Complete Arc Welder Career Guide
Arc welders are essential craftspeople who fuse metal components using intense electric arcs, creating the structural backbone for everything from towering skyscrapers and bridges to precision machinery and artistic sculptures. This hands-on, highly skilled trade demands precision and expertise, offering a direct path to building tangible products and infrastructure. You will find opportunities to specialize in diverse techniques, making this a rewarding career for those who enjoy working with their hands and seeing immediate results.
Key Facts & Statistics
Median Salary
$48,270 USD
(U.S. national median, BLS, May 2023)
Range: $35,000 - $75,000+ USD
Growth Outlook
2%
(little or no change), slower than average (BLS, 2022-2032)
Annual Openings
≈42,300
openings annually (BLS, 2022-2032)
Top Industries
Typical Education
High school diploma or equivalent, often followed by a welding certificate program or apprenticeship
What is an Arc Welder?
An Arc Welder is a skilled tradesperson who uses intense heat generated by an electric arc to fuse metal components together. This process involves creating a short circuit between an electrode and the metal workpiece, melting both and allowing them to solidify into a strong, unified bond. Arc welders are fundamental to manufacturing, construction, and repair industries, building everything from bridges and pipelines to machinery and vehicles.
Unlike general fabricators who might also cut and shape metal, an Arc Welder specializes specifically in the welding process, focusing on the precision and integrity of the joint. They possess deep knowledge of different welding techniques, metal properties, and safety standards, ensuring that structural integrity and quality are maintained in critical applications. Their expertise is crucial for creating durable and reliable metal structures and products.
What does an Arc Welder do?
Key Responsibilities
- Prepare metal surfaces by cleaning, grinding, or beveling edges to ensure proper fusion during welding.
- Operate various arc welding equipment, including shielded metal arc welding (SMAW) and gas metal arc welding (GMAW), to join metal parts.
- Read and interpret blueprints, welding symbols, and schematics to determine the precise specifications and dimensions of the weld.
- Inspect finished welds for defects such as cracks, porosity, and undercut, using visual inspection and sometimes non-destructive testing methods.
- Maintain welding equipment and tools, performing routine cleaning and minor repairs to ensure optimal performance and safety.
- Adhere strictly to safety protocols and procedures, including wearing personal protective equipment (PPE) and ensuring proper ventilation in the work area.
- Fabricate and assemble metal structures and components according to engineering designs and quality standards.
Work Environment
Arc welders typically work in industrial settings such as manufacturing plants, fabrication shops, construction sites, and repair facilities. The environment can be noisy, dusty, and may involve exposure to fumes and sparks, necessitating strict adherence to safety protocols. Work often involves standing for long periods, bending, and lifting heavy materials. Collaboration is common, often with other welders, fabricators, or construction teams, to ensure projects meet specifications and deadlines.
Schedules are usually full-time, often including overtime, especially in project-driven industries like construction or manufacturing. The pace can be fast, particularly when meeting tight production schedules. Some roles may require travel to different job sites, while others are facility-based. Remote work is generally not an option for this hands-on role.
Tools & Technologies
Arc welders utilize a range of specialized equipment, primarily focusing on different types of arc welding machines such as SMAW (stick welders), GMAW (MIG welders), GTAW (TIG welders), and FCAW (flux-cored arc welders). They work with various electrodes, welding wires, and shielding gases specific to the welding process and base metals. Essential hand tools include grinders, chipping hammers, wire brushes, clamps, and vises for metal preparation and post-weld cleaning.
Safety gear like welding helmets with appropriate shade lenses, flame-resistant clothing, heavy-duty gloves, and safety boots are crucial. Arc welders often use measuring tools such as tape measures, calipers, and squares to ensure accuracy. Depending on the complexity of the job, they may also interact with oxy-fuel cutting equipment or plasma cutters for metal fabrication.
Arc Welder Skills & Qualifications
Becoming a proficient Arc Welder involves a structured progression of skills and certifications. Employers prioritize practical experience and demonstrated competency over academic degrees. A strong portfolio of successful welds, often showcased through on-site practical tests, is crucial for securing positions. Entry-level welders typically start with foundational processes and advance to specialized techniques.
Requirements for Arc Welders vary significantly by industry. For instance, structural welding in construction demands different certifications and safety protocols than pipeline welding in oil and gas, or precision welding in aerospace. Company size also plays a role; larger companies often have more formalized training programs and stricter certification requirements, while smaller shops might value versatility and a broader skill set. Geographic location can influence demand for specific welding processes, with some regions having a higher need for pipe welders and others for fabrication welders.
Formal education, such as a vocational school diploma, provides a strong foundation. However, continuous practical experience and obtaining specific certifications are paramount. Certifications from organizations like the American Welding Society (AWS) are industry standards and often mandatory for specific projects or materials. The field is evolving with new materials and automated welding processes, requiring welders to adapt and continually update their skills to remain competitive.
Education Requirements
Technical Skills
- Shielded Metal Arc Welding (SMAW) - Stick Welding
- Gas Metal Arc Welding (GMAW) - MIG Welding
- Gas Tungsten Arc Welding (GTAW) - TIG Welding
- Flux-Cored Arc Welding (FCAW)
- Blueprint and Welding Symbol Interpretation
- Joint Preparation (beveling, cleaning, fitting)
- Material Identification and Properties (carbon steel, stainless steel, aluminum)
- Welding Safety Procedures and Equipment Operation
- Welding Distortion Control and Heat Management
- Post-Weld Inspection Techniques (visual inspection, basic NDT principles)
- Use and Maintenance of Welding Equipment and Power Sources
- Cutting Processes (oxy-fuel cutting, plasma cutting)
Soft Skills
- Attention to Detail: Arc welding demands extreme precision; even minor inconsistencies can compromise structural integrity and safety.
- Problem-Solving: Welders frequently encounter unexpected material behaviors or fit-up issues, requiring on-the-spot solutions.
- Safety Consciousness: Working with high heat, electricity, and heavy materials requires unwavering adherence to safety protocols to prevent serious injury.
- Physical Stamina and Dexterity: The role involves prolonged standing, bending, and precise hand-eye coordination in often challenging environments.
- Reliability and Consistency: Projects rely on welders producing consistent, high-quality work within deadlines and specifications.
- Adaptability: Welders must adjust techniques for different materials, joint configurations, and environmental conditions.
- Blueprint Reading and Interpretation: Accurately understanding technical drawings is essential for precise execution of welding tasks.
- Team Collaboration: Welders often work as part of a larger construction or manufacturing team, coordinating with fitters, inspectors, and other tradespeople for project success and safety on site.
How to Become an Arc Welder
Becoming an Arc Welder involves several pathways, each with different timelines and advantages. Many enter through vocational schools or community college programs, which typically last 6-18 months and provide hands-on training and certification. Others gain entry through apprenticeships, which combine paid on-the-job training with classroom instruction over 2-5 years, offering comprehensive skill development and often leading to higher earning potential.
Entry strategies can vary significantly by industry and geographic region. For instance, construction sites in urban centers might prioritize welders with specific structural welding certifications, while manufacturing plants could seek those proficient in robotic welding or specialized alloys. Smaller fabrication shops often value generalists who can handle diverse tasks. Misconceptions include believing that a quick course guarantees immediate high-paying work; consistent practice and building a robust portfolio of diverse welds are crucial.
Networking within the trades, attending local industry events, and connecting with experienced welders can open doors to opportunities not advertised publicly. The hiring landscape values proven practical skills and safety adherence above all. Overcoming barriers often means investing in specialized training and personal protective equipment, while continuously practicing and refining techniques to meet industry standards.
Complete a certified welding training program at a vocational school or community college. These programs, typically 6-12 months long, provide foundational knowledge in various welding processes like SMAW (stick), GMAW (MIG), and GTAW (TIG), along with crucial safety protocols. Focus on achieving practical proficiency in at least two common methods.
Obtain relevant welding certifications from recognized bodies such as the American Welding Society (AWS). These certifications validate your skills to potential employers and are often required for specific jobs. Prepare diligently for the practical and written exams, as passing them significantly enhances your employability.
Build a practical portfolio of diverse welding projects and joint types. Document your work with clear photographs or videos, showcasing different materials, thicknesses, and weld quality. This portfolio serves as tangible proof of your capabilities and attention to detail, which is essential for demonstrating your skills to hiring managers.
Seek out entry-level or assistant welding positions, or apply for welding apprenticeships. Entry-level roles allow you to gain real-world experience under supervision, while apprenticeships offer structured learning and mentorship. Focus on opportunities that provide exposure to different welding applications and industry environments.
Network with experienced welders, shop owners, and industry professionals. Attend local trade shows, join professional organizations, and participate in online forums to make connections. These relationships can provide valuable insights, job leads, and mentorship opportunities that accelerate your career progression.
Prepare for and excel in practical welding tests during job interviews. Many employers require a hands-on demonstration of your welding skills on-site. Practice various joint configurations and positions regularly to ensure you can perform under pressure, demonstrating precision, speed, and adherence to safety standards.
Step 1
Complete a certified welding training program at a vocational school or community college. These programs, typically 6-12 months long, provide foundational knowledge in various welding processes like SMAW (stick), GMAW (MIG), and GTAW (TIG), along with crucial safety protocols. Focus on achieving practical proficiency in at least two common methods.
Step 2
Obtain relevant welding certifications from recognized bodies such as the American Welding Society (AWS). These certifications validate your skills to potential employers and are often required for specific jobs. Prepare diligently for the practical and written exams, as passing them significantly enhances your employability.
Step 3
Build a practical portfolio of diverse welding projects and joint types. Document your work with clear photographs or videos, showcasing different materials, thicknesses, and weld quality. This portfolio serves as tangible proof of your capabilities and attention to detail, which is essential for demonstrating your skills to hiring managers.
Step 4
Seek out entry-level or assistant welding positions, or apply for welding apprenticeships. Entry-level roles allow you to gain real-world experience under supervision, while apprenticeships offer structured learning and mentorship. Focus on opportunities that provide exposure to different welding applications and industry environments.
Step 5
Network with experienced welders, shop owners, and industry professionals. Attend local trade shows, join professional organizations, and participate in online forums to make connections. These relationships can provide valuable insights, job leads, and mentorship opportunities that accelerate your career progression.
Step 6
Prepare for and excel in practical welding tests during job interviews. Many employers require a hands-on demonstration of your welding skills on-site. Practice various joint configurations and positions regularly to ensure you can perform under pressure, demonstrating precision, speed, and adherence to safety standards.
Education & Training Needed to Become an Arc Welder
Becoming an Arc Welder primarily involves hands-on skill development, with formal education playing a supportive but not always mandatory role. Vocational schools, community colleges, and dedicated welding institutes offer structured programs that range from certificate courses to associate degrees. These programs typically cost between $5,000 and $20,000 for certificates, and $15,000 to $30,000 for associate degrees, with completion times varying from 6 months to 2 years. Self-study combined with extensive practical experience is also a viable but more challenging path, often taking 1-2 years to build proficiency and requiring an investment in personal equipment.
Employers highly value practical experience and industry certifications, such as those from the American Welding Society (AWS). While a degree can provide a broader theoretical foundation, many employers prioritize candidates with proven welding skills and relevant certifications. Bootcamps and intensive short courses, typically lasting 4-12 weeks and costing $2,000-$10,000, focus on specific welding processes and prepare individuals for certification exams. These options are often preferred by those seeking rapid entry into the workforce.
Continuous learning is crucial for Arc Welders, as new techniques, materials, and equipment emerge regularly. Specialized training in areas like pipe welding, structural welding, or exotic metals can significantly increase earning potential and job opportunities. The cost-benefit analysis often favors shorter, focused programs and certifications for direct job entry, with longer degree programs providing a more comprehensive understanding that can lead to supervisory or inspection roles. Quality programs often boast strong job placement rates and access to industry networks.
Arc Welder Salary & Outlook
Compensation for an Arc Welder varies significantly based on several key factors. Geographic location plays a substantial role; areas with high industrial demand or a higher cost of living, such as the Northeast, Pacific Northwest, or major metropolitan areas, generally offer higher wages. Conversely, regions with lower living costs or less industrial density may see lower pay rates.
Years of experience dramatically impact earning potential. Entry-level positions command starting wages, while experienced welders with specialized certifications, such as those in TIG or MIG welding, or expertise in specific materials like stainless steel or exotic alloys, can secure premium compensation. Performance, particularly the quality and speed of work, also influences pay through bonuses or faster promotions.
Total compensation packages for Arc Welders often extend beyond base salary. These can include overtime pay, which is common given the demand for skilled labor, and production bonuses tied to project completion or efficiency. Comprehensive benefits like health insurance, retirement plans (401k), and paid time off are standard. Some employers also offer allowances for professional development or certification renewals, further enhancing the overall value of the compensation package.
Industry-specific trends also drive salary growth. Specialized fields like aerospace, shipbuilding, or pipeline construction typically offer higher wages due to the precision and critical nature of the work. Unionized positions often provide structured pay scales and benefit packages. Remote work is generally not applicable to this hands-on role, but travel to different project sites can increase earning potential through per diems and travel allowances. While figures are presented in USD, international markets have their own varying rates, often influenced by local demand and economic conditions.
Salary by Experience Level
Level | US Median | US Average |
---|---|---|
Junior Arc Welder | $38k USD | $40k USD |
Arc Welder | $52k USD | $55k USD |
Senior Arc Welder | $68k USD | $70k USD |
Lead Arc Welder | $82k USD | $85k USD |
Welding Supervisor | $92k USD | $95k USD |
Market Commentary
The job market for Arc Welders shows consistent demand, driven by ongoing infrastructure projects, manufacturing, and energy sector needs. The U.S. Bureau of Labor Statistics projects about 24,000 new jobs for welders, cutters, solderers, and brazers over the next decade, indicating a steady growth outlook. This growth is primarily fueled by the need to maintain and upgrade existing infrastructure, including bridges, pipelines, and buildings, alongside new construction initiatives.
Emerging opportunities for Arc Welders are appearing in advanced manufacturing, including robotics and automation integration, where welders are needed to build and maintain automated systems. There is also a rising demand for welders with expertise in specialized techniques like robotic welding programming and laser welding, which command higher wages. The supply and demand dynamics often favor skilled welders, as there is a persistent shortage of highly qualified professionals, especially those with advanced certifications or experience in niche areas.
Technological changes, such as the increasing use of automated welding systems, are transforming the role. While some routine tasks may become automated, skilled Arc Welders will remain essential for complex, custom, or repair work, as well as for overseeing and maintaining these automated systems. This makes the profession relatively recession-resistant, as essential infrastructure and manufacturing require continuous maintenance and development regardless of economic cycles.
Geographic hotspots for Arc Welders include industrial centers in the Midwest, Gulf Coast regions with strong oil and gas sectors, and coastal areas with shipbuilding industries. Continuous learning and obtaining new certifications are crucial for future-proofing an Arc Welder's career, ensuring adaptability to new materials, technologies, and industry standards. This proactive approach helps professionals secure higher-paying roles and navigate evolving job requirements.
Arc Welder Career Path
Career progression for an Arc Welder involves a clear path from foundational skills to advanced specialization and leadership. Advancement hinges on mastering various welding techniques, consistently producing high-quality work, and adhering strictly to safety protocols. Professionals typically progress from individual contributor (IC) roles, focusing on hands-on welding, towards supervisory or specialized technical positions.
Advancement speed depends on several factors, including individual performance, the complexity of projects undertaken, and the specific industry (e.g., manufacturing, construction, energy). Specializing in niche areas like pipe welding, aerospace welding, or exotic materials can accelerate progression and open doors to higher-paying roles. Company size also plays a role; smaller shops might offer quicker advancement to supervisory roles, while larger corporations provide more opportunities for highly specialized IC tracks or extensive management training.
Lateral movement often involves transitioning between different welding processes (e.g., TIG to MIG), or moving into related fields like quality inspection, fabrication, or even welding instruction. Continuous learning, often through certifications in advanced welding techniques or materials, is crucial. Networking within the industry, participating in professional organizations, and building a reputation for precision and reliability significantly aid career growth and open up mentorship opportunities.
Junior Arc Welder
0-2 yearsPerforms basic arc welding tasks under direct supervision, focusing on simple joints and components. Works on production lines or structural fabrication with clear instructions. Responsibilities include preparing materials, setting up basic welding equipment, and executing welds on non-critical parts. Decisions are limited to immediate task execution.
Key Focus Areas
Develop foundational welding skills across common processes like SMAW, GMAW, and FCAW. Prioritize understanding material properties, joint preparation, and basic blueprint reading. Focus on rigorous adherence to all safety regulations and personal protective equipment (PPE) use. Practice consistent bead control and penetration.
Arc Welder
2-5 yearsExecutes a wider range of arc welding tasks with minimal supervision, working on more complex assemblies or critical components. Responsible for setting up and adjusting equipment for various welding processes. Makes independent decisions regarding weld parameters and techniques within established procedures. May train junior welders informally.
Key Focus Areas
Master advanced welding techniques and processes, including TIG and specialized applications. Improve efficiency and speed while maintaining quality standards. Develop troubleshooting skills for welding equipment and common weld defects. Begin to interpret complex blueprints and welding symbols independently.
Senior Arc Welder
5-8 yearsHandles highly complex and critical arc welding projects, often involving specialized materials or intricate designs. Provides technical guidance to other welders and ensures work meets stringent quality and code requirements. Exercises significant autonomy in planning and executing welding operations. May interact with engineering teams on project specifications.
Key Focus Areas
Specialize in demanding welding applications such as pipe welding, exotic metals, or precision fabrication. Focus on optimizing welding procedures for efficiency and material conservation. Develop strong problem-solving skills for complex welding challenges. Start mentoring junior welders and contributing to process improvement.
Lead Arc Welder
8-12 yearsLeads a team of arc welders on specific projects or production lines, overseeing daily operations and ensuring project timelines are met. Responsible for assigning tasks, monitoring progress, and ensuring adherence to quality and safety standards. Acts as the primary technical point of contact for the welding team, troubleshooting issues and providing expert guidance. Conducts initial quality checks.
Key Focus Areas
Develop strong leadership and communication skills to guide welding teams effectively. Focus on project planning, resource allocation, and workflow optimization. Gain expertise in quality control, inspection standards, and non-destructive testing (NDT) methods. Understand production schedules and cost implications of welding operations.
Welding Supervisor
12+ yearsManages the entire welding department or a significant section of it, overseeing multiple teams and projects. Responsible for departmental budgeting, staffing, and performance reviews. Develops and implements welding procedures, ensures compliance with safety regulations, and champions continuous improvement initiatives. Collaborates with other departments like engineering, production, and quality assurance to optimize overall operations.
Key Focus Areas
Cultivate advanced leadership, management, and strategic planning capabilities. Focus on developing and implementing training programs for the welding department. Gain comprehensive knowledge of industry codes, regulatory compliance, and budget management for welding operations. Build strong interpersonal skills for managing diverse teams.
Junior Arc Welder
0-2 yearsPerforms basic arc welding tasks under direct supervision, focusing on simple joints and components. Works on production lines or structural fabrication with clear instructions. Responsibilities include preparing materials, setting up basic welding equipment, and executing welds on non-critical parts. Decisions are limited to immediate task execution.
Key Focus Areas
Develop foundational welding skills across common processes like SMAW, GMAW, and FCAW. Prioritize understanding material properties, joint preparation, and basic blueprint reading. Focus on rigorous adherence to all safety regulations and personal protective equipment (PPE) use. Practice consistent bead control and penetration.
Arc Welder
2-5 yearsExecutes a wider range of arc welding tasks with minimal supervision, working on more complex assemblies or critical components. Responsible for setting up and adjusting equipment for various welding processes. Makes independent decisions regarding weld parameters and techniques within established procedures. May train junior welders informally.
Key Focus Areas
Master advanced welding techniques and processes, including TIG and specialized applications. Improve efficiency and speed while maintaining quality standards. Develop troubleshooting skills for welding equipment and common weld defects. Begin to interpret complex blueprints and welding symbols independently.
Senior Arc Welder
5-8 yearsHandles highly complex and critical arc welding projects, often involving specialized materials or intricate designs. Provides technical guidance to other welders and ensures work meets stringent quality and code requirements. Exercises significant autonomy in planning and executing welding operations. May interact with engineering teams on project specifications.
Key Focus Areas
Specialize in demanding welding applications such as pipe welding, exotic metals, or precision fabrication. Focus on optimizing welding procedures for efficiency and material conservation. Develop strong problem-solving skills for complex welding challenges. Start mentoring junior welders and contributing to process improvement.
Lead Arc Welder
8-12 yearsLeads a team of arc welders on specific projects or production lines, overseeing daily operations and ensuring project timelines are met. Responsible for assigning tasks, monitoring progress, and ensuring adherence to quality and safety standards. Acts as the primary technical point of contact for the welding team, troubleshooting issues and providing expert guidance. Conducts initial quality checks.
Key Focus Areas
Develop strong leadership and communication skills to guide welding teams effectively. Focus on project planning, resource allocation, and workflow optimization. Gain expertise in quality control, inspection standards, and non-destructive testing (NDT) methods. Understand production schedules and cost implications of welding operations.
Welding Supervisor
12+ yearsManages the entire welding department or a significant section of it, overseeing multiple teams and projects. Responsible for departmental budgeting, staffing, and performance reviews. Develops and implements welding procedures, ensures compliance with safety regulations, and champions continuous improvement initiatives. Collaborates with other departments like engineering, production, and quality assurance to optimize overall operations.
Key Focus Areas
Cultivate advanced leadership, management, and strategic planning capabilities. Focus on developing and implementing training programs for the welding department. Gain comprehensive knowledge of industry codes, regulatory compliance, and budget management for welding operations. Build strong interpersonal skills for managing diverse teams.
Job Application Toolkit
Ace your application with our purpose-built resources:
Global Arc Welder Opportunities
Arc welding is a globally vital skill, foundational to construction, manufacturing, and infrastructure projects worldwide. Demand for skilled welders remains consistently high across industrialized and developing nations. While techniques are universal, local building codes and industry standards vary significantly. Many welders seek international work for higher pay or specialized project experience. International certifications like ISO 9606 or AWS D1.1 enhance global mobility.
Global Salaries
Salaries for arc welders vary widely by region and experience. In North America, a skilled arc welder earns between $50,000 and $80,000 USD annually in countries like the United States and Canada. This reflects a high cost of living but also strong demand in construction and energy sectors.
European salaries typically range from €30,000 to €55,000 (approximately $32,000-$60,000 USD) in Germany or Scandinavia, where benefits like robust healthcare and generous vacation time supplement lower base pay. Southern Europe offers lower wages, often €20,000-€35,000 ($21,000-$38,000 USD). Asian-Pacific nations like Australia and New Zealand offer competitive salaries, around AUD 60,000-90,000 ($40,000-$60,000 USD), often with attractive living standards.
In contrast, Latin American countries might offer $15,000-$30,000 USD annually, but the purchasing power of local currencies can make this more substantial. Middle Eastern countries, particularly in the oil and gas sectors, often provide tax-free salaries from $40,000-$70,000 USD, sometimes including accommodation allowances. Tax implications significantly impact take-home pay; for example, Nordic countries have higher income taxes than some Middle Eastern nations. Experience and specialized skills, like pipe welding or working with exotic metals, consistently command higher compensation globally.
Remote Work
True remote work for an arc welder is generally not possible. The nature of the job requires physical presence, specialized equipment, and adherence to on-site safety protocols. Arc welders must operate machinery and perform tasks directly on materials at a specific location.
However, some related roles, such as welding instructors, quality control inspectors, or welding engineers, may involve partial remote work for planning, design, or administrative tasks. Digital nomad opportunities are not applicable to the hands-on nature of arc welding. Employers in this field prioritize on-site presence for production and safety. Salary expectations for welders are tied to their physical labor and location-specific projects.
Visa & Immigration
Skilled worker visas are the primary pathway for arc welders seeking international employment. Popular destinations include Canada (Express Entry, Provincial Nominee Programs), Australia (Skilled Nominated Visa subclass 190, Skilled Independent Visa subclass 189), Germany (EU Blue Card, skilled worker visa), and the UK (Skilled Worker visa). These countries often list welding as an in-demand occupation.
Requirements typically include recognized trade qualifications, several years of experience, and sometimes English or German language proficiency tests. Credential recognition is crucial; applicants often need their qualifications assessed by relevant trade bodies. The application process usually involves submitting an online application, providing documentation, and attending an interview. Processing times vary, from a few months to over a year. Some countries offer pathways to permanent residency after a few years of skilled employment. Family visas are often available for dependents of skilled workers.
2025 Market Reality for Arc Welders
Understanding the current market realities is essential for arc welders planning their next career steps. The industry has seen significant shifts between 2023 and 2025, influenced by post-pandemic recovery, supply chain adjustments, and increasing automation. Broader economic factors, such as inflation and interest rates, directly impact construction and manufacturing, which are key employers for welders.
Market realities for arc welders vary significantly based on experience level—entry-level positions face more competition than highly specialized roles. Geographic location plays a critical role, with demand concentrated in industrial and energy-producing regions. Company size also matters; large fabrication shops might offer stable employment, while smaller custom operations provide diverse project experience. This analysis offers an honest assessment to help welders navigate these complexities.
Current Challenges
Arc welders face increasing competition, particularly for entry-level positions, as automation handles simpler tasks. Economic uncertainty in manufacturing and construction can slow hiring. Adapting to new welding techniques and materials for advanced projects is crucial. Job searches can extend several weeks to a few months for specialized roles.
Growth Opportunities
Despite challenges, strong demand persists for arc welders specializing in niche areas like aerospace, renewable energy infrastructure (wind turbines, solar farms), and pipeline construction. These sectors require high-precision welding on critical components. Emerging opportunities exist in advanced manufacturing where welders work alongside automation, focusing on complex prototypes or repair of robotic systems.
Welders can position themselves advantageously by pursuing certifications in advanced processes, such as certified welding inspector (CWI) or specialized pipe welding. There is an underserved market for welders capable of working with exotic materials like titanium or superalloys, often found in defense or medical device manufacturing. Strategic career moves involve targeting regions with new large-scale industrial projects or investing in training for automated welding system maintenance and programming. Sectors like shipbuilding and custom fabrication remain robust, offering consistent opportunities for skilled craftspeople.
Current Market Trends
Demand for skilled arc welders remains steady, though not rapidly expanding, in 2025. Industrial growth and infrastructure projects drive much of the hiring. However, the integration of robotic welding systems impacts the need for manual welders in high-volume, repetitive production environments. Companies now seek welders with advanced certifications and experience in specialized processes like TIG or orbital welding, moving beyond basic stick welding.
Economic conditions, especially in heavy manufacturing and energy sectors, directly influence job availability. Layoffs in one industry might be offset by growth in another, creating a mixed landscape. Technology trends emphasize precision, efficiency, and material expertise. Employers prioritize candidates who can interpret complex blueprints, perform quality control, and work with exotic alloys, rather than just basic fabrication. Salary trends show modest increases for highly specialized welders but stagnation for those with only fundamental skills. Geographic demand varies, with stronger markets in the Gulf Coast, Midwest industrial hubs, and regions with active construction or shipbuilding. Remote work is not applicable to this hands-on profession.
Emerging Specializations
The field of arc welding is undergoing a significant transformation, driven by advancements in materials science, automation, and digital integration. These technological shifts are creating novel specialization opportunities beyond traditional fabrication and repair. Understanding these emerging niches allows welders to strategically position themselves for career advancement and increased earning potential in 2025 and beyond.
Early adoption and skill development in these cutting-edge areas often lead to premium compensation and accelerated career growth. While established welding specializations remain vital, focusing on emerging fields offers a distinct competitive advantage. These areas are not yet oversaturated, providing a chance to become a leading expert as demand escalates.
Emerging specializations typically take several years to move from niche applications to widespread industry adoption, creating a window for professionals to gain expertise before they become mainstream. This timeline allows for deliberate skill acquisition. However, pursuing highly specialized, nascent fields carries inherent risks, as some trends may not fully materialize. Balancing this risk with the potential for significant rewards requires careful consideration of industry trajectories and personal career goals.
Robotic Additive Manufacturing Welder
This specialization focuses on the precise application of arc welding in additive manufacturing processes, particularly in large-scale metal 3D printing. Welders in this area work with robotic systems and specialized software to build complex components layer by layer. The demand for customized, high-strength metal parts in aerospace, automotive, and heavy industry is driving rapid growth in this field.
Advanced Materials Welding Specialist
Welders specializing in advanced materials work with alloys and composites that require precise heat control and shielding to maintain structural integrity. This includes reactive metals like titanium, nickel-based superalloys, and new generation lightweight materials. Industries such as aerospace, medical devices, and clean energy are increasingly relying on these specialized welding techniques for critical components.
Smart Welding & Data Integration Technician
This area involves the integration of sensors, data analytics, and real-time monitoring into the welding process. Welders utilize smart equipment to collect data on arc stability, penetration, and material deposition, optimizing quality and efficiency. This specialization is crucial for quality assurance in high-stakes environments like nuclear power, defense, and infrastructure projects, where precise documentation and verifiable quality are paramount.
Renewable Energy Infrastructure Welder
This specialization focuses on welding techniques for renewable energy infrastructure, including wind turbine components, solar panel frames, and nascent fusion energy reactors. Welders must adapt to diverse on-site conditions and work with materials optimized for extreme environments. The global push for clean energy solutions ensures sustained demand for these specialized skills in construction and maintenance.
Pros & Cons of Being an Arc Welder
Making a career choice requires a thorough understanding of both the potential benefits and the genuine challenges of a profession. This is particularly true for hands-on roles like an Arc Welder, where the day-to-day realities significantly impact job satisfaction and long-term career viability. Career experiences can vary significantly based on the specific industry, company culture, project complexity, and individual specialization within welding. Furthermore, the pros and cons may shift at different career stages; for instance, physical demands might be more manageable early on but become a challenge later. What one person considers a benefit, such as working independently, another might see as a drawback, like limited team interaction. This assessment aims to provide a realistic, balanced view to help set appropriate expectations.
Pros
- Arc welders are in high demand across many industries, including construction, manufacturing, automotive, and energy, ensuring consistent job opportunities and stability.
- The skills of an arc welder are highly specialized and tangible, providing a clear sense of accomplishment when completing projects and seeing the results of their craftsmanship.
- Arc welding often offers competitive wages, especially for skilled and certified professionals, with opportunities for overtime pay on urgent or large-scale projects.
- There are diverse work environments available for arc welders, ranging from large industrial plants and shipyards to smaller fabrication shops or mobile welding services, offering variety in daily tasks.
- Entry into the arc welding profession typically requires vocational training or an apprenticeship, which is generally less time-consuming and costly than a four-year college degree.
- Experienced arc welders have clear pathways for career advancement, including becoming a certified welding inspector, supervisor, or even starting their own welding business.
- The ability to create and repair essential structures and products provides a strong sense of contribution and importance to various industries and infrastructure projects.
Cons
- Arc welders face significant safety risks, including exposure to intense UV radiation, fumes, gases, and extreme heat, which necessitates strict adherence to safety protocols and the consistent use of personal protective equipment.
- The work environment for an arc welder is often physically demanding, requiring prolonged standing, kneeling, bending, and lifting heavy materials or equipment in various industrial settings.
- Arc welding can be repetitive, involving similar motions and tasks for extended periods, which may lead to boredom or musculoskeletal strain over time.
- Job sites for arc welders can vary widely, from comfortable indoor shops to outdoor construction sites exposed to harsh weather, or confined spaces with limited ventilation.
- The demand for arc welders can fluctuate with economic cycles, especially in industries like construction or manufacturing, potentially leading to periods of reduced work or layoffs.
- Continuous training and certification updates are often required to maintain proficiency with new welding techniques, materials, and safety standards, which can be time-consuming and costly.
- The noise levels in welding environments are frequently high, necessitating hearing protection and potentially contributing to long-term hearing impairment if not adequately managed.
Frequently Asked Questions
Arc Welders face distinct challenges around safety, precision, and physical demands, making this role unique within the skilled trades. This section addresses the most common questions about entering this hands-on career, from mastering specific welding techniques to understanding job site conditions and long-term career prospects.
What is the typical starting salary for an Arc Welder, and how much can I expect to earn with experience?
Entry-level Arc Welders typically earn between $35,000 and $45,000 annually, varying by location, industry, and specific certifications. With experience, specialized skills like pipe welding, and advanced certifications, salaries can increase significantly, often reaching $60,000 to $80,000 or more for highly skilled professionals. Overtime opportunities are common and can boost earnings considerably.
How long does it take to become a certified and job-ready Arc Welder if I'm starting without experience?
Becoming a proficient Arc Welder generally takes 6 to 18 months of dedicated training, depending on your chosen path. Vocational schools or community college programs often run for 6-12 months, providing hands-on experience and certification preparation. Apprenticeships can take 3-5 years but offer paid on-the-job training alongside classroom instruction, making you job-ready throughout the process.
What are the physical demands and typical working conditions for an Arc Welder?
Arc welding is physically demanding, requiring good hand-eye coordination, steady hands, and the ability to work in various positions, including confined spaces or at heights. You will lift heavy materials, stand for long periods, and work in environments with heat, fumes, and noise. Physical fitness and stamina are crucial for long-term success and injury prevention in this trade.
Is there a good job market for Arc Welders, and what industries hire them most?
Yes, the demand for skilled Arc Welders remains strong across various industries, including construction, manufacturing, energy, and infrastructure. Many experienced welders are retiring, creating a consistent need for new talent. Specializing in niche areas like underwater welding or pipeline welding can further enhance job security and open up higher-paying opportunities.
What are the typical career advancement opportunities for an Arc Welder?
Career advancement for an Arc Welder can involve specializing in advanced techniques like TIG or MIG welding, becoming a certified welding inspector, or moving into supervisory roles. Many welders also transition into related fields such as fabrication management, welding instruction, or starting their own mobile welding businesses. Continuous learning and new certifications are key to progression.
Do I need a college degree to become an Arc Welder, or are there alternative education paths?
No, you do not need a college degree to become a successful Arc Welder. Most employers prioritize practical skills, certifications, and hands-on experience. Vocational training programs, community college courses, and apprenticeships are the most common and effective pathways. These programs focus on developing the specific techniques and safety knowledge required for the job.
What is the typical work-life balance for an Arc Welder, and how much travel is involved?
Work-life balance for an Arc Welder varies significantly by industry and project. Some roles offer consistent day shifts, while others may involve long hours, night shifts, or extensive travel for project-based work, particularly in construction or oil and gas. Project deadlines and client needs often dictate schedules, so flexibility and adaptability are important for maintaining balance.
Related Careers
Explore similar roles that might align with your interests and skills:
Mig Welder
A growing field with similar skill requirements and career progression opportunities.
Explore career guideWelder
A growing field with similar skill requirements and career progression opportunities.
Explore career guideWelder Fabricator
A growing field with similar skill requirements and career progression opportunities.
Explore career guideMachine Welder
A growing field with similar skill requirements and career progression opportunities.
Explore career guideSub Arc Operator
A growing field with similar skill requirements and career progression opportunities.
Explore career guideAssess your Arc Welder readiness
Understanding where you stand today is the first step toward your career goals. Our Career Coach helps identify skill gaps and create personalized plans.
Skills Gap Analysis
Get a detailed assessment of your current skills versus Arc Welder requirements. Our AI Career Coach identifies specific areas for improvement with personalized recommendations.
See your skills gapCareer Readiness Assessment
Evaluate your overall readiness for Arc Welder roles with our AI Career Coach. Receive personalized recommendations for education, projects, and experience to boost your competitiveness.
Assess your readinessLand your dream job with Himalayas Plus
Upgrade to unlock Himalayas' premium features and turbocharge your job search.
Himalayas
Himalayas Plus
Himalayas Max
Find your dream job
Sign up now and join over 100,000 remote workers who receive personalized job alerts, curated job matches, and more for free!
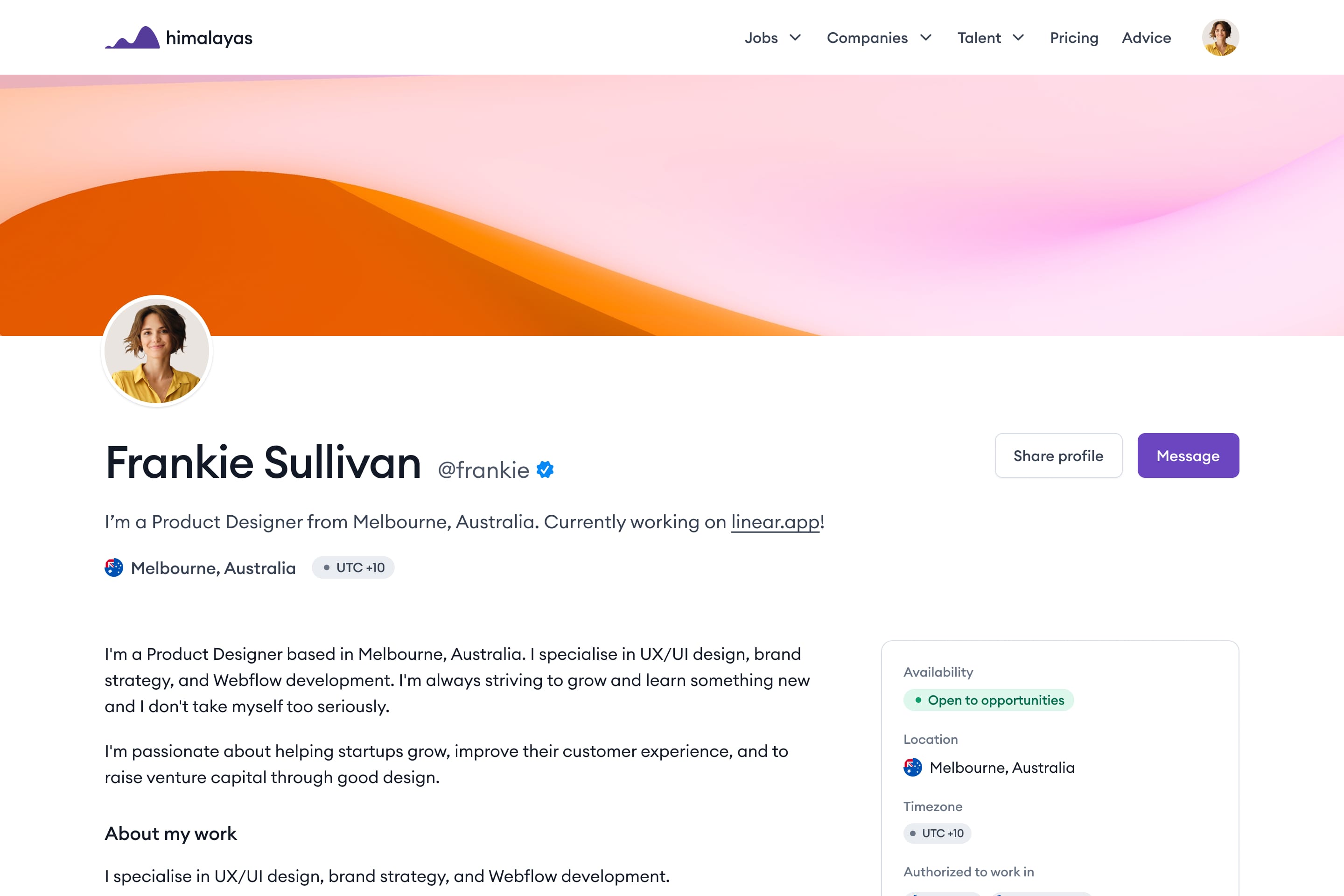