Complete Smelter Operator Career Guide
Smelter operators are the backbone of primary metal production, transforming raw materials like ore into essential metals crucial for manufacturing, infrastructure, and technology. This hands-on role involves overseeing high-temperature processes, ensuring efficiency and safety in environments that demand precision and adherence to strict protocols. It's a vital career for those who thrive in industrial settings and want to contribute to the foundational elements of modern society, offering stable employment and a direct impact on global supply chains.
Key Facts & Statistics
Median Salary
$62,910 USD
(U.S. Bureau of Labor Statistics, May 2023)
Range: $45k - $85k+ USD (U.S. national range, varies by experience and location)
Growth Outlook
2%
slower than average (U.S. Bureau of Labor Statistics, 2022-2032)
Annual Openings
≈6,000
openings annually (U.S. Bureau of Labor Statistics, 2022-2032)
Top Industries
Typical Education
High school diploma or equivalent, with on-the-job training; some employers prefer vocational training or an associate's degree in a related field.
What is a Smelter Operator?
A smelter operator is a skilled industrial professional responsible for the critical process of extracting raw metals from ore concentrates or recycled materials through intense heat. They manage and control large-scale furnaces and associated equipment to melt down metal-bearing materials, separate impurities, and produce purified molten metal. This role is fundamental to the primary metals industry, including copper, aluminum, lead, and zinc production.
Unlike a general furnace operator who might manage heat treatment or melting for casting, a smelter operator specifically focuses on the chemical reduction and refining of raw ore into its base metal form. They are the frontline experts in metallurgical processing, ensuring the efficient and safe transformation of raw materials into valuable metallic products used across countless industries.
What does a Smelter Operator do?
Key Responsibilities
- Monitor and control smelting furnaces, ensuring optimal temperature, pressure, and material flow for efficient metal extraction.
- Charge raw materials, such as ore concentrates, fluxing agents, and recycled scrap, into the smelting furnace using various loading mechanisms.
- Operate and maintain heavy machinery, including forklifts, loaders, and overhead cranes, to transport materials and manage furnace operations.
- Conduct regular inspections of equipment, refractory linings, and ventilation systems, identifying and reporting any malfunctions or safety hazards.
- Collect samples of molten metal and slag for laboratory analysis, adjusting process parameters based on metallurgical test results.
- Manage the pouring and casting of molten metal into molds or ladles, ensuring proper cooling and solidification processes.
- Adhere strictly to safety protocols, environmental regulations, and operational procedures to prevent accidents and minimize emissions.
Work Environment
Smelter operators primarily work in industrial facilities, often within hot, noisy, and dusty environments. The work involves exposure to high temperatures from molten metal and furnaces, requiring stringent safety precautions and personal protective equipment. Shifts typically operate on a rotating basis, including nights, weekends, and holidays, to maintain continuous production. The role demands strong teamwork and clear communication with fellow operators, engineers, and maintenance staff. The pace is often fast, requiring constant vigilance and quick decision-making in a potentially hazardous setting. The job is physically demanding, involving standing, walking, and sometimes lifting heavy objects.
Tools & Technologies
Smelter operators regularly use and monitor large-scale industrial equipment, including electric arc furnaces, blast furnaces, reverberatory furnaces, and induction furnaces. They operate heavy machinery such as forklifts, front-end loaders, and overhead cranes for material handling. Key tools include thermocouples for temperature measurement, pressure gauges, flow meters, and control panels for process monitoring and adjustment. They also work with specialized refractory materials for furnace lining maintenance. Safety gear, including heat-resistant clothing, respirators, and eye protection, is essential. Communication systems like two-way radios facilitate coordination within the plant.
Smelter Operator Skills & Qualifications
A Smelter Operator's qualification landscape emphasizes practical experience and safety certifications over traditional academic degrees. Employers prioritize hands-on competency in operating heavy machinery and understanding metallurgical processes. Requirements vary significantly based on the type of smelter (e.g., aluminum, copper, steel), the specific technology used, and the scale of operations.
Entry-level positions often require a high school diploma or equivalent, coupled with vocational training or an apprenticeship. Senior roles, such as Lead Smelter Operator or Shift Supervisor, demand extensive experience, often five to ten years, along with demonstrated leadership and advanced troubleshooting abilities. Smaller operations might accept less formal training if a candidate possesses a strong work ethic and a willingness to learn on the job.
Certifications in forklift operation, crane operation, hazardous materials handling, and confined space entry are crucial and often mandatory. These credentials signal a commitment to safety and operational proficiency. While formal education is less critical, a strong understanding of chemistry, physics, and metallurgy provides a significant advantage, particularly for career advancement. The industry is evolving with automation and advanced process controls, requiring operators to adapt to more technologically driven tasks and understand digital interfaces. This shift means a balance of traditional mechanical aptitude and emerging digital literacy is becoming increasingly valuable.
Education Requirements
Technical Skills
- Smelting process operation and control (e.g., blast furnace, electric arc furnace, reverberatory furnace)
- Heavy equipment operation (e.g., overhead cranes, forklifts, loaders, mobile equipment)
- Process control systems (DCS/SCADA) monitoring and basic adjustments
- Refractory material handling and maintenance principles
- Temperature and pressure gauge reading and interpretation
- Molten metal tapping and casting procedures
- Chemical and metallurgical principles (e.g., oxidation, reduction, slag formation)
- Emergency response procedures (e.g., spill containment, fire suppression)
- Basic mechanical troubleshooting and preventative maintenance checks
- Material handling and storage best practices
- Lockout/Tagout (LOTO) procedures and confined space entry protocols
- Use of personal protective equipment (PPE) and safety protocols
Soft Skills
- Attention to Detail: Critical for monitoring process parameters, identifying anomalies, and ensuring product quality while preventing equipment damage or safety incidents.
- Problem-Solving: Essential for quickly diagnosing and resolving operational issues, equipment malfunctions, or unexpected process deviations to minimize downtime and maintain production.
- Situational Awareness: Vital for recognizing potential hazards, understanding the overall plant environment, and reacting appropriately to rapidly changing conditions to ensure personal and team safety.
- Adherence to Procedures: Crucial for consistently following strict safety protocols, standard operating procedures, and environmental regulations to prevent accidents and maintain compliance.
- Teamwork and Collaboration: Necessary for coordinating tasks with other operators, maintenance personnel, and supervisors, ensuring smooth shift transitions and efficient overall plant operation.
- Stress Management: Important for remaining calm and effective under pressure, especially during equipment breakdowns, emergency situations, or when facing tight production deadlines.
- Communication Skills: Key for clear and concise reporting of operational status, equipment issues, and safety concerns to supervisors and colleagues, both verbally and in written logs.
- Physical Stamina and Endurance: Required for performing tasks in hot, noisy, and physically demanding environments, often involving lifting, standing, and moving heavy materials for extended periods.
How to Become a Smelter Operator
Entering the Smelter Operator field involves a blend of industrial skills, safety adherence, and physical aptitude. Traditional entry often occurs through vocational training or entry-level laborer positions within smelters, where individuals learn on the job and advance. Non-traditional paths might include transitioning from other heavy industrial roles, leveraging existing mechanical or electrical experience.
Timeline expectations vary; a complete beginner might spend 6-12 months in an entry-level role before being considered for operator training, while someone with relevant industrial experience could transition in 3-6 months. The hiring landscape is often tied to commodity prices and plant operational cycles. Larger corporations typically have structured training programs, while smaller operations might rely more on direct on-the-job learning. Geographic location heavily influences opportunities, with most roles concentrated near mineral deposits or processing hubs.
A common misconception is that this role requires only brute strength; in reality, precision, attention to detail, and a strong understanding of complex machinery and chemical processes are crucial. Networking within industrial communities and expressing genuine interest in the smelting process can open doors. Overcoming barriers often involves demonstrating reliability, a strong work ethic, and a commitment to safety protocols, which are paramount in this high-risk environment.
Step 1
Step 2
Step 3
Step 4
Step 5
Step 6
Education & Training Needed to Become a Smelter Operator
Becoming a Smelter Operator primarily involves hands-on training and specific vocational certifications rather than traditional university degrees. While some foundational knowledge in chemistry or metallurgy from a two-year associate's program can be beneficial, it is rarely a strict requirement. The industry values practical experience and adherence to safety protocols above all else. Formal programs like vocational school certificates or apprenticeships typically range from 6 to 18 months, costing between $5,000 and $15,000. These pathways offer focused training on smelting processes, equipment operation, and critical safety procedures.
In contrast, direct entry positions often involve on-the-job training, which can span 1 to 3 years. This self-study or employer-led training is often unpaid during the initial learning phase, but it provides immediate exposure to the operational environment. Employers highly value candidates with proven safety records and mechanical aptitude. While a four-year degree is generally unnecessary, continuous learning through industry-specific workshops on new technologies or advanced safety standards remains crucial for career progression. The market perception strongly favors practical, hands-on skills over theoretical academic credentials for this role.
The cost-benefit analysis for a Smelter Operator points towards vocational training or direct entry. These paths offer a quicker entry into the workforce and a faster return on investment compared to a more expensive, time-consuming degree. Specific certifications in areas like hazardous materials handling, confined space entry, or heavy equipment operation significantly enhance employability. These certifications often cost a few hundred to a few thousand dollars each and can be completed in days or weeks. Geographic availability of quality programs often aligns with regions having active smelting operations, with many companies offering internal training programs.
Smelter Operator Salary & Outlook
Compensation for a Smelter Operator is influenced by several critical factors, extending beyond base salary. Geographic location significantly impacts earnings; operators in regions with major mining and metallurgical industries, such as Nevada, Arizona, or parts of the Pacific Northwest, often see higher pay dueings to concentrated demand and higher cost of living. Conversely, areas with fewer smelting operations may offer lower wages. International markets also present variations, but the figures provided here are benchmarked against USD.
Experience and specialized skills like advanced furnace operation, refractory maintenance, or specific metal processing techniques create dramatic salary variations. Total compensation packages frequently include overtime pay, which can substantially boost annual earnings due to the continuous nature of smelting operations. Performance bonuses tied to production targets, safety records, or efficiency improvements are also common.
Beyond cash compensation, benefits packages are a significant component. These typically include comprehensive health insurance, retirement contributions such as 401(k) plans, and paid time off. Some companies offer allowances for professional development or certifications in metallurgy or safety. Larger corporations with multiple facilities often provide more robust benefits and structured career progression than smaller, independent operations. Remote work is not applicable to this hands-on role.
Salary by Experience Level
Level | US Median | US Average |
---|---|---|
Junior Smelter Operator | $52k USD | $55k USD |
Smelter Operator | $65k USD | $68k USD |
Senior Smelter Operator | $77k USD | $80k USD |
Lead Smelter Operator | $88k USD | $92k USD |
Smelting Supervisor | $100k USD | $105k USD |
Market Commentary
The job market for Smelter Operators is stable, driven by the continuous demand for refined metals across various industries, including construction, automotive, and electronics. The U.S. Bureau of Labor Statistics projects a modest growth for metal and plastic machine workers, a category that includes smelter operators, with a general outlook of about 2% through 2032. This growth is slower than the average for all occupations, reflecting increasing automation in some processes.
Current trends show a focus on efficiency and environmental compliance within the smelting industry. This creates emerging opportunities for operators skilled in advanced process control systems, emission reduction technologies, and waste management. The demand for specific metals, like copper and aluminum, remains strong, underpinning the need for skilled operators. However, the supply of new, skilled operators can be limited, creating localized demand imbalances.
Automation and AI are increasingly integrated into smelting operations, particularly in monitoring, quality control, and raw material handling. While this may reduce the need for purely manual tasks, it increases the demand for operators with strong technical skills to manage and troubleshoot these sophisticated systems. Future-proofing this career involves continuous learning in process automation, data interpretation, and environmental regulations. Geographically, states with established mining and metals industries will remain primary employment hubs.
Smelter Operator Career Path
Career progression for a Smelter Operator involves a clear path from entry-level roles to supervisory positions, emphasizing hands-on experience, safety adherence, and a deep understanding of metallurgical processes. Individuals typically advance by demonstrating consistent operational proficiency, problem-solving skills, and a commitment to safety protocols.
Advancement speed depends on factors like individual performance, the complexity of the smelting operations, and the size of the facility. Larger operations often have more structured progression paths and specialized roles, while smaller smelters may offer broader responsibilities earlier. Continuous learning, often through internal training and specific certifications related to furnace types or metal processing, also drives progression.
The career path in smelting is primarily an individual contributor (IC) track focused on operational excellence. However, opportunities exist to transition into management or leadership roles, moving from direct operational tasks to overseeing teams and processes. Lateral moves might involve specializing in different types of metals or furnace technologies, or moving into roles like quality control or maintenance planning within the same facility.
Junior Smelter Operator
0-2 yearsKey Focus Areas
Smelter Operator
2-5 yearsKey Focus Areas
Senior Smelter Operator
5-8 yearsKey Focus Areas
Lead Smelter Operator
8-12 yearsKey Focus Areas
Smelting Supervisor
12+ years total experience, 2+ years as Lead OperatorKey Focus Areas
Junior Smelter Operator
0-2 yearsAssists experienced operators with routine tasks such as charging furnaces, tapping molten metal, and monitoring basic control parameters. Works under direct supervision, primarily focusing on learning and adhering to all safety regulations. Handles material preparation and clean-up duties.
Key Focus Areas
Develop foundational knowledge of furnace operations, material handling, and basic safety procedures. Learn to identify common operational issues and report them promptly. Focus on mastering routine tasks and understanding the flow of materials through the smelting process.
Smelter Operator
2-5 yearsOperates smelting furnaces and related equipment independently, ensuring optimal process conditions for metal production. Monitors gauges, controls, and alarms, making real-time adjustments to maintain product quality and operational efficiency. Identifies and resolves minor operational issues.
Key Focus Areas
Master advanced operational techniques, including precise temperature control, slag management, and metal refining. Develop strong troubleshooting skills for equipment malfunctions and process deviations. Focus on optimizing efficiency and minimizing waste while maintaining strict safety standards.
Senior Smelter Operator
5-8 yearsLeads specific shifts or sections of the smelting operation, providing guidance to less experienced operators. Handles complex operational challenges, including significant process adjustments and equipment troubleshooting. Ensures compliance with environmental regulations and production targets for their area.
Key Focus Areas
Take initiative in process improvement projects and contribute to standard operating procedure (SOP) development. Mentor junior operators and share expertise on complex operational scenarios. Develop a deeper understanding of metallurgical chemistry and its impact on product quality.
Lead Smelter Operator
8-12 yearsActs as the primary operational lead on a shift, coordinating the activities of a team of smelter operators. Makes critical real-time decisions regarding process adjustments, equipment utilization, and emergency response. Reports directly to the Smelting Supervisor and assists with production planning.
Key Focus Areas
Lead by example in safety and operational excellence, fostering a culture of continuous improvement. Develop strong communication and coordination skills to manage shift activities effectively. Begin to understand production planning and resource allocation at a higher level.
Smelting Supervisor
12+ years total experience, 2+ years as Lead OperatorManages and oversees all smelting operations for a designated area or shift, ensuring production goals are met safely and efficiently. Responsible for scheduling, training, and performance management of smelting teams. Collaborates with maintenance, quality control, and engineering departments to optimize overall plant performance.
Key Focus Areas
Cultivate leadership and team management skills, including performance evaluation and conflict resolution. Develop strategic planning abilities for production scheduling and resource management. Focus on budgeting, cost control, and implementing new technologies or processes effectively.
Job Application Toolkit
Ace your application with our purpose-built resources:
Smelter Operator Cover Letter Examples
Personalizable templates that showcase your impact.
View examplesSmelter Operator Job Description Template
Ready-to-use JD for recruiters and hiring teams.
View examplesGlobal Smelter Operator Opportunities
Smelter operators find consistent global demand in countries with active mining and metallurgical industries. This profession involves overseeing the high-temperature processing of ores to extract metals, a critical step in industrial supply chains worldwide. Cultural differences impact workplace safety standards and operational protocols, while regulatory frameworks dictate environmental compliance. International opportunities arise from new plant constructions or expansions in regions rich in mineral resources. While no single international certification exists, experience with specific smelting technologies or safety protocols can facilitate global mobility.
Global Salaries
Smelter operator salaries vary significantly by region, reflecting local economic conditions and industry scale. In North America, particularly Canada and the United States, annual salaries range from USD 50,000 to USD 80,000. This range reflects higher living costs but also robust industrial sectors. European countries like Germany or Norway offer EUR 40,000 to EUR 65,000 (approximately USD 43,000 to USD 70,000), where comprehensive social benefits and longer vacation times often supplement the base pay.
Australia presents strong compensation, with salaries typically ranging from AUD 70,000 to AUD 100,000 (around USD 46,000 to USD 66,000), driven by its extensive mining operations. Latin American nations such as Chile or Peru, key copper producers, offer lower nominal salaries, often USD 25,000 to USD 45,000, but these provide higher purchasing power due to significantly lower living expenses. Asian markets like China or India pay USD 15,000 to USD 30,000, reflecting lower local wages, though some multinational operations may offer competitive packages.
Salary structures also differ. North America often includes performance bonuses, while Europe emphasizes robust healthcare and pension contributions. Tax implications vary widely; for instance, Scandinavian countries have higher income taxes but provide extensive public services. Experience and specialized skills, such as operating specific types of furnaces or advanced control systems, can significantly increase compensation globally. There are no standardized international pay scales, making local market research essential.
Remote Work
Smelter operator roles inherently require on-site presence due to the hands-on nature of the work. Operators must be physically present to monitor equipment, manage processes, and respond to immediate operational needs in high-temperature, high-risk environments. This profession offers virtually no international remote work opportunities.
Digital nomad lifestyles or countries with favorable remote work policies do not apply to this role. While some supervisory or engineering roles within the metallurgical industry might have remote components for planning or analysis, the core function of a smelter operator remains deeply tied to the physical plant. Equipment setup, internet requirements, or workspace considerations for remote work are not relevant for this position.
Visa & Immigration
Smelter operators seeking international work typically pursue skilled worker visas. Countries like Canada, Australia, and parts of Europe (e.g., Germany, Sweden) have specific immigration streams for skilled trades, often requiring a job offer. These visas usually fall under categories for industrial or manufacturing roles. Requirements commonly include relevant work experience, vocational qualifications, and sometimes an English or local language proficiency test.
Credential recognition for vocational training is crucial; some countries may require skills assessments or equivalency tests. The visa application process can take several months to over a year, depending on the country and visa type. Employers often sponsor these visas, particularly for specialized roles or in regions facing labor shortages. Pathways to permanent residency can exist after several years of continuous employment, aligning with national immigration policies.
Family visas are generally available for spouses and dependents of skilled worker visa holders, allowing them to accompany the operator. Language requirements vary; for instance, Canada often requires IELTS, while Germany may need a basic level of German for integration. Some countries prioritize skilled trades, potentially offering a smoother immigration process for qualified smelter operators. Understanding each country's specific labor market needs and immigration points systems is vital for successful international relocation.
2025 Market Reality for Smelter Operators
Understanding current market conditions is crucial for smelter operators to navigate a transforming industry. The sector has seen shifts driven by global supply chain changes and increased focus on sustainability.
Post-pandemic, commodity demand fluctuated, impacting smelter output, while the AI revolution indirectly influences operational efficiency through automation. Broader economic factors like infrastructure spending and manufacturing output directly dictate demand for smelted materials. Market realities vary significantly by metal type, facility age, and geographic location, making a tailored understanding vital for career planning.
Current Challenges
Smelter operators face significant challenges from declining domestic primary metal production and increased recycling, which reduces demand for new smelting. Automation of material handling and furnace control also displaces some roles. Furthermore, stringent environmental regulations increase operational costs, sometimes leading to plant closures or reduced output. Job seekers must also contend with the remote locations of many facilities, requiring relocation or long commutes.
Growth Opportunities
Despite challenges, opportunities exist for smelter operators. Facilities focusing on rare earth metals, battery components, or specialized alloys are experiencing growth. Operators with expertise in pyrometallurgy or hydrometallurgy for these specific materials are in high demand.
Emerging opportunities also lie in metal recycling and refining operations, which are expanding due to sustainability mandates. Operators skilled in advanced process control systems, data analysis for operational efficiency, and environmental compliance protocols gain a significant competitive edge. Certifications in hazardous material handling and advanced safety practices are also highly valued.
Some older facilities are upgrading their technology, creating roles for operators who can adapt to new digital interfaces and troubleshoot complex machinery. Strategic career moves include specializing in niche metal processing or pursuing roles in facilities with strong environmental records and modernization plans. The market correction in some industrial sectors might create opportunities for operators to move into more stable or high-growth segments within the broader metals industry.
Current Market Trends
The market for smelter operators is stable but not expanding in 2025. Demand for primary metal production is shifting globally, with some domestic facilities facing reduced output or closures. Automation and process optimization are reducing the need for manual oversight, particularly in material loading and furnace monitoring. Companies seek operators with strong understanding of automated systems and data interpretation.
Economic conditions, particularly in manufacturing and construction, directly influence demand for smelted metals. A slowdown in these sectors can lead to production cuts and hiring freezes. Generative AI is not directly impacting operator roles, but advanced analytics and predictive maintenance tools are becoming standard. These tools require operators to interpret data and troubleshoot complex systems rather than just perform manual tasks.
Employer requirements now emphasize safety certifications, environmental compliance knowledge, and proficiency with digital control interfaces. Salaries for experienced operators remain competitive due to specialized skills and hazardous working conditions, but entry-level saturation is not a major issue as training is often on-the-job. Geographic variations are pronounced; opportunities are concentrated near existing smelters, often in specific industrial regions, with limited remote work options.
Emerging Specializations
The smelting industry, while foundational, is undergoing significant transformation driven by advancements in material science, automation, and environmental regulations. These shifts create new specialization opportunities for smelter operators who are willing to adapt and acquire new skills. Understanding these future-oriented paths is crucial for career advancement and securing high-value roles beyond 2025.
Early positioning in emerging areas often commands premium compensation and accelerated career growth. As new technologies become standard, demand for operators with specialized knowledge in these fields increases, leading to higher earning potential and more leadership opportunities. This strategic choice helps professionals differentiate themselves in a evolving market.
While established specializations remain vital, focusing exclusively on traditional methods limits long-term growth. Emerging areas, though initially niche, are rapidly moving towards mainstream adoption, creating significant job opportunities within the next 3-7 years. Evaluating the risk and reward of specializing in cutting-edge areas involves assessing the investment in new training against the potential for significant career dividends. Those who embrace these changes will be at the forefront of the industry's evolution.
Automated Smelting Systems Operator
This specialization focuses on operating and maintaining advanced robotic systems and automated machinery used in modern smelting processes. These systems handle tasks like material loading, furnace tapping, and product handling, significantly improving safety and efficiency. Operators in this area ensure the seamless integration of robotics with human oversight, troubleshooting complex automated sequences.
Green Smelting & Carbon Capture Operator
With increasing global emphasis on carbon reduction, this specialization involves operating and optimizing smelters equipped with carbon capture and storage (CCS) technologies. Operators focus on monitoring CO2 capture rates, managing capture equipment, and ensuring compliance with environmental standards. This role is critical for reducing the industry's environmental footprint and meeting regulatory requirements.
Digital Twin & Predictive Maintenance Specialist
This area focuses on operating and maintaining advanced digital twins and predictive maintenance systems within the smelter. Operators use real-time data from sensors and historical performance to anticipate equipment failures, optimize operational parameters, and improve overall plant efficiency. This proactive approach minimizes downtime and maximizes output.
Complex Feedstock & Recycling Smelter Operator
This specialization involves operating and managing smelters that process complex and diverse raw materials, including recycled metals and electronic waste. Operators must understand the varying compositions of these materials and adjust smelting parameters to ensure efficient recovery and purity. This area addresses the growing need for circular economy practices in metal production.
Energy Recovery Smelter Operator
This emerging role centers on operating smelters that incorporate advanced energy recovery and waste heat utilization systems. Operators monitor and control systems designed to capture and repurpose waste heat from the smelting process for electricity generation or other industrial uses. This specialization is vital for improving energy efficiency and reducing operational costs.
Pros & Cons of Being a Smelter Operator
Making informed career decisions requires a clear understanding of both the benefits and challenges of a profession. The experience within any career field, including that of a Smelter Operator, can vary significantly based on factors such as the specific company, the type of metals being processed, and individual personality. What one person considers a benefit, another might see as a challenge, reflecting diverse values and lifestyle preferences. Additionally, the demands and rewards of a role can evolve as an individual progresses from an entry-level position to a more senior or specialized one. This assessment provides an honest, balanced perspective to help potential Smelter Operators set realistic expectations for this demanding but essential industrial role.
Pros
- Smelter operators typically receive competitive wages, often above the industrial average, due to the specialized skills, hazardous working conditions, and critical nature of their role in metal production. Many companies also offer shift differentials for night or weekend work, further boosting income.
- The demand for skilled smelter operators remains consistent as long as there is a need for primary metal production, offering good job security in a foundational industry. Experienced operators with a strong safety record are particularly sought after.
- Working as a smelter operator provides opportunities to develop highly specialized skills in metallurgy, furnace operation, process control, and heavy machinery. These skills are valuable within the metals industry and can lead to advancement to supervisory or technical specialist roles.
- The work involves direct interaction with large-scale industrial processes and the transformation of raw materials into essential metals, which many operators find intellectually stimulating and rewarding. There is a tangible sense of accomplishment in contributing to the production of vital materials.
- Many smelter operations offer comprehensive benefits packages, including health insurance, retirement plans, and paid time off, which are often more robust than those found in less hazardous or less unionized industrial sectors.
- Smelter operations are typically team-oriented environments, requiring close coordination and communication among operators, maintenance staff, and supervisors. This fosters a strong sense of camaraderie and teamwork among colleagues.
- Entry-level positions often require a high school diploma or equivalent, with on-the-job training provided, making it an accessible career path without the need for extensive higher education. Vocational training or certifications can further enhance opportunities but are not always mandatory.
Cons
- Smelter operators work in extremely high-temperature environments, often exceeding 10000C, which requires constant vigilance to prevent heat stress and exhaustion. Prolonged exposure to intense heat can lead to significant physical discomfort and health risks over time.
- There is a significant risk of exposure to hazardous materials, including molten metal, toxic fumes (sulfur dioxide, carbon monoxide), and heavy metals. Operators must strictly adhere to safety protocols, wear extensive personal protective equipment, and undergo regular health monitoring to mitigate these dangers.
- The work environment is inherently noisy due to machinery, furnaces, and ventilation systems, requiring hearing protection at all times. Constant loud noise can contribute to fatigue and, if not properly managed, long-term hearing damage.
- Smelter operations often run 24/7, necessitating shift work, including nights, weekends, and holidays. This irregular schedule can disrupt personal life, affect sleep patterns, and make it challenging to maintain a consistent social life.
- The job is physically demanding, involving heavy lifting, standing for long periods, climbing stairs and ladders, and operating heavy machinery. This can lead to physical strain, muscle fatigue, and an increased risk of injuries over time.
- Smelter operators work in a dusty environment, often with particulate matter from raw materials and by-products. This necessitates respiratory protection and can pose long-term respiratory health risks if not properly managed.
- Operational errors can have severe consequences, including equipment damage, environmental incidents, or serious injury. This high-stakes environment can create significant pressure and stress, especially during critical phases of the smelting process or when troubleshooting issues.
Frequently Asked Questions
Smelter Operators face distinct challenges around safety protocols, physically demanding tasks, and mastering complex machinery. This section addresses the most common questions about entering this role, from required training and shift patterns to career progression and adapting to a high-temperature environment.
What are the basic education and experience requirements to become a Smelter Operator?
You typically need a high school diploma or GED. Many employers prefer candidates with a background in industrial operations, manufacturing, or heavy machinery. Some smelters offer apprenticeships or on-the-job training programs, which are excellent entry points if you lack direct experience. Certifications in safety, such as OSHA, are highly beneficial.
How long does it take to become a fully qualified Smelter Operator from a beginner level?
The training period varies but generally takes several months to a year to become fully proficient and independent. This includes extensive on-the-job training, learning specific smelting processes, safety procedures, and equipment operation. Initial training often involves shadowing experienced operators and classroom instruction.
What is the typical work schedule and physical environment like for a Smelter Operator?
Smelter Operators often work 12-hour shifts, including nights, weekends, and holidays, as smelters operate continuously. This schedule can be physically demanding and requires adaptability to rotating shifts. The work environment is hot, noisy, and requires constant vigilance regarding safety protocols and equipment.
What are the salary expectations for a new Smelter Operator, and how does it grow with experience?
Entry-level salaries for Smelter Operators vary by region and company, but they are generally competitive, reflecting the demanding nature of the work. With experience, specialized skills, and seniority, your earning potential significantly increases. Many positions also offer benefits like health insurance, retirement plans, and overtime pay.
What are the career growth opportunities for a Smelter Operator?
Yes, there are clear paths for advancement. Experienced Smelter Operators can move into lead operator roles, supervisory positions, or specialized maintenance and technical roles. Further education or certifications in areas like metallurgy or industrial management can open doors to management or engineering support positions within the industry.
Is the Smelter Operator role stable, or is it at high risk from automation or industry changes?
Smelter operations are essential for many industries, including construction, automotive, and electronics, which generally provides stable employment. While demand can fluctuate with economic cycles, the need for processed metals remains constant. Automation is increasing, but skilled operators who can manage complex systems remain vital.
What are the primary safety concerns, and how are they managed in a smelter environment?
Safety is paramount in a smelter. Operators must strictly adhere to rigorous safety protocols, including wearing extensive personal protective equipment (PPE) and understanding emergency procedures. The main risks include burns, respiratory issues from fumes, and injuries from heavy machinery or molten metal. Continuous training and strict adherence to rules minimize these risks.
Can Smelter Operators work remotely, or is it strictly an on-site role?
No, remote work is not possible for a Smelter Operator. This role requires constant physical presence on-site to monitor equipment, manage processes, and respond immediately to operational needs. The nature of working with high temperatures and heavy machinery necessitates being physically present in the smelter.
Related Careers
Explore similar roles that might align with your interests and skills:
Furnace Operator
A growing field with similar skill requirements and career progression opportunities.
Explore career guideProcess Operator
A growing field with similar skill requirements and career progression opportunities.
Explore career guideElectric Arc Furnace Operator
A growing field with similar skill requirements and career progression opportunities.
Explore career guideElectrolysis Operator
A growing field with similar skill requirements and career progression opportunities.
Explore career guideMelt Room Operator
A growing field with similar skill requirements and career progression opportunities.
Explore career guideAssess your Smelter Operator readiness
Understanding where you stand today is the first step toward your career goals. Our Career Coach helps identify skill gaps and create personalized plans.
Skills Gap Analysis
Get a detailed assessment of your current skills versus Smelter Operator requirements. Our AI Career Coach identifies specific areas for improvement with personalized recommendations.
See your skills gapCareer Readiness Assessment
Evaluate your overall readiness for Smelter Operator roles with our AI Career Coach. Receive personalized recommendations for education, projects, and experience to boost your competitiveness.
Assess your readinessSimple pricing, powerful features
Upgrade to Himalayas Plus and turbocharge your job search.
Himalayas
Himalayas Plus
Himalayas Max
Find your dream job
Sign up now and join over 100,000 remote workers who receive personalized job alerts, curated job matches, and more for free!
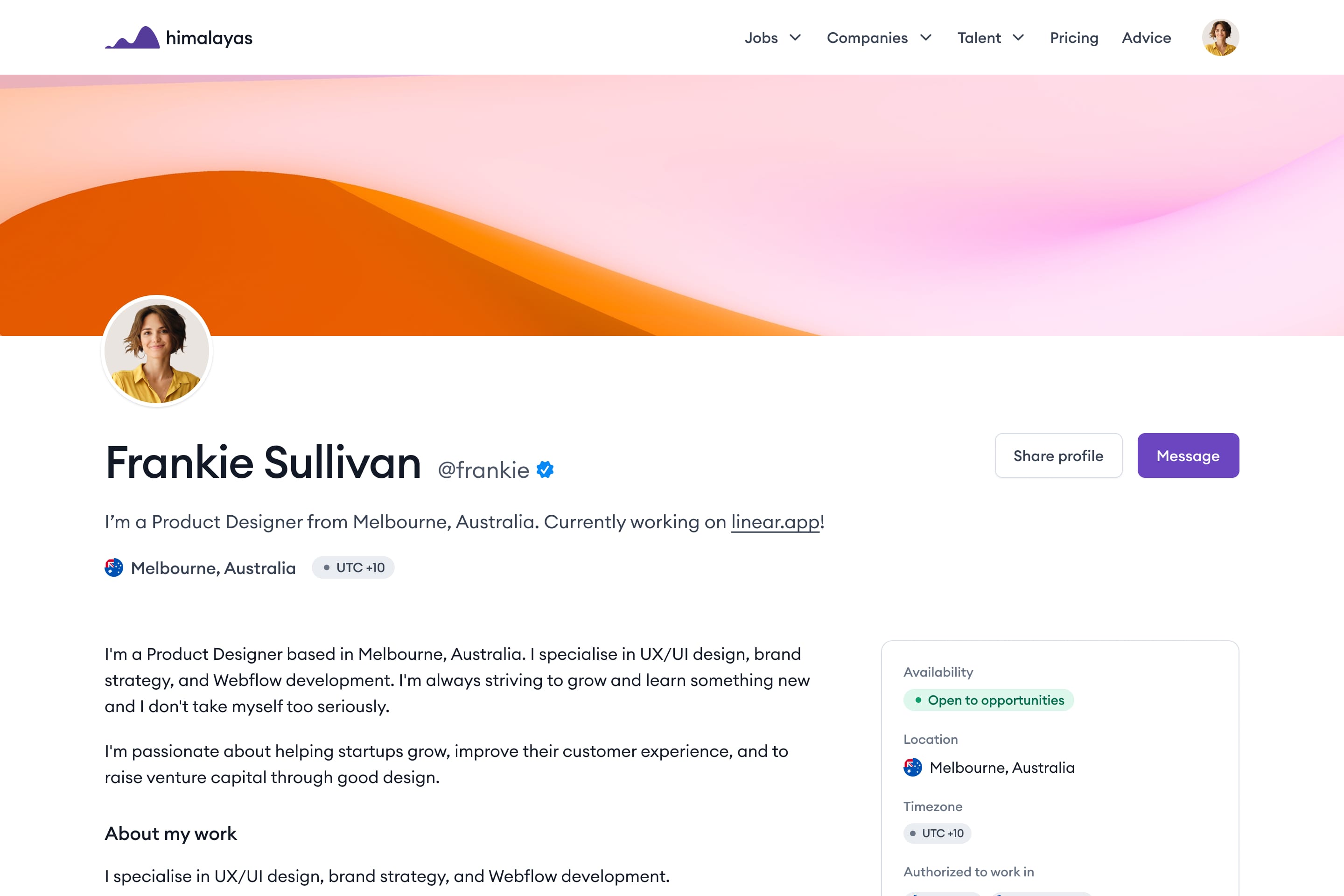