Complete Sheet Metal Worker Career Guide
Sheet metal workers are the skilled artisans who fabricate, assemble, install, and repair products made from thin metal sheets, creating everything from intricate HVAC systems to durable building exteriors. They translate blueprints into tangible structures, ensuring precise fit and function in critical infrastructure. This hands-on career offers a clear path to mastery and stable employment in diverse industries, building essential components that keep our world running.
Key Facts & Statistics
Median Salary
$57,210 USD
(U.S. national median, May 2023, BLS)
Range: $38k - $89k+ USD
Growth Outlook
1%
slower than average (2022-2032)
Annual Openings
≈10,100
openings annually
Top Industries
Typical Education
High school diploma or equivalent, often followed by a 4-5 year apprenticeship
What is a Sheet Metal Worker?
A sheet metal worker is a skilled tradesperson who fabricates, assembles, installs, and repairs products made from thin sheets of metal. These professionals shape and join various metals like steel, aluminum, and copper into items ranging from HVAC ducts and roofing systems to precision components for aircraft and specialized industrial equipment. Their work is fundamental to construction, manufacturing, and maintenance across numerous industries.
Unlike general welders who focus primarily on joining metal, or ironworkers who deal with structural steel beams, sheet metal workers specialize in lighter gauge metals and intricate designs. They interpret blueprints, measure, cut, bend, and fasten sheets to create custom products that meet precise specifications. Their expertise ensures proper air flow in buildings, weatherproofing of structures, and the functionality of many mechanical systems.
What does a Sheet Metal Worker do?
Key Responsibilities
- Interpret blueprints, schematics, and construction drawings to determine project specifications, material requirements, and installation sequences.
- Fabricate sheet metal parts and products by cutting, bending, punching, and shaping metal sheets using hand tools, power tools, and specialized machinery like press brakes and shears.
- Assemble and install fabricated sheet metal components, such as ducts, roofs, and siding, ensuring precise fit, alignment, and adherence to safety standards and building codes.
- Inspect finished products for quality assurance, checking dimensions, seams, and finishes to meet design specifications and prevent defects.
- Perform routine maintenance and calibration on sheet metal machinery and tools to ensure their proper functioning and extend their lifespan.
- Collaborate with other tradespeople, including plumbers, electricians, and HVAC technicians, to coordinate work and ensure seamless integration of sheet metal systems.
- Troubleshoot and repair existing sheet metal installations, identifying issues like leaks or damage and implementing effective solutions to restore functionality and integrity.
Work Environment
Sheet metal workers typically work in a variety of environments, including fabrication shops, construction sites, and existing buildings. Shop work involves operating heavy machinery in a controlled setting, often with noise and dust requiring personal protective equipment. On construction sites, they work outdoors in varying weather conditions or indoors in unfinished structures, which can be physically demanding. The work often involves standing, bending, lifting, and working at heights or in confined spaces. Collaboration with other skilled trades is common, requiring good communication and teamwork. Schedules are usually full-time, though project deadlines or emergency repairs may require overtime.
Tools & Technologies
Sheet metal workers utilize a wide array of specialized tools and machinery. They frequently operate power tools such as plasma cutters, shears, press brakes, and roll formers for precise cutting and shaping of metal. Hand tools like snips, hammers, punches, and measuring tapes are essential for detailed work and adjustments. Welders, including MIG, TIG, and stick welders, are crucial for joining metal components securely. They also work with various types of sheet metal, including galvanized steel, stainless steel, aluminum, and copper, selecting the appropriate material based on project requirements. Familiarity with Computer Numerical Control (CNC) machines and CAD software is becoming increasingly important for programming and automating complex fabrication tasks.
Sheet Metal Worker Skills & Qualifications
A Sheet Metal Worker's qualification landscape emphasizes practical experience and demonstrated proficiency over formal academic degrees. While foundational knowledge is essential, employers prioritize hands-on skills, safety adherence, and the ability to interpret complex blueprints. Requirements vary significantly based on the industry sector and the type of work involved, whether it's HVAC installation, aerospace manufacturing, or architectural fabrication.
For entry-level roles, vocational training or an apprenticeship is often sufficient, providing a structured pathway to competence. More senior positions, or those in specialized fields like aviation, demand extensive on-the-job experience, advanced certifications, and a proven track record of precision and problem-solving. Certifications such as OSHA 10/30, specific welding certifications (e.g., AWS D1.1, D1.2), or HVAC-specific credentials significantly enhance a candidate's marketability and earning potential.
The skill landscape for Sheet Metal Workers is evolving with the increasing adoption of automated machinery, CAD/CAM software, and advanced materials. While traditional hand skills remain critical, a growing understanding of digital fabrication processes and computer-controlled equipment is becoming vital. This balance between traditional craftsmanship and modern technology defines success in the field, making continuous learning and adaptation essential for career progression.
Education Requirements
Technical Skills
- Blueprint and schematic interpretation (reading and understanding technical drawings)
- Precision measuring tools (calipers, micrometers, tape measures, protractors)
- Metal fabrication techniques (cutting, bending, forming, shaping, rolling)
- Welding processes (TIG, MIG, Stick, spot welding) specific to sheet metal gauges
- Hand tools proficiency (snips, hammers, drills, crimpers, fasteners)
- Power tools operation (shears, press brakes, grinders, plasma cutters)
- HVAC ductwork fabrication and installation (for HVAC-focused roles)
- Sheet metal layout and pattern development (flat pattern layout, triangulation)
- Material knowledge (steel, aluminum, copper, stainless steel gauges and properties)
- Safety procedures and equipment usage (PPE, lockout/tagout, fall protection)
- Soldering and brazing techniques (for sealing and joining metal seams)
- Basic CAD/CAM software understanding (for interpreting digital designs or programming CNC machines)
Soft Skills
- Attention to detail: Essential for ensuring precision in measurements, cuts, and bends, as errors can lead to material waste and structural integrity issues.
- Problem-solving: Required to troubleshoot issues with material, machinery, or design discrepancies that arise during fabrication or installation.
- Spatial reasoning: Critical for visualizing how flat patterns will form three-dimensional objects and for interpreting complex blueprints and schematics.
- Adherence to safety protocols: Non-negotiable for working with heavy machinery, sharp materials, and elevated structures, preventing accidents and ensuring compliance.
- Teamwork and collaboration: Necessary when working on large projects, coordinating with other trades, and sharing tools or workspace efficiently.
- Adaptability: Important for adjusting to new designs, materials, or equipment, and for working in varied environments from workshops to construction sites.
- Time management: Crucial for meeting project deadlines, managing workload, and optimizing efficiency in fabrication and installation tasks.
How to Become a Sheet Metal Worker
Becoming a sheet metal worker involves several pathways, primarily through apprenticeships or vocational training, rather than traditional university degrees. Apprenticeships offer hands-on experience and paid training, making them a popular and effective route. Vocational programs provide foundational skills and certifications, which can shorten apprenticeship durations or prepare individuals for entry-level fabrication roles.
The timeline for entry varies; a full apprenticeship typically lasts 3-5 years, but individuals with prior construction experience or relevant certifications might enter faster. Entry strategies can differ by location; larger metropolitan areas with more construction or manufacturing often have more apprenticeship opportunities. Smaller companies or specialized fabricators might favor candidates with specific project experience or certifications.
A common misconception is that this work is solely about heavy lifting; precision, mathematical aptitude, and problem-solving are equally crucial. Networking within local unions, trade associations, and construction companies can significantly open doors. The hiring landscape values practical skills, safety knowledge, and a strong work ethic. Barriers might include competition for limited apprenticeship spots or the physical demands of the job, but persistence and preparation help overcome these.
Step 1
Step 2
Step 3
Step 4
Step 5
Step 6
Education & Training Needed to Become a Sheet Metal Worker
Becoming a Sheet Metal Worker typically involves a blend of formal training and hands-on experience. The most common and highly regarded pathway is through a registered apprenticeship program. These programs combine paid on-the-job training with classroom instruction, usually lasting 4-5 years. Apprenticeships generally cost very little or nothing to the apprentice, as employers often cover tuition for related instruction, and apprentices earn wages while learning. This contrasts with trade school programs, which can range from $10,000 to $30,000 for 1-2 years of full-time study, and do not include paid work experience.
Employers highly value practical experience and certifications. Apprenticeship programs provide a structured environment to gain both, leading to journey-level status upon completion. While trade school offers foundational knowledge, it often requires graduates to seek entry-level positions or further on-the-job training to achieve full proficiency. Self-study alone is rarely sufficient for this skilled trade due to the need for specialized equipment and direct mentorship. Continuous learning is essential, with many workers pursuing certifications in areas like welding, HVAC, or specific fabrication techniques to enhance their skills and career prospects.
The market perception of a Sheet Metal Worker's credentials heavily favors union-affiliated or nationally recognized apprenticeship completions. These demonstrate a comprehensive skill set and adherence to industry standards. While a high school diploma or GED is usually a prerequisite for entry into most programs, some apprenticeships may require applicants to pass basic math and mechanical aptitude tests. The investment in an apprenticeship, while long-term, offers a high return through paid training and strong career placement, often with union benefits. This contrasts with shorter, unaccredited programs that may not lead directly to journey-level employment or competitive wages.
Sheet Metal Worker Salary & Outlook
Compensation for a Sheet Metal Worker varies significantly based on several factors. Geographic location plays a crucial role, with higher wages typically found in metropolitan areas and regions with strong industrial or construction sectors due to higher cost of living and increased demand. For instance, coastal cities or areas with significant infrastructure projects often command better pay.
Experience levels dramatically influence earning potential. An Apprentice Sheet Metal Worker starts at a lower scale, gaining skills over several years. As workers progress to journeyman, senior, and lead roles, their expertise in fabrication, installation, and specialized techniques like HVAC or architectural sheet metal work directly translates to higher salaries. Union membership often provides structured wage increases, benefits, and training opportunities, impacting total compensation.
Total compensation packages extend beyond base salary. Many Sheet Metal Workers receive comprehensive benefits, including health insurance, retirement plans like 401(k)s, and paid time off. Overtime pay is common, especially during peak construction periods or large projects, significantly boosting annual earnings. Some roles may include per diem for travel or specialized tool allowances. Performance or project-based bonuses are less common but can occur on large, complex jobs.
The industry sector also affects pay; those in industrial manufacturing or specialized custom fabrication might earn differently than those primarily in residential or commercial construction. Remote work is generally not applicable to this hands-on trade, meaning geographic location dictates the local market rate. Understanding these elements, coupled with strong negotiation skills based on proven expertise and certifications, helps maximize a Sheet Metal Worker's earning potential. International markets have their own distinct pay scales and economic conditions, so the figures provided here are specific to the United States.
Salary by Experience Level
Level | US Median | US Average |
---|---|---|
Apprentice Sheet Metal Worker | $40k USD | $45k USD |
Sheet Metal Worker | $58k USD | $60k USD |
Senior Sheet Metal Worker | $70k USD | $72k USD |
Lead Sheet Metal Worker | $78k USD | $80k USD |
Sheet Metal Foreman | $90k USD | $92k USD |
Sheet Metal Supervisor | $102k USD | $105k USD |
Market Commentary
The job market for Sheet Metal Workers shows consistent demand, driven primarily by growth in the construction sector and the ongoing need for HVAC system installation and maintenance. The U.S. Bureau of Labor Statistics projects employment of sheet metal workers to grow 5 percent from 2022 to 2032, which is about as fast as the average for all occupations. This translates to approximately 6,800 openings each year, on average, over the decade.
Key drivers include new commercial and residential construction, as well as the retrofitting and modernization of existing buildings for energy efficiency. Specialized areas, such as the fabrication and installation of custom architectural elements, industrial ventilation systems, and renewable energy infrastructure (e.g., solar panel mounting structures), present emerging opportunities. The demand for skilled workers often outpaces supply, particularly for those with advanced welding or CAD/CAM skills, creating a favorable environment for experienced professionals.
Technological advancements, such as automated fabrication machinery and Building Information Modeling (BIM), are changing the tools and skills required, but they are not replacing the fundamental need for skilled hands-on work. Instead, these technologies enhance efficiency and precision. The profession is generally resilient to economic downturns, as infrastructure maintenance and essential building services remain necessary. Geographic hotspots for employment include major urban centers and regions experiencing population growth or significant industrial development.
Sheet Metal Worker Career Path
Career progression for a Sheet Metal Worker typically follows a structured path, heavily reliant on hands-on experience, skill acquisition, and adherence to safety and quality standards. Initial stages focus on mastering fundamental techniques and tools, while later stages emphasize leadership, project management, and specialized fabrication skills. This field offers both individual contributor (IC) tracks, where workers become highly specialized fabricators or estimators, and management/leadership tracks, moving into supervisory or foreman roles.
Advancement speed depends on several factors, including the complexity of projects undertaken, continuous learning of new welding or fabrication techniques, and the ability to consistently meet demanding deadlines. Company size also influences career paths; larger firms might offer more specialized roles or structured training programs, while smaller shops might provide broader experience across various tasks. Lateral movement often involves specializing in areas like HVAC ductwork, architectural metalwork, or custom fabrication.
Networking within trade associations and pursuing advanced certifications in welding, CAD/CAM, or specific machinery operations can significantly accelerate progression. Mentorship from experienced journeymen is crucial for skill development and understanding industry best practices. Common career pivots include moving into roles like estimator, CAD designer, or welding inspector, leveraging the deep understanding of metal properties and fabrication processes gained from this trade.
Apprentice Sheet Metal Worker
0-4 yearsKey Focus Areas
Sheet Metal Worker
4-8 years total experienceKey Focus Areas
Senior Sheet Metal Worker
8-12 years total experienceKey Focus Areas
Lead Sheet Metal Worker
10-15 years total experienceKey Focus Areas
Sheet Metal Foreman
15+ years total experienceKey Focus Areas
Sheet Metal Supervisor
20+ years total experienceKey Focus Areas
Apprentice Sheet Metal Worker
0-4 yearsWorks under direct supervision, assisting experienced Sheet Metal Workers. Performs basic tasks such as cutting, bending, forming, and assembling sheet metal components. Focuses on learning proper tool usage and maintaining a clean, safe workspace. Assists with material preparation and site cleanup.
Key Focus Areas
Mastering basic hand tools, power tools, and cutting equipment. Learning to read blueprints and shop drawings. Developing foundational safety practices and understanding material handling procedures. Focusing on precision in measurements and cuts, and understanding different types of sheet metal.
Sheet Metal Worker
4-8 years total experienceIndependently performs a wide range of sheet metal fabrication and installation tasks. Interprets complex blueprints and specifications to create components, often working on-site or in a shop setting. May guide junior apprentices on specific tasks and ensures work adheres to quality and safety standards.
Key Focus Areas
Refining fabrication techniques, including advanced welding (TIG, MIG, Stick) and soldering. Understanding complex HVAC systems, architectural designs, or industrial applications. Developing problem-solving skills for fitting and installation challenges. Improving efficiency and material optimization.
Senior Sheet Metal Worker
8-12 years total experienceHandles highly complex and specialized sheet metal projects, often requiring custom fabrication or intricate designs. Provides technical guidance and mentorship to less experienced workers. Troubleshoots difficult installation issues and ensures adherence to stringent project specifications and codes. Works with minimal supervision.
Key Focus Areas
Specializing in complex fabrication methods, advanced layout techniques, and intricate installations. Mentoring junior Sheet Metal Workers and apprentices. Contributing to project planning and material estimation. Developing expertise in specific areas like stainless steel, aluminum, or exotic alloys.
Lead Sheet Metal Worker
10-15 years total experienceLeads a small team of Sheet Metal Workers on specific project sections or sub-projects. Responsible for assigning tasks, monitoring progress, and ensuring quality control. Acts as a primary point of contact for technical questions within the team. Helps plan daily activities and manage material flow.
Key Focus Areas
Taking ownership of project sections, coordinating tasks, and managing workflows for small teams. Developing leadership skills, including communication and delegation. Improving cost estimation accuracy and material procurement processes. Understanding project timelines and resource allocation.
Sheet Metal Foreman
15+ years total experienceManages a team of Sheet Metal Workers and apprentices on a large project or multiple concurrent smaller projects. Oversees all aspects of fabrication, installation, and project completion, ensuring adherence to blueprints, codes, and deadlines. Responsible for site safety, quality control, and personnel management.
Key Focus Areas
Comprehensive project management, including scheduling, budgeting, and resource allocation. Advanced safety management and quality assurance protocols. Conflict resolution and team motivation. Developing strong communication skills for interacting with clients, engineers, and other trades.
Sheet Metal Supervisor
20+ years total experienceSupervises multiple foremen and their respective teams, or manages the operations of an entire sheet metal fabrication department. Responsible for overall project profitability, client satisfaction, and ensuring compliance with industry regulations. Involved in hiring, training, and performance evaluations for the entire team.
Key Focus Areas
Strategic planning for multiple projects or departmental operations. Advanced understanding of business financials, contract management, and client relations. Developing long-term personnel development plans. Implementing new technologies or fabrication methods to improve efficiency.
Job Application Toolkit
Ace your application with our purpose-built resources:
Sheet Metal Worker Resume Examples
Proven layouts and keywords hiring managers scan for.
View examplesSheet Metal Worker Cover Letter Examples
Personalizable templates that showcase your impact.
View examplesTop Sheet Metal Worker Interview Questions
Practice with the questions asked most often.
View examplesSheet Metal Worker Job Description Template
Ready-to-use JD for recruiters and hiring teams.
View examplesGlobal Sheet Metal Worker Opportunities
The Sheet Metal Worker profession translates globally, with demand driven by construction, manufacturing, and aerospace sectors worldwide. International job market trends for 2025 show consistent need, particularly in developed and rapidly industrializing economies. Cultural nuances affect workplace safety standards and project execution, while regulatory differences impact material specifications and building codes. Professionals seek international roles for higher wages, diverse project experience, and skill development. International certifications like AWS welding certifications or specific national trade qualifications can facilitate global mobility.
Global Salaries
Sheet Metal Worker salaries vary significantly by region and cost of living. In North America, a skilled Sheet Metal Worker earns between $50,000 and $80,000 USD annually in the United States, and $55,000 to $90,000 CAD (approximately $40,000-$65,000 USD) in Canada. These figures reflect strong union presence and high demand in construction and manufacturing.
European salaries differ, with Germany offering €35,000 to €50,000 (about $38,000-$55,000 USD) annually, while the UK ranges from £28,000 to £40,000 (around $35,000-$50,000 USD). Scandinavian countries like Norway might offer higher wages, around NOK 400,000 to NOK 550,000 ($38,000-$52,000 USD), but with a significantly higher cost of living. Purchasing power parity means a lower nominal salary in some European countries may offer similar living standards to a higher North American salary.
In Australia, salaries for experienced Sheet Metal Workers are typically AUD 60,000 to AUD 85,000 (approximately $40,000-$57,000 USD). The Middle East, particularly the UAE and Saudi Arabia, offers tax-free salaries ranging from $25,000 to $45,000 USD, often with housing allowances, which boosts take-home pay. Asian markets like Singapore or South Korea offer $20,000-$35,000 USD, but with varying benefits and tax structures.
Salary structures also differ; North American packages often include extensive health benefits and retirement plans, while European countries may have more robust public healthcare and generous vacation time. Experience and specialized skills, such as TIG welding or CNC programming, can increase compensation globally. International pay scales are not standardized, but national trade unions often influence local wage agreements.
Remote Work
International remote work opportunities for Sheet Metal Workers are extremely limited. This role is inherently hands-on, requiring physical presence for fabrication, installation, and repair of metal structures. Digital nomad setups are generally not applicable to this trade.
However, some niche areas might involve remote collaboration. For example, a senior Sheet Metal Worker might remotely review blueprints, perform virtual quality control checks on designs, or provide online technical guidance to teams in different locations. This is not common for the core job functions.
Legal and tax implications for such rare remote scenarios would involve navigating local labor laws and tax residency rules, which are complex. Companies hiring internationally for this role expect on-site presence. Remote work for Sheet Metal Workers is not a viable career path; the profession demands direct physical engagement with materials and equipment.
Visa & Immigration
Sheet Metal Workers often qualify for skilled worker visas in countries with labor shortages. Popular destinations include Canada (Express Entry), Australia (Skilled Nominated/Regional Visas), New Zealand (Skilled Migrant Category), Germany (Skilled Immigration Act), and the UK (Skilled Worker Visa). These countries frequently list trades like sheet metal work on their in-demand occupation lists.
Requirements typically include formal qualifications (e.g., trade certificates, apprenticeships), a minimum number of years of experience, and often a job offer. Credential recognition is crucial; applicants may need their qualifications assessed by an authorized body. For instance, Australia's Trades Recognition Australia (TRA) assesses overseas trade qualifications. Professional licensing varies; some countries require specific local certifications or assessments before employment.
Visa timelines range from several months to over a year, depending on the country and application complexity. English language proficiency (IELTS, PTE) is often required for English-speaking countries. Pathways to permanent residency exist, especially in Canada and Australia, where skilled workers can transition after a few years of employment. Some countries may offer specific fast-track programs for highly skilled trades. Family visas are usually available for spouses and dependent children.
2025 Market Reality for Sheet Metal Workers
Understanding current market conditions is crucial for any aspiring or established sheet metal worker. The landscape has evolved significantly since 2023, shaped by post-pandemic recovery and technological advancements.
Broader economic factors, such as interest rates impacting construction and manufacturing output, directly influence job availability. Market realities for sheet metal workers vary by experience level, with specialized skills commanding higher demand, and by geographic region, as industrial and construction hubs offer more opportunities. This analysis provides an honest assessment of these realities.
Current Challenges
Sheet metal workers face increased competition for specialized roles, particularly in advanced manufacturing where automation is growing. Entry-level positions see significant saturation, making initial job searches longer.
Economic uncertainty in construction and manufacturing sectors can slow project starts, directly impacting demand. Additionally, a skills gap exists as employers seek workers proficient with new materials and digital fabrication tools.
Growth Opportunities
Despite challenges, strong demand exists in specialized areas like architectural sheet metal, pharmaceutical manufacturing, and aerospace components. These sectors require high precision and often offer better compensation.
Emerging opportunities include roles focused on sustainable building practices, such as fabricating components for energy-efficient HVAC systems or solar panel installations. Workers who upskill in CAD/CAM software, robotic welding, or advanced material handling gain a significant competitive edge.
Underserved markets often appear in regions with new industrial development or critical infrastructure upgrades, where skilled labor is scarce. Professionals with diverse fabrication skills, including welding, bending, and installation, are highly valued. Market stability in maintenance and repair also creates consistent, recession-resistant opportunities.
Investing in certifications for specific machine operations or advanced safety protocols can open doors. Timing career moves to align with large-scale infrastructure projects or manufacturing expansions can yield better prospects. The ongoing need for skilled trades ensures a foundational demand for capable sheet metal workers.
Current Market Trends
Hiring for sheet metal workers shows steady demand in 2025, primarily driven by infrastructure projects, commercial construction, and specialized manufacturing. The sector benefits from ongoing maintenance needs in existing structures and industrial facilities. While overall demand remains stable, specific areas like HVAC installation and custom fabrication show consistent growth.
Recent industry changes include a greater emphasis on precision and efficiency, often supported by computer numerical control (CNC) machinery and advanced welding techniques. The integration of AI primarily impacts design and planning phases, leading to more complex blueprints that require precise execution from skilled workers. Economic conditions, particularly interest rates affecting construction, can cause project delays, but a general backlog of work sustains demand.
Employer requirements increasingly favor candidates with certifications in specific welding processes, blueprint reading, and experience with automated bending and cutting equipment. Basic computer literacy for machine operation is becoming essential. Salary trends show a moderate upward trajectory for experienced, multi-skilled workers, while entry-level wages remain competitive but not rapidly increasing. Geographic variations are significant; urban and industrial centers offer more opportunities than rural areas, although remote work is not applicable here.
Seasonal patterns influence demand, with construction-related work peaking in warmer months and slowing in winter. The aging workforce also creates consistent openings, as experienced workers retire and new talent is needed to fill those gaps.
Emerging Specializations
Technological advancements and evolving industry demands are continuously reshaping traditional career fields, including sheet metal fabrication. These shifts create novel specialization opportunities that reward forward-thinking professionals. Early positioning in these emerging areas is crucial for career advancement, offering a competitive edge in 2025 and beyond.
Specializing in cutting-edge areas often leads to premium compensation and accelerated career growth. While established specializations remain vital, exploring emerging niches can unlock significant long-term potential. These new fields, driven by innovations in automation, materials, and design, typically transition from niche to mainstream within five to ten years, creating substantial job opportunities.
Professionals considering these paths must weigh the risk and reward. Pursuing a cutting-edge specialization requires continuous learning and adaptability. However, the potential for becoming an in-demand expert in a rapidly expanding field often outweighs the initial investment in new skills.
Robotic Fabrication Specialist
Advanced Materials Fabricator
Digital Design & Fabrication Specialist
Renewable Energy Component Fabricator
Hybrid Manufacturing Technician
Pros & Cons of Being a Sheet Metal Worker
Making informed career decisions requires a clear understanding of both the benefits and challenges associated with a specific profession. A career as a sheet metal worker, like any other, comes with its own unique set of advantages and disadvantages. These experiences can vary significantly based on the industry sector, the specific company culture, and the particular specialization within sheet metal work.
Moreover, the relevance of certain pros and cons may shift at different stages of a career, from entry-level positions to more senior roles. What one individual perceives as a benefit, another might view as a challenge, depending on personal values, physical capabilities, and lifestyle preferences. This assessment provides an honest, balanced perspective to help individuals set realistic expectations before committing to this skilled trade.
Pros
- There is consistent demand for skilled sheet metal workers in various industries, including construction, manufacturing, and HVAC, offering stable employment opportunities.
- The ability to work with your hands and see tangible results from your efforts provides a strong sense of accomplishment and job satisfaction.
- Sheet metal workers often acquire highly specialized and transferable skills in fabrication, welding, and installation, making them valuable across different sectors.
- Many entry-level positions can be secured through apprenticeships or vocational training, providing a direct path to employment without requiring a four-year degree.
- Skilled and experienced sheet metal workers can command competitive wages, with opportunities for increased earnings through specialization, overtime, or supervisory roles.
- The work environment is dynamic, often involving different projects and locations, which prevents monotony and offers variety in daily tasks.
- There are clear paths for career advancement, such as becoming a foreman, supervisor, estimator, or moving into design and project management roles within the industry.
Cons
- The work often involves physically demanding tasks, including lifting heavy materials, bending, and working in awkward positions, which can lead to fatigue and potential musculoskeletal issues over time.
- Sheet metal workers frequently operate noisy machinery and handle sharp materials, increasing the risk of cuts, burns, and hearing damage if proper safety protocols are not strictly followed.
- Many projects require working outdoors or in unconditioned environments, exposing workers to extreme temperatures, dust, and other weather elements.
- Some projects, particularly in construction or large manufacturing, may involve irregular hours, including early mornings, late nights, or weekend work, to meet tight deadlines.
- Specialized skills and certifications are often required for advanced projects or specific types of sheet metal work, demanding continuous learning and training to stay competitive.
- Job opportunities can sometimes be tied to the health of the construction or manufacturing industries, leading to potential fluctuations in demand during economic downturns.
- The repetition of certain tasks in sheet metal fabrication can lead to monotony and a lack of varied intellectual stimulation compared to roles with more diverse problem-solving challenges.
Frequently Asked Questions
Becoming a Sheet Metal Worker involves unique considerations beyond general construction. Individuals often wonder about the physical demands, the balance between shop work and on-site installations, and the specific skill set required for precision fabrication and assembly. This section addresses key questions about training, daily life, and career progression in this specialized trade.
What are the common entry requirements and training paths to become a Sheet Metal Worker?
Most Sheet Metal Workers enter the trade through a formal apprenticeship program, which typically lasts four to five years. These programs combine on-the-job training with classroom instruction, covering blueprint reading, welding, HVAC system installation, and various fabrication techniques. While not strictly required, a high school diploma or GED is usually a prerequisite for apprenticeship programs.
What does a typical day look like for a Sheet Metal Worker, and what are the primary responsibilities?
A typical workday for a Sheet Metal Worker can vary significantly. In a fabrication shop, you might spend the day cutting, bending, and shaping metal components using specialized machinery. On a construction site, tasks involve installing ductwork, roofing, or other sheet metal systems, often requiring work at heights or in confined spaces. The job demands precision, problem-solving, and adherence to safety protocols.
How physically demanding is the Sheet Metal Worker role, and what are the typical working conditions?
The physical demands are significant. Sheet Metal Workers frequently lift heavy materials, work in various postures, and use hand and power tools for extended periods. The job requires good stamina, strength, and dexterity. You must also be comfortable working at heights, in outdoor conditions, and sometimes in noisy or dusty environments.
What is the job outlook and security like for Sheet Metal Workers?
The job market for skilled Sheet Metal Workers is generally stable, driven by demand in construction, HVAC, and manufacturing. Infrastructure projects and the need for energy-efficient building systems contribute to ongoing demand. While economic downturns can affect construction, specialized skills in areas like HVAC or custom fabrication often provide resilience.
What are the salary expectations for a Sheet Metal Worker, from entry-level to experienced?
Salaries for Sheet Metal Workers vary based on experience, location, and union affiliation. Apprentices start at a lower wage, which increases as they gain skills and progress through their program. Experienced journeymen can earn competitive wages, often with benefits packages. Overtime opportunities can also significantly boost annual earnings.
What are the potential career advancement opportunities for a Sheet Metal Worker?
Career advancement for a Sheet Metal Worker can lead to roles such as foreman, supervisor, or project manager, overseeing teams and larger projects. Some specialize in specific areas like welding, HVAC system design, or architectural sheet metal, becoming highly sought-after experts. There are also opportunities to move into estimating or teaching roles within trade schools.
What is the typical work-life balance for a Sheet Metal Worker, and how does it compare between shop and site work?
Work-life balance can vary. Construction and installation projects often have strict deadlines, which can lead to longer hours, including evenings and weekends, particularly during peak seasons. However, shop-based fabrication roles may offer more consistent schedules. Union agreements often provide predictable hours and benefits, which can help manage work-life integration.
Are there significant safety concerns in this profession, and how are they addressed?
Yes, safety is paramount. Sheet Metal Workers routinely handle sharp materials, operate heavy machinery, and work at heights. Strict adherence to safety protocols, proper use of personal protective equipment (PPE), and continuous training are essential to minimize risks. Apprenticeship programs heavily emphasize safety education and practices from day one.
Related Careers
Explore similar roles that might align with your interests and skills:
Sheet Metal Mechanic
A growing field with similar skill requirements and career progression opportunities.
Explore career guideSheet Metal Fabricator
A growing field with similar skill requirements and career progression opportunities.
Explore career guideSheet Metal Installer
A growing field with similar skill requirements and career progression opportunities.
Explore career guideSheet Metal Layout Worker
A growing field with similar skill requirements and career progression opportunities.
Explore career guideSheet Metal Roofer
A growing field with similar skill requirements and career progression opportunities.
Explore career guideAssess your Sheet Metal Worker readiness
Understanding where you stand today is the first step toward your career goals. Our Career Coach helps identify skill gaps and create personalized plans.
Skills Gap Analysis
Get a detailed assessment of your current skills versus Sheet Metal Worker requirements. Our AI Career Coach identifies specific areas for improvement with personalized recommendations.
See your skills gapCareer Readiness Assessment
Evaluate your overall readiness for Sheet Metal Worker roles with our AI Career Coach. Receive personalized recommendations for education, projects, and experience to boost your competitiveness.
Assess your readinessSimple pricing, powerful features
Upgrade to Himalayas Plus and turbocharge your job search.
Himalayas
Himalayas Plus
Himalayas Max
Find your dream job
Sign up now and join over 100,000 remote workers who receive personalized job alerts, curated job matches, and more for free!
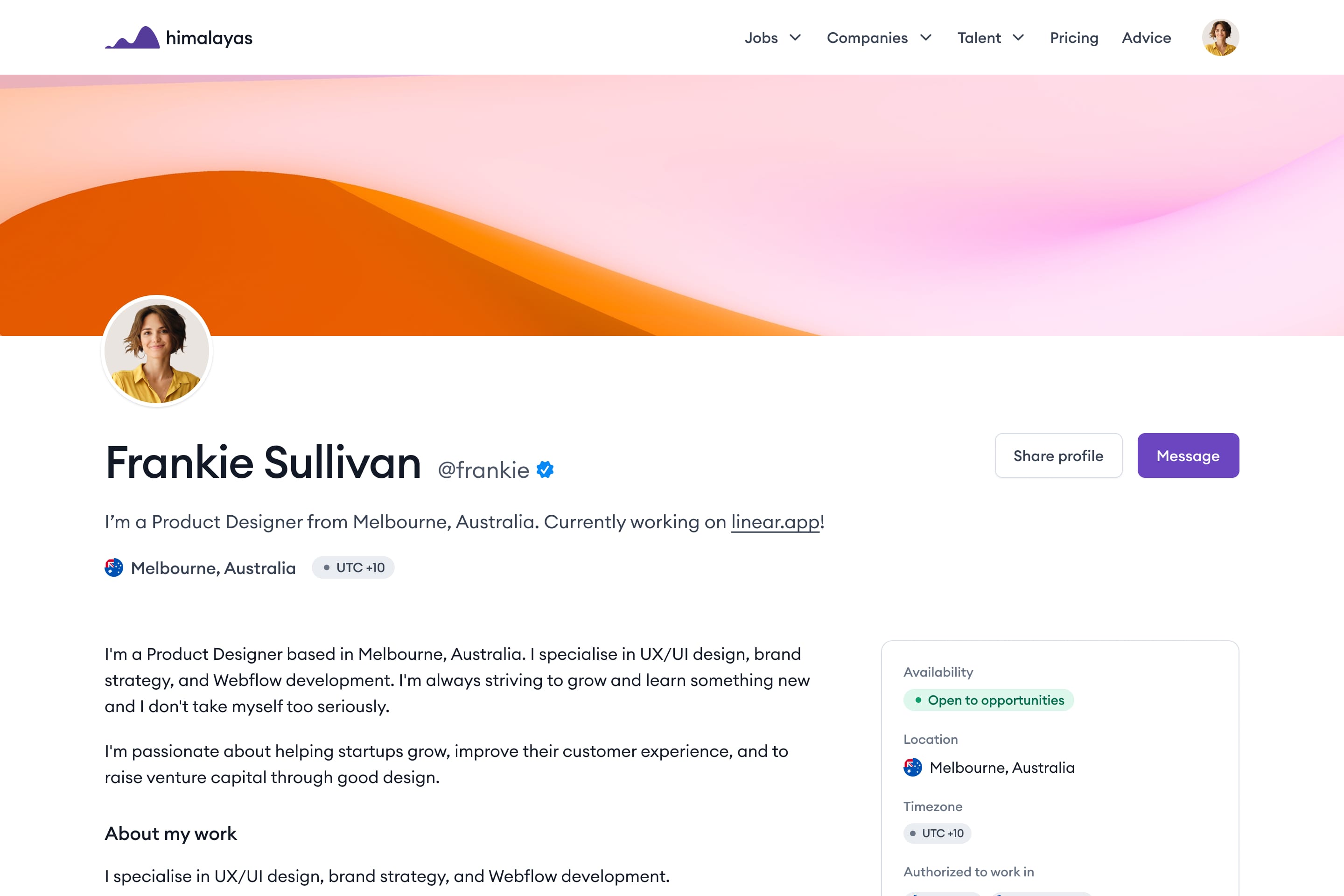