Complete Process Operator Career Guide
Process operators are the vigilant guardians of industrial production, overseeing complex machinery and systems that transform raw materials into essential goods. They ensure efficiency, safety, and quality in environments ranging from chemical plants to power stations, making critical real-time adjustments. This hands-on career offers stable opportunities for those who excel at precision, problem-solving, and maintaining rigorous operational standards.
Key Facts & Statistics
Median Salary
$64,740 USD
(U.S. national median, BLS May 2023)
Range: $40k - $90k+ USD (varies significantly by industry and experience)
Growth Outlook
3%
as fast as average (BLS)
Annual Openings
≈30k
openings annually (BLS)
Top Industries
Typical Education
High school diploma or equivalent, often with on-the-job training or an associate's degree in process technology
What is a Process Operator?
A Process Operator is a skilled professional responsible for monitoring, controlling, and optimizing the complex machinery and systems that transform raw materials into finished products within an industrial facility. They ensure that production processes run safely, efficiently, and according to precise specifications. This role involves continuous oversight of various operational parameters, making real-time adjustments to maintain product quality and operational integrity.
Unlike a maintenance technician who repairs equipment, or a chemical engineer who designs processes, the Process Operator's primary focus is on the ongoing execution and control of the manufacturing or treatment process. They are the hands-on individuals who directly manage the flow, temperature, pressure, and chemical reactions, ensuring that the plant operates within safe and productive limits, directly impacting output and preventing costly downtime or environmental incidents.
What does a Process Operator do?
Key Responsibilities
- Monitor control panels and instrumentation to ensure all process parameters remain within specified limits.
- Adjust valves, pumps, and other equipment to regulate flow, temperature, pressure, and chemical reactions.
- Conduct routine inspections of plant equipment, identifying and reporting any malfunctions, leaks, or safety hazards.
- Perform minor maintenance tasks, such as cleaning filters, lubricating machinery, or assisting maintenance technicians with repairs.
- Collect samples of raw materials, in-process products, and finished goods for quality control testing.
- Document operational data, production logs, and incident reports accurately and promptly.
- Adhere strictly to safety protocols, environmental regulations, and standard operating procedures at all times during shifts.
Work Environment
Process Operators typically work in industrial settings such as manufacturing plants, chemical facilities, power generation stations, water treatment plants, or refineries. The environment can range from a climate-controlled control room to outdoor areas exposed to varying weather conditions, noise, and sometimes hazardous materials. Safety is paramount, and operators must rigorously follow protocols.
The work often involves shift rotations, including nights, weekends, and holidays, as plants operate continuously. Collaboration with other operators, maintenance technicians, and supervisors is constant, requiring clear communication and teamwork. The pace can be steady with routine monitoring, but also includes periods of high intensity during startups, shutdowns, or emergencies, demanding quick decision-making and problem-solving skills.
Tools & Technologies
Process Operators use a range of specialized tools and technologies to manage industrial operations. They regularly interact with Distributed Control Systems (DCS) or Supervisory Control and Data Acquisition (SCADA) systems, which provide real-time data and control over the plant's processes. Operators also work with various sensors, gauges, and meters to monitor conditions like pressure, temperature, flow rates, and levels.
Physical tools include wrenches, hand tools for minor adjustments, and personal protective equipment (PPE) such as hard hats, safety glasses, and chemical-resistant suits. They might also use communication devices like two-way radios and computerized maintenance management systems (CMMS) for logging issues and tracking work orders. Familiarity with specific process equipment like pumps, compressors, heat exchangers, and distillation columns is crucial.
Process Operator Skills & Qualifications
Qualifications for a Process Operator center on a blend of practical experience, technical acumen, and adherence to safety protocols. Employers prioritize candidates who demonstrate a strong understanding of industrial processes, equipment operation, and troubleshooting. The role demands meticulous attention to detail and a proactive approach to maintaining operational efficiency and safety standards.
Requirements for Process Operators vary significantly based on industry sector, facility size, and the complexity of the processes involved. For instance, a chemical plant operator faces different challenges and requires specialized knowledge compared to an operator in a food processing facility. Entry-level positions may accept candidates with vocational training or a high school diploma and relevant certifications, while senior roles often require several years of direct experience and a proven track record of managing complex systems. Certifications, particularly in safety (e.g., OSHA), hazardous materials handling, or specific equipment operation, add significant value across all levels.
Formal education, like an associate's degree in process technology or a related engineering field, is highly valued, especially for advancement. However, many successful Process Operators begin their careers through apprenticeships or on-the-job training programs, demonstrating that practical experience can often outweigh a traditional degree. The skill landscape for Process Operators is evolving with increasing automation and data integration; therefore, an aptitude for learning new technologies and interpreting data is becoming increasingly important. While foundational mechanical and operational skills remain critical, the ability to interact with sophisticated control systems and predictive maintenance tools is now a significant advantage, particularly in modern facilities.
Education Requirements
Technical Skills
- Process Control Systems (DCS/SCADA) operation and monitoring
- Industrial safety protocols and procedures (LOTO, confined space, hot work)
- Equipment operation and troubleshooting (pumps, valves, compressors, heat exchangers, reactors)
- Reading and interpreting Process & Instrumentation Diagrams (P&IDs) and flow charts
- Basic mechanical and electrical troubleshooting
- Quality control procedures and sampling techniques
- Hazardous materials handling and emergency response
- Preventive and predictive maintenance principles
- Data logging and report generation
- Environmental regulations and compliance
- Industrial hygiene practices
- Basic chemistry and physics principles as applied to process operations
Soft Skills
- Attention to Detail: Critical for monitoring process parameters, identifying anomalies, and ensuring product quality and safety compliance. Missing small deviations can lead to significant operational issues.
- Problem-Solving: Essential for diagnosing equipment malfunctions, process upsets, and implementing corrective actions efficiently to minimize downtime and prevent further complications.
- Safety Consciousness: Paramount for adhering to strict safety protocols, recognizing potential hazards, and promoting a safe working environment for all personnel. Process Operators work with potentially dangerous materials and machinery.
- Communication: Vital for relaying accurate information about process status, equipment issues, and safety concerns to supervisors, maintenance teams, and other operators during shift changes.
- Teamwork and Collaboration: Necessary for coordinating tasks with other operators, maintenance staff, and engineers to ensure smooth transitions between shifts and efficient resolution of operational challenges.
- Adaptability: Important for responding to unexpected process changes, equipment failures, or emergency situations while maintaining calm and making sound decisions under pressure.
- Time Management: Crucial for prioritizing tasks, managing multiple monitoring points, and executing procedures within strict operational timelines to maintain production schedules.
- Responsibility and Accountability: Key for taking ownership of assigned processes and equipment, ensuring procedures are followed, and accurately documenting all operational activities and incidents.
How to Become a Process Operator
Becoming a Process Operator involves managing and controlling machinery and systems in manufacturing or industrial settings. Entry pathways vary significantly, from vocational training and apprenticeships to direct entry with a high school diploma, especially for entry-level assistant roles. The typical timeline for a complete beginner to secure their first role can range from 6 months to 2 years, depending on the chosen educational path and local industry demand.
Many roles do not strictly require a four-year degree; instead, employers value practical skills, safety knowledge, and a strong work ethic. Geographic considerations play a large part, with more opportunities in areas rich in manufacturing, chemical plants, power generation, or food processing. Larger corporations often have structured training programs, while smaller companies might offer more hands-on learning from day one.
Misconceptions include believing the work is entirely automated or that it requires extensive prior experience. While automation is increasing, human oversight remains critical. Breaking into this field often involves demonstrating a commitment to safety, a willingness to learn, and mechanical aptitude, rather than just academic credentials. Networking within local industrial communities and seeking out mentorship can also significantly accelerate the job search.
Step 1
Step 2
Step 3
Step 4
Step 5
Step 6
Education & Training Needed to Become a Process Operator
Becoming a Process Operator typically involves a combination of vocational training, certifications, and on-the-job experience. While four-year degrees are less common for entry-level roles, some employers prefer candidates with an Associate's degree in Process Technology, Chemical Engineering Technology, or a related field. These two-year programs often cost between $8,000 and $25,000 and provide a strong theoretical foundation in process control, safety, and equipment operation. Completion time is usually two years.
Alternatively, many individuals enter the field through vocational training programs or apprenticeships. These pathways can range from 6 to 18 months, with costs from $3,000 to $15,000, depending on the program's intensity and focus. Many industries also offer in-house training programs, which are often paid apprenticeships, providing hands-on experience and direct employment opportunities. Employers highly value practical experience and relevant certifications, such as OSHA safety certifications or specific equipment operation licenses.
Continuous learning is crucial for Process Operators due to evolving technologies and safety regulations. This involves regular participation in professional development courses, often provided by employers, to maintain proficiency and advance within the role. The specific educational needs vary significantly by the industry (e.g., chemical, oil and gas, manufacturing) and the complexity of the processes managed. While theoretical knowledge is important, hands-on experience and a strong understanding of safety protocols are paramount for success and career progression in this field.
Process Operator Salary & Outlook
Compensation for Process Operators varies significantly based on several key factors. Geographic location plays a crucial role; areas with a higher concentration of manufacturing, chemical processing, or energy plants often offer higher wages due to increased demand and competitive markets. Cost of living in these regions also influences salary scales.
Years of experience dramatically impact earning potential. Entry-level operators earn less than those with extensive experience who can handle complex machinery and critical processes. Specializations, such as hazardous material handling, advanced control systems, or specific industry certifications, command premium compensation.
Total compensation packages extend beyond base salary. They frequently include overtime pay, shift differentials for night or weekend work, and performance bonuses. Comprehensive benefits, including health insurance, retirement plans like 401(k)s with employer contributions, and paid time off, are standard. Some roles might offer profit-sharing or professional development allowances, further increasing overall value.
Industry-specific trends also affect pay. For instance, the oil and gas sector historically pays higher than general manufacturing due to the complexity and risk involved. Remote work is generally not applicable for this hands-on role, but regional demand shifts can still create geographic arbitrage opportunities within the U.S. All salary figures provided are in USD, acknowledging that international markets will have different compensation structures.
Salary by Experience Level
Level | US Median | US Average |
---|---|---|
Junior Process Operator | $50k USD | $55k USD |
Process Operator | $65k USD | $70k USD |
Senior Process Operator | $80k USD | $85k USD |
Lead Process Operator | $95k USD | $100k USD |
Process Supervisor | $110k USD | $115k USD |
Market Commentary
The job market for Process Operators shows steady demand, driven by the continuous operation of manufacturing, chemical, energy, and water treatment plants. As of 2025, the outlook for this role is stable, with projections indicating a slight growth. This growth is primarily tied to the maintenance and expansion of existing industrial infrastructure rather than significant new plant construction.
Automation and AI are influencing the role, but not diminishing it entirely. While some routine monitoring tasks may become automated, the need for skilled operators to oversee complex systems, troubleshoot issues, and respond to emergencies remains critical. This shift emphasizes the need for operators to possess stronger analytical and diagnostic skills, moving beyond purely manual controls.
Supply and demand dynamics vary regionally. In some industrial hubs, there's a consistent need for experienced operators, while other areas might see more competition. The profession is generally considered recession-resistant due to the essential nature of the industries it serves; plants must operate regardless of economic cycles. Future-proofing involves continuous training in new control technologies, safety protocols, and advanced problem-solving techniques.
Emerging opportunities might arise in renewable energy facilities or advanced materials manufacturing, requiring operators to adapt to new processes and equipment. Geographic hotspots for Process Operators include the Gulf Coast region, the Midwest's industrial belt, and areas with significant pharmaceutical or food processing industries.
Process Operator Career Path
Career progression for a Process Operator involves a clear path from foundational operational tasks to advanced oversight and leadership. This field typically distinguishes between individual contributor (IC) tracks, where operators deepen their technical expertise and problem-solving skills, and management/leadership tracks, which involve supervising teams and managing broader operational processes. Operators can advance by mastering complex equipment, optimizing procedures, and demonstrating consistent adherence to safety and quality standards.
Advancement speed depends on several factors, including individual performance, the complexity of the processes managed, and the size and type of the manufacturing or processing facility. Larger corporations often have more structured advancement paths, while smaller companies might offer quicker opportunities for increased responsibility. Specializing in particular types of machinery or process control systems can also accelerate progression. Lateral movement might involve transitioning to roles in quality control, maintenance, or process engineering, leveraging deep operational knowledge.
Networking within the industry, participating in professional organizations, and securing relevant certifications significantly enhance career prospects. Continuous learning about new technologies and automation plays a crucial role. Operators often transition into supervisory roles, leveraging their hands-on experience to guide and train others. Alternative pathways include moving into training and development, or becoming a technical specialist supporting process optimization and equipment upgrades.
Junior Process Operator
0-2 yearsKey Focus Areas
Process Operator
2-5 yearsKey Focus Areas
Senior Process Operator
5-8 yearsKey Focus Areas
Lead Process Operator
8-12 yearsKey Focus Areas
Process Supervisor
12+ yearsKey Focus Areas
Junior Process Operator
0-2 yearsOperate basic machinery under direct supervision, perform routine checks, and record process data. Follow established safety guidelines and assist senior operators with more complex tasks. Responsibilities involve maintaining cleanliness and order in the work area.
Key Focus Areas
Mastering basic equipment operation, understanding safety protocols, and learning standard operating procedures. Focus on developing strong attention to detail, following instructions precisely, and effective communication with team members. Building foundational knowledge of process parameters and quality checks.
Process Operator
2-5 yearsIndependently operate a range of process equipment, monitor control systems, and adjust parameters to maintain product quality and output. Conduct routine maintenance checks and identify potential issues. Train junior operators on standard procedures and safety practices.
Key Focus Areas
Developing independent problem-solving skills, optimizing process efficiency, and troubleshooting minor equipment malfunctions. Focus on improving understanding of cause-and-effect relationships within the process. Participating in safety audits and contributing to process improvement initiatives.
Senior Process Operator
5-8 yearsManage complex operational sequences and troubleshoot significant process deviations. Optimize equipment performance and contribute to the development of new operating procedures. Act as a subject matter expert, providing guidance and training to other operators.
Key Focus Areas
Advanced troubleshooting and diagnostic skills, process optimization techniques, and mentoring junior staff. Focus on understanding complex control systems and data analysis for process improvement. Developing leadership qualities and contributing to training material development.
Lead Process Operator
8-12 yearsCoordinate daily operational activities, assign tasks to operators, and oversee shift performance. Lead efforts to resolve complex operational challenges and implement process improvements. Ensure compliance with production schedules, quality standards, and safety regulations across the team.
Key Focus Areas
Strategic planning for daily operations, advanced problem-solving for systemic issues, and cross-functional collaboration with engineering and maintenance teams. Focus on improving overall line efficiency, reducing downtime, and implementing new technologies. Developing informal leadership and coaching skills.
Process Supervisor
12+ yearsDirectly supervise a team of Process Operators, manage their schedules, and conduct performance reviews. Oversee entire operational shifts, ensuring production targets are met efficiently and safely. Responsible for departmental budgets, training initiatives, and implementing company policies.
Key Focus Areas
Team leadership, performance management, budget oversight, and strategic operational planning. Focus on developing strong communication, conflict resolution, and decision-making skills. Building relationships with other departments and contributing to long-term operational strategy.
Job Application Toolkit
Ace your application with our purpose-built resources:
Process Operator Cover Letter Examples
Personalizable templates that showcase your impact.
View examplesProcess Operator Job Description Template
Ready-to-use JD for recruiters and hiring teams.
View examplesGlobal Process Operator Opportunities
Process Operators manage and monitor industrial processes globally, from manufacturing plants to energy facilities. This role is highly standardized across borders, with strong demand in industrialized nations and emerging economies. International opportunities arise from multinational corporations expanding operations or specialized projects requiring specific expertise. Understanding local safety regulations and operational standards is crucial for global mobility in this field. Professionals often seek international roles for career advancement and exposure to diverse technologies.
Global Salaries
Salaries for Process Operators vary significantly by region, industry, and experience. In North America, particularly the US and Canada, annual salaries range from USD 50,000 to USD 90,000. High-demand areas like Texas or Alberta may see higher figures. European salaries show a wide range; for instance, in Germany, operators might earn EUR 40,000 to EUR 65,000 (approx. USD 43,000-70,000), while in Eastern Europe, salaries could be EUR 20,000 to EUR 35,000 (approx. USD 21,500-38,000).
Asia-Pacific countries like Australia and Singapore offer competitive wages, often between AUD 60,000 and AUD 100,000 (approx. USD 40,000-67,000) and SGD 45,000 to SGD 75,000 (approx. USD 33,000-55,000) respectively. Latin American salaries are generally lower, with Brazil offering BRL 30,000 to BRL 60,000 (approx. USD 6,000-12,000) annually, but purchasing power parity should be considered. These figures reflect base pay; international packages often include housing allowances, relocation bonuses, and health benefits, which significantly impact total compensation. Tax rates and social security contributions differ greatly by country, affecting take-home pay. Experience and specialized certifications, like those for specific machinery, enhance earning potential globally.
Remote Work
Process Operator roles inherently require on-site presence due to the hands-on nature of monitoring and controlling physical machinery. Therefore, traditional international remote work is generally not feasible for this specific position. The job involves direct interaction with plant equipment, safety protocols, and immediate response to operational issues.
However, some very limited opportunities might exist in supervisory or training roles that oversee multiple sites, which could involve occasional remote coordination or virtual instruction. These are not typical Process Operator functions. Digital nomad lifestyles are not compatible with this profession. Employers in this field prioritize on-site personnel for continuous plant operation and safety compliance. Salary expectations are tied to the physical location of the plant.
Visa & Immigration
Process Operators often qualify for skilled worker visas in countries with industrial sectors. Popular destinations include Canada, Australia, Germany, and the United States. Each country has specific requirements, usually demanding recognized vocational training or relevant work experience, often 2-5 years. Education credential recognition is vital; applicants may need to have their qualifications assessed by local authorities to ensure equivalence.
Common visa categories include Canada's Express Entry (under specific NOC codes) or Australia's Skilled Independent visa (subclass 189) if the occupation is on the skilled list. European countries like Germany offer Blue Card options for highly skilled workers, though Process Operator roles might fall under different skilled labor categories. Application timelines vary from a few months to over a year. Some countries offer pathways to permanent residency after a certain period of skilled employment. Language proficiency, typically English or the local language, is often a requirement for visa applications and professional integration.
2025 Market Reality for Process Operators
Understanding current market conditions is crucial for Process Operators navigating their careers. The industrial landscape has significantly evolved from 2023 to 2025, driven by post-pandemic reshoring initiatives and the accelerating integration of automation and AI.
Broader economic factors, such as energy costs and supply chain resilience, directly influence manufacturing output and, consequently, the demand for operators. Market realities for Process Operators vary considerably by experience level—entry-level roles face different challenges than experienced lead operators—and by geographic region, with industrial hubs offering more opportunities. Company size also matters, as large corporations might have more structured career paths than smaller, specialized plants. This analysis provides an honest assessment to help set realistic expectations.
Current Challenges
Process Operator roles face increased competition, especially for entry-level positions. Automation and AI tools are streamlining some tasks, leading to higher productivity expectations per operator. Economic uncertainty in manufacturing sectors can slow hiring. Companies often seek specific certifications or advanced technical skills, creating a mismatch for some candidates.
Job searches can take longer due to specialized requirements and fewer open positions in some regions.
Growth Opportunities
Strong demand persists for Process Operators in critical infrastructure and highly regulated industries such as water treatment, power generation, and specialized chemical manufacturing. These sectors offer stability and often require specific certifications, creating a barrier to entry that benefits qualified candidates.
Emerging opportunities exist for operators skilled in advanced automation, predictive analytics, and digital twin technologies. Roles focused on optimizing smart factory operations or managing human-robot collaboration are growing. Professionals can position themselves advantageously by acquiring certifications in industrial control systems (ICS), cybersecurity basics for operational technology (OT), or advanced data visualization. Underserved markets often include regions with new industrial developments or specialized processing plants facing skilled labor shortages.
Operators with a deep understanding of lean principles and continuous improvement methodologies offer a competitive advantage, as companies seek efficiency gains. Market corrections might open opportunities for operators willing to cross-train into different industrial processes or relocate to areas with expanding manufacturing bases. Industries like renewable energy production and advanced materials manufacturing are resilient and offer growth prospects. Strategic career moves now involve investing in specialized training that aligns with future automation trends rather than solely relying on traditional operational experience.
Current Market Trends
Hiring for Process Operators shows steady demand in essential industries like chemicals, food processing, pharmaceuticals, and utilities as of 2025. These sectors require continuous production, ensuring a baseline need for skilled operators. However, the market is not uniform; growth varies significantly by industry segment and geographic concentration of manufacturing plants.
Recent industry changes emphasize automation and data-driven process control. Companies are investing in smart factories and IoT, meaning operators increasingly monitor automated systems, interpret data, and troubleshoot complex machinery rather than performing purely manual tasks. Generative AI is not directly displacing operators but enhances predictive maintenance and operational analytics, requiring operators to adapt to new digital tools and interfaces. This shift demands a more analytical and technologically proficient operator.
Economic conditions, particularly energy prices and supply chain stability, influence hiring. Expansions or contractions in specific manufacturing industries directly impact job availability. Employer requirements now frequently include proficiency with digital control systems, SCADA, and basic data analysis. Certifications in lean manufacturing or Six Sigma are becoming more valued. Salary trends remain stable, with slight increases for operators possessing advanced technical skills or specialized certifications. Market saturation is low for highly skilled operators in niche industries but higher for general entry-level roles. Remote work is generally not applicable, making geographic location critical. Hiring tends to be consistent year-round, driven by production needs rather not seasonal cycles.
Emerging Specializations
Technological advancements and evolving industry demands consistently create new specialization opportunities for Process Operators. Understanding these shifts and positioning oneself early in emerging areas is crucial for career advancement from 2025 onwards. Such foresight allows professionals to move into roles that often command premium compensation and offer significant career growth.
While established specializations provide stable career paths, emerging areas offer a distinct competitive edge. These cutting-edge fields, driven by innovations in automation, data analytics, and sustainability, are not yet oversaturated. They represent the next wave of job opportunities, moving from niche applications to mainstream adoption within a three to five-year timeline.
Strategically pursuing an emerging specialization involves balancing risk and reward. It requires investing in new skills and adapting to novel operational paradigms. However, the potential for leadership roles, higher earning potential, and becoming a subject matter expert in a nascent field significantly outweighs the initial learning curve. This proactive approach ensures Process Operators remain indispensable as industries transform.
Digital Twin & Predictive Operations Specialist
Sustainable Process & Green Energy Operator
Industrial Additive Manufacturing Operator
OT Cybersecurity Process Operator
Flexible & Modular Production Operator
Pros & Cons of Being a Process Operator
Making an informed career decision requires understanding both the benefits and the genuine challenges of a profession. The experience of a Process Operator can vary significantly depending on the industry sector, the specific plant's culture, and the level of automation involved. Aspects like work-life balance and daily tasks may shift between an entry-level position and a senior operational role. What one person views as a pro, such as a structured work environment, another might see as a con, like limited autonomy. This assessment provides a realistic overview to help set appropriate expectations for anyone considering a career as a Process Operator.
Pros
- Process Operators often receive competitive salaries and comprehensive benefits packages, including health insurance, retirement plans, and sometimes overtime pay for shift work, making it a financially stable career.
- There is consistent demand for Process Operators across various industries such as chemical manufacturing, oil and gas, food processing, and pharmaceuticals, providing strong job security.
- Many companies provide extensive on-the-job training and opportunities for certifications, allowing individuals to enter the field with a high school diploma and develop valuable skills without extensive prior education.
- The role offers a structured work environment with clear procedures and protocols, which can be appealing to individuals who prefer routine and predictability in their daily tasks.
- Process Operators gain hands-on experience with complex machinery and automated systems, developing practical technical skills that are highly transferable within industrial settings.
- The work of a Process Operator is critical to production and safety, providing a sense of responsibility and direct contribution to the plant's output and overall success.
- Working as part of a team in a plant environment fosters strong camaraderie among colleagues, as operators often rely on each other for support, communication, and shared responsibility during shifts.
Cons
- Working as a Process Operator often involves shift work, including nights, weekends, and holidays, which can significantly disrupt personal life and social schedules.
- Process Operators frequently work in environments with exposure to loud noises, chemicals, extreme temperatures, or hazardous materials, requiring strict adherence to safety protocols and the use of personal protective equipment.
- The job can be physically demanding, requiring long periods of standing, walking, climbing stairs and ladders, and occasionally lifting heavy equipment or materials.
- Process Operators are responsible for continuous monitoring and quick troubleshooting of complex systems, which can be mentally taxing and require constant vigilance to prevent costly errors or safety incidents.
- Career progression for a Process Operator can be limited within the operational hierarchy, often requiring additional certifications or a shift into management or specialized technical roles for significant advancement.
- Repetitive tasks are common in process operation, such as routine checks, data logging, and equipment adjustments, which can lead to monotony for some individuals over long periods.
- Unexpected equipment malfunctions or process upsets can lead to high-stress situations, requiring immediate and effective responses under pressure to restore normal operations and ensure safety, sometimes leading to extended shifts without notice.
Frequently Asked Questions
Process Operators face unique challenges managing complex industrial systems while ensuring safety and efficiency. This section addresses key questions about entering this hands-on role, from required certifications and shift work to job stability and career progression within manufacturing environments.
What are the essential educational and certification requirements to become a Process Operator?
Entry-level Process Operator roles typically require a high school diploma or GED. Many employers prefer candidates with vocational training, a certificate in process technology, or an associate's degree in a related field like chemical processing or instrumentation. Experience in a manufacturing or industrial setting, even in a different capacity, can also be a significant advantage.
How long does it typically take to become job-ready as a Process Operator if I'm starting without prior experience?
The timeline varies based on your starting point. If you pursue a vocational program or associate's degree, it can take 1-2 years to gain the necessary technical knowledge. For those with relevant industrial experience, direct entry into an operator trainee program might be possible, lasting a few months to a year. Building practical skills and understanding plant operations is crucial for readiness.
What are the typical salary expectations for an entry-level Process Operator, and how does that grow with experience?
Starting salaries for Process Operators can range from $40,000 to $60,000 annually, depending on the industry, location, and specific plant. Experienced operators in highly specialized or demanding environments, such as chemical plants or refineries, can earn significantly more, often exceeding $80,000 to $100,000 with overtime and shift differentials. Benefits packages are usually robust.
What is the typical work schedule for a Process Operator, and how does it affect work-life balance?
Process Operator roles often involve shift work, including nights, weekends, and holidays, as plants operate 24/7. This can impact work-life balance, requiring careful planning for personal and family time. While demanding, many operators appreciate the extended blocks of time off that shift schedules can provide, and overtime opportunities are frequently available.
How secure is the job market for Process Operators, and is this field growing or declining?
The job outlook for Process Operators is generally stable, especially in essential industries like chemical manufacturing, power generation, and food processing. While automation can change some tasks, the need for skilled operators to monitor, troubleshoot, and maintain complex machinery remains high. Economic fluctuations can impact specific sectors, but overall demand is consistent.
What are the common career advancement opportunities for a Process Operator?
Process Operators have several avenues for career growth. You can advance to Lead Operator, Senior Operator, or Shift Supervisor roles, taking on more responsibility for teams and operations. Opportunities also exist to specialize in areas like instrumentation, quality control, or safety, or to move into maintenance, engineering support, or training positions within the same facility or company.
What are the biggest day-to-day challenges or stressors that Process Operators face?
A significant challenge is adapting to continuous shift work and the demanding nature of plant environments, which can be noisy, hot, or involve handling hazardous materials. Operators must also maintain a high level of vigilance and attention to detail, as errors can have serious consequences. Continuous learning and adherence to strict safety protocols are essential.
Is remote work a possibility for Process Operators, or is it strictly an on-site role?
Remote work is generally not an option for Process Operators, as the role requires a constant physical presence on the plant floor to monitor equipment, perform inspections, and respond to incidents immediately. While some administrative tasks might be done digitally, the core responsibilities demand on-site presence. This is a hands-on, facility-based career.
Related Careers
Explore similar roles that might align with your interests and skills:
Chemical Operator
A growing field with similar skill requirements and career progression opportunities.
Explore career guideOperator
A growing field with similar skill requirements and career progression opportunities.
Explore career guidePlant Operator
A growing field with similar skill requirements and career progression opportunities.
Explore career guideProcess Technician
A growing field with similar skill requirements and career progression opportunities.
Explore career guideProduction Operator
A growing field with similar skill requirements and career progression opportunities.
Explore career guideAssess your Process Operator readiness
Understanding where you stand today is the first step toward your career goals. Our Career Coach helps identify skill gaps and create personalized plans.
Skills Gap Analysis
Get a detailed assessment of your current skills versus Process Operator requirements. Our AI Career Coach identifies specific areas for improvement with personalized recommendations.
See your skills gapCareer Readiness Assessment
Evaluate your overall readiness for Process Operator roles with our AI Career Coach. Receive personalized recommendations for education, projects, and experience to boost your competitiveness.
Assess your readinessSimple pricing, powerful features
Upgrade to Himalayas Plus and turbocharge your job search.
Himalayas
Himalayas Plus
Himalayas Max
Find your dream job
Sign up now and join over 100,000 remote workers who receive personalized job alerts, curated job matches, and more for free!
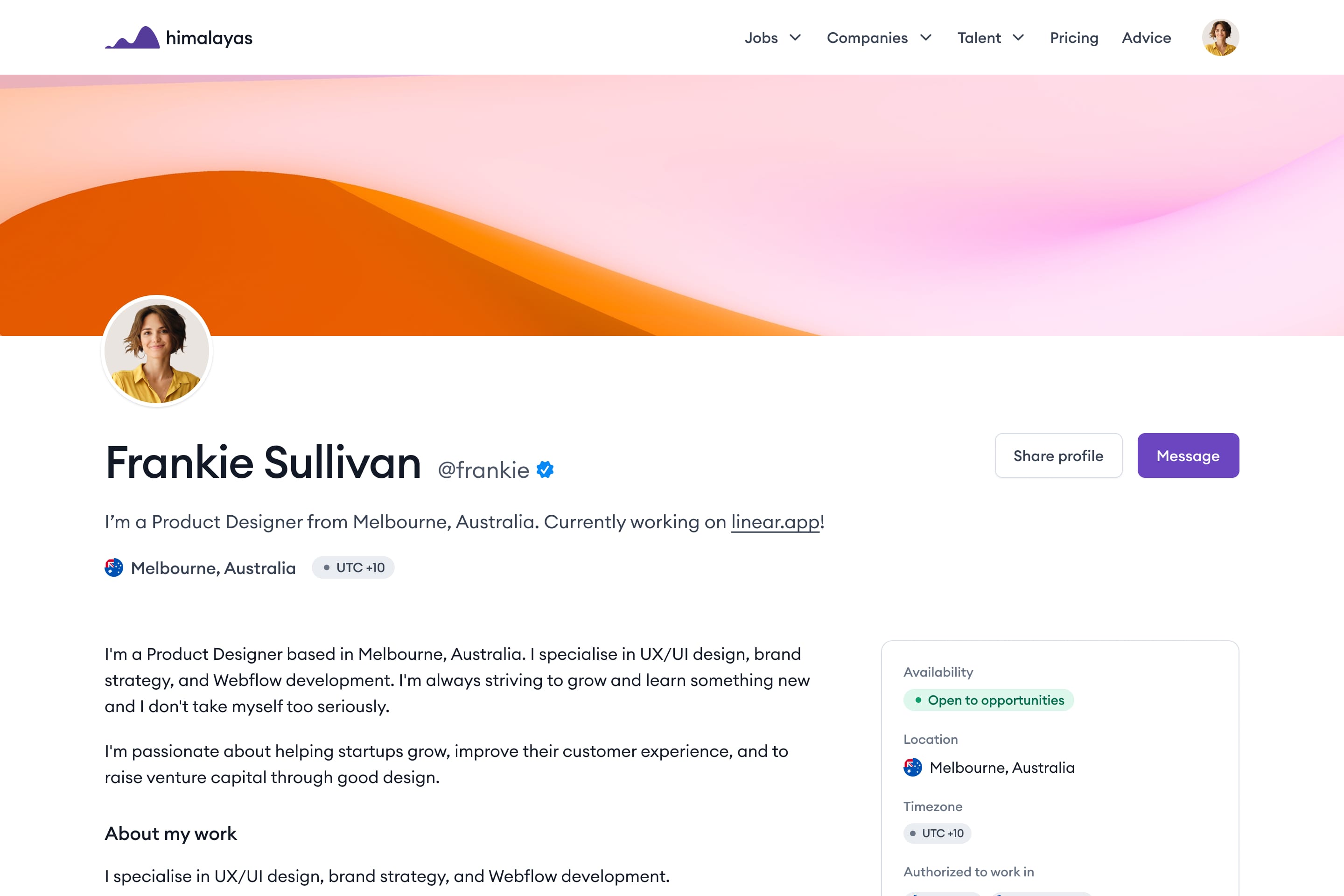