5 Smelter Operator Interview Questions and Answers
Smelter Operators are responsible for overseeing the smelting process, which involves extracting metals from their ores through heating and melting. They monitor equipment, ensure safety protocols are followed, and maintain the quality of the output. Junior operators focus on assisting with basic tasks and learning the process, while senior operators and supervisors take on leadership roles, troubleshooting issues, and managing teams. Need to practice for an interview? Try our AI interview practice for free then unlock unlimited access for just $9/month.
Unlimited interview practice for $9 / month
Improve your confidence with an AI mock interviewer.
No credit card required
1. Junior Smelter Operator Interview Questions and Answers
1.1. Can you describe a time when you had to work under pressure in a manufacturing environment?
Introduction
This question assesses your ability to handle stressful situations, which is crucial in a fast-paced and potentially hazardous environment like a smelter.
How to answer
- Use the STAR method to structure your response: Situation, Task, Action, Result.
- Clearly describe the specific situation that created pressure.
- Explain the tasks you were responsible for and what was at stake.
- Detail the actions you took to manage the pressure and ensure safety and productivity.
- Share the positive outcomes that resulted from your actions.
What not to say
- Minimizing the importance of safety and compliance under pressure.
- Being vague about the situation and your role in it.
- Failing to discuss specific actions you took.
- Not highlighting the results or learning from the experience.
Example answer
“During my internship at a local smelting plant, we faced a sudden equipment malfunction that halted production. With only a few hours to resolve the issue before penalties were incurred, I coordinated with the maintenance team to troubleshoot while ensuring my colleagues followed safety protocols. We managed to fix the issue and resume production in under two hours, minimizing downtime. This experience taught me the importance of quick decision-making and teamwork under pressure.”
Skills tested
Question type
1.2. What safety protocols do you think are essential in a smelting operation?
Introduction
This question evaluates your understanding of safety measures, which are critical in preventing accidents and ensuring a safe work environment.
How to answer
- Identify key safety protocols relevant to smelting operations.
- Explain the importance of each protocol in preventing hazards.
- Discuss how you would implement and follow these protocols.
- Mention any training or certifications you have related to safety.
- Provide examples of how you prioritized safety in previous roles or training.
What not to say
- Ignoring the importance of safety by focusing solely on production efficiency.
- Listing vague protocols without explanation or context.
- Failing to acknowledge the role of teamwork in maintaining safety.
- Underestimating the consequences of disregarding safety measures.
Example answer
“In smelting operations, essential safety protocols include wearing appropriate personal protective equipment (PPE), conducting regular equipment inspections, and adhering to lockout/tagout procedures. Each of these measures helps minimize the risk of accidents. During my training, I always emphasized PPE usage and participated in safety drills, which reinforced the importance of maintaining a culture of safety. My commitment to these protocols ensures that I can contribute to a safe working environment.”
Skills tested
Question type
2. Smelter Operator Interview Questions and Answers
2.1. Can you describe your experience operating smelting furnaces and any challenges you faced?
Introduction
This question is crucial for understanding your hands-on experience with smelting operations and your ability to troubleshoot issues that may arise in this role.
How to answer
- Begin by detailing your experience with different types of furnaces and their operational parameters.
- Discuss specific challenges you encountered, such as temperature control or material inconsistencies.
- Explain the steps you took to resolve these issues, highlighting your problem-solving skills.
- Include any safety protocols or procedures you followed to ensure a safe working environment.
- Quantify your achievements, if possible, such as improvements in efficiency or reductions in downtime.
What not to say
- Providing vague responses without specific examples.
- Focusing solely on routine tasks without mentioning challenges.
- Neglecting to discuss safety measures or protocols.
- Taking credit for team successes without acknowledging collaboration.
Example answer
“In my role at a smelting plant in France, I operated an electric arc furnace, where I faced challenges with maintaining optimal temperature levels during peak production. After analyzing the furnace's performance data, I identified fluctuations due to inconsistent raw material quality. I collaborated with the procurement team to adjust our sourcing, which improved our material consistency. As a result, we increased our production efficiency by 15% while ensuring compliance with safety protocols.”
Skills tested
Question type
2.2. How do you ensure safety and compliance in a smelting operation?
Introduction
Safety is paramount in smelting operations. This question assesses your understanding of safety protocols and your commitment to maintaining a safe workplace.
How to answer
- Discuss specific safety regulations and standards you are familiar with, such as those from the French labor code.
- Explain your experience with safety training and risk assessments.
- Share examples of how you have implemented or improved safety measures in previous roles.
- Highlight your ability to identify potential hazards and take proactive steps to mitigate risks.
- Discuss how you communicate safety protocols to your team and encourage a culture of safety.
What not to say
- Minimizing the importance of safety in your role.
- Failing to provide concrete examples of safety initiatives.
- Ignoring the need for compliance with regulations.
- Suggesting a lack of awareness about safety training or protocols.
Example answer
“At my previous job, I was responsible for conducting regular safety audits and ensuring compliance with both internal and external safety regulations. I initiated a safety training program that included practical drills and workshops, which led to a 30% decrease in reportable incidents over a year. I always emphasize the importance of reporting near misses, creating an environment where everyone feels responsible for safety.”
Skills tested
Question type
3. Senior Smelter Operator Interview Questions and Answers
3.1. Can you describe a time when you identified a safety hazard in the smelting process and how you addressed it?
Introduction
This question is crucial for evaluating your commitment to safety and your ability to proactively manage risks in a high-stakes environment like a smelter.
How to answer
- Begin with a clear description of the safety hazard you identified.
- Explain the potential consequences if the hazard was not addressed.
- Detail the steps you took to mitigate the risk, including stakeholder involvement.
- Discuss how you communicated the issue and the resolution to your team.
- Emphasize any positive outcomes or changes that resulted from your actions.
What not to say
- Downplaying the seriousness of the hazard or its potential impact.
- Claiming you had no input in safety procedures.
- Not providing a specific example or being vague.
- Failing to mention teamwork or collaboration in resolving the issue.
Example answer
“At ArcelorMittal, I noticed that the ventilation system in one of the furnaces was not functioning properly, leading to a buildup of harmful gases. I immediately reported the issue to my supervisor and initiated a temporary shutdown of the furnace. Together with the maintenance team, we conducted a thorough inspection and resolved the issue within hours. This not only ensured the safety of my colleagues but also reinforced our team's safety protocols, resulting in a 20% decrease in safety violations over the following months.”
Skills tested
Question type
3.2. How do you ensure the quality of the metal produced in the smelting process?
Introduction
Quality control is vital in smelting operations. This question assesses your knowledge of processes and techniques to maintain high standards.
How to answer
- Describe your understanding of the quality parameters for the metal produced.
- Explain the monitoring techniques you use during the smelting process.
- Discuss how you handle deviations from quality standards.
- Mention any quality improvement initiatives you have been involved in.
- Highlight the importance of collaboration with other departments for quality assurance.
What not to say
- Neglecting to mention specific quality control methods.
- Offering vague responses without concrete examples.
- Claiming that quality is not your responsibility.
- Ignoring the role of teamwork in achieving quality standards.
Example answer
“In my role at Umicore, I closely monitored the temperature and chemical composition during the smelting process using real-time data analysis. When discrepancies arose, I quickly adjusted the parameters and communicated with my team to rectify the situation. I also implemented a weekly review of our processes, which led to a 15% improvement in the purity of the final product over six months. This experience taught me the importance of vigilance and teamwork in maintaining quality.”
Skills tested
Question type
4. Lead Smelter Operator Interview Questions and Answers
4.1. Can you describe a time when you had to troubleshoot a significant issue during the smelting process? What steps did you take to resolve it?
Introduction
This question is important as it evaluates your problem-solving abilities and technical expertise in handling operational challenges, which are critical in a lead smelter operator role.
How to answer
- Use the STAR method (Situation, Task, Action, Result) to structure your answer
- Clearly outline the specific issue and its impact on production
- Detail the steps you took to diagnose the problem and the resources you utilized
- Highlight any collaboration with team members or other departments
- Discuss the outcome and any lessons learned from the experience
What not to say
- Avoid vague descriptions without clear actions or results
- Don't assign blame to others without taking responsibility
- Refrain from discussing problems that were minor or easily resolved
- Avoid technical jargon without explanation that might confuse the interviewer
Example answer
“In my previous role at Alcoa, we experienced a sudden drop in output due to an unexpected furnace malfunction. I quickly organized a team to investigate, and we discovered a blockage in the feed line. We coordinated with maintenance to clear the blockage, and I implemented a temporary operational adjustment to minimize downtime. As a result, we restored normal production levels within two hours and prevented a potential loss of significant output. This experience reinforced the importance of teamwork and swift action in operational settings.”
Skills tested
Question type
4.2. How do you ensure safety and compliance in the smelting operation, especially when training new operators?
Introduction
This question assesses your commitment to safety protocols and your ability to lead and train others, which are vital aspects of a lead smelter operator's responsibilities.
How to answer
- Discuss your approach to safety training and the importance of compliance
- Mention specific safety protocols or standards you adhere to
- Describe how you assess the understanding of safety procedures among new operators
- Provide examples of safety initiatives you've implemented or improved
- Highlight the importance of creating a safety-first culture in the workplace
What not to say
- Neglecting to mention specific safety protocols or regulations
- Suggesting safety is solely the responsibility of management
- Failing to provide examples of past training or safety improvements
- Overlooking the importance of ongoing safety assessments and feedback
Example answer
“At Nucor, I prioritize safety by implementing a comprehensive training program for new operators that includes hands-on practice and safety simulations. I ensure they understand OSHA regulations and our internal safety protocols. For instance, I developed a peer mentoring system where experienced operators guide new hires, fostering a culture of safety and compliance. This initiative led to a 30% reduction in safety incidents over the past year, emphasizing the importance of every team member's commitment to safety.”
Skills tested
Question type
5. Smelting Supervisor Interview Questions and Answers
5.1. Can you describe a time when you identified a safety hazard in the smelting process and how you addressed it?
Introduction
Safety is paramount in the smelting industry. This question assesses your ability to recognize potential dangers and implement effective safety measures, which is critical for a supervisory role.
How to answer
- Use the STAR method to structure your response.
- Clearly describe the hazard you identified and the context.
- Explain the steps you took to address the hazard, including consultation with team members and management.
- Detail the impact of your actions on safety and operations.
- Mention any follow-up measures to ensure the hazard was permanently mitigated.
What not to say
- Minimizing the importance of safety protocols.
- Describing a situation where you did not take action.
- Failing to acknowledge the role of teamwork in safety improvements.
- Providing vague responses without specific details.
Example answer
“At my previous job with BHP, I noticed a significant risk of overheating in one of the furnaces due to inadequate cooling system maintenance. I immediately reported it to my supervisor and organized a team meeting to discuss potential solutions. We implemented a stricter maintenance schedule and improved monitoring systems, resulting in a 30% reduction in overheating incidents over the following months. This experience reinforced the importance of vigilance and proactive communication in ensuring workplace safety.”
Skills tested
Question type
5.2. How do you prioritize tasks and manage your team's workload during peak production periods?
Introduction
This question evaluates your organizational and leadership skills, especially during high-pressure situations that are common in smelting operations.
How to answer
- Describe your approach to task prioritization, including any frameworks or tools you use.
- Discuss how you communicate priorities to your team.
- Explain how you assess the workload and delegate tasks effectively.
- Provide an example of a peak period you managed and the outcomes.
- Mention any tools or technologies you leverage to enhance productivity.
What not to say
- Suggesting that you handle everything yourself without delegation.
- Failing to show adaptability to changing priorities.
- Ignoring the importance of team input in task management.
- Providing a generic answer without specific examples.
Example answer
“During high-demand periods at Rio Tinto, I use a combination of a Kanban board and regular team check-ins to prioritize tasks effectively. For instance, during a recent production surge, I identified critical areas needing immediate attention and delegated tasks based on individual strengths. This approach led to a 15% increase in overall productivity while ensuring that all safety protocols were adhered to. I believe clear communication and team engagement are key to managing workloads effectively.”
Skills tested
Question type
Similar Interview Questions and Sample Answers
Simple pricing, powerful features
Upgrade to Himalayas Plus and turbocharge your job search.
Himalayas
Himalayas Plus
Himalayas Max
Find your dream job
Sign up now and join over 100,000 remote workers who receive personalized job alerts, curated job matches, and more for free!
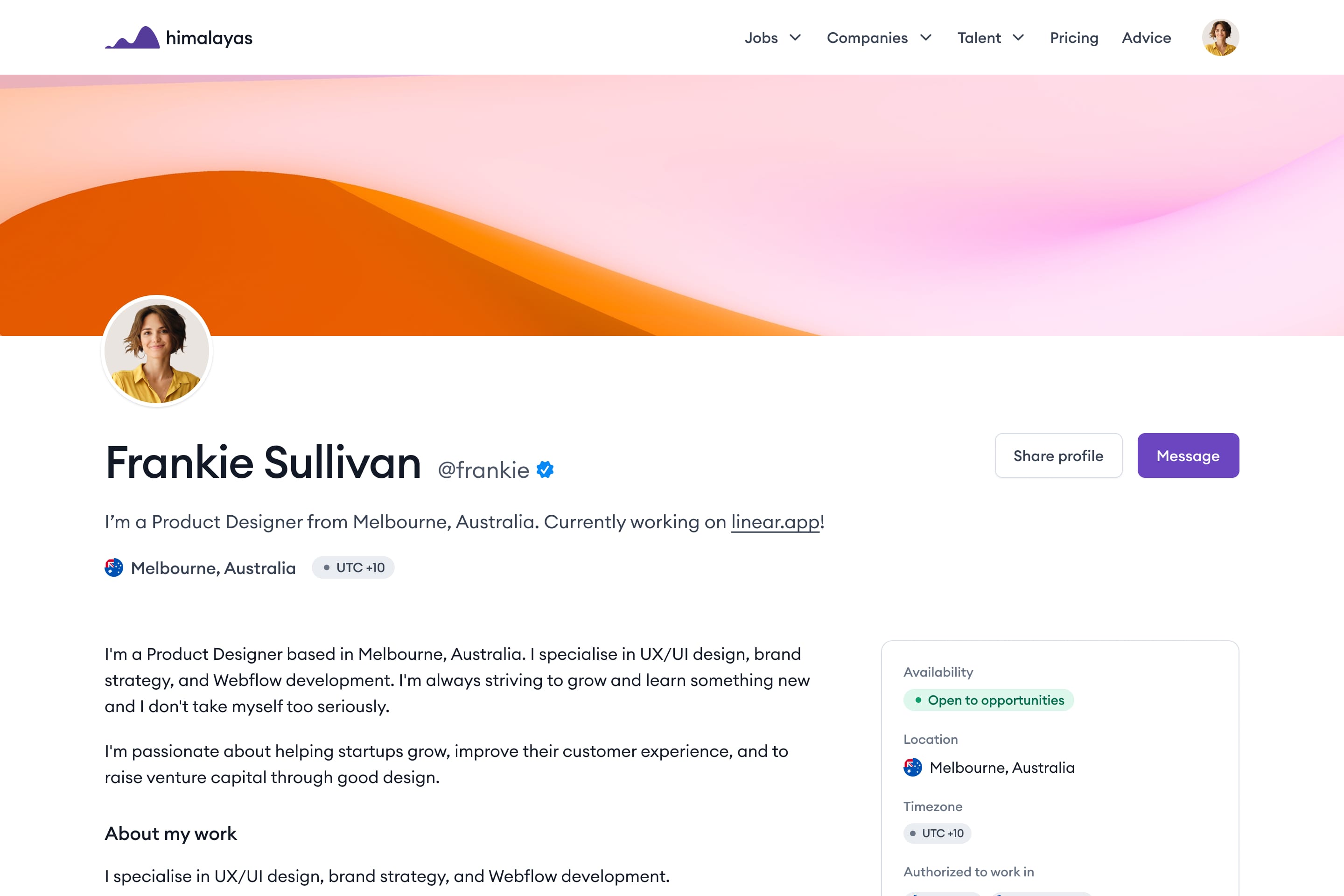