaries, often ranging from $15,000 to $30,000 USD, but with a significantly lower cost of living.
Experience and specific certifications, such as those for exotic materials or advanced robotic systems, directly increase earning potential across all regions. Tax implications vary widely; some countries have progressive income tax systems, while others offer lower rates or tax-free income in specific sectors, impacting take-home pay. International pay scales are not standardized, but global demand for skilled machine welders often drives compensation upwards in developed economies.
Remote Work
Machine welding is primarily a hands-on profession requiring physical presence at a manufacturing plant or construction site. Therefore, traditional remote work opportunities are virtually non-existent for this role. The nature of operating and maintaining heavy machinery demands on-site engagement. Digital nomad opportunities do not apply to direct machine welding tasks.
However, some peripheral roles may offer limited flexibility. For instance, a highly experienced machine welder might transition into a supervisory, training, or quality control role that could involve some remote consultation or documentation. Such roles are rare for the core machine welder position. Companies hiring machine welders typically require full-time, on-site commitment, with no impact on salary expectations for remote work given its impracticality.
Visa & Immigration
Skilled machine welders often qualify for skilled worker visas in countries with industrial demand. Popular destinations include Canada, Australia, Germany, and the UK, all offering pathways for tradespeople. Requirements typically include a recognized trade qualification or equivalent work experience, often assessed through skills assessments. For example, Canada's Express Entry system or Australia's skilled migration program list welding as an in-demand occupation.
Education credential recognition is crucial; applicants often need their qualifications assessed by designated authorities in the target country. Professional licensing for welders is less common than for other trades, but specific certifications are vital. Visa timelines vary, from a few months to over a year, depending on the country and visa type. Many skilled worker visas offer pathways to permanent residency after a few years of employment. Language requirements, such as English proficiency tests (IELTS, CELPIP) or German (Goethe-Institut), are standard for many skilled worker visas. Some countries, like Germany, have specific visa programs for skilled trades, which can streamline the process. Family visas are often available for dependents of skilled visa holders.
2025 Market Reality for Machine Welders
Understanding the current market reality for machine welders is crucial for career progression and stability. The field has evolved significantly from 2023 to 2025, influenced by post-pandemic manufacturing shifts and the accelerating integration of AI.
Broader economic factors, such as industrial output and infrastructure spending, directly impact job availability. Market realities for machine welders vary considerably by experience level, with senior operators of advanced robotic systems in higher demand than entry-level manual machine operators. Geographic location and the size of manufacturing operations also play a significant role. This analysis provides an honest assessment of these dynamics.
Current Challenges
Skilled machine welders face increased competition from automated systems and a push for multi-skilled technicians. Economic uncertainty can slow down large-scale manufacturing projects, impacting demand. Entry-level saturation exists where basic certifications are common, but advanced, specialized skills are scarce. Job searches often take longer for positions requiring precision and complex machine operation.
Growth Opportunities
Strong demand exists for machine welders specializing in advanced robotic welding, laser welding, and additive manufacturing. These roles require programming, troubleshooting, and maintenance of complex automated systems, moving beyond simple operation. Companies seek professionals who can optimize machine performance and integrate new technologies.
Underserved markets include precision manufacturing for medical devices and defense, where quality control and specialized material handling are paramount. Machine welders with certifications in specific robotic platforms or advanced materials (e.g., titanium, composites) gain a significant competitive edge. Upskilling in data analytics for predictive maintenance or simulation software for weld path optimization creates new opportunities.
Market corrections, especially labor shortages in highly technical manufacturing, can open doors for those with specialized training. Sectors like renewable energy infrastructure (e.g., wind turbine components) and electric vehicle manufacturing are experiencing consistent growth, offering stable employment for skilled machine welders. Timing educational investments in automation and programming skills now can lead to long-term career advantages.
Current Market Trends
Demand for machine welders remains steady in 2025, particularly for those proficient with advanced robotic and automated welding systems. Industries like automotive, aerospace, and heavy machinery continue to invest in automation, shifting the need from manual welders to operators and programmers of welding robots. This requires a stronger blend of mechanical aptitude and software understanding.
Economic conditions show a mixed picture; while some sectors like infrastructure projects are robust, others sensitive to consumer spending exhibit slower growth. Generative AI impacts the design and optimization of welding paths, making welders who can interpret and validate AI-generated programs more valuable. Employers now prioritize candidates with experience in CAD/CAM software, sensor integration, and predictive maintenance for welding equipment.
Salary trends for highly skilled machine welders, especially those managing advanced robotics, are seeing upward pressure. However, basic machine operator roles face stagnation due to increased automation efficiency. Market saturation is low for specialized roles, but high for general machine welding tasks. Geographically, demand is strongest in manufacturing hubs across the Midwest and Southern U.S., with remote work virtually non-existent for this hands-on role. Cyclical trends tie closely to industrial production cycles and capital expenditure in manufacturing.
Emerging Specializations
The field of welding is undergoing significant transformation, driven by advancements in automation, materials science, and digital fabrication technologies. These shifts are creating entirely new specialization opportunities for machine welders, moving beyond traditional manual techniques towards roles that integrate advanced machinery and data.
Positioning oneself early in these emerging areas is crucial for career advancement from 2025 onwards. Professionals who acquire expertise in these cutting-edge specializations often command premium compensation and experience accelerated career growth, as their skills are in high demand but short supply.
While established welding specializations remain vital, focusing on emerging areas provides a strategic advantage. These new niches are not just incremental improvements; they represent fundamental shifts in how welding is performed and managed. Many emerging areas, initially niche, are rapidly becoming mainstream, creating a significant number of job opportunities within a few years.
Pursuing cutting-edge specializations involves a balance of risk and reward. It requires proactive learning and adapting to new technologies. However, the potential for higher earning potential and leading roles in innovative projects often outweighs the initial investment in new skill acquisition.
Robotic Welding Systems Operator & Programmer
As robotic welding systems become more sophisticated and prevalent across manufacturing, machine welders are specializing in programming, operating, and troubleshooting these advanced robotic cells. This involves setting up complex weld paths, calibrating sensors, and ensuring quality control through automated processes. The role shifts from direct manual welding to managing and optimizing robotic performance for high-volume, precision production.
Additive Manufacturing Post-Processing Welder
Additive manufacturing, particularly in metals, is creating a demand for machine welders specialized in post-processing and repair of 3D-printed metal components. This involves using advanced welding techniques to fuse sections, repair defects, or add features to parts created by technologies like DED (Direct Energy Deposition) or powder bed fusion. Welders ensure structural integrity and surface finish meet stringent engineering standards.
AI-Assisted Welding System Monitor
The integration of vision systems and artificial intelligence into welding processes is creating a need for machine welders who can operate and monitor AI-driven welding equipment. This specialization focuses on overseeing systems that use machine learning to detect weld defects, adjust parameters in real-time, or optimize weld quality. Welders analyze data outputs and intervene when AI systems require human oversight or fine-tuning.
Sustainable Component Repair Welder
With increasing emphasis on sustainability and material efficiency, machine welders are specializing in advanced repair and refurbishment techniques for high-value industrial components. This involves using precise welding methods, often with exotic materials, to extend the lifespan of critical parts rather than replacing them. This reduces waste and conserves resources, requiring a deep understanding of material properties and stress points.
Precision Micro-Welding Technician
The aerospace and defense sectors demand extremely high precision and quality for critical components, leading to a specialization in micro-welding for intricate assemblies. This area involves using highly controlled, often automated, welding processes on very small parts with minimal heat input, typically for electronics, sensors, or lightweight structures. Welders must ensure microscopic accuracy and structural integrity.
Pros & Cons of Being a Machine Welder
Making a career choice requires a clear-eyed understanding of both the benefits and the difficulties inherent in a profession. A career as a Machine Welder, like any other, comes with its own unique set of advantages and challenges that can significantly impact daily work life and long-term satisfaction. It is important to recognize that individual experiences can vary greatly depending on the specific company culture, the industry sector (e.g., automotive, aerospace, construction), the type of machinery used, and personal aptitudes. Furthermore, the perceived pros and cons may shift at different stages of a career, from entry-level positions to more experienced roles. What one person views as a positive, another might see as a drawback, underscoring the importance of aligning a career with personal values and lifestyle preferences. This assessment provides an honest, balanced perspective to help potential machine welders set realistic expectations for the role.
Pros
- Machine welders typically earn a stable income, often with opportunities for overtime pay, especially in industries with high production demands or specialized projects.
- The demand for skilled machine welders remains consistent across various manufacturing and industrial sectors, providing good job security and relatively easy transferability of skills between companies and regions.
- Operating advanced welding machinery often involves less physical strain and exposure to direct welding hazards compared to manual welding, as the machines perform the most intense and hazardous tasks.
- There are clear pathways for skill development, including learning to program and maintain robotic welding systems, which can lead to higher-paying specialized roles and increased responsibility.
- Machine welding offers a structured work environment with predictable tasks and procedures, which can be appealing to individuals who prefer routine and clear guidelines.
- The role contributes directly to the production of essential goods and infrastructure, providing a sense of purpose and tangible results from daily work.
- Entry into machine welding often requires vocational training or an apprenticeship, which can be a faster and less expensive route to a skilled trade career compared to traditional four-year college degrees.
Cons
- Machine welders often work in environments with fumes, dust, and loud noise, requiring consistent use of personal protective equipment (PPE) and posing long-term health risks if safety protocols are not strictly followed.
- The work can be physically demanding, involving prolonged standing, repetitive motions, and occasional heavy lifting, which can lead to musculoskeletal issues over time.
- While machine welding automates much of the process, it still requires precision and attention to detail; errors can lead to costly material waste or structural failures, adding pressure to the role.
- Job security can be tied to the manufacturing sector's health, meaning economic downturns or shifts in production can lead to layoffs or reduced work hours.
- There is a continuous need for training and certification updates to stay current with new welding technologies, materials, and safety standards, which requires ongoing investment of time and sometimes money.
- The work can become monotonous due to the repetitive nature of operating machinery for extended periods, which may not suit individuals who thrive on variety and dynamic tasks.
- Opportunities for creative expression or independent problem-solving are often limited compared to manual welding roles, as the work primarily involves operating and monitoring equipment according to strict specifications and programmed parameters, which can feel restrictive to some individuals and limit professional growth in certain areas of the trade, as well as lead to fewer opportunities for advancement into supervisory or design roles without additional training and experience in other aspects of manufacturing or engineering, which can be a significant drawback for those seeking a more varied and challenging career path.
Frequently Asked Questions
Machine Welders face distinct challenges around precision, automation, and adapting to new technologies. This section addresses common questions about entering this specialized field, from required certifications and safety protocols to career growth within advanced manufacturing environments.
What are the essential qualifications and certifications needed to become a Machine Welder?
Becoming a Machine Welder typically requires vocational training or an associate's degree in welding technology, focusing on automated systems. Many employers also look for certifications like those from the American Welding Society (AWS) in relevant automated processes. Prior experience with manual welding is often beneficial but not always mandatory if you have strong technical aptitude and training in machine operation. Familiarity with robotics or CNC programming can be a significant advantage.
How long does it take to become proficient enough to secure an entry-level Machine Welder position?
The timeline to become job-ready as a Machine Welder varies but generally ranges from 6 months to 2 years. A focused vocational program can provide foundational skills in 6-12 months. An associate's degree may take up to 2 years. The key is gaining hands-on experience with various welding machines and automated systems, which is often integrated into these programs. Building a portfolio of projects and obtaining specific process certifications further accelerates readiness.
What are the typical salary expectations for a new Machine Welder, and how does it compare to manual welding?
Entry-level Machine Welders can expect a starting salary that varies by region, industry, and the specific automation technologies used. Generally, it is competitive with or slightly higher than manual welding due to the specialized skills involved. With experience and mastery of advanced robotic or laser welding systems, earning potential significantly increases. Overtime opportunities are common in manufacturing, which can boost overall income.
What is the typical work environment and work-life balance like for a Machine Welder?
Machine Welders typically work in manufacturing plants, which often operate on shifts (day, evening, or night) to maximize production. While the work involves operating machinery, it requires significant attention to detail and problem-solving. The work-life balance depends on the employer and production demands, but structured shifts can offer predictability. Unlike manual welding, physical strain is often reduced, but mental focus on programming and quality control is high.
Is the demand for Machine Welders growing, or is it a field at risk of being fully automated?
The job outlook for Machine Welders remains strong due to increasing automation in manufacturing sectors. Companies are investing in robotic welding to improve efficiency, consistency, and safety, creating a consistent demand for skilled operators and programmers. While some manual welding jobs may decline, the need for professionals who can set up, operate, and maintain advanced welding machinery is growing. Continuous learning in new technologies ensures long-term job security.
What are the potential career advancement opportunities for an experienced Machine Welder?
Career growth for Machine Welders can lead to roles such as Robotic Welding Programmer, Welding Technician, Quality Control Inspector, or even supervisory positions in manufacturing. Opportunities also exist in specialized areas like laser welding or additive manufacturing. Continuous training in new software, robotics, and materials science can open doors to more advanced and higher-paying roles, allowing for significant upward mobility within the industry.
What are the biggest challenges or common difficulties faced by Machine Welders in their daily work?
The primary challenges include adapting to rapidly evolving automation technologies, maintaining complex machinery, and troubleshooting programming issues. Machine Welders must possess a strong understanding of metallurgy and blueprint reading, even though the welding process is automated. Ensuring consistent quality and precision across large production runs also requires meticulous attention and problem-solving skills. Safety protocols around automated machinery are paramount.
Can Machine Welders work remotely, or is it primarily an on-site role?
Remote work is generally not feasible for Machine Welders, as the role requires direct interaction with and operation of physical machinery on a manufacturing floor. However, some aspects like programming or diagnostics might involve remote access to systems for troubleshooting or updates. The core responsibilities of setting up, monitoring, and maintaining the welding cells necessitate an on-site presence. Therefore, location flexibility is limited to the manufacturing facility.
Related Careers
Explore similar roles that might align with your interests and skills:
Machine Builder
A growing field with similar skill requirements and career progression opportunities.
Explore career guideMig Welder
A growing field with similar skill requirements and career progression opportunities.
Explore career guideWelder
A growing field with similar skill requirements and career progression opportunities.
Explore career guideWelder Fabricator
A growing field with similar skill requirements and career progression opportunities.
Explore career guideWelding Machine Operator
A growing field with similar skill requirements and career progression opportunities.
Explore career guideAssess your Machine Welder readiness
Understanding where you stand today is the first step toward your career goals. Our Career Coach helps identify skill gaps and create personalized plans.
Skills Gap Analysis
Get a detailed assessment of your current skills versus Machine Welder requirements. Our AI Career Coach identifies specific areas for improvement with personalized recommendations.
See your skills gapCareer Readiness Assessment
Evaluate your overall readiness for Machine Welder roles with our AI Career Coach. Receive personalized recommendations for education, projects, and experience to boost your competitiveness.
Assess your readinessSimple pricing, powerful features
Upgrade to Himalayas Plus and turbocharge your job search.
Himalayas
Himalayas Plus
Himalayas Max
Find your dream job
Sign up now and join over 100,000 remote workers who receive personalized job alerts, curated job matches, and more for free!
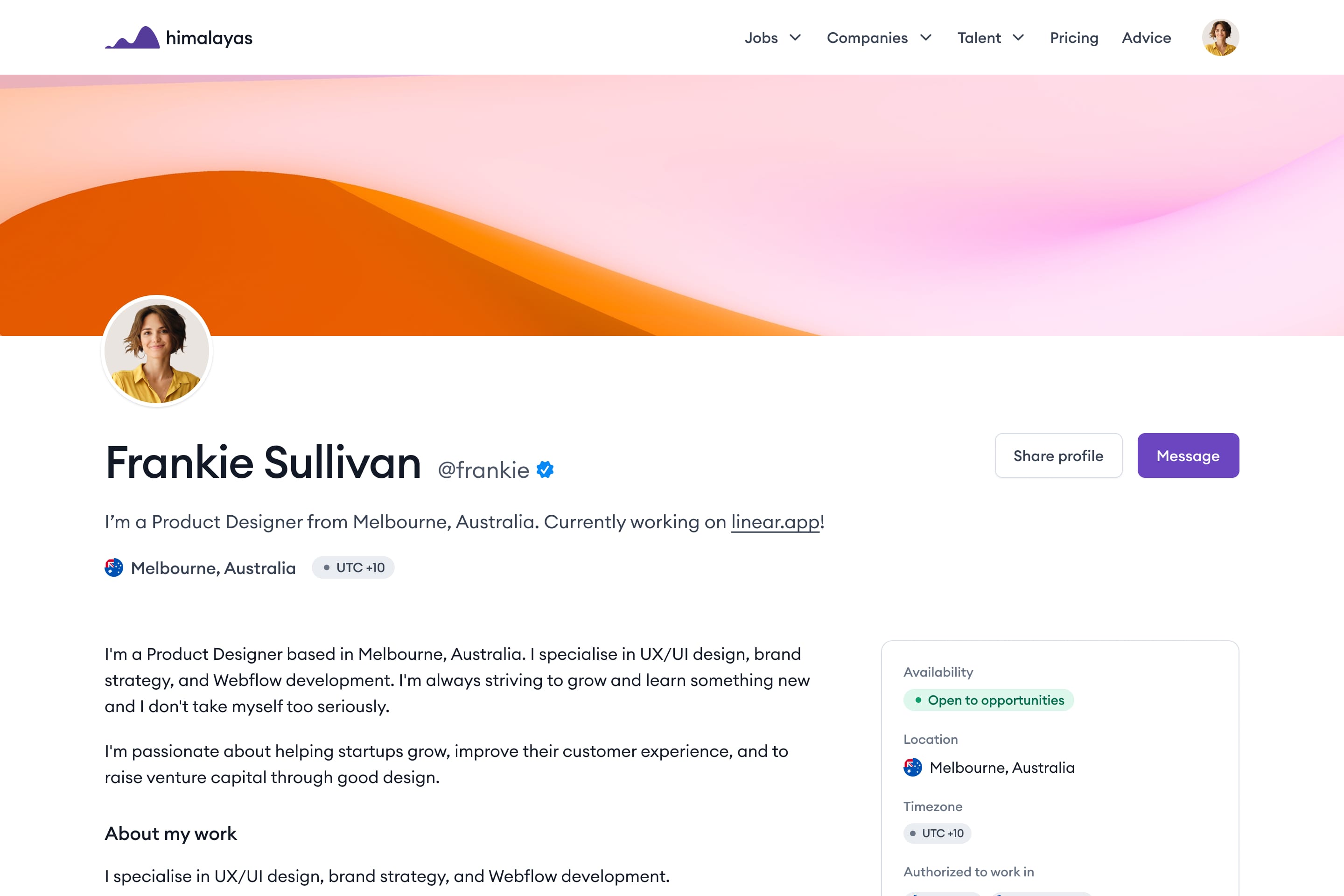