Complete Melt Room Operator Career Guide
Melt Room Operators are the backbone of foundational manufacturing, precisely controlling high-temperature furnaces to transform raw materials into molten metal. This critical role demands meticulous attention to safety and process, directly impacting the quality and integrity of countless industrial products. You'll ensure the initial purity and composition that underpins everything from automotive parts to aerospace components, offering a hands-on career with direct influence on production.
Key Facts & Statistics
Median Salary
$49,080 USD
(U.S. national median, Source: U.S. Bureau of Labor Statistics, May 2023 for Furnace, Kiln, Oven, Drier, and Kettle Operators and Tenders)
Range: $35k - $65k+ USD (Range can vary by experience, industry, and location. Source: U.S. Bureau of Labor Statistics, May 2023 for Furnace, Kiln, Oven, Drier, and Kettle Operators and Tenders)
Growth Outlook
Annual Openings
≈11
.2k openings annually (Source: U.S. Bureau of Labor Statistics, 2022-2032 projection for Pourers and Casters, Metal; and Furnace, Kiln, Oven, Drier, and Kettle Operators and Tenders)
Top Industries
Typical Education
High school diploma or equivalent, with on-the-job training. Some employers may prefer vocational training or certifications in metallurgy or related fields.
What is a Melt Room Operator?
A Melt Room Operator is a skilled industrial professional responsible for overseeing the melting of metals in furnaces to prepare them for casting or further processing. They manage the entire melting cycle, from loading raw materials and controlling furnace temperatures to ensuring the molten metal meets specific quality and compositional standards. This role is fundamental to foundries and metal fabrication plants, directly impacting the quality and integrity of the final metal products.
This position differs significantly from a general 'Foundry Worker' or 'Caster.' While a Foundry Worker might assist in various stages of metal production, and a Caster focuses specifically on pouring molten metal into molds, the Melt Room Operator specializes in the critical preparatory phase of melting and refining the raw materials. They possess deep knowledge of metallurgy, furnace operation, and safety procedures specific to high-temperature metal processing, ensuring the molten metal is perfectly prepared before it even reaches the casting stage.
What does a Melt Room Operator do?
Key Responsibilities
- Operate induction furnaces to melt various metals, ensuring precise temperature control and material composition for quality castings.
- Load raw materials, including scrap metal, alloys, and fluxes, into the furnace according to specific melt recipes and production schedules.
- Monitor furnace operations, observing molten metal for impurities, slag formation, and maintaining proper bath levels during the melting process.
- Skim dross and slag from the molten metal surface using appropriate tools, preparing the melt for pouring into molds or ladles.
- Perform routine maintenance checks on furnace equipment, refractory linings, and associated machinery to ensure safe and efficient operation.
- Conduct quality control tests on molten metal samples, verifying chemical composition and temperature against specifications before casting.
- Adhere strictly to safety protocols, including wearing personal protective equipment and following lockout/tagout procedures, to prevent accidents in a high-temperature environment.
Work Environment
Melt Room Operators work in a hot, noisy, and often dusty industrial environment. The work involves exposure to high temperatures from molten metal and furnaces, requiring constant vigilance and adherence to safety protocols. This role typically operates on a shift basis, including nights and weekends, to maintain continuous production. Teamwork is crucial for coordinating material flow and ensuring safe operations, but much of the work involves independent monitoring and physical tasks. The pace can be fast and demanding, especially during pouring cycles, with a strong emphasis on precision and safety.
Tools & Technologies
Melt Room Operators regularly use induction furnaces, arc furnaces, and other specialized melting equipment to achieve precise temperatures. They handle various ladles, crucibles, and pouring mechanisms for transferring molten metal. Measurement tools include pyrometers for temperature readings and spectrometers or X-ray fluorescence (XRF) analyzers for material composition verification. They also operate material handling equipment like forklifts or overhead cranes for loading raw materials. Safety gear such as heat-resistant clothing, gloves, face shields, and respirators are essential. Data logging systems and basic computer interfaces help them monitor process parameters and record production data.
Melt Room Operator Skills & Qualifications
A Melt Room Operator's qualifications center on a blend of practical experience, safety adherence, and technical understanding of metallurgical processes. Employers prioritize hands-on experience with melting furnaces and related equipment. This role is highly safety-critical, meaning a strong record of following protocols and understanding industrial hazards is non-negotiable.
Requirements vary significantly by the type of foundry (e.g., ferrous vs. non-ferrous, investment casting vs. sand casting) and the specific metals handled. Larger operations may demand more formal training or certifications, while smaller foundries often value direct on-the-job experience. Seniority levels dictate the depth of knowledge expected; entry-level operators focus on routine tasks, while senior operators manage complex pours, troubleshoot issues, and train new personnel. Certifications in forklift operation, overhead crane operation, or specific furnace types add considerable value.
Formal education requirements are generally less stringent than practical experience in this field. Many successful operators begin with a high school diploma and gain expertise through apprenticeships or internal training programs. However, a vocational certificate in metallurgy or a related industrial field can accelerate career progression. The skill landscape evolves with new automation and safety technologies, making continuous learning about modern melting practices important. Understanding material properties and quality control is also increasingly vital for this role, moving beyond just operating machinery.
Education Requirements
Technical Skills
- Furnace operation and control (e.g., induction, arc, cupola furnaces)
- Temperature monitoring and control systems
- Molten metal handling and pouring techniques
- Spectrometer and other analytical equipment operation
- Refractory material handling and maintenance
- Alloy addition and chemistry adjustment
- Slagging and dross removal procedures
- Material handling equipment operation (e.g., forklifts, overhead cranes)
- Basic metallurgical principles and material properties
- Blueprint and work order interpretation
- Preventive maintenance and minor equipment troubleshooting
- Lockout/Tagout procedures and confined space entry protocols
Soft Skills
- Safety Consciousness: Critical for adhering to strict safety protocols and preventing accidents in a hazardous environment.
- Attention to Detail: Essential for precise measurements, temperature control, and identifying subtle changes in metal quality or equipment performance.
- Problem-Solving: Important for troubleshooting minor equipment malfunctions, addressing material inconsistencies, and optimizing melt processes.
- Teamwork and Communication: Necessary for coordinating with other operators, supervisors, and downstream departments to ensure smooth production flow and convey critical information.
- Physical Stamina and Endurance: Required for standing for long periods, lifting heavy materials, and working in hot environments.
- Responsibility and Reliability: Crucial for consistently showing up on time, completing tasks accurately, and taking ownership of the melting process from start to finish.
- Adaptability: Valuable for adjusting to changing production schedules, different metal alloys, or unexpected equipment issues.
- Discipline: Key for following established procedures and maintaining a clean, organized work area to prevent contamination and ensure safety.
How to Become a Melt Room Operator
Becoming a Melt Room Operator involves a blend of practical skills and a commitment to safety within industrial environments. Many entry points exist, ranging from direct entry-level positions requiring minimal prior experience to roles that prefer vocational training or certifications. The timeline for entry can be relatively short, often a few weeks to a few months, especially for those who demonstrate a strong work ethic and a willingness to learn on the job.
Traditional pathways often include vocational programs in metallurgy or manufacturing, but many employers prioritize hands-on experience and a mechanical aptitude. Companies of all sizes, from large foundries to smaller specialized metalworks, hire Melt Room Operators, with opportunities varying by geographic region based on industrial concentration. Misconceptions include believing extensive formal education is always necessary; often, employers seek reliability and a capacity for rigorous training.
Networking within industrial sectors, even through local job fairs or community college programs, can reveal unadvertised openings. The hiring landscape values practical skills and a strong safety record. While barriers to entry are low, consistent attendance and adherence to strict protocols are paramount. Focus on demonstrating a commitment to safety and continuous learning to overcome these initial hurdles.
Develop foundational industrial skills by completing relevant safety certifications. Obtain certifications such as OSHA 10 or OSHA 30, which are highly valued by employers in heavy industrial settings. These certifications demonstrate a basic understanding of workplace safety protocols and can make your application stand out.
Gain practical experience in a manufacturing or industrial environment. Seek entry-level positions like production assistant, general labor, or machine operator in any factory or plant. This experience builds familiarity with industrial equipment, shift work, and a demanding physical environment, which are crucial for a Melt Room Operator role.
Learn about metallurgy and basic metal casting processes through online courses or self-study. Understand different types of metals, their properties, and the fundamentals of melting and pouring. This knowledge will help you grasp the technical aspects of the job and demonstrate your commitment during interviews.
Network with professionals in local foundries or manufacturing plants. Attend local job fairs, industry events, or connect with current operators on professional platforms. Informational interviews can provide insights into specific company needs and potentially lead to referrals for open positions.
Prepare a focused resume highlighting your safety certifications, industrial experience, and any relevant mechanical aptitude. Tailor your resume to emphasize physical stamina, attention to detail, and your ability to follow strict procedures. Practice articulating your commitment to safety and teamwork during potential interviews.
Apply for entry-level Melt Room Operator or Foundry Worker positions and prepare for practical assessments. Many employers require physical aptitude tests or a demonstration of basic mechanical skills. Be ready to discuss your understanding of safety protocols and your willingness to work in a hot, demanding environment.
Step 1
Develop foundational industrial skills by completing relevant safety certifications. Obtain certifications such as OSHA 10 or OSHA 30, which are highly valued by employers in heavy industrial settings. These certifications demonstrate a basic understanding of workplace safety protocols and can make your application stand out.
Step 2
Gain practical experience in a manufacturing or industrial environment. Seek entry-level positions like production assistant, general labor, or machine operator in any factory or plant. This experience builds familiarity with industrial equipment, shift work, and a demanding physical environment, which are crucial for a Melt Room Operator role.
Step 3
Learn about metallurgy and basic metal casting processes through online courses or self-study. Understand different types of metals, their properties, and the fundamentals of melting and pouring. This knowledge will help you grasp the technical aspects of the job and demonstrate your commitment during interviews.
Step 4
Network with professionals in local foundries or manufacturing plants. Attend local job fairs, industry events, or connect with current operators on professional platforms. Informational interviews can provide insights into specific company needs and potentially lead to referrals for open positions.
Step 5
Prepare a focused resume highlighting your safety certifications, industrial experience, and any relevant mechanical aptitude. Tailor your resume to emphasize physical stamina, attention to detail, and your ability to follow strict procedures. Practice articulating your commitment to safety and teamwork during potential interviews.
Step 6
Apply for entry-level Melt Room Operator or Foundry Worker positions and prepare for practical assessments. Many employers require physical aptitude tests or a demonstration of basic mechanical skills. Be ready to discuss your understanding of safety protocols and your willingness to work in a hot, demanding environment.
Education & Training Needed to Become a Melt Room Operator
The Melt Room Operator role primarily relies on hands-on training and practical experience rather than formal academic degrees. While some foundational knowledge in metallurgy or materials science can be beneficial, most employers prioritize direct experience with furnace operations, safety protocols, and quality control within a foundry or similar industrial setting. This contrasts sharply with roles requiring extensive theoretical knowledge, like metallurgical engineering, which typically demands a four-year bachelor's degree costing $40,000-$100,000+ over four years.
Alternative learning paths are the most common and effective for this profession. Many individuals enter through entry-level manufacturing or foundry positions, receiving on-the-job training. Some companies offer apprenticeships or structured internal training programs that can last 6-18 months, providing a direct pathway to operator roles. Community colleges sometimes offer industrial technology or manufacturing technology programs, which might include relevant courses in safety, basic electrical, and mechanical systems. These programs typically cost $3,000-$10,000 and take 1-2 years for a certificate or associate's degree, but they are not always a direct prerequisite for operator roles.
Employer acceptance of credentials heavily favors practical experience and certifications in safety (e.g., OSHA 10/30, confined space entry) and specific equipment operation. Continuous learning for a Melt Room Operator involves staying updated on new furnace technologies, safety regulations, and material handling best practices, often through manufacturer training or internal company workshops. Unlike professions requiring continuous professional development units for licensing, the emphasis here is on demonstrated competence and adherence to evolving operational standards, which are often verified through recurrent internal training and performance evaluations. Investing in specific certifications related to industrial safety or hazardous materials handling can significantly enhance a candidate's profile and demonstrate a commitment to workplace safety and operational excellence.
Melt Room Operator Salary & Outlook
Compensation for a Melt Room Operator varies significantly based on several key factors. Geographic location plays a crucial role, with areas having a higher cost of living or a concentration of industrial manufacturing often offering higher wages. Local demand for skilled operators and the presence of large foundries or metal production facilities also influence pay scales.
Years of experience dramatically impact earning potential. Entry-level operators earn less than those with a decade of experience mastering complex melting processes. Specialization in certain metal alloys, advanced furnace operation, or safety certifications can also command premium compensation. Total compensation packages extend beyond base salary, frequently including overtime pay, shift differentials, production bonuses, and comprehensive benefits such as health insurance, retirement contributions, and paid time off.
Industry-specific trends, particularly in steel, aluminum, or specialized alloy production, drive salary growth. Companies with larger production capacities or those adopting advanced melting technologies may offer more competitive salaries to attract top talent. Operators with a proven track record of efficiency, safety, and problem-solving gain significant negotiation leverage. While remote work is not applicable to this hands-on role, international market variations are notable; salary figures provided are specific to the United States Dollar (USD) context.
Salary by Experience Level
Level | US Median | US Average |
---|---|---|
Junior Melt Room Operator | $42k USD | $45k USD |
Melt Room Operator | $55k USD | $58k USD |
Senior Melt Room Operator | $68k USD | $72k USD |
Lead Melt Room Operator | $81k USD | $85k USD |
Melt Room Supervisor | $94k USD | $98k USD |
Market Commentary
The job market for Melt Room Operators shows stable demand, primarily driven by the ongoing needs of manufacturing, construction, and automotive industries. These sectors rely heavily on metal production, ensuring a consistent need for skilled operators. Projections indicate a steady outlook, though specific growth percentages are often tied to the broader manufacturing sector's performance, which is expected to see modest growth in the coming years.
Emerging opportunities in this field involve the adoption of more energy-efficient melting technologies and automation within foundries. Operators who can adapt to new furnace systems, understand advanced control interfaces, and integrate with automated material handling systems will be highly valued. The demand for specialized alloys for aerospace and defense also creates niche opportunities for operators with specific expertise.
Supply and demand dynamics for Melt Room Operators tend to be balanced, with a consistent need for replacements due to retirement or career changes. There can be shortages of highly skilled or specialized operators, particularly those with experience in specific metal types or advanced furnace operations. Future-proofing this role involves continuous training on new safety protocols, environmental regulations, and technological advancements in melting processes. While automation may assist some tasks, the core hands-on nature and critical decision-making required in a melt room make the role largely recession-resistant and unlikely to be fully automated.
Melt Room Operator Career Path
Career progression for a Melt Room Operator typically involves a steady accumulation of practical experience, deep technical knowledge of metallurgy and furnace operations, and a strong commitment to safety and quality. Advancement often follows a clear individual contributor (IC) track before branching into leadership or specialized roles. Performance, adherence to safety protocols, and a willingness to continuously learn new processes and equipment significantly influence the speed of progression.
Advancement pathways in a melt room environment often distinguish between hands-on operational mastery and supervisory responsibilities. An IC track focuses on becoming a highly skilled and efficient operator, capable of handling complex melts and troubleshooting equipment. The management track, however, emphasizes leadership, team coordination, and broader operational oversight. Company size and the specific type of foundry or metal production facility also shape career paths. Larger corporations may offer more structured training and diverse opportunities for specialization, while smaller operations might require a more generalized skill set and faster assumption of responsibility.
Lateral movement opportunities within this field might include specializing in specific alloy production, furnace maintenance, or quality control. Continuous learning through certifications in metallurgy, refractory maintenance, or advanced safety practices marks significant progression. Networking within the industry and mentorship from experienced operators and supervisors also play a crucial role, providing insights into best practices and potential advancement opportunities. Common career pivots include moving into roles such as quality assurance technician, process metallurgist, or even maintenance technician, leveraging the foundational knowledge of materials and machinery gained in the melt room.
Junior Melt Room Operator
0-2 yearsPerforms routine tasks in the melt room under direct supervision, focusing on learning the basics of furnace operation, material handling, and safety procedures. Assists more experienced operators with charging furnaces, monitoring melt temperatures, and preparing molds. Responsibilities include maintaining a clean and organized work area and adhering to all established safety guidelines. Decision-making authority is minimal, with all critical actions requiring approval.
Key Focus Areas
Develop fundamental understanding of furnace types, melting processes, and safety protocols. Focus on learning to operate basic equipment under supervision, including charging, tapping, and pouring. Absorb knowledge regarding raw material handling and proper waste disposal. Emphasize strict adherence to all safety procedures and environmental regulations. Begin to identify common operational issues and report them promptly.
Melt Room Operator
2-5 yearsOperates various types of melting furnaces independently, including charging, melting, refining, and tapping operations. Monitors critical process parameters, adjusts furnace controls, and adds alloying elements as required to meet metallurgical specifications. Performs routine maintenance checks and identifies potential equipment issues. Works with quality control to ensure molten metal meets strict standards. Provides initial guidance to junior staff.
Key Focus Areas
Master efficient furnace operation, including precise temperature control and alloying additions. Develop strong troubleshooting skills for common equipment malfunctions and process deviations. Understand and apply quality control procedures for molten metal. Focus on optimizing melt cycles for efficiency and energy conservation. Begin to train new junior operators on basic tasks and safety.
Senior Melt Room Operator
5-8 yearsLeads melting operations for complex alloys and specialized castings, ensuring adherence to stringent quality and production schedules. Troubleshoots advanced operational issues, implements corrective actions, and optimizes melting processes for efficiency and yield. Provides technical guidance and mentorship to other operators. Collaborates with engineering and quality teams on process improvements and new product development. May oversee specific shifts or production lines.
Key Focus Areas
Develop expertise in complex alloy production and advanced metallurgical principles. Lead efforts in process optimization, waste reduction, and energy efficiency initiatives. Mentor and train junior and mid-level operators, sharing best practices and technical knowledge. Participate in equipment upgrade planning and new process implementation. Focus on continuous improvement and problem-solving.
Lead Melt Room Operator
8-12 yearsActs as the primary point of contact for a shift or a specific section of the melt room, coordinating the activities of a team of operators. Ensures production targets are met while maintaining the highest standards of safety and quality. Resolves operational issues, allocates resources, and provides immediate supervision and support to the team. Conducts initial performance reviews and identifies training needs for operators. Reports directly to the Melt Room Supervisor.
Key Focus Areas
Cultivate strong leadership skills, including delegation, conflict resolution, and performance management. Develop a comprehensive understanding of production planning, scheduling, and resource allocation. Focus on strategic problem-solving and implementing long-term process improvements. Build cross-functional communication skills to liaise with other departments effectively. Take ownership of team development and training initiatives.
Melt Room Supervisor
12+ yearsManages the entire melt room operation, overseeing all shifts, personnel, and equipment. Responsible for achieving production goals, maintaining quality standards, and ensuring a safe working environment. Develops and implements operational procedures, manages budgets, and oversees maintenance schedules. Leads continuous improvement initiatives, conducts performance evaluations, and makes hiring decisions for the melt room team. Collaborates with other department heads to optimize overall plant efficiency.
Key Focus Areas
Develop advanced management and leadership competencies, including budget management, strategic planning, and human resource management. Master the ability to analyze production data to identify trends and implement continuous improvement strategies. Focus on fostering a strong safety culture and ensuring compliance with all regulations. Cultivate stakeholder management skills for interaction with upper management and external vendors. Drive innovation in melting processes and technologies.
Junior Melt Room Operator
0-2 yearsPerforms routine tasks in the melt room under direct supervision, focusing on learning the basics of furnace operation, material handling, and safety procedures. Assists more experienced operators with charging furnaces, monitoring melt temperatures, and preparing molds. Responsibilities include maintaining a clean and organized work area and adhering to all established safety guidelines. Decision-making authority is minimal, with all critical actions requiring approval.
Key Focus Areas
Develop fundamental understanding of furnace types, melting processes, and safety protocols. Focus on learning to operate basic equipment under supervision, including charging, tapping, and pouring. Absorb knowledge regarding raw material handling and proper waste disposal. Emphasize strict adherence to all safety procedures and environmental regulations. Begin to identify common operational issues and report them promptly.
Melt Room Operator
2-5 yearsOperates various types of melting furnaces independently, including charging, melting, refining, and tapping operations. Monitors critical process parameters, adjusts furnace controls, and adds alloying elements as required to meet metallurgical specifications. Performs routine maintenance checks and identifies potential equipment issues. Works with quality control to ensure molten metal meets strict standards. Provides initial guidance to junior staff.
Key Focus Areas
Master efficient furnace operation, including precise temperature control and alloying additions. Develop strong troubleshooting skills for common equipment malfunctions and process deviations. Understand and apply quality control procedures for molten metal. Focus on optimizing melt cycles for efficiency and energy conservation. Begin to train new junior operators on basic tasks and safety.
Senior Melt Room Operator
5-8 yearsLeads melting operations for complex alloys and specialized castings, ensuring adherence to stringent quality and production schedules. Troubleshoots advanced operational issues, implements corrective actions, and optimizes melting processes for efficiency and yield. Provides technical guidance and mentorship to other operators. Collaborates with engineering and quality teams on process improvements and new product development. May oversee specific shifts or production lines.
Key Focus Areas
Develop expertise in complex alloy production and advanced metallurgical principles. Lead efforts in process optimization, waste reduction, and energy efficiency initiatives. Mentor and train junior and mid-level operators, sharing best practices and technical knowledge. Participate in equipment upgrade planning and new process implementation. Focus on continuous improvement and problem-solving.
Lead Melt Room Operator
8-12 yearsActs as the primary point of contact for a shift or a specific section of the melt room, coordinating the activities of a team of operators. Ensures production targets are met while maintaining the highest standards of safety and quality. Resolves operational issues, allocates resources, and provides immediate supervision and support to the team. Conducts initial performance reviews and identifies training needs for operators. Reports directly to the Melt Room Supervisor.
Key Focus Areas
Cultivate strong leadership skills, including delegation, conflict resolution, and performance management. Develop a comprehensive understanding of production planning, scheduling, and resource allocation. Focus on strategic problem-solving and implementing long-term process improvements. Build cross-functional communication skills to liaise with other departments effectively. Take ownership of team development and training initiatives.
Melt Room Supervisor
12+ yearsManages the entire melt room operation, overseeing all shifts, personnel, and equipment. Responsible for achieving production goals, maintaining quality standards, and ensuring a safe working environment. Develops and implements operational procedures, manages budgets, and oversees maintenance schedules. Leads continuous improvement initiatives, conducts performance evaluations, and makes hiring decisions for the melt room team. Collaborates with other department heads to optimize overall plant efficiency.
Key Focus Areas
Develop advanced management and leadership competencies, including budget management, strategic planning, and human resource management. Master the ability to analyze production data to identify trends and implement continuous improvement strategies. Focus on fostering a strong safety culture and ensuring compliance with all regulations. Cultivate stakeholder management skills for interaction with upper management and external vendors. Drive innovation in melting processes and technologies.
Job Application Toolkit
Ace your application with our purpose-built resources:
Melt Room Operator Resume Examples
Proven layouts and keywords hiring managers scan for.
View examplesMelt Room Operator Cover Letter Examples
Personalizable templates that showcase your impact.
View examplesTop Melt Room Operator Interview Questions
Practice with the questions asked most often.
View examplesMelt Room Operator Job Description Template
Ready-to-use JD for recruiters and hiring teams.
View examplesGlobal Melt Room Operator Opportunities
Melt Room Operators are crucial in foundries and metal production, overseeing furnace operations, material loading, and quality control. This role's global demand remains steady, particularly in industrialized nations and emerging economies with growing manufacturing sectors. International opportunities exist in countries with robust automotive, aerospace, and heavy machinery industries. While core duties are universal, regulatory differences in safety and environmental standards impact operations. Professionals consider international roles for specialized experience or better compensation. No specific international certifications exist; experience and company-specific training are key.
Global Salaries
Salaries for Melt Room Operators vary significantly by region, reflecting local industrial demand and cost of living. In North America, specifically the United States, annual salaries range from $45,000 to $70,000 USD, with higher wages in states with large manufacturing bases like Michigan or Ohio. Canadian operators typically earn $40,000 to $65,000 CAD (approximately $30,000 to $50,000 USD).
European salaries show considerable dispersion. In Germany, operators can expect €35,000 to €55,000 (approximately $38,000 to $60,000 USD) annually, reflecting high living costs and strong industrial unions. The United Kingdom offers £28,000 to £45,000 (about $35,000 to $56,000 USD). Eastern European countries like Poland or Czech Republic provide lower nominal wages, often €15,000 to €25,000 (around $16,000 to $27,000 USD), but purchasing power can be comparable due to lower living expenses.
In Asia-Pacific, Australian operators earn $60,000 to $85,000 AUD (roughly $40,000 to $57,000 USD). Japanese salaries range from ¥3.5 million to ¥5.5 million (approximately $24,000 to $37,000 USD). China, with its vast manufacturing industry, pays operators ¥60,000 to ¥120,000 CNY (about $8,500 to $17,000 USD), often including housing or meal benefits. Latin American countries like Mexico offer $10,000 to $20,000 USD annually, adjusting for local economic conditions. Salary structures internationally often include varying benefits, vacation time, and healthcare provisions, which significantly impact take-home pay and overall compensation value. Tax implications also differ widely, affecting net income. Experience and specialized skills, such as operating specific furnace types, positively influence international compensation.
Remote Work
The Melt Room Operator role is inherently hands-on and requires direct physical presence in a foundry or production facility. Consequently, international remote work opportunities for this specific position are virtually nonexistent. The job involves direct supervision of heavy machinery, handling molten metals, and ensuring safety protocols, tasks that cannot be performed off-site.
Digital nomad lifestyles or working from different countries are not applicable to this role. Any remote work would be limited to administrative or supervisory tasks for a manager, not the operator themselves. Employers hiring Melt Room Operators internationally require on-site presence, eliminating considerations for time zones, equipment for home offices, or international tax implications related to remote work.
Visa & Immigration
Melt Room Operators seeking international work typically fall under skilled worker visa categories. Popular destination countries include Germany, Canada, Australia, and the United States due to their robust manufacturing sectors. Requirements often include a job offer from an employer, relevant experience, and sometimes vocational training or certifications recognized by the host country.
For example, Canada's Express Entry system or Australia's skilled migration programs may consider this occupation if listed on their in-demand occupations list, often requiring an employer sponsorship. German work visas necessitate a valid job contract and potentially an assessment of equivalent qualifications. The U.S. offers H-2B visas for temporary non-agricultural workers, which some foundry roles might qualify for.
Credential recognition for vocational trades varies; some countries may require specific trade assessments or apprenticeships. Visa timelines range from a few months to over a year. Language requirements are common, particularly for European countries, often requiring basic proficiency for daily communication. Pathways to permanent residency often exist after several years of continuous skilled employment. Practical considerations include securing accommodation and understanding local labor laws.
2025 Market Reality for Melt Room Operators
Understanding current market conditions is vital for Melt Room Operators. The industrial landscape, particularly in manufacturing and foundries, has seen significant shifts between 2023 and 2025 due to post-pandemic supply chain adjustments and increasing automation.
Broader economic factors, like fluctuating material costs and demand from key industries, directly influence hiring within this specialized field. Market realities for Melt Room Operators can vary significantly based on the type of foundry, its size, and its geographic location. This analysis prepares job seekers for an honest assessment of current opportunities and challenges.
Current Challenges
Securing a Melt Room Operator position faces several challenges. Automation in foundries reduces the need for manual oversight, intensifying competition for available roles. Entry-level positions are particularly scarce as companies prioritize experienced candidates to minimize training costs and production risks.
Economic fluctuations directly impact manufacturing output, leading to hiring freezes or reduced shifts. Some older facilities might also struggle with outdated equipment, complicating the work environment and potentially limiting job stability.
Growth Opportunities
Despite automation, strong demand persists for Melt Room Operators with specialized skills in niche areas such as aerospace alloys or custom casting. Foundries producing high-value, low-volume components often require more human oversight and precision, creating stable opportunities.
Operators who gain proficiency in operating and troubleshooting automated melting systems, including induction furnaces and robotic pouring systems, hold a significant advantage. Certifications in metallurgy, quality control, or advanced safety protocols can also differentiate candidates.
Underserved markets exist in regions with aging industrial infrastructure where companies are upgrading facilities. These areas may offer better entry points for skilled operators. Furthermore, a career path into supervisory roles or maintenance for melting equipment presents a clear progression for experienced operators.
Strategic career moves might involve targeting foundries that are expanding or investing in new technology, as these companies often seek skilled labor to integrate new systems. Focusing on continuous learning in automation and materials science can open doors to more advanced roles within the industry.
Current Market Trends
Hiring for Melt Room Operators in 2025 shows a stable but not rapidly expanding demand. Foundries continue to require skilled personnel for metal preparation and pouring, but technological advancements, particularly in automated melting systems, are influencing staffing needs. These systems reduce the number of operators required per shift, shifting the focus towards supervisory and maintenance roles rather than pure operational ones.
Economic conditions, especially in the automotive and construction sectors, directly affect foundry output and, consequently, operator demand. A slowdown in these industries can lead to reduced production schedules and fewer new hires. Conversely, strong demand from these sectors can create temporary spikes in hiring.
Generative AI and advanced analytics are not directly operating melt furnaces, but they are influencing predictive maintenance and material optimization. This means operators now need a basic understanding of data interpretation and system monitoring. Employers increasingly seek candidates with strong safety compliance records and a willingness to adapt to new, automated equipment. Salary trends for experienced operators remain competitive, reflecting the specialized nature and inherent risks of the role, but entry-level wages have seen slower growth due to increased automation.
Geographically, opportunities are concentrated near manufacturing hubs and industrial zones. Remote work is not applicable for this hands-on role. Seasonal patterns are less pronounced, but demand often aligns with broader economic cycles, peaking when industrial output is high.
Emerging Specializations
Technological advancements and evolving industry demands are continuously reshaping traditional manufacturing roles, including that of a Melt Room Operator. Understanding these shifts is crucial for professionals seeking to advance their careers beyond established paths. Early positioning in emerging specialization areas provides a significant advantage, often leading to premium compensation and accelerated career growth in 2025 and beyond.
While foundational skills in melt room operations remain essential, new specializations are emerging at the intersection of traditional metallurgy and advanced technologies like automation, data analytics, and sustainable practices. These next-generation roles require operators to blend hands-on expertise with analytical capabilities and an understanding of integrated systems.
The timeline for emerging areas to become mainstream varies, but many are already creating significant job opportunities. Specializing in these cutting-edge fields involves a balance of risk and reward. While established specializations offer stability, emerging areas offer greater potential for innovation, leadership, and higher earning potential, provided operators invest in acquiring new, relevant skills.
Automated Foundry Systems Operator
Melt Process Data Analyst
Sustainable Melting Operations Specialist
Metal Additive Manufacturing Operator
Melt Furnace Maintenance Technician
Pros & Cons of Being a Melt Room Operator
Making informed career decisions requires a clear understanding of both the benefits and challenges of a chosen profession. The experience of a Melt Room Operator, like any career, varies significantly based on the specific company culture, the type of metals processed, and the level of automation present in the facility. Furthermore, the pros and cons can shift at different career stages; for instance, initial physical demands might ease with experience or lead to supervisory roles. What one person considers a challenge, such as a fast-paced environment, another might view as an advantage. This assessment provides an honest look at the realities of working as a Melt Room Operator, helping individuals set appropriate expectations for this demanding but vital role.
Pros
- Melt Room Operators often earn a competitive wage, particularly with experience and specialized skills, reflecting the demanding nature and critical importance of the role within manufacturing operations.
- There is consistent demand for skilled Melt Room Operators in various heavy industries, including steel, aluminum, and foundry operations, providing strong job security.
- The role offers a hands-on, tangible work experience, allowing operators to directly see the results of their efforts in producing essential metal components and products.
- Operators gain specialized technical skills in metallurgy, furnace operation, and material handling, which are valuable and transferable within the manufacturing sector.
- Working in a melt room fosters a strong sense of team camaraderie, as operators rely heavily on each other for safety and efficient production in a high-stakes environment.
- Many facilities provide comprehensive safety training and certifications, enhancing an operator's professional qualifications and emphasizing a culture of safety.
- The work environment is dynamic and rarely monotonous, as operators manage varying batch sizes, metal types, and equipment states, requiring constant attention and problem-solving.
Cons
- Working in a melt room involves constant exposure to extreme heat, which can be physically demanding and potentially lead to heat stress or fatigue over long shifts.
- The environment often contains airborne particulates, fumes, and loud machinery, requiring strict adherence to personal protective equipment (PPE) and posing long-term respiratory or hearing risks if safety protocols are not rigorously followed.
- Operating heavy machinery and handling molten metal carries significant safety risks, including burns, explosions, or crush injuries, necessitating constant vigilance and adherence to safety procedures.
- Shift work is common in melt rooms, often involving rotating schedules that include nights, weekends, and holidays, which can disrupt personal life and sleep patterns.
- The work is physically strenuous, requiring heavy lifting, standing for extended periods, and repetitive motions, which can lead to musculoskeletal issues over time.
- There is limited direct career progression within the melt room itself; advancement often requires moving into supervisory roles or specialized technical positions outside of direct operation.
- Troubleshooting equipment malfunctions under pressure can be stressful, as downtime in a melt room directly impacts production schedules and company profitability, leading to high-stakes problem-solving scenarios.
Frequently Asked Questions
Melt Room Operators face distinct challenges around safety, precision, and physical demands within a hot, industrial environment. This section addresses the most common questions about entering this specialized role, from essential safety training to understanding the shift work and physical requirements involved in managing molten metal.
What are the basic educational and certification requirements to become a Melt Room Operator?
Entry-level Melt Room Operator positions typically require a high school diploma or GED. Many employers prefer candidates with vocational training in manufacturing, metallurgy, or a related industrial field. You will also need to complete specific safety certifications, such as OSHA 10 or 30, and potentially specialized training in forklift operation or overhead crane use, which companies often provide during onboarding.
How long does it take to become fully trained and competent as a Melt Room Operator?
Becoming a proficient Melt Room Operator usually involves an initial training period of 3-6 months. This includes on-the-job training, shadowing experienced operators, and learning specific safety protocols and equipment operation. Full competency and the ability to work independently might take up to a year, as you gain experience with different alloys, furnace types, and troubleshooting procedures.
What are the typical salary expectations for an entry-level Melt Room Operator, and how does it progress?
Starting salaries for Melt Room Operators generally range from $18 to $25 per hour, depending on location, company size, and specific industry. Experienced operators with specialized skills or leadership responsibilities can earn $28 to $35 per hour or more. Many positions also offer overtime pay due to shift work and production demands, significantly impacting annual earnings.
What is the typical work schedule like for a Melt Room Operator, and how does it impact work-life balance?
Work-life balance can be challenging for Melt Room Operators due to the prevalence of shift work, including nights, weekends, and holidays. Many facilities operate 24/7, requiring rotating shifts or fixed overnight schedules. While this can impact personal time, it often comes with shift differentials and opportunities for overtime pay. Some companies offer more predictable schedules, but flexibility is often necessary.
Is the Melt Room Operator role a secure career, or is it at high risk from automation?
The job outlook for Melt Room Operators remains stable, particularly in industries like automotive, aerospace, and heavy manufacturing that rely on metal casting. While automation is increasing, human oversight and skilled operation of melting processes are still essential. Job security often depends on the specific industry's health and the company's commitment to in-house production versus outsourcing.
What are the typical career advancement opportunities for a Melt Room Operator?
Career growth for a Melt Room Operator often involves becoming a lead operator, a supervisor, or moving into quality control, maintenance, or metallurgy technician roles. You can advance by gaining expertise in different furnace types, metal alloys, and advanced production techniques. Pursuing certifications in lean manufacturing or Six Sigma can also open doors to operational improvement positions.
What are the biggest challenges and physical demands of working as a Melt Room Operator?
The primary challenges include working in extreme heat, managing physically demanding tasks, and adhering to strict safety protocols around molten metal. You will need to be highly attentive, detail-oriented, and capable of quick problem-solving under pressure. The environment can be noisy, and you will wear extensive personal protective equipment (PPE) for extended periods.
Can Melt Room Operators work remotely, or is this strictly an on-site position?
Melt Room Operators primarily work on-site in industrial facilities, foundries, or manufacturing plants. The nature of handling molten metal and operating large furnaces makes remote work impossible for this role. You should expect to commute to a fixed industrial location daily. Some companies might have multiple plants, offering internal transfer opportunities if you want to relocate.
Related Careers
Explore similar roles that might align with your interests and skills:
Furnace Operator
A growing field with similar skill requirements and career progression opportunities.
Explore career guideProcess Operator
A growing field with similar skill requirements and career progression opportunities.
Explore career guideAnnealing Furnace Operator
A growing field with similar skill requirements and career progression opportunities.
Explore career guideElectric Arc Furnace Operator
A growing field with similar skill requirements and career progression opportunities.
Explore career guideSmelter Operator
A growing field with similar skill requirements and career progression opportunities.
Explore career guideAssess your Melt Room Operator readiness
Understanding where you stand today is the first step toward your career goals. Our Career Coach helps identify skill gaps and create personalized plans.
Skills Gap Analysis
Get a detailed assessment of your current skills versus Melt Room Operator requirements. Our AI Career Coach identifies specific areas for improvement with personalized recommendations.
See your skills gapCareer Readiness Assessment
Evaluate your overall readiness for Melt Room Operator roles with our AI Career Coach. Receive personalized recommendations for education, projects, and experience to boost your competitiveness.
Assess your readinessSimple pricing, powerful features
Upgrade to Himalayas Plus and turbocharge your job search.
Himalayas
Himalayas Plus
Himalayas Max
Find your dream job
Sign up now and join over 100,000 remote workers who receive personalized job alerts, curated job matches, and more for free!
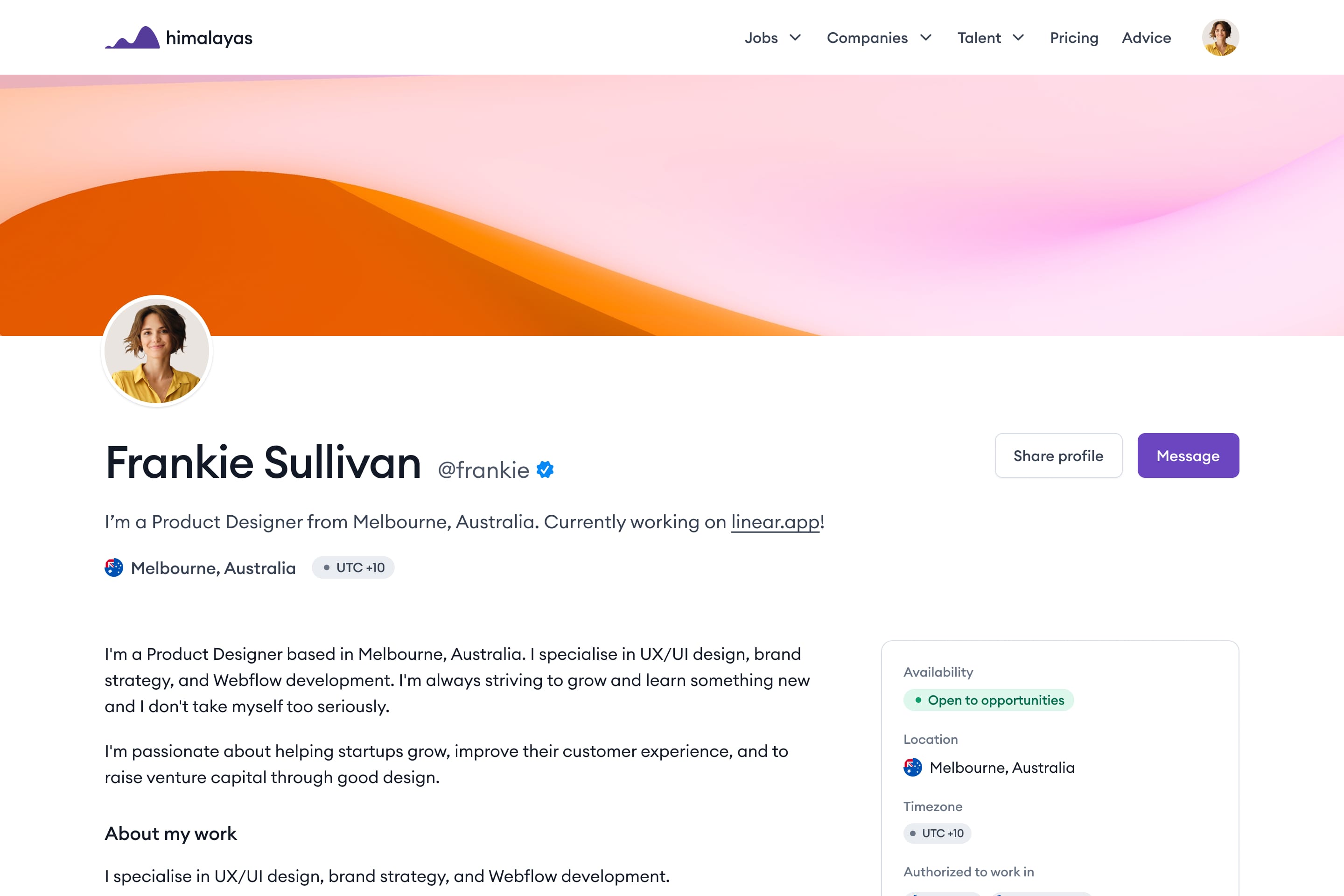